
ТКМ часть 3
.pdf
нием имеет более низкие механические свойства, чем мелкозернистая сталь. Ширина этого участка – 0,7 – 4 мм;
5 – участок рекристаллизации. Температура нагрева этого участка ниже первой критической точки Ас1 (727С). При сварке горячекатаной или отожженной стали, на этом участке ЗТВ никакие структурные изменения в металле не происходят.
Если же сталь перед сваркой была наклепана (нагартована) в результате холодной пластической деформации (штамповка, гибка, правка), то при нагреве в интервале температуры 550 – 600С произойдет процесс рекристаллизации (рост новых равноосных зерен за счет исходных деформированных). По сравнению с исходным металлом прочность и твердость стали снизятся, а пластичность увеличится. В случае если температура нагрева металла на этом участке близка к первой критической точке (727 С) и длительность пребывания его при этой температуре значительна, то происходит процесс собирательной рекристаллизации. При этом укрупняется зерно и происходит разупрочнение металла. Данный участок в этом случае называют участком разупрочнения.
а |
б |
в |
Рис. 1.3. Структура стали Ст3сп при автоматической дуговой сварке: а – металл шва, феррит и перлит (проволока Св-08ГА, флюс АН-348А); б – участок перегрева зоны термического влияния (видманштеттовая структура); в – основной металл. ×100
6 – участок синеломкости. Температура нагрева металла на данном участке сварного шва в интервале 200 – 400С, при котором на поверхности стали появляются синие цвета побежалости (пленки окислов). Характеризуется тем, что прочность и твердость металла повышаются, а пластичность и ударная вязкость – резко падают. Это явление получило название «синеломкость». Ве-
11
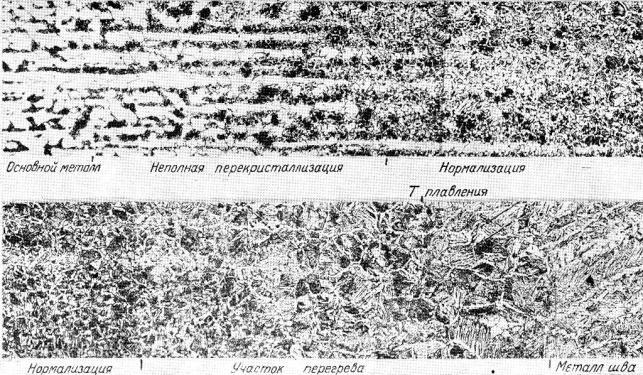
роятной причиной этого является старением металла – выделение по границам зерен из пересыщенного твердого раствора дисперсных карбидов и нитридов.
1.1.3. Влияние структуры шва на механические свойства сварного соединения
Таким образом, структура и, соответственно, механические свойства металла отдельных зон и участков сварного соединения неодинаковы (рис. 1.4).
Рис. 1.4. Микроструктура зоны термического влияния при дуговой сварке низкоуглеродистой стали Ст3сп (смотреть слева направо – от основного металла к металлу шва) ×100
В зоне термического влияния наиболее низкие механические свойства наблюдаются у металла шва, на границе сплавления, участке перегрева и участке синеломкости. У наплавленного металла шва это объясняется литой структурой металла и вероятностью наличия дефектов (инородных включений, пор, непроваров, трещин и т. п.) (рис. 1.5), в переходной зоне шва – тем, что структура стали состоит из литых зерен и крупных кристаллов перегретого металла с характерной для них низкой прочностью. На участке синеломкости также низкие пластичность и ударная вязкость. Такая разносвойственность участков сварного шва особенно резко проявляется при эксплуатации сварных конструкций, испытывающих динамические и циклические нагрузки.
12
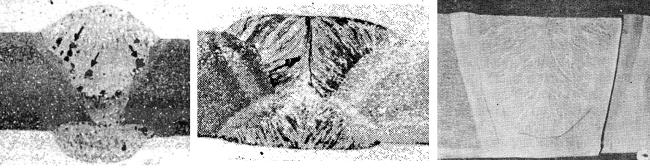
Структурную неоднородность сварного соединения можно в определенной степени устранить термической обработкой. Если на термическую обработку возлагается только задача снятия внутренних напряжений, возникших в результате сварки, то можно ограничиться низкотемпературным отжигом при 500 – 600С с последующим медленным охлаждением. Перегрев и видманштеттовая структура ЗТВ устраняются измельчением зерна стали за счет повторной перекристаллизации (полным отжигом или нормализацией).
