
u_lectures
.pdf
Рис.11.2. Схемы компоновки сборочной единицы
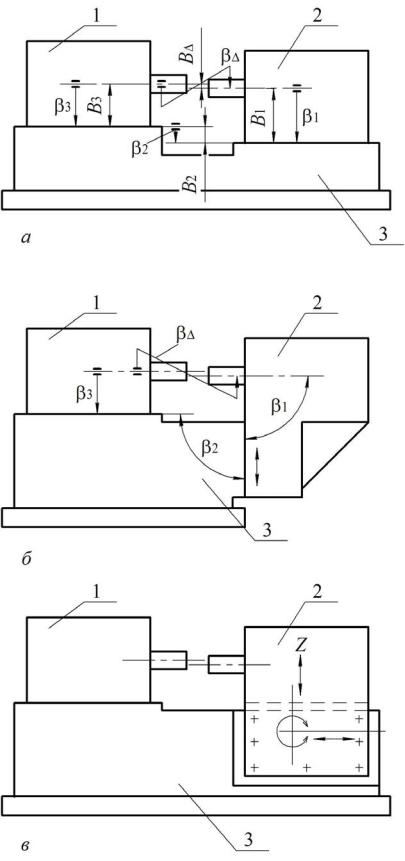
Рис.11.3. Схемы компоновки сборочной единицы
2.Пригонкой плиты станины 3 или основных баз головок 1 и 2.
3.Методом регулирования – путем применения компенсаторовпрокладок, клиньев.
При компоновке по схеме, приведенной на рис. 11.3.а, направляющие буртики отсутствуют. Благодаря этому сборочные единицы имеют степени свободы перемещения по осям X и Y и поворота вокруг вертикальной оси, что позволяет обеспечить требуемую точность совпадения и параллельность осей в горизонтальной плоскости методом регулирования. Для этого перемещают и поворачивают узлы в этой плоскости до тех пор, пока оси валов не совпадут и не будут параллельными. Точность совпадения осей будет зависеть от применяемых сборочных приспособлений, точности контрольных средств и квалификации сборщиков.
Совпадение и параллельность осей шпинделей в вертикальной плоскости, как в предыдущей схеме, можно обеспечить методами взаимозаменяемости, т.е. точным изготовлением деталей по размерам В1 - В3, β1 - β3, пригонкой или применением компенсаторов.
В схеме компоновки, приведенной на рис. 11.3.б, головку 2 крепят к вертикальной торцевой плоскости плиты. Базовые плоскости станины для головок 1 и 2 расположены взаимно перпендикулярно. Каждая головка имеет при установке по три степени свободы. Это дает возможность обеспечить совпадение осей шпинделей в вертикальной и горизонтальной плоскостях и их параллельность в горизонтальной плоскости выверкой положения расточных головок. И лишь параллельность осей шпинделей в вертикальной плоскости обеспечивается точным изготовлением деталей по угловым размерам β1 –β3.
В схеме компоновки, показанной на рис. 2.в, головка 2 установлена на боковой вертикальной плоскости плиты. Каждая из головок имеет три степени свободы во взаимно перпендикулярных плоскостях, что дает возможность обеспечить все требования точности к относительному положению сборочных единиц выверкой их положения.
Если компоновочные схемы равноценны с точки зрения удобства эксплуатации и габаритных размеров, тогда выбор наилучшей схемы компоновки будет зависеть от результатов экономических расчетов: принимается вариант схемы, обеспечивающей минимальную стоимость изготовления машины.
Наиболее простую и дешевую сборку обеспечивает схема, приведенная на рис. 1, т.к. она требует выверки, пригонки или регулирования. Наиболее трудоемкой будет сборка по схеме, приведенной на рис. 2.в. Зато схема, приведенная на рис. 1, потребует больших затрат на механическую
обработку деталей для обеспечения необходимой точности размеров В1 - В3,
В′1 - В′3 и β1 - β3, β′1 - β′3.

Размерный анализ сборочной единицы
Проведем размерный анализ шестеренного масляного насоса трактора
(рис. 11.4), [13].
Рис.11.4.Схемы размерных цепей шестеренного насоса
Насос предназначен для подачи смазки к трущимся поверхностям деталей трактора под давлением 0,6 МПа, в объеме не менее 30 л/мин при частоте вращения зубчатых колес 2350 об/мин.
При изготовлении насоса необходимо обеспечить с требуемой точностью:
-радиальный зазор между зубчатыми колесами и корпусом насоса;
-зазор между корпусом и торцами зубчатых колес (торцовый зазор);
-боковой зазор между зубьями зубчатых колес;
-зазор между торцом оси ведомого зубчатого колеса и крышкой корпуса;
-зазор между корпусом и торцом ведомого зубчатого колеса; плотность контакта зубьев; легкость вращения зубчатых колес.
Первые пять задач могут быть решены при помощи размерных цепей А, Б, В, Г и Д (рис. 11.4). Плотность контакта зубьев зубчатых колес зависит от относительного поворота образующих эвольвентных поверхностей зубьев
вдвух координатных плоскостях.
