
Воробева Нуцлеар Реацтор Тыпес (Леарн то реад бы реадинг) 2010
.pdfnificant capital expenditure in upgrading systems and components, including building in extra performance margins. There is widespread agreement that further extensions may be justified, and this prospect is driving research on ageing to ensure both safety and reliability in older plants.
The IAEA has a safety knowledge base for ageing and long term operation of nuclear power plants (SKALTO) which aims to develop a framework for sharing information on ageing management and long term operation of nuclear power plants. It provides published documents and information related to this.
Reporting nuclear incidents
The International Nuclear Event Scale (INES) was developed by the IAEA and OECD in 1990 to communicate and standardise the reporting of nuclear incidents or accidents to the public. The scale runs from a zero event with no safety significance to 7 for a "major accident" such as Chernobyl. Three Mile Island rated 5, as an "accident with off-site risks" though no harm to anyone, and a level 4 "accident mainly in installation" occurred in France in 1980, with little drama. Another accident rated at level 4 occurred in a fuel processing plant in Japan in September 1999. Other accidents have been in military plants.
Terrorism
Since the World Trade Centre attacks in New York in 2001 there has been concern about the consequences of a large aircraft being used to attack a nuclear facility with the purpose of releasing radioactive materials. Various studies have looked at similar attacks on nuclear power plants. They show that nuclear reactors would be more resistant to such attacks than virtually any other civil installations.A thorough study was undertaken by the US Electric Power Research Institute (EPRI) using specialist consultants and paid for by the US Dept. of Energy. It concludes that US reactor structures "are robust and (would) protect the fuel from impacts of large commercial aircraft".
The analyses used a fully-fuelled Boeing 767 — 400 of over 200 tonnes as the basis, at 560 km/h — the maximum speed for precision flying near the ground. The wingspan is greater than the diameter of reactor containment buildings and the 4.3 tonne engines are 15 metres apart. Hence analyses focused on single engine direct impact on the centreline — since this would be the most penetrating missile — and on the impact of the entire aircraft if the fuselage hit the centreline (in which case the engines
151
would ricochet off the sides). In each case no part of the aircraft or its fuel would penetrate the containment. Other studies have confirmed these findings.
Penetrating (even relatively weak) reinforced concrete requires multiple hits by high speed artillery shells or specially-designed "bunker busting" ordnance — both of which are well beyond what terrorists are likely to deploy. Thin-walled, slow-moving, hollow aluminum aircraft, hitting containment-grade heavily-reinforced concrete disintegrate, with negligible penetration. But further (see Sept 2002 Science paper and Jan 2003 Response & Comments), realistic assessments from decades of analyses, lab work and testing, find that the consequence of even the worst realistic scenarios — core melting and containment failure — can cause few if any deaths to the public, regardless of the scenario that led to the core melt and containment failure.
In 1988 Sandia National Laboratories in USA demonstrated the unequal distribution of energy absorption that occurs when an aircraft impacts a massive, hardened target. The test involved a rocket-propelled F4 Phantom jet (about 27 tonnes, with both engines close together in the fuselage) hitting a 3.7 m thick slab of concrete at 765 km/h. This was to see whether a proposed Japanese nuclear power plant could withstand the impact of a heavy aircraft. It showed how most of the collision energy goes into the destruction of the aircraft itself — about 96 % of the aircraft's kinetic energy went into the its destruction and some penetration of the concrete, while the remaining 4 % was dissipated in accelerating the 700-tonne slab. The maximum penetration of the concrete in this experiment was 60 mm, but comparison with fixed reactor containment needs to take account of the 4 % of energy transmitted to the slab. The study of a 1970s US power plant in a highly-populated area is assessing the possible effects of a successful terrorist attack which causes both meltdown of the core and a large breach in the containment structure — both extremely unlikely. It shows that a large fraction of the most hazardous radioactive isotopes, like those of iodine and tellurium, would never leave the site.
Much of the radioactive material would stick to surfaces inside the containment or becomes soluble salts that remain in the damaged containment building. Some radioactive material would nonetheless enter the environment some hours after the attack in this extreme scenario and affect areas up to several kilometres away. The extent and timing of this means that with walking-pace evacuation inside this radius it would not be a major
152
health risk. However it could leave areas contaminated and hence displace people in the same way as a natural disaster, giving rise to economic rather than health consequences.
Looking at spent fuel storage pools, similar analyses showed no breach. Dry storage and transport casks retained their integrity. "There would be no release of radionuclides to the environment".
Similarly, the massive structures mean that any terrorist attack even inside a plant (which are well defended) and causing loss of cooling, core melting and breach of containment would not result in any significant radioactive releases.
