
ТКМ Часть 2
.pdf.ks – коэффициент, учитывающий потери в механизме подачи станка, ks = 0,96;
a, b, c, d – соответственно, число ремней в передаче, зубчатых передач, пар подшипников скольжения, пар подшипников качения в кинематической цепи, передающей движение от электродвигателя до шпинделя.
Т а б л и ц а 2.1 Значения коэффициентов полезного действия элементов кинематической цепи
Элементы кинематической цепи |
Коэффициент полезного действия |
|
|
Клиноременная передача (один ремень) |
0,98 |
Зубчатая передача |
0,99 |
Подшипники скольжения (одна пара) |
0,98 |
Подшипники качения (одна пара) |
0,995 |
|
|
2.1.2. Расчет кинематической цепи привода подачи
Подачей при точении называется перемещение суппорта с резцом за один оборот шпинделя с деталью (Sо), при этом продолжительность такого оборота не имеет значения. Поэтому приводным валом механизма подачи является шпиндель (nпр. вала = nшп = 1 об/мин).
Привод подачи начинается от шестерни z10 (см. рис. 2.2), неподвижно посаженной на шпинделе и передающей вращение шпинделя на четыре шестерни z10-z11-z12-z13 реверсивного механизма – трензеля (см. рис. 1.4), обеспечивающего изменение подачи по направлению.
Шестерня z15 является промежуточной, а шестерни z13, z14 и z16 – сменные, установлены на приспособлении, называемом гитарой (гитара сменных шестерен), и обеспечивают возможность изменения общего передаточного отношения кинематической цепи подачи и, соответственно, значения подачи при настройке станка на резьбонарезную операцию. К станку прилагается комплект сменных шестерен (пятковый набор) с числом зубьев кратным 5; 20; 25; 30; 40; 45; 50; 55; 60; 65; 70; 80; 90; 100, а также шестерня со 127 зубьями для настройки станка на нарезание дюймовой резьбы (1” = 25,4 мм = 127/5).
Сменная шестерня z16 вращает ведущий вал коробки подач IV, обеспечивающий изменение значения подачи, а именно шесть различных значений подачи за счет реализации шести вариантов передачи вращения (передаточного
21
отношения) на выходной вал VII коробки подач. Три варианта передаточного отношения обеспечивается включением муфты М2, при котором за счет работы механизма Нортона вращение передается от шестерни z17 на накидную шестерню z18 и далее по очереди на z19, z20, z21, или при выключенной муфте М2
– через валы V и VI за счет зубчатых зацеплений z22-z23 и z25-z24.
Если включить муфту М3, вращение выходного вала коробки подач VII передается на ходовой винт, преобразующий вращательное движение шпинделя в поступательное перемещение суппорта с резцом за счет разъемной гайки, закрепленной в фартуке станка.
Продольная подача по ходовому винту применяется при нарезании резьбы резцом. Для нарезания однозаходной резьбы подача равна:
Sо хв 1 i0б1tхв , |
(2.5) |
где iоб1 – общее передаточное отношение кинематической цепи от шпинделя до ходового винта;
tх.в – шаг ходового винта, мм.
При выключенной муфте М3 вращение вала VII через зубчатое зацепление z26-z27 передается на ходовой вал и далее через конические шестерни z28- z29 – на механизм фартука. Если включить муфту М4, то вращение ходового вала через коническую зубчатую передачу z28-z29 и цилиндрические передачи z31-z30, z33-z35 передается на реечную шестерню z38, которая находится в зацеплении с зубчатой рейкой закрепленной под продольными направляющими станины. Таким образом, обеспечивается продольная подача суппорта станка.
Продольная подача за счет вращения ходового вала равна перемещению реечного колеса вместе с суппортом за один оборот шпинделя, мм:
S х.в.пр i02 m zрш , |
(2.6) |
где – общее передаточное отношение кинематической цепи от шпинделя до реечной шестерни;
m, zрш – модуль и число зубьев реечной шестерни соответственно.
