
Методички для специальности "Машины и аппараты..." / новосельская
.pdfСмещение оси вала от оси вращения за счет зазоров в опорах составит:
– в месте установки верхней мешалки
|
|
|
|
|
|
Dl1 |
= Dz3 = |
( Б − |
А )z3 |
+ DА, |
|
|
|
|
(5.34) |
|||||||||||||
|
|
|
|
|
|
|
L |
|
|
|
|
|
|
|
||||||||||||||
|
|
|
|
|
|
|
|
|
|
|
|
|
|
|
|
|
|
|
|
|
|
|
|
|
|
|
||
где |
DА – |
|
смещение для радиального |
|
однорядного |
|
шарикового |
|||||||||||||||||||||
подшипника (табл. 5.1), |
DА = 0,03×10–3 |
|
м; |
DБ – |
смещение |
для |
||||||||||||||||||||||
подшипника скольжения нижней опоры (табл. 5.2), DБ = 0,03×10–3 |
м, т. |
|||||||||||||||||||||||||||
е. DА = DБ, |
тогда |
|
|
|
|
|
|
|
|
|
|
|
|
|
|
|
|
|
|
|
|
|
|
|||||
|
Dl1 = |
(0,03×10−3 - 0,03×10−3 ) × 2,08 |
+ 0,03×10−3 = 0,03×10−3 м; |
|
||||||||||||||||||||||||
|
|
|
|
|
|
|
|
|||||||||||||||||||||
|
|
|
|
|
3,85 |
|
|
|
|
|
|
|
|
|
|
|
|
|
|
|
|
|
|
|
|
|
||
– |
в месте установки нижней мешалки |
|
|
|
|
|
|
|
|
|
|
|
||||||||||||||||
|
|
|
|
|
|
Dl 2 = Dz 4 = |
( Б − А )z4 |
+ DА = |
|
|
|
|
|
|
||||||||||||||
|
|
|
|
|
|
|
|
|
|
|
|
|
|
|
||||||||||||||
|
|
|
|
|
|
|
|
|
|
|
|
L |
|
|
|
|
|
|
|
|
|
|
|
|
|
|||
|
= |
(0,03×10−3 - 0,03×10−3 ) ×3,08 |
+ 0,03×10−3 = 0,03×10−3 м; |
|
||||||||||||||||||||||||
|
|
|
|
|
|
|||||||||||||||||||||||
|
|
|
|
|
3,85 |
|
|
|
|
|
|
|
|
|
|
|
|
|
|
|
|
|
|
|
|
|
|
|
– |
в месте установки уплотнения вала |
|
|
|
|
|
|
|
|
|
|
|
|
|
||||||||||||||
|
|
|
|
|
|
Dz1 |
= |
|
( Б − А )z1 |
+ DА = |
|
|
|
|
|
|
|
|||||||||||
|
|
|
|
|
|
|
|
|
|
|
|
|
||||||||||||||||
|
|
|
|
|
|
|
|
|
|
L |
|
|
|
|
|
|
|
|
|
|
|
|
|
|
|
|
|
|
|
= |
|
(0,03×10−3 - 0,03×10−3 ) ×0,6 |
+ 0,03 |
×10 |
−3 |
= 0,03 |
×10 |
−3 |
м. |
|
|||||||||||||||||
|
|
|
|
3,85 |
|
|
|
|
|
|
|
|
||||||||||||||||
|
|
|
|
|
|
|
|
|
|
|
|
|
|
|
|
|
|
|
|
|
|
|
|
|
|
|
||
|
|
|
|
|
|
|
|
|
|
|
|
|
|
|
|
|
|
|
|
|
|
|
|
|
|
|
Таблица 5.1 |
|
|
|
|
|
|
|
Радиальные зазоры А и |
|
Б, мкм, |
|
|
|
|
|
|
||||||||||||||
|
|
|
|
|
по основному ряду в радиальных подшипниках |
|
|
|
|
|||||||||||||||||||
|
|
|
|
|
|
|
|
|
|
|
|
|
|
|||||||||||||||
Внутренний |
|
|
|
|
|
Подшипники качения |
|
|
|
|
|
|
||||||||||||||||
диаметр |
|
однорядный |
|
|
однорядный роликовый * |
|
|
|
двухрядный |
|||||||||||||||||||
подшипников, |
|
|
|
взаимозаменяе |
|
|
невзаимозамен |
|
|
сферический |
||||||||||||||||||
|
шариковый |
|
|
|
|
|
|
|||||||||||||||||||||
|
мм |
|
|
|
|
|
|
|
мый |
|
|
|
|
|
яемый |
|
|
роликовый ** |
||||||||||
30–40 |
|
|
|
12–26 |
|
|
|
20–55 |
|
|
|
|
|
30–45 |
|
|
|
|
25–40 |
|
||||||||
40–50 |
|
|
|
12–29 |
|
|
|
20–55 |