Для легкого вращения зубчатых колес необходимо, чтобы между торцами колес, корпусом и крышкой был выверен зазор не меньше толщины масляной пленки. Для этого должны быть обеспечены с соответствующей точностью расстояния между дном корпуса и торцами колес и поворот их относительно дна корпуса. Эти задачи позволяют решить в одной из координатных плоскостей размерные цепи Б и γ (рис. 11.5,а).
Необходимо также, чтобы были соблюдены требуемые зазоры в подшипниках, зависящие от диаметральных размеров отверстий втулок и валика (рис. 11.5,а, размерная цепь Е) и от точности относительного смещения и поворота осей отверстий в двух координатных плоскостях. Эти задачи могут быть решены в одной из координатных плоскостей при помощи размерных цепей К и µ (рис. 11.5,б).
Выявленные размерные цепи дают возможность выбрать методы достижения точности каждого из перечисленных параметров и оценить правильность простановки размеров и допусков на чертежах деталей насоса.
Например, радиальный зазор А∆ (рис. 11.5) описывается следующим уравнением размерной цепи А:
А = -А1+А2+А3+А4+А5. |
(11.1) |
Подставив номинальные значения составляющих звеньев из чертежей деталей, получим
А = -48,75+0+0+0+4,75=0. |
(11.2) |

Рис.11.5.Схемы размерных цепей шестеренчатого насоса
После допуска замыкающего звена при расчете по методу полной взаимозаменяемости

TA p = m∑−1TAi =17 +30 + 72 +50 +50 = 219мкм. |
(11.3) |
i=1 |
|
Координаты середины поля допуска этого звена
0А = 0А1 + 0А2 + 0А3 + 0А4 + 0А5 =8 + 0 + 0 + 0 +100 =108мкм. (11.4)
Верхнее и нижнее предельные отклонения
ВА р = |
0А Р + 0,5ТА р =108 + 0,5 219 = 218мкм. |
(11.5) |
НА р = |
0А Р −0,5ТА р =108 −0,5 219 = 2мкм. |
(11.6) |
Техническими условиями на насос зазор задается в |
пределах |
70-150 мм. Таким образом, при значениях допусков на размеры деталей, заданных чертежами, невозможно получить требуемый радиальный зазор методом полной взаимозаменяемости.
Проверим возможность достижения радиального зазора в требуемых пределах по методу неполной взаимозаменяемости при риске 0,25% ( t=3) и при условии, что рассеяние погрешностей составляющих звеньев подчинено закону Гаусса ( λAi=1/9). При этом целесообразно несколько уменьшить зазор
вподшипниках, который обычно назначается для насосов среднего давления
впределах 0,002-0,003 от диаметра вала. Для вала диаметром 15 мм можно считать допустимым зазор в подшипниках от 30 до 45 мкм. Изменив в соответствии с этим значение допуска ТА3, при расчете точности радиального зазора по методу неполной взаимозаменяемости можно получить погрешность
ТА = t |
m∑−1λAi TAi |
2 = 3 (172 +302 + 452 +502 )/ 9 = 90мкм. |
(11.7) |
|
i=1 |
|
|
причем ВА
НА
=108 + 0,5 90 =153мкм
=108 −0,5 90 = 63мкм
Таким образом, при условии, что допуск на зазор в подшипниках изменен, радиальный зазор в насосе можно обеспечить методом неполной взаимозаменяемости при риске 0,27%, если при заданном объеме выпуска такой риск приемлем.
Аналогично можно найти метод решения каждой из сформулированных выше задач и, если нужно, внести необходимые коррективы в чертежи деталей.
Кроме нахождения метода достижения точности замыкающего звена, размерный анализ позволяет определить последовательность сборки узла. Например, последовательность сборки насоса рассматриваемой конструкции существенно зависит от того, каким методом обеспечивается соосность отверстий подшипников скольжения вала.
Минимальный зазор в подшипниках, как было установлено выше, должен составлять 30 мкм, наименьшая толщина масляного слоя в любой точке касания вала не должна быть меньше 10мкм. Следовательно, для
компенсации |
отклонения |
от |
соосности |
отверстий |
втулок |
остается |
30-10=20 мкм. Отклонение от соосности отверстий |
втулок состоит из |
|||||
относительного смещения К и поворота µ |
их осей в двух координатных |
|||||
плоскостях (см. рис. 11.5,б) |
|
|
|
|
|
|
Допуски на размеры деталей, заданные на чертежах, составляют: |
||||||
звено |
К1К4 |
К2 |
К3 |
µ1µ4 |
µ2 |
µ3 |
допуск, мкм |
50 |
70 |
150 |
20/45 |
100/45 |
70/45 |
Если зазор в подшипниках полностью использовать для компенсации погрешностей только в одной из координатных плоскостей, то допуски замыкающих звеньев размерных цепей К и µ составляют
ТХ = 10 мкм и Тµ = 100/45 мкм/мм.
