
u_lectures
.pdf
В данном примере fс = 2 станка. В этом случае (рис. 10.4, б) возникают значительные простои рабочего, что отражается на производительности его труда.
Введение многостаночного обслуживания требует такой расстановки оборудования и организации рабочего места, при которых рабочим затрачивается наименьшее время на переходы от одного станка к другому и их обслуживание. Например, при расстановке станков по схеме, показанной на рис. 10.5, а, путь рабочего больше, чем при расстановке станков по схеме, приведенной на рис. 10.5, б.
Рис. 10.5. Расстановка оборудования, сокращающая время переходов рабочего от одного стайка к другому
Таким образом, внедрение обслуживания одним рабочим нескольких единиц оборудования требует комплексного решения нескольких технологических и организационных вопросов.
10.3.Сокращение расходов на содержание, амортизацию
иэксплуатацию средств труда
Средства труда на предприятии должны находиться в таком состоянии, чтобы в любой момент времени их можно было применить в производственном процессе. Для этого средства труда нужно содержать в надлежащих условиях и своевременно ремонтировать.
Средства труда постепенно изнашиваются в физическом и моральном смысле, в результате чего их использование становится либо невозможным, либо экономически невыгодным. Средства, необходимые для замены износившихся или морально устаревших оборудования и приспособлений новыми, накапливают за определенный период в виде амортизационных отчислений, входящих в себестоимость единицы продукции.
Сумму амортизационных отчислений рассчитывают по-разному для универсальных и специальных средств труда.
Для универсальных средств труда подсчитывают сумму амортизационных отчислений, приходящихся на 1 мин работы оборудования, приспособления, инструмента, занятых при выполнении операции, множат их на длительность операции и, суммируя по операциям технологического процесса, определяют сумму амортизационных отчислений, приходящихся на единицу продукции.
Для специальных средств труда амортизационные отчисления определяют, относя первоначальные расходы на необходимое оборудование, приспособления и инструменты к общему числу изделий, подлежащих изготовлению по неизменяемому чертежу.
Для приведения средств труда в действие расходуются электроэнергия, сжатый воздух, топливо, охлаждение, смазочные материалы и пр. Затраты на эксплуатацию средств труда и расходы на амортизацию части здания, относящейся к ним, так же включаются в себестоимость единицы продукции.
Основными путями сокращения расходов на содержание, амортизацию
иэксплуатацию средств труда являются следующие.
1.Бережное отношение к средствам труда: соблюдение условий эксплуатации, предусмотренных техническими паспортами; защита от воздействия факторов (производственной пыли, влаги, химически активных веществ и др.), ускоряющих изнашивание оборудования и приспособлений; тщательный уход (чистка, смазывание, хранение и т.п.); систематический контроль состояния, своевременное техническое обслуживание и ремонт.
Приобретение оборудования, приспособлений и инструментов, стоимость которых находится в соответствии с видом, объемом и длительностью выпуска производимой продукции,
2.Повышение коэффициента использования оборудования, особенно дорогостоящего оборудования (уникального и специального). Например, эксплуатацию многооперационных станков, гибких производственных систем и т.п. нередко ведут в три смены и даже в праздничные дни при коэффициенте загрузки 0,9–0,95 с тем, чтобы получить наибольшую отдачу и снизить амортизационные расходы на единицу продукции.
3.Снижение затрат на силовую электроэнергию за счет применения оборудования, мощность электродвигателей которого не завышена и соответствует выполняемой работе. Экономия электроэнергии, расходуемой на нагрев, сварку, обработку заготовок, а также затрат на пар, газ, сжатый воздух и другие энергоносители.
Экономически целесообразное приобретение и использование инструментов.
4.Эксплуатация режущих инструментов с режимами, соответствующими их экономичной стойкости, своевременный вывод из работы затупившегося инструмента, снижение стоимости перетачивания.
5.Рациональное использование объема части здания, относящейся к изготовлению данного изделия и используемой для размещения оборудования, стеллажей, заделов и пр.
