
u_lectures
.pdf
длительного основного перехода: tм = toiнб , где toi – затраты времени на выполнение i-го основного перехода.
Рис. 9.6. Совмещение во времени основных переходов при многорезцовой обработке заготовки блока зубчатых колес
Сокращение основного технологического времени, если оно является ручным, может быть достигнуто механизацией ручного труда.
9.4.3. Вспомогательное время
Может быть сокращено двумя путями: непосредственным сокращением времени, затрачиваемого на выполнение вспомогательных переходов и совмещением выполнения вспомогательных переходов с основными переходами. Затраты времени на выполнение j-го вспомогательного перехода обозначим через tвj .
Непосредственное сокращение вспомогательного времени возможно за счет уменьшения затрат времени на замену обработанной заготовки следующей из партии; увеличения скорости холостых перемещений рабочих органов станка; уменьшения затрат времени на управление оборудованием и приспособлениями; уменьшения времени, затрачиваемого на контроль за ходом технологического процесса.
Установка с требуемой точностью заготовок на станке может отнимать много времени. Например, установка и закрепление заготовок крупногабаритных деталей иногда занимает 8–12 ч. Применение специальных, универсальных и других видов приспособлений или нормализованных средств в виде опор, планок, подкладок и т.п. обеспечивает базирование деталей по правилу шести точек с меньшими затратами времени. Этому же способствует использование быстродействующих пневматических, гидравлических и электромеханических зажимов, встраиваемых в приспособления.
Для уменьшения затрат времени на вспомогательные хода все современные станки оснащают механизмами ускоренных перемещений рабочих органов и автоматическими устройствами, обеспечивающими переход к рабочей подаче.
Время, затрачиваемое на управление станком и приспособлением, сокращают в результате концентрации управления в одном месте. На тяжелых станках пульты управления дублируют, что позволяет рабочему управлять станком с разных точек рабочего места. Введение механизмов ускоренных

перемещений инструментов (заготовок) в исходное рабочее положение, устройств для быстрой смены инструментов, автоматизация управления ходом операции являются основными мерами по непосредственному сокращению вспомогательного времени.
К уменьшению оперативного времени приводит полное или частичное совмещение вспомогательных переходов с выполнением основных переходов. Примером такого совмещения может служить установка очередной заготовки на одном конце поворотного стола фрезерного станка в то время, как на другом его конце идет обработка предшествующей заготовки. По окончании обработки стол поворачивается на 180°, начинается обработка очередной заготовки, а на свободном конце стола обработанная заготовка заменяется новой.
Совмещение времени установки заготовки с ее обработкой может быть получено при "маятниковой" обработке (рис. 9.7). Сущность ее заключается в том, что во время обработки одной заготовки, установленной на одном конце стола станка, осуществляется смена другой, установленной на другом конце стола и ранее обработанной.
Рис. 9.7. Схема "маятниковой" обработки
С основными переходами могут быть совмещены замена инструментов в инструментальных магазинах, измерения заготовок в ходе обработки, изменения режимов обработки и другие вспомогательные приемы. Полное совмещение вспомогательных приемов с основными приводит к тому, что оперативное время становится равным основному технологическому времени:
tоп = tо. т
9.5. Структуры временных связей в операциях технологического процесса
Структуры оперативного времени в операциях могут отличаться в зависимости от способов выполнения основных переходов; степени совмещения с основными переходами выполнения вспомогательных переходов; числа потоков, дублирующих выполнение одинаковых переходов при изготовлении одноименных изделий.