Согласно допускам на размеры деталей, указанным на чертежах, образуются следующие значения погрешностей К и µ :
ТК Р = 50+70+150+50 = 320 мкм; |
|
Тµ Р = (20+10+70+20)/45 = 210/45 мкм/мм. |
(11.8) |
Очевидно, что в этом случае для обеспечения требуемого зазора в подшипниках нельзя использовать ни один из методов взаимозаменяемости. Нельзя достичь этого и уменьшением допусков, поскольку это уменьшение должно быть очень значительным и сильно усложнит изготовление деталей.
Метод регулирования в данном случае также неприемлем.
ЛЕКЦИЯ 20
11.2.5. Анализ технологичности конструкции изделия
Целью анализа технологичности конструкций и вносимых на его основе изменений является обеспечение возможности оптимальных затрат труда, средств, материалов и времени при технологической подготовке производства, изготовлении, эксплуатации и ремонте.
Основное внимание в проекте необходимо обратить на производственную технологичность, т.е. технологичность конструкции изделия с точки зрения его изготовления.
Анализ производится на основе ГОСТ 14.201-83 «Технологичность конструкции. Термины и определения», ГОСТ 2.116-84*, ГОСТ 14.205-83, «Правила обеспечения технологичности конструкции изделия», а также рекомендаций [2,4,5].
Впервую очередь оцениваются качественные характеристик технологичности конструкции (ГОСТ 14.004-83):
-взаимозаменяемость;
-регулируемость конструкции;
-контролепригодность конструкции;
-инструментальная доступность конструкции.
Впроекте необходимо дать качественную оценку соответствия конструкции следующим требованиям:
– Требования к составу:
1. Сборочная единица расчленяется на рациональное число составных частей на основе принципа агрегатирования.
2.Конструкция сборочной единицы обеспечивает возможность ее компоновки из стандартных и унифицированных частей без применения сложной технологической оснастки.
3.Виды используемых соединений, их конструкции и месторасположение отвечают требованиям механизации и автоматизации сборочных работ.
4.В конструкции сборочной единицы и ее составных частей, имеющих массу более 20 кг, предусматриваются конструктивные элементы для удобного захвата грузоподъемными средствами, используемыми в процессе сборки, разборки и транспортирования.
5.Конструкция сборочной единицы предусматривает базовую составную часть, которая является основной для размещения остальных составных частей.
6.Базовую составную часть выбирают удобной для правильной установки на рабочем месте сборки (в приспособлении, на рабочем столе, сборочной площадке и пр.). Компоновка конструкции сборочной единицы должна позволять производить сборку при неизменном базировании составных частей.
Вконструкции базовой составной части предусматривают возможность использования конструктивных сборочных баз в качестве технологических и измерительных.
Компоновка сборочной единицы обеспечивается:
1) общей сборкой без промежуточной разборки и повторных сборок
составных частей;
2)удобным доступом к местам, требующим контроля, регулировки и проведения других работ;
3)легкосъемностью составных частей с малым ресурсом;
4)рациональным расположением такелажных узлов, монтажных опор и других устройств для обеспечения транспортабельности изделия.
– Требования к конструкции соединений составных частей: Наименьшее количество поверхностей и мест соединений составных
частей в конструкции.
Доступность мест соединения составных частей при механизации сборочных работ и контроле качества соединения.
Отсутствие сложной и необоснованно точной обработки сопрягаемых поверхностей соединения составных частей.
Недопустимость дополнительной обработки составных соединений в процессе сборки конструкции.
Рациональность методов закрепления деталей (запрессовка, пластическая деформация, точечная сварка и др.).
Обоснованность посадок и ограничение их количества.
Наличие комплектов основных и вспомогательных конструкторских баз, обеспечивающих определенность базирования.
Наличие конструктивных элементов для ориентации деталей.
– Требования к точности и методу сборки:
Точность расположения составных частей обуславливается точностью изготовления составных частей. Выбирают метод сборки для данного объема выпуска и типа производства на основании расчета и анализа размерных цепей.
При выборе метода сборки следует учитывать трудоемкость сборочных работ и затраты на изготовление составных частей с точностью, необходимой для данного метода сборки.
Примечание. Методы сборки располагаются по убывающей производительности труда сборочных работ в следующем порядке:
-с полной взаимозаменяемостью;
-с неполной взаимозаменяемостью;
-с групповой взаимозаменяемостью;
-с регулировкой компенсаторами;
-с пригонкой.
Вконструкции предусматриваются устройства, обеспечивающие заданную точность относительного расположения составных частей (центрирующие, фиксирующие, компенсирующие).
Пределы регулирования и параметры компенсаторов рассчитываются на основе теории размерных цепей.
Компенсирующие, центрирующие и фиксирующие устройства имеют простую конструкцию, свободный доступ для рабочего и контрольного инструмента.
На основе выполненного анализа технологичности конструкции