10.4. Сокращение накладных расходов
Накладные расходы охватывают те расходы, которые не могут быть определены прямым путем, а только косвенным. В формуле себестоимости накладные расходы учитываются величиной а2 в виде процента от расходов на заработную плату основных рабочих.

К накладным расходам относятся расходы на заработную плату инженерно-технических работников, счетно-конторского персонала, обслуживающего персонала, вспомогательных рабочих, если они не закреплены за определенными рабочими местами; расходы по содержанию транспорта; расходы по охране труда и технике безопасности; расходы по хозяйственному инвентарю; канцелярские расходы и пр.
Сокращение накладных расходов может осуществляться за счет уменьшения значений всех слагаемых, составляющих накладные расходы: упрощения управленческого аппарата, сокращения брака и потерь и т.д.
10.5. Технологичность конструкции изделия
Конструкцию машины или детали принято называть технологичной, если она позволяет в полной мере использовать для изготовления наиболее экономичный технологический процесс, обеспечивающий ее качество при надлежащем количественном выпуске.
Являясь одним из свойств конструкции, технологичность дает возможность снизить трудоемкость изготовления изделия и его себестоимость. Опыт машиностроения показывает, что путем повышения технологичности конструкции машины можно получить дополнительно сокращение трудоемкости ее изготовления на 15 – 25% и снижения себестоимости на 5 – 6 % . Отсюда становится очевидной важность учета возможностей технологии при конструировании машины, ее сборочных единиц и деталей.
В качестве примера на рис. 9.8 приведен чертеж корпуса гидравлического цилиндра, конструкцию которого нельзя считать технологичной. Стоимость обработки отверстия диаметром 8 на глубину свыше 90 его диаметров в несколько раз превысила бы стоимость всех остальных операций по изготовлению корпуса цилиндра. Предназначенное для отвода воздуха из полости гидроцилиндра отверстие могло бы быть направлено от левого торца и быть коротким.
Рис. 10.6. пример нетехнологичной конструкции корпуса гидравлического цилиндра.
На рис. 10.7 с левой стороны расположены примеры нетехнологичного оформления конструкций деталей и их элементов, с правой стороны те же конструкции, но более технологичные.
Обработка отверстия со стороны наклонной и криволинейной поверхности (рис. 10.7, а) затруднена тем, что при врезании сверло будет скользить и может сломаться. Нужна плоская поверхность. Без канавки для

выхода шлифовального круга (рис. 10.7, б) переход от цилиндрической к плоской поверхности получится с закруглением. Долбить шпоночный паз во втулке до упора (рис. 10.7, в) невозможно; необходимо отверстие (кольцевая выточка) для выхода резца. Обработка сквозного ступенчатого отверстия проще, чем обработка двух отверстий с противоположных сторон втулки
(рис. 10.7, г) .
Размещение крепежных отверстий в корпусе на сплошной полке, а не на лапках (рис. 10.7, д) позволяет обрабатывать поверхность полки на проход и воспользоваться преимуществами многоместной обработки. Если отверстия дополнить цековками, то необходимость в обработке полки отпадает. Фасонные отверстия (рис. 10.7, ё) Могут быть обработаны только протяжкой и вырубкой в листовом материале, что экономично лишь при большом объеме выпуска изделий.
Рис. 10.7. Примеры нетехнологичных и технологичных конструкций деталей
Вопрос создания технологичных конструкций машин и их деталей необходимо рассматривать как комплексный и оценивать технологичность деталей во взаимосвязи с другими деталями, составляющими сборочную

единицу. Например, для валов наиболее технологичной является бесступенчатая цилиндрическая поверхность. Однако такая конструкция вала усложнила бы конструкцию сборочной единицы из-за усложнения конструкции сопрягаемых с валом деталей и введения дополнительных деталей. В целом себестоимость изготовления сборочной единицы возросла бы.
Конструкция машины или детали, технологичная при одном количественном выпуске, может оказаться нетехнологичной при другом. Объясняется это тем, что при различных объемах выпуска изделий в единицу времени и по неизменяемым чертежам используют оборудование и технологическую оснастку различной производительности и с разными первоначальными затратами.