Если включить муфту М5, то вращение ходового вала будет передаваться через шестерни z31-z32, z36-z37 на ходовой винт поперечной подачи. Вращение ходового винта преобразуется в поперечное перемещение суппорта за счет смещения по винту гайки, закрепленной в поперечных салазках суппорта.
22
Значение поперечной подачи определяется по формуле:
S х.в.п i03tn , |
(2.7) |
где iоб3 – общее передаточное отношение от шпинделя до ходового винта поперечной подачи;
tп – шаг ходового винта поперечной подачи, мм.
Структурная схема привода механизма подачи строится аналогично построению схемы (1.12).
2.2.Порядок выполнения работы
1)Изучить конструкцию токарно-винторезного станка.
2)Ознакомиться с устройством и назначением основных узлов станка.
3)Выполнить анализ кинематической схемы станка по индивидуальному заданию (выдается преподавателем).
4)Составить структурную схему механизма привода главного движения.
5)Определить значения частоты вращения шпинделя и крутящего момента на шпинделе.
6)Составить структурную схему механизма привода подачи.
7)Определить значения продольной и поперечной подачи по ходовому валу и продольной подачи по ходовому винту при нарезании резьбы.
2.3.Содержание отчета
1)Описание назначения и устройства основных узлов, приводов и механизмов токарно-винторезного станка.
2)Кинематическая схема токарно-винторезного станка.
3)Структурные схемы механизма приводов главного движения и движения подачи.
4)Расчет значений частоты вращения шпинделя, крутящих моментов на шпинделе и значений подачи.
2.4.Контрольные вопросы
1)Из каких основных узлов состоит токарно-винторезный станок. Каково их устройство и назначение?
23
2)Из каких узлов и механизмов состоят приводы главного движения и движения подачи. Каково устройство и назначение этих узлов и механизмов?
3)Как осуществляются поперечная и продольные подачи суппорта станка?
4)Возможно ли одновременное включение продольной и поперечной подачи за счет вращения ходового вала. Если нет, то почему?
5)Возможно ли одновременное включение продольных подач за счет вращения ходового вала и ходового винта. Если нет, то почему?
Лабораторная работа 3
УСТРОЙСТВО И КИНЕМАТИЧЕСКАЯ СХЕМА ОДНОШПИНДЕЛЬНОГО ВЕРТИКАЛЬНО-СВЕРЛИЛЬНОГО СТАНКА
Ц е л ь р а б о т ы: изучить устройство, управление и кинематическую схему одношпиндельного вертикально-сверлильного станка; освоить методику выбора параметров режима резания при сверлении.
3.1. Краткие теоретические сведения
Одношпиндельный вертикально-сверлильный станок состоит из следующих основных узлов (рис. 3.1): станины, установленной на фундаментной плите шпиндельной бабки, в которой расположен привод главного движения резания, кронштейна, в котором расположен привод движения подачи, и стола, закрепленного на направляющих станины. Станок предназначен для выполнения операций изготовления и обработки отверстий при производстве и ремонте деталей: сверления, рассверливания, надсверливания, зенкерования, развертывания.
Привод главного движения состоит из электродвигателя, коробки скоростей и шпиндельного узла.
Шпиндель представляет собой сплошной шлицевый вал, который вращается вместе с посаженным на него тройным блоком зубчатых колес с числами зубьев 37, 62 и 40 в подшипниках шпиндельной бабки, а также в радиальноупорных подшипниках гильзы (пиноли), расположенной в кронштейне.
Привод движения подачи, смонтированный в кронштейне, обеспечивает вертикальное перемещение цилиндрической гильзы с зубчатой рейкой и вращающимся в ней шпинделем.
