
Методички для специальности "Машины и аппараты..." / новосельская
.pdfГидростатическое давление учитывается в расчетах на прочность, если оно составляет 5% и более от газового. Если эта величина меньше, то влияние гидростатического давления идет в коэффициент запаса прочности.
Все сосуды перед сдачей в эксплуатацию подвергаются гидравлическим испытаниям (проверка герметичности и прочности сварных швов).
Если сосуд работает под вакуумом, то он подвергается гидроиспытаниям (наливом водой).
Если сосуд работает под избыточным давлением, то давление гидроиспытаний устанавливается в зависимости от способа изготовления: литые, кованые, сварные.
Давление гидроиспытаний ргидр = 1,25р, но не менее р + 0,2 МПа. Гидроиспытания проводятся в течение 15–20 мин, т. е.
кратковременно. За это время материал не успевает достичь предела текучести, поэтому расчет ведется по законам упругих деформаций, неучтенные деформации учитываются коэффициентом запаса прочности. При окончательном проверочном расчете толщины стенки проводится расчет на давление гидроиспытаний.
Допускаемое напряжение [σ], МПа, при расчете по предельным нагрузкам сосудов и аппаратов, работающих при статических
однократных нагрузках, определяется: |
|
|
|
|
|
|
|
|
|
|
||||||
– для углеродистых и низколегированных сталей |
|
|
|
|||||||||||||
|
σ |
т |
|
σ |
0,2 |
|
σ |
в |
|
σ |
д10 |
5 |
|
σ |
5 |
|
[σ] = ηmin |
|
или |
|
; |
|
; |
|
|
; |
1%10 |
|
; (3.3) |
||||
|
|
|
|
|
|
|
|
|
|
|
||||||
|
пт |
пт |
пв |
пд |
|
|
пп |
|
|
– для аустенитных сталей |
|
|
|
|
|
|
|
|
|
|
||
|
σ |
σв |
|
σ |
д10 |
5 |
|
σ |
5 |
|
|
|
[σ] = η min |
1,0 |
; |
; |
|
|
; |
1%10 |
|
, |
(3.4) |
||
|
|
|
|
|
|
|
||||||
|
пт |
пв |
пд |
|
|
пп |
|
|
|
|||
|
|
|
|
|
|
где η – поправочный коэффициент к допускаемым напряжениям, учитывающий коррозионность среды (должен быть равен единице); σт – минимальное значение предела текучести при расчетной температуре, МПа; σв – минимальное значение предела прочности при расчетной температуре, МПа; σ0,2 – минимальное значение условного предела текучести при расчетной температуре (напряжение, при котором остаточное удлинение составляет 0,2%), МПа; σ1,0 – минимальное значение условного предела текучести при расчетной температуре (напряжение, при котором остаточное удлинение
21
составляет 1,0%), МПа; σд105 – среднее значение предела длительной прочности за 105 ч при расчетной температуре, МПа; σ1%105 – средний 1%-ный предел ползучести за 105 ч при расчетной температуре, МПа.
Если сосуды и аппараты работают при многократных статических нагрузках и количество циклов нагружения от давления, стесненности температурных деформаций или других воздействий не превышает 103, то такая нагрузка в расчетах на прочность условно считается однократной. При установлении числа циклов нагружения не учитывается колебание нагрузки в пределах 15% от расчетной.
Предел ползучести используется для определения допускаемого напряжения в тех случаях, когда отсутствуют данные по пределу длительной прочности или по условиям эксплуатации. Следовательно, необходимо ограничить величину деформации (перемещения).
В случае отсутствия данных по условному пределу текучести при 1%-ном остаточном удлинении допускаемое напряжение для аустенитной стали вычисляют по следующей формуле:
[σ] = σ20т |
, или [σ] = |
σ0,220 |
. |
(3.5) |
|
||||
пт |
|
пт |
|
Коэффициенты запаса прочности п в рабочих условиях принимаются равными по пределу прочности пв = 2,4; по пределу текучести пт = 1,5; по пределу длительной прочности пд = 1,1; по пределу ползучести пп = 1,1.
Коэффициент прочности сварного шва ϕр выбирается в зависимости от типа сварного шва и способа сварки [1, 3, 15] (таблица).
