
методички 2 курс ПБ / Каф. мех. и инж. графики / Детали машин
.pdf
51
Таблица 4.4
aω, мм |
80 |
100 |
125 |
140 |
160 |
180 |
200 |
225 |
250 |
280 |
|
|
|
|
|
|
|
|
|
|
|
А, м2 |
0,19 |
0,24 |
0,36 |
0,43 |
0,54 |
0,67 |
0,8 |
1,0 |
1,2 |
1,4 |
|
|
|
|
|
|
|
|
|
|
|
ψ – коэффициент, учитывающий отвод тепла через основание; для сталь-
ной или чугунной поверхности установки редуктора ψ =0,3, для бетона ψ = 0. [tM] - допускаемая температура масла. Для обычных редукторных масел
[tM] = 80 – 90 oС. Если tM > [tM], то применяют искусственное охлаждение,
устанавливая на червяк обдуваемый вентилятор. Тем самым повышается коэф-
фициент теплоотдачи KT.
Пример расчета.
Исходные данные: крутящий момент на колесе Тт = 700Нм, угловая ско-
рость на валу колеса ωТ = 4,73 с-1, число оборотов nт = 45,2 об/мин, передаточ-
ное число U = 20, мощность на червяке Рб = 4,2 кВт.
Выбираем материал червяка согласно таблице приложения 6.
Сталь 40Х.
Определяем ожидаемую скорость скольжения по формуле (4.1):
Vs' 4,3 Т U 3 ТT 4,3 4,73 213700 3,065(м/с); 103 103
Выбираем материал колеса в зависимости от скорости скольжения со-
гласно таблице приложения 14. Скорость скольжения 3 м/с, по таблице видно,
что это материал II группы.
Марка материала – БрА9ЖЗЛ;
Способ отливки – в землю;
Предел прочности σв = 392 МПа;
Предел текучести σТ = 200 МПа;
Допускаемые напряжения при изгибе [σ0]и = 100 МПа.
Находим допускаемое контактное напряжение червячного колеса:
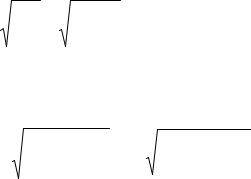
52
Для колес из оловянной бронзы при шлифованных и полированных чер-
вяках с твердостью поверхности витков >НВ420 по формуле 4.2: [σ]Н2 = 0.9·σВ2 ·КHL=0,9∙392∙0,79 = 279 (МПа),
где σВ2 и σT2 - соответственно предел прочности и текучести материала
(приложение 13);
КHL - коэффициент долговечности определяют по формуле:
КHL = (107 / NHE2)1/8 = 0,79,
где NHE2 - эквивалентное число циклов напряжения червячного колеса
NHE2 = 60∙С∙nт=60∙24000∙45,2= 6,5∙107
где С – срок службы привода.
Для заданных условий работы принимаем С = 24000 часов. Коэф-
фициент долговечности для червячной передачи находится в рекомендованных пределах – (0.67 … 1.15).
[σ]Н2=279≤ 4σT2 = 200∙4=800 (МПа) – условие выполняется.
Находим допускаемое контактное напряжение на изгиб по формуле (4.5). [σ ]F2 = (0,08σв + 0,25σт)КFL,
где КFL – коэффициент долговечности при расчёте на изгиб. По формуле
(4.6): КFL =9 |
106 |
9 |
106 |
=1,5. |
|
Т |
24000 |
||||
|
|
|
[σ ]F2 = (0,08∙392+0,25∙200) ∙1,5=122,04 (МПа).
Определяем межосевое расстояние по формуле (4.7):
|
Т |
Т 103 1,1 |
61 |
700 103 |
1,1 |
||
а =61 |
[ ]2H |
2792 |
|
=130 (мм). По ГОСТу (табл.4.1) |
|||
3 |
|
|
|
3 |
|
|
|
|
|
|
|
|
|
|
принимаем а = 140 (мм).
Определяем число витков червяка Z1. Оно зависит от передаточного чис-
ла червячного редуктора. При U= 15…30 Z1 = 2. Предварительно число зубьев червячного колеса по формуле (4.8):
Z2 = Z1·U= 2∙20 = 40.
Находим модуль зацепления по формуле (4.9):
m = (1,4…1,7) а / Z2 = (1,5…1,7)140/ 40= 5…5,6 (мм). Примем m= 5(мм).
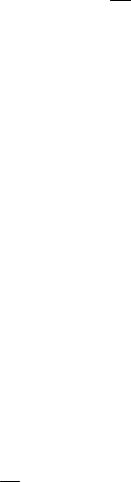
53
Определяем коэффициент диаметра червяка по формуле (4.10): q = 2 а /m - Z2 = 2∙140/5 - 40 (мм) = 16 (мм). Примем q = 16мм.
