
Записка
.pdf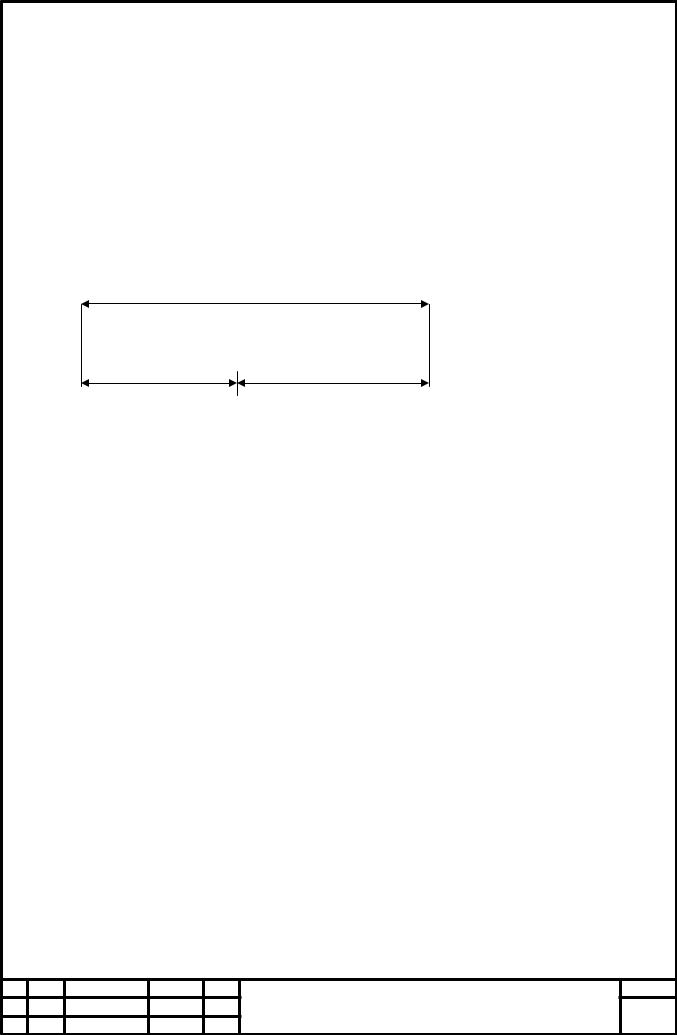
Таким образом, S4 101 0.2 мм.
Выполняем проверку по условию
0.8 = 0.4 + 0.4 = 0.8, следовательно, расчет выполнен верно. 6. Размерная цепь имеет вид
S4 = 201 0.2
[A3] = 15 0.4 |
S5 |
A3min = S4min – S5max
S5max = S4min – A3min = 100.8 – 14.6 = 86.2 мм
A3max = S4max – S5min
S5min = S4max – A3max = 101.2 – 15.4 = 85.8 мм
S5ном = S4ном – A3ном = 101 – 15 = 86 мм
Таким образом, S5 86 0.2 мм.
Лист
МСиИ.2013.09-ИСМП.ПЗ
33
Изм. Лист |
№ Докум. |
Подпись Дата |

10. Расчет и назначение нормы времени
Рассчитаем норму времени на операцию 015 Токарную с ЧПУ технологического процесса механической обработки.
