
Детали машин / ДМ4
.pdf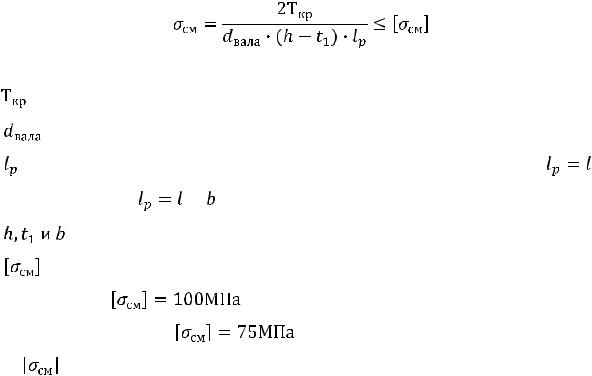
6 Проверка прочности шпоночных соединений
После завершения конструктивной компоновки редуктора, когда опреде-
лены и уточнены окончательные размеры всех его деталей, деталей открытой пе-
редачи и муфты, выбран режим смазки зацепления и подшипников, проводят ряд проверочных расчетов, которые должны подтвердить правильность принятых конструкторских решений. Главным из таких расчетов является расчет шпоноч-
ных соединений.
Для передачи вращающего момента в основном применяют призматиче-
ские шпонки, изготавливаемые из стали, имеющей (сталь 45, Ст6).
Для относительно тонких валов допускается применение и сегментных шпонок.
Призматические шпонки выполняют прямоугольного сечения со скругленными или плоскими концами. Стандарт предусматривает для каждого размера вала оп-
ределенные размеры поперечного сечения шпонки.
Призматические шпонки, применяемые в проектируемых редукторах, про-
веряют на смятие и на срез. Проверке подлежат шпонки в местах посадки эле-
ментов открытой гибкой связи и зубчатых колес.
Условие прочности на смятие имеет вид
где |
- крутящий момент на валу, Нмм; |
|
||
|
- диаметр вала в месте посадки шпонки, мм; |
|
||
|
- рабочая длина шпонки, мм; для шпонки с плоскими торцами |
, при |
||
скругленных торцах |
|
; |
|
|
|
|
|||
|
– стандартные размеры, определяемые по таблице 6.1, мм; |
|
||
|
- допускаемое напряжение смятия, МПа; при стальной ступице и спо- |
|||
койной нагрузке |
|
; при колебаниях нагрузки принимают значение |
||
на 20…25% меньше, т.е. |
|
; при чугунной ступице приведенные зна- |
||
чения |
следует снижать вдвое. |
|
||
|
|
~ 146 ~ |
|
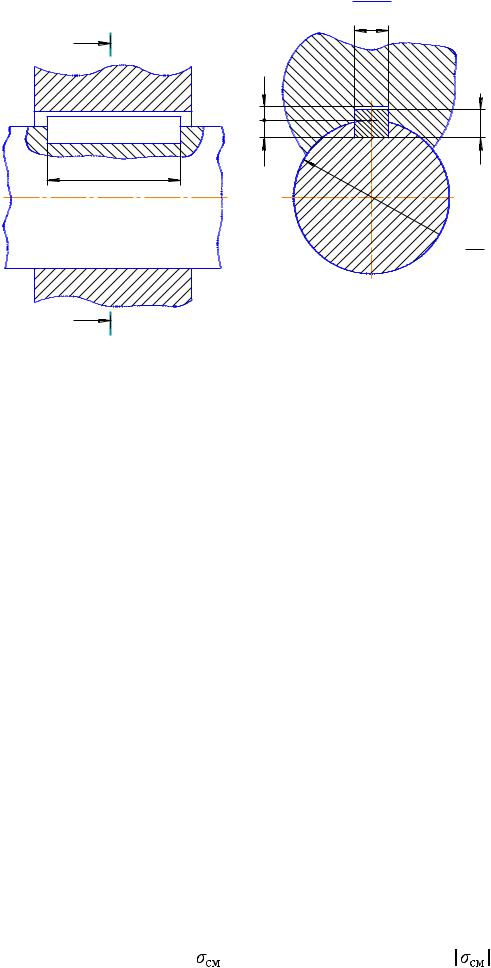
A
l |
|
А-А |
|
b |
2 |
|
t |
|
1 |
h |
t |
d
A
Рисунок 6.1 – Схема шпоночного соединения
Таблица 6.1 – Шпонки призматические
|
|
|
|
Сечение |
|
|
