
Методички для специальности "Машины и аппараты..." / новосельская
.pdf
операций, но предназначенных для выполнения взаимосвязанных эксплуатационных функций. Например, в установку (комплекс) для производства сливочного масла входят дезодоратор, маслосбиватель, сливкоподготовитель и др. Каждое из входящих в комплекс специфицированных изделий служит для выполнения одной из нескольких основных функций, установленных для всего комплекса.
Комплект – два и более изделия, которые не соединены на заводеизготовителе с помощью сборочных операций и представляют набор изделий, имеющих общее эксплуатационное назначение вспомогательного характера (комплект ЗИП, комплект измерительной аппаратуры, комплект упаковочной тары).
К комплектам также относят сборочные единицы или деталь, поставляемую вместе с набором других сборочных единиц и (или) деталей, предназначенных для выполнения вспомогательных функций при эксплуатации этой сборочной единицы или детали (например, осциллограф в комплекте с укладочным ящиком, запасными частями, монтажным инструментом и сменными частями).
2.3. Оптимальное проектирование
Методы конструирования (проектирования) условно можно разделить на эвристический и алгоритмический. Эвристическое проектирование основывается на интуитивном мышлении подобно мозговому штурму и спонтанно принятых решениях [4–6 ].
В реальных условиях наиболее приемлем алгоритмический метод, который содержит подробную характеристику условий проведения процессов, условий назначения конструкций и цели проектирования. При этом выбирается формально идеальное решение (рис. 2.2).
|
|
Выбор основной оценки |
|
|
Критерий |
|
|
|
|
|
|
|
|
||
Задача |
|
|
|
|
|
|
|
|
|
Поиск |
|
|
Новые |
|
Оптимальные |
|
|
возможных решений |
|
|
решения |
|
решения |
Рис. 2.2. Формально идеальное решение
В основе алгоритмического проектирования заложена следующая структура: анализ → синтез → оценка.
Анализ – сбор данных, их классификация, определение их взаимосвязи.
11
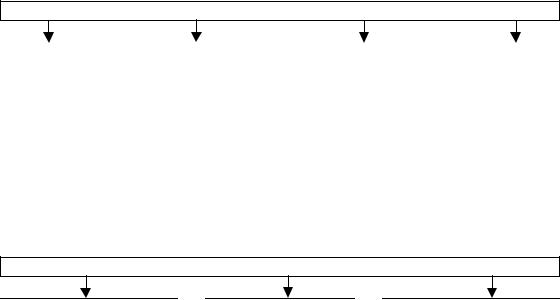
Синтез – творческое осмысление конструкции в целом и разработка ее частей.
Оценка – совокупность принятых решений.
Оптимальное проектирование характеризуется следующими принципами:
1)оптимальное нагружение (рис. 2.3);
2)оптимальная стабильность, или надежность (рис. 2.4–2.5);
3)оптимальный материал (рис. 2.6);
4)оптимальная технология (рис. 2.7);
5)оптимальный размер.
Принципы конструирования намечают способы приближения к оптимальным конструкциям. Чем больше конструкция отвечает выбранным критериям, тем меньше нагружение отличается от оптимального. Изменение нагрузок лежит в сфере возможностей конструктора. На основании анализа работы оборудования предложены следующие возможности оптимизации нагрузок (рис. 2.3). При этом форма поперечного сечения изделия должна быть подобрана так, чтобы в области, где напряжения значительно меньше допускаемых, было и меньше сечение. Постоянство сечений изделия бывает причиной неравномерности напряжений. Сочетание материалов с различными свойствами дает возможность перераспределить нагрузки, а следовательно, и напряжения (армированный бетон). Разделение нагружений предполагает создание конструктивных элементов, работающих на растяжение-сжатие, и позволяет избегать изгибов и точечных нагрузок.
Оптимальное нагружение
Разделение |
|
Избежание |
|
Перераспределение |
|
Распределение |
нагружений |
|
точечных нагрузок |
|
нагрузок |
|
нагрузок |
Рис. 2.3. Принцип оптимального нагружения
При любом способе оптимизации методика основывается на трех принципах: задача (постановка) → путь (способ) → решение
Стабильность заключается в надежности работы всех элементов конструкции без отказов за весь расчетный срок службы при соблюдении социальных требований (рис. 2.4).
