
ТКМ Часть 2
.pdf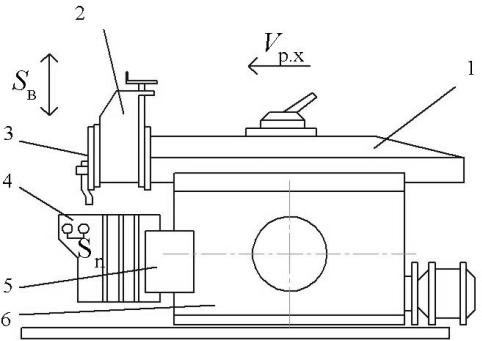
Лабораторная работа 4
УСТРОЙСТВО И КИНЕМАТИЧЕСКАЯ СХЕМА ПОПЕРЕЧНО-СТРОГАЛЬНОГО СТАНКА
Ц е л ь р а б о т ы: изучить устройство, принцип работы механизмов приводов и кинематическую схему станка; освоить методику выбора режимов резания при строгании и последовательность настройки станка.
4.1. Краткие теоретические сведения
Поперечно-строгальные станки предназначены для обработки плоских и фасонных поверхностей, канавок, пазов и прочих поверхностей на коротких деталях длиной до 1000 мм.
Главное движение резания при строгании – поступательное перемещение резца, закрепленного в откидном резцедержателе вертикального суппорта 3 (рис. 4.1), установленного на торце ползуна 1, который совершает возвратнопоступательное движение по горизонтальным направляющим станины 6.
Движение подачи – прерывистое поступательное движение стола 4 с деталью перпендикулярно главному движению резания по направляющим траверсы 5, установленной на вертикальные направляющие станины 6.
Рис. 4.1. Основные узлы поперечно-строгального станка
31
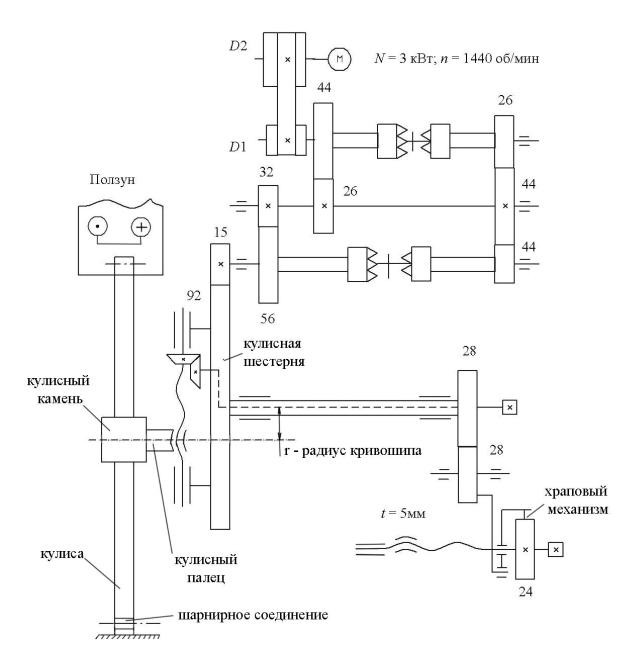
Привод главного движения резания состоит из электродвигателя, ременной передачи, коробки скоростей, закрепленной на станине, и кулисного механизма, расположенного внутри станины, который служит для преобразования вращательного движения кулисной шестерни (рис. 4.2) в возвратнопоступательное движение ползуна, шарнирно соединенного с качающейся кулисой.
