
- •ЦЕЛЬ И ЗАДАЧИ КУРСОВОГО ПРОЕКТА
- •ОБЪЁМ И СОДЕРЖАНИЕ КУРСОВОГО ПРОЕКТА
- •ЗАДАНИЕ НА КУРСОВОЙ ПРОЕКТ
- •ТРЕБОВАНИЯ К ОФОРМЛЕНИЮ КУРСОВОГО ПРОЕКТА
- •ВВЕДЕНИЕ
- •1. АНАЛИЗ КОНСТРУКЦИЙ СТАНКОВ АНАЛОГИЧНОГО НАЗНАЧЕНИЯ ПО ЛИТЕРАТУРНЫМ И ПАТЕНТНЫМ ИСТОЧНИКАМ, А ТАКЖЕ ОБОСНОВАНИЕ ТЕХНИЧЕСКОГО СОВЕРШЕНСТВОВАНИЯ СТАНКА
- •2. ТЕХНИЧЕСКОЕ ЗАДАНИЕ НА ПРОЕКТИРОВАНИЕ (МОДЕРНИЗАЦИЮ) ОБОРУДОВАНИЯ
- •3. РАЗРАБОТКА ПРИНЦИПИАЛЬНЫХ СХЕМ, ВЫБОР СИСТЕМЫ УПРАВЛЕНИЯ И ПРИВОДОВ
- •Касательная составляющая силы резания определяется по зависимости, Н
- •4. РАСЧЁТЫ И ОПИСАНИЕ КОНСТРУКЦИИ ФУНКЦИОНАЛЬНОГО МЕХАНИЗМА
- •4.1 ПРОЕКТИРОВАНИЕ МЕХАНИЗМА РЕЗАНИЯ
- •4.2 ПРОЕКТИРОВАНИЕ МЕХАНИЗМА ПОДАЧИ
- •4.3 ОБЩИЕ ИНЖЕНЕРНЫЕ РАСЧЕТЫ
- •4.4. РАСЧЁТЫ НА ПРОЧНОСТЬ, ЖЁСТКОСТЬ И ВИБРОУСТОЙЧИВОСТЬ
- •4.4.1. ОБЩИЕ ПОЛОЖЕНИЯ
- •4.4.2. УКАЗАНИЯ К РАСЧЁТУ ВАЛОВ И ШПИНДЕЛЕЙ
- •4.4.3. РАСЧЁТ ВАЛОВ И ШПИНДЕЛЕЙ НА ПРОЧНОСТЬ.
- •4.4.4. РАСЧЕТ ВАЛОВ И ШПИНДЕЛЕЙ НА ЖЕСТКОСТЬ (НА ПРОГИБ).
- •5. РАЗРАБОТКА ЧЕРТЕЖА ОБЩЕГО ВИДА ОБОРУДОВАНИЯ
- •ЗАКЛЮЧЕНИЕ
- •БИБЛИОГРАФИЧЕСКИЙ СПИСОК
- •ПРИЛОЖЕНИЯ
На кинематической схеме (рис.3.4): 1, 9- электромотор; 2, 3- ступенчатый шкив; 4- редуктор; 5, 6, 7, 8, 17, 18 - цепная передача; 10, 11клиноременная передача; 13, 15передача винт-гайка; 14, 16передача винт-гайка; 19, 20червячная передача; 21, 22передача винт-гайка;
Если в качестве привода исполнительного механизма принят гидродвигатель или пневмодвигатель, далее приступают к разработке гидравлической или принципиальной пневматической схемы. При разработке гидропривода следует принимать стандартные гидроаппараты и унифицированные схемы их включения. Методика разработки принципиальных гидравлических схем изложена в [3]. Окончательно откорректированную и правильно составленную принципиальную гидравлическую или пневматическую схему вычерчивают на первом листе графической, части проекта. Пример оформления схемы дан на рис.3.5.
4. РАСЧЁТЫ И ОПИСАНИЕ КОНСТРУКЦИИ ФУНКЦИОНАЛЬНОГО МЕХАНИЗМА
В зависимости от темы проекта устанавливают наиболее важный механизм проектируемого оборудования. Такими механизмами могут быть: узел резания, механизм подачи, прижимное устройство, суппорт настройки, оградительное устройство, загрузчик, конвейер и т.п.
