
Krovelnye_raboty
.pdf
как жидкое стекло.
Для придания покрытию лучших пластических свойств в него вводят формующие добавки – такие, как бетонит, каолин, декстрин, слюда и пр.
В зависимости от свариваемых материалов все электроды делятся на следующие группы:
Л – для сварки легированных конструкционных сталей с временным сопротивлением разрыву свыше 600 МПа (пять типов: Э70, Э85, Э100, Э125, Э150);
У – для сварки углеродистых и низкоуглеродистых конструкционных сталей; В – для сварки высоколегированных сталей с особыми свойствами; Т – для сварки легированных теплоустойчивых сталей – 9 типов;
Н – для наплавки поверхностных слоев с особыми свойствами – 44 типа.
Гарантируемый предел прочности металла шва обозначается в марке электродов цифрами. Например, название электрода, обозначенное Э42, говорит о том, что он предназначен для дуговой сварки; минимальный предел прочности металла шва – 420 МПа.
Основные виды сварки
Дуговая сварка представляет собой соединение расплавленных металлов между собой с помощью электрической дуги (рис. 95).
Рис. 95. Дуговая сварка: 1 – соединяемые детали; 2 – электрод; 3 – дуга; 4 – сварочная ванна.
Этот тип сварки включает в себя такие виды, как плазменная, электрошлаковая, электронно-лучевая и термитная.
Плазменная сварка основана на пропускании электрического тока большой плотности через газовую среду, находящуюся под некоторым давлением. Ионизированный газ называют плазмой. Температура плазменной струи достигает 50 000 °C.
В электрошлаковой сварке плавление металла происходит за счет теплоты, выделяемой электрическим током, проходящим через расплавленный шлак (рис. 96).

Рис. 96. Электрошлаковая сварка: 1 – электрод; 2 – электропроводный шлак; 3 – образуемый шов; 4 – сварочная ванна; 5 – перегородки, формирующие шов; 6 – металл.
Энергия электронного луча нашла свое применение в электронно-лучевой сварке. Теплота выделяется в результате бомбардировки поверхности металла электронами, имеющими большие скорости; анодом служит свариваемая деталь, катодом – вольфрамовая спираль (рис. 97).
Рис. 97. Электронно-лучевая сварка: 1 – катод; 2 – пучок; 3 – соединяемые заготовки; 4 – магнитная линза; 5 – катушка.
Поверхность катода испускает электроны, формируемые в пучок, который фокусируется на соединяемые заготовки магнитной линзой. Перемещает луч специальная катушка.
Использование теплоты, выделяемой нагретой смесью оксида железа и алюминия, лежит в основе термитной сварки. Свариваемые детали находятся в огнеупорной форме, а в тигле, находящемся сверху, находится смесь металлов. При горении температура этой смеси (по-другому, термита) достигает более 2000 °C. В результате образуется жидкий металл, который при заполнении формы оплавляет кромки свариваемых изделий, заполняет зазор, образуя тем самым шов.
В ультразвуковой сварке ультразвуковые колебания передаются по волноводу от преобразователя к рабочему наконечнику.
Соединяемые изделия помещают между наконечником и специальной опорой.
Под действием вертикального сжимающего усилия и ультразвуковых колебаний в заготовках возникают силы трения, достаточные для получения сварного соединения (рис. 98).

