
ЧАСТЬ 2 ТЭП (МГУП 2012)
.pdfопределённой последовательности и подачу зерна в требуемом количестве из участка разгрузки к месту загрузки. Управление материальными потоками связано с переключением потока движения сырья и готовой продукции. Эти операции выполняют регулирующие органы (задвижки и клапаны), управляемые с помощью исполнительных механизмов.
К их числу относят компактные, простые и дешёвые автоматизированные исполнительные механизмы, которые развивают достаточные усилия для регулирования степени открытия и закрытия задвижек; надёжные датчики уровня зерна и продуктов его переработки с подачей соответствующих импульсов на автоматическое закрытие задвижек и остановку машин при возникновении препятствий для прохождения потока зернопродуктов по маршруту; влагомеры зерна, способные автоматически контролировать влажность зерна при сушке, и др.
11.4 Исполнительные механизмы
На элеваторах наибольшее распространение получили датчики уровня. Они применяются при контроле уровня сыпучих материалов в силосах, бункерах и оперативных ёмкостях, а также при контроле состояния транспортирующего продукта в самотёках и нориях. В связи с тем, что физико-механические свойства сыпучих продуктов (зерно, крупа, мука и др.) различны, были созданы несколько типов датчиков для того, чтобы полнее удовлетворить требования надёжности, точности и стоимости. В настоящее время находят применение простейшие мембранные и флажковые датчики контактного действия, электронные — емкостного принципа действия.
Мембранные датчики уровня МДУ-З, МДУ-ЗМ, МДУ-ЗСМ применяются на хлебоприёмных предприятиях для контроля уровня хорошо сыпучих материалов. Отличительной особенностью мембранных датчиков является простота и низкая стоимость.
Внастоящее время серийно выпускаются новые мембранные сигнализаторы уровня СУМ-1 и СУМ-1-01, предназначенные для предупреждения аварийного накопления зерна и продуктов его переработки
вподводящих и отводящих самотеках зерноперерабатывающих машин (СУМ-1), а также для контроля уровня сыпучих продуктов в производственных емкостях (СУМ-1-01). В этих сигнализаторах в основном устранены недостатки, присущие датчикам уровня МДУ.
Сигнализатор уровня СУМ-1-01 — модификация сигнализатора СУМ-1. Также разработан новый флажковый сигнализатор уровня СУГ-1, предназначенный для контроля заполнения зерном и продуктами его переработки бункеров, силосов, подводящих и отводящих самотеков
зерноперерабатывающих машин.
Этот сигнализатор уровня устанавливают в силосах так, чтобы струя зерна не попадала на него, а середина вертикально висящего флажка была бы на высоте заданного уровня.
Вэлеваторной промышленности широкое распространение получили электромеханические исполнительные механизмы Е8-УРВ, ТЭА, ЭПВ,
21
РИМЗ, ПР, ИМ, МЭО, которые устанавливаются на пещих органах. Исполнительный механизм Е8-УРВ служит для привода реечных задвижек и перекидных клапанов. Благодаря простоте устройства он получил широкое распространение на предприятиях по хранению и переработке зерна.
Механизм Е8-УРВ не имеет датчиков для обратной связи и дистанционной передачи положения регулирующего органа.
Исполнительный механизм РИМЗ разработан специально для предприятий по хранению и переработке зерна. Он может быть использован для дистанционного и автоматического управления задвижками и клапанами. От других исполнительных механизмов он отличается встроенной системой обратной связи положения регулирующего органа. Степень открытия задвижки (величину хода) можно регулировать конечными выключателями.
11.5 Системы дистанционного управления работой элеваторов
К середине 1990-х гг. около 300 элеваторов были оборудованы установками для дистанционного управления оборудованием с единого пульта, установками автоблокировки и контроля за загрузкой норий и заполнения зерновых емкостей. Такое диспетчерское управление (система ДУ) повышает коэффициент использования машин и упрощает эксплуатацию элеваторов.
В настоящее время на хлебоприёмных предприятиях комплексная автоматизация технологических процессов на всех участках осуществляется с помощью систем диспетчерского автоматизированного управления +AY).
Система ДАУ предусматривает централизованное управление машинами и механизмами элеватора с единого пульта, а также местных постов управления для повышения производительности и облегчения условий труда, оперативного ведения технологического процесса, более интенсивного использования оборудования, улучшения условий эксплуатации и т. п.