4.1 ПРОЕКТИРОВАНИЕ МЕХАНИЗМА РЕЗАНИЯ
Механизмы резания современных станков весьма разнообразны в конструктивном отношении. В их состав входят валы, опоры валов, устройствадля крепления инструментов и другие. При конструктивной разработке механизмов резания необходимо обосновать конструкцию опорных узлов (подшипников), дать чертежи механизма резания проектируемого станка, указать необходимые его размеры и технические условия, привести спецификацию деталей. Примеры оформления механизмов резания станков показаны на рис. 4.1 и 4.2. При наличии в станке нескольких различных механизмов резания детальную разработку дать по одному механизму, а для других указать основные параметры.
27
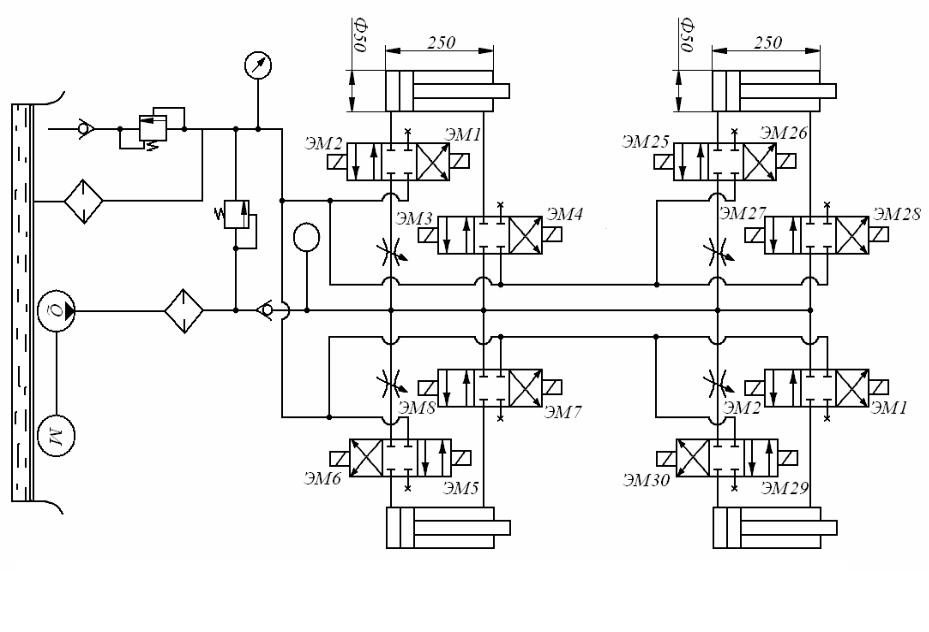
28
Рис. 3.5 Гидравлическая схема управления станка (пример оформления): М-мотор; Q-насос
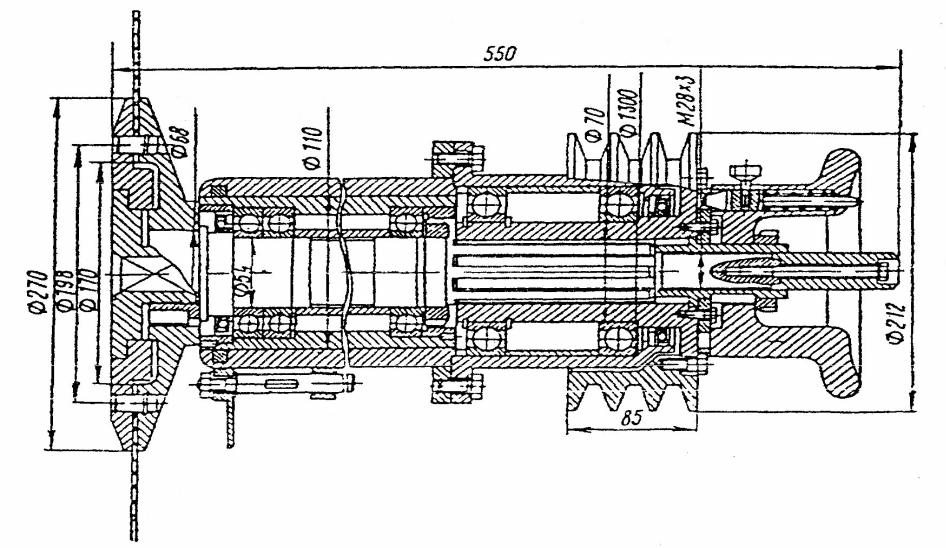
29
Рис. 4.1 Механизм резания круглопильного станка (пример оформления чертежа)
29
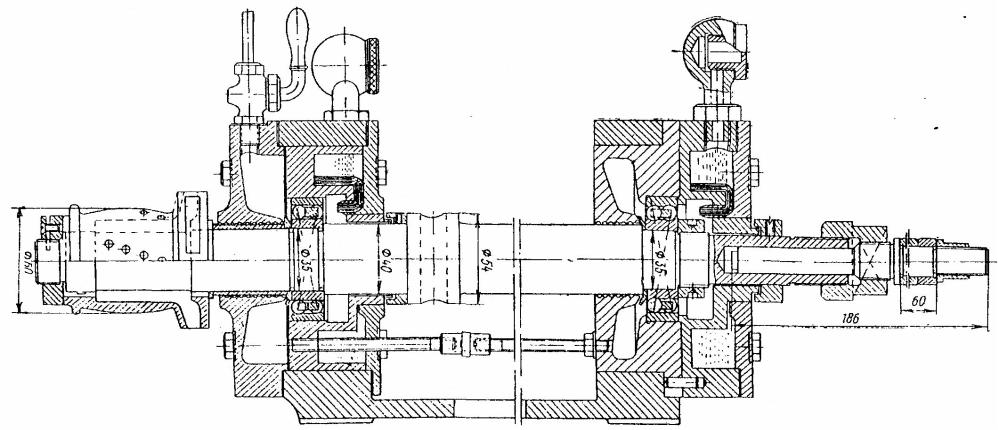
30
Рис. 4.2 Механизм резания фрезерного станка( пример оформления)
30
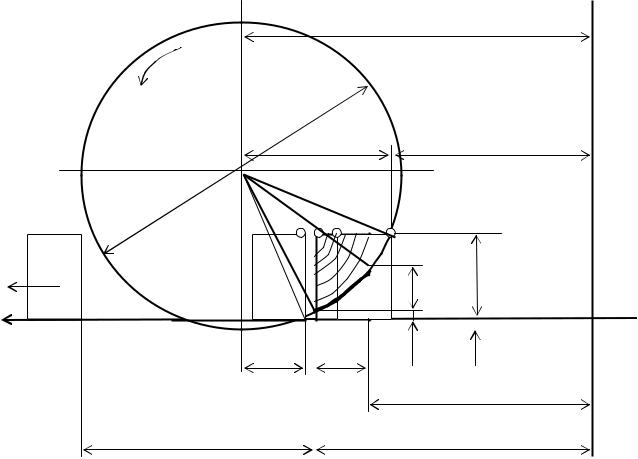
Математическая модель процесса обработки включает в себя алгоритм поиска состояний рабочих органов и расчет параметров резания в некоторые дискретные моменты времени обработки партии деталей.