Рис. 98. Ультразвуковая сварка: 1 – магнитострикционный преобразователь; 2 – волновод; 3 – рабочий наконечник; 4 – соединяемые изделия; 5 – опора.
При контактной сварке, которая, в свою очередь, делится на точечную и стыковую, происходит сварка давлением. Здесь соединяемые заготовки зажимаются электродами. В зоне контакта под действием сварочного тока происходит сильный разогрев, затем сжатие заготовок и, как результат, образование сварного соединения (рис. 99).
Рис. 99. Контактная сварка: 1 – соединяемые заготовки; 2 – электроды; 3 – зона контакта.
Если при соединении изделия используют радиочастотную сварку, то свариваемые заготовки нагреваются с помощью высокочастотного индуктора. В результате этого происходит оплавление кромок заготовок. Сварное соединение получается в результате сжимающего действия роликов (рис. 100). Сердечник из феррита повышает эффективность процесса.
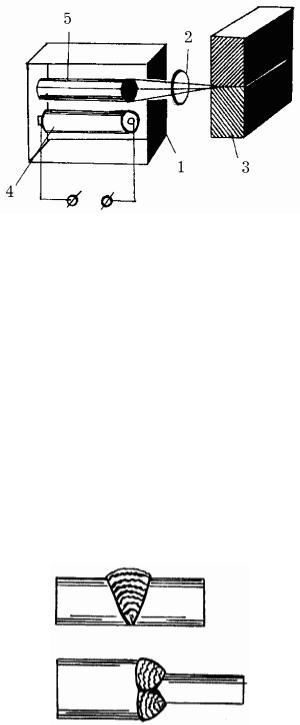
Рис. 100. Радиочастотная сварка: 1 – высокочастотный индуктор; 2 – свариваемые части; 3 – ролики; 4 – ферритовый сердечник.
Лазерная сварка осуществляется световым лучом, получаемым от специальных твердых и газовых излучателей. Вакуум при сварке лазером не нужен, и ее можно выполнять на воздухе даже на значительном расстоянии от генератора (рис. 101).
Рис. 101. Лазерная сварка: 1 – излучение лазера; 2 – линза; 3 – свариваемые заготовки; 4 – лампа накачки; 5 – рубиновый стержень.
Сварка трением осуществляется с помощью вращения одного из стержней и соприкосновения его торца с торцом закрепленного стержня; концы стержней разогреваются и с приложением осевого усилия свариваются.
Холодная сварка базируется на свойстве металла схватываться при значительном давлении.
В зависимости от механизации процесса сварку можно разделить на ручную, механизированную и автоматическую.
Виды сварных соединений и швов при дуговой сварке
Сварные швы можно разделить на 4 вида: стыковые, тавровые, угловые и нахлесточные.
Сам по себе шов представляет закристаллизовавшийся металл, который в процессе сварки находился в расплавленном состоянии.
Стыковой шов предназначен для соединения торцевых поверхностей деталей, причем толщина их может быть различной (рис. 102).
Рис. 102. Стыковой шов.
Стыковые швы широко применяют в машиностроении, а также при сварке больших емкостей и труб. В тавровом шве торец одной заготовки приваривается к боковой поверхности другой (рис. 103).

Рис. 103. Тавровый шов.
Обычно такие соединения имеют вид буквы «Т» (отсюда и название).
Элементы в тавровом соединении можно соединять как под прямым, так и под любым другим углом. Угловой шов соединяет два элемента, которые находятся под любым углом друг к другу (рис. 104).
Рис. 104. Угловой шов.
Такие швы получили распространение в строительстве.
При соединении 2 листов металла, в котором один лист накладывается на другой с нахлестом, образуется нахлесточный шов (рис. 105).
Рис. 105. Нахлесточный шов.
Нахлесточные швы применяются в конструкциях металлических форм, резервуаров и пр.
Подготовительные работы

Подготовительные работы включают в себя правку, разметку, резку, подготовку кромок под сварку и холодную или горячую гибку.
Правку выполняют на станках или вручную. При правке устраняются деформации металла. Металл небольшой толщины правится в холодном состоянии, а толстый предварительно подогревается до 250– 300 °C.
Целью разметки является нанесение размеров детали на металл. Обычно ее наносят по шаблонам из алюминиевого листа. При разметке используют линейку, угольник, рулетку, чертилку.
Резка может быть как механической, так и термической. Наиболее производительной является механическая. Термическая же, уступая ей, является более универсальной, так как позволяет с большей точностью выкроить заготовки различной геометрической формы.
Подготовка кромок, как и резка, ведется 2 способами: механическим и термическим. В основном используется механический способ. Используя 2 или 3 резака, расположенных под разными углами, можно получить кромки с односторонним или двусторонним скосом.
Кроме классической гибки, осуществляемой на листогибочных вальцах, существует множество других способов.
В подготовительные работы, кроме вышеперечисленных, входит также очистка металла от масла, ржавчины, окалины, влаги и различных неметаллических загрязнений. Присутствие этих загрязнений часто является причиной образования в сварных швах пор, трещин, шлаковых включений, что ведет к снижению прочности сварного соединения.
Техника выполнения ручной дуговой сварки
Дуговая сварка металлическими электродами с покрытием остается самым распространенным методом, применяемым при изготовлении и монтаже конструкций. В начале работы следует зажечь (возбудить) дугу, установив нужное значение сварочного тока. Оно зависит от марки электрода и типа сварного соединения.
Зажигать дугу можно разными способами. При первом способе электрод приближают перпендикулярно к поверхности изделия и, коснувшись металла, быстро отводят вверх на необходимую длину дуги. При втором способе электродом вскользь чиркают по поверхности металла.
Существует такое понятие, как длина дуги. Она напрямую зависит от марки и диаметра электрода, разделки свариваемых кромок.
Нормальная длина дуги составляет 0,5–1,1 диаметра электрода. Если длину увеличить, то качество наплавленного металла шва снижается ввиду его интенсивного окисления и азотирования; глубина проплавления основного металла уменьшается, ухудшая внешний вид шва. Сварку можно вести в разных направлениях: от себя, к себе, слева направо, справа налево (рис. 106).
Рис. 106. Направление движения электродов: а – движение электрода вправо; б – движение электрода влево; в – движение электрода вверх; г – движение электрода вниз.