Оптимальная стабильность
12
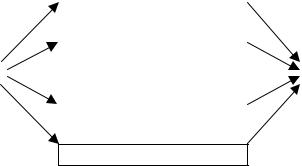
Выбор конструкционных |
|
Упрощение |
|
Увеличение прочностных |
материалов |
|
силовой схемы |
|
свойств |
Рис. 2.4. Принцип оптимальной стабильности (надежности)
Оптимальная стабильность характеризуется коэффициентом безопасности. По этому принципу стоит задача увеличить коэффициент безопасности n (запас прочности). Это обеспечивает надежность за счет использования специальных материалов, способов защиты и упрочнения (рис. 2.5).
|
|
Увеличение n |
|
|
|
|
|
|
|
||
|
|
Использование |
|
|
|
|
|
специальных материалов |
|
|
|
Надежность |
|
|
|
|
Стоимость |
|
|
|
|
|
|
|
|
Способы защиты |
|
||
|
|
и упрочнения |
|
|
Конфликтная ситуация
Рис. 2.5. Принцип обеспечения надежности
Анализ различных таблиц значений коэффициентов безопасности свидетельствует о том, что расхождения численных значений этих величин определяются ожидаемой надежностью прочностных свойств материала и надежностью комплекса с точки зрения нагружения и эксплуатации. С учетом этих факторов n меняется в пределах:
1,5–2,0 – если хорошо известны свойства материала и действующие нагрузки легко определить;
2,0–2,5 – при ориентировочных значениях нагрузки для обычных материалов и средних условиях эксплуатации;
2,5–4,0 – в случае непредвиденных обстоятельств (по балке движется груз);
5–10 – коэффициент на всякий случай.
Значения коэффициентов запаса прочности приведены в ГОСТ 14249-83. На практике стремятся к разработке упрощенных моделей. Показатель надежности должен быть исследован экспериментально.
При выборе оптимального материала основной принцип – обеспечить коррозийную стойкость, восприятие нагрузок при минимальной стоимости (рис. 2.6). Исходя из общих критериев обоснования целесообразности создания изделия, этот метод
13
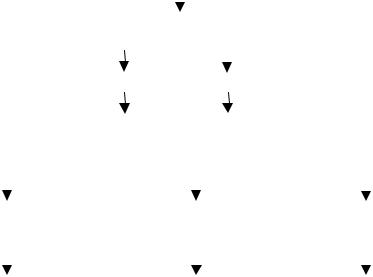
предполагает доступность, возможность получения предполагаемого для использования материала, его структуры, возможность восприятия нагрузок, особенности открытых поверхностей (трение, адгезия, когезия (сцепление), чувствительность к воздействию внешних факторов, коррозионная стойкость, жаропрочность, физические параметры, механическая обрабатываемость и т. п.).
Механическая обработка – один из дорогих способов изготовления деталей. Поэтому этот принцип предполагает использование составных конструкций или заготовок, по форме близких к изготавливаемой детали.
|
|
|
Оптимальный материал |
|
|
|
|
|
|
||||||
|
|
|
|
|
|
|
|
|
|
|
|
|
|
|
|
|
|
|
|
|
|
|
|
|
|
|
|
|
|
|
|
|
|
|
|
Углеродистые |
|
|
|
|
|
|
|
|
|||
|
|
|
|
(спокойные) стали |
|
|
|
|
|
|
|||||
|
|
|
|
|
|
|
|
|
|
|
|
|
|
|
|
|
|
|
|
|
|
|
|
|
|
|
|
|
|
|
|
|
Легированные стали |
|
|
|
Заменители |
|
|
|
|||||||
|
|
|
|
|
|
|
|
|
|
|
|
|
|||
|
|
|
|
Сменные элементы |
|
|
|
|
|
|
|||||
|
Рис. 2.6. Принцип оптимального материала |
|
|
|
|||||||||||
|
|
Оптимальная технология |
|
|
|
||||||||||
|
|
|
|
|
|
|
|
|
|
|
|
|
|
|
|
|
|
|
|
|
|
|
|
|
|
|
|
|
|
|
|
|
|
|
|
|
|
|
|
|
|
|
|
|
|
|
|
Максимальное |
|
|
Технологичность |
|
|
Способность |
|||||||||
использование |
|
|
|
|
|
к сборке |
|||||||||
|
|
при изготовлении детали |
|
|
|
||||||||||
стандартных деталей |
|
|
|
|
|
и разборке |
|||||||||
|
|
|
|
|
|
|
|
|
|
|
|
||||
|
|
|
|
|
|
|
|
|
|
||||||
|
|
|
|
|
|
|
|
|
|
|
|
|
|
|
|
Ремонтопригодность |
|
|
Лучшая механическая |
|
|
Ликвидация |
|||||||||
|
|
обработка |
|
|
|
|
|
|
подгонок |
||||||
|
|
|
|
|
|
|
|
|
|
Рис. 2.7. Принцип оптимальной технологии
Принцип оптимального размера – не назначать лишних размеров, четко обозначать сопрягаемые размеры и соблюдать основные требования ГОСТов.
