
книги / Технология производства и методы обеспечения качества зубчатых колес и передач
..pdfКонструкции и расчет зуборезного инструмента |
591 |
20. Диаметр впадин зубьев долбяка:
^/о = ^о_ 2А^0.
21. Наибольшая допустимая величина стачивания долбяка ДВ ограничивается проч ностью зуба сточенного долбяка и отсутствием подрезания зубьев нарезаемых им колес: ДВ = В - е, где е — длина зуба окончательно сточенного долбяка; рекомендуется е = (1/4 -1/3)Я , но не менее 5 мм; В — длина зуба нового долбяка (принимается по ГОСТ 9323-79).
22. При работе окончательно сточенным долбяком может происходить подрезание ножки зуба шестерни и колеса. Подрезание отсутствует, если выполняется условие р„ > 0 (для шестерни) и рп > 0 (для колеса). Расчет р/( и рй ведут по формулам, приведенным в п. 15, принимая ж0 = лг0|11Ш:
( а - Д В ) tg a „
х0 min — ‘
"т
23.На отсутствие срезания головки зуба колеса окончательно сточенным долбяком проверка производится по формуле
аш sin |
га 2 sin <ха2. |
Здесь
m (zQ- z2)cos a
inv 0*02= inv a + 2 tg a (x2 + x0min)/(z2 + z0), где x 2 — коэффициент смещения для колеса.
24.Остальные элементы конструкции долбяка выбираются по ГОСТ 9323-79 или из конструктивных соображений.
25.По ГОСТ 9323-79 определяются допуски на все элементы долбяка и технические
требования к его изготовлению.
1 6 .2 .3 . Обкаточные резцы
Обкаточные резцы работают по методу зуботочения и представляют собой колесо с винтовыми зубьями, снабженными режущими лезвиями. Иначе обкаточный резец мож но представить как червячную фрезу, у которой число заходов равно числу зубьев обка точного резца. Принцип работы такого инструмента основан на использовании относи тельного скольжения профилей зубчатых колес с перекрещивающимися осями. В про цессе обработки инструмент 1 вращается вокруг своей оси согласованно с заготовкой 2 и, кроме того, имеет продольную подачу 50, параллельную оси заготовки (рис. 16.26). За счет разности скоростей скольжения профилей обкаточного резца и заготовки (vp - г/, - = 25-55 м/мин) при осевой подаче 50 - 0,5—0,8 мм/об происходит обработка заготовки. Угол перекрещивания осей инструмента и заготовки составляет 60-90°.
Переднюю поверхность зубьев обкаточного резца затачивают под углом у к плоско сти, нормальной к направлению зубьев, а задние углы на боковых сторонах профиля зубь ев выполняются как у косозубых зуборезных долбяков, т. е. с одной стороны с большим, а с другой — с меньшим, чем угол наклона зубьев резца, углом наклона.
592 |
Глава 16 |
Рис. 16.26. Схемы нарезания колес обкаточными резцами: а — косоэубого колеса прямозубым резцом; б— прямозубого колеса прямозубым резцом; в — косозубого колеса косозубым резцом
Кпреимуществам метода зуботочения перед зубофрезерованием следует отнести:
1)одинаковую нагрузку на все зубья инструмента и, следовательно, равномерный износ;
2)сокращение расхода быстрорежущей стали на 70-80%; 3) повышение производитель ности в 4 -5 раз за счет увеличения минутной подачи.
Недостатки этого метода следующие: 1) обкаточный резец является сугубо специаль ным инструментом; 2) обкаточным резцом можно производить обработку колес с числом нарезаемых зубьев не менее 80-100. Этот недостаток связан с ограниченными возможно стями кинематических цепей обычных зубофрезерных станков, на которых применяются обкаточные резцы.
1 6 .2 .4 . Ш еверы
Конструкции шсверов для нарезания зубчатых колес. Шеверы применяют для чис товой обработки прямозубых и косозубых колес наружного и внутреннего зацепления по сле предварительного нарезания. Они повышают точность зубчатых колес, снижают ше роховатость боковых сторон зубьев, не уменьшают шум при работе шевингованиых зубча тых колес.
