
ПИМС и МП. Лекции, задания / УчебнПособ_Р2_1_м
.pdf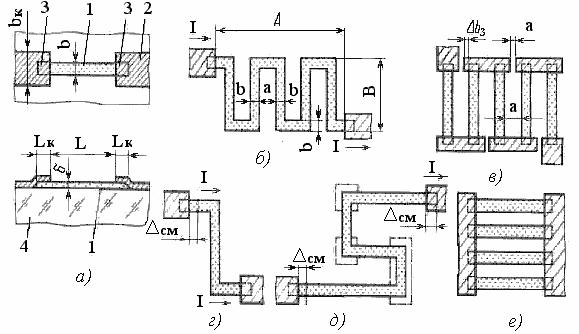
10
Рисунок 4.1
изогнутые конфигурации окон в масочных трафаретах приводят к их «провисанию» и искажению размеров формируемых плёночных фрагментов. Переход к изогнутым и составным конфигурациям резисторов, как отмечалось применительно к полупроводниковым резисторам, может потребоваться при необходимости рационализации компоновки топологических фрагментов в монтажном пространстве платы.
В толстопленочных микросхемах используют главным образом прямоугольные полосковые резисторы (см. рис. 4.1, а). Резисторы сложной (4.1, б...е) формы используют в тонкопленочных гибридных микросхемах для формирования сопротивлений больших номиналов. Применение таких конструкций позволяет несколько сэкономить площадь, отводимую под резистор, и рационально скомпоновать топологию для размещения других элементов и компонентов микросхемы.
Резисторы типа меандр имеют технологические ограничения на уменьшение размера а и увеличение размера В (см. рис. 4.1, б) аналогично полосковым резисторам в отношении их коэффициента формы. Обычно при масочном методе в конфигурации резисторов стараются придерживаться соотношения В/а ≤10, и а ≈ 2 t, где t — толщина биметаллической маски, а 2 t — минимальное допустимое технологией расстояние между двумя щеля-
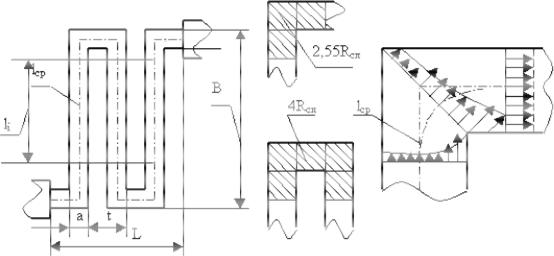
11
ми в биметаллической маске. Для составного резистора (см. рис. 4.1, в) допускается Вх/а ≤ 50, так как прямоугольные резистивные полоски и проводящие перемычки формируются раздельно с помощью двух различных масок. Эта же технологическая особенность позволяет формировать тонкопленочные резисторы сложной нерегулярной формы (см. рис. 4.1, д) с применением дополнительных металлических перемычек по углам контура резистора.
Конструкция (см. рис. 4.1, е), представляющая собой параллельное соединение группы резистивных полосок, характерна для мощных резисторов. В ней обеспечивается более равномерное распределение температуры по поверхности подложки, занятой резистором.
Врезисторах сложной формы для исключения влияния неточности совмещения резистивного слоя с контактами необходимо располагать контакты относительно резистивной полосы так, чтобы направления тока втекающего в резистор и вытекающего совпадали.
Вконструкциях резисторов топологическими конфигурациями изображёнными на рис. 4.1, б, г, д, плотность тока в изгибах неравномерна. Участок изгиба (см. рис. 4.2, г) имеет пониженное сопротивление в сравнении с линейным участком той же длины (по средней линии), что требует корректировки длины резистора в сторону её увеличения. Участок, включающий три
квадрата (см. рис. 4.2, б), вместо 3R□ имеет сопротивление
а
б
г
в
Рисунок 4.2
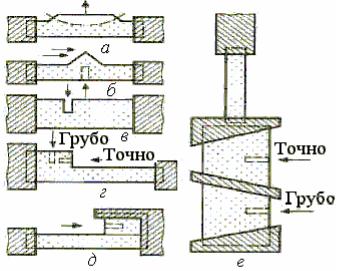
12
2,55R□. Участок из пяти квадратов (см. рис. 4.2, в) вместо 5R□ имеет сопротивление 4R□. Коэффициенты «2,55» и «4» являются коэффициентами формыКфи соответствующихизогнутых участков.
