
[ТМиП]metodichka_part1
.pdf
определить, какому участку поля рассеяния она соответствует. К примеру, точки А и В, соответствующие размерам пробной заготовки, могут принадлежать кривым 1 и 2, расположение которых исключает появление брака, но они могут также относится и к кривым 1а и 2а, которые в значительной мере выходят за пределы допуска, что связано с появлением большого количества брака (заштрихованные участки на рис. 4.1). По мере увеличения числа пробных заготовок вероятность появления значительного брака снижается, но опасность его появления полностью не устраняется.
С целью исключения опасности появления брака в случае, когда поле допуска превышает поле рассеяния, т. к. ω IT , необходимо с помощью настройки обеспечить расположение кривой фактического распределения размеров внутри поля допуска с таким расчетом, чтобы ее центр группирования (математическое ожидание Em ) отстоял от предельных размеров на расстоянии не менее, чем 3σ.
Методом настройки станков по рабочим калибрам при небольшом числе пробных заготовок эту задачу решить нельзя. Для этого более рациональным является метод настройки станков с помощью универсальных измерительных средств по суженным допускам.
Настройка по пробным заготовкам с помощью универсальных измерительных средств
Вотличие от предыдущих, при этом методе настройки станков установка режущих инструментов и упоров станка производится на
определенный рабочий настроечный размер Lн, а правильность настройки устанавливается обработкой некоторого количества т пробных заготовок. При этом настройка признается правильной, если среднее арифметическое
размеров пробных заготовок находится в пределах некоторого допуска IТн на настройку. Следовательно, в этом методе задачей расчета настройки является определение величины поля допуска настройки IТн.
Воснову этого метода настройки положены следующие положения теории вероятностей. Если имеется некоторая совокупность (партия) заготовок, распределение размеров которых подчиняется закону нормального распределения Гаусса со средним квадратическим отклонением σ, и, если эту совокупность заготовок разбить на группы по т штук и определить среднее арифметическое значение размеров внутри каждой из этих групп, то распределение размеров групповых средних Lгр.ср
тоже будет подчиняться закону Гаусса со средним квадратическим отклонением σ1, которое равно:
1 σт .
101

При этом принципиально важно то обстоятельство, что центр группирования групповых средних всегда совпадает с центром группирования всей партии заготовок (рис. 6.2).
Расчет настройки без учета переменных систематических погрешностей
Прежде чем перейти к методике расчета, проанализируем случаи возможного появления брака при условии 6σ < IT. Для этого обратимся к схемам, представленным на рис.6 3.
Если центр группирования размеров пробных заготовок располагается по отношению к предельным размерам партии заготовок ближе, чем на расстоянии 3σ (точка М на рис. 6.3а), то часть общей кривой рассеяния размеров обработанной партии заготовок может выйти за пределы допуска, и возникает опасность появления брака. Даже если это расстояние несколько больше 3σ (точка М на рис. 6.3б), то брак обработанных заготовок возможен, так как точка М может принадлежать кривой групповых средних, центр группирования которых, а, следовательно, и центр группирования размеров всей партии заготовок, смещен на величину Р влево (рис.6.3б) от требуемого положения кривой, исключающего возможность брака.
Рис. 6.2. Распределение размеров партии заготовок со средним квадратическим σ и распределение групповых средних со средним квадратическим σ = σ m .
102

а) |
б) |
Рис. 6.3. Случаи возможного брака при 6σ < IТ (возможный брак показан штриховой).
Появление брака невозможно только в том случае, когда минимальный размер групповых средних пробных заготовок, определяющий положение точки М, будет определяться (рис.6.4):
Lгрmin.ср Lmin 3σ 3σ .
m
Рис.6. 4. Правильная настройка станка, исключающая опасность брака.
103

Очевидно, что при этом условии даже в том случае, когда центр
группирования групповых средних располагается на расстоянии 3 левее
m
точки М, он отстоит от границы наименьшего предельного размера заготовки на величину 3σ, и брак является невозможным. Аналогично сказанному:
Lгрmax.ср Lmin 3 3 .
m
Разность предельных значений групповых средних определяет величину допуска настройки Tн:
Т Lгр.ср Lгр.ср IT 6σ(1 |
1 |
|
). |
(6.5) |
|
|
|
|
|||
н max min |
|
|
|||
|
|
m |
|
Из формулы (6.6) видно, что допуск настройки зависит от общего допуска IT на обработку партии заготовок и от количества т пробных заготовок. Увеличивая число т пробных заготовок, можно расширить допуск настройки Тн, однако при этом возрастает время обработки пробных заготовок, что увеличивает продолжительность настройки. Как правило, количество пробных заготовок берется от 2 до 8.