Шевингование при нормальных условиях обработки обеспечивает точность колес до 5 -6 степени и шероховатость боковых сторон зубьев до R„ = 0,63 мкм.
Способ зубошевингования основан на принципе зацепления зубчатых колес с пере крещивающимися осями. Угол скрещивания обеспечивается поворотом оси инструмента относительно оси заготовки.
При одноименном наклоне зубьев шевера и колеса углы наклона их зубьев суммиру ются, а при разноименном — вычитаются. Оптимальная величина угла скрещивания осей составляет 10-20°.
По конструкции шеверы бывают реечные и дисковые (рис. 16.27). На боковых сторо нах зубьев шеверов всех типов для образования режущих кромок делают канавки вдоль эвольвентного профиля зубьев.
Ш евер-рейка представляет собой зуборезную рейку, на боковых поверхностях кото рой прорезаны стружечные канавки шириной 0,8-1,0 мм, глубиной 1,0 с шагом 1,6-2,0 мм, образующие режущие кромки.
В процессе обработки зубчатое колесо, установленное на оправке в центрах, находит ся в плотном зацеплении с шевер-рейкой, закрепленной на столе станка. Стол с инстру ментом имеет возвратно-поступательное движение и приводит во вращение обрабатывае мое колесо. Для последовательного удаления припуска периодически осуществляется по дача, т. е. приближение оси заготовки к шеверу-рейке на величину 0,025-0,08 мм.

594 |
Глава 16 |
Рис. 16.29. Схемы шевингования: В0, В, — соответственно ширина шевера и нарезаемого коле са; L— величинаотносительногосмещения шевера иколеса; 7,2—начальное иконечное положе ния нарезаемого колеса
Приведенные на рис. 16.29 схемы шевингования различаются положением заготовки относительно продольной подачи 5. В зависимости от угла разворота заготовки е различа ют три метода шевингования:
а) параллельный метод — е = 0; 6) диагональный — при остром угле е; в) касатель ный — при е = 90°, т. е. продольная подача направлена перпендикулярно оси детали.
При параллельном методе шевингования стол станка с обрабатываемым колесом со вершает от 6 до 10 одинарных ходов, в конце каждого продольного хода стола осуществ ляется радиальная подача на 0,02-0,06 мм с одновременным изменением направления вращения шевера. Сближение шевера и колеса после каждого прохода продолжается до тех пор, пока толщина обрабатываемого зуба не достигнет заданного размера. При послед них двух-четырех зачищающих ходах шевингование происходит без радиальной подачи, как бы «выхаживая» обработанный профиль. Ширина дискового шевера. не зависит от ширины обрабатываемого зубчатого колеса, поэтому узким шевером можно обрабатывать колеса с венцом неограниченной ширины. Таким образом, шевингование с продольной подачей не может быть полностью заменено другими методами, так как оно позволяет об рабатывать зубчатые колеса большой ширины.
При диагональном методе шевингования линия зацепления непрерывно перемещает ся вдоль оси колеса и шевера, что обеспечивает более равномерный износ зубьев шевера, способствуя тем самым повышению стойкости инструмента.
Шеверы для касательного, или, иначе, тангенциального шевингования в связи с от сутствием смещения заготовки по оси должны выполняться по ширине несколько боль шими ширины обрабатываемого колеса, чтобы обеспечить полное перекрытие зубчатого венца заготовки. Поэтому область их применения ограничена шириной обрабатываемых колес. Максимальная ширина дисковых шеверов по технологическим соображениям должна быть не более 40 мм.
Для шевингования зубчатых колес широко применяются также кромочные шеверы [3]. Принцип их работы аналогичен рассмотренным методам шевингования. Однако для обра ботки обеих сторон зубьев колеса применяют два шевера, причем каждый шевер обраба тывает только одну сторону зуба. Обрабатываемое колесо 4 подводится к шеверу 2 (рис. 16.30), затем включается рабочая подача и обрабатывается одна сторона профиля зубьев А. После этого колесо отводится в положение 3. В этом положении реверсируется враще ние колеса и шевера, и колесо вводится снова в зацепление с шевером. При включении ра бочей подачи отделывается вторая сторона профиля зубьев В.