а б в
Рис. 1.5. Макродефекты сварных соединений: а – поры и шлаковые включения; б – межкристаллитная трещина; в – трещина в околошовной зоне
Наиболее эффективным средством изменения параметров термического цикла является предварительный или сопутствующий подогрев места сварки (последующее снижение скорости охлаждения для уменьшения закалочных явлений). Однако подогрев иногда не может быть использован из-за возможности чрезмерного роста зерна стали (перегрева), образования околошовных горячих трещин или из-за трудности осуществления.
Прочность сварного соединения зависит также от дефектов, не связанных со структурными превращениями, – это неправильное формирование шва, образование наплывов и подрезов, образование трещин при неравномерной усадке в процессе кристаллизации металла шва. При затвердевании объем шва уменьшается, а основной металл препятствует этой усадке. В результате могут образоваться значительные внутренние напряжения и даже трещины.
1.2. Порядок выполнения работы
1) Исследовать под микроскопом ММУ-3 структуру наплавленного металла и зоны термического влияния. Выявить дефекты сварного соединения.
13
2)Зарисовать схему строения сварного шва (см. рис. 1.2) и описать особенности структуры каждого участка зоны термического влияния.
3)Определить по структуре сварного шва наиболее вероятное место его разрушения.
1.3. Содержание отчета
1)Схема строения сварного шва с расшифровкой всех обозначений. Описание выявленных дефектов макроструктуры.
2)Описание особенностей структуры каждого участка зоны термического влияния.
3)Выводы о прочности и надежности исследованного сварного шва.
1.4. Вопросы для самоконтроля
1)От чего зависит состав, структура и свойства металла шва и какие дефекты снижают его эксплуатационную надежность?;
2)Что собой представляет зона термического влияния сварного соединения и из каких участков она состоит?;
3)Чем объяснить формирование в ЗТВ участка перегретого металла. Какая его структура и свойства?
4)Какая термическая обработка используется для исправления дефектной структуры (видманштеттовой) в ЗТВ сварных швов?
14
Лабораторная работа 2
ОПРЕДЕЛЕНИЕ ТЕХНОЛОГИЧЕСКИХ КОЭФФИЦИЕНТОВ ПРИ ДУГОВОЙ СВАРКЕ СТАЛИ
Ц е л ь р а б о т ы:
1)исследовать влияние сварочного тока на значения коэффициентов расплавления р, наплавления н, потери на угар и разбрызгивания ψ при сварке электродами заданной марки;
2)определить оптимальное значение сварочного тока при выполнении наплавочных работ электродом заданного диаметра.
Н е о б х о д и м ы е м а т е р и а л ы и о б о р у д о в а н и е: электроды ОММ-5, К-2-55 или УОНИ-13/45 (выдаются преподавателем); пластины из низкоуглеродистой стали размером 200 80 10 мм; сварочный трансформатор ТС-300, весы лабораторные, секундомер.
2.1. Краткие теоретические сведения
На практике значение сварочного тока ориентировочно определяется по формуле:
Iсв k dэл , |
(1) |
где Iсв – сварочный ток, А;
k – коэффициент, для углеродистых сталей k = 35 – 50 А/мм;
dэл – диаметр электрода, мм. Выбирается в зависимости от толщины свариваемых листов.
Таким образом, значение сварочного тока может выбираться в широких пределах расчетного интервала варьирования (например, при dэл = 4 мм
Iсв = 140 – 200 А).
Интенсивность расплавления электродного металла характеризуется коэффициентом расплавления р, г/А ч, – масса расплавленного металла в единицу времени, отнесенная к единице сварочного тока для данного режима сварки. С увеличением сварочного тока интенсивность теплового потока от горения дуги увеличивается пропорционально квадрату тока q = I2R. Поэтому р изменяется по параболическому закону (рис. 2.1).