|
|
|
|
|
30–45 |
|
|
|
|
30–45 |
|
||||||||
50–65 |
|
|
|
13–33 |
|
|
|
25–65 |
|
|
|
|
|
35–55 |
|
|
|
|
30–50 |
|
||||||||
65–80 |
|
|
|
14–34 |
|
|
|
30–70 |
|
|
|
|
|
40–60 |
|
|
|
|
40–60 |
|
||||||||
80–100 |
|
|
|
16–40 |
|
|
|
35–80 |
|
|
|
|
|
45–65 |
|
|
|
|
45–70 |
|
||||||||
100–120 |
|
|
|
20–46 |
|
|
|
40–90 |
|
|
|
|
|
50–75 |
|
|
|
|
50–80 |
|
||||||||
120–140 |
|
|
|
23–53 |
|
|
|
45–100 |
|
|
|
|
|
60–90 |
|
|
|
|
60–90 |
|
||||||||
140–160 |
|
|
|
23–58 |
|
|
|
50–115 |
|
|
|
|
|
70–105 |
|
|
|
|
65–100 |
|
81
160–180 |
24–65 |
60–125 |
75–115 |
70–110 |
180–200 |
29–75 |
65–135 |
80–120 |
80–120 |
200–225 |
33–83 |
75–150 |
90–135 |
90–140 |
225–250 |
35–90 |
90–165 |
100–150 |
100–150 |
250–280 |
40–100 |
100–180 |
110–165 |
110–170 |
280–315 |
45–105 |
110–195 |
120–180 |
120–180 |
315–355 |
50–115 |
125–215 |
135–205 |
140–210 |
355–400 |
55–125 |
140–235 |
150–225 |
150–230 |
400–450 |
– |
160–260 |
165–245 |
170–260 |
450–500 |
– |
180–290 |
185–275 |
190–290 |
*Короткие цилиндрические ролики и цилиндрическое отверстие.
**Цилиндрическое отверстие.
Таблица 5.2
Радиальные зазоры в подшипнике скольжения при посадке Н7/е8
Номинальные диаметры вала, dА и dБ, мм |
Зазоры, А и |
Б, мкм |
||||
(предельные) |
||||||
|
|
|
|
max |
|
min |
Свыше 30 до 50 |
114 |
|
50 |
|||
» |
50 |
» |
80 |
136 |
|
60 |
» |
80 |
» |
120 |
161 |
|
72 |
» |
120 |
» |
180 |
188 |
|
85 |
» |
180 |
» 250 |
218 |
|
100 |
|
» |
250 |
» 315 |
243 |
|
ПО |
|
» |
315 |
» 400 |
271 |
|
125 |
Смещение оси вала от оси вращения за счет начальной изогнутости вала (радиальное биение вала) составит:
– в месте установки верхней мешалки
|
|
|
|
|
|
|
εl1 = εz3 = εв |
|
z3 , |
(5.35) |
|
|
|
|
y |
||||||||
где |
eв – начальная изогнутость вала |
в |
точке приведения В, |
||||||||
принимаемая |
по |
табл. 5.3, eв = f(L/d). |
При |
L/d = 3,85/0,065 = 59,2 |
|||||||
eв = 0,09 × 10–3 |
м; тогда |
|
|
||||||||
|
|
ez 3 |
= 0,09 ×10 −3 × 0,96 = 0,086 ×10 −3 м; |
||||||||
– |
в месте установки нижней мешалки |
|
|
||||||||
|
|
el 2 = ez 4 = eв |
|
z 4 = 0,09 ×10−3 × 0,5 = 0,045 ×10−3 м; |
|||||||
|
|
y |
|||||||||
– |
в месте установки уплотнения вала |
|
|
||||||||
|
|
ez1 = eв |
|
z1 = 0,09 ×10−3 ×0,65 = 0,059 ×10−3 м. |
|||||||
|
|
y |
Таблица 5.3
82
Начальная изогнутость ε (z) вала
Отношение длины вала к его диаметру |
Радиальное биение вала в точке |
L/d |
приведения, εв, мм |
До 20 |
0,04 |
Свыше 20 до 50 |
0,05 |
Свыше 50 |
0,06 |
Примечание. Радиальное биение шеек под ступицы перемешивающих устройств и нерабочих поверхностей вала не должно превышать данных значений, увеличенных в 1,5 раза.