Самым прочным является стыковой шов с двухсторонним проваром. При автоматической и ручной сварке ϕр = 1. Недостатком является то, что при малых диаметрах трудно выполнить внутренний шов. При одностороннем проваре автоматической сваркой ϕр = 0,95, при ручной сварке ϕр = 0,9.
Иногда конструкцию укрепляют накладным листом и ϕр = 0,95 при ручной и автоматической сварке.
Таблица
Коэффициенты прочности сварных швов (ГОСТ 14249–83)
Вид сварного шва |
Значение коэффициентов |
|
прочности сварных швов |
||
|
22
|
|
|
Длина |
Длина |
|
|
|
контролируе |
контролируе |
|
|
|
мых швов от |
мых швов от |
|
|
|
общей длины |
общей длины |
|
|
|
составляет |
составляет |
|
|
|
100% |
от 10 до 50% |
Стыковой или тавровый с двухсторонним |
|
|
||
сплошным |
проваром, |
выполняемый |
|
|
автоматической и полуавтоматической сваркой |
1,0 |
0,9 |
||
Стыковой с подваркой корня шва или тавровый с |
|
|
||
двухсторонним |
сплошным |
проваром, |
|
|
выполняемый вручную |
|
1,0 |
0,9 |
|
Стыковой, доступный к сварке только с одной |
|
|
||
стороны и имеющий в процессе сварки |
|
|
||
металлическую подкладку со стороны корня шва, |
|
|
||
прилегающую по всей длине шва к основному |
|
|
||
металлу |
|
|
0,9 |
0,8 |
Стыковой, выполняемый автоматической и |
|
|
||
полуавтоматической сваркой с одной стороны с |
|
|
||
флюсовой или керамической подкладкой |
0,9 |
0,8 |
||
Стыковой, выполняемый вручную с одной стороны |
0,9 |
0,65 |
||
Втавр, с конструктивным зазором свариваемых |
|
|
||
деталей |
|
|
0,8 |
0,65 |
Примечание. Объем контроля определяется техническими требованиями на изготовление и правилами Госгортехнадзора СССР.
Сварка внахлест прочная, но при малых толщинах металла наступает прогар, поэтому не рекомендуется таким швом варить металл толщиной менее 6 мм.
Стыковые (тавровые) швы – самые слабые. Рекомендуются для сварки соединений с плоскими днищами. При автоматической сварке
ϕр = 0,85, при ручной – ϕр = 0,8.
По требованию ГОСТа, исходя из условий прочности, не рекомендуется сваривать металл толщиной менее 3 мм. Так как при повышенных температурах тонкий металл подвергается ползучести и релаксации и разрушается значительно раньше, чем основной металл.
Отверстия являются концентраторами напряжения, поскольку ослабляют сечение. Ослабление сечения характеризуется соотношением диаметра аппарата к диаметру отверстия. В соответствии с этим не укрепляются и не учитываются отверстия, установленные в цилиндрических корпусах.
23
Коэффициент ослабления конструкции отверстиями определяется по формуле
ϕотв = 1− ∑ dотв , |
(3.6) |
D |
|
где ∑ dотв – сумма диаметров отверстий, м. |
|
Исполнительная толщина стенки элемента сосуда и аппарата s, мм, |
|
вычисляется по следующей формуле: |
|
s ³ sR + с, |
(3.7) |
где с – величина прибавки к расчетной толщине, мм. |
|
Величина прибавки с, мм, рассчитывается по формуле |
|
с = с1 + с2 + с3, |
(3.8) |
где с1 – конструктивная добавка на отрицательный допуск металла, мм; с2 – конструктивная добавка на механическую коррозию (эрозию), мм; с3 – конструктивная добавка на химическую коррозию, мм.
Допускаемое внутреннее избыточное давление [р], МПа, определяется по следующей формуле:
[ р] = |
2 |
[σ] ϕр (s − с) |
|
|
|
|
. |
(3.9) |
|
|
|
|||
|
|
D + (s − с) |
|
При соблюдении условия (3.9) расчетная толщина стенки принимается к проекту.
Для сосудов и аппаратов, работающих при многократных нагрузках с количеством циклов нагружения от давления, стесненности температурных деформаций или других воздействий более 103 за весь срок эксплуатации, кроме расчета на прочность, выполняется проверка на усталостную прочность.