24
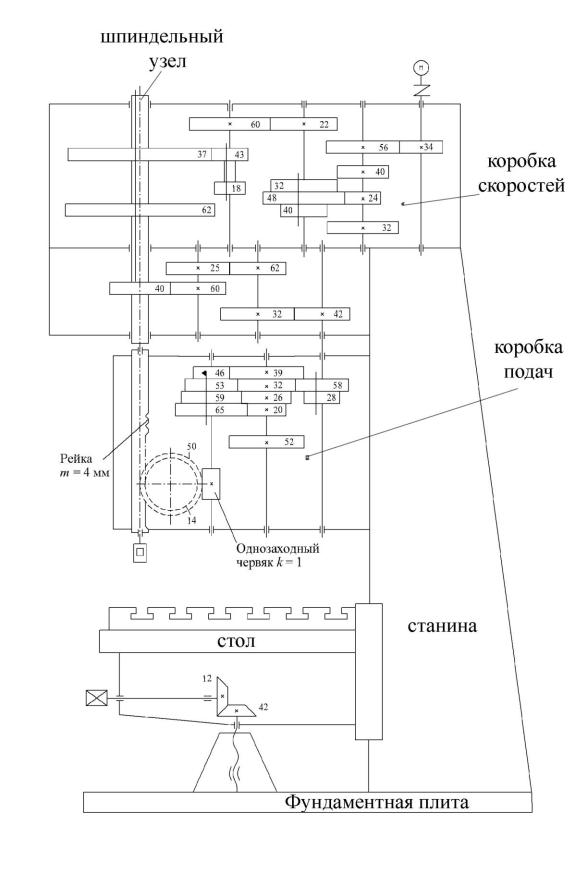
Рис. 3.1. Кинематическая схема одношпиндельного вертикально-сверлильного станка
25

Жесткое соединение вращающегося шпинделя с неподвижной гильзой обеспечивается применением радиально-упорных подшипников качения. При включении подачи рукояткой управления кулачковой муфтой на оси штурвала подачи, вращение шпинделя от шестерни с числом зубьев 40 через промежуточные шестерни, шестерни и валы коробки подач, червячную передачу, передается реечной шестерне с 14 зубьями, вращающейся на одном валу с червячным колесом с 50 зубьями. Таким образом, вращение шпинделя преобразуется в его поступательное перемещение вместе с гильзой в сторону подачи.
Русский академик А. В. Гадолин в 1878 году предложил при построении ряда частот вращения и подач для металлорежущих станков со ступенчатым регулированием значений этих величин, применять закон геометрической прогрессии, по которому каждое последующее значение такой величины больше предыдущего на постоянное для этого ряда число – показатель геометрической прогрессии. Данный показатель для ряда частот вращения шпинделя определяется по следующей формуле:
z 1 |
nmax |
, |
(3.1) |
|
|||
|
nmin |
|
где z – количество ступеней регулирования частоты вращения шпинделя;
nmax, nmin – максимальная и минимальная частоты вращения шпинделя, об/мин.
Расчетное значение φ округляется до ближайшего стандартного.
Таким образом, значения частоты вращения шпинделя рассчитываются:
n |
n ; n |
n ; … ni n i 1 . |
(3.2) |
||
2 |
1 |
3 |
2 |
1 |
|
где n1 = nmin – минимальное значение величины частоты вращения шпинделя, рассчитанное по структурной схеме привода главного движения, об/мин. Расчет ряда значений подачи выполняется аналогично.
Определение значений параметров режима резания для сверления отверстий производится в следующей последовательности:
а) определить расчетную подачу, допускаемую прочностью сверла по формуле:
Sð Cs Dхs ks ; |
(3.3) |
26

где Cs – коэффициент, зависящий от прочности обрабатываемого материала;
Cs 36 â0,91 ; |
(3.4) |
где в – предел прочности при растяжении обрабатываемого материала, МПа; xs – показатель степени (при сверлении инструментом из быстрорежущей
стали xs = 0,6);
ks – поправочный коэффициент (табл. 3.1).