Конструкции и расчет зуборезного инструмента |
595 |
Рис. 16.30. Схема обработки кромочнымшевером
Дисковый шевер соответствует зубчатому колесу с наклонными зубьями (рис. 16.31). В процессе окончательного образования зубьев колеса его зубья и зубья шевера должны за цепляться с одной и той же косозубой инструментальной рейкой, поэтому у шевера и колеса в сечении, нормальном к направлению их зубьев, должны быть равны шаги и углы профиля.
По ГОСТ 8570-80 установлены следующие номинальные диаметры делительной окружности шеверов: 85, 180 и 250 мм. Принятый диаметр должен удовлетворять сле дующим условиям: 1) возможности использования шевера на данном станке; 2) возмож ности обработки самого малого по диаметру колеса, исходя из минимально допустимого межосевого расстояния шевер-заготовка.
Для улучшения условий обработки, чтобы избежать совпадения контакта одних и тех же зубьев при следующих оборотах колеса, число зубьев шевера не должно иметь общих множителей, а тем более не может быть кратным числу зубьев обрабатываемого колеса. Поэтому у шеверов общего назначения (ГОСТ 8570-80) число зубьев принимают из ряда чисел 29, 31, 37, 41, 43, 47, 53, 61, 67, 73, 83 и только в одном случае 27 (для т = 8 мм).
Высота зуба шевера должна обеспечить обработку профиля зуба колеса на высоте ра бочей (активной) части зуба. Вершина зуба шевера нс должна резать дно впадин зубьев колеса, поэтому высота головки зуба шевера должна быть меньше высоты головки зубьев предварительного инструмента.
Новые шеверы проектируют с учетом припуска на переточку по толщине зуба. При каждой перешлифовке профиля снимается слой 0,05-0,07 мм. Обычно производится не менее четырех перешлифовок.
Величина и положение припуска на переточку влияют на размеры зубьев шевера, ус ловия его эксплуатации и изготовления: толщину вершин зубьев нового шевера, высоту головки и ножки зуба, диаметр окружностей выступов впадин, диаметр центров отвер стий, положение рабочего профиля по высоте зуба, обеспечение превышения рабочего участка под основным цилиндром.
После каждой переточки и уменьшения толщины зуба шевера соответственно умень шается высота его головки, считая от делительного диаметра, путем шлифования наруж ного цилиндра (выступов) шевера.
Режущие кромки образуются на зубьях шевера канавками, полученными долблением гребенкой обычно в радиальном направлении (рис. 16.32). Для выхода гребенки в основа нии впадин зубьев шеверов сверлятся отверстия, наклонно расположенные по отношению к оси шевера в соответствии с углом наклона зубьев.
Конструкции и расчет зуборезного инструмента |
597 |
Исполнение 1 Исполнение 2 Исполнение 3
Рис. 16.32. Стружечные канавкишевера
быть достаточными для размещения стружки не только при работе новыми, но и перето ченными шеверами.
Глубина канавок должна обеспечить достаточное пространство для размещения стружки, в особенности у переточенных шеыеров. Недостаточная глубина влечет некаче ственную обработку зубьев колеса и часто является причиной выкрашивания и поломок зубьев шевера, а также сокращает количество его переточек.
Шевер базируется на шпинделе станка отверстием и одним торцом. Для уменьшения размеров торцовой поверхности шевера с точной обработкой ширина его ступицы делает ся больше ширины обода приблизительно на 1 мм. Торцы ступицы для обеспечения точ ности базирования должны быть перпендикулярны оси отверстия; торцы обода могут быть выполнены с меньшей точностью; они разделены неглубокой канавкой. Для переда чи крутящих моментов в отверстии предусмотрена продольная шпоночная канавка.
Боковые поверхности зубьев шевера, на которых расположены режущие кромки, представляют собой эвольвентные винтовые поверхности, имеющие одинаковые углы на клона.