2.4. Унификация и стандартизация оборудования
Унификация заключается в возможности многократного применения в конструкции одних и тех же элементов. Это способствует сокращению номенклатуры деталей и уменьшению стоимости изготовления и ремонта машин [7].
14
Унификация – рациональное сокращение числа видов, типов, марок и типоразмеров изделий одинакового функционального назначения, основных и второстепенных размеров, марок материалов, способов изготовления, технической документации и т. д.
Это сокращение вступает в конфликт с изобретательством. Этот конфликт кажущийся, а его разрешением будет чисто конструкторское решение. Конструктору не надо стремиться внедрить все возможные изобретения, а нужно сократить число этих вариантов и найти оптимальный вариант.
Различают следующие виды унификации:
1)конструктивных элементов – посадочных сопряжений, резьбовых соединений, шпоночных, шлицевых зацеплений и т. д.;
2)деталей и узлов (лучшие – заимствованные детали серийно изготавливаемых машин);
3)стандартных изделий (нормализация) – подшипников, крепежных деталей;
4)марок и сортамента материалов;
5)технической документации.
Унификация позволяет:
–снизить объем конструкторских работ и сроков проектирования;
–уменьшить сроки подготовки и освоения производства;
–повысить уровень механизации и автоматизации путем организации специализированных производств;
–сократить стоимость и срок изготовления;
–улучшить качество, надежность и долговечность машин вследствие тщательной отработки технологии;
–повысить технико-экономические показатели машиностроительных заводов.
Унификация в машиностроении предполагает создание сборочных заводов, получающих унифицированные узлы и детали со специализированных заводов для сборки машин. Образование производных машин на базе унификации осуществляется следующими
методами:
1. Секционирование – разделение машины на одинаковые секции и образование производных машин путем набора унифицированных секций (ленточные, скребковые транспортеры, теплообменники, насосы).
15
2.Метод изменения линейных размеров состоит в изменении длины машины или агрегата с сохранением формы поперечного сечения (мельницы, барабаны, мешалки и т. п.).
3.Метод базового агрегата позволяет путем присоединения к основному агрегату специального оборудования превратить базовый агрегат в машины различного назначения (самоходные краны).
4.Конвертирование – использование базовой машины или основных ее элементов для создания агрегатов различного назначения (перевод поршневых двигателей внутреннего сгорания с одного вида топлива на другой).
5.Компаундирование – применение параллельного соединения машин с целью увеличения общей мощности или производительности (установка двух или более двигателей, двухшнековых смесителей и т. п.).
6.Модифицирование – переделка машины для приспособления
еек иным условиям работы.
7.Агрегатирование – создание машин путем сочетания унифицированных агрегатов, представляющих собой автономные узлы, устанавливаемые в различном числе и комбинациях на общей станине.
8.Комплексная стандартизация – использование для агрегатов простого типа оборудования (днища, трубы, фланцы).
Степень унификации оценивается коэффициентом унификации:
K |
|
= |
1 − |
Nун |
100% , |
(2.2) |
ун |
|
|||||
|
|
|
|
|
|
|
|
|
|
|
∑ N |
|
где Nун – количество унифицированных узлов в агрегате; ∑N – суммарное количество узлов.
Стандартизация – это установление и применение правил с целью упорядочения деятельности в определенной области для достижения общей оптимальной экономии при соблюдении условий эксплуатации и требований безопасности.
Стандартизация является следующей оценкой конструкции после унификации. Она позволяет:
–уменьшить трудоемкость процесса проектирования;
–снизить стоимость изделия;
–использовать условия взаимозаменяемости.
Степеньстандартизацииоцениваетсякоэффициентомстандартизации:
16
|
|
Nст |
|
|
|
Kст = 1 |
− |
100% , |
(2.3) |
||
|
|||||
|
|
∑ N |
∑N – |
||
где Nст – количество стандартных деталей в агрегате; |
суммарное количество деталей.
Удовлетворительной считается конструкция, в которой степень унификации и стандартизации составляет 60–70%.