Введем следующие обозначения .
ν 3 |
Χ
S
bh |
u1 |
3 |
4 |
2 |
1 |
|
D |
|
|
|
tsl |
|
|
|
dt |
|
|
|
|
|
|
|
|
|
|
|
0 |
|
|
|
ht |
|
|
|
|
bw |
Ld |
|
hw |
||
|
|
|||||
|
|
|
|
XK |
||
Lr |
|
|
XH |
Рис. 4.3 Схема взаимодействия рабочего органа с деталью
Ld=150 ,Lr-50- размер (длина или ширина) детали и промежуток между деталями в направлении подачи;
XH=1000 ,XK=850координата переднего и заднего конца детали относительно системы координат станка, XK=XH-Ld;
S=1200координата рабочего органа;
tsl=200толщина обработки (снимаемого слоя); D=600диаметр резания;
bw=800расстояние по горизонтали от оси рабочего органа до точки контакта зуба с нижней поверхностью детали;
31
bh=250тоже с верхней поверхностью детали;
hw=50 - выступ зубьев рабочего органа над поверхностью детали; Расчетными параметрами являются:
isсостояние рабочего органа, определяемое координатой передней и задней кромки детали;
u1,u2,u3,u4координаты характерных точек контакта резцов с деталью; htтекущее значение выступа рабочего органа при срезе
неполномерных стружек;
dtфактическая текущая толщина обработки (снимаемого слоя). Поиск состояния рабочего органа выполняется по следующему алго-
ритму, реализованному на языке TURBO-BASIC.