Уточняем межосевое расстояние:
а = 0,5m(q + Z2) = 0,5∙5(16+40) = 140 (мм).
Фактическое передаточное число:
Z
U 2 =40/2=20.
ф Z1
Расхождение с принятым не должно превышать 3%. В нашем случае рас-
хождение 0%.
Определяем геометрические размеры червячной передачи.
Основные размеры червяка.
Делительный диаметр: d1 = mq= 5∙16 = 80 (мм).
Диаметр вершин витков:
da1 = d1+2m = 80 + 2∙5 = 90 (мм).
Диаметр впадин витков:
df1 = d1-2,4m= 80 - 2,4∙5 = 68 (мм).
Начальный диаметр:
dw1 = m(q + 2x)= 5(16 + 0) = 80 (мм).
Угол подъёма витка червяка:
γ = arctg Z1 = 22º q
Длина нарезаемой части червяка:
b1 = (10 + 5,5|x| + Z1)m= (10 + 0 + 2 )5 = 60 (мм).
Основные размеры червячного колеса.
Делительный диаметр: d2 = mZ2 =5∙40 = 200 (мм).
Диаметр вершин зубьев:
da2 = d2+2m(1+х)=200 + 2∙5 = 210 (мм).
54
Диаметр впадин зубьев:
df2 = d2 - 2m(1,2-х) =200 - 2∙5 = 190 (мм).
Наибольший диаметр колеса:
d |
|
d |
|
|
6m |
= 210 + 6∙5/(2+2) = 222 (мм). |
aM 2 |
a2 |
|
||||
|
|
|
Z1 2 |
Ширина венца:
b2 = 0,355a при Z1 = 1 или 2; b2 = 0,315a при Z1 = 4. b2 = 0,355∙140 =50 (мм).
Условный угол обхвата червяка венцом колеса по формуле (4.24):
sin δ = |
|
b2 |
= |
50 |
= 0,57. Тогда δ = 34,80. |
|
da1 |
0,5m |
90 0,5 5 |
||||
|
|
|
Определяем фактическую скорость скольжения по формуле (4.26):
V |
s |
|
u тd1 |
|
|
20 4,73 40 |
=2,14 (м/с). |
||||||
2cos 103 |
2 cos22 103 |
||||||||||||
|
|
|
|
|
|
|
|
||||||
Тогда – угол трения |
φ=2 по таблице приложения 15. |
||||||||||||
Коэффициент полезного действия червячного редуктора по формуле |
|||||||||||||
(4.25): |
|
|
|
|
|
|
|
|
|
|
|
|
|
|
|
|
|
|
|
|
tg |
|
|
|
tg20 |
0,93. |
|
|
|
|
|
|
|
tg |
|
||||||
|
|
|
|
|
|
|
|
tg(20 2) |
Определяем силы в зацеплении червячной пары по формулам (4.27) – (4.29).
Окружная сила на червяке и осевая сила на колесе:
F |
F |
|
2T 10 |
3 |
|
2 22 103 |
|
Б |
|
= |
|
= 1100 (Н). |
|||
|
|
||||||
t1 |
a2 |
|
d1 |
|
|
40 |
|
|
|
|
|
|
|
Окружная сила на колесе и осевая на червяке:
F |
F |
|
2T 103 |
|
2 369.6 |
103 |
|
T |
= |
|
|
= 4400 (Н). |
|||
t2 |
a1 |
|
d2 |
|
168 |
|
|
|
|
|
|
|
|
Радиальная сила
Fr1 = Fr2 = Ft2tgα = 4,4·tg20 = 1600 (Н), где α = 20˚ - угол зацепления.

55
Проверочный расчёт передачи на контактную прочность. Условие кон-
тактной прочности червячной передачи по формуле (4.30):
|
|
|
170q |
|
H |
Z2 |
|||
|
|
3
Z /q 12 a TТ
3 |
KН |
|
170 16 |
|
40/16 1 3 |
|
3 |
|
||
10 |
|
|
|
|
|
|
700 10 |
|
1 225(МПа), |
|
40 |
|
140 |
|
|||||||
|
|
|
|
|
|
|
|
|
где KН – коэффициент нагрузки, принимаемый в зависимости от окруж-
ной скорости колеса: V |
2 |
|
d2nТ |
. |
|
||||
|
|
60 1000 |
V2 3,14 200 45.2 =0,6 (м/с). При V2 ≤ 3 (м/с) КН = 1. 60 1000
Так как 225<279МПа - условие выполняется.
Проверяем напряжение изгиба зубьев колеса.
