
ПИМС и МП. Лекции, задания / УчебнПособ_Р2_1_м
.pdf20
Контактные пары «резистивная плёнка — проводящая плёнка» характеризуются удельным переходным сопротивлением (Ro Ом∙мм2), значение которого зависит от выбираемых материалов пары и технологии формирования контакта. Значение Ro находится в широком диапазоне от (0,3–6) мОм/мм2 для пары Сr-Al до (20–300) мОм/мм2 для пары Au-Ta. В расчётных методиках принимаеся усреднённое значение Ro = (0,05–0,25) Ом/мм2.
4.3.4 Материалы толстоплёночных резисторов
Агрегатное состояние материалов толстопленочных резисторов — это пасты, состоящие из основного функционального материала (наполнителя), порошка-стекла (фритта) и органической связки. В качестве наполнителя резистивных паст применяют серебро, палладий и их сплавы, окислы таллия и рутения. Для получения фритты наиболее широко используются свинцовые и цинковые бороcиликатные стекла. После термообработки пасты, нанесенной на подложку через маску, образуется резистивная стеклоэмаль. Поверхностное сопротивление резистивной стеклоэмали и температурный коэффициент её сопротивления зависят от процентного содержания наполнителя и стекла в исходной пасте. Повышенными температурной и временной стабильностью характеризуются стеклоэмали, в состав которых входит сплав палладий-серебро.
Таблица 4.5 — Резистивные пасты толстоплёночных ГИС
Марка |
ПР- |
ПР- |
ПР- |
ПР- |
ПР- |
|
ПР- |
ПР- |
|
ПР- |
|
|
ПР- |
ПР- |
пасты |
5 |
20 |
100 |
500 |
1К |
|
3К |
6К |
|
20К |
|
|
50К |
100К |
|
|
|
|
|
|
|
|
|
|
|
|
|
||
R□, |
5 |
20 |
1∙102 |
5∙102 |
103 |
|
3∙103 |
6∙103 |
2∙104 |
|
5∙104 |
1∙105 |
||
Ом |
|
|
|
|
|
|
|
|
|
|
|
|
|
|
ТКС, |
|
|
|
|
|
±8 |
|
|
|
|
|
|
|
|
10–4 К–1 |
|
|
(в диапазоне температур — 60 |
÷ +125 |
°С) |
|
|
|||||||
Ро, |
|
|
|
|
|
|
|
|
|
|
|
|
|
|
Вт/см2 |
|
|
|
|
|
(3–8) |
|
|
|
|
|
|
|
Промышленностью выпускается совокупность типов резистивных паст с удельным поверхностным сопротивлением получаемых из них толстых стеклоэмалевых пленок от 5 Ом до 100 кОм.
21
Параметры резистивных паст приведены в табл. 4.5. Растекаемость паст на одну сторону составляет от 70 до 100 процентов толщины пасты до вжигания, что соответствует (30–50) мкм. После вжигания толщина резистивной плёнки определяется на уровне (15–20) мкм. Температура обжига резистивных толстых плёнок в зависимости от металлической основы пасты составляет
(750–1000) °С.
В качестве контактных к резистивным плёнкам и соединительных проводников толстопленочных конструкций микросхем применяются проводящие пасты, параметры которых приведены в табл. 4.6. В отличие от тонкоплёночных конструкций резисторов в толстоплёночных резисторах резистивные плёнки предпочтительно исполнять вторым слоем по проводящим слоям. Эта особенность определяется спецификой нанесения пасты через сетчатый трафарет и фактором согласования температур вжигания, когда требуется обеспечивать для последующих слоёв меньшие температуры вжигания в сравнении с температурами вжигания предшествующих слоёв.
