
книги / Нанодисперсные и гранулированные материалы, полученные в импульсной плазме
..pdfу-фаза железа или (3-фаза кобальта, имеющие ГЦК решетку. С учетом того, что значение поверхностной энергии у р-Со ниже, чем у y-Fe [6.23], в поверхност ных слоях происходит перераспределение этих атомов, приводящее к обогаще нию поверхности частиц кобальтом.
Проведенные авторами измерения магнитных свойств УДП сплава Fe-Co показали, что добавка к железу 3 % масс, кобальта привела к повышению на магниченности насыщения приблизительно в два раза (4nls = 14297 Гс) и к уменьшению коэрцитивной силы до Нс = 0,4 кЭ по сравнению со значением этих характеристик для УДП железа (см. п. 5.1).
Таким образом, использование импульсной плазмы для получения УДП многокомпонентных веществ —КМ и сплава —дает возможность в широких пределах составов получать их прямой обработкой сложных парогазовых сме сей. Полученные УДП характеризуются хорошей равномерностью распреде ления компонентов в них. Использование методов ОЭС и ВИМС дало воз можность установить характер межфазных взаимодействий в исследованных системах Mo—TiC, Fe—TiC, Fe—Со при формировании УДЧ, которые опреде ляются взаимной растворимостью компонентов. Одновременно с этим УДЧ КМ и сплава характеризуются структурной неоднородностью, проявляющей ся в перераспределении атомов составляющих их компонентов в поверхност ных слоях частиц, направленной на понижение избыточной поверхностной энергии УДЧ.
6 .5 . Возм ож ны е обнести применения наноразмерны х порошков, попученны х о импульсной пназм е
Анализ возможных областей применения УДП, полученных в плазме кон денсаторного разряда, может быть проведен по двум направлениям:
1) использование УДП в качестве исходных компонентов шихты для изго товления компактных материалов;
2) использование УДП непосредственно в дисперсном состоянии. Использование УДП при изготовлении компактных материалов дает воз
можность сформировать устойчивую высокодисперсную структуру с повышен ной плотностью, которая характеризуется высокими значениями твердости и прочности. Этот вывод основывается на предположениях об обратной зависи мости прочности материалов от размера зерна, а также на том, что образование и рост трещин критического размера в материалах с мелкозернистой структу рой тормозится из-за малого размера структурных фрагментов и наличия боль шого числа границ [6.13]. Однако надо иметь в виду то, что применение УДП ограничивается их малой насыпной массой, огромной усадкой при спекании. Поэтому в ряде случаев более целесообразным следует считать использование
УДП в качестве модифицирующих добавок, введение которых может изменять процессы структурообразования при компактировании материалов и активи ровать процесс спекания.
Были проведены исследования по изучению модифицирующего влияния синтезированных в импульсной плазме УДП Fe, В4С и SiC на карбидостали, спеченный карбид бора и композиционный материал Si3N4—SiC [6.32 —6.35]. В режиме спекания всех шихт, содержащих УДП, на определенных стадиях нагре ва предусмотрены изотермические выдержки для дегазации с поверхности по рошков адсорбированных газов. Влияние добавок УДП железа исследовалось при получении карбидостали состава TiC + 60 % масс. Х6ВЗМ.
Средний размер частиц используемого порошка карбида титана составлял 2...3 мкм. В состав исходной шихты вводили от 5 до 15 % масс. УДП железа. Об разцы карбидостали спекали в вакууме при 1673 К в течение 60 мин. При тем пературе 1073 К в режиме нагрева образцов, как отмечено выше, предусмотре на изотермическая выдержка в течение 30...60 мин.
По кинетическим кривым усадки образцов (рис. 6.18, а) можно судить о снижении ее температуры с 1400 до 1230 К. Понижение температуры начала усадки в образцах с добавками УДП железа объясняется, по-видимому, более ранним появлением жидкой фазы при спекании. Это происходит из-за смеще ния линий фазовых равновесий диаграммы состояния с соответствующим снижением температуры эвтектической точки в системах с УДП из-за избы точной свободной энергии, обусловленной, в частности, избыточной поверх ностной энергией УДП [6.19].