С целью выявления оптимальных режимов распиловки, рассмотрены исследования конструктивно-технологических параметров [14, 15, 16, 17] в результате которых было установлено, что толщина ленточной пилы должна удовлетворять зависимости [16]
S =(0,0007 −0,001)D , |
(4.1) |
где D-диаметр шкивов, мм.
Максимальная толщина ленточной пилы обуславливается величиной напряжений, испытываемых ею в процессе работы:
а) от центробежных сил; б) от изгиба ленты на шкивах;
в) в результате предварительного натяжения; г) от сил сопротивления резанию , теплового воздействия и др.
С учетом данной зависимости установлены параметры пил для ленточнопильных станков [16], представленные в табл. 4.1 (ГОСТ 10070-83).
32
|
|
|
Таблица 4.1 |
|
Размеры пил для распиловки бревен ГОСТ 10070-83 |
||||
|
|
|
|
|
Ширина (с зубьями)В, мм |
Толщина S,мм |
Шаг зуба t,мм |
ДлинаL |
|
|
|
|
(кратная),м |
|
|
|
|
|
|
20 |
1,4; 1,6 |
50;60 |
10,4 |
|
50 |
1,6; 1,8; 2 |
60 |
12,2 |
|
70 |
2; 2,2 |
80 |
14,6 |
|
70 |
1,8; 2; 2,2 |
60 |
14,6 |
|
|
|
|
|
|
Напряжение от изгиба ленты на шкивах в общем балансе напряжений, испытываемых ею в процессе работы, имеет большое удельное значение и является функцией от толщины ленты S и диаметра пильных шкивов D.
На нижней стороне ленты в результате изгиба – растягивающие напряжения, на внутренней – сжимающие.
Напряжение от изгиба ленты на шкивах выражается следующим образом [16]:
σ = Е |
S |
, |
(4.2) |
|
D |
||||
|
|
|
где Е–модуль упругости, Н/мм2.
Из формулы (4.1) видно, что напряжение от изгиба ленты прямо пропорционально толщине пилы и обратно пропорционально диаметру шкивов. Следовательно, для снижения напряжения с конструктивной точки зрения необходимо либо увеличить диаметр шкивов, либо уменьшить толщину ленточной пилы. Однако снижение толщины возможно до определенной величины, обеспечивающей ее прочность при пилении.
Приняв для стали Е=const=200 кН/мм2 и σ =300 Н/мм2, определим из выражения (4.1) величину S для минимального диаметра шкива D=500 мм при которой обеспечивается достаточная прочность пилы. Расчет показал, что исходя из условия обеспечения достаточной прочности, толщина пилы не
33
должна быть менее 0,75 мм.
Временное сопротивление на разрыв ленты в спаянном месте не превосходит 700 – 800 Н/мм2, а общее сопротивление на разрыв не должно превышать 300 – 400 Н/мм2 при минимальном запасе прочности К=2. Из условия обеспечения достаточной прочности σ ≤ [σ], т.е σ≤300 Н/мм2 [44].
В табл. 4.2 представлены расчетные значения толщин ленточных пил в зависимости от диаметра шкивов.
Таблица 4.2 Расчетные значения толщин ленточных пил в зависимости от диаметра
шкивов
D, мм |
500 |
600 |
700 |
800 |
900 |
1000 |
1100 |
1200 |
1300 |
1400 |
1500 |
1600 |
1700 |
1800 |
1900 |
2000 |
2100 |
|
|
|
|
|
|
|
|
|
|
|
|
|
|
|
|
|
|
|
|
|
|
|
|
|
|
|
|
|
|
|
|
|
|
|
|
S, мм |
0,75 |
0,9 |
1,05 |
1,2 |
1,35 |
1,5 |
1,65 |
1,8 |
1,95 |
2,1 |
2,25 |
2,40 |
2,45 |
2,6 |
2,75 |
2,90 |
3,05 |
|
|
|
|
|
|
|
|
|
|
|
|
|
|
|
|
|
|
|
|
|
|
|
|
|
|
|
|
|
|
|
|
|
|
|
|
Для номинального диаметра шкивов используемого в ленточнопильных станках (600 – 700 мм) толщина ленты должна быть в пределах 0,9 – 1,05 мм, что больше расчетной величины равной 0,75 мм. Для использования шкивов меньшего диаметра толщина пилы уменьшается и с учетом прочностных характеристик будет работать на пределе. Поэтому, шкивы диаметром менее 500 мм не рекомендуются, а толщина ленты менее 0,75 мм недопустима, так как не может обеспечить нормальную работу станка.