Таблица 4.6 — Параметры проводящих паст
Марка пасты |
4350 |
4350К |
4351 |
4005 |
4205 |
4320 |
|
|
|
|
|
|
|
Растекаемость |
|
|
|
|
|
|
(на одну сторону), |
|
|
|
|
|
|
мкм, не более |
50 |
25 |
25 |
50 |
25 |
50 |
Температура вжига- |
|
|
|
|
|
|
ния, °С |
820±10 |
820±10 |
870±5 |
820±10 |
870±3 |
855±5 |
R□, Ом |
|
|
|
|
|
|
не более |
0,05 |
0,05 |
0,05 |
0,05 |
0,02 |
0,02 |
Адгезия, |
|
|
|
|
|
|
кгс/см2, не менее |
50 |
50 |
100 |
50 |
80 |
50 |
После вжигания толщина проводящих плёнок, как и резистивных, должна быть на уровне 17±4 мкм. По проводящим плёнкам для последующего электромонтажа компонент должно быть проведено лужение припоями ПОС-61, ПСрОС-3-58. Для этой цели могут быть применены лудящие пасты, нанесение которых исполняется трафаретной печатью или дозатором. Параметры ряда распространённых лудящих паст приведены в табл. 4.7.
22
Таблица 4.7 — Параметры лудящих паст толстоплёночных ИМС
Марка |
Припой |
Флюс |
Растворитель остатков |
|
пасты |
связки |
|||
|
|
|||
|
|
|
|
|
Пл-111 |
ПОС-61 |
Активный, средне- |
Вода |
|
|
|
коррозийный |
|
|
|
|
|
|
|
Пл-112 |
ПОС-61 |
Некоррозийный |
Хлористый метилен |
|
|
|
|
|
|
Пл-113 |
ПОС-61 |
Слабокоррозийный |
Спирто-бензиновая смесь |
|
|
|
|
(1:1). Водные моющие рас- |
|
|
|
|
творы |
|
ПЛ-312 |
ПСрОС-3-58 |
Некоррозийный |
Хлористый метилен |
В лудящих пастах число частиц припоя с максимальным размером (40–80) мкм не должно превышать 80 %. Лудящие пасты, как ранее упоминалось, наносятся трафаретной печатью или дозатором. Температура оплавления перечисленных лудящих паст равна (225±5) °С. Лужение по процессу производства толстоплёночных плат является заключительным сравнительно высокотемпературным этапом.
Температура вжигания паст, как и температура испарения материала при напылении тонких плёнок, определяется температурными свойствами применённых металлов и их сплавов. В табл. 4.8 приведены температуры плавления ряда металлов, применяемых в чистом виде или в качестве наполнителей для паст.
Таблица 4.8 — Температура плавления металлов плёнок ГИМС
Материал |
Аl |
|
Ag |
Au |
|
Cu |
Ni |
|
Pd |
Ti |
|
Pt |
|
|
|
|
|
|
|
|
|
|
|
|
|
Температура |
|
|
|
|
|
|
|
|
|
|
|
|
плавления,°С |
660 |
|
961 |
1063 |
|
1083 |
1455 |
|
1555 |
1725 |
|
1774 |
Материал |
|
Cr |
|
Mo |
|
Ta |
|
W |
||||
|
|
|
|
|
|
|
|
|
|
|
|
|
Температура |
|
|
|
|
|
|
|
|
|
|
|
|
плавления,°С |
1800 |
|
2622 |
2996 |
3382 |
Процентный состав металла наполнителя в пасте и его температура плавления влияют на температуру вжигания паст толстых плёнок. Выбирая материал и изменяя в определённых пределах процентный состав наполнителя, изменяют температуру
23
вжигания и согласуют очерёдность формирования толстоплёночных слоёв.
Для тонкоплёночных технологий температура плавления незначительно отличается от температуры испарения металла, и приводимая таблица характеризует температурные режимы нанесения плёнок. К примеру, такие материалы, как Mo, Ta, W, в производстве микросхем могут применяются в составе технологической оснастки (тигли, испарители) установок испарения. Как функциональные материалы пленок, они могут применятся в ионно-лучевых технологиях распыления и в качестве присадок для паст.