М/1, %
Pue. 6.J8. Кривые усадки (а)иДТА (б)образцов с добавками УДП железа для систем: i —TiC + 60% масс. Х6ВЗМ + 7 % масс. Fe; 2 —TiC + 60% масс. ХбВЗМ + 7 % масс. УДП Fe; 3 — TiC + 60% масс. Х6ВЗМ + 10 % масс. УДП Fe
Это подтверждается и результатами дифференциально-термического анали за (рис. 6.18, б). Появлением большого количества жидкой фазы при спекании образцов с добавками УДП и, возможно, улучшением смачиваемости карбида жидкой связкой за счет свободного углерода, который дополнительно привно сится в шихту в составе ультрадисперсных добавок, можно объяснить и повы шенную плотность получаемой в этом случае карбидостали (табл. 6.1).
Таблица 6.1. Свойства спеченных материалов
С остав компакгируемого |
Относительная |
Твердость |
О’и зп М П з |
К1С, М Па м 1/2 |
стсж, М Па |
материала |
плотность |
|
|
|
|
T iC +60% масс. |
0,99 |
65HRC |
1530 |
|
2620 |
Х 6В ЗМ +7% масс. |
|
|
|
|
|
УДП Fe |
|
|
|
|
|
T iC +60% масс. |
0,96 |
52HRC |
1380 |
— |
2350 |
Х 6В ЗМ +7% масс. Fe |
|
|
|
|
|
Si3N 4+ 2 0 % масс. УДП SiC |
0,97 |
- |
850 |
8,3 |
— |
Si3N 4+ 2 0 % масс. SiC |
0,95 |
— |
550 |
6,8 |
— |
В4С + 10% масс. УДП В 4С |
0,98 |
98HRA |
480 |
5,9 |
1640 |
В4С |
0,94 |
94HRA |
380 |
4,5 |
1500 |
На рис. 6.19 представлены фотографии микроструктур полученных образцов карбидосталей и распределение по размерам частиц карбида титана в них. Ана лиз полученных результатов показывает, что при добавлении УДП железа в ис ходную шихту в карбидостали формируется структура с более мелким карбид ным зерном. Это находит хорошее объяснение с позиции механизма спекания, определенного по значению энергии активации Еа, равной ~ 5 кДж/моль [6.36]. Подобная величина Еахарактеризует механизм усадки, лимитирующей стадией которого является жидкоподобная коалесценция частиц [6.37].
Введение УДП железа в состав карбидостали, как отмечалось выше, приводит к раннему появлению жидкой фазы в большем количестве по сравнению со спека нием карбидостали из шихты без модифицирующихдобавок УДП. В свою очередь, это ведет к изоляции зерен карбида друг от друга и замедлению процесса их роста.
Формирование более мелкозернистой и плотной структуры у карбидостали, полученной из шихты с добавками УДП железа, объясняет и ее повышенные механические свойства (см. табл. 6.1).
Совершенствование средств индивидуальной защиты требует освоения про изводства новых материалов, способных противостоять локальному ударному воздействию с энергией свыше 3500 Дж при минимальной удельной массе изде лия (менее 50 кг/м2). Возможным решением этой задачи является создание средств индивидуальной защиты на основе высокомодульных нанокристаллических керамических материалов и их композиций с повышенными твердостью, прочностью и ударной вязкостью. Наиболее распространенными примерами та ких средств являются броневые пластины из карбида бора и карбида кремния.