Switzerland's Nuclear Safety Inspectorate studied a similar scenario and reported in 2003 that the danger of any radiation release from such a crash would be low for the older plants and extremely low for the newer ones.
The conservative design criteria which caused most power reactors to be shrouded by massive containment structures with biological shield has provided peace of mind in a suicide terrorist context. Ironically and as noted earlier, with better understanding of what happens in a core melt accident inside, they are now seen to be not nearly as necessary in that accident mitigation role as was originally assumed.
Advanced reactor designs
The designs for nuclear plants being developed for implementation in coming decades contain numerous safety improvements based on operational experience. The first two of these advanced reactors began operating in Japan in 1996.
The main feature they have in common (beyond safety engineering already standard in Western reactors) is passive safety systems, requiring no operator intervention in the event of a major malfunction.
These designs are one or two orders of magnitude safer than older ones in respect to the likelihood of core melt accidents, but the significance of that is more for the owner than the neighbours, who — as Three Mile Island showed — are safe also with older types.
Safety relative to other energy sources
Many occupational accident statistics have been generated over the last 40 years of nuclear reactor operations in the US and UK. These can be compared with those from coal-fired power generation. All show that nuclear is a distinctly safer way to produce electricity. Two simple sets of figures are quoted in the Table below. A major reason for coal's unfa-
153

vourable showing is the huge amount which must be mined and transported to supply even a single large power station. Mining and multiple handling of so much material of any kind involves hazards, and these are reflected in the statistics.
Comparison of accident statistics in primary energy production.
(Electricity generation accounts for about 40 % of total primary energy)
Fuel |
Immediate fatalities |
Who? |
Normalised to deaths |
|
1970-1992 |
per TWy1 electricity |
|||
Coal |
6400 |
workers |
342 |
|
Natural |
1200 |
workers & |
85 |
|
gas |
public |
|||
|
|
|||
Hydro |
4000 |
public |
883 |
|
Nuclear |
31 |
workers |
8 |
Annex 4
High Temperature Gas Cooled /Pebble Bed Modular/ Reactors
PBMRs and HTGRs have a long history of development which include several phases.
Originally the necessity to develop the reactor type was motivated by a possibility to achieve power generation using natural uranium and relatively inexpensive and available materials as moderator and coolant, the choice for these being graphite as a moderator and a gas as a coolant.
Graphite is known to be characterized by both high moderating capacity and small cross section for neutron absorption. Neutron diffusion length for pure graphite is about 0.5 m. Due to these facts graphite moderated reactor core is larger and power density is lower than those of LWRs. The requirement for lower neutron release is particularly significant for natural U reactors in order to be able to provide for adequate reactivity margin. Combination of natural U and graphite moderator make it necessary to load fuel heterogeneously in the core to minimize effective resonance integral.
1Basis: per million MWe operating for one year, not including plant construction, based on historic data which is unlikely to represent current safety levels in any of the industries concerned.
154
It should be noted that the basic drawback of gaseous coolants is that their thermal characteristics are worse as compared with those of liquid coolants. This fact also results in lower power capacity of the reactor and consequently bigger reactor core dimensions. Therefore to create an efficient system for removing heat in the reactor type involved it was necessary to use gas under high pressure. For the early projects CO was chosen as a coolant which is apart from low cost characterized by low absorption of thermal neutrons, weak interaction with graphite at temperatures which allow using metal U fuel. Low neutron absorption is important not only for neutron balance but also for preventing significant reactivity changes in case of a sudden loss of primary loop integrity.
The first phase resulted in developing reactors of Magnox type, natural metal U being used as fuel and CO2 as coolant. The first reactor of this type was constructed in GB in 1956. By 1971 there had been 26 reactors of this type in GB and 7 in France. The first phase has led to a number of novel technical solutions. The most important one for further development of gas cooled reactors is the technology of pre-stressed concrete reactor vessel / PCRV/. Use of this type of the vessel instead of a metal one made it possible to significantly raise pressure in the primary circuit up to 2.8 — 3.0 MPa, to increase unit power, to shift to integral layout of instruments and components of the primary circuit which is more convenient and safer in operating, to improve thermal efficiency up to 30 % and upper limit of coolant temperature to 414 °C.
The latter restrictions are because the temperatures of fuel and fuel pins cladding made of Mg alloy i.e. magnox should be within certain acceptable limit. The alloy is known to have low cross section. This enabled one to increase surface for heat exchange within reactor core without considerable change in neutron balance.