Основное технологическое время на операцию
Тм = 2.02 мин (см. таблицу 11)
Время цикла автоматической работы станка по программе рассчитывается по формуле
Т ЦА Т М Т МВ , |
[8, с.5] |
где:
Тмв - машинно-вспомогательное время работы станка по программе
(включает в себя время на ускоренное перемещение инструмента в зону резания, на установочные движения инструмента в зоне резания, на автоматическую смену инструмента и т.д.), мин
Т МВ 6 0.03 0.1 0.04 0.02 1.14 мин [7, с.605]
Таким образом,
Т ЦА 2.02 1.14 3.16 мин
Вспомогательное время на операцию, не перекрываемое временем автоматической работы станка по программе, рассчитывается по формуле
Т В |
Т |
В уст |
Т |
В оп |
Т |
В изм |
, |
[8, с.5] |
|
|
|
|
|
|
Где:
Тв уст - время на установку и снятие детали, мин,
Лист
МСиИ.2013.09-ИСМП.ПЗ
34
Изм. Лист |
№ Докум. |
Подпись Дата |
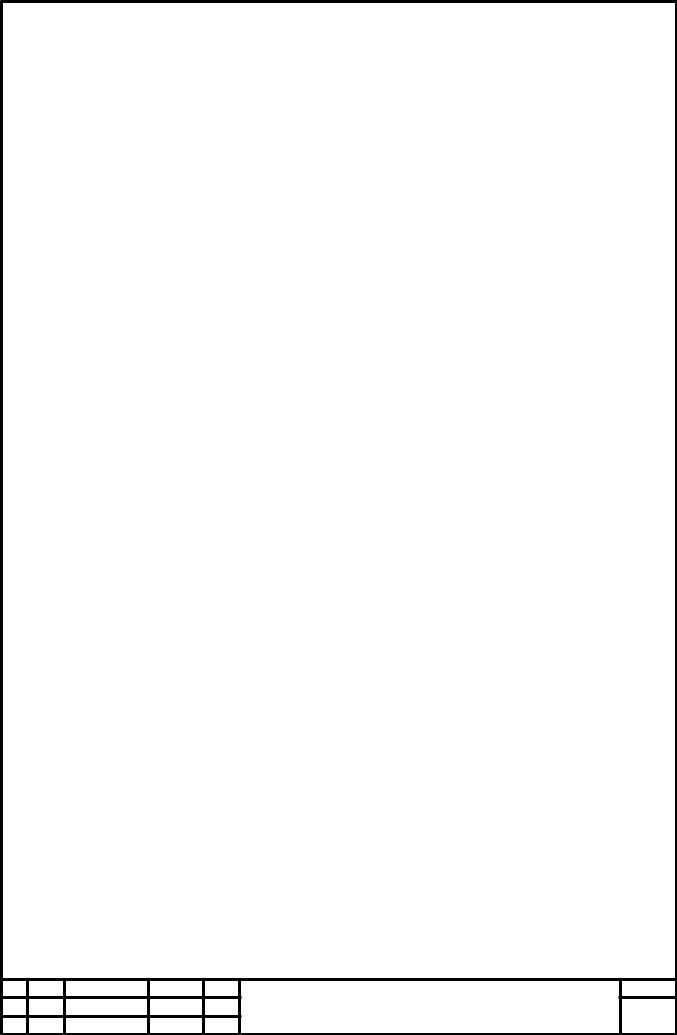
Тв оп - время, связанное с операцией, не вошедшее в управляющую программу (время на проверку прихода инструмента в заданную точку после обработки, на установку и снятие щитка от разбрызгивания эмульсией), мин
Тв изм - время на технические измерения, мин
Принимаем
Т В уст 3 0.7 2.1 мин [8, с.57]
Т В оп 0,32 0.15 0.03 0,5 мин [8, с.79]
Принимаем время на измерение поверхностей: [8, c.80-89]
Т В изм 2 0,07 0,14 мин
Т В 2,1 0,5 0,14 2.74 мин
Штучное время на операцию определяется по формуле
Т |
|
Т |
|
Т |
|
К |
|