При внедрении системы ДАУ в дополнение к системе ДУ вводится дистанционное управление сбрасывающими тележками, поворотными трубами и другими механизмами, а также осуществляется контроль заполнения силосов зерном, расширен объём автоблокировок.
В дальнейших разработках ДАУ элеваторами предусматривается улучшение систем автоматизации, увеличение автоблокировок, управление сепараторным узлом и порционными весами с пульта управления, что позволит повысить надежность этих систем, улучшить их обслуживание и сократить численность обслуживающего персонала.
Житомирский завод «Промавтоматика» освоил производство пультов ПДУ-2М, которые предназначены для работы в системе ДАУ на предприятиях мукомольной, комбикормовой промышленности и элеваторноскладского хозяйства.
С пульта осуществляются дистанционное управление машинами и оборудованием технологических линий, сигнализация о работе
22
электродвигателей и заполнении бункеров, а также автоблокировка, выполненная в соответствии с требованиями пуска и остановки машин.
Связь пульта ПДУ-2М с электродвигателями технологического оборудования элеватора осуществляется через блоки реле, релейные шкафы, шкафы управления и силовые шкафы, распределительные ящики с автоматическими выключателями, которые устанавливают в отдельных помещениях — релейных пунктах (РП).
Всоответствии с требованиями объёмов ДАУ различными проектными
инаучно-исследовательскими организациями разработаны блочные системы диспетчерского автоматизированного управления поточно-транспортными системами. Блоки, удовлетворяющие требованиям функциональности, универсальности и простоты конструкции, позволяют создавать системы ДАУ из готовых элементов, соединения между которыми определяются технологической схемой данного элеватора. Такие системы экономичны и удобны в обслуживании.
Внастоящее время блочные системы ДАУ эксплуатируются на элеваторах Москвы, Одессы, Полтавы, Ново-Московска, Твери и др.
Проектами автоматизации этих элеваторов предусматривается: выбор и пуск транспортных механизмов, участвующих в маршруте при задании диспетчером начальной и конечной точек маршрута; дистанционноавтоматизированное управление сбрасывающими тележками, поворотными трубами, перекидными клапанами, вентиляторами; дистанционное сблокированное управление всеми задвижками и регулирование открытия подсилосных задвижек на заданную величину; останов любого работающего маршрута с доработкой (разгрузкой) зерна, находящегося на лентах транспортеров и норий; аварийный останов всех механизмов элеватора.
Разработанные в проектах схемы обеспечивают противозавальные блокировки, автоматическое закрытие задвижек опорожняемых емкостей, сигнализацию уровня зерна в ёмкостях, контролируют состояние транспортных механизмов, положение задвижек и работу аспирационных сетей. Пуску любого маршрута предшествует предупредительная звуковая сигнализация.
Для всех механизмов элеватора предусмотрены два режима работы: диспетчерское автоматизированное и местное неблокированное. Включение механизмов грузопотока осуществляется в направлении, обратном движению продукта. Перед остановом транспортных механизмов питающие ёмкости автоматически закрываются, и транспортные механизмы разгружаются от зерна, т. е. происходит доработка. Задвижки открывают ёмкости только при работе соответствующих транспортных механизмов. В аварийной ситуации транспортные механизмы могут быть остановлены без выдержки времени; при этом задвижки питающих емкостей закрываются.
Пуску транспортных механизмов предшествует предупредительная звуковая поэтапная сигнализация.
23
Разработанные функциональные блоки не привязаны к одному типу элеватора и в случае необходимости могут обеспечить работу практически любого элеватора. Изменяется только количество используемых блоков.
Функциональный признак построения блоков является наиболее удобным и перспективным с точки зрения эксплуатации системы ДАУ, позволяя при необходимости быстро отыскать неисправный блок и заменить его заведомо исправным, резервным Обычно на отыскание и замену неисправного блока уходит не более 10 мин, тогда как в системе, выполненной не по функциональному признаку, обслуживающий персонал при осмотрах, ревизиях и ремонте аппаратуры основные профилактические работы вынужден выполнять в стеснённых условиях. В то же время система, состоящая из функциональных, взаимозаменяемых блоков, позволяет производить ревизию или ремонт аппаратуры в лабораториях или в специально приспособленных для этой цели помещениях.
Тема 12 ОПЕРАТИВНЫЙ РАСЧЁТ РАБОТЫ ЭЛЕВАТОРА
12.1 Аналитический расчёт элеватора
Зерновой элеватор снабжён оборудованием для комплексной механизации операций с зерном и характеризуется вместимостью (в тоннах тяжёлого зерна) и оперативной способностью (возможным объёмом операций с зерном в течение суток). Если вместимость элеватора можно определить сравнительно просто, зная геометрические размеры и число силосов, то оперативную способность определить значительно сложнее. Для этого необходимо знать перечень оборудования элеватора, организацию работы, схему элеватора и другие факторы.