Смещение оси вала от оси вращения в точке приведения В за
счет зазоров в опорах вычисляется по формуле |
|
|
|
|
||||||||||||
|
|
|
|
|
DВ = |
А + |
Б , |
|
|
|
|
(5.36) |
||||
|
|
|
|
|
|
2 |
|
|
|
|
|
|
|
|
|
|
|
DВ = |
0,03 ×10−3 + 0,03 ×10−3 |
= 0,03 ×10−3 м. |
|
||||||||||||
|
|
|
|
|
|
|
|
|||||||||
|
|
|
|
|
2 |
|
|
|
|
|
|
|
|
|
|
|
Приведенный эксцентриситет массы вала с мешалками |
||||||||||||||||
находится из уравнения |
|
|
|
|
|
|
|
|
|
|
|
|
|
|||
|
е = |
m1пре1пр + m2пре2пр |
+ D |
|
+ e |
|
, |
(5.37) |
||||||||
|
|
|
|
|
В |
в |
||||||||||
|
|
пр |
|
mэ.пр |
+ mв.пр |
|
|
|
|
|
||||||
|
|
|
|
|
|
|
|
|
|
|
|
|||||
е = |
60,8 × 2,06 ×10−4 +16,5 ×3,96 ×10−4 |
|
+ 0,03 ×10−3 + 0,09 ×10−3 = |
|||||||||||||
|
|
|
|
|||||||||||||
пр |
77,3 |
+ 50 |
|
|
|
|
|
|
|
|
|
|
|
|||
|
|
|
|
|
|
|
|
|
|
|
|
|||||
|
|
|
|
|
= 2,7 ×10−4 |
м. |
|
|
|
|
|
|||||
Динамический прогиб оси вала в точке приведения В |
||||||||||||||||
определяется из уравнения |
|
|
|
|
|
|
|
|
|
|
|
|
||||
|
|
yв = |
епp |
|
, |
|
|
|
|
|
|
|
(5.38) |
|||
|
|
(w / w)2 - |
|
|
|
|
|
|
|
|
||||||
|
|
|
|
|
1 |
|
|
|
|
|
|
|
|
|||
|
|
|
|
|
кр |
|
|
|
|
|
|
|
|
|
|
|
|
yв = |
|
2,7 ×10−4 |
=1,8 ×10−4 м. |
|
|
||||||||||
|
|
|
|
|
|
|
||||||||||
|
(40,3/ 25,5)2 -1 |
|
|
|
|
|
|
|
|
|
|
Динамическое смещение центров тяжести мешалок составит:
– верхней мешалки
|
Аl1 = yв |
|
l1 + εl1 + l1 + e1, |
(5.39) |
|
y |
|||
А |
= 1,8 ×10−4 ×0,96 + 0,086 ×10−3 + 0,03 ×10−3 +1,98 ×10−4 |
= 4,87 ×10−4 м; |
||
l1 |
|
|
|
|
|
– нижней мешалки |
|
83
|
Аl 2 = yв |
|
l 2 + εl 2 + l 2 + e2 , |
(5.40) |
|
y |
|||
А |
= 1,8 ×10−4 × 0,5 + 0,045 ×10−3 + 0,03 ×10−3 +1,98 ×10−4 |
= 3,63 ×10−4 м. |
||
l 2 |
|
|
|
|
Динамическое смещение оси вала в опасном по жесткости сечении в месте установки уплотнения вала рассчитывается по следующей формуле:
|
Аz1 = yв |
|
z1 + ε z1 + z1 , |
(5.41) |
|
|
y |
||||
А |
= 1,8 ×10−4 ×0,38 + 0,059×10−3 |
+ 0,03×10−3 = 1,57 ×10−4 м. |
|||
z1 |
|
|
|
|
|
Динамическое смещение вала в точке приведения В |
|||||
определяется по формуле |
|
|
|||
|
Ав = yв + εв + |
В, |
(5.42) |
||
|
А = 1,8 ×10−4 + 0,09 ×10−3 + 0,03×10−3 |
= 3×10−4 м. |
|||
|
в |
|
|
||
Условие жесткости имеет следующий вид: |
|||||
|
Аz1 ≤ [ А]z1 , |
|
|||
где [А]z1 – |
допускаемое смещение |
вала в |
зоне уплотнительного |
устройства (табл. 5.4). Для сальникового уплотнения [А]z1 = 0,1 × 10–4 , для торцового уплотнения [А]z1 = 2,5 × 10–4 . Таким образом, условие жесткости выполняется лишь при использовании торцового уплотнения: 1,57 × 10–4 < 2,5 × 10–4 .