Параллельный способ обработки характеризуется одновременностью обработки поверхностей заготовки многими инструментами, поэтому основное технологическое время равно наибольшему
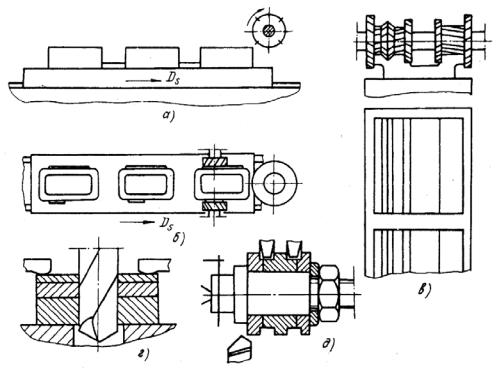
времени обработки одной или нескольких поверхностей, равноценных по затратам времени:
tо.т = toiнб
На рис. 9.8 приведены примеры использования трех способов осуществления основных переходов при многоместной обработке заготовок одинаковых (рис. 9.8, а, б, в) и разных деталей (рис. 9.8, г, д). Оперативное время tоп, приходящееся при многоместной обработке на одну заготовку, будет
равно оперативному времени tопn обработки п заготовок, отнесенному к числу
п:
tоп = tопn / n
Рис. 9.8. Три способа осуществления основных переходов при многоместной обработке
Затраты времени tв на выполнение вспомогательных переходов могут быть разложены на составляющие их элементы:
tв = tс. у + tупр + tх + tк
где tс. у – время, затрачиваемое на установку и съем заготовки; tупр – время, затрачиваемое на управление станком и приспособлением; tх – время вспомогательных ходов (подводов заготовки к инструментам или наоборот, поворотов и фиксации положения столов, револьверных головок, смены инструментов и т.п.); tк – время, затрачиваемое на контроль за ходом технологического процесса.
Для упрощения структуры вспомогательного времени представим его в виде двух слагаемых: tс. у и tх , включив в состав последнего все остальные виды вспомогательных переходов. Будем считать, что
tв = tс. у + tх
Вспомогательные переходы могут сочетаться с основными переходами при всех способах выполнения основных переходов и быть

А – несовмещенными, Б – частично совмещенными, В – полностью совмещенными.
Когда ни основные, ни вспомогательные переходы не совмещены, оперативное время
p |
s |
tоп = ∑toi +tс.у + ∑txj |
|
i =1 |
j =1 |
где s – число вспомогательных ходов.
Совмещение затрат времени tc . y на установку заготовки и съем детали с основными переходами возможно при наличии на станке отдельной установочной позиции. Такие позиции обычно предусмотрены на многопозиционных станках, примером которых может быть четырехпозиционвый агрегатный станок с поворотным столом (рис. 9.9).
Рис. 9.9. Совмещение с основными переходами установки (съема) заготовки на четырехпозиционном агрегатном станке
Рис. 9.10. Полное совмещение установки (съема) заготовки и вспомогательных переходов с основными
Полное совмещение t c . y и t x со временем выполнения основных переходов достигается в непрерывных процессах, характеризуемых непрерывностью перемещения заготовок с рабочей подачей. Примерами непрерывных процессов могут быть бесцентровое шлифование поршневых пальцев (рис. 9.10, а) и непрерывное фрезерование плиток на карусельнофрезерном станке (рис. 9.10, б).
ЛЕКЦИЯ 18
10.ЭКОНОМИЧЕСКИЕ СВЯЗИ
ВПРОИЗВОДСТВЕННОМ ПРОЦЕССЕ
Производственный процесс изготовления машины не может быть осуществлен без затрат живого и овеществленного труда. Поскольку ресурсы человеческого труда представляют собой наивысшую ценность для человеческого общества, то их рациональное расходование предопределяет уровень благосостояния всех членов общества. В процессе производства продукции экономию затрат труда дает ресурсосберегающая технология.
Связь между затратами обоих видов труда и их сумму отражает формула себестоимости единицы продукции
p |
m |
|
|
|
α +α |
|
|
С = ∑M + ∑ |
О+ П + И + 1 |
+ |
1 |
2 З |
|
||
= |
= |
|
|
|
100 |
|
|
i 1 |
i 1 |
|
|
|
|
|
|
Снижение себестоимости машины, также как и ее отдельных сборочных единиц и деталей, может быть достигнуто путем уменьшения значений всех ее слагаемых.