|
1 |
|
a |
|
, [8, с.5] |
ШТ |
ЦА |
В |
tb |
|
|
|
|||||||
|
|
|
|
|
|
100 |
|
||||||
|
|
|
|
|
|
|
|
|
|
|
|
где:
Кtb - поправочный коэффициент на вспомогательное время,
а - время на техническое и организационное обслуживание рабочего места, отдых и личные потребности, в % от оперативного
Принимаем Кtb = 1.32 [8, с.50]
а = 6% [8, с.90]
Тогда,
Т |
|
3,16 2.74 1.32 |
1 |
6 |
|
7.18 мин |
|
ШТ |
|
|
|
||||
|
|
|
100 |
|
|||
|
|
|
|
|
|
Лист
МСиИ.2013.09-ИСМП.ПЗ
35
Изм. Лист |
№ Докум. |
Подпись Дата |
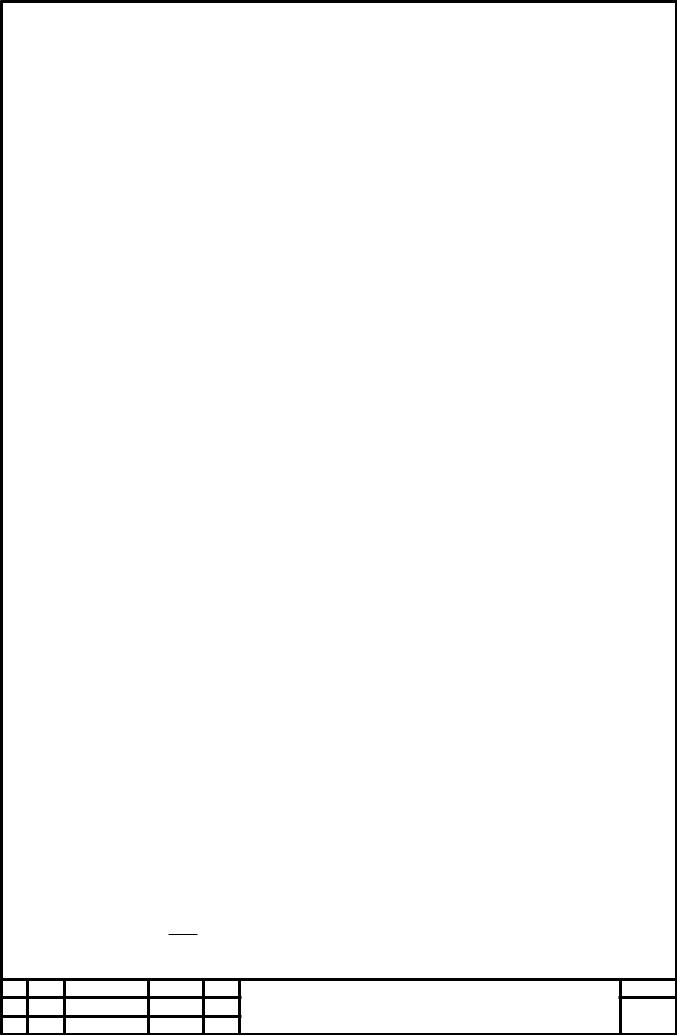
Штучно-калькуляционное время на операцию рассчитывается по
формуле
Т ШТ .К . Т ШТ |
|
Т П.З. |
, [8, с.5] |
|
|||
|
|
n |
где:
Тпз - подготовительно-заключительное время на операцию
Т П.З Т П.З.1 Т П.З.2 Т П.З.3 , [8, с.8]
где:
Тпз1 - время на организационную подготовку;
Тпз2 - время на наладку станка, приспособления, инструментов;
Тпз3 - время на пробную обработку детали.
Принимаем
Тпз1 = 9 + 2+ 2 = 13 мин [8, с.96] (время на получение наряда, чертежа,
комплекта технологической документации, инструмента и оснастки (в
инструментально-раздаточной кладовой), на ознакомление с документами на инструктаж мастера).
Тпз2 = 2.5·3+0,8·3+0,3·3= 10,8 мин [8, с.96] (время на наладку станка,
приспособлений, инструмента, программных устройств).
Тпз3 = 0 мин (пробную обработку производить не будем).
Т П.З 13 10.8 23,8 мин
Таким образом,
Т ШТ .К .