15

р |
р |
н |
|
ψ |
|
ψ
н
Iсв опт |
Iсв, А |
Рис. 2.1. Влияние сварочного тока на значении технологических коэффициентов при дуговой сварке плавящимся электродом
Производительность процесса сварки характеризуется коэффициентом наплавления н, г/А ч, – масса наплавленного металла в единицу времени, отнесенная к единице сварочного тока для данного режима сварки.
Потери электродного металла на разбрызгивание, испарение и окисление характеризуются коэффициентом потерь электродного металла ψ.
Проблема определения оптимального значения сварочного тока, при котором достигаются максимальная производительность и минимальные потери электродного металла, решается экспериментальным путем (см. рис. 2.1).
Как видно из рисунка 2.1, сварка при меньших значениях тока имеет более низкую производительность процесса вследствие снижения интенсивности расплавления электрода и увеличения потерь на разбрызгивание расплава в результате нестабильного (прерывистого) горения дуги и крупнокапельного переноса электродного металла в сварочной дуге.
С увеличением сварочного тока до определенного (оптимального) значения производительность процесса возрастает за счет стабильного горения дуги, мелкокапельного переноса электродного металла и увеличения скорости плавления электрода. Сварка при значениях тока выше оптимального часто приводит к снижению производительности процесса, так как увеличиваются потери
16

на окисление и испарение электродного металла вследствие повышения температуры в зоне горения дуги.
2.2. Порядок выполнения работы
1)Ознакомиться со схемой включения в сварочную цепь измерительных приборов (рис. 2.2).
2)Произвести настройку режима работы сварочного агрегата в зависимости от выбранного диаметра электродов.
3)Определить массу контрольной пластины (если пластина ранее подвергалась наплавке, нужно тщательно удалить с нее шлаковые корки) и массу электрода без обмазки. Данные занести в табл. 2.1.
4)Произвести контрольную наплавку на контрольной пластине, расплавив за один опыт не менее ¾ длины электрода. В процессе наплавки замерить среднюю силу сварочного тока и время горения дуги.
5)После наплавки определить массу наплавленного на пластину металла
имассу расплавленного металла электрода, для чего необходимо:
а) зачистить наплавленный валик от шлака и брызг до металлического блеска и взвесить. Разница в массе пластины до наплавки и после дает массу наплавленного металла Gн;
б) удалить с огарка электрода обмазку, зачистить его до металлического блеска и взвесить. Разница в массе электрода даст массу расплавленного металла электрода Gр. Данные занести в табл. 2.1.
А
V
Рис. 2.2. Схема включения измерительных приборов в сварочную цепь
17
|
|
|
|
|
|
|
|
|
|
|
|
|
Т а б л и ц а 2.1 |
|
|
Исходные данные для расчета технологических коэффициентов |
|
||||||||||||
|
|
|
|
|
|
|
|
|
|
|
|
|
|
|
Режим |
Масса |
Масса |
|
|
|
Масса прутка |
Масса |
Время |
||||||
пластины, г |
наплавленного |
|
|
|
|
электрода, г |
расплавленного |
|||||||
сварки |
|
|
|
|
наплавки |
|||||||||
|
|
электродного |
|
|
|
|
|
|
электродного |
|||||
до |
после |
|
|
|
до |
после |
||||||||
Iсв, А |
|
|
|
t, с |
||||||||||
наплавки |
наплавки |
металла Gн ,г |
|
наплавки |
наплавки |
металла Gр, г |
||||||||
|
|
|
||||||||||||
|
|
|
|
|
|
|
|
|
|
|
||||
|
|
|
|
|
|
|
|
|
|
|
|
|
|
|
|
6) Вычислить коэффициент расплавления по формуле: |
|
||||||||||||
|
|
|
р |
3600 Gр |
. |
|
|
|
(2) |
|||||
|
|
|
|
|
|
|
|
|
|
|
||||
|
|
|
|
I |
св t |
|
|
|
||||||
|
|
|
|
|
|
|
|
|
|
|
|
|||
|
7) Вычислить коэффициент наплавления по формуле: |
|
||||||||||||
|
|
|
н |
3600Gн |
. |
|
|
(3) |
||||||
|
|
|
|
|
|
|||||||||
|
|
|
|
|
|
|
I св t |
|
|
|
|
|
|
|
|
8) Вычислить потери на угар и разбрызгивание по формуле: |
|
||||||||||||
|
|
|
|
Gр Gн |
100 %. |
|
(4) |
|||||||
|
|
|
|
|
|
|
|
|
Gр
9) Исследовать влияние силы сварочного тока на коэффициенты расплавления, наплавления и на потери на угар и разбрызгивание, определить оптимальное его значение, для чего необходимо
а) повторить два цикла опытов при силе сварочного тока большей и меньшей на 25 – 30 % от рассчитанного по формуле (1) значения и приведенной выше методике;
б) полученные расчетные данные занести в табл. 2.2 и построить графики зависимости коэффициентов р, н и ψ от силы сварочного тока.