Рис. 4.2. Кинематическая схема поперечно-строгального станка
32
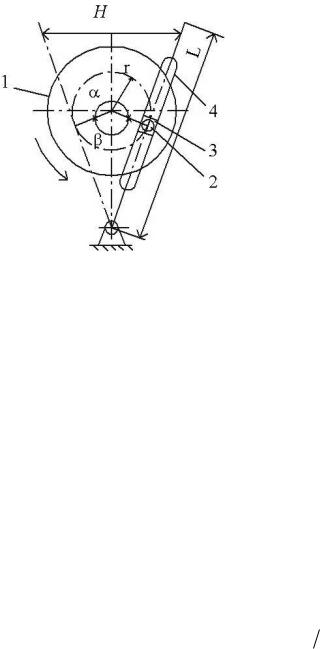
Устройство и схема работы кулисного механизма приведены на рис. 4.3. Кулисная шестерня 1 на боковой поверхности имеет радиальные направляющие, в которых установлен кулисный палец 2, который фиксируется в необходимом положении относительно оси кулисной шестерни 1 с помощью винтовой передачи (см. рис. 4.2). На пальце 2 закреплен кулисный камень 3, входящий в паз кулисы 4, которая одним концом закреплена в станине, а другим соединена через серьгу с ползуном.
При включении станка кулисная шестерня с числом зубьев 92 вращается от шестерни с 15 зубьями, посаженной на выходном валу коробки скоростей. Кулисный камень, вращаясь с кулисной шестерней, одновременно перемещается в пазу кулисы, которая, раскачиваясь, обеспечивает возвратно-поступательное движение ползуна (за один оборот кулисной шестерни – один двойной ход ползуна).
Длина хода ползуна Н зависит от радиуса кривошипа r, который устанавливается вращением рукоятки, надеваемой на вал кулисной шестерни. Ее вращение
через коническую и винтовую передачи обеспечивает перемещение гайки кулисного пальца по радиальным направляющим кулисной шестерни, изменяя значение радиуса кривошипа r.
При постоянной угловой скорости вращения кулисного камня, скорость холостого хода ползуна больше скорости рабочего хода (движения резания), т. к. угол поворота кулисного пальца на рабочий ход больше угла его поворота на холостой ход (α > β). Это существенно снижает затраты на непроизводительный холостой ход. Скорость движения ползуна в среднем положении максимальна, а в крайних положениях – равна нулю. При расчете параметров режима резания определяют среднюю скорость рабочего хода по формуле:
Vð.ñðõ nH 1 k 1000 , |
(4.1) |
где n2х – число двойных ходов ползуна в минуту, равное частоте вращения кулисной шестерни, дв.ход/мин;
33
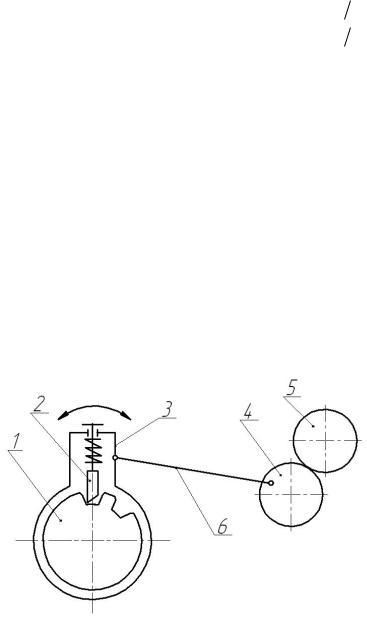
n2х = nэд io, |
(4.2) |
где nэд – частота вращения вала электродвигателя, об/мин;
io – общее передаточное отношение кинематической цепи от электродвигателя до кулисной шестерни;
H – длина хода ползуна, мм;
k – отношение времени холостого хода к времени рабочего хода,
k |
180 2arcsin H 2L |
|
|
(4.3) |
|
|
; |
||||
180 2arcsin H 2L |
|||||
|
|
|
При вычислении k принимать длину кулисы L равной 950 мм.
На поперечно-строгальном станке за подачу принимают перемещение стола с деталью за время одного двойного хода ползуна с резцом (за один оборот кулисной шестерни), т. е. подача на двойной ход Sдв.х, мм/дв.ход.