Таблица 5.4
Допускаемые динамические перемещения вала [A]z j и [A]z1j, мм, в месте установки уплотнения
Частота вращения вала |
|
Уплотнение |
|
||
перемешивающего |
|
|
|
|
|
торцовое |
сальниковое |
манжетное |
гидравлический |
||
устройства, об/мин |
|||||
|
|
|
затвор |
||
До 100 |
0,25 |
0,10 |
0,15 |
0,25 |
|
|
|
|
|
|
|
100–500 |
0,25 |
– |
0,15 |
0,25 |
|
|
|
|
|
|
|
500–750 |
0,15 |
– |
0,10 |
0,25 |
|
|
|
|
|
|
|
750–2900 |
0,10 |
– |
– |
– |
|
|
|
|
|
|
Сосредоточенная центробежная сила, действующая на мешалки, рассчитывается по следующим формулам:
– на верхнюю мешалку
F = m w2 A |
, |
(5.43) |
|
1 1 |
l1 |
|
|
84
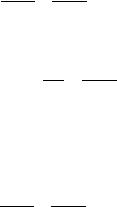
F1 = 66 × 25,52 × 4,87 ×10−4 = 20,9 Н;
– на нижнюю мешалку
F = m |
w2 A |
, |
(5.44) |
2 2 |
l 2 |
|
|
F2 = 66 × 25,52 ×3,63×10−4 = 15,6 Н.
Приведенная центробежная сила, действующая в точке приведения В, от собственной массы вала находится по следующей формуле:
F |
= m |
w2 A , |
(5.45) |
в.пр |
в.пр |
в |
|
Fв.пр = 50 × 25,52 ×3 ×10−4 = 9,75 Н.
Реакции опор вычисляются по следующим формулам:
– реакция опоры А (верхней)
R = |
B |
+ |
Fв.пр |
|
1 |
|
, |
||
|
|
|||
A |
L |
|
2 |
|
где |
|
|
||
|
|
|
|
В1 = F1(L - l1) + F2 (L - l2 )
В1 = 20,9 × (3,85 - 2,08) +15,6 × (3,85 - 3,08) = 49 Н × м,
RA = 49 + 9,75 =17,6 Н; 3,85 2
– реакция опоры Б (нижней)
RБ = B3 + Fв.пр ,
L 2
где
B3 = F1L1 + F2l2 ,
B3 = 20,9 × 2,08 +15,6 ×3,08 = 91,5 Н× м,
(5.46)
(5.47)
(5.48)
(5.49)
RБ = 91,5 + 9,75 = 28,6 Н. 3,85 2
Изгибающий момент в опасном сечении составит:
– в промежутке между А и В
|
|
Ми z 2 = RA z2 , |
(5.50) |
|
Ми z 2 |
= |
49 ×3,85 |
= 94,3 Н×м; |
|
|
|
|||
|
2 |
|
|
– в промежутке между В и Б
85
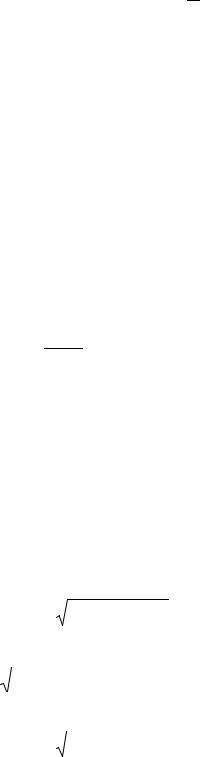
Ми z 3 = RA z3 - Fв.пр z3 - L ,