Сопротивление изогнутых резисторов представляется суммой сопротивлений прямолинейных участков и изгибов и определяется по формуле
R = R□ ∙[ (L/a) +2 ∙Kфко + N∙Kфи], |
(4.1) |
где R — номинал сопротивления;
R□ — сопротивление квадрата резистивного слоя (поверхностное сопротивление слоя);
Kфко — коэффициент формы контактной области;
N — число изгибов (если введены в топологию резистивной полосы);
Кфи — коэффициент формы изгиба (3 или 5 квадратов);
L, a — суммарная длина линейных участков резистивной полосы между границами уголковых изгибов и ширина резистивной полосы соответственно.
В плёночных резисторах при несоответствии технологического отклонения сопротивления заданным требованиям по точности применяется технологическая корректировка (подгонка) сопротивления после группового формирования плёночных структур. Для такой корректировки предусматриваются ряд способов. Подстраиваемые плёночные резисторы принято называть резисторами с подгонкой сопротивления. Конструкции подгоняемых резисторов с плавной подгонкой сопротивления изображены на рис. 4.3.
Применяют «плавную» и ступенчатую подгонку сопротивлений резисторов. Понятие «плавная» подгонка в определённой степени условное, так как ак-
13
ты воздействия на резистор для изменения его сопротивления вынужденно сопровождаются определённой паузой (выдержкой) перед контролем изменённого значения. Плавную подгонку сопротивления тонкопленочных резисторов осуществляют изменяя удельное поверхностное сопротивление плёнки (R□). Для этого применяется термическое, химическое или механическое воздействие на резистивную плёнку, при котором преобладает один из механизмов влияния:
–упорядочение структуры плёнки и снижение R□;
–окисление пленки и увеличение R□.
Распространённым способом плавной подгонки является изменение формы и размеров резистивной полосы механическим, термическим или электроискровым удалением части резистивного материала.
Для такой подгонки предусматривается увеличение ширины и длины резистивной полосы или в конструкцию резистивной полосы вводятся специальные расширенные подгоночные зоны. Плавная подгонка изменением размеров и формы проводящей области выполняется в сторону увеличения сопротивления (рис. 4.3, а...е). При плавной подгонке обеспечивается снижение отклонения сопротивления до значений сравнимых с температурными и временными изменениями (сотые доли процента).
Для целей подгонки используют воздушно-абразивную или лазерную технологию. Сопротивление при этом может изменяться только в сторону увеличения, поэтому при проектировании резисторов предусматривают отрицательный допуск сопротивлений относительно номинальных значений. Воздушно-абразивная подгонка проводится на установке, в которой струя воздуха, содержащая абразивный порошок, через сопло направляется на подгоняемый резистор и производит его фрезерование (см. рис. 4.3, а, б). Недостаток способа заключается в повреждении абразивными частицами соседних элементов; кроме того, в процессе подгонки разрушается верхний слой резистора, в основном состоящий из стекла и являющийся защитой от климатических воздействий. Процесс такой подгонки сопровождается выделением пыли.
При термической (лазерной) подгонке грубую подгонку выполняют выжиганием пленки поперек резистора. Изменение сопротивления в этом случае происходит с возрастающим по зако-
14
ну гиперболы вкладом и соответственно нарастающей погрешностью. Выжигание материала вдоль резистора (по направлению протекания тока) изменяет сопротивление по линейному закону в зависимости от длины участка выжигания с коэффициентом пропорциональности, зависящим от ширины резистивной полосы, при которой поперечное (грубое) выжигание материала прекращено.