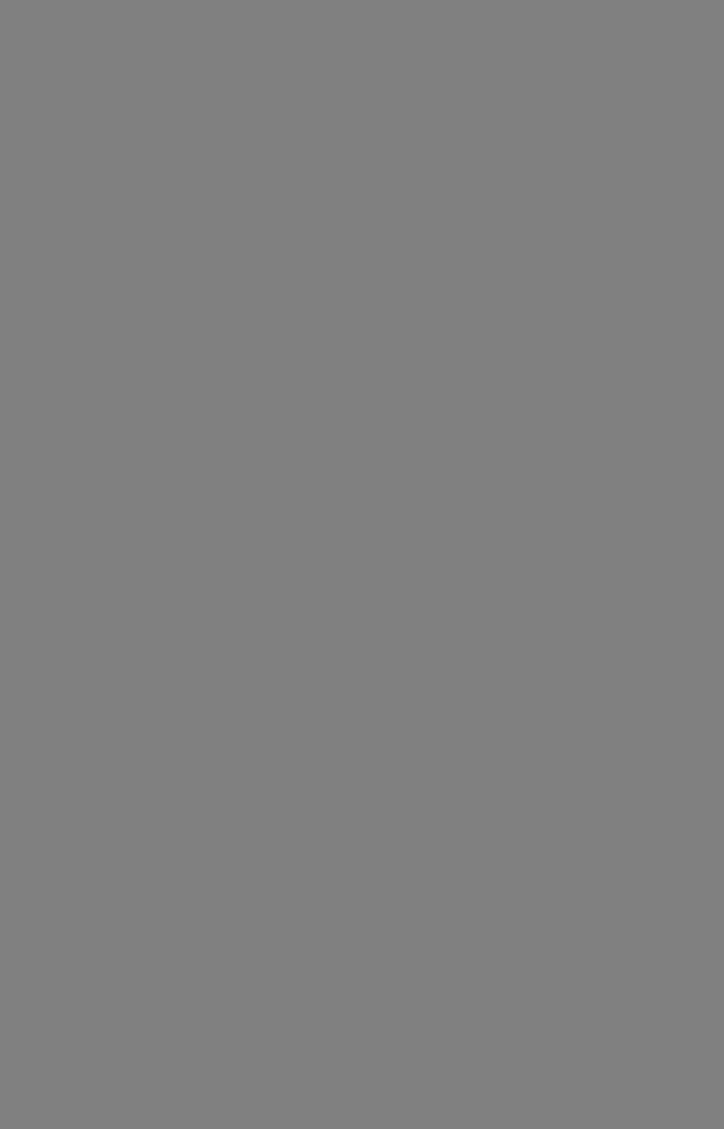
Компактирование образцов проводилось на прессе горячего прессования при температуре 2473 К и давлении 30 МПа с выдержкой под давлением в тече ние 10 мин в вакууме. В процессе нагрева образцов в области температур 1600... 1700 К предусмотрена изотермическая выдержка в течение 30 мин. При исследовании кинетики уплотнения в процессе горячего прессования исполь зовали автоматическую запись усадки с помощью электронного потенциомет ра, регистрирующего перемещение пуансонов. Плотность полученных образ цов определяли методом гидростатического взвешивания в воде.
Испытание на изгиб проводили по схеме трехточечного нагружения, а испы тания на сжатие —на машине ZD -10/90 (Германия). Средние значения проч ности получены в результате испытания 12 образцов; относительная погреш ность составляла 5 %.
Для определения трещиностойкости К1Сиспользовали метод микровдавли вания с применением пирамиды Виккерса при нагрузке 150 Н. Значение Кхс вычисляли по формуле [7.8]:
*.с =0.075^5-,
где Р —нагрузка на индентор; С = (2Сх+ 2Су)/4 (2Сх, 2Су—сумма размеров тре щин и диагонали отпечатка по соответствующей оси).
Твердость измерялась по Роквеллу и Виккерсу, при этом нагрузка на инден тор составляла 100 Н.
Результаты проведенных исследований по изучению процесса усадки образ цов свидетельствуют о том, что кинетика уплотнения образцов несколько отли чалась в зависимости от содержания в них УДП. Так, при содержании УДП до 5 % масс, усадка и ее скорость практически не отличались от таковых для образ цов, в которые УДП не вводили. При содержании УДП В4С 10 %масс, эти харак теристики были примерно на 5 % больше. Относительная плотность этих образ цов составляла ~ 0,98, по сравнению с 0,94 для образцов без добавления УДП.
Микроструктура образцов из шихты с УДП карбида бора характеризовалась высокой однородностью по зерновому составу. Размер зерен составлял 2...4 мкм. В структуре образцов, не содержащих УДП В4С, наблюдается нерарномерный рост отдельных зерен, размер которых достигает ~ 10 мкм (рис. 6.20 (I)).
Пределы прочности при сжатии а сж и при изгибе стиз, твердость, коэффици ент интенсивности напряжений Л^с для исследованных образцов представлены в табл. 6.1.
Заметно повышение физико-механических свойств керамики, полученной из шихты с добавками УДП В4С, синтезированного в импульсной плазме. Это связано, по-видимому, с большей плотностью керамики и более мелкозернис той ее структурой.