4.3.5 Технологические ограничения
Технологические ограничения по формированию размеров топологических конфигураций резисторов для разных технологических методов приведены в табл. 4.9. Погрешность линейных размеров и связанный с ней пропорциональной зависимостью минимально-допустимый технологический размер учитываются в расчётах размеров резисторов по заданной точности. Технологическое перекрытие разных топологических слоёв позволяет исключить влияние погрешности смещения одних слоёв относительно других. При этом увеличиваются топологические размеры резисторов, но исключается возможное изменение сопротивления. По табличным значениям абсолютной погрешности ∆b и перекрытию ∆С определяется абсолютная погрешность совмещения слоёв ∆совм с учётом равенства
∆С = 2∙(∆совм + ∆b).
Так для масочной технологии по значениям табл. 4.9 погрешность совмещения составляет 40 мкм.
Применение половинных погрешностей совмещения ∆совм и линейных размеров ∆b позволяет контролировать погрешности формирования на любом из краёв топологического элемента.
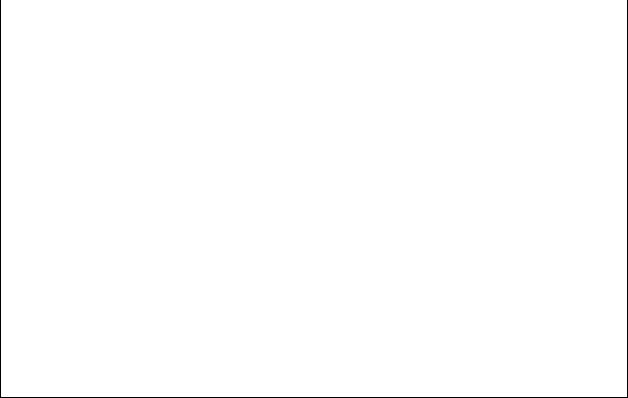
24
Таблица 4.9 — Технологические ограничения методов формирования элементов топологии плёночных и гибридных ИМС
|
Ограничения технологического |
|||||
Наименование параметра |
метода формирования топологии |
|||||
|
М |
Ф |
МФ |
ЭИ |
ТА |
ТП |
Абсолютная погрешность линейных |
|
|
|
|
|
|
размеров длины и ширины элементов |
|
|
|
|
|
|
одного слоя, 2∆L, 2∆b, мкм |
±10 |
±10 |
±10 |
±10 |
±10 |
±100 |
Минимально-допустимый технологиче- |
|
|
|
|
|
|
ский размер в одном слое Lmin, bmin, |
|
|
|
|
|
|
мкм |
100 |
50 |
100 |
150 |
50 |
800 |
Максимальное отношение размеров по- |
|
|
|
|
|
|
лосы L / b |
10 |
100 |
30 |
100 |
100 |
100 |
Перекрытие для совмещения элементов |
|
|
|
|
|
|
топологии разных слоёв, ∆С, мкм |
200 |
100 |
200 |
100 |
100 |
400 |
Минимальная ширина проводника, |
|
|
|
|
|
|
bп min |
100 |
50 |
100 |
100 |
100 |
800 |
Обозначения метода: М — масочный; Ф — фотолитографический; МФ — масочно-фотолитографический; ЭИ — электронно-ионный; ТА — танталовая технология; ТП — толстоплёночная технология.
Другим технологическим ограничением для плёночной технологии является погрешность исполнения толщины плёнки и искажение электро-физических свойств материала вследствие неоднородности состава плёнки. Названные источники погрешности определяют суммарную относительную погрешность δR□ удельного поверхностного сопротивления. Погрешность δR□ учитывается в расчётах резисторов по заданной точности. Относительные погрешности поверхностного сопротивления для выбранного материала, применяемого для диапазона значений R□, повышаются с увеличением устанавливаемого значения R□.