10.1. Сокращение расходов на материалы
Расходы на материалы
p |
p |
M = ∑G1q1 − ∑G2q2 |
|
i =1 |
i =1 |
где G1 – масса материала каждой марки, расходуемого на изготовление машины, кг; q1 – стоимость 1 кг материала надлежащей марки, руб.;
G2 – масса отходов материалов, кг; q2 – стоимость 1 кг отходов, руб.; р – число марок материалов, расходуемых на изготовление машины.
Следовательно, существуют следующие основные сокращения расходов на материалы:
сокращение массы материалов, расходуемых на изготовление машины; использование, по-возможности, более дешевых материалов; получение отходов материалов в виде, пригодном для последующего
использования.
Расход материала при изготовлении машины определяется материалоемкостью ее конструкции и массой отходов, образующихся в процессе изготовления. Так как основными материалами, из которых изготовляют машины, являются металлы, то именно их экономии и следует уделить большее внимание.
Металлоемкость конструкции машины полностью зависит от конструктора. Недостаточное знание свойств материалов, приближенные методы расчета, преднамеренное завышение запасов прочности приводят к излишнему расходу материалов. К тому же результату может привести непродуманное конструктивное оформление деталей. В качестве примера на рис. 10.1 показаны две конструкции корпуса редуктора; вторая из них (рис. 10.1, б) менее металлоемка.

Рис. 10.1. Два варианта конструкции корпусной детали с точки зрения металлоемкости
Для суждения о рациональности использования материалов служит коэффициент ηм использования материала, представляющий собой отношение массы Gизд готового изделия к массе Gмат материала, затраченного на его изготовление:
ηм = Gизд /Gмат
Значительное количество отходов и потерь металла возникает на машиностроительных заводах при получении заготовок деталей. К такого рода потерям относится угар металлов при плавке, сплески, остатки в плавильных агрегатах, окалина, отходы в виде заусенцев, облоя, обрезков, брака заготовок.
При механической обработке большую долю отходов составляет стружка. Но помимо нее в отходы идут обрезки проката, из которого получают заготовки, обрезки при раскрое листового материала и забракованные детали.
Сокращение потерь и отходов не только экономит материалы, позволяя увеличить выпуск изделий, но и экономит затраты обоих видов труда как на данной, так и на всех предшествующих стадиях производства.
Потери материала сокращаются с уменьшением числа стадий, которые проходит предмет природы до его превращения в изделие.
Например, непосредственное получение болтов из круглого прутка на холодновысадочных автоматах с накаткой резьбы снизило отход металла при изготовлении болтов М10 в 2,4 раза по сравнению с изготовлением тех же болтов из шестигранного прутка на токарном автомате.
Если получить готовую деталь непосредственно из полуфабрикатов не удается, наибольший эффект дает максимальное приближение форм и размеров заготовки к готовой детали. Примером может служить сопоставление масс заготовок коленчатого вала, одна из которых, полученная свободной ковкой (рис. 10.2, а), имеет массу 163 кг, а другая, полученная штамповкой в закрытых штампах (рис. 10.2, б), имеет массу 87 кг. С переходом к штампованной заготовке расход материала сокращается почти в 2 раза. Трудоемкость механической обработки заготовки при одинаковом объеме выпуска и на том

же оборудовании в первом случае составляет 40,6, а во втором – 19 нормочасов, т.е. сокращается на 59 %.
Рис. 10.2. Заготовки коленчатого вала
Большую экономию материала и снижение трудоемкости механической обработки дают переход от литья в землю к литью в кокиль, оболочковые формы, центробежному литью и другим способам литья, а также использование сварных заготовок.
Уменьшение отходов листового материала дает рациональный раскрой листов.
Использование наиболее дешевых материалов. Выбору наиболее дешевых материалов при конструировании деталей способствует точность формулировки их служебного назначения и условий, в которых им предстоит работать.