2
|
|
|
3,85 |
|
|
|
Ми z3 |
= 49 × 2,08 - 9,75× 2,08 |
- |
|
|
|
= 100,4 Н×м. |
2 |
|
|||||
|
|
|
|
|
|
Крутящий момент в опасных сечениях равен:
– в середине пролета вала
|
|
Мк z 2 |
= |
N1 + N2 |
, |
||
|
|
w |
|||||
|
|
5300 + 5300 |
|
||||
Мк z 2 |
= |
= 415,6 Н×м; |
|||||
|
|||||||
|
25,5 |
|
|
|
|
– в месте установки верхней мешалки
(5.51)
(5.52)
Мк z3 |
= |
N2 |
, |
(5.53) |
|
w |
|||||
|
|
|
|
Мк z3 = 5300 = 207,8 Н×м. 25,5
Момент сопротивления вала в сечениях z2, z3 находится по формуле
|
|
|
W |
= W |
= |
pd 3 |
(5.54) |
|
|
|
, |
||||
|
|
|
z 2 |
z 3 |
|
32 |
|
|
|
|
|
|
|
|
|
W |
= W |
= |
3,14 × 0,0653 |
= 2,69 ×10−5 |
м3. |
||
|
|||||||
z 2 |
z 3 |
32 |
|
|
|
||
|
|
|
|
|
Эквивалентные напряжения в этих сечениях рассчитываются по следующим формулам:
|
|
|
|
|
|
M 2 |
+ M 2 |
|
||||
|
sэкв z 2 = |
|
и z 2 |
|
|
к z 2 |
, |
(5.55) |
||||
|
|
Wz 2 |
|
|
||||||||
|
|
|
|
|
|
|
|
|
|
|||
sэкв z 2 |
= |
|
94,32 + 415,62 |
|
=1,58 ×107 Па; |
|
||||||
|
|
|
|
|
||||||||
|
|
|
2,69 ×10−5 |
|
|
|
|
|
|
|||
|
|
|
|
|
|
M 2 |
+ M 2 |
|
|
|||
|
sэкв z3 = |
|
|
и z3 |
|
|
к z3 |
, |
(5.56) |
|||
|
|
|
Wz3 |
|
||||||||
|
|
|
|
|
|
|
|
|
|
86

sэкв z3 |
= |
100,42 + 208,72 |
= 1,04 ×107 |
Па. |
||
|
|
|||||
|
|
2,69 ×10−5 |
|
|||
Допускаемые напряжения в сечениях zi определяются по |
||||||
формуле |
|
|
εмσ−1 |
|
||
|
|
[s]zi = |
|
|||
|
|
|
, |
(5.57) |
||
|
|
Кσ zi nmin |
где eм – масштабный фактор (коэффициент влияния абсолютных размеров вала), определяемый по рис. 5.6; s–1 – предел выносливости материала вала, s–1 » (0,4 – 0,5) sв; sв – предел прочности материала вала, МПа; Кσ zi – эффективный коэффициент концентрации напряжений, определяемый по табл. 5.5; пmin – минимальный запас прочности вала.