3.3.Расчет от наружного давления
Втех случаях, когда технологический процесс протекает в условиях вакуума или аппарат снабжен рубашкой, стенки сосуда нагружены снаружи. Сосуды, работающие под внешним давлением, могут разрушаться еще до того, как в их стенках возникнут опасные напряжения. При этом теряется форма цилиндрического сосуда. По аналогии с продольным изгибом стержней это явление получило название потери устойчивости оболочки. Внешнее давление, которое вызывает в оболочке деформации, ведущие к потере устойчивости, называется критическим давлением, так как эта
24

потеря устойчивости является следствием невозможности длительного существования данной геометрической формы при данных геометрических и механических параметрах. Под потерей устойчивости оболочки понимается резкое качественное изменение характера деформации элемента оболочки, вызванное характерным значением внешнего давления. При этом образующая не теряет своей прямолинейной формы, оболочка деформируется в поперечном сечении с возникновением волн. Установлено, что длинные оболочки при потере устойчивости сплющиваются с образованием двух волн, а короткие – тридцати двух волн [17, 18].
Замена внутреннего давления внешним может привести к тому, что при некотором определенном значении внешнего давления оболочка, рассчитанная на прочность, подвергнется опасным деформациям и даже разрушению, хотя возникающие в стенках оболочки напряжения будут ниже разрушающих. Нагрузка, при которой начальная форма равновесия перестает быть устойчивой, называется критической.
Таким образом, расчет оболочки на устойчивость в принципе сводится к определению величины критического давления, значение которого позволяет сделать вывод о работоспособности конструкции.
Расчет оболочек от наружного давления ведется в зависимости от отношения их длины к внутреннему диаметру. Оболочка рассматривается как длинная, если соблюдается следующее условие:
|
lR |
> |
D |
|
, |
(3.10) |
|
|
|
|
|||
|
D |
2(s - c) |
|
|||
где lR – расчетная длина обечайки, |
находящейся под |
действием |
наружного давления, м. Принимается в зависимости от ее конфигурации (рис. 3.2).
Расчетная толщина стенки сосуда sR, мм, находится по формуле
|
|
−2 |
|
1,1рR D |
|
||
sR |
= max K2 D ×10 |
|
; |
|
|
|
(3.11) |
|
|
|
|||||
|
|
|
|
|
2[s] |
|
где K2 – коэффициент, определяемый в зависимости от значения коэффициентов K1 и K3 (рис. 3.3); D – внутренний диаметр аппарата, м; рR – расчетное давление, Па; 2 – коэффициент, означающий, что расчет ведется по максимальным кольцевым напряжениям; [s] – допускаемое напряжение, МПа.
25
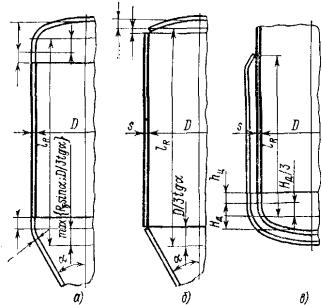
hц Hд
s
hц
Rб
H/3