При лазерной подгонке толстопленочных резисторов поврежденные участки резистора закрываются расплавленным стеклом. Для получения качественного реза важно подобрать режимы работы установки. Большая часть мощности лазерного излучения должна расходоваться на испарение резистивного материала. В противном случае при охлаждении после подгонки вокруг лазерного реза образуется множество микротрещин, которые приводят к снижению стабильности сопротивления резистора.
Процесс подгонки толстопленочных резисторов не отличается от подгонки (плавной) тонкопленочных резисторов. Разброс сопротивлений толстоплёночных резисторов после вжигания составляет 30...40 % вследствие изменения параметров подложек в партии, погрешности оснастки, используемой при нанесении, отклонений в поддержании режимов вжигания и целого ряда других факторов. Если все резисторы на подложке имеют отклонения сопротивлений в одну сторону, может быть проведена групповая подгонка путем повторного вжигания. При этом происходит уменьшение сопротивлений. Низкая точность групповой подгонки не позволяет полностью отказаться от индивидуальной подгонки каждого резистора.
Для ступенчатой подгонки сопротивления в конструкциях резисторов предусматриваются металлические перемычки в подгоночных секциях. Сопротивление изменяется образованием или разрушением перемычек в подгоночных секциях. В конструкциях резисторов, изображённых на рисунках 4.4, а, б, в, к сопротивлению основного резистора добавляют сопротивление секций с постоянным (см. рис. 4.4, б) или переменным (см. рис. 4.4, а, в) шагом. В конструкции резистора, изображённой на рис. 4.4, г, применяемой при подгонке сопротивлений низкоомных резисторов, сопротивление подгоночной секции увеличивается за счет уменьшения количества шунтов.
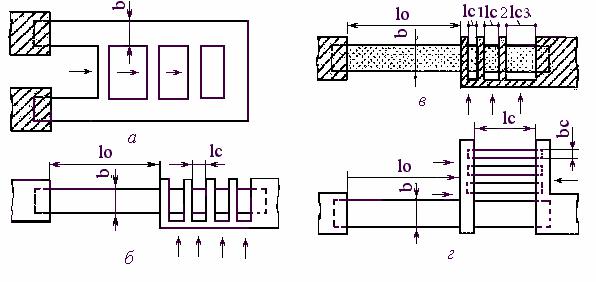
15
Рисунок 4.4
Качество ступенчатой подгонки зависит от технологического отклонения поверхностного сопротивления (δR□), так как в резисторах со ступенчатой подгонкой число контактных переходов «проводник-резистивная плёнка», повышающих вносимую погрешность сопротивления, увеличивается с повышением планируемой точности подгонки. Минимальная погрешность сопротивления при ступенчатой подгонке пропорциональна (δR□)2 и для ГИМС превышает 0,5 %.
При лужении проводников толстопленочной микросхемы изменяются и сопротивления резисторов на 1...2 % в зависимости от материала резистивной пасты и ее удельного сопротивления. Поэтому точная подгонка прецизионных толстопленочных резисторов должна проводиться после лужения проводников.
4.3.2 Функциональные параметры резисторов ГИС
Функциональными параметрами плёночных конструкций резисторов, как элементов электрических схем, являются:
–номинальное сопротивление резистора, R;
–допустимое отклонение сопротивления резистора, dR;
–допустимое эксплуатационное отклонение сопротивления, dRэ;
–допустимая мощность рассеяния, Р
–верхняя граничная частота резистора, Fгр.
16
Имея аналогичными ряд параметров с полупроводниковыми, плёночные резисторы обретают определённую специфику, связанную с плёночной технологией исполнения. Специфичность проявляется:
–в отсутствии ограничений на рабочие напряжения, кроме связанных с допустимой величиной мощности рассеяния резисторов;
–относительно низкая теплопроводность несущих диэлектрических подложек обуславливает потребность учёта требований к мощности резистора в индивидуальном порядке;
–в отличии конструкций контактных областей к резистору;
–в возможности и доступности корректировки сопротивления резисторов после формирования топологических конфигураций;
–в «размытости» ёмкостных эффектов конструкции плёночных резисторов;
–в «технологических ограничениях» на форму и размеры резисторов в связи с возможностями трафаретных технологий формообразования топологических конфигураций.