Напряжение изгиба в зубьях червячного колеса по формуле (4.31):
F |
0,7YF2 |
Ft2 |
KF |
0,7 1,45 |
4400 |
1 17,86 |
(МПа), |
b m |
|
||||||
|
|
|
|
50 5 |
|
||
|
|
2 |
|
|
|
|
|
где
YF2 – коэффициент формы зуба, принимаемый в зависимости от эквива-
лентного числа зубьев колеса. Zv2 = Z2/cos3γ=40/cos22=40/0,8=50. Тогда
YF2=1,45 по таблице приложения 16.
KF = KH - коэффициент нагрузки; KF =1.
Так как 17,86 МПа < 122,04 МПа, то есть F 2 F 2 - условие прочности
на изгиб выполняется.
Проведем тепловой расчет редуктора.
Температура масла в редукторе по формуле (4.32):
tМ tO |
|
P (1 ) 103 |
20 |
4,2(1 0,93) 103 |
o |
Б |
|
||||
|
|
= 63,8( С), |
|||
KT A(1 ) |
12 0,43(1 0,3) |
где t0 - температура окружающей среды: t0 = 20oС; PБ – мощность на червяке, PБ = 4,2кВт ;
η - коэффициент полезного действия червячного редуктора, определен-
ный в п.4.3. η=0,93;
KT - коэффициент теплоотдачи. Примем KT = 12 Вт/м2;

56
А- площадь теплоотвода корпуса червячного редуктора, м2. Определяется по табл. 4.4. При межосевом расстоянии aω = 140мм А=0,43 м2;
ψ – коэффициент, учитывающий отвод тепла через основание; для сталь-
ной поверхности установки редуктора – рамы ψ =0,3.
Проведем сравнение полученной температуры с [tM] - допускаемой тем-
пературой масла. Для обычных редукторных масел [tM] = 80 – 90 oС.
Так как 63,8 oС < 80 oС, то есть, tM < [tM], то дополнительных мер по охлаждению червячного редуктора применять не следует.
5.Расчет ременной передачи
Вработе рекомендуется производить расчет клиноременной передачи на основании данных: условия эксплуатации, крутящий момент Т1, частота вра-
щения вала ведущего шкива n1, передаточное число ременной передачи U1-2.
Данные берутся из табл. 1.1.
5.1. Определяют сечение ремня в зависимости от крутящего момента на
ведущем шкиве по табл. 5.1.
Таблица 5.1
Минимальные значения диаметров шкивов для передачи наибольших
моментов
Обозначение сечения |
Крутящий момент Т1, Нм |
Минимально возможный |
ремня |
|
диаметр шкива D1min |
|
Нормальное сечение |
|
Z |
<30 |
63 |
A |
15…60 |
90 |
B |
50…150 |
125 |
C |
120…600 |
200 |
|
Узкое сечение |
|
SPZ |
<150 |
63 |
SPA |
90…400 |
90 |
SPB |
300…2000 |
140 |
SPC |
>1500 |
224 |
Стандартный ряд диаметров шкивов, мм: 63, 71, 80, 90, 100, 112, 125, 140, 160, 180, 200, 224, 250, 280, 315

57
5.2.Определяют минимально возможный диаметр ведущего шкива D1min
взависимости от сечения ремня по табл. 5.1. Для повышения эффективности работы передачи и сокращения числа ремней рекомендуется принимать в ка-
честве диаметра ведущего шкива D1 следующий стандартный размер после
значения D1min.
5.3. Диаметр ведомого шкива, мм с учетом относительного скольжения ремня по шкиву ε = 0,015:
D2 = D1U1-2 (1-0,015). |
(5.1) |
Принимают ближайшее стандартное значение диаметра шкива по таблице
5.1.
5.4. Определяют минимально возможное межосевое расстояние, мм:
amin 0,55 D1 |
D2 T0 , |
|
|
(5.2) |
||
где То– высота сечения ремня, мм. Принимается в зависимости от вы- |
||||||
бранного сечения ремня по приложению 17. |
|
|
|
|
|
|
5.5. Определяют максимальное значение межосевого расстояния, мм: |
|
|||||
amax D1 |
D2 . |
|
|
(5.3) |
||
Принимают межосевое расстояние a из промежутка amin< a <amax. |
|
|||||
5.6. Длина ремня, мм: |
|
|
|
|
|
|
L 2a 1,57 D D |
|
D2 |
D1 2 |
. |
(5.4) |
|
|
|
|||||
1 |
2 |
|
|
4a |
|
|
|
|
|
|
|
Округляют L до ближайшего стандартного значения (приложение 17).