Hд
H/3
|
|
|
|
|
D |
|
|
|
|
|
|
|
|
D |
|
|
|
|
|
|
|
|
|
D |
|
||||||
|
s |
|
|
|
s |
|
|
|
|
|
|||||||||||||||||||||
|
|
/3tg} |
|
|
|
|
|
|
|
|
|
|
|
|
|
|
|
|
|
|
|
|
|
|
|
|
|
|
|
||
l |
|
|
|
|
|
|
|
|
|
|
|
|
|
|
|
|
l |
|
|
|
|
|
|
||||||||
|
|
l |
|
|
|
|
|
|
|
|
|
|
|
|
|
|
|
|
|
|
|||||||||||
R |
|
D |
|
|
|
|
|
|
R |
|
|
|
|
|
|
|
|
|
|
|
|
R |
|
|
|
|
|||||
|
|
|
|
|
|
|
|
|
|
|
|
|
|
|
|
|
|
|
|
|
|
|
|
|
|
||||||
|
|
|
|
|
|
|
|
|
|
|
|
|
|
|
|
|
|
|
|
|
|
|
|
|
|
|
|
|
|||
|
|
|
|
|
|
|
|
|
|
|
|
|
|
|
|
|
|
|
|
|
|
|
|
|
|
|
|
|
|||
|
|
|
|
|
|
|
|
|
|
|
|
|
|
|
|
|
|
|
/3 |
|
|
|
|
||||||||
|
|
|
|
|
|
|
|
|
|
|
|
ц |
|
|
|
|
|
|
|
|
|||||||||||
|
|
α; |
|
|
|
|
|
|
|
|
|
|
|
|
|
|
|
|
|
|
|
|
|
д |
|
|
|||||
|
|
|
|
|
/3tgα |
|
|
|
h |
|
|
|
H |
|
|
|
|||||||||||||||
|
|
|
б |
|
|
|
|
|
|
|
|
|
|
|
|
|
|
|
|||||||||||||
|
|
sin |
|
|
|
|
|
|
|
D |
|
|
|
|
|
|
|
|
|
|
|
|
|
|
|
||||||
|
|
|
|
|
|
|
|
|
|
|
|
|
|
|
|
|
|
|
|
||||||||||||
|
|
max{R |
|
|
|
|
|
|
|
|
|
|
|
|
|
|
|
|
|
|
|
||||||||||
|
|
H |
|
|
|
|
|
|
|
|
|
||||||||||||||||||||
|
|
|
|
|
|
|
|
|
|
|
|
|
|
|
|
|
|
|
|
д |
|
|
|
|
|
|
|
|
|
|
|
|
|
|
|
|
|
|
|
|
|
|
|
|
|
|
|
|
|
|
|
|
|
|
|
|
|
|
|
|
|
|
|
|
|
|
|
|
|
|
|
|
|
|
|
|
|
|
|
|
|
|
|
|
|
|
|
|
|
|
|
||||
|
|
|
|
|
|
|
|
|
|
|
|
|
|
|
|
|
|
|
|
|
|
|
|
|
|
|
|
|
|||
|
|
|
|
|
α |
|
|
|
|
|
|
|
|
|
|
|
|
||||||||||||||
|
α |
|
|
|
|
|
|
|
|
|
|
|
|
|
|
|
|
|
|
|
|
||||||||||
|
|
|
|
|
|
|
|
|
|
|
|
|
|
|
|
|
|
|
|
|
|
|
|||||||||
|
|
|
|
|
а |
|
|
|
|
|
|
б |
|
|
|
|
|
|
|
|
|
|
|
в |
|||||||
|
|
|
|
|
|
|
|
|
|
|
|
|
|
|
|
|
|
|
|
|
|
|
|
|
|
|
|
|
|
|
|
Рис. 3.2. Конструкция гладких цилиндрических |
|
|
|
обечаек (корпусов) аппаратов: |
|
а – |
с отбортованными эллиптическим |
|
|
и коническим днищами; |
|
б – |
с неотбортованными сферическим |
|
|
и коническим днищами; |
|
в – с рубашкой на нижней части аппарата |
|
|
Исполнительная толщина стенки элемента сосуда s, мм, |
||
определяется по следующей формуле [1, 2] |
|
|
|
s ³ sR + с, |
(3.12) |
где с – величина прибавки к расчетной толщине, мм. |
|
|
Величина прибавки с, мм, рассчитывается по формуле |
|
|
|
с = с1 + с2 + с3, |
(3.13) |
где с1 – конструктивная добавка на отрицательный допуск металла, мм; с2 – конструктивная добавка на механическую коррозию (эрозию), мм; с3 – конструктивная добавка на химическую коррозию, мм.
Значение коэффициентов K1 и K3 вычисляется по следующим формулам:
K = |
|
пи р |
|
; |
K = |
lR |
, |
(3.14) |
2, 4 |
×10−6 |
|
|
|||||
1 |
Е |
3 |
D |
|
||||
|
|
|
|
|
|
|
где пи – коэффициент запаса устойчивости, пи = 2,4; Е – модуль упругости материала стенки, МПа.