Для тонкоплёночных конструкций резисторов значение погрешности δR□ составляет (2–5) %, тогда как для толстоплёночных исполнений значение погрешности δR□ достигает (30–50) %. Погрешность сопротивления резисторов (5–20) % для многих применений является приемлемой, тогда как значения (30–50) % в большинстве случаев не допускаются. Поэтому тонкоплёночные резисторы могут быть исполнены и применены как без корректировки (подгонки), так и с корректировкой сопротивления.
25
Толстоплёночные конструкции резисторов применяются преимущественно с подгонкой сопротивления.
Основанием к исполнению резисторов с подгонкой сопротивления и, соответственно, усложнению конструкции и процесса производства являются:
–превышение производственным отклонением δR□ заданного допуска на сопротивление резистора;
–недопустимо завышенные размеры резистора при близости значений δR□ и заданного допуска на сопротивление резистора.
4.3.6 Тонкоплёночные резисторы без подгонки
Проектный вариант конструкции тонкоплёночного резистора изображён на рис. 4.1, а. В результате проектных расчётов определяются длина L и ширина резистора, ширина контактных площадок Вк и перекрытие Lк контактных площадок и резистивной полосы. Проектирование резисторов основывается на согласовании четырёх критериев выбора названных размеров:
–сопротивление резистора должно соответствовать номиналу, R;
–сопротивление должно соответствовать рассеиваемой мощности, Р;
–производственная погрешность сопротивления δRп не должна превосходить заданное значение допуска сопротивления резистора δRз;
–размеры резистора должны быть не менее технологически реализуемых, Lmin.
Перечисленные критерии позволяют представить следующие расчётные соотношения для связей функциональных параметров с размерами конструкции, параметрами материалов и технологическими отклонениями:
R= R□∙ (Кф = L/b); |
(4.2) |
P ≤ Po∙L∙b; |
(4.3) |
26 |
|
(δRз– δRэ) ≥ δRп = δL + δb + δR□ + δRк. |
(4.4) |
{L, b, Lк} ≥ Lmin; |
(4.5) |
δRк = 2Rк./R; |
(4.6) |
Rк = (1,5/b)√(R□Rко); |
(4.7) |
Lк ≈ (1,5 √(Rко/ R□). |
(4.8) |
В формулах (4.2) — (4.5) введены обозначения: Кф — коэффициент формы резистора;
δRэ — суммарная погрешность сопротивления резистора, определяемая изменением температуры и временным старением; δL, δb, δR□, δRк — относительные погрешности длины и ширины резистора, погрешность поверхностного сопротивления R□ и погрешность, вносимая сопротивлениями контактных пере-
ходов.
Комбинируя выражения (4.2) — (4.7) при Кф = R/R□ ≥1, размеры резистора определить по формулам
bт ≥ { b∙ [(R□/ R) + 1] + (3/R)∙√(Rко∙R□)}/(δRп–δR□); (4.10)
Lт = Кф∙ bт |
(4.10а) |
по критерию точности и |
|
bр ≥ √[Р∙R□/(Ро∙R)]; |
(4.11) |
Lp = Кф∙bр |
(4.11а) |
по критерию мощности рассеяния резистора.
Ширина контактной площадки Вк и перекрытие её с резистивной полосой определяется с учётом погрешности совмещения ∆совм по соотношениям
Вк ≥ (b + 2∆C); |
(4.12) |
27
Lп ≥ (Lк + ∆C). |
(4.12 а) |
Аналогично при Кф < 1 первым определяется размер L и далее, с учётом Кф, определяется размер b по формулам:
Lт ≥ { L∙[(R/ R□) + 1] + 3√(Rко/ R□)}/(δRп–δR□); |
(4.13) |
bт = Кф∙ Lт |
(4.13а) |
по критерию точности и |
|
Lр ≥ √[Р∙R/(Ро∙R□)]; |
(4.14) |
bp = Кф∙ Lp |
(4.14а) |
по критерию заданной мощности.