7.18 23.8 11,94 мин 5
Лист
МСиИ.2013.09-ИСМП.ПЗ
36
Изм. Лист |
№ Докум. |
Подпись Дата |
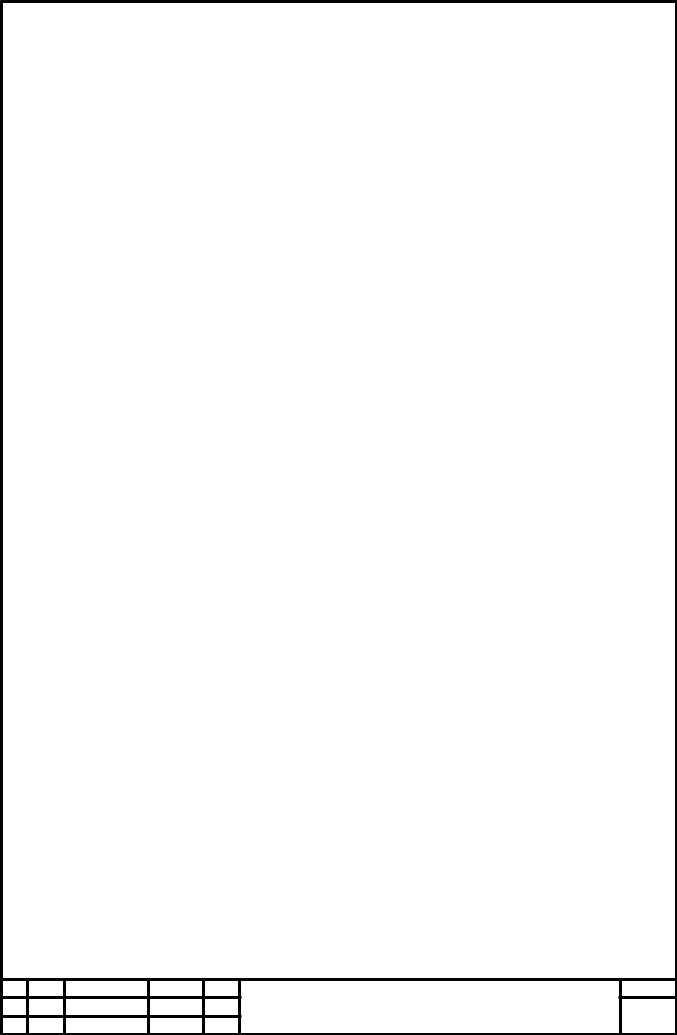
Нормы времени на операции проектного технологического процесса изготовления представлены в таблице 12:
Таблица 12. Нормы времени на операции проектного технологического процесса
|
|
Т о., |
Т в., |
|
а, |
Тшт., |
Т п.з., |
Тшт.к, |
|
Операция |
|
|
Кtb |
|
|
|
|
|
|
|
% |
|
|
|
||
|
|
мин |
мин |
|
мин |
мин |
мин |
|
|
|
|
|
|||||
|
|
|
|
|
|
|
|
|
005 |
Отрезная |
0.18 |
0.4 |
1.4 |
8 |
0.80 |
12 |
3.2 |
|
|
|
|
|
|
|
|
|
010 |
Токарная с ЧПУ |
2,02 |
2,74 |
1.32 |
6 |
7,18 |
23,8 |
11,94 |
|
|
|
|
|
|
|
|
|
030Шлифовальная с ЧПУ |
3.08 |
2,92 |
1,32 |
14 |
7,43 |
7,5 |
8,93 |
|
|
|
|
|
|
|
|
|
|
015 |
Сверлильно – фрезерно - |
|
|
|
|
|
|
|
|
|
0.28 |
2,02 |
1,32 |
14 |
3 |
3,75 |
6,75 |
- расточная |
|
|
|
|
|
|
|
|
|
|
|
|
|
|
|
|
|
045 |
Шлифовальная |
0,2 |
1,05 |
1,32 |
8 |
1,6 |
8,5 |
10,1 |
|
|
|
|
|
|
|
|
|
Лист
МСиИ.2013.09-ИСМП.ПЗ
37
Изм. Лист |
№ Докум. |
Подпись Дата |

11. Расчет погрешности обработки
Проведем расчет погрешности для чистового точения 25g7
токарной операции 015.