|
|
εм |
|
|
|
|
|
|
|
|
|
|
|
|
|
|
|
|
|
|
|
|
|
|
|
|
|
|
|
|
|
|
|
|
|
|
|
|
|
|
|
|
|
|
|
|
|
|
|
|
|
||
|
0,8 |
|
|
|
|
|
|
|
|
|
|
|
|
|
|
|
|
|
|
|
|
|
|
|
||
|
|
|
|
|
|
|
|
|
|
|
|
|
|
|
|
1 |
|
|
|
|
|
|
||||
|
|
|
|
|
|
|
|
|
|
|
|
|
|
|
|
|
|
|
|
|
|
|
|
|||
|
|
|
|
|
|
|
|
|
2 |
|
|
|
|
|
|
|
|
|
|
|
|
|||||
|
|
|
|
|
|
|
|
|
|
|
|
|
|
|
|
|
|
|
||||||||
0,6 |
|
|
|
|
|
|
|
|
|
|
|
|
|
|
||||||||||||
|
|
|
|
|
|
|
|
|
|
|
|
|
|
|
|
|
|
|
|
|
|
|
||||
|
|
|
|
|
|
|
|
|
|
|
|
|
|
|
|
|
|
|
|
|
|
|
|
|
||
0,4 |
|
|
|
|
|
|
|
|
|
|
|
|
|
|
|
|
|
|
|
|
|
|
|
|||
|
|
|
|
|
|
|
|
|
|
|
|
|
|
|
|
|
|
100 |
|
150 |
200 |
300 |
|
|
||
|
|
|
|
|
|
|
|
|
20 |
|
30 |
|
40 |
50 |
d, мм |
|||||||||||
|
|
|
0,5 |
|
10 |
|||||||||||||||||||||
|
|
|||||||||||||||||||||||||
|
|
|
|
|
|
|
|
|
|
|
|
|
|
|
|
|
|
|
|
|
|
|
|
|
|
|
|
|
|
|
|
|
|
|
|
|
|
|
|
|
|
|
|
|
|
|
|
|
|
|
|
|
|
Рис. 5.6. Зависимость масштабного фактора εм от диаметра d и материала вала:
1 – углеродистая сталь;
2 – легированная сталь
Для вала d = 65 мм, изготовленного из легированной стали Х18Н10Т, согласно рис. 5.6, коэффициент eм = 0,67, а при температуре 80° С предел выносливости s–1 = 200 МПа. Так как на валу в местах установки мешалок имеются шпоночные канавки, выполненные торцовой фрезой, то Кσ z3 = 1,14 (согласно табл. 5.5). В неослабленном сечении Кσ z2 = 1. Приняв ориентировочно пmin = 2, получим
[s]z 2 |
= |
|
0,67 × 2 |
×108 |
|
= 6,7 ×107 Па; |
|
|
|||||
|
1× 2 |
|
|
|||
[s]z3 = |
0,67 × 2 |
×108 |
|
= 5,9 ×107 Па. |
1,14 × 2
Таблица 5.5
87
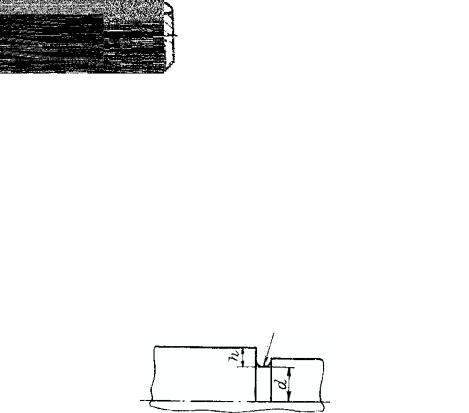
Эффективный коэффициент концентрации напряжений Кσ zi
Предел |
|
|
|
|
|
|
|
|
|
|
|
|
|
|
|
|
прочности |
|
|
|
|
|
|
|
|
|
|
|
|
|
|
|
|
материала, |
|
|
|
|
|
|
|
|
|
|
|
|
|
|
|
|
|
|
|
|
|
Кσ zi |
|
|
|
|
|
|
|||||
σв, МПа |
|
|
|
|
|
|
|
|
|
|
|
|
|
|
||
|
|
для валов со шпоночной канавкой, |
|
|
для валов |
|||||||||||
|
|
|
выполненной фрезой |
|
|
|
с метрической |
|||||||||
|
|
торцовой |
|
|
|
дисковой |
|
|
резьбой |
|||||||
400 |
|
1,30 |
|
1,51 |
|
|
|
|
1,45 |
|||||||
500 |
|
1,38 |
|
1,64 |
|
|
|
|
1,78 |
|||||||
600 |
|
1,46 |
|
1,76 |
|
|
|
|
1,96 |
|||||||
700 |
|
1,54 |
|
1,89 |
|
|
|
|
2,20 |
|||||||
800 |
|
1,62 |
|
2,01 |
|
|
|
|
2,32 |
|||||||
900 |
|
1,69 |
|
2,14 |
|
|
|
|
2,47 |
|||||||
1000 |
|
1,77 |
|
2,26 |
|
|
|
|
2,61 |
|||||||
1200 |