26
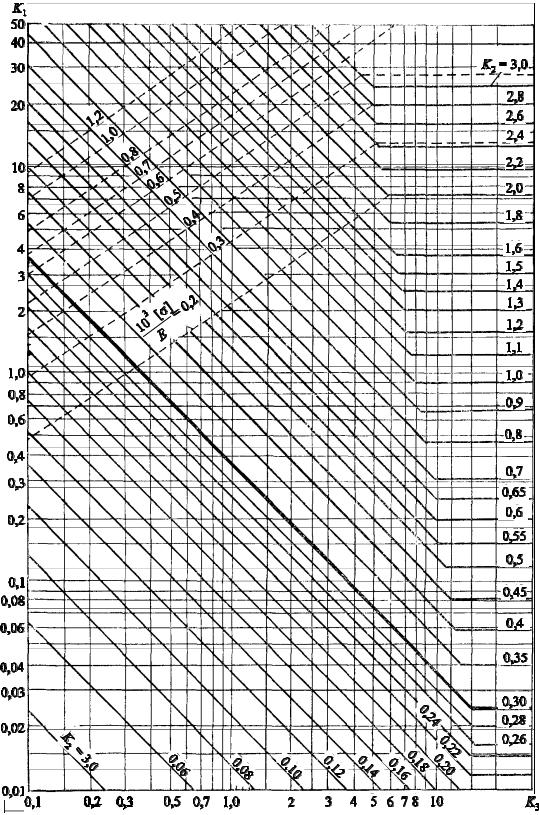
Рис. 3.3. Номограмма определения толщины |
цилиндрических стальных обечаек, работающих под наружным давлением |
27
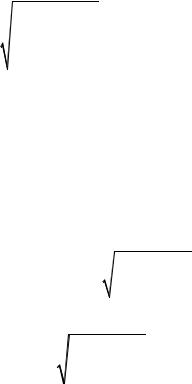
Допускаемое наружное давление [р], МПа, определяется по формуле
[ р] = |
|
[ р]р |
|
|
, |
(3.15) |
|
|
|
|
|
|
|||
|
|
|
|
|
|||
|
|
|
[ р] |
2 |
|
||
|
1 + |
р |
|
||||
|
|
|
[ р] |
|
|
||
|
|
|
е |
|
где [р]р – допускаемое давление из условия прочности, МПа; [р]е – допускаемое давление из условия устойчивости в пределах упругости, МПа.
Допускаемое давление соответственно из условия прочности и устойчивости рассчитывается по следующим формулам:
|
|
[ р] |
= |
|
2[s] (s - с) |
; |
|
|
|
|
|
|
|
|||||
|
|
D + (s - с) |
|
|
|
|
|
|
||||||||||
|
|
р |
|
|
|
|
|
|
|
|
|
|
|
|||||
|
|
|
|
|
|
|
|
|
|
|
|
|
|
|||||
|
|
18 ×10−6 Е |
|
|
|
100(s - с) |
2 |
|
|
|
|
|
|
|||||
[ р] |
= |
|
D |
|
100(s - с) |
, |
||||||||||||
|
|
|
|
|
|
|
|
|
||||||||||
е |
nиB1 |
|
|
|
|
|
D |
|
|
|
|
|
|
D |
||||
|
|
|
|
lR |
|
|
|
|
|
|
|
|||||||
где |
|
|
|
|
|
|
|
|
|
|
|
|
|
|
|
|
|
|
|
|
|
|
|
|
|
|
|
|
|
|
|
|
|||||
|
|
|
|
D |
|
|
|
D |
|
|
|
|||||||
|
B1 = min 1,0; 8,15 |
|
|
|
|
|
|
. |
||||||||||
|
lR |
|
|
|
|
|
||||||||||||
|
|
|
|
|
|
100(s - с) |
(3.16)
(3.17)
(3.18)
При соблюдении условия (3.15) расчетная толщина стенки принимается к проекту.
28
4.ПОДБОР И РАСЧЕТ ПЕРЕМЕШИВАЮЩИХ УСТРОЙСТВ
4.1.Подбор и расчет мешалки
Мешалки являются одним из основных элементов аппарата для перемешивания жидких сред. Они предназначены для передачи механической энергии от динамических элементов аппарата к перемешиваемой среде. ГОСТ 20680–83 регламентирует двенадцать типов мешалок. Каждый тип мешалки имеет обозначение, указанное цифрами в скобках: трехлопастная с углом наклона лопасти a = 24° (01); винтовая (02); турбинная открытая (03); турбинная закрытая (04); шестилопастная с углом наклона лопасти a = 45° (05); клетьевая (06); лопастная (07); шнековая (08); якорная (09); рамная (10); ленточная (11); ленточная со скребками (12).