In Magnox type reactors problems of metal U stability and heat removal from fuel rods confine depth of burn up to 3600 MWt/day/t and power density of fuel to 5 MWt/T. Moreover inadequate burn up in such reactors is also determined by low content of fissile material in fuel. These restrictions can be avoided if one uses oxide U fuel and higher heat resistive material for fuel pins cladding, e.g., stainless steal. These measures were realized in advanced gas cooled reactor AGR. However the improvement was achieved due to fuel enrichment. Thus AGR reactor types developed in GB have become the second generation of gascooled graphite-moderated reactors.
155
As a result of all these efforts to develop and improve AGR is an adequately reliable design of a power rector of average capacity 600 MWt (el). Nevertheless the reactor designers have failed to meet the basic challenge – to create a reactor which could either successfully compete with LWR type reactors or provide utilities with absolutely new quality of heat produced which could be used not only in power engineering.
Further development of this concept was focused on improving thermodynamics efficiency of power generating facilities. This has resulted in a generally new design of High temperature (gas) reactor which did not have restrictions on coolant temperature and core power density characteristics of AGR. To achieve this the following measures were taken:
CO2 as a coolant which under irradiation and at temperatures higher than 600 °C vigorously interacts with graphite has been substituted by chemically inert helium which can operate with graphite at temperatures up to 1000 °C and even higher. One should admit that helium as compared to CO2 at equal temperatures has lower thermal capacity and demands greater energy for circulating. However possessing good thermal conductivity helium at the same temperatures provides for higher power density in the core.
Heterogeneous structure of fuel assembly has been given up and instead micro fuel elements which are dispersed throughout graphite matrix have been used. Increase of the heat exchange surface area obtained decreases temperature drop between fuel and coolant. Highly resistive cladding of micro fuel elements made of PyC and carbide selicon eliminates additional restrictions for core power density. During the 1-rst phase of HTGR development intensive tests of this fuel type were conducted which proved practical feasibility of the fuel.
So, high structural stability, chemical inertness and good nuclear physics characteristics of helium combined with oxide (or carbide) U fuel in the form of micro particles with multi layer cover which are dispersed throughout graphite matrix allow to obtain in HTGR good neutron balance and temperature up to 1000 °C. The latter principally expands the range of possible application of nuclear power generating facilities including apart from electrical engineering industrial heat supply of high temperature technological processes.
Such countries as Russia, United States, Germany and Japan have
156
accumulated considerable experience in developing HTGRs. Reactor Fort Saint Vrain of 837 MWt of heat in US, AVR 15 MWt el. and THTR — 300 750 MWt of heat capacity in FRG have been operating successfully.
It is worth mentioning that at present due to joint efforts of US (General Atomics), Russia (OKBM), France (Framatom), Japan (Fudji Electric) a conceptual design has been accomplished for GT-MHR of 600 MWt, the NPP with modular helium reactor and gas turbine. The designers claim that thermal efficiency of the NPP is about 50 %.
Simultaneously with developing general concept of gas-cooled graphite moderated reactors safety barriers of these reactors were also under investigation. As far as safety is concerned gas cooled reactor is simpler than LWR. First of all there is no risk of a considerable increase of reactivity due to sharp change of either of quantity or density of moderator (coolant) in the core. Compare HTGR with PWR where there is always a risk that cold water free of boron can get into the core.
In a gas-cooled reactor there are no problems (or in case there are they are really insignificant) of fuel elements cladding and fuel interacting with steam and water in case of emergency. In particular, in gas cooled reactors there is a lower probability of release of non nuclear energy accumulated in graphite than that in water-cooled uranium graphite reactors since the probability itself has been fractured in such reactors i.e. there is a more reliable separation in space of potential components of exothermal reactions.
Graphite moderated air — cooled commercial reactor Windscale – 1 is known to have suffered an accident in 1957. It happened when the reactor was shut down for removing Vigner energy accumulated in the coolant during operating at low temperature through heating the graphite. After the second reactor shut down when the cooling system became unavailable a sharp increase of fuel elements temperature happened due to Vigner energy release. Fuel elements overheating resulted in damaging their claddings, oxidizing the metal U and setting fire in graphite. Activity released into the
environment during the accident was 1.35 107 GBq, 137I being 6*105 GBq. Radionuclides 137Cs, 89Sr, 90Sr were not released due to the filters. In AGR
and HTGR accumulating energy in graphite is not a hazard since the graphite temperature here is much higher than that in the region where Wigner effect is significant.
In a gas cooled reactor in case of integrity loss of the cooling circuit sharp decrease in cooling efficiency does not occur as it does in a water
157
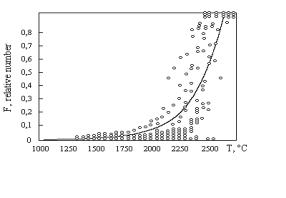
cooled reactor in case of water boiling. Effectiveness of heat removal with gaseous coolant is approximately proportional to its pressure. So, in AGR reactor coolant pressure drop from 4 to 0.1 MPa would cause decrease in heat removal effectiveness down to 2.5 % of nominal value.