Т а б л и ц а 3.1 Значения поправочного коэффициента ks
Длина отверстия l, мм |
3D |
(3 – 5)D |
(5 – 7)D |
(7 – 10)D |
|
|
|
|
|
Коэффициент ks |
1,0 |
0,9 |
0,8 |
0,75 |
Фактическая подача выбирается из условия:
Sô S Sð , |
(3.5) |
где S – ближайшее меньшее значение из ряда значений подачи станка, мм/об. б) рассчитать допускаемую скорость резания по заданной стойкости при
сверлении стали инструментом из быстрорежущей стали по формуле:
Väîï |
Cv D0,4 |
(3.6) |
|
|
Kv , |
||
|
|||
|
T 0,2 S yv |
|
где Cv – коэффициент, зависящий от условий обработки (Cv = 7 при S 0,2 мм/об; Cv = 9,8 при S > 0,2 мм/об);
yv – показатель степени (yv = 0,7 при S 0,2 мм/об; yv = 0,5 при S 0,2 мм/об);
Kv – поправочный коэффициент, учитывающий условия обработки,
Kv kèv klv kìv , |
(3.7) |
27

где kиv – коэффициент, учитывающий свойства инструментального материала (для быстрорежущей стали kиv = 1);
klv – коэффициент, учитывающий глубину отверстия l (табл. 3.2);
kмv – коэффициент, учитывающий свойства обрабатываемого материала,
|
|
|
kìv 750 в ; |
|
|
|
|
(3.8) |
||||||
|
T – период стойкости инструмента, мин (табл. 3.3). |
|
|
|
|
|||||||||
|
|
|
|
|
|
|
|
|
|
|
Т а б л и ц а |
3.2 |
||
|
|
|
Значения коэффициента k1v |
|
|
|
|
|||||||
|
|
|
|
|
|
|
|
|
|
|
|
|
|
|
Длина отверстия l, мм |
|
3D |
4D |
5D |
6D |
|
|
8D |
10D |
|
|
|||
|
|
|
|
|
|
|
|
|
|
|
|
|
|
|
Коэффициент k1v |
|
1,0 |
|
0,85 |
|
0,74 |
0,7 |
|
|
0,6 |
0,5 |
|
|
|
|
|
|
|
|
|
|
|
|
|
|
Т а б л и ц а |
3.3 |
||
|
|
Значения периода стойкости сверла Т |
|
|
|
|
||||||||
|
|
|
|
|
|
|
|
|
|
|
|
|
||
|
Диаметр сверла D, мм |
|
|
|
5 |
|
6 – 10 |
11 – 20 |
|
21 – 30 |
31 – 40 |
|
||
|
|
|
|
|
|
|
|
|
|
|
|
|
||
|
Период стойкости сверла T, мин |
|
15 |
|
25 |
45 |
|
|
50 |
70 |
|
|
||
|
|
|
|
|
|
|
|
|
|
|
|
|
|
|
в) по найденной допускаемой скорости резания рассчитать необходимую частоту вращения шпинделя:
nð 1000Väîï |
D . |
(3.9) |
Фактическую частоту вращения шпинделя выбирают из условия:
nф n nр , |
(3.10) |
где n – частота вращения шпинделя, рассчитанная по кинематической схеме станка, об/мин.
Фактические значения подачи станка и частоты вращения шпинделя выбирают из ряда значений подачи станка и ряда частот соответственно с таким
28
расчетом, чтобы они были ближайшими наименьшими к рассчитанным значениям.
3.2.Порядок выполнения работы
1)Ознакомиться с устройством станка и назначением основных узлов.
2)Изучить кинематическую схему станка (см. рис. 3.1).
3)Согласно кинематической схеме построить структурные схемы механизмов привода главного движения резания и привода движения подачи.
4)По закону А. В. Гадолина произвести расчет значений ряда частот вращения шпинделя и подач станка.