т

низкой дисперсности. Тем самым создаются условия, тормозящие процессы массопереноса между УДЧ и частицами низкой дисперсности, что, по-видимо му, и затрудняет рост кристаллов из частиц низкой дисперсности и ограничива ет максимальный размер кристаллов.
Компакты из промышленно получаемых порошков В4С с добавками УДП В4С, синтезированного в импульсной плазме, были использованы для изготов ления элементов керамической брони. Проведенные испытания изделий во ВНИИ спецтехники и связи МВД России показали перспективность использо вания полученных УДП В4С для изготовления ударопрочной керамики для средств индивидуальной защиты.
Керамический композит Si3N4—SiC является перспективным для получения материалов электротехнического и конструкционного назначения [6.39, 6.40]. Проведены исследования по созданию такого КМ и изучению его свойств с ис пользованием в качестве компонента шихты УДП SiC, синтезированного в им пульсной плазме.
Синтезируемый карбид кремния в качестве компонента шихты вводился до 20 % масс, в смесь с Si3N4 промышленного производства с дисперсностью ~1 мкм. Методом горячего прессования готовились образцы (температура спека ния 1950 К, давление 30 МПа, выдержка 30 мин). При компактировании образ цов в процессе нагрева при температуре 1200 К без приложения давления про водилась изотермическая выдержка в течение 30 мин для дегазации с поверх ности порошков адсорбированных газов.
Результаты исследования спеченных образцов свидетельствуют о том, что из шихты, содержащей УДП SiC, получен КМ с большей плотностью (относитель ная плотность 0,97) и с меньшим размером зерна (0,5...2 мкм) по сравнению с образцами, приготовленными на основе промышленно производимых Si3N4 и SiC (0,95 и 5...7 мкм соответственно —рис. 6.20 (II). Именно это, по-видимому, и является причиной того, что КМ на основе УДП SiC имел высокие механи ческие свойства (см. табл. 6.1).
Сравнение этих результатов с данными, полученными в Киеве в ИПМ АНУ [6.40] (аИЗг = 500 МПа, Кхс= 6,8 М Пам1/2) и Японии1(стшг= 900 МПа, К[С= 7,5 МПа-м1/2), свидетельствует о существенном улучшении механических характеристик мате риала Si3N4—SiC при использовании в качестве компонентов шихты УДП и приближении их к лучшим зарубежным аналогам.
В качестве областей возможного использования УДП, полученных в плазме конденсаторного разряда, непосредственно в дисперсном состоянии исследо валось их применение в качестве катализаторов и магнитно-абразивных по рошков [6.50 —6.52].
* Результаты совместныхисследованийфирмы MitsubishiGasChemicalСо иуниверситетав Осака.
12- 1548 |
337 |
Были изучены каталитические свойства синтезированных УДП железа и сплава Fe—Со для процесса прямого синтеза углеводородов из СО и Н2 (про цесс Фишера—Тропша) [6.50].
Проблема дефицита нефти, вызванная постепенным истощением ее запа сов, привлекает все большее внимание исследователей к технологиям прямого синтеза углеводородов из монооксида углерода и водорода, т. е. к так называе мому синтезу Фишера—Тропша. Этот процесс помимо синтеза жидких углево дородов позволяет получить ряд ценных полупродуктов для дальнейшего хими ческого синтеза, что стимулирует интенсивные исследования. В последнее вре мя активно ведутся работы по созданию новых каталитических систем с целью поиска путей управления селективностью этого процесса как в отношении распределения продуктов по молекулярным массам, так и в отношении получе ния алкенов, алканов и спиртов [5.29, 5.28].
Катализаторами синтеза углеводородов из СО и Н2 являются железо, никель, кобальт, рутений, на которых в промышленности этот процесс и осуществляет ся. В основном используются железные катализаторы из-за их высокой селек тивности и сравнительно низкой цены. С повышением дисперсности порошка железа его каталитические свойства возрастают. Это может быть объяснено уве личением удельной поверхности с уменьшением размера частиц, приводящей к возрастанию вклада поверхностной энергии в свободную энергию системы. Избыточная поверхностная энергия приводит к повышению химической и сорбционной активности порошка, влияет на решеточную и электронную под системы, приводит к образованию на поверхности дефектов и структур, не при сущих массивному состоянию этого вещества [5.1]. Все перечисленные факто ры могут привести к увеличению на поверхности катализатора количества ак тивных центров и изменению характера сорбции на них атомов и молекул. Многие авторы [5.29,6.41,6.42] считают размер частиц металлического катали затора главным фактором, влияющим на селективность и распределение про дуктов синтеза в процессе Фишера-Тропша.