Глубина паза |
|
|
||
Диаметр вала d |
шпонки |
|
Фаска |
Длина l |
|
||||||
|
|
|
|
||||||||
|
|
|
|
b |
h |
|
|
вала t1 |
ступицы t2 |
|
|
Свыше 12 |
до |
17 |
5 |
5 |
|
0,25…0,4 |
3,0 |
2,3 |
10…56 |
|
|
>> |
17 |
>> |
22 |
6 |
6 |
|
3,5 |
2,8 |
14…70 |
|
|
|
|
|
|||||||||
>> |
22 |
>> |
30 |
8 |
7 |
|
|
4,0 |
|
18…90 |
|
>> |
30 |
>> |
38 |
10 |
8 |
|
|
5,0 |
3,3 |
22…110 |
|
>> |
38 |
>> |
44 |
12 |
|
0,4…0,6 |
|
28…140 |
|
||
|
|
|
|
|
|||||||
>> |
44 |
>> |
50 |
14 |
9 |
|
5,5 |
3,8 |
36…160 |
|
|
|
|
|
|||||||||
>> |
50 |
>> |
58 |
16 |
10 |
|
|
6,0 |
4,3 |
45…180 |
|
>> |
58 |
>> |
65 |
18 |
11 |
|
|
7,0 |
4,4 |
50…200 |
|
>> |
65 |
>> |
75 |
20 |
12 |
|
|
7,5 |
4,9 |
56…220 |
|
>> |
75 |
>> |
85 |
22 |
14 |
|
0,6…0,8 |
9,0 |
5,4 |
63…250 |
|
>> |
85 |
>> |
95 |
25 |
|
|
70…280 |
|
|||
|
|
|
|
|
|
||||||
Примечания. 1.Длины призматических шпонок l выбирают из следующего |
|
||||||||||
ряда: 16 – 18 – 20 – 22 – 25 – 28 – 32 – 36 – 40 – 45 – 50 – 56 – 63 – 70 – 80 – |
|
||||||||||
90 – 100 – 100 – 125 – 140 – 160 – 180 – 200 – 220 – 250. 2.Пример условного |
|
||||||||||
обозначения шпонки исполнения 1, размерами b = 16мм, h =10мм, l=50мм: |
|
||||||||||
Шпонка 16×10×50 ГОСТ 23360-78. |
|
|
|
|
|
||||||
|
Длину шпонки выбирают из стандартного ряда так, чтобы она была не- |
||||||||||
сколько меньше (на 5…10мм) длины ступицы насаживаемой детали. |
|||||||||||
|
Если при проверке шпонки |
окажется значительно ниже |
, то можно |
||||||||
|
|
|
|
|
|
|
~ 147 ~ |
|
|
|
|
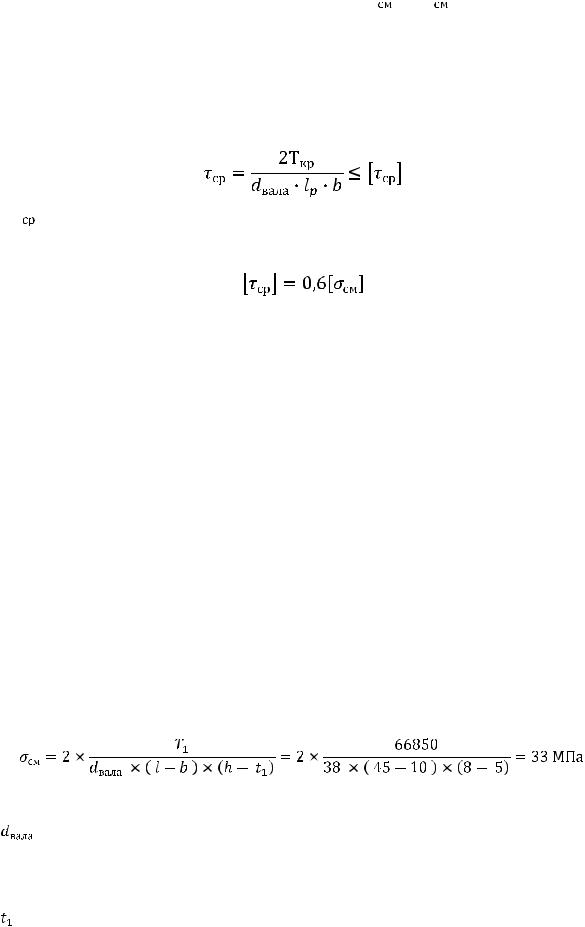
взять шпонку меньшего сечения – как для вала предыдущего диапазона, но обяза-
тельно проверить ее на смятие. Если получится , то рациональнее пе-
рейти на посадку с натягом или принять две шпонки данного сечения, располо-
женные под углом 1800, при проверке принимают, что каждая шпонка передает половину нагрузки.