5)В соответствии с заданным вариантом (табл. 3.4) рассчитать режим резания для сверления отверстия в заготовке из углеродистой конструкционной стали инструментом из быстрорежущей стали.
|
|
|
|
|
|
|
|
|
Т а б л и ц а 3.4 |
|
|
Исходные данные для расчета режима резания при сверлении |
|||||||||
|
|
|
|
|
|
|
|
|
||
|
Размеры отверстия, |
Временное сопро- |
|
Размеры отверстия, |
Временное сопротив- |
|
||||
|
|
мм |
тивление разрыву |
|
|
мм |
|
|||
Номер |
|
Номер |
|
ление разрыву |
|
|||||
|
|
|
обрабатываемого |
|
|
|
|
|||
D |
|
l |
D |
|
l |
|||||
варианта |
|
варианта |
|
обрабатываемого |
|
|||||
|
|
|
материала в, |
|
|
|
|
|||
|
|
|
|
|
|
|
|
материала в, МПа |
|
|
|
|
|
|
МПа |
|
|
|
|
|
|
|
|
|
|
|
|
|
|
|
|
|
|
|
|
|
|
|
|
|
|
|
|
1 |
20 |
|
100 |
800 |
17 |
35 |
|
200 |
750 |
|
|
|
|
|
|
|
|
|
|
|
|
2 |
25 |
|
80 |
800 |
18 |
18 |
|
180 |
550 |
|
|
|
|
|
|
|
|
|
|
|
|
3 |
20 |
|
30 |
800 |
19 |
40 |
|
65 |
650 |
|
|
|
|
|
|
|
|
|
|
|
|
4 |
15 |
|
60 |
800 |
20 |
30 |
|
250 |
700 |
|
|
|
|
|
|
|
|
|
|
|
|
5 |
10 |
|
40 |
500 |
21 |
12 |
|
85 |
850 |
|
|
|
|
|
|
|
|
|
|
|
|
6 |
22 |
|
85 |
600 |
22 |
35 |
|
90 |
600 |
|
|
|
|
|
|
|
|
|
|
|
|
7 |
10 |
|
50 |
700 |
23 |
38 |
|
350 |
500 |
|
|
|
|
|
|
|
|
|
|
|
|
8 |
27 |
|
60 |
600 |
24 |
21 |
|
150 |
750 |
|
|
|
|
|
|
|
|
|
|
|
|
9 |
23 |
|
100 |
500 |
25 |
5 |
|
50 |
850 |
|
|
|
|
|
|
|
|
|
|
|
|
10 |
25 |
|
30 |
700 |
26 |
17 |
|
45 |
400 |
|
|
|
|
|
|
|
|
|
|
|
|
11 |
12 |
|
30 |
500 |
27 |
39 |
|
280 |
650 |
|
|
|
|
|
|
|
|
|
|
|
|
12 |
15 |
|
80 |
500 |
28 |
9 |
|
86 |
700 |
|
|
|
|
|
|
|
|
|
|
|
|
13 |
17 |
|
90 |
500 |
29 |
23 |
|
170 |
800 |
|
|
|
|
|
|
|
|
|
|
|
|
14 |
12 |
|
65 |
800 |
30 |
7 |
|
28 |
600 |
|
|
|
|
|
|
|
|
|
|
|
|
15 |
24 |
|
100 |
600 |
31 |
37 |
|
350 |
550 |
|
|
|
|
|
|
|
|
|
|
|
|
16 |
28 |
|
140 |
400 |
32 |
14 |
|
88 |
400 |
|
|
|
|
|
|
|
|
|
|
|
|
29
3.3. Содержание отчета
1)Краткое описание устройства станка и работы его механизмов.
2)Структурные схемы приводов станка.
3)Расчет значений частоты вращения шпинделя и подачи станка.
4)Выбор режима резания в соответствии с описанной выше методикой.
3.4.Контрольные вопросы
1)Какое движение в сверлильном станке является главным движением резания и чем оно характеризуется?
2)В каких узлах станка расположены привод главного движения и привод движения подачи?
3)Какая передача обеспечивает вертикальное перемещение шпинделя сверлильного станка и где находятся ее элементы?
4)Что понимается под геометрическим рядом частот и подач А. В. Гадолина и как определяются значения этих рядов для коробок скоростей и подач металлорежущего станка?
30