|
1,92 |
|
2,50 |
|
|
|
|
2,90 |
|||||||
|
|
|
|
|
|
|
|
|
|
|
|
Окончание табл. 5.5 |
||||
|
|
|
|
|
|
|
|
|
|
|
|
|
|
|
|
|
|
|
|
|
|
|
|
|
r |
|
|
|
|
|
|
||
|
|
|
|
|
|
|
h |
|
|
|
|
|
|
|||
|
|
|
|
|
|
|
|
|
|
|
|
|
|
|
|
|
|
|
|
|
|
|
|
|
|
|
|
|
|
|
|
|
|
|
|
|
|
|
|
|
|
|
|
|
|
|
|
|
||
Предел |
|
|
|
|
|
|
|
|
|
d |
|
|
|
|
|
|
|
|
|
|
|
|
|
|
|
|
|
|
|
|
|
|
|
|
|
|
|
|
|
|
|
|
|
|
|
|
|
|
|
|
прочности |
|
|
|
|
|
|
|
|
|
|
|
|
|
|
|
|
|
|
|
|
|
Кσ zi |
|
|
|
|
|
|
|||||
материала, |
|
|
|
|
|
|
|
|
|
|
|
|||||
σв, МПа |
|
|
|
для валов с выточкой при h/r |
|
|
|
|
||||||||
|
|
|
0,5 |
|
|
|
|
|
|
|
|
|
|
1 |
||
|
|
|
|
|
|
|
|
|
|
|
|
|
|
|||
|
|
|
|
|
|
при r/d |
|
|
|
|
|
|
||||
|
0,01 |
|
0,02 |
0,03 |
|
0,05 |
|
|
0,10 |
0,01 |
|
0,02 |
||||
400 |
1,88 |
|
1,79 |
1,72 |
|
1,61 |
|
|
1,44 |
2,09 |
|
1,99 |
||||
500 |
1,93 |
|
1,84 |
1,77 |
|
1,66 |
|
|
1,48 |
2,15 |
|
2,05 |
||||
600 |
1,98 |
|
1,82 |
1,82 |
|
1,71 |
|
|
1,52 |
2,21 |
|
2,11 |
||||
700 |
2,04 |
|
1,95 |
1,87 |
|
1,77 |
|
|
1,55 |
2,27 |
|
2,17 |
||||
800 |
2,09 |
|
2,00 |
1,92 |
|
1,82 |
|
|
1,59 |
2,37 |
|
2,20 |
||||
900 |
2,15 |
|
2,06 |
1,97 |
|
1,88 |
|
|
1,62 |
2,39 |
|
2,28 |
||||
1000 |
2,20 |
|
2,11 |
2,02 |
|
1,93 |
|
|
1,66 |
2,45 |
|
2,35 |
||||
1200 |
2,31 |
|
2,22 |
2,12 |
|
2,04 |
|
|
1,73 |
2,57 |
|
2,49 |
||||
|
|
|
|
|
|
|
|
|
|
|
|
|
|
|||
Предел |
|
|
|
|
|
Кσ zi |
|
|
|
|
|
|
||||
|
|
|
для валов с выточкой при h/r |
|
|
|
|
|||||||||
прочности |
|
|
|
|
|
|
|
|||||||||
|
1 |
|
2 |
|
|
|
|
|
|
|
3 |
|||||
материала, |
|
|
|
|
|
|
|
|
|
|||||||
|
|
|
|
|
при r/d |
|
|
|
|
|
|
|||||
σв, МПа |
|
|
|
|
|
|
|
|
|
|
|
|||||
0,03 |
|
0,05 |
0,01 |
|
0,02 |
|
|
0,03 |
0,01 |
|
0,02 |
|||||
|
|
|
|
|
|
|||||||||||
400 |
1,91 |
|
1,79 |
2,29 |
|
2,18 |
|
|
2,10 |
2,38 |
|
2,28 |
||||
500 |
1,97 |
|
1,85 |
2,36 |
|
2,25 |
|
|
2,16 |
2,47 |
|
2,35 |
||||
600 |
2,03 |
|
1,91 |
2,43 |
|
2,32 |
|
|
2,22 |
2,56 |
|
2,42 |
88
700 |
2,08 |
1,97 |
2,50 |
2,38 |
2,28 |
2,64 |
2,49 |
800 |
2,14 |
2,03 |
2,56 |
2,45 |
2,35 |
2,73 |
2,56 |
900 |
2,19 |
2,09 |
2,63 |
2,51 |
2,41 |
2,81 |
2,63 |
1000 |
2,25 |
2,15 |
2,70 |
2,58 |
2,47 |
2,90 |
2,70 |
1200 |
2,36 |
2,27 |
2,84 |
2,71 |
2,59 |
3,07 |
2,84 |
Иными словами, условия прочности выполняются
sэкв z 2 £ [s]z 2 , 1,58 ×107 Па < 6,7 ×107 Па;
sэкв z3 £ [s]z3 , 1,04 ×107 Па < 5,9 ×107 Па.