Условие прочности на срез имеет вид
где – допускаемое напряжение при расчете на срез, МПа; рекомендуется принимать
Контрольные вопросы:
2.Какие виды шпонок существуют?
3.По каким критериям проводится расчѐт шпоночного соединения?
4.В каких случаях следует уменьшать допускаемое напряжение
смятия?
5.Как выбирается длина шпонки?
6.Условие прочности на срез шпоночного соединения.
ПРИМЕР 6.1 ПРОВЕРКА ПРОЧНОСТИ ШПОНОЧНЫХ СОЕДЕНЕНИЙ
ЦИЛИНДРИЧЕСКАЯ ШЕСТЕРНЯ Для данного элемента подбираем шпонку призматическую со скругленными торцами
108. Размеры сечений шпонки и пазов и длины шпонок по ГОСТ 23360-78. Материал – шпонки сталь 45 нормализованная.
Напряжение смятия и условия прочности проверяем по формуле
где = 66850 Нмм – момент на валу;
= 38 мм – диаметр вала;
= 8 мм – высота шпонки;
= 10 мм – ширина шпонки;
= 45 мм – длина шпонки;
= 5 мм – глубина паза вала.
~ 148 ~
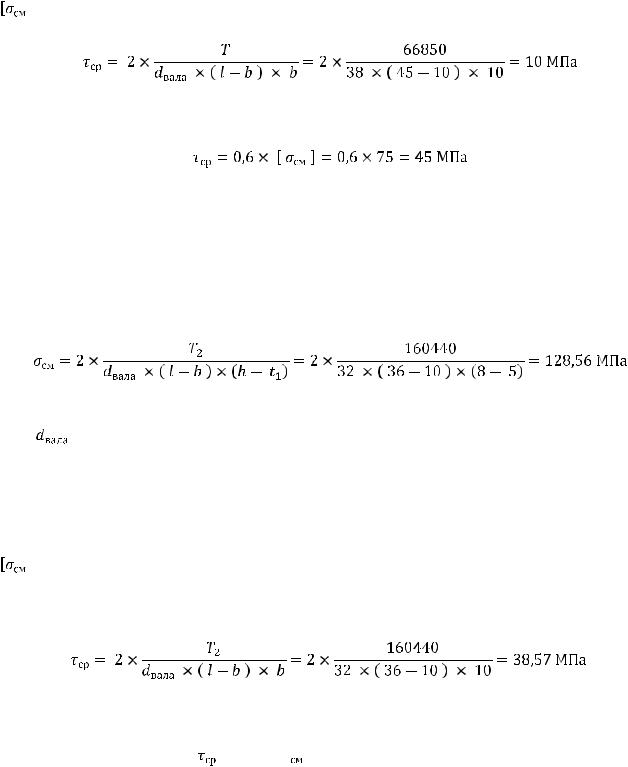
Допускаемые напряжения смятия при переменной нагрузке и при стальной ступице . Проверим шпонку на срез
Допускаемые напряжения среза при стальной ступице:
Все условия прочности выполнены.
ЦИЛИНДРИЧЕСКОЕ КОЛЕСО Для данного элемента подбираем шпонку призматическую со скругленными торцами
108. Размеры сечений шпонки и пазов и длины шпонок по ГОСТ 23360-78. Материал – шпонки сталь 45 нормализованная.
Напряжение смятия и условия прочности проверяем по формуле
где = 160440 Нмм – момент на валу;
= 32 мм – диаметр вала;
= 8 мм – высота шпонки;
= 10 мм – ширина шпонки;
= 36 мм – длина шпонки;
= 5 мм – глубина паза вала.
Допускаемые напряжения смятия при переменной нагрузке и при стальной ступице
.
Поскольку условие прочности на смятие не выполняется, то принимаем 2 шпонки данного сечения, расположенные на валу под углом 1800 друг к другу. Проверим шпонку на срез
Допускаемые напряжения среза при стальной ступице:
0,6
= 0,6
Все условия прочности выполнены.
ВЕДУШИЙ ШКИВ РЕМЕННОЙ ПЕРЕДАЧИ Для данного элемента подбираем шпонку призматическую со скругленными торцами
128. Размеры сечений шпонки и пазов и длины шпонок по ГОСТ 23360-78. Материал – шпонки сталь 45 нормализованная.