К проектированию резисторов (одного или массива) формируются три группы исходных ограничений:
–на параметры функционального назначения резисторов;
–допусковые ограничения технологии производства рези-
сторов;
–допусковые отклонения параметров в процессе эксплуатации резисторов.
Согласование названных ограничений реализуется в выпуске информационных документов, по которым осуществляется производство, контроль, приёмка и последующая эксплуатация изделия.
Последняя группа ограничений учитывается рациональным выбором материалов конструкций и мерами по стабилизации свойств конструкции в процессе ее проектирование, производства и эксплуатации. Для рационального выбора материалов необходим справочный материал по совокупности определяющих параметров, а по мерам стабилизации свойств необходим плохо формализуемый опыт работы. Определяющими параметрами материалов для перечисленных функциональных параметров резисторов являются:
17
–сопротивление квадрата плёнки R□, Ом;
–удельная мощность рассеяния Руд, Вт/см2;
–удельное переходное сопротивление контактной пары «резистив-проводник» Ro, Ом∙см2;
–диэлектрическая проницаемость материала платы п;
–диэлектрические потери материала платы tgδ;
–удельное объёмное сопротивление материала платы ρ,
Ом∙см.
Проектные расчёты опираются на учёт трёх первых из названных параметров материалов. Три последних параметра учитываются в предельных оценках. Точный их учёт затруднён и характеризуется значительной неопределённостью.
При выборе форм и размеров конструкций резисторов учёту подлежат следующие технологические ограничения:
–относительное производственное отклонение удельного поверхностного сопротивления δ R□;
–абсолютная погрешность линейного размера ∆L, ∆b по одной стороне топологического фрагмента;
–абсолютная погрешность совмещения (∆совм) топологических элементов в смежных слоях;
–допустимые формы и отношения размеров.
4.3.3 Материалы тонкоплёночных резисторов
Как отмечалось ранее, в зависимости от толщины плёнок микросхемы резисторы классифицируются как тонко- и толстоплёночные. Различны и материалы, применяемые для исполнения тонко- и толстоплёночных резисторов. В части агрегатного состояния материалы тонкоплёночных резисторов являются твёрдыми телами, которые в процессе формирования плёнок подвергаются термическому плавлению с последующим испарением в газообразное состояние и осаждением на подготовленные твёрдые основания (подложки и платы). В процессах катодного, анодного, высокочастотного распыления удаётся исключить высокотемпературные процессы испарения и транспортировать для осаждения на платах атомарные и молекулярные частицы твёрдого вещества.
18
В качестве резистивных материалов тонкопленочных резисторов используют чистые металлы и сплавы с высоким электрическим сопротивлением, а также специальные резистивные материалы — керметы, которые состоят из частиц металла и диэлектрика (например, Сг и SiO). Широко распространены пленки хрома и тантала. Сплавы имеют большее значение R□ по сравнению с пленками чистых металлов. На основе керметов получают высокоомные резисторы. Наиболее распространен кермет, в состав которого входят хром и моноокись кремния 50...90 % Сг, 50...10 % SiO. В зависимости от содержания хрома можно получить резистивные пленки с R□ = 100...10 000 Ом, обладающие высокой стабильностью. В табл. 4.3 приведены параметры ряда резистивных металлосилицидных составов, применяемых для изготовления резистивных плёнок.