Независимо от этого электрод всегда должен быть наклонен к оси шва таким образом, чтобы основной металл проплавлялся на наибольшую глубину. Для получения гладкого и плотного шва необходимо, чтобы угол наклона электрода в сторону ведения шва составлял 15°.
Существует 3 основных направления движения электрода. Первое из них – поступательное вдоль оси. Движение вдоль оси позволяет обеспечить постоянство длины дуги и связать это со скоростью плавления электродов.
Второе движение электрода – перемещение вдоль оси образуемого валика в направлении наплавки для образования шва. Образуется узкий валик, ширина которого зависит от скорости перемещения дуги по поверхности и сварочного тока. Узкий валик накладывают, проваривая корень шва или сваривая тонкие листы.
Третье движение включает в себя поперечные колебательные движения электрода (рис. 107).
Рис. 107. Виды поперечных движений электрода при различных режимах прогрева: а – при слабом прогреве кромок; б – при усиленном прогреве кромок; в – при усиленном прогреве одной кромки; г – при хорошем прогреве корня шва.
Техника сварки в нижнем положении
При этом положении можно получить сварные швы наиболее высокого качества, так как в этом случае значительно облегчаются условия выделения неметаллических включений и газов из расплавленного металла сварочной ванны. Сечение шва можно заполнить в один проход, многослойно
ив несколько проходов.
Однопроходная сварка с v-образной разделкой кромок выполняется с поперечными колебаниями
электрода на всю ширину, с выходом дуги со скоса кромок на необработанную поверхность (рис. 108).
Рис. 108. Однопроходное сечение стыкового шва.
Если число слоев равно числу проходов дуги, то шов называют многослойным. Если слой выполняется за несколько проходов, шов называют многопроходным.

При сварке шва с v-образной разделкой за несколько проходов можно обеспечить гораздо лучший провар первого слоя в корне разделки (рис. 109).
Рис. 109. Многослойное сечение стыкового шва.
Сварку ведут без поперечных колебаний с помощью электродов диаметром 3–4 мм. В зависимости от толщины металла последующие слои выполняют электродами большего диаметра, с поперечными колебаниями. Необходимо тщательно очищать от шлака и брызг металла все предыдущие слои: это обеспечит хороший провар и высокое качество шва.
Разделку кромок можно заполнять швами с шириной на всю разделку или отдельными валиками. В многопроходных швах последний валик можно выполнить на всю ширину разделки (рис. 110).
Рис. 110. Многопроходное сечение стыкового шва.
Вышеперечисленные виды швов нашли свое применение в различных соединениях: многослойные швы в стыковых, многопроходные – в угловых и тавровых соединениях. Протяженность швов варьируется от 300 до 1000 мм. В зависимости от этого все швы подразделяются на три группы: короткие – до 300 мм, средние – 300–1000 мм, длинные – свыше 1000 мм.
На выбор того или иного способа сварки влияют протяженность шва, свойства свариваемого материала и качество сварных соединений.
Выполнение коротких швов (до 300 мм) относят к наиболее простому способу. От начала до конца шва осуществляется движение напроход (рис. 111, а). При шве средней длины сварка ведется от середины к концу (рис. 111, б) или обратноступенчатым способом.
Рис. 111. Различные схемы сварки: а – сварка напроход; б – сварка от середины к краям; в – обратноступенчатый способ; г – «каскад»; д – «горка».
Швы, имеющие большую протяженность, можно варить как обратноступенчатым способом, так и вразброс. При обратноступенчатом способе удобно разбить шов на небольшие участки длиной 150–200