Напряжение смятия и условия прочности проверяем по формуле
~ 149 ~
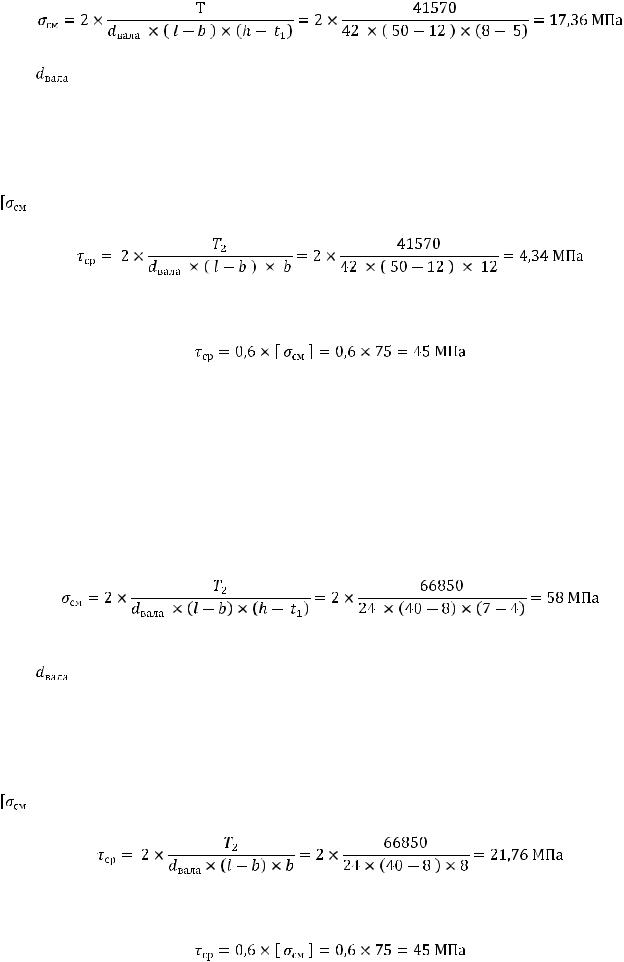
где = 41570 Нмм – момент на валу;
= 42 мм – диаметр вала электродвигателя;
= 8 мм – высота шпонки;
= 12 мм – ширина шпонки;
= 50 мм – длина шпонки;
= 5 мм – глубина паза вала.
Допускаемые напряжения смятия при переменной нагрузке и при стальной ступице
. Проверим шпонку на срез
Допускаемые напряжения среза при стальной ступице:
Все условия прочности выполнены.
ВЕДОМЫЙ ШКИВ РЕМЕННОЙ ПЕРЕДАЧИ Для данного элемента подбираем шпонку призматическую со скругленными торцами
87. Размеры сечений шпонки и пазов и длины шпонок по ГОСТ 23360-78. Материал – шпонки сталь 45 нормализованная.
Напряжение смятия и условия прочности проверяем по формуле
где = 66850 Нмм – момент на валу;
= 24 мм – диаметр вала;
= 7 мм – высота шпонки;
= 8 мм – ширина шпонки;
= 80 мм – длина шпонки;
= 4 мм – глубина паза вала.
Допускаемые напряжения смятия при переменной нагрузке и при стальной ступице
. Проверим шпонку на срез
Допускаемые напряжения среза при стальной ступице:
Все условия прочности выполнены.
~ 150 ~
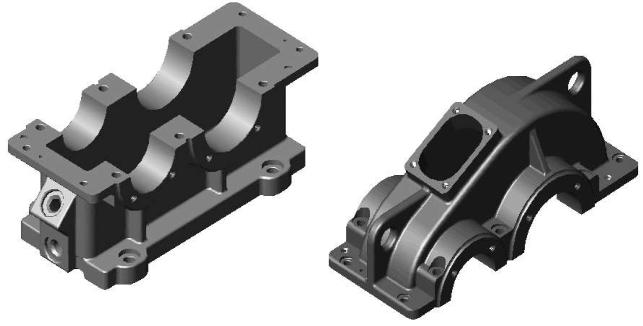
7 Конструктивные размеры корпусных деталей редуктора
Корпус редуктора служит для размещения и координации деталей пере-
дачи, защиты их от загрязнения, организации системы смазки, а также воспри-
ятия сил, возникающих в зацеплении редукторной пары, подшипниках, открытой передачи. При его конструировании должны быть обеспечены прочность и жест-
кость, исключающие перекосы валов.