При отсутствии влияния систематических погрешностей условие обработки заготовок без брака можно представить в виде:
IТ Tн 6σ(1 |
1 |
|
). |
(6.6) |
|
|
|
|
|||
|
m |
||||
|
|
|
|
|
В том случае, когда систематические погрешности оказывают существенное влияние на точность обработки заготовок, условие обработки без брака приобретает вид:
IТ T |
|
6σ(1 |
1 |
|
). |
|
сист |
|
|
|
|||
н |
|
|
m |
|
|
|
|
|
|
|
|
|
Следует заметить, что введенная в выражения (6.5) и (6.6) величина допуска настройки Тн не совпадает с погрешностью настройки н = ωн, которая определяет расстояние между крайними допустимыми положениями вершин кривых при настройке. Погрешность настройки в этом случае равна:
н ωн 1,2ω2рег ωизм2 ωсмещ2 ,
где ωрег – погрешность регулирования положения режущего инструмента; ωизм погрешность измерения пробных заготовок; ωсмещ погрешность смещения центра группирования групповых средних.
Допуск Тн настройки представляет разрешенное колебание
групповых |
средних, вызываемое |
погрешностями регулирования |
и |
измерения, |
и является частью |
общей погрешности настройки. |
В |
|
104 |
|

зависимости от погрешности регулирования и измерения допуск настройки можно определить по формуле:
Т |
н |
1,2 ω2 |
ω2 |
|
|
|
|
|
рег |
изм |
|
|
|
|
|
Как видно из рис.6.4, допуск Тн настройки меньше общей |
|||||||
погрешности н настройки на |
|
величину |
ωсмещ |
6σ |
|
, представляющую |
|
|
|
|
|
||||
|
|
m |
|||||
|
|
|
|
|
|
|
собой поле вероятного смещения положения вершины кривой рассеяния размеров групповых средних пробных заготовок.
Приведенный метод расчета настройки станков применяется при обработке точных заготовок, когда поле допуска IT незначительно превышает рассеяние размеров 6σ, что не дает возможности заранее предусмотреть компенсацию переменных систематических погрешностей, к примеру, износа режущего инструмента. Поэтому данный метод настройки станков приемлем при обработке заготовок, когда износ инструментов незначителен, например, при алмазной обработке цветных сплавов, а также при обработке небольших партий заготовок, когда износ режущего инструмента внутри обрабатываемой партии не оказывает серьезного влияния на потерю точности обработки.
Во всех этих случаях задача настройки станка сводится к обеспечению совмещения вершины кривой фактического распределения размеров с серединой поля допуска, т. к. Em Ес . При этом настроечный
размер определяется по выражению:
L |
|
|
Lmax |
Lmin |
0,5Т |
|
. |
н |
|
2 |
н |
||||
|
|
|
|
(6.7) |
|||
|
|
|
|
|
|
Расчет настройки с учетом переменных систематических погрешностей
В тех случаях, когда осуществляется обработка крупных партий заготовок, на точность процесса существенное влияние оказывает износ режущего инструмента, вызывающий появление переменных систематических погрешностей. Поэтому при настройке возникает задача наиболее рационального расположения кривой рассеяния в поле допуска с целью использования части этого поля для компенсации переменных систематических погрешностей обработки. За счет этого удается увеличить продолжительность работы станка без поднастройки, и, как следствие, повысить производительность.
На рис.6. 5 показана схема рациональной настройки станка для обеспечения заданной точности при обработке охватываемого размера (вала).