Суммарную погрешность обработки деталей определяем по
зависимости [3, стр.188]:
2 2У 2Н (1,73 и )2 (1,73 ст )2 (1,73 т )2
где: |
|
и – погрешность вызванная размерным износом, которая |
|||||
определяется по следующей зависимости [3, стр.192]: |
|||||||
|
|
|
L L0 |
u |
|
|
|
И |
|
0 |
|
|
|||
|
1000 |
|
|
|
|||
|
|
|
|
|
|
||
L – длина пути резания при обработки партии N=10шт; |
|||||||
L |
D l N |
|
3,14 25 175,5 10 |
1060м |
|||
1000 s |
|
||||||
|
|
|
1000 0,13 |
L0 = 1000м начальный износ вершины резца;
u0 – относительный износ для материала Т30К4 [3, стр.276] u0=3мкм;
И 1060 1000 3 6мкм 1000
У – погрешность вызванная упругими деформациями технологической системы под влиянием силы резания [3, стр.192]:
|
W |
P |
W |
P |
; |
У |
max |
Y max |
min |
У min |
|
Wmax; Wmin; - наибольшая и наименьшая податливость системы;
PYmax; PYmin – наибольшее и наименьшее значение составляющей силы
Лист
МСиИ.2013.09-ИСМП.ПЗ
38
Изм. Лист |
№ Докум. |
Подпись Дата |
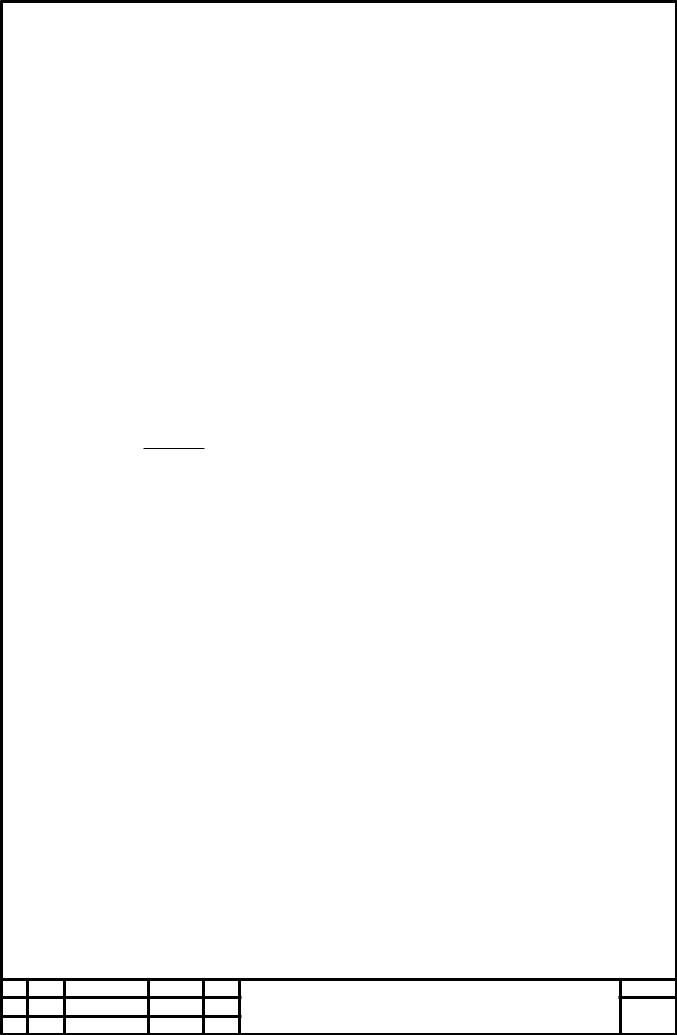
резания совпадающей с направлением выдерживаемого размера;
Наибольшее и наименьшее перемещение продольного суппорта под нагрузкой 686 Н составляет 40мкм и 50 мкм [7, стр.29];
Тогда наименьшая податливость:
Wmin |
|
40 |
|
58мкм / кН |
|
|
|||