Рисунок 7.1 – Картер и крышка цилиндрического редуктора
сразъемом по осям валов
Впроектируемых одноступенчатых редукторах принята в основном конст-
рукция разъемного корпуса, состоящего из крышки и основания (его еще иногда называют картер). Плоскость разъема проходит через оси валов. Корпуса верти-
кальных цилиндрических редукторов имеют в отдельных случаях два разъема,
что определяет еще одну часть корпуса - среднюю.
При конструировании червячных и легких зубчатых редукторов иногда применяют неразъемные корпуса со съемными крышками.
Несмотря на разнообразие форм корпусов, они имеют одинаковые конст-
руктивные элементы – подшипниковые бобышки, фланцы, ребра, соединенные стенками в единое целое, - и их конструирование подчиняется некоторым общим
~ 151 ~
правилам.
Формы корпуса определяется в основном технологическими, эксплуатаци-
онными и эстетическими условиями с учетом его прочности и жесткости. Этим требованиям удовлетворяют корпуса прямоугольной формы, с гладкими наруж-
ными стенками без выступающих конструктивных элементов; подшипниковые бобышки и ребра внутри; стяжные болты только по продольной стороне корпуса в нишах; крышки подшипниковых узлов преимущественно врезные; фундамент-
ные лапы не выступают за габариты корпуса.
Материал корпуса обычно чугун СЧ 12-28 или СЧ 15-32. Сварные конст-
рукции из листовой стали Ст 2 и Ст 3 применяют редко, главным образом для крупногабаритных редукторов индивидуального изготовления. Толщина стенок сварных корпусов на 20 - 30% меньше, чем чугунных.
При конструировании таких корпусов следует придерживаться установ-
ленных литейных уклонов, радиусов галтелей и переходов. Радиусы галтелей R
выбирают из ряда: 1, 2, 3, 5, 8, 10, 15, 20, 25, 30, 40 мм.
Основание корпуса и крышку фиксируют относительно друг друга двумя коническими штифтами, устанавливаемыми без зазора до расточки гнезд под подшипники. Основание и крышку корпуса соединяют болтами для обеспечения герметичности.
Для предотвращения протекания масла плоскости разъема смазывают спиртовым лаком или жидким стеклом. Ставить прокладку между основанием и крышкой нельзя, так как при затяжке болтов она деформируется и посадка под-
шипников нарушается.
Для захватывания редуктора при подъеме делают под фланцем основания приливы в виде крюков. Для снятия крышки делают крюки или петли на ней.
Для заливки масла и осмотра в крышке корпуса имеется окно, закрываемое крышкой. В редукторах с большим выделением тепла (червячных) предусматри-
вают отдушину, соединяющую внутреннюю полость редуктора с атмосферой. Ус-
тановка отдушины повышает надежность уплотнений. Простой отдушиной может быть ручка крышки смотрового отверстия или пробка с отверстиями.
~ 152 ~
Для удаления загрязненного масла и для промывки редуктора в нижней части корпуса делают отверстие под пробку с цилиндрической или конической резьбой. Под цилиндрическую пробку ставят уплотняющую прокладку из кожи,
маслостойкой резины, алюминия или меди. Надежнее уплотняет коническая резь-
ба.
Маслоспускное отверстие выполняют на уровне днища или несколько ни-
же его. Желательно, чтобы днище имело наклон 1 - 20 в сторону маслоспускного отверстия.
Для облегчения отделения крышки от основания корпуса при разборке на поясе крышки устанавливают два отжимных болта. Подшипники закрывают чу-
гунными крышками (литье СЧ 12-28 и СЧ 15-32).
Редуктор и электродвигатель обычно устанавливают на сварной раме.
При конструировании корпусов редукторов стремятся к устранению вы-
ступающих элементов с наружных поверхностей. Бобышки подшипниковых гнезд убирают внутрь корпуса; крепежные болты размещают в нишах, располагая их вдоль длинных сторон (там, где есть бобышки). Крышки подшипниковых гнезд врезные.
Контрольные вопросы:
1.Из каких частей состоит корпус редуктора?
2.Для чего служит корпус редуктора?
3.Сколько плоскостей разъема может быть в корпусе редуктора?
4.Какие конструктивные элементы характерны для всех видов
корпусов?
5.Из какого материала изготавливают редукторные корпуса?
6.Как соединяются между собой основание и крышка корпуса?
7.Как контролируется уровень масла в редукторе?