Основные закономерности и метод расчёта оперативной способности элеватора были разработаны профессором Д. В. Шумским. В дальнейшем этот метод был развит и дополнен элементами теории вероятности и, в частности, теории массового обслуживания.
Число единиц оборудования, установленного в рабочем здании элеватора, номинальная производительность машин диктуют возможную оперативную способность элеватора, но для точного её определения необходимо знать ещё действительную, фактическую производительность машин и продолжительность их работы в течение суток. О возможной оперативной способности элеватора можно судить только по графику (сменному или суточному) работы всех машин. Суточный или сводный график можно строить на основании частных графиков для операций приёмки зерна из вагонов, автомобилей, с судов, операций отпуска зерна, его очистки, сушки, смешивания помольных смесей и внутренних перемещений. Все эти операции связаны с перемещением зерна цепочкой механизмов, в которой обязательно участвует нория. Поскольку нории диктуют производительность конвейеров, грузоподъёмность весов, вместимость над- и подвесовых бункеров, а также размеры рабочего здания, в частных
24
графиках и аналитических формулах анализируют именно работу норий элеватора на разных операциях при различных схемах.
Различают техническую, паспортную, и фактическую производительность нории на различных операциях. Техническая производительность нории (т/ч) определяется её конструктивными параметрами
Q = 3,6izγνКзап
где i — вместимость ковша, л; z — число ковшей на 1 м длины ленты; ν
— скорость ленты, м/с; γ — насыпная масса зерна, т/м3; Кзап— расчётный коэффициент заполнения ковша.
Техническая производительность достигается норией при нормальной загрузке во время работы, исключая периоды холостой работы и работы с неполной нагрузкой.
Эксплуатационную, фактическую производительность нории Qф (т/ч) определяют за более длительный период, включая периоды работы с пониженной производительностью и без нагрузки.
Очевидно, что Qф меньше Q и лишь как предел может к ней приближаться Qф <Q.
Коэффициент использования норий Ки= Qф /Q
Выявление зависимости Ки от различных факторов и схемы элеватора на различных операциях — задача оперативного расчёта. Тогда Qф = QКи
(Ки<1,0).
Зерно внутри элеватора перемещают отдельными несмешиваемыми партиями. Партией может служить выгруженное из вагона в приёмный бункер зерно определённой массы и качества, Зерно просепарированное и скопившееся в подсепараторном бункере, скопившееся в подсушильном бункере и т. п.
Если рассмотреть теоретическое время (мин) перемещения партии зерна при технической (полной) производительности нории, то
τ = (Е/Q) 60, а фактическое время τф (мин) перемещения той же партии с фактической (эксплуатационной) производительностью нории
τф = (Е/Qф) 60
Сопоставив эти соотношения, получим:
Q = (Е / τф) 60 и Qф=(Е/ τф )60, тогда
Ки = Qф /Q= τ/∑
В дальнейшем для определения расчётного значения Ки оперируют выражением (3). Из анализа частных графиков получают аналитическое выражение τф, рассчитывают его и определяют Ки. Зная Ки, определяют Qф = QKи для разных операций.
Рассматривают также суточные или сменные коэффициенты использования норий элеватора по времени Ки по производительности Кид и средней величине Ки
Киτ=∑ τф/(nн ∙24);
25
КиQ= ∑G/( nн ∙24Q); Киср=∑G/(∑ τсрQ) (6)
где ∑ τср — часы работы нории за сутки (смену); nн — число норий; ∑G
— общая масса зерна, поднятая нориями за сутки, т; Q — техническая производительность нории, т/ч.
Оперативная способность элеватора, возможный суточный объём операций элеватора
∑G = nнQ ∙24Киτ Киср
В качестве примера определения фактического времени (τф) перемещения партии зерна рассматривают операцию приёмки зерна из железнодорожных вагонов. В эту операцию входят: разгрузка вагона в приёмный бункер, передвижка вагонов над бункерами, опорожнение приёмных бункеров на приёмный конвейер, подача зерна норией на весы элеватора, выпуск зерна с весов на надсилосный конвейер и размещение его в соответствующий силос. Эта операция состоит из внешней и внутренней работы. К внешней работе относят разгрузку вагонов в бункера и их передвижение, а также операции, не зависящие от элеваторного оборудования; к внутренней — перемещение разгруженного в бункер зерна (партии) в силосы; она полностью зависит от оборудования элеватора, его схемы и организации работы. Именно для внутренней работы характерно время τф, называемое циклом внутренней работы.