В табл. 4.3 приведены размеры зубьев ленточных пил для распиловки
бревен ГОСТ 10670–83. |
|
|
|
Радиус кривизны ρ линии пропила зависит от величины развода |
и |
||
ширины пилы В [16] |
|
|
|
|
0,12В2 |
|
|
ρ ≈ |
|
. |
(4.3) |
|
34

|
|
|
Таблица 4.3 |
|
Размеры зубьев ленточных пил для распиловки бревен |
||||
|
ГОСТ 10670–83 |
|
|
|
|
|
|
|
|
Шаг зубьев t , мм |
Высота зубьев h , мм |
|
Радиус закругления |
|
|
|
|
впадины r, мм |
|
50 |
16 |
|
5 |
|
60 |
18 |
|
6 |
|
80 |
24 |
|
8 |
|
|
|
|
|
|
Шаг зубьев выбирается из условия обеспечения достаточной емкости межзубовых впадин и заданной шероховатости получаемых пиломатериалов. Для этого следует пользоваться зависимостью [16]
5hmax Uz ≤ t ≤ Uz |
60v |
, |
(4.4) |
|
U |
|
|
где hmax– максимальная высота пропила, мм; Uz– подача на зуб, принимается по допустимой шероховатости поверхности материалов; v – скорость резания , м/с; U – скорость подачи , м/мин, t – шаг зубьев.
Высота зуба определяется из выражения [16]
h = (0,5 −0,6)t . |
(4.5) |
Анализируя выражения (4.4) и (4.5), можно заключить, что геометрические параметры пилы, а именно шаг зубьев и высота зуба напрямую зависят от скорости подачи на зуб Uz, которая принимается по допустимой шероховатости поверхности материалов. При постоянной скорости пиления величина Uz является константой. Следующим моментом анализа является изучение углов резания зубьев в зависимости от механических свойств распиливаемой древесины, которые определяют силы сопротивления резанию.
Профиль зубьев делительных и бревнопильных пил может быть с прямой спинкой (а), с прямой впадиной (б) с выпуклой спинкой (в) рис. 4.4.
35
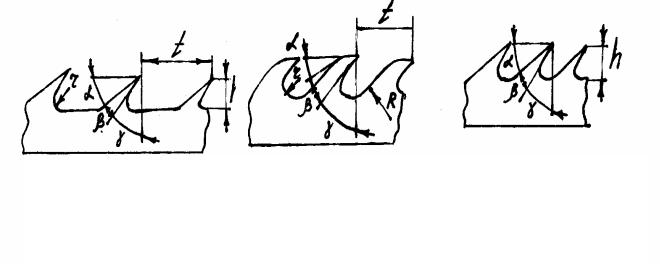
а |
б |
в |
Рис. 4.4 Форма и параметры зубьев ленточных пил:
а– спрямойспинкой; б– спрямойвпадиной; в– свыпуклойспинкой
Угол заострения зубьев делительных ленточных пил следует выдерживать в пределах 40 – 550 в зависимости от твердости древесины.
В табл. 4.4 приведены рекомендуемые практикой значения углов резания зубьев в зависимости от механических свойств распиливаемой древесины
[17].
|
|
|
|
|
Таблица 4.4 |
||
Угловыезначения профилей зубьев делительных и бревнопильных |
|||||||
|
|
ленточных пил |
|
|
|
||
|
|
|
|
|
|
|
|
Профиль зуба |
Угловые значения, град. |
Примечания |
|
||||
|
|
|
|
|
|||
γ |
β |
α |
δ |
||||
|
|
|
|||||
|
|
|
|
|
|
|
|
|
|
|
|
|
Для твердых |
|
|
С прямой впадиной |
25–15 |
45–55 |
20 |
65–75 |
пород и мерз- |
|
|
лой сучкова- |
|
||||||
|
|
|
|
|
|
||
|
|
|
|
|
той древесины |
|
|
|
|
|
|
|
|
|
|
|
|
|
|
|
Для мягкой |
|
|
Выпуклый |
30 |
40 |
|
60 |
древесины |
|
|
|
|
|
|
|
|
||
С прямой задней |
30 |
45 |
|
60 |
хвойных по- |
|
|
|
|
|
|||||
|
|
род |
|
||||
гранью |
|
|
|
|
|
||
|
|
|
|
|
|
||
|
|
|
|
|
|
|
36