105
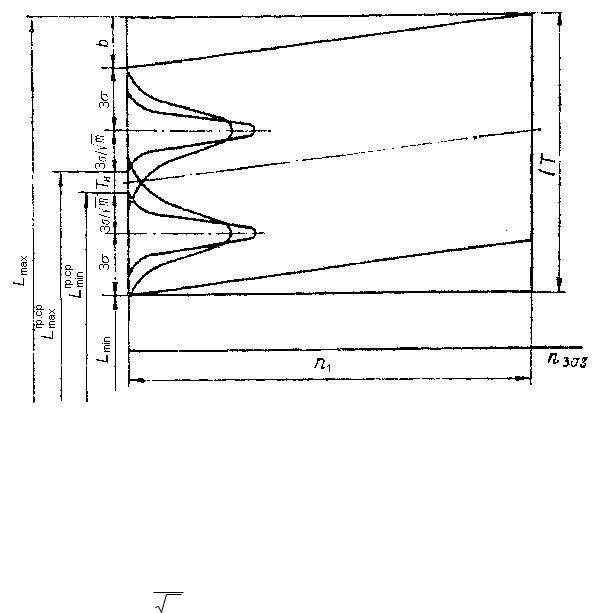
Рис.6. 5. Настройка станка с учетом переменных систематических погрешностей.
Отсюда видно, что некоторая часть Тн общего поля допуска IT используется для компенсации погрешностей настройки (Тн = ωн). Вторая часть общего поля допуска служит для компенсации случайных погрешностей, вызывающих рассеяние размеров, которая определяется
величиной 6σ(1 1m ) . Оставшаяся часть в общего поля допуска
предназначена для компенсации погрешностей, вызываемых совокупным действием систематически действующих факторов, как постоянных по величине, так и закономерно изменяющихся (например, износ режущего инструмента). В ходе обработки партии заготовок из-за износа режущего инструмента происходит изменение положения кривой рассеяния внутри поля допуска. Поэтому после обработки некоторого количества заготовок п1 кривая рассеяния размеров заготовок пересекает линию наибольшего
предельного размера, и возникает опасность появления брака. В этот момент необходимо осуществить поднастройку станка, в результате которой кривая рассеяния возвратится вниз в свое исходное положение, достигнутое первоначальной настройкой.
При такой настройке, очевидно, нельзя определять настроечный групповой средний размер по величине среднего арифметического, а следует вычислять его по значениям предельных размеров. Во избежание
106

получения при обработке маломерных заготовок чтобы минимальное значение группового среднего выражению:
Lгрmin.ср Lmin 3σ(1 |
1 |
|
|
|
|
|
|
|
|
|
|
|
m |
|
|
|
|
|
необходимо (рис.6.5), размера удовлетворяло
). (6.8)
Если при обработке партии заготовок проявляется существенное влияние переменных систематических погрешностей, уменьшающих размеры охватываемых заготовок (к примеру, при значительном удлинении резца от нагрева в начальный период резания), в формулу (6.8) необходимо дополнительно ввести возможную величину погрешности а:
Lгр.ср L а 3σ(1 |
1 |
). |
(6.9) |
|
|
|
|||
min min |
|
|||
|
|
m |
|
Как правило, обработка заготовок производится при наличии интенсивного охлаждения зоны резания, поэтому значение а ничтожно мало, и расчет наименьшего настроечного размера производится по формуле (6.8).
Для подсчета максимального значения группового среднего размера с учетом части допуска в с целью компенсации переменных систематических погрешностей используется зависимость:
Lгр.ср L в 3σ(1 |
1 |
). |
(6.10) |
|
|
|
|||
max max |
|
|||
|
|
m |
|
Как и в предыдущем случае, допуск на настройку определяется разностью предельных значений групповых средних размеров:
Тн Lгрmax.ср Lгрmin.ср и после преобразований формул (6.8) и (6.10) приводится
квиду:
Tн IT 6σ(1 |
1 |
|
) в. |
(6.11) |
|
|
|
|
|||
|
m |
||||
|
|
|
|
|
Из (6.10) видно, что при увеличении Тн с целью упрощения и ускорения настройки при прочих равных условиях приходится сокращать величину в, что, в свою очередь, приводит к возрастанию числа необходимых поднастроек и снижает производительность операции. По этой причине производить расширение поля допуска на настройку обычно целесообразно при условии изменения других факторов, входящих в приведенные выражения, в частности, при расширении общего поля допуска IT или уменьшении рассеяния 6σ.