мм. Направление сварки каждого участка не должно совпадать с общим направлением сварки (рис. 111, в).
Швы конструкций, несущих большую нагрузку и имеющих значительную толщину свариваемых поверхностей, обычно сваривают способом «каскад» (рис. 111, г) или «горка» (рис. 111, д).
Чтобы в зоне сварки не возникали объемные напряжения, ведущие к образованию трещин, необходимо во время работы поддерживать в ней высокую температуру. Величина сварочного тока влияет на толщину шва свариваемых деталей из низкоуглеродистой стали. Она может колебаться от 3 до 5 мм.
При силе тока, равной 100 А, происходит расплавление металла на глубину 1 мм с термической обработкой нижнего слоя на глубину 1–2 мм. Если сила тока достигает 200 А, то толщина слоя возрастает до 4 мм. При этом происходит термическая обработка нижнего слоя на глубину 2–3 мм.
Если сварка ведется на весу (рис. 112), то необходимо обеспечить максимальный провар корня шва и сформировать качественный обратный валик. В этом случае хорошо зарекомендовал себя способ сварки на съемной медной (рис. 113) или остающейся стальной подкладке (рис. 114). При этом в медной подкладке делается формирующая канавка. Чтобы расплавленный металл не вытекал из сварочной ванны, необходимо обеспечить плотное обжатие подкладок к свариваемым кромкам. Остающиеся подкладки не всегда технологичны, так как увеличивают расход металла. Если допустима выпуклость обратной стороны, то допускается подварка корня шва с последующей укладкой основного шва (рис. 115).
Рис. 112. Сварка на весу.
Рис. 113. Сварка на медной съемной подкладке.
Рис. 114. Сварка на остающейся стальной подкладке.
Р ис. 115. Сварка с предварительным подварочным швом.
Окончание сварки
Правильная заварка кратера при обрыве дуги – окончание сварки – играет важную роль в сварочном процессе.
В зоне кратера скапливается наибольшее количество вредных примесей, образовавшихся в процессе кристаллизации металла. В этой зоне трещины образуются наиболее часто. Если сварка закончена, то при обрыве дуги не рекомендуется резко отводить электрод от изделия. Перемещения электрода следует прекратить и до обрыва медленно удлинять дугу. Такой прием способствует заполнению кратера электродным металлом. В некоторых случаях, например при сварке низкоуглеродистой стали, кратер выводят на основной металл, в сторону от шва. Если понадобилась смена электродов или произошел случайный обрыв дуги, то ее можно возбудить на еще нерасплавленном основном металле перед кратером. Металл проплавляют на кратере. Если ведется сварка стали, которая образует закалочные структуры, то вывод кратера в сторону недопустим из-за возможности образования трещин. Определение режима сварки
Основными параметрами нормального режима сварки являются величина и полярность тока, диаметр

электрода, скорость сварки и напряжение на дуге. Существуют и дополнительные параметры – толщина покрытия электрода и его состав, положение электрода и положение изделия.
Сварочный ток выбирают, ориентируясь на марку и диаметр электрода, учитывая при этом положение шва в пространстве, вид соединения, а также толщину свариваемого изделия. При этом сила тока должна быть максимально возможной. Чем больше ток, тем выше производительность труда и больше наплавляется металла. Увеличение силы тока влияет также на глубину провара.
Полярность тока и его вид (постоянный или переменный) оказывают влияние на размеры шва и его форму. Если сварка ведется при постоянном токе, имеющем обратную полярность, то глубина провара на 50 % больше, чем при постоянном токе прямой полярности. Это объясняется тем, что на аноде и катоде выделяется разное количество теплоты. Глубина провара при сварке переменным током на 15 % меньше той, которая получается при сварке постоянным током прямой полярности.
На диаметр электрода влияют толщина свариваемого металла, вид соединения и форма подготовленных кромок под сварку. Если ведется сварка стыков металла, толщина которых достигает 4 мм, то используются электроды того же диаметра, что и толщина кромок.
Если свариваемый металл имеет большую толщину, то задействуются электроды диаметром 4–8 мм. При этом должны соблюдаться условия провара основного металла. Если стыковые швы имеют несколько слоев, то желательно первый шов выполнить электродом диаметром 3–4 мм, с обязательной сваркой последующих слоев электродами большего диаметра.
Техника выполнения горизонтальных, вертикальных и потолочных швов
Если сварка швов ведется в положениях, отличающихся от нижнего, то возникает вероятность вытекания расплавленного металла из сварочной ванны. В таких положениях металл может капать мимо нее. Для предотвращения этого сварку следует вести наиболее короткой дугой, ведя поперечные колебания электродов.
Слой расплавленного металла удерживается от вытекания из сварочной ванны силой поверхностного натяжения. Чем тоньше пленка расплавленного металла, тем больше вероятность ее удержания этой силой. Достигается это за счет периодического отведения в сторону от ванны конца электрода. Такое отведение создает возможность быстрой кристаллизации металла. Удерживать металл от вытекания помогают и такие приемы, как понижение на 10–20 % силы тока и применение электродов уменьшенного диаметра: для вертикальных и горизонтальных швов – не более 5 мм, для потолочных – 10 мм.
Выполнение вертикальных швов
Сварку таких швов можно осуществлять как на подъем, так и на спуск (рис. 116).
Рис. 116. Вертикальный шов.
При сварке на подъем нижележащий металл шва, который почти закристаллизовался, удерживает расплавленный металл, находящийся в сварочной ванне. Сварка на подъем дает возможность более тщательно проваривать корень шва и кромки, так как расплавленный металл стекает с электрода прямо в сварочную ванну. Недостатком данного способа является грубый внешний вид шва: его поверхность как будто покрыта чешуей.
При сварке на спуск трудно получить качественный провар места соединения деталей, так как шлак и расплавленный металл подтекают под дугу. При малом значении силы поверхностного натяжения