Совершенствование конструкций шеверов и методов шевингования идет по путям по вышения режущих свойств, стойкости и работоспособности инструмента, а также созда ния конструкций и методов шевингования, упрощающих кинематику станка и снижаю щих время и трудоемкость обработки. Режущие свойства можно повысить за счет созда ния составных и сборных конструкций шеверов [3], оснащенных твердыми сплавами, алмазами и композитами, закрепленными на корпусе пайкой, клиньями или винтами (рис. 16.33, а, 6). Однако в связи со сложностью их изготовления на практике такие шеверы широкого применения не получили.
Для обработки закаленных колес, для снятия заусенцев незаменимы шеверы состав ной конструкции с режущим слоем из абразивных, алмазных и композиционных материа лов, нанесенных на металлические зубья корпуса (рис. 16.33, в).
Для сокращения времени на обработку применяют однопроходные шеверы и шеверы с измененным направлением подачи. У однопроходных шеверов зубья на 2/3 их длины равномерно уменьшаются по толщине, образуя заборную часть. Уменьшение толщины зубьев должно быть намного больше припуска на шевингование. На остальной длине зу бья имеют нормальный требуемый размер и выполняют роль калибрующей части. При работе таких шеверов не требуется сближения осей шевера и колеса, а вся обработка ве дется за один двойной ход.
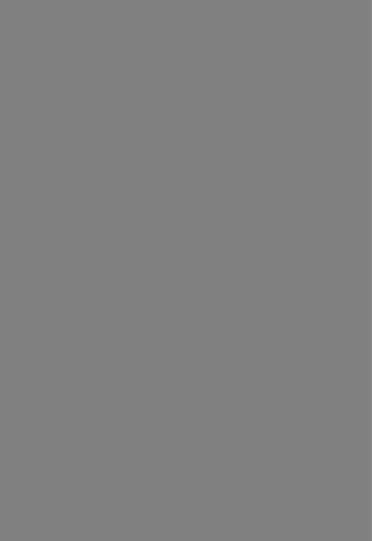
Конструкции и расчет зуборезного инструмента |
599 |
необходимости на передние поверхности зубцов шевера наносится износостойкое покрытие из нитрида или карбида тита на. На задние (контактные) поверхности зубцов шевера, которыми они зацепляют ся с профилями зубьев обрабатываемого колеса, покрытие наносить нецелесооб разно, т. к. применяемые покрытия име ют очень низкий коэффициент трения, что вызывает уменьшение глубины вне дрения зубцов шевера и толщины срезае мого слоя. Поскольку перетачивание ше вера производится по профилю зубьев, оставлять покрытие не имеет смысла, т. к. оно будет снято при перешлифовке.
Расчет шсвсров для нарезания зубчатых колес. Последовательность расчета шевера приведена ниже [6].
1. Угол наклона зубьев по делительной окружности
Po = Y ± Pi.
где у — угол скрещивания осей шевера и колеса; Р( — угол наклона зубьев колеса. Знак «+» берется при одноименном направлении зубьев шевера и колеса, знак
при разноименных.
Оптимальные значения угла скрещивания находятся в пределах 10-20°. Лучшие ре зультаты работы дают шеверы, имеющие у = 15° . При этом значении Y обеспечивается скорость резания 35-45 м/мин.
Для косозубых правозаходных колес обычно принимают левозаходный шевер, для левозаходных и прямозубых колес — правозаходный. Для косозубых колес можно про ектировать прямозубые шеверы. Значение р0 не должно быть больше 30° из-за трудно сти при шлифовании боковых поверхностей зуба шевера. Стандартные шеверы изготов ляются с углом наклона зубьев по делительной окружности р0 = 5, 10 или 15°.
2. Число зубьев шевера
Zo = (da max-3/nn) cos Р0/щ „ ,
где da mnx — наибольший допустимый диаметр шевера (выбирается по станку) согласно табл. 16.11.
Число зубьев z0 не должно быть кратным или иметь общие множители с числом зубь ев нарезаемого колеса; по возможности z„ должно быть простым числом.
3. Диаметр делительной окружности шевера:
do - В Д /cos ро,
колеса и шестерни:
^i(2)= ro„z,(2)/cos р1(2).
4. Торцовый профильный угол шевера, рассчитываемый с точностью до угловых се кунд:
tg a f «tgcc/cos р0,
колеса и шестерни:
tg a ti ~ t g a /2 = tg a /c o s p 1(2).