Таким образом, вал диаметром 65 мм и длиной 3,85 м при заданной нагрузке является виброустойчивым, прочным и достаточно жестким в опасных сечениях.
ЛИТЕРАТУРА
1. Лащинский, А. А. Конструирование сварных химических аппаратов / А. А. Лащинский. – Л.: Машиностроение, 1981. –
382с.
2.ГОСТ 24306–80. Сосуды и аппараты. Технические требования. – М.: Госкомитет СССР по стандартам, 1980. – 46 с.
3.ГОСТ 14249–83. Сосуды и аппараты. Нормы и методы расчета на прочность. – М.: Госкомитет СССР по стандартам, 1983.
–62 с.
4.Уайлд, Д. Оптимальное проектирование / Д. Уайлд. – М.: Мир,
1981. – 271 с.
5.Дитрих, Я. Проектирование и конструирование. Системный подход / Я. Дитрих. – М.: Мир, 1981. – 454 с.
6.Джонс, Дж. К. Методы проектирования / Дж. К. Джонс. – М.:
Мир, 1986. – 626 с.
7.Остриков, А. Н. Расчет и конструирование машин и аппаратов пищевых производств / А. Н. Остриков, О. В. Абрамов. –
СПб.: ГИОРД, 2004. – 352 с.
8.Лащинский, А. А. Основы конструирования и расчета химической аппаратуры / А. А. Лащинский, А. Р. Толчинский. – Л.: Машиностроение, 1970. – 712 с.
89
9.Васильцов, Э. А. Аппараты для перемешивания жидких сред: справ. пособие / Э. А. Васильцов, В. Г. Ушаков. – Л.: Машиностроение, 1979. – 272 с.
10.Тимонин, А. С. Основы конструирования и расчета химикотехнологического оборудования: справочник / А. С. Тимонин. – Т. 1. – Калуга: изд-во Н. Бочкаревой, 2006. – 592 с.
11.Тимонин, А. С. Основы конструирования и расчета химикотехнологического оборудования: справочник / А. С. Тимонин. – Т. 2. – Калуга: изд-во Н. Бочкаревой, 2006. – 674 с.
12.Соколов, В. И. Основы расчета и конструирования деталей и узлов пищевого оборудования / В. И. Соколов. – М.: Машиностроение,
1963. – 430 с.
13.Канторович, З. Б. Основы расчета химических машин и аппаратов / З. Б. Канторович. – М.: Машиностроение, 1960. – 743 с.
14.Михалев, М. Ф. Расчет и конструирование машин и аппаратов / М. Ф. Михалев. – Л.: Машиностроение, 1984. – 299 с.
15.Николаев, Г. А. Сварные конструкции / Г. А. Николаев, С. А. Куркин. – М.: Машиностроение, 1971. – 758 с.
16.Вихман, Г. Л. Основы конструирования аппаратов и машин нефтеперерабатывающих заводов / Г. Л. Вихман, С. А. Круглов. – М.: Машиностроение, 1978. – 326 с.
17.Харламов, С. В. Практикум по расчету и конструированию машин и аппаратов пищевых производств / С. В. Харламов. – Л.: Агропромиздат, 1991 – 256 с.
18. |
Машины |
и аппараты |
химических |
производств / |
под ред. |
В. Л. Соколова. – |
Л.: Машиностроение, 1982. – 384 с. |
|
|||
19. |
Правила |
устройства и |
безопасной |
эксплуатации |
сосудов, |
работающих под давлением. – Минск: ДИЭКОС, 2006. – 2003 с.
90