
книги / Технология производства и методы обеспечения качества зубчатых колес и передач
..pdf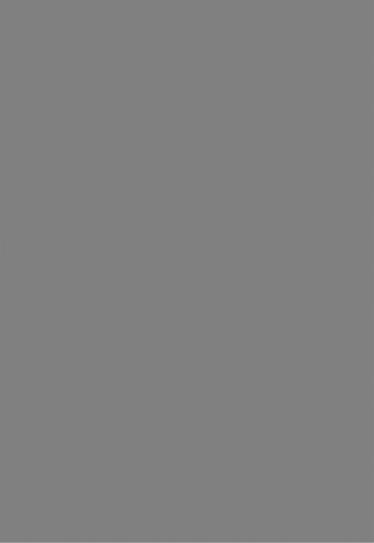
614 |
Г л а в а 16 |
1 6 .4 .2 . Ф р езер ны е головки
Недостатком обработки конических прямозубых колес с помощью зубострогаль ных резцов является низкая производительность процесса. Н аиболее совершенным, более производительным методом получения конических колес является обработка их сдвоенными фрезами (головками) и круговой протяжкой с зубьями, расположен ными по периферии ее корпуса [3, 7].
Дисковые сдвоенные фрезы по конструкции соответствуют одиоугловым фрезам. Профили рующая кромка (рис. 16.43) находится на тор цовой стороне зубьев фрезы. Работая в паре, фрезы 1 и 2 одновременно обрабатывают обе стороны впадины зубьев, т. к. зубья фрезы ко пируют зуб воспроизводящего колеса.
Оси фрез устанавливаются под углами, со ответствую щ ими углу проф иля нарезаемы х зубьев. Стружечная канавка между зубьями фрезы делается увеличенной ширины для раз мещения в ней зубьев второй фрезы, которая об рабатывает другую сторону впадины зубьев. Для обеспечения обкаточного движения заго товка 3 вращается вокруг своей оси и поступа тельно перемещается вдоль нарезаемых зубьев, а поэтому дно впадины имеет вогнутую форму.
Рис. 16.43 . Схема нарезания кониче |
Такой метод нарезания пригоден только для ко |
ских прямозубых колес дисковыми лес с зубьями небольшой длины. |
|
фрезами |
|
1 6 .4 .3 . Круговы е протяж ки
Особого внимания заслуживает процесс обработки конических прямозубых колес с применением дисковой протяжки с круговым зубом. Заметим, что при использовании фрез-протяжек значительно упрощается кинематика станка, сводясь к главному враща тельному движению, движениям подачи и деления [3].
В процессе обработки заготовка остается неподвижной, подача же осуществляется за счет прямолинейного перемещения протяжки вдоль впадины зуба. При черновой обработке (рис. 16.44) протяжка перемещается вдоль нарезаемой впадины в направлении от узкого конца зуба к широкому, а при чистовом нарезании она подается в обратном направлении. В начале рабочего цикла ось протяжки располагается в точке А, а первый резец касается са мой верхней точки L заготовки. В работу вступают первые резцы с широкими вершинными кромками. При этом ось протяжки медленно начинает перемещаться от точки А до точки С. Черновые резцы в количестве 48 шт., предназначенные для максимального удаления метал ла из впадины, работают в основном своими вершинными кромками.
Они делятся на две группы: резцы в количестве 18 шт. с № 1 по № 18 прорезают впа дину при медленной подаче, которая в точке В прекращается. Затем следует обработка без подачи группой черновых резцов в количестве 30 шт. (с № 19 по № 48), которые прореза ют впадину на полную глубину. После этого начинается оформление боковых поверхно стей по всей длине зуба. В работу вступают получистовые резцы в количестве 7 шт.
Конструкции и расчет зуборезного инструмента |
615 |
|
(с № 49 по № 55). При этом ось протяж |
|
|
ки быстро перемещается от точки В до |
|
|
точки С. Получистовые резцы макси |
|
|
мально удаляют припуск иод оконча |
|
|
тельную обработку боковых сторон |
|
|
зубьев заготовки и зачищают дно впади |
|
|
ны у широкого конца зубьев. В точке С |
|
|
заканчивается вся предварительная об |
|
|
работка впадины. Чистовое нарезание |
|
|
производится при обратном движении |
|
|
от точки С до точки D, в которой оно за |
|
|
канчивается. За это время боковые сто |
|
|
роны впадины оформляются при помо |
|
|
щи чистовых резцов в количестве 20 шт. |
|
|
(с № 56 по № 75). После окончания об |
|
|
работки заготовка поворачивается на |
|
|
одно деление, а ось протяжки переме |
|
|
щается от точки D до точки А, т. е. до |
|
|
исходного положения. |
|
|
Таким образом, преимущества дан |
|
|
ного способа нарезания зубчатых кони |
|
|
ческих колес сводятся к следующему: |
|
|
а) совмещение чернового и чистового |
|
|
нарезания в одну операцию; б) отсутст |
Рис. 16.44. Схема нарезания конических пря |
|
вие подачи инструмента на глубину ре |
мозубыхколес методом кругового протягивания |
зания; в) отсутствие отвода заготовки от инструмента во время деления; г) одновременная обработка обеих сторон впадины; д) не
прерывность процесса нарезания зубьев заготовки; е) постоянство расположения зоны ка сания (в средней части зуба); ж) профиль нарезаемого зуба очерчен приблизительно по дуге окружности вместо эвольвенты, что несколько упрощает изготовление инструмента.