Все мешалки условно могут быть разделены [8, 9, 18] на быстроходные и тихоходные. Под быстроходными понимаются мешалки, используемые для перемешивания жидких сред преимущественно при турбулентном и переходном режимах движения жидкости; под тихоходными – при ламинарном режиме движения жидкости.
Быстроходные и тихоходные мешалки обычно применяются в аппаратах, симплекс геометрического подобия которых ГD = D/dм соответственно определяется неравенствами: 2,0 £ ГD £ 8,0 и
1,04 £ ГD £ 2,0.
Мешалки обычно устанавливаются по оси аппарата на расстоянии hм2 от его дна.
Для быстроходных мешалок 0,4 £ hм2/dм £ 1,0.
Максимальное расстояние от дна аппарата составляет hм2 = 0,5Н, где Н – высота уровня жидкости в аппарате, м.
Для тихоходных мешалок hм2/dм = (0,5 – 5,0)( ГD – 1,0).
Максимальное |
расстояние от дна аппарата составляет |
hм2 = 0,25D, где D – |
внутренний диаметр аппарата, м. |
Быстроходные мешалки могут быть также использованы и в виде многорядных перемешивающих устройств, когда на одном и том же валу устанавливаются две, три, четыре и более одинаковых мешалок. При этом минимальное расстояние между двумя соседними мешалками не должно быть меньше их диаметра dм; минимальная высота Н в случае установки двух мешалок на валу должна выбираться из соотношения Н ³ 1,3D.
29

Конструкции быстроходных мешалок приведены в табл. 4.1. Быстроходные мешалки могут использоваться в гладкостенных
аппаратах, а также в аппаратах, оборудованных различными внутренними устройствами. Помимо этого, мешалки с наклонными лопастями могут применяться в аппаратах с циркуляционной трубой.
Таблица 4.1
Быстроходные мешалки
Обозн |
Конструкция мешалки |
Диаметр мешалки, dм, мм |
|
|||||
ачение |
по ГОСТ 20680–83 |
по ОСТ 26-01-1245-83 |
||||||
|
|
|||||||
1 |
|
2 |
3 |
|
|
4 |
|
|
01 |
Трехлопастная |
80; 100; |
От |
80 |
до |
1250 |
||
|
|
|
125; 160; |
соответствует |
|
|||
|
|
|
180; 200; |
ГОСТ 20680–83, |
далее |
|||
|
|
|
220; 250; |
применяются только 1320 |
||||
|
|
|
280; 320; |
и 1400 |
|
|
|
|
|
d |
м |
360; 400; |
|
|
|
|
|
|
450; 500; |
|
|
|
|
|||
|
|
|
|
|
|
|
||
|
|
|
560; 630; |
|
|
|
|
|
|
|
|
710; 800; |
|
|
|
|
|
02 |
Винтовая |
Не |
|
применяется. |
||||
900; 1000; |
|
|||||||
|
|
|
Заменяется трехлопастной |
|||||
|
|
|
1120; 1250; |
|||||
|
|
|
|
|
|
|
||
|
|
|
1400; 1600; |
|
|
|
|
|
|
|
|
1800; 2000; |
|
|
|
|
|
|
dм |
|
2240; 2500 |
|
|
|
|
|
|
|
|
|
|
|
|
||
03 |
Турбинная открытая |
|
От |
100 |
до |
1250 |
||
|
|
|
|
соответствует |
|
|||
|
|
|
|
ГОСТ 20680–83, |
далее |
|||
|
|
|
|
используются только 1320 |
||||
04 |
Турбинная закрытая |
|
||||||
|
и 1400 |
|
|
|
||||
|
|
|
|
|
|
|
||
|
|
d |
|
|
|
|
|
|
|
|
м |
|
|
|
|
|
|
|
|
|
|
|
|
|
|
30