Для иллюстрации изложенного на рис. 10.8 показаны три различных способа изготовления колпачка, каждому из которых соответствует свое представление о технологичности его конструкции.
При малом объеме выпуска колпачок будет изготовлен на токарном станке (рис. 10.8, а) . Все переходы (подрезка торца, сверление отверстия, обтачивание наружной поверхности, снятие фаски и отрезка) будут выполняться последовательно. Такой технологии в наибольшей мере отвечает конструкция колпачка, показанная на рис. 10.8, а.
Рис. 10.8. Конструкция колпачка, технологичная для различных объемов выпуска и технологических процессов изготовления
С увеличением объема выпуска колпачков становится целесообразным использование токарно-револьверного станка (рис. 10.8, б), позволяющего совместить сверление отверстия и обтачивание большей части наружной поверхности. Оставшаяся часть может быть проточена с поперечного суппорта широким резцом. Для того чтобы при этом избежать образование порожка, следует заведомо уменьшить диаметр хвостовой части колпачка. Для изготовления колпачка на токарно-револьверном станке технологичной будет конструкция, показанная на рис. 10.8, б.

При значительном увеличении объема выпуска колпачков может быть применен для изготовления четырехшпиндельный токарный автомат
(рис10.8, в).
При большом количестве колпачков, подлежащих изготовлению, становится экономичным получать их из листа вытяжкой. В этом случае конструкция колпачка должна быть такой, как показано на рис. 10.8, г.
Не редки случаи, когда с понятием о технологичности отождествляется понятие об экономичности конструкции. Так как источники экономии затрат в первом и втором случае различны, то смешивать эти понятия недопустимо. К тому же может оказаться, что более технологичная конструкция изделия не будет экономичной. Так, на рис. 10.9 представлены две конструкции подшипника скольжения. Первая из них будет более технологичной из-за простоты конструкции, а следовательно, и более экономичного технологического процесса изготовления. Технологический процесс изготовления второй втулки более сложен и дорог. Однако то, что втулка первой конструкции целиком изготовляется из дорогостоящей бронзы, а вторая имеет лишь бронзовый вкладыш в стальном корпусе, делает конструкцию последней более экономичной, хотя она и менее технологична.
Понятие о технологичности конструкции распространяется не только на технологические процессы изготовления, но и на процессы технического обслуживания и ремонта машины.
Рис. 10.9. Технологичная (а) и экономичная, но менее технологичная (б) конструкция подшипника скольжения
10.6. Унификация конструкций машин
Под унификацией машин понимают использование в различных машинах одних и тех же сборочных единиц и деталей. Унификация позволяет увеличить объем выпуска унифицированных изделий и организовать для их изготовления специальные цеха и заводы с применением передовой технологии и организации производства. При сосредоточении выпуска одинаковых изделий на специализированных заводах и цехах открывается возможность использования более дорогого, но более производительного оборудования, инструмента и другой технологической оснастки, способствующих снижению трудоемкости изготовления изделий. Примерами унифицированных изделий могут служить подшипники качения, электродвигатели, детали и узлы автомобилей и т.д.
Массовое производство широкой номенклатуры подшипников на специализированных заводах позволило автоматизировать их изготовление, создать автоматические цеха, в которых изготовление деталей, контроль и сборка ведутся автоматически.
Американская фирма "Ford", выпуская 72 типа автомобилей, использует для них пять типов моторов, три типа задних мостов и три типа коробок скоростей. Широкая унификация деталей и узлов достигнута и на отечественных автомобильных заводах. Например, Горьковский автомобильный завод использовал в грузовых автомобилях ГАЗ-51А - 55 %,
ГАЗ-52-03 - 71 %, ГАЗ-53 - 62,3 %, ГАЗ-66 — 42,5 % унифицированных деталей.
Широкое распространение в машиностроении унификации изделий приводит к существенным экономическим выгодам, получаемым в результате увеличения объемов их выпуска.