1 6 .4 .4 . Резцовы е головки
Для получения конических колес с круговым зубом применяются конические червяч ные фрезы и резцовые головки [3, 7, 8]. Рассмотрим эти инструменты.
Резцовая головка (рис. 16.45) состоит из корпуса 1, в пазах которого с помощью вин тов 9 крепятся наружные 6 и внутренние 5 резцы. Точная установка и регулировка рез цов 2 относительно центра резцовой головки осуществляется за счет регулировочных клиньев 3 и прокладок 4 и 8. Регулирование клиньев производят винтами 7. Два резца го ловки являются нерегулируемыми в радиальном направлении и служат установочными для остальных резцов головки. Для нарезания всех размеров конических колес имеется несколько типоразмеров головок диаметром 1/2-12". Число резцов в головке может быть 2-32. Внутренние и наружные резцы устанавливаются в головке попеременно. Внешний вид резцов к головкам показан на рис. 16.46. Установка их должна обеспечивать такое по ложение, чтобы в момент резания режущие кромки резцов представляли собой зуб плос кого колеса. Кромки при этом должны быть прямыми, лежащими в плоскости, совпадаю щей с осью резцовой головки и составляющей с этой осью угол, равный требуемому углу
Конструкции и расчет зуборезного инструмента |
617 |
Ли т е р а т у р а
1.Лютксвич Е. Г., Волчков А. И. Расчеты зуборезных инструментов. Новочеркасск: НПИ, 1978.
2.Моисеенко О. И., Павлов Л. Е., Диденко С. И. Твердосплавные зуборезные инструменты. М.: Ма шиностроение, 1977.
3.Металлорежущие инструменты / Г. Н. Сахаров, О. А. Арбузов, 10. А. Боровой и др. М.: Машино строение, 1989.
4.Никитина 3. А. Инструкция по расчету червячных фрез. М.: ВНИИ, 1966.
5.Радзевич С. П., Палагута В. А. Новые достижения в области чистовой обработки цилиндрических зубчатых колее. М.: ВНИИТЭМР, 1988.
6.Романов В. Ф. Расчеты зуборезных инструментов. М.: Машиностроение, 1969.
7.Семепчепко И. И., Матюшин В. М., Сахаров Г. Н. Проектирование металлорежущих инструмен тов. М.: Машгиз, 1962.
8.Справочник инструментальщика/И. А. Ординарцев, Г. В. Филиппов, А. Н. Шевченко идр. М.: Ма шиностроение, 1987.
Глава 17
РАСЧЕТ ФОРМУЮЩЕГО ИНСТРУМЕНТА ДЛЯ ПЛАСТМАССОВЫХ ЗУБЧАТЫХ КОЛЕС
17.1. Общие положения
В процессе производства литых зубчатых колес особые требования предъявляются к расчету и изготовлению зубчатых матриц, при этом необходимо учитывать компенса цию усадки полимерного материала и самой матрицы (при изготовлении матриц из цветных сплавов по мастер-модели или электроэрозионным способом с помощью зубча того колеса-электрода). В большинстве случаев после опытных отливок требуется до полнительная корректировка матриц.
Анализ точности литых пластмассовых детален показывает [1], что около 60% по грешностей составляют отклонения формы поверхности, образующиеся при неравномер ной усадке в различных сечениях детали. Из данных об усадке литых пластмассовых зуб чатых колес следует, что модель равномерной радиальной усадки пригодна для прибли женного описания изм енения размеров достаточно ограниченной ном енклатуры цельнопластмассовых колес. При малом числе зубьев и сложной конфигурации отливки, а также при использовании армирующих вставок усадка имеет более сложный, неравно мерный характер. Поскольку отклонения формы частично являются систематическими погрешностями, можно существенно повысить точность изделий, учитывая в размерах формующего инструмента, наряду со средней величиной усадки, и ее неравномерность.
Технологическую усадку можно компенсировать посредством смешения исходного контура (коэффициент смещения х), изменения угла профиля а или модуля зацепления т, причем корректировка может производиться либо по всем указанным параметрам (х , б, т), либо по двум (б, х ) или одному (т) из них. Размеры мастер-модели рассчитывают, исходя из размера детали с учетом среднего значения допуска на размер и средней величины тех нологической усадки [2,3]. Учитывая что технологическая усадка зубчатого венца колеса вследствие сложной конфигурации его контура происходит неравномерно, в общем слу чае матрицы должны иметь нестандартные значения параметров исходного контура и для их изготовления необходимо проектировать специальный инструмент.