3.РАСЧЕТ ВЕРТИКАЛЬНЫХ СОСУДОВ
3.1.Основные положения безмоментной теории прочности
Расчет тонкостенных сосудов базируется на безмоментной и моментной теориях оболочек [12, 13]. Моментная теория оболочек дает более точное описание нагруженного состояния материала стенок сосуда. Вместе с тем сложность самой теории, громоздкость решения частных задач накладывает известные ограничения на ее использование в инженерной практике. Моментная теория оболочек применяется в тех случаях, когда напряжения от изгиба сопоставимы с напряжениями растяжения или сжатия.
17
Безмоментная теория оболочек в ряде случаев позволяет получить простые и достаточно надежные рекомендации по расчету сосудов.
Поэтому в тех случаях, когда расчет по моментной теории дает погрешности, лежащие в пределах допустимого, применяется более простая безмоментная теория оболочек, согласно которой предполагается, что напряжения в стенках оболочки распределяются равномерно по ее толщине.
Основное условие существования моментной теории прочности – отсутствие причин, вызывающих изгиб. В основе теории лежит аксиома, что оболочки работают на растяжениесжатие и не воспринимают изгибающих нагрузок. По такой схеме рассчитываются цилиндрические, сферические, эллиптические и конические оболочки. Элементы аппаратов, рассчитываемые по безмоментной (мембранной) теории, должны удовлетворять следующим условиям [3]:
1.Сосуд должен состоять из оболочек с соотношением Dн/Dвн ≤ 1,2.
2.Оболочка должна представлять собой тело вращения.
3.Оболочка не должна иметь резких перегибов образующей.
4.Нагрузка должна быть симметрична относительно оси и непрерывна вдоль образующей.
5.Края оболочки должны быть жестко закреплены.
Первое условие позволяет считать напряжения равномерно распределенными по толщине всей стенки сосуда. Допущение о равномерности напряжений по толщине стенки теряет силу при нарушении любого из перечисленных условий.
Четвертое условие означает отказ от учета влияния изгибающих моментов, а значит, и напряжений изгиба, возникающих в стенках сосуда. Это допущение влечет за собой исключение учета влияния напряжений, нормальных к срединной поверхности, и, следовательно, позволяет пренебречь деформациями сдвига, упрощая тем самым расчетную модель.
Построение безмоментной теории прочности оболочек так же, как и всякой другой теории, начинается с моделирования. Создается некая модель оболочки, при этом учитываются только те факторы, которые оказывают существенное влияние на работу нагруженной оболочки. Факторами, степень влияния которых на точность решения незначительна, допустимо пренебречь в интересах упрощения решения.
Так как корпус аппарата большей частью делается с таким расчетом, чтобы его стенки не подвергались значительным
18
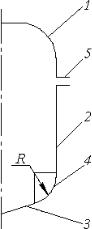
напряжениям изгиба, то расчетные уравнения, основанные на безмоментной теории, имеют наибольшее распространение.
Расчет оболочки на прочность по безмоментной теории заключается в определении наибольших напряжений, действующих в главных ее сечениях, а по ним – и толщины ее стенок.
3.2. Расчет сосудов, работающих под внутренним давлением
Основу всякого аппарата составляет его корпус. Корпус определяет размеры аппарата, его форму и объем, изолирует содержимое аппарата от внешней среды, служит для подвода и отвода
|
|
|
|
|
|
|
|
|
тепла |
и |
воспринимает внутренние или |
||||||
|
|
|
|
|
|
1 |
|
||||||||||
|
|
|
|
|
|
|
наружные нагрузки. Корпус состоит из |
||||||||||
|
|
|
|
|
|
|
|
|
|||||||||
|
|
|
|
|
|
|
|
|
пластин |
и |
элементарных |
оболочек |
|||||
|
|
|
|
|
5 |
|
|||||||||||
|
|
|
|
|
|
вращения (рис. 3.1). |
|
|
|
||||||||
|
|
|
|
|
|
|
|
|
|
|
|
||||||
|
|
|
|
|
|
|
|
|
Оболочка – |
геометрическое |
тело, у |
||||||
|
|
|
|
|
|
|
|
|
которого |