Привод подачи работает от шестерни с числом зубьев 28, вращающейся в одном блоке с кулисной шестерней (92 зуба), свободно посаженным на вал (см. рис. 4.2). Эта шестерня передает вращение промежуточной шестерне (28 зубьев), на которой эксцентрично установлен палец, связанный тягой с храповым механизмом, преобразующим вращательное движение кулисной шестерни в прерывистое поступательное перемещение стола по направляющим траверсы.
Устройство и схема работы храпового механизма приведены на рис. 4.4. Храповой механизм состоит из двух основных деталей: храпового колеса 1, неподвижно закрепленного на ходовом винте подачи стола и собачки 2, представляющей собой стержень, рабочий торец которого скошен под углом и, под действием пружины входит во впадину между зубьями храпового колеса. Собачка с пружи-
ной находятся в корпусе 3, свободно посаженном на ходовом винте подачи сто-
34

ла и соединенном тягой 6 с эксцентриком шестерни 4 с числом зубьев 28, которая получает вращение от шестерни 5 с 28 зубьями, вращающейся вместе с кулисной шестерней (см. рис. 4.2).
За один оборот кулисной шестерни корпус с собачкой 2, качаясь, отклоняется в две стороны: в момент рабочего хода – в сторону скоса собачки 2, при этом она выходит из впадины между зубьями колеса 1 и скользит по ним своим торцом; в момент холостого хода ползуна – в противоположную сторону, при этом под действием пружины собачка 2 входит во впадину зубьев колеса 1 и поворачивает его, вращая ходовой винт подачи стола только в момент холостого хода. Направление подачи можно изменить, повернув собачку скосом «вперед» или «назад». В рассматриваемой конструкции данного механизма за один двойной ход собачка поворачивает храповое колесо с числом зубьев 24 максимум на 4 зуба, т. е. ходовой винт повернется на 1/6 оборота, при шаге винта 5 мм, максимальная подача стола составит 5/6 мм/дв.ход (0,83 мм/дв.ход). Для уменьшения значения подачи часть зубьев, доступных собачке закрывают кожухом 3, например, открывают только один, два или три зуба и получают подачу на один зуб, а по остальным собачка проскальзывает сверху по кожуху.
Таким образом, значение подачи определяется по формуле:
S ix zõ.êt ; |
(4.4) |
где i – общее передаточное отношение от кулисной шестерни до храпового механизма;
x – число зубьев храпового колеса, захватываемых собачкой за один двойной ход ползуна;
zх.к – число зубьев храпового колеса;
t – шаг ходового винта поперечной подачи стола, мм.
Определение значений параметров режима резания для строгания производится в следующей последовательности:
а) по заданной длине обрабатываемой поверхности определить необходимую длину хода ползуна:
H = l + l1 + l2, |
(4.5) |
где l – длина обрабатываемой поверхности, мм; l1 + l2 – перебег резца (табл. 4.1).
35

|
|
Т а б л и ц а 4.1 |
|
Значения перебега резца l1 + l2 |
|
|
|
|
Длина строгания l, мм |
|
Перебег резца l1 + l2, мм |
До 100 |
|
35 |
Св. 100 до 200 |
|
50 |
Св. 200 до 300 |
|
60 |
Св. 300 |
|
75 |
|
|
|
б) по заданному значению подачи определить ее фактическое значение из условия:
S Sз, |
(4.6) |
где Sдв.х – рассчитанное значение подачи по формуле (4.4), мм/дв.ход; S – заданное значение подачи (табл. 4.4), мм/дв.ход.
в) рассчитать допустимую скорость резания при строгании по формуле:
V Cv |
t Хv s Yv kv , |
(4.7) |
где Cv, Xv, Yv – постоянная величина и коэффициенты, зависящие от условий обработки (табл. 4.2);
t – глубина резания, мм;
S – фактическое значение подачи, мм/дв. ход; kv – поправочный коэффициент, kv = kнkc,
где kн – коэффициент, учитывающий длину хода ползуна (табл. 4.3); kc – коэффициент, учитывающий тип станка, kc = 1.