8.К чему крепится основание корпуса редуктора?
~153 ~
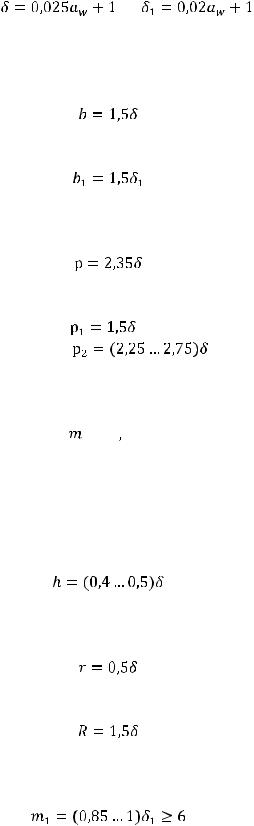
КОНСТРУКТИВНЫЕ РАЗМЕРЫ КОРПУСА РЕДУКТОРА
ЦИЛИНДРИЧЕСКИЙ РЕДУКТОР
1.Для одноступенчатого цилиндрического редуктора толщину стенки корпуса и крышки, отвечающую требованиям технологии литья, необходимой прочности и жѐсткости вычисляют по формулам:
и
2.Если после проведения расчѐтов получили , то принимаем 8мм. 3.Толщина верхнего пояса (фланца) корпуса:
4.Толщина нижнего пояса (фланца) крышки корпуса:
5.Толщина нижнего пояса корпуса без бобышки
при наличии бобышки
6.Толщина рѐбер основания корпуса:
.
Округляем в большую сторону.
7.Учитывая неточности литья, размеры сторон опорных платиков для литых корпусов должны быть на 2…4мм больше размеров опорных поверхностей прикрепляемых деталей. Обрабатываемые поверхности выполняются в виде платиков, высота h которых принимается
8.Плоскости стенок, встречающихся под прямым углом, сопрягают радиусом
9.Плоскости стенок, встречающихся под тупым углом, сопрягают радиусом
10.Толщина внутренних рѐбер из-за более медленного охлаждения металла корпуса и крышки:
~ 154 ~
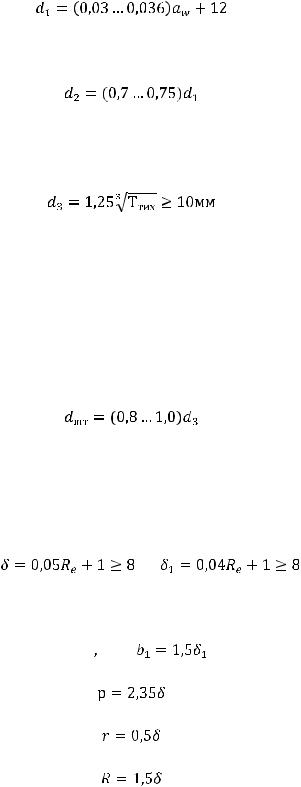
Округляем в большую сторону.
11.Диаметр фундаментных болтов (их число ≥ 4):
12.Диаметр болтов у подшипников
13.Диаметр винтов крепления крышки корпуса вычисляем в зависимости от вращающего момента на выходном валу редуктора:
14.Размер q, определяющий положение болтов d2:
, где
- диаметр винтов крепления крышки подшипника (М8 - М12).
15.Высота бобышки под болт
выбирают конструктивно так, чтобы образовалась опорная поверхность под головку болта и гайку. Желательно, чтобы у всех бобышек иметь одинаковую высоту
.
16.Диаметр штифтов:
КОНИЧЕСКИЙ РЕДУКТОР
1.Для одноступенчатого конического прямозубого редуктора толщину стенки корпуса и крышки, отвечающую требованиям технологии литья, необходимой прочности и жѐсткости вычисляют по формулам:
и
2.Толщина фланцев (поясов) корпуса и крышки: верхний пояс корпуса и пояс крышки:
и
нижний пояс корпуса:
3.Плоскости стенок, встречающихся под прямым углом, сопрягают радиусом
4.Плоскости стенок, встречающихся под тупым углом, сопрягают радиусом
5.Толщина внутренних рѐбер корпуса и крышки из-за более медленного охлаждения металла:
и
6.Учитывая неточности литья, размеры сторон опорных платиков для литых корпусов
должны быть на 2…4мм больше размеров опорных поверхностей прикрепляемых деталей. Обрабатываемые поверхности выполняются в виде платиков, высота h которых принимается
~ 155 ~