0,686 |
|
|||
|
|
|
|
|
Wmax |
Wст max |
Wзагmax |
где: Wст max – наибольшая податливость станка;
W 40 50 65мкм
ст max |
2 |
0,686 |
|
Wзагmax - наибольшая податливость заготовки [3, стр.193];
|
2 |
|
l |
д |
3 |
Wзагmax |
|
|
|
|
|
|
|
|
|||
|
dпр |
|
|
|
|
|
d |
пр |
где: dпр – приведенный диаметр, dпр =25мм
lд – длина детали lд = 175,5мм
|
|
2 |
175,5 |
3 |
|
||
Wзагmax |
|
|
|
|
|
27,6мкм |
|
25 |
25 |
||||||
|
|
|
|
|
Wmax 65 27,6 92,6мкм
Силы резания определяем по формуле [3, стр.193];
PY CP t x s y vn
Лист
МСиИ.2013.09-ИСМП.ПЗ
39
Изм. Лист |
№ Докум. |
Подпись Дата |

, x, y, n – коэффициент и показатели степеней для составляющих сил резания [3, стр.276];
CP = 243; x = 0,9; y = 0,6; u = -0,3
При обработки допуск IT7 Td = 0,021 колебание глубины резания будет: tmin = 0,5мм; tmax = 0521мм;
PY max 243 0,5210,9 0,130,6 163 0,3 19Н 0,051кН
PY min 243 0,50,9 0,130,6 163 0,3 19Н 0,050кН
У 92,6 0,051 58 0,050 1,8мкм
ст – погрешность связанная с неточностью станка[3, стр.193];
ст C l L
C – Допустимое отклонение от параллельности оси шпинделя относительно направляющих станка в плоскости выдерживаемого размера на длине L = 300мм C=7
7 175,5 ст 300 4мкм
Н – погрешность наладки станка;
|
|
|
|
2 |
|
|
|
|
изм |
2 |
Н |
|
К |
Р |
Р |
К |
|