Т а б л и ц а 4.2 Значения постоянной Cv и коэффициентов Xv, Yv
(обрабатываемый материал – среднеуглеродистая сталь)
Материал режущей части резца |
Подача |
Cv |
Xv |
Yv |
|
Быстрорежущая сталь |
0,25 |
30,4 |
0,25 |
0,5 |
|
|
|
|
|
||
0,25 |
24,3 |
0,25 |
0,66 |
||
|
|||||
|
|
|
|
|
|
Твердый сплав |
0,3 |
170 |
0,18 |
0,2 |
|
|
|
|
|
||
0,3 |
141,5 |
0,18 |
0,35 |
||
|
|||||
|
|
|
|
|
36

Т а б л и ц а 4.3
Значение коэффициента kн
Длина хода резца l, мм |
50 |
100 |
150 |
200 |
300 |
500 |
|
|
|
|
|
|
|
Коэффициент kн |
1,18 |
1,11 |
1,02 |
1,00 |
0,96 |
0,87 |
г) определить необходимое число двойных ходов по формуле:
näâр.õ 1000V H 1 k . |
(4.8) |
д) определить фактическое число двойных ходов из условия:
n(ф)дв.х n(р)дв.х, |
(4.9) |
где n(ф)дв.х – рассчитанное значение числа двойных ходов по кинематической схеме станка, дв.ход/мин.
е) определить по формуле (4.1) среднее фактическое значение скорости резания.
4.2.Порядок выполнения работы
1)Ознакомиться с конструкцией и назначением основных узлов станка, устройством и принципами работы механизмов его приводов.
2)Изучить кинематическую схему станка (см. рис. 4.2).
3)По кинематической схеме определить число двойных ходов ползуна в минуту и значения подачи на двойной ход ползуна.
4)По заданному варианту (табл. 4.4) определить параметры режима резания при строгании.
4.3.Содержание отчета
1)Кинематическая схема станка. Краткое описание устройства и назначения основных узлов и механизмов станка (кулисного и храпового).
2)Структурные схемы механизмов приводов главного движения резания
иподачи, результаты расчета их характеристик.
37
3)Результаты расчета параметров режима резания по варианту.
4.4.Контрольные вопросы
1)Какое движение в строгальном станке является главным движением резания, а какое движением подачи и чем они характеризуются?
2)Как устроен и работает привод главного движения и привод движения подачи поперечно-строгального станка?
3)Как изменить длину и границы хода ползуна?
4)За счет чего изменяется значение подачи стола на двойной ход ползуна поперечно-строгального станка и как она реверсируется?
5)С какой целью строгальные резцы изготавливаются изогнутыми и крепятся в откидном резцедержателе?
|
|
|
|
Т а б л и ц а 4.4 |
|
|
Исходные данные для выполнения индивидуального задания |
||||
|
|
|
|
|
|
Вариант |
Глубина ре- |
Подача S, |
Длина обрабатывае- |
Материал резца |
|
|
зания t, мм |
мм/дв. ход |
мой поверхности l, мм |
|
|
|
|
|
|
|
|
1 |
2,0 |
0,25 |
400 |
Твердый сплав |
|
2 |
1,2 |
0,45 |
380 |
То же |
|
3 |
1,2 |
0,45 |
425 |
» |
|
4 |
1,5 |
0,65 |
375 |
» |
|
5 |
1,0 |
0,85 |
250 |
» |
|
6 |
2,0 |
0,25 |
220 |
» |
|
7 |
1,7 |
0,85 |
400 |
» |
|
8 |
1,9 |
0,25 |
230 |
Быстрорежущая сталь |
|
9 |
2,1 |
0,45 |
375 |
То же |
|
10 |
2,0 |
0,65 |
200 |
» |
|
11 |
1,5 |
0,85 |
250 |
» |
|
12 |
1,5 |
0,25 |
300 |
» |
|
13 |
2,0 |
0,45 |
290 |
» |
|
14 |
1,5 |
0,65 |
410 |
» |
|
15 |
2,3 |
0,25 |
290 |
» |
|
|
|
|
|
|
|
38
Лабораторная работа 5
ЛИМБОВАЯ ДЕЛИТЕЛЬНАЯ ГОЛОВКА
Ц е л ь р а б о т ы: изучить устройство, кинематическую схему и методы настройки лимбовой делительной головки.