12.2 Анализ внутренней работы элеватора
Каждую партию зерна, выгруженного в приемный бункер из вагона, взвешивают на весах и направляют в силос с соответствующим по качеству зерном, поэтому перемещать последующую партию можно только после освобождения всей цепочки транспортирующих машин (конвейеров, норий, самотечных труб) от предыдущей партии, а также после подготовки маршрута зерна для приемки второй партии (передвижение сбрасывающей тележки надсилосного конвейера или поворот распределительной трубы).
Таким образом, после освобождения бункера от первой партии следует ожидать сигнала об освобождении маршрута от зерна и о готовности его для новой партии. Время ожидания сигнала, разрешающего начать перемещение второй партии зерна (τож), прибавляется к чистому теоретическому времени перемещения партии, увеличивая фактическое время занятости нории. Кроме того, при расчете τф следует учитывать, что при истечении зерна из бункера на приемный конвейер, пропускная способность выпускных отверстий в конце истечения падает, конвейер и нория оказываются недогруженными и время τф увеличивается на величину х1, называемую временем истечения хвостов. Эта задержка происходит в связи с самосортированием зерна при загрузке и истечении.
По исследованиям Д. В. Шумского, при истечении зерна из железобетонных бункеров xl определяют эмпирической формулой
x1= 7.5(Ел + 15) / (Q + 80),
26
где Ел — масса зерна, т; Q номинальная производительность конвейера и нории, т/ч.
Учитывая время ожидания и время истечения хвостов, полное фактическое время занятости нории на перемещении одной партии
τф = τ+ x1 + τож
Первые два слагаемых определяют по приведенным выше формулам) и, а тож — из анализа частного графика операции.
График работы элеватора представляет собой изображение работы машин (во времени) условными символами в определенном масштабе, наполнения и опорожнения бункеров, действий отдельных работников и сигнальных устройств.
12.3 Графическое изображение работы элеватора
В сетке прямоугольных координат х и у в определенном масштабе по оси у откладывают массу зерна, а по оси х — время, тогда тангенс угла наклона линии, характеризующей заполнение бункера, будет соответствовать производительности заполнения (рис. 11.1,а)
у/х = tgα = ЕμЕ /τμτ
где μЕ — масштаб бункера, мм/т; μτ — масштаб времени, мм/мин.
При равномерной подаче зерна в бункер линия заполнения будет прямой, при неравномерной — ломаной или кривой. В последнем случае производительность в каждый момент будет характеризоваться наклоном к оси абсцисс касательной, проведенной к кривой (рис. 11).
На рисунке 11.1 в показано последовательное заполнение приемного бункера за время тн, п и опорожнение его на приемный конвейер производительностью Qтр
27
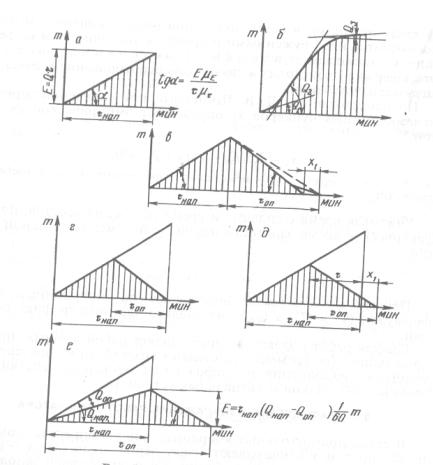
Рисунок 11.1 - . График работы бункера а, б — заполнение с постоянной и с переменной производительностью
соответственно; в—последовательное заполнение и опорожнение при τоп<τнап; d — то же, с учетом задержки истечения; г — одновременное заполнение и опорожнение бункера при временное заполнение и опорожнение
при τоп<τнап
28
В этом случае время опорожнения
τоп = τ+ x1 = Ел ∙60/Qтр + 7,5 (Ел +15) /( Qтр +80).
Линия опорожнения показана сначала прямой, а в конце — кривой, характеризующей задержку истечения х1. Для упрощения линию опорожнения показывают пунктирной прямой (см. рис. 10 в).