Из полученных расчётных значений размеров L, b принимается больший из определяющих размеров в соответствии с неравенствами
b > max {bp, bт, bтехн}, |
(4.15) |
при Кф >1 и |
|
L > max {Lp, Lт, Lтехн}. |
(4.15а) |
Размеры Lтехн, bтехн рассматриваются как технологически минимально допустимые (см. табл. 4.9).
Ширина контактной площадки Вк и перекрытие её с резистивной полосой определяется по соотношениям (4.12), (4.12а).
Следует обратить внимание на расчётные соотношения (4.10) и (4.13), согласно которым при наличии требований к допуску сопротивления резистора, условие физической реализуемости определяется неравенством
(δRп–δR□) > 0. |
(4.16) |

28
Можно показать, что выбором сопротивления R□ минимизируется площадь резистора и окружающей его защитной зоны при Кф = 1. Для массива резисторов с разными сопротивлениями условия минимизации не реализуются. Тем не менее при выборе поверхностного сопротивления в диапазоне значений {Rmin … Rmax} по неравенству
Rmin < R□ < Rmax
возможно уменьшить занимаемую резисторами площадь. Определённое приближение к минимальной площади, занимаемой N резисторами, достигается при выборе R□ по формуле
n |
n |
|
R□ опт = Ri |
1 Ri , |
(4.17) |
1 |
1 |
|
в которой Ri — значения сопротивлений резисторов массива. Методика проектирования тонкоплёночных резисторов без
подгонки сопротивления сводится к последовательности действий:
–формирование необходимого набора исходных данных;
–определение значения удельного поверхностного сопротивления R□ по выражению (4.17);
–выбор марки резистивного сплава по найденному значе-
нию R□ с повышенным значением Ро и меньшими значениями t
ис и расширение набора исходных данных;
–оценка эксплуатационного допуска δRэ по температурной по-
грешности δRt = ТКЕ∙∆Т и погрешности старения плёнки δRcт = = с∙ Δt (отклонение сопротивления по старению δRcт принимается из паспортных данных выбранной марки сплава и корректируется с учётом требуемого времени эксплуатации Δt, а температурное отклонение сопротивления определяется произведением температурного коэффициента сопротивления плёнки (ТКЕ) на отклонение температуры ∆Т) и производственного допуска δRп;
–проверка реализуемости резисторов без подгонки сопротивления по условию (3.16);
–определение размеров резисторов по формулам (4.10) —
(4.12а);
–выбор определяющих размеров согласно условиям (4.15) —
(4.15а);
29
– оформляется эскиз топологии с перечнем размеров резистора.
Удельное переходное сопротивление контактной пары принимается равным Rко = 0,05–0,25 [Ом∙мм2].
4.3.7 Проектирование резисторов в форме меандра
Для уменьшения длина высокоомных резистора, сокращения длины связей в микросхеме может потребоваться ввести в
ленточную конструкцию резистора изгибы. Варианты изгибов и изогнутых резисторов изображены на рисунках 4.1 — 4.2. Учёт Г-образных и П-образных изгибов в корректировке размеров исходного полоскового резистора рассмотрен в п. 4.3.1. Одним из вариантов изогнутых резисторов является резистор типа «меандр» (см. рис. 4.2), который используется для упрощения последующей коммутации, хотя занимаемая резистором площадь при этом возрастает. Геометрическими параметрами резисторамеандра являются: ширина резистивной полоски а, шаг звеньев меандра t (под звеном подразумевается Г-образная часть меандра), ширина резистора В и длина L.
Так как имеют место соотношения
L ≈ n ∙t, В ≈ Lo/n, |
(4.18) |
где Lo есть длина исходного полоскового резистора, а n есть число звеньев, то
n ≈ √[(Lo∙L)/(t∙B)]. |
(4.19) |
Обычно принимается t = 2a и L = B, т.е. ленту с изгибами вписывают в квадрат, что обеспечивает минимальные габаритные размеры внешнего защитного промежутка. Тогда
n ≈ √[Lo/(2a)], |
(4.19а) |
где Lo и а — длина и ширина предварительно спроектированного резистора линейной конфигурации.