Таблица 4.3 — Параметры резистивных металлосилицидных сплавов
Марка сплава |
R□, Ом |
ТКС, ( t) |
Ро, |
c, |
10–4, К–1 |
Вт/см2 |
10–5, 1/час |
||
РС-5006 |
3–20 |
0,5 |
5 |
2 |
РС-5402 |
5–100 |
0,5 |
2 |
1 |
РС-5406К |
10–500 |
0,5 |
2 |
1 |
РС-5406Н |
50–500 |
0,3 |
2 |
1 |
РС-3710 |
50–3000 |
1 |
5 |
0,5 |
РС-4800 |
100–1000 |
2 |
5 |
1 |
РС-1714 |
300–500 |
2 |
5 |
1 |
РС-4206 |
103 |
0,5 |
2 |
0,5 |
РС-4400 |
(1–5)103 |
3 |
10 |
1 |
РС-1004 |
(3–50)103 |
15 |
5 |
2 |
РС-2310 |
(1–8)103 |
12 |
5 |
2 |
РС-2005 |
(8–50)103 |
12 |
5 |
2 |
|
|
|
|
|
В связи с тем, что свойства керметных пленок в сильной степени зависят от технологических факторов, резисторы имеют худшую воспроизводимость номиналов и больший ТКС по сравнению с металлическими. В настоящее время промышленностью освоена большая группа металлосилицидных сплавов системы Сг-Si, легированных небольшими добавками железа, никеля, кобальта, вольфрама (РС-3001, РС-3710, РС-5604К, МЛТ-ЗМ,
19
РС-5406Н). При сравнительно малом ТКС и высокой воспроизводимости удельных поверхностных сопротивлений диапазон номиналов сплавов РС достаточно широк: R□ = 0,05...50 кОм.
Наиболее часто используют сплавы РС-3001, РС-3710 (37,9 % Сг, 9,4 % N1, 52,7 % Si), МЛТ-ЗМ (43,6 % Si, 17,6 % Сг, 14,1 % Fе, 24,7 % W). Параметры ряда распространённых тонкоплёночных резистивных материалов, в дополнение к приведенным в табл. 4.3, представлены в табл. 4.4.
Таблица 4.4 — Параметры материалов тонких резистивных плёнок
|
Материал |
R□, |
Диапазон, |
Ро, |
|
ТКС, |
Материал плёнки |
контактных |
Ом |
2 |
10–4 |
||
|
площадок |
Ом |
|
Вт/см |
|
К–1 |
Нихром, проволока, |
Медь лужёная |
300 |
2 |
2 |
|
1 |
Х20Н80, 0,3–0,8 |
|
|
|
|
|
|
мм (ГОСТ 12766-67) |
|
|
|
|
|
|
Нихром, проволока, |
Золото — под- |
10 |
(100 –104) |
2 |
|
–2,3 |
(ГОСТ 8803-58) |
слой хрома |
50 |
5∙(100 – |
|
|
|
|
|
|
104 |
|
|
|
Сплав МЛТ-3М |
Медь лужёная — |
500 |
5∙(100 –104) |
2 |
|
2 |
(бКО.028.005 ТУ) |
подслой ванадия |
|
|
|
|
|
|
Медь (защита |
|
|
|
|
|
|
никель) — под- |
|
|
|
|
|
|
слой нихрома |
|
|
|
|
|
Хром (ГОСТ 5905- |
Медь лужёная |
500 |
50–3∙103 |
1 |
|
0,6 |
67) |
|
|
|
|
|
|
Кермет К-50С |
Золото — под- |
3∙103 |
103–104 |
|
|
3 |
(ЕТО.021.013.ТУ) |
слой хрома (ни- |
5∙103 |
|
2 |
|
–4 |
|
хрома) |
103 |
|
|
|
–5 |
|
Алюминий — |
20– |
102–104 |
3 |
|
–2 |
Тантал ТВЧ, лента, |
слой ванадия |
100 |
|
|
|
|
толщина 0,3–3 мм |
|
|
|
|
|
|
(РЭТУ 1244 -67) |
Медь лужёная — |
100 |
5∙102–105 |
3 |
|
–2 |
|
подслой нихрома |
|
|
|
|
|
|
Тантал |
10 |
101–1,5∙104 |
3 |
|
–2 |
Сплав РС 3001 |
Золото — под- |
103 |
102 – 5∙104 |
3 |
|
–0,2 |
(ЕТО.021.019.ТУ) |
слой хрома (ни- |
2∙103 |
2∙102–105 |
|
|
|
|
хрома) |
|
|
|
|
|