На рисунке 11 показан пример одновременного заполнения и опорожнения бункера на конвейер в случае, если производительность опорожнения Qоп>Qнап, а время τоп<τнап. В этом случае тангенс угла наклона линии опорожнения характеризует разность Qоп — Qнап = tgα. Начало опорожнения бункера отстает от начала заполнения на величину τнап — τоп, что сделано для загрузки приемного конвейера на его полную номинальную производительность. С учетом того, что τоп = τ + х1 и что заключительный момент заполнения не может совпасть с моментом полного опорожнения, а отстает на величину х1, график примет следующий вид (рис. д)
На рисунке приведен случай опорожнения при Qоп < Qнап и соответственно τоп > τнап. В этом случае tg α1= Qнап tgα3 = Qоп, tg α2= Qнап —
Qоп
Максимальное скопление зерна (т) в бункере
E = τнап (Qнап - Qоп) /60
Работу норий, конвейеров, самотечных труб изображают полосой, ширина которой пропорциональна производительности машины, а длина соответствует времени работы машины под нагрузкой.
12.4 Анализ внешней работы элеватора
Для определения влияния внешних факторов на коэффициент использования норий работу элеватора обычно оценивают по приёмке зерна из вагонов.
Приёмка зерна из вагонов характеризуется значительной неравномерностью производительности механизмов на выгрузке зерна и транспортирующих механизмов элеватора. Поэтому между приемными механизмами и вагоном необходимо устанавливать приемные бункера.
Расчетное выражение для определения полного времени обработки партии вагонов (τвн) определяют по графикам внешней работы для поперечного и продольного расположения бункеров.
При поперечном расположении бункеров τвн = τр + τм — это сумма продолжительности разгрузки и времени, необходимого на маневры с вагонами. При этом смена вагонов над разгрузочной точкой возможна сразу по окончании разгрузки вагона независимо от остальных вагонов, так как каждый бункер расположен на своем пути.
При продольном расположении бункеров все разгружаемые вагоны стоят на одном пути и могут быть заменены лишь все сразу. Раздельная приемка (перевеска и размещение) из каждого бункера диктует поочередный выпуск зерна на конвейер с интервалом τож, а следовательно, и к неодновременному началу разгрузки вагонов. После разгрузки первого вагона партия ожидает в течение времени tnp до тех пор, пока не закончится
29
разгрузка последнего вагона; затем начинается смена всех вагонов в течение времени τм. Тогда
τвн = τр + τпр + τм
Если время τр и τм принимают по нормам, то время τпр определяют из графика. Для этого сравнивают отрезок времени внизу графика, куда входят время для зачистки и проверки бункера аког после выхода из него зерна первой партии вагонов и время разгрузки последнего вагона второй партии тр с отрезком вверху графика, в который войдет τож+ τ+ τпр (см. рис).
После завершения разгрузки зерна первой партии вагонов из последнего бункера, и окончания разгрузки последнего вагона второй партии вагонов можно начинать смену (маневры) всех вагонов одновременно. Тогда из уравнения τог+ τр = τож + τ+ τпр получим расчетное значение
τпр = τor+ τр - τ - τож τвн =2 τр + τм + τor - τ - τож
Расчетные формулы для определения необходимого числа бункеров примут вид:
при поперечном расположении
nл 2 (τр + τм)/ τф
при продольном расположении
nл ( τр + τм + τor - τ- τож) τф
12.5 Сводный график работы элеватора
Анализ внутренней и внешней работы, проводимой по графикам отдельных элеваторных операций, так называемым частным графикам, дает возможность оценить правильность компоновки схемы элеватора, подбора оборудования, а также организацию различных операций. Критерием такой оценки является коэффициент использования норий (Kи ) для различных операций, схем элеватора и принятой производительности норий. В качестве технологического проектирования утверждены средние значения Kи норий
(табл.11.1.)
Другим вопросом, рассматриваемым в графо-аналитическом расчёте оперативной работы элеватора, является организация работы элеватора в течение всей смены или суток — сводный график работы элеватора, задачей которого является предварительное планирование операций на элеваторе и их подготовка. Без такого плана элеватор не способен выполнить заданный объем операций в сутки, а машины будут простаивать.
Сводный график позволяет правильно оценить проект с точки зрения выполнимости заданного объема операций за сутки, достаточности и степени использования принятого оборудования, вместимости оперативных бункеров, энергоёмкости операций.
Таким образом, сводный график работы элеватора является элементом научной организации труда, способствует увеличению объёма работы элеватора за сутки и смену, повышению производительности труда обслуживающего персонала, лучшему использованию оборудования —
30