5.1. Краткие теоретические сведения
Делительная головка – универсальное приспособление, применяемое на фрезерных, строгальных, шлифовальных и других станках для периодического поворота заготовки относительно ее оси на определенный угол, а также для непрерывного вращения заготовки при фрезеровании винтовых канавок.
Делительная головка устанавливается на стол станка. Обрабатываемая заготовка закрепляется в приспособлении, установленном на шпинделе 1 делительной головки, вращающемся в подшипниках корпуса (рис. 5.1) вместе с червячным колесом (40 зубьев) от однозаходного червяка, насаженного на вал, который поворачивается рукояткой 3 (передаточное отношение червячной передачи равно 1/40). На этот вал свободно посажен блок, который может вращаться от конической зубчатой передачи. С внешней стороны на блок закреплен делительный диск 2 (лимб), с нанесенными на него с двух сторон концентрическими окружностями в количестве 9 штук. Каждая из них разделена на равные части (деления) просверленными отверстиями, в которые может входить фиксатор рукоятки. Лимб имеет окружности с числами делений (отверстий):
Т а б л и ц а 5.1
Количество делений на окружностях лимба
первая сторона |
15 |
16 |
18 |
29 |
31 |
37 |
40 |
43 |
47 |
|
|
|
|
|
|
|
|
|
|
вторая сторона |
17 |
19 |
20 |
21 |
23 |
27 |
33 |
39 |
40 |
|
|
|
|
|
|
|
|
|
|
К лимбовой делительной головке прилагается комплект из 12 сменных зубчатых колес с числом зубьев: 20; 25; 30; 40 (2 шт.); 50; 55; 60; 70; 80; 90; 100, которые устанавливаются на гитару 1 (рис. 5.2), чтобы при необходимости существовала возможность вращать блок с лимбом.
39
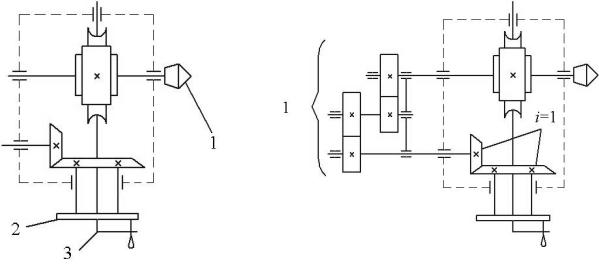
Одним из основных параметров лимбовой делительной головки является ее характеристика N – величина обратная передаточному отношению червячной передачи. Для изучаемой делительной головки (модель УДГ-40) N = 40, т.е. 40 оборотов рукоятки на один оборот заготовки (шпинделя).
Применяются следующие способы наладки лимбовой делительной головки: на простое и дифференциальное деление заготовки на равные и неравные части и наладка для нарезания винтовых (спиральных) канавок. Способ непосредственного деления из-за его простоты в работе не рассматривается.
Рис. 5.1. Кинематическая схема |
Рис. 5.2. Кинематическая схема |
делительной головки, настроенной |
делительной головки, настроенной на |
на простое деление: 1 – шпиндель; |
дифференциальное деление: 1 – гитара |
2 – лимб; 3 – рукоятка |
со сменными зубчатыми колесами |
5.2. Описание наладок делительной головки
Простое деление заключается в определении количества оборотов рукоятки относительно неподвижного лимба (блок с лимбом закреплен фиксатором к корпусу) для поворота шпинделя на заданный угол по формуле:
n |
N |
, |
(5.1) |
|
z |
||||
|
|
|
где п – число оборотов рукоятки;
N – характеристика делительной головки, обычно N равно 40; z – число делений, которое нужно получить на заготовке.
40