Экономию дорогих металлов дает конструкция детали, отдельные части которой сделаны из разных материалов. Например, головка выхлопного клапана двигателей внутреннего сгорания работает в потоке горящих газов с высокой температурой, в то время как стержень клапана работает в нормальных условиях. Стыковая сварка позволяет сделать стержень клапана из хромистой стали 40Х, а головку клапана из мартенситной стали 40Х10С2М (рис. 10.3).
Те же результаты дает применение биметаллов – двухслойных материалов (сталь – бронза, сталь – алюминиевые сплавы и др.). Из биметаллических материалов изготовляют втулки, служащие опорами валов, вкладыши подшипников автомобильных и тракторных двигателей и другие детали.
Широкие возможности в экономии металлов создает появление новых неметаллических материалов с высокими механическими свойствами. Примером такого рода материалов может служить синтегран – материал,

получаемый из крошки гранита и связующей смеси. Обладая высокой прочностью, синтегран не дает усадки, хорошо гасит вибрации, легко схватывается с металлом. Синтегран можно использовать для изготовления корпусных деталей, валов, ступиц зубчатых колес, стержней инструментов и многих деталей других типов.
Рис. 10.3. Заготовка клапана (а) и готовая деталь (б) из двух различных материалов, соединенных стыковой сваркой
Получение отходов в наиболее ценном виде. Отходы металла, получаемые при изготовлении деталей, могут иметь различную стоимость в зависимости от возможностей их дальнейшего использования.
Отходы в виде стружки, обрезков, облоев, лома и пр., непригодные для машиностроительного предприятия, являются ценным сырьем для металлургических предприятий.
Если отходы могут быть использованы для получения полноценных заготовок других деталей, их стоимость или не отличается от первоначальной стоимости материала или близка к ней.
10.2. Сокращение расходов на заработную плату
Расходы на заработную плату основных производственных рабочих
m |
szt |
|
З = ∑ |
|
|
f 60 |
||
i =1 |
где s – часовая ставка рабочего первого разряда, устанавливаемая на определенный период времени коллективным договором, руб.; z – разрядный коэффициент работы, определяемый по квалификационному справочнику;
t – время, затрачиваемое на выполнение операции (штучно-калькуляционное время), мин.; f – число станков, оборудования другого вида или рабочих мест, обслуживаемых одним рабочим; т – число операций, необходимых для изготовления единицы продукции.
Затраты на заработную плату наладчиков рассчитываются так же, как и расходы на заработную плату основных рабочих, но при своих значениях s , z , f и t .

Сокращение расходов на заработную плату производственных рабочих и наладчиков может быть осуществлено путем уменьшения числа операций, необходимых для изготовления изделия, снижения квалификации работы за счет ее упрощения, сокращения времени, затрачиваемого на выполнение операции, увеличения числа единиц оборудования, обслуживаемых рабочим и наладчиком.
За время работы станка или оборудования другого вида у рабочего может быть свободное время, в течение которого он может осблужить дополнительно несколько единиц другого оборудования. Так, число станков, которое может обслужить один рабочий при полном использовании его времени и при условии выполнения на каждом станке одинаковых операций,
f ≥ tо /(tр +tп ) .т
где t о. т – основное технологическое время на операции; t p – время обслуживания станка; t п – среднее время перехода рабочего от одного станка к другому.
Например, при t о. т =11,2 мин, t p = 3,7 мин и t п = 1,0 мин рабочий может обслужить fр ≥ 11,2/(3,7 + 1,0) = 2,38, т.е. 3 станка.
При этом он будет полностью загружен, в то время как станки какое-то время будут простаивать. Это видно из циклограммы работы станков и рабочего (рис. 10.4, а) .
Рис. 10.4. Циклограммы многостаночного обслуживания
Число станков при полном их использовании можно определить из предыдущего соотношения, изменив знак неравенства на противоположный:
fс ≤ tо.т/(tр + tп)