Снижение себестоимости изделий при переходе от мелкосерийного их производства к массовому достигает 75 % и более. Отсюда следует, что унификация конструкции изделий является эффективным средством снижения их себестоимости.
10.7. Типизация технологических процессов
Под типизацией технологических процессов понимают разработку технологических процессов на изготовление типовых деталей, сборочных единиц и машин в целом, отражающих наиболее передовой опыт и достижения промышленности, науки и техники.
Для отнесения машины или детали к тому или иному типу их принято делить на классы. Классом называют совокупность изделий (машин, сборочных единиц или деталей), обладающих близостью служебного назначения.
Сходство служебного назначения изделий порождает сходство требований, которым должна удовлетворять машина, сборочная единица или деталь, близость конструктивных форм, размеров и других качественных показателей. Например, токарные станки делят в зависимости от точности выполняемых на них работ на высокоточные, повышенной и нормальной точности, внося в каждом из классов дополнительное деление по размерам изготовляемых на них деталей на мелкие, средние и тяжелые станки, предназначенные для изготовления крупногабаритных деталей.
В каждом классе машин, сборочных единиц и деталей выбирают типовую машину, сборочную единицу или деталь. Типовой называют деталь, сборочную единицу или машину, наиболее полно представляющую служебное назначение данного класса.
Так, типовая деталь должна охватывать все конструктивные элементы, присущие данному классу деталей, отличаться наиболее высокими требованиями к точности размеров, изготовляться из материала, соответствующего служебному назначению деталей данного класса. В случае, если ни одна из деталей данного класса не отвечает в полной мере указанным требованиям, то разрабатывают конструкцию детали-представителя, учитывающую особенности всех деталей, составляющих класс.
При разработке технологии изготовления конкретной детали из технологического процесса типовой детали выбирают операции и переходы, касающиеся ее конструкции, указывают численные значения ее размеров и требований к точности. Порядок же обработки заготовок остается общим для всех деталей, включенных в класс.
Разработку типовых технологических процессов ведут с учетом типа производства. Для разных объемов выпуска изделий будут свои типовые технологические процессы, ориентированные на применение наиболее производительного оборудования и технологической оснастки, экономичных для данного типа производства.
Типовые технологические процессы способствуют следующему: облегчению труда технологов и сокращению затрат времени на
разработку технологии изготовления новых изделий; сокращению циклов подготовки производства новых изделий;
внедрению в производство наиболее передового опыта и достижений науки и техники;
выявлению потребностей в новых видах оборудования и технологической оснастки;
отработке технологичности конструкции машины, сборочных единиц и деталей.
10.8.Метод групповой обработки заготовок деталей
Вмассовом и крупносерийном производстве увеличение производительности процессов изготовления деталей достигается главным образом за счет применения высокопроизводительных специальных оборудования и технологической оснастки.
Вмелкосерийном и единичном производстве, где объемы партий изготовляемых деталей обычно невелики, обходятся в основном универсальными средствами производства. Специальные приспособления и инструмент применяют лишь в исключительных случаях.
Метод групповой обработки предоставляет возможность расширить применение более производительного оборудования в мелкосерийном и единичном производстве. Его сущность сводится к следующему.
Детали, подлежащие изготовлению, группируют по близости их служебного назначения, что приводит к общности конструктивных форм, материалов, размеров, требований к точности. В группе выбирают наиболее сложную деталь и для каждой операции ее технологического процесса разрабатывают схему настройки станка. Другие детали, входящие в группу, могут быть изготовлены на данной операции либо без поднастройки станка и с использованием только части инструмента, установленного на станке, либо с частичной заменой инструмента и частичной поднастройкой станка. Затраты подготовительно-заключительного времени при этом существенно сокращаются. Большая производительность используемых станка и технологической оснастки уменьшает штучное время.