As has been mentioned in respect to safety one of the safety advantages of gas cooled reactor design is pre-stressed concrete reactor vessel (PCRV) which cannot rupture like steel vessel of BWR or PWR. Any real destruction of such a vessel would be of a step-by-step character due to multi-layer partitions in the way of a possible release. Another advantage in safety is a better heat removal because of high thermal capacity of graphite.
Fig. 1. Experimental data on relative yield of fission products from HTGR fuel v s temperature
In high temperature gas cooled reactor utilizing graphite ceramics fuel elements with dispersed in space micro-fuel improves system safety. In routine operating reliable containment of radioactive fission products due to micro-fuel with multi-layer cladding allows to decrease specific releases of radio-nuclides into atmosphere by 1 — 2 orders as compared to the releases from LWR-based NPPs. Fuel particles could withstand a considerable temperature rise before they would start losing their integrity because of chemical interaction of fuel with the cladding material (see fig.).Even in case of such unlikely events as air or water vapors getting into the core which would make fuel elements vigorously interact with graphite their multilayer cover would be able to prevent dramatic release of fission products.
158
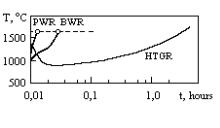
For HTGR in transient regimes accompanied with the core heating an accident would develop relatively slow due to lower power density. In order to illustrate it Fig. 2 compares two transient processes in case of LOCA, all safety systems being unavailable.
Fig. 2. Transient processes during LOCA without activating protecting systems
In the figure one can see that the time which is taken by the reactor to achieve 1600 °C is by two orders longer for HTGR than that by other reactor types.
Current State-of-Art
In current HTGR projects each fuel particle d = 500 mkm is covered with 3 layers shielding. The inner layer made of PyC has a relatively high porous structure and serves for collecting fission products released from fuel. The middle layer of SiC effectively contains rare earth fission products which otherwise would readily diffuse through PyC. The external layer is made of highly dense PyC which gaseous fission products cannot penetrate. A typical pebble fuel element d = 6 cm accommodates about 20 000 fuel particles dispersed within spherical matrix d = 5 cm.
It is known that the number of damaged fuel particles in a fuel element produced during fuel manufacturing and under irradiation during routine operation at temperature lower than 1100 °C is not more than 6 10–5 and 2 10– 4. Under normal operation the release of fission products from fuel is really insignificant. Fission products exiting the fuel elements are carried with the gaseous coolant and deposited onto cooler graphite and metallic surfaces of the reactor circuit. For instance for modular HTR designs in FRG the calculated integral yield of 137 Cs for the period of 32 years under normal operating conditions is 2.5 10 12Bq or about 70 Cu. According to the experimental data obtained at
159
AVR reactor 73 % of the released Cs is deposited onto metallic surfaces, 5 % is carried with graphite dust and the remainder is separated in the graphite reflector.
Some Conclusions on Coolant Technology
In analyzing high temperature reactors as a power generating technology one should pay special attention to pretty complicated technology of operating coolant. In order to assure quality of the coolant one has to incorporate into the reactor unit a system for cleaning the primary circuit which would be able to provide for cleaning helium from impurities when operating routinely, primarily from such impurities as H2O,
CO2, H2.
Generally speaking the coolant should posses the following features:
•High specific thermal capacity and good thermal conductivity;
•Taking minimal energy for circulating;
•Resistant to thermal and radiation exposure;
•Minimal ability to be activated;
•Minimal neutron cross section;
•Chemical inertness not to be able to react with reactor materials;
•Economic feasibility.
If one compares helium with carbon dioxide one will see that helium thermal capacity is lower than that of carbon dioxide. In order to be able to accumulate considerable quantity of heat in helium one should provide for significant drop between the core inlet and outlet temperatures. Helium thermal conductivity is 10 times as high as that of CO2, this feature making heat removal easier. Helium is known to be extremely volatile which entails the challenge of creating helium-tight systems. Nevertheless it is of great importance to realize that PBMR has to have several systems of this sort – the primary circuit, the decontaminating system, a storage for pure and a storage for dirty helium, means of transportation.
Some Aspects of Fuel Cycle Back End
At present the technology of manufacturing ball fuel elements is well developed. One has already mentioned above of the problems during manufacturing as well as of the defects induced under irradiation.
Getting down to reprocessing one should admit that there are a number of problems here brought about by the structure of the fuel elements.
The first phase of reprocessing is to separate graphite from nuclear fuel, breeding material and fission products. In principle there are sev-
160