5.7. Поскольку длина ремня была округлена до стандартной, необходимо пересчитать межосевое расстояние, мм:
a 0,25 L w |
|
, |
|
L w 2 2y |
(5.5) |

58
где |
|
|
|
w 1,57 D1 |
D2 ,мм; |
(5.6) |
|
y D D 2 |
мм2. |
(5.7) |
|
2 |
1 |
|
|
5.8. Определяют угол обхвата меньшего шкива, град:
1 |
180 57 |
D2 D1 |
. |
(5.8) |
|
||||
|
|
a |
|
Для клиноременных передач должно соблюдаться условие α1 >120o.
5.9. Определяют скорость ремня, м/с:
V |
n1D1 |
(м/с); |
(5.9) |
|
Р60 1000
5.10.Определяют необходимое для передачи заданной мощности число
ремней:
PC |
p , |
(5.10) |
Z 1 |
PoCLC CZ
где Ро – мощность, допускаемая для передачи одним ремнем, кВт:
Определяют по приложениям 17-18 в зависимости от сечения ремня,
диаметра D1,частоты вращения вала ведущего шкива n1.
CL – коэффициент, учитывающий влияние длины ремня. Определяют по отношению расчетной длины, принятой в пункте 5.6, к базовой L/L0. Базовая длина, мм дана в приложениях 17-18 в скобках после сечения ремня;
Cα – коэффициент, учитывающий угол обхвата;
CZ – коэффициент, учитывающий число ремней в передаче. Предвари-
тельно число ремней в передаче определяется отношением P1/P0; Cр – коэффициент динамичности нагрузки.
Численные значения коэффициентов даны в приложении 20.
Если Z > 8; то следует перейти к следующему сечению ремня или
увеличить диаметр ведущего шкива D1.
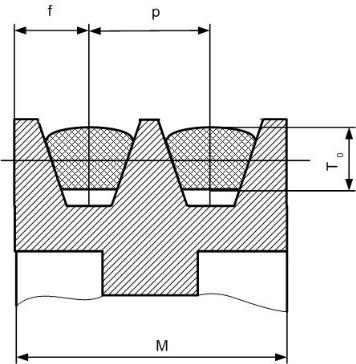
59
5.11. Определяют силу, действующую на валы, Н:
F |
|
2F Zsin |
|
, |
(5.12) |
p |
|
||||
|
o |
2 |
|
|
|
|
|
|
|
|
где Fo – предварительное натяжение ветвей ремня, Н;
F |
850P1CpCL |
V |
2 |
; |
(5.13) |
|
Р |
||||
0 |
ZVРC |
|
|
||
|
|
|
|
θ – коэффициент влияния натяжения от центробежной силы. Определяют по таблице приложения 20.
5.12. Шкив для клиноременной передачи рекомендуется изготовлять из чугуна Сч15 и Сч18. При скоростях свыше 30 м/с - из стали 25 Л или алюми-
ниевых сплавов. Конфигурация обода шкива и размеры канавок приведены в таблице в приложении 24. Шкивы диаметры до 300 - 400 мм выполняются дис-
ковыми, свыше 400 мм - со спицами.
Вычисляют основные конструктивные размеры шкива (см. рис.5.2).
Ширина венца шкива М = (Z-1)p + 2f. Толщина обода δо = 1,2 Т0. Толщи-
на ступицы с = 1,2 δо. Значения p, f, T0 принимаются по таблице 17 приложения.
Рис. 5.2. Шкив
По завершении расчетов заполняют таблицу.
60
|
|
Таблица 5.2 |
|
|
|
параметр |
обозначение |
величина |
|
|
|
Тип ремня |
- |
|
|
|
|
Диаметр ведущего шкива, мм |
D1 |
|
|
|
|
Диаметр ведомого шкива, мм |
D2 |
|
|
|
|
Передаточное число |
U1-2 |
|
|
|
|
Межосевое расстояние, мм |
a |
|
|
|
|
Длина ремня, мм |
L |
|
|
|
|
Число ремней |
Z |
|
|
|
|
Сила, действующая на валы, Н |
Fp |
|
|
|
|
Пример расчета.
Исходные данные: мощность на ведущем валу Р1 = 6 кВт; число оборотов ведущего вала n1 = 953 об/мин; передаточное число Uр = 2; крутящий момент Т1 = 60 Нм.
Выбираем сечения ремня:
При Т1 = 60 Нм выбираем ремень сечения B ГОСТ 1284-89 по таблице
5.1. Ремень имеет параметры (по приложению 17): h = 10,5 мм – высота ремня;
q = 0,18 кг – масса 1 м длины ремня; D1min = 125 мм.
Увеличиваем диаметр меньшего шкива, руководствуясь размерами табл.5.1, на два размера.
Примем диаметр меньшего шкива D1 = 160 мм.
Определяем диаметр большего шкива по формуле (5.1): D2 = D1·Up·(1- ), где
относительное скольжение = 0,015; D2 = 160·5·0,985 = 315,2 (мм).
Примем D2 = 315 мм (приложение 22).