Например, для изготовления каждой из деталей, показанных на рис. 9.14, при условии, что объемы партий не будут превышать 10 шт., вероятнее

всего будет избран универсальный токарно-винторезный станок. Однако объединение втулок в группу А, колец в группу Б и валиков в группу В позволяет вести изготовление групп деталей на токарном станке с ЧПУ, используя групповые настройки.
Рис. 10.10. Объединение деталей в группы
Метод групповой обработки используют в среднесерийном производстве при создании переналаживаемых агрегатных станков и автоматических линий. Благодаря методу групповой обработки стала возможна автоматизация мелкосерийного и единичного производства и построение ГПС.
10.9.Выбор наиболее экономичного варианта технологического процесса
Для сопоставления двух и большего числа возможных вариантов
технологического процесса с целью выбора наиболее экономичного можно использовать графо-аналитический метод. Для этого все расходы, связанные с осуществлением каждого варианта, делят на две группы: не зависящие и зависящие от числа подлежащих изготовлению изделий.
Впервую группу включают расходы на оборудование, приспособления
икомплект инструментов. Во вторую группу включают расходы на заработную плату рабочих и наладчиков, расходы на материалы, содержание, эксплуатацию
иамортизацию оборудования, приспособлений и инструментов.
Если обозначить первую группу расходов через b , вторую через т и число изделий через х, то себестоимость изготовления х изделий
С = b + тх
Для сравнения нескольких вариантов технологического процесса, например трех, необходимо составить три уравнения
С1 = b 1 + т1 х; С2 = b 2 + т2 х; С3 = b 3 + т3 х
каждое из которых действительно при своих предельных значениях х, что и отображает график, приведенный на рис. 10.11. Первый вариант технологического процесса будет экономичнее второго при 0 < х < х1 и х3 = х < х4 , второй вариант – экономичнее первого при х1 = х < х3, а третий вариант оказывается экономичным при х = х3 и больших значениях х.
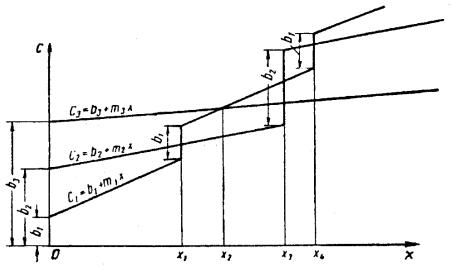
Рис. 10.11. Графическое сопоставление себестоимости трех различных вариантов технологического процесса
Изложенный метод позволяет правильно и быстро выявлять наиболее экономичный вариант технологического процесса применительно к данным производственным условиям, что бывает необходимым при освоении выпуска изделий, применении новых видов оборудования, приспособлений, инструмента и т.д.
10.10. Экономические связи в производственном процессе изготовления машины
Под экономическими связями в производственном процессе изготовления машины следует понимать отношения между затратами живого и овеществленного труда, определяющими себестоимость единицы продукции.
Количественную сторону экономических связей наиболее полно отображает формула себестоимости единицы продукции. Слагаемые себестоимости получают первоначальные значения при разработке конструкции машины и построении технологического и производственного процессов ее изготовления. Все действия, выполняемые при этом, нацелены на обеспечение требуемого качества машины с наименьшими затратами обоих видов труда, т.е. при минимальной ее себестоимости.
Выбор материала деталей и разработка их конструктивных форм, выбор методов достижения требуемой точности машины и расчет конструкторских размерных цепей, выбор вида и формы организации производственных процессов сборки машины и изготовления деталей, выбор способов получения заготовок и их обработки, выбор технологического, транспортного и других видов оборудования, их планировка и т.д. сопровождаются экономической оценкой принимаемых решений.
Экономическую оценку ведут с учетом связей данного решения с затратами на его реализацию на различных стадиях технологического и производственного процессов. Например, выбор метода достижения требуемой точности замыкающего звена размерной цепи и распределения допуска замыкающего звена между составляющими звеньями делают в предвидении затрат на сборку и изготовление деталей. Способ получения заготовок выбирают не только с учетом их себестоимости, но и стоимости материала, переводимого в стружку, а также затрат, связанных с удалением припусков в