одно |
измерение |
(толщина) |
|||||
|
|
|
|
|
2 |
|
|||||||||||
|
|
|
|
|
|
несоизмеримо мало по сравнению с двумя |
|||||||||||
|
|
|
|
|
|
|
|
|
|||||||||
|
|
|
|
|
|
|
|
|
другими (диаметр, высота). |
|
|
||||||
|
|
R |
|
|
|
|
|
|
|
|
|||||||
|
|
|
|
4 |
|
|
|
|
|||||||||
|
|
|
|
|
|
Оболочка |
|
вращения |
образована |
||||||||
|
|
|
|
||||||||||||||
|
|
|
|
|
|
|
|
|
|
||||||||
|
|
|
|
|
|
|
|
|
вращением образующей (меридиана) |
||||||||
|
|
|
|
|
|
|
|
|
вокруг |
|
центральной |
оси. |
Форма |
||||
|
|
|
|
3 |
|
|
|
||||||||||
|
|
|
|
|
|
образующей определяет форму оболочки. |
|||||||||||
Рис. 3.1. Характерные |
|||||||||||||||||
При |
расчете |
цилиндрической |
|||||||||||||||
|
оболочки вращения |
||||||||||||||||
|
оболочки |
(далее обечайки) вертикальных |
|||||||||||||||
1 – |
корпуса сосуда: |
||||||||||||||||
сферическая оболочка; |
сосудов |
учитываются |
следующие |
||||||||||||||
2 – цилиндрическая оболочка; |
нагрузки: давление среды на стенки сосуда |
||||||||||||||||
3 – |
коническая оболочка; |
(внешнее |
или |
внутреннее); нагрузки от |
|||||||||||||
4 – торовая оболочка; |
|||||||||||||||||
веса |
аппарата |
|
и |
среды; |
нагрузки, |
||||||||||||
|
5 – |
пластина |
|
||||||||||||||
|
|
|
|
|
|
|
|
|
приложенные |
эксцентрично; |
ветровые; |
сейсмические; снеговые.
Согласно ГОСТ 14249–83, напряжение, возникающее в стенках тонкостенных оболочек, определяется по первой и третьей теориям прочности.
С учетом ослабления конструкции сварными швами и отверстиями расчетная толщина стенки сосуда sR, мм, рассчитывается по формуле
sR = |
рR D |
|
|
|
, |
(3.1) |
|
|
|||
|
2[σ]ϕрϕотв − рR |
|
19
где рR – расчетное давление, Па; D – внутренний диаметр аппарата, м; 2 – коэффициент, означающий, что расчет ведется по максимальным кольцевым напряжениям; [σ] – допускаемое напряжение, МПа; ϕр – коэффициент прочности сварного шва; – коэффициент ослабления конструкции отверстиями.
За расчетное давление рR принимается рабочее давление в сосуде при максимальном нагружении. Рекомендуются следующие расчетные давления для аппаратов:
–с рабочим избыточным давлением р > 0,07 МПа, снабженных
предохранительными клапанами, рR = 1,1p, но не менее р + 0,2 МПа для огневзрывоопасных или токсичных сред и не менее р + 0,1 МПа для остальных сред;
–с рабочим избыточным давлением р ≤ 0,07 МПа независимо от типа предохранительных устройств и для любых сред, кроме углеводородных фракций и других сжиженных газов: при р = 0,05– 0,07 МПа рR = 0,1 МПа; при р < 0,05 МПа рR = 0,06 МПа;
–с углеводородными фракциями и другими сжиженными газами
во всех случаях принимать: для фракций С2 рR = 2,0 МПа, для фракций С3 на всасывающей линии рR = 1,0 МПа, на нагнетательной линии рR = 2,0 МПа, для фракций С4 рR = 0,6 МПа, для фракций С5 рR = 0,3 МПа, для аммиака рR = 1,6 МПа, для фреона 12 рR = 1,0 МПа,
для сернистого ангидрида рR = 0,8 МПа, для хлористого метила рR = 0,9 МПа, для углекислого газа рR = 7,6 МПа;
– работающих без избыточного давления при вместимости аппарата менее 30 м3 рR = 0,01 МПа, при вместимости свыше 30 м3
рR = 0,005 МПа;
– работающих под вакуумом с остаточным давлением до
0,05 МПа, рR = 0,1 МПа.
Для элементов аппарата с раздельными пространствами, имеющими разные давления, за расчетное давление принимается каждое из них (без учета других). Допускается производить расчет на разность давлений, если при эксплуатации в любом случае обеспечивается наличие давлений во всех пространствах.
Расчетным давлением при испытаниях аппарата является
пробное давление. |
|
|
Если |
сосуд находится под действием |
гидростатического |
давления |
и действием газа над жидкостью, то за расчетное |
|
принимается давление газа и столба жидкости: |
|
|
|
рR = р0 + ргидр = р0 + ρgh. |
(3.2) |
20