Опыт исследований показывает, что для описания изменения размеров колеса и кон фигурации зубьев при усадке целесообразно использовать предложенные Э. Б. Булгаковым [4] обобщающие параметры, которые характеризуют геометрию зуба вне связи с параметра ми производящего исходного контура и метода формообразования зубьев. В качестве обоб щающих параметров, как это было показано в главе 8, можно принять диаметры основных окружностей dfo'2, вершин зубьев rffl12 или параметр, определяющий толщину зуба на ок ружности вершин та = sa / dt„ а также один из следующих параметров: углы профилей на окружности заострения зубцов пары сопряженных колес o )2, или углы развернутости эвольвенты на окружности заострения н12, или эвольвентные углы профилей зубцов на окружности заострения 012 = inv x i2, или приращение к12 = Д д у г о в о й толщины зубцов Aslt2 на основной окружности по отношению к некоторой исходной толщине.
Расчет формующего инструмента для пластмассовых зубчатых колес |
619 |
Аналогичное направление развивается в работах А.Л. Капелевича и Р.Е. Клейсса [5,6]. Методика расчета геометрии зубчатых передач с фирменным названием Direct Gear Design, также как и теория зубчатых зацеплений в обобщающих параметрах, предполагает на первом этапе проведение расчета и выбор оптимальных геометрических параметров зубчатой передачи и составляющих ее колес, исходя из требований и условий работы пе редачи; формообразующий инструмент проектируется и его геометрия рассчитывается та ким образом, чтобы обеспечить полученные при проектировании передачи оптимальные параметры зацеплений. В качестве обобщающих параметров в [5, 6] приняты: v - угол профиля на окружности заострения (в точке пересечения двух эвольвент, определяющих правую и левую боковые поверхности зуба):
v = arc cos (d h /dA),
где dA - диаметр окружности заострения; dh - диаметр основной окружности; ть - отно сительная толщина зуба на основной окружности:
mb^ s b/ p b = z'm v{v)/% ,
где sb - толщина зуба на основной окружности; рь - основной шаг:рь = ndb/z\ та - относи тельная толщина зуба на окружности вершин:
mn = Sa/Ph>
где sa - толщина зуба на окружности вершин.
Нами в качестве независимых параметров приняты: диаметр вершин зубьев d„, диаметр основной окружности db и угол, соответствующий толщине зуба на основной окружности 0*. Соответственно выбранным обобщающим параметрам по формулам (8.1)—(8.3) рас считывают коэффициенты усадки: по ок ружности вершин 5а (уменьшение диа метральных размеров колеса), по профилю
зуба Sb (изменение параметров эвольвен ты), по толщине зуба Ss (уменьшение его толщ ины). Указанные коэффициенты полностью описывают изменения геомет рических параметров зубчатого колеса в процессе усадки (рис. 17.1). Предлагаемая модель универсальна, она включает в себя известные частные случаи, например, при Ss = 0; rk - rb/cos ô*; 5„ = Sbона соответству ет модели равномерной усадки по радиусу (профиль 2); при 5), = 0; d b = d b = ^ п р о исходит изменение толщины и высоты зуба (профиль 3), а усадка зубчатого вен ца колеса в размерах матрицы компенси руется изменением параметров da и х.
620 |
Г л а в а 17 |
17.2. Методы расчета коэффициентов усадки
При исследовании влияния технологической усадки на геометрические параметры литых зубчатых колес большое значение имеет точное определение обобщающих пара метров и коэффициентов усадки. Ниже приведены способы расчета указанных коэффи циентов.
1 7 .2 .1 . Р асчет о б о б щ аю щ и х пар ам етр о в зу б ч а то го венц а и ко эф ф ициенто в усад ки по к о о р д и н а там т о ч е к проф иля зуб а
По этой методике профиль зуба литого колеса аппроксимируют эвольвентой, а от клонения профиля от аппроксимирующей эвольвенты относят к погрешностям профи ля. По координатам точек профиля зуба рассчитывают параметры эвольвенты, отражаю щей реальный профиль зуба. Аппроксимацию проводят, минимизируя сумму квадратов отклонений точек профиля, по нормали к аппроксимирующей эвольвенте [7]:
= |
mi.«. |
(17.1) |
1=1 |
i=1 |
|
Условие (17.1) выполняется при |
|
|
|
э 1 |
< 4 - ) 2 |
I |
|
|
м ь |
эd b |
(17.2) |
|
|
||
э21 |
( 4 ) 2 |
р 2(//п-)2 |
|
~ H d f , |
’ ’ ЭА \ |
(17.3) |
|
> 0 ‘ |
Анализ функции f fri показывает, что в рассматриваемой области значений dh условие (17.3) выполняется. Из условия (17.2) получаем уравнение для определения среднего диаметра d h основной окружности аппроксимирующей эвольвенты:
|
(17.4) |
X ^ Y sin(X? |
(17.5) |
где
К; = а ? ± arctg— + invfarccos— | :
y î |
I |
D ) |
a* = arccos-^-; d- |
= 2 ^(x? )2 + (y -)2. |