|
|
|
|
И |
2 |
|||||||||
|
|
|
|
|
|
|
|
|
где: Р – погрешность регулирования положения резца;
Р = 2мкм [7, стр 71]
из – погрешность измерения размера детали;
Лист
МСиИ.2013.09-ИСМП.ПЗ
40
Изм. Лист |
№ Докум. |
Подпись Дата |
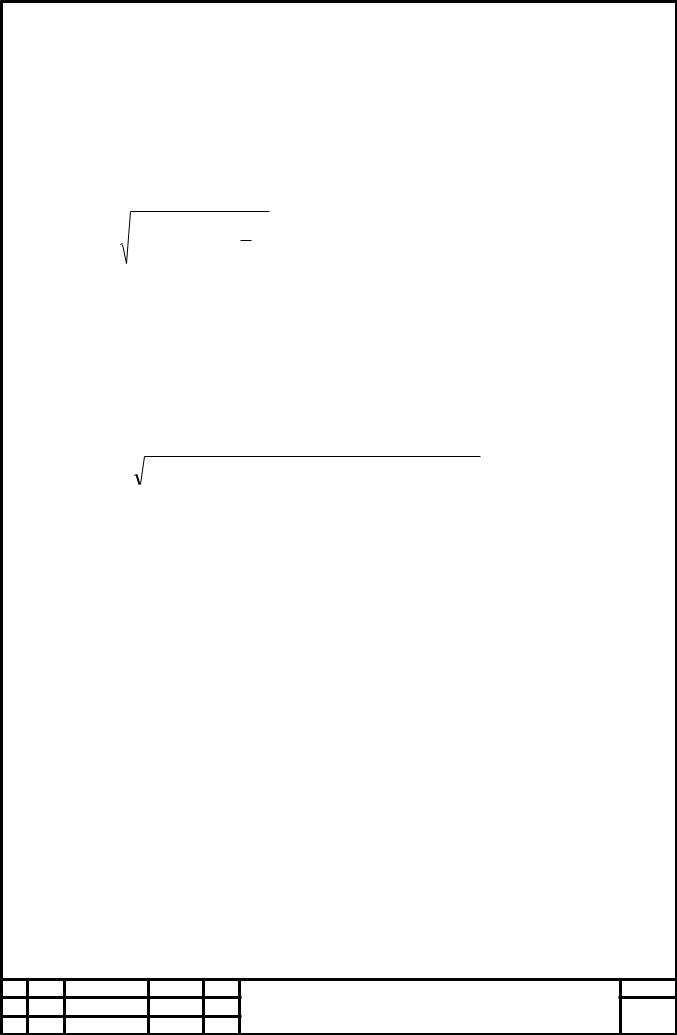
|
из = 6мкм [7, стр 71] |
|
|
|||||||
|
КР = 1,73 и КИ =1 –коэффициенты учитывающие отклонения величин |
|||||||||
Р и |
из |
от нормального закона распределения. |
||||||||
|
|
|
|
|
2 |
|
|
6 |
|
2 |
|
Н |
|
|
|
|
3,4мкм |
||||
|
1,73 2 |
1 |
2 |
|
||||||
|
|
|
|
|
|
|
|
|
|
|
|
Т |
– температурная погрешность, зависящая от температурных |
||||||||
деформаций технологических систем приняв их равными 15% от суммы |
||||||||||
остальных погрешностей. |
|
|
|
|||||||
|
Т |
0,15(6 1,8 4 3,4) 2,2мкм |
||||||||
|
|
|
2 |
|
1,82 3,42 (1,73 6)2 (1,73 4)2 (1,73 2,2)2 20,2мкм |
|||||
|
|
|
|
|
|
|
|
|
|
|
|
|
|
|
|
|
|
|
|
|
Лист |
|
|
|
|
|
|
|
|
|
|
МСиИ.2013.09-ИСМП.ПЗ |
Изм. Лист |
№ Докум. |
Подпись |
Дата |
|
|
41 |
||||
|
|
|
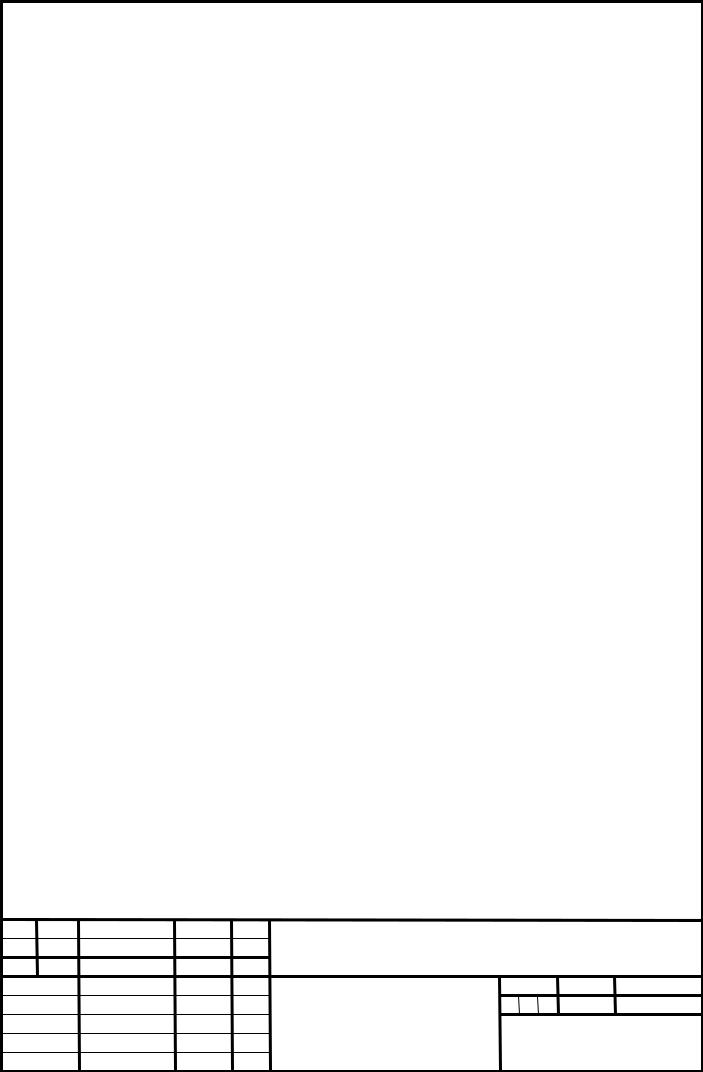
КОНСТРУКТОРСКИЙ
РАЗДЕЛ
МСиИ.2013.09-ИСМП.ПЗ
Изм. Лист № докум. Подпись Дата
Студ. Матьякубов А.А.
Рук.
Конструкторский раздел |
Лит. |
Лист |
Листов |
|
|
|
|
Пояснительная записка |
|
|
|
БГТУ УНТИ гр.09-ИСМП