Полученная формула (6.11) отличается от выражения (6.6) тем, что при учете переменных систематических погрешностей допуск настройки Тн уменьшается на величину в, которая предназначена для компенсации влияния этих погрешностей на точность размеров. Выполнять расчет настройки станка для случая обработки вала с учетом переменных систематических погрешностей удобно в следующей последовательности:
107
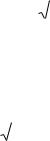
1.Пользуясь формулой (6.8), определяют величину Lгрmin.ср .
2.По формуле (6.11) находится минимально необходимая для условия данной операции величина Tн .
3.Значение Lгрmax.ср определяется по формуле:
Lгр.ср Lгр.ср |
|
T . |
(6.12) |
|||
max |
min |
|
н |
|
|
|
4. Часть допуска в, предназначенная для компенсации износа |
||||||
инструмента, определяется по формуле (1.3.6) из соотношения: |
||||||
в IT 6σ(1 |
1 |
|
) Т |
|
. |
|
|
|
|
н |
|||
|
||||||
|
|
m |
|
|
|
|
|
|
|
|
|
|
При заданном в значение Lгрmax.ср находится из выражения (6.10).
Если условие обработки заготовок без брака не выполняется, и сумма случайных и систематических погрешностей обработки оказывается
больше поля допуска, т. к. 6σ(1 |
1 |
|
) Т |
|
|
|
IT , то при обработке |
|
|
|
|
н |
сис |
||||
|
||||||||
|
|
m |
|
|
||||
|
|
|
|
|
|
возможен брак.
В том случае, когда отсутствует возможность повысить точность операции, настройку станка следует производить с таким расчетом, чтобы полученный брак (при обработке валов) оказался исправимым при дальнейшей обработке заготовок.
Окончательное решение о настройке станка с заведомо технически возможно исправимым или неисправимым браком можно принять только на основе точного расчета экономической целесообразности нового варианта обработки.
Порядок выполнения работы
Исходные данные к работе – комплект заготовок Ø 14 h 9(– 0,043)
Rz = 16 мм.
1. Измерить партию заготовок с помощью универсальных измерительных средств. (результаты занести в таблицу 6.1)
Таблица 6.1 Результаты измерений
№ детали |
|
1 |
|
2 |
|
… |
|
n |
Действительный |
|
13,973 |
|
13,980 |
|
… |
|
… |
размер детали |
|
|
|
|
|
|
|
|
2. Определить |
настроечный |
размер при |
статической |
настройке |
станка по формулам 6.1, 6.2 (настроечные размеры установочного калибра или эталонной детали).
3. Определить допуск настройки и настроечный размер:
108
а) без учета переменных систематических погрешностей, формулы
6.5; 6.7.
б) с учетом переменных систематических погрешностей формулы
6.9;6.10; 6.11.
Содержание отчета
1.Наименование и цель работы.
2.Инструмент и принадлежности.
3.Таблица с результатами измерений 4. Расчет настроечного размера и допуска настройки для каждого метода.
5Выводы.
Контрольные вопросы
1.Методы настройки станков.
2.По каким размерам производится настройка при статическом
методе?
3.Какую точность обеспечивает статическая настройка станка?
4.Преимущества и недостатки статической настройки станков.
5.Для какого типа производства используется статическая настройка станков?
6.Сущность метода настройки станков с помощью универсальных измерительных средств.
7.Условие обработки заготовок без брака при отсутствии влияния систематических погрешностей.
8.ЛИТЕРАТУРА
1. Маталин А.А. Технология машиностроения. Учебник для вузов. – М.: Машиностроение, 1985. – С. 106-116.
109
Лабораторный практикум по дисциплине «Технология приборостроения», для студентов
специальностей Т 06.01.00 – «Приборостроение», Т 06.03.00 – «Биотехнические и медицинские аппараты и системы», Т 06.04.00 – «Технология и оборудование ювелирного производства»
В 2-ух частях Часть 1
Учебное пособие
Ответственный за выпуск Аношко А. П.
Подписано в печать 15.09.2003. Бумага офсетная. Формат 60х40/16. Гарнитура Times. Печать офсетная. Усп. печ. л. 5,3. Тираж 200 экз. Заказ 238.
Издательство УП «Технопринт», ЛВ №380 от 28.04.99 Отпечатано в типографии УП «Технопринт», ЛП №203 от 28.01.2003 г.
220027, Минск, пр. Скорины, 65, корп. 14, оф. 317, Тел./факс 231-86-93.
110