|
|
|
Т а б л и ц а 2.2 |
|
|
Результаты опытов |
|
||
|
|
|
|
|
Сила |
Коэффициент |
Кэффициент наплавления |
Потери на угар и |
|
сварочного тока, |
расплавления |
разбрызгивание |
||
н, г/А ч |
||||
А |
р, г/А ч |
ψ, % |
||
|
||||
|
|
|
|
|
|
|
18 |
|

2.3. Содержание отчета
1)Схема включения измерительных приборов.
2)Расчет коэффициентов р, н и при различном значении Iсв.
3)Описание методики проведения опытов, их результаты в виде табл. 2.1,
2.2и графика.
4)Выводы.
2.4. Вопросы для самоконтроля и задания
1)Что характеризуют коэффициенты расплавления, наплавления и потери на угар и разбрызгивание, их размерность?
2)Может ли коэффициент наплавления быть больше коэффициента расплавления (если да, то в каких случаях)?
3)Как влияет плотность тока на потери электродного металла при ручной дуговой сварке?
4)От каких факторов зависит производительность электрической сварки плавящимся электродом?
5)Установите количественную взаимосвязь между коэффициентами
р, н и .
6)Определите количество наплавленного металла, если сварка произво-
дится электродом АНО (коэффициент наплавления н = 8 – 9 г/А ч) при силе тока I = 140 А, время сварки t = 0,02 ч.
7)Определите количество расплавленного металла, если сварка производится электродами УОНИ 13/45 при силе тока I = 160 А, время сварки t = 0,32 ч
ир = 8,5 г/А ч.
8)Определите коэффициент наплавления н, если известны коэффициен-
ты расплавления р = 14 г/А ч и потерь = 20 %.
19
Лабораторная работа 3
ИЗУЧЕНИЕ КОНСТРУКЦИИ, ПРИНЦИПА ДЕЙСТВИЯ СВАРОЧНОГО ТРАНСФОРМАТОРА ТС-300 И ИССЛЕДОВАНИЕ ЕГО ВНЕШНИХ ХАРАКТЕРИСТИК
Ц е л ь р а б о т ы:
1)ознакомиться с конструкцией и принципом действия источника питания сварочной дуги, изучить работу и взаимодействие всех узлов сварочного трансформатора ТС-300;
2)приобрести навыки снятия внешних характеристик источника питания;
3)построить и исследовать семейство внешних характеристик источника питания.
Н е о б х о д и м о е о б о р у д о в а н и е: сварочный трансформатор ТС-300, реостат и измерительные приборы.
3.1. Краткие теоретические сведения
На практике в качестве источников сварочного тока применяются сварочные трансформаторы (для сварки на переменном токе); сварочные генераторы или полупроводниковые выпрямительные установки (для сварки на постоянном токе).
Источники питания сварочной дуги должны удовлетворять следующим требованиям:
1) напряжение холостого хода, т. е. напряжение на зажимах источника питания при разомкнутой сварочной цепи, должно быть достаточным для зажигания дуги, но не превышать значения, безопасного для сварщика;
мощность источника должна быть достаточной для питания дуги необходимым сварочным током;
источники питания сварочной дуги должны иметь устройства для плавного регулирования силы тока в необходимых для сварки пределах;
источники питания должны иметь небольшие массу, габариты и стоимость, а также быть удобными в эксплуатации.
Одной из важнейших характеристик источника питания сварочной дуги является его внешняя статическая (вольтамперная) характеристика – зависимость напряжения в сварочной цепи от силы сварочного тока. Для ручной ду-
20