В работе [6.50] приведены результаты исследований каталитических свойств ультрадисперсных порошков железа и сплава железо —кобальт, полученных пи ролизом карбонилов в плазме импульсного высоковольтного конденсаторного разряда. Целью проводившихся экспериментов было отыскание катализатора процесса гидрогенизации СО с наиболее высокой активностью и селектив ностью по олефинам (С2Н4, С3Н6).
В табл. 6.2 представлены данные о составе продуктов каталитической гидроге низации СО с использованием в качестве катализатора УДП железа и сплава Fe-C o. Для сравнения здесь приведены данные, полученные на катализаторах на основе порошка железа, изготовленного методом электрического взрыва прово лочек, а также промышленно используемого катализатора СА на основе плавле-
ного железа. При одинаковой суммарной активности по углеводородам (0,5...0,7 г/ч) УДП, полученные в импульсной плазме, имеют существенно более высокую селективность по наиболее ценным продуктам синтеза —олефинам. Это превосходит и лучшие зарубежные аналоги катализаторов на основе железа, имеющие, по данным [6.43], приблизительно такую же селективность, как и у отечественных катализаторов, что может быть связано с более высокой дисперс ностью плазмохимических порошков, полученных в импульсной плазме. Однако надо учесть, что значительный рост селективности при переходе к плазмохими ческим порошкам может быть вызван и различиями в фазовом составе порош ков, например, присутствием в плазменных порошках высокотемпературной у- фазы железа или более благоприятными соотношениями оксидов [6.44, 6.45].
Таким образом, УДП железа и сплава Fe—Со, синтезированные в импульс ной плазме, могут считаться перспективными для создания на их основе ката лизаторов для получения олефинов прямым синтезом из СО и Н2 при атмос ферном давлении.
Возможность получения в импульсной плазме УДП композитов, в которых КМ формируется непосредственно в микрообъеме частицы, дала возможность использовать УДП, содержащие ферромагнитную составляющую и карбидную фазу, для магнитно-абразивного полирования (МАЛ) поверхностей различных материалов.
Таблица 6.2. Сравнение состава продуктов процесса пирогенизации СО, получаемых на разных ка тализаторах ( Т = 573 К, Р = 0,1 М П а)
Способ получения |
Средний размерчастиц |
|
Состав продуктов |
||
по Фишеру-Тропшу, %ат. |
|||||
катализаторов |
порошка, dcp, нм |
||||
метан |
парафин |
олефины |
|||
|
|
||||
Метод электрического |
35 |
53 |
18 |
29 |
|
взрыва проволочек |
25 |
52 |
19 |
29 |
|
На основе плавленогожелеза |
15 |
47 |
20 |
33 |
|
100 |
68 |
22 |
10 |
||
Метод импульсной плазмы — |
8 |
38 |
12 |
50 |
|
пиролиз Fe(CO)5 |
|
|
9 |
62 |
|
Метод импульсной плазмы— |
12 |
29 |
|||
пиролиз Fe(CO)5—Co2(CO)g |
|
|
|
|
|
(Fe:Co = 9:1) |
|
|
|
|
Метод МАП предназначен для снятия тонких (0,1 мкм и менее) слоев метал ла и улучшения качественных характеристик обработанной поверхности. При МАП деталь обрабатывается с помощью порошков, частицы которых прижи маются к этим деталям посредством магнитного поля. Магнитное поле выпол няет роль связки, формирующей из отдельных зерен порошка эластичный аб разивный инструмент, и обеспечивает силовое воздействие, с помощью которо
го зернам порошка сообщаются нормальные и тангенциальные силы резания. Особенностью формируемого магнитным полем абразивного инструмента яв ляется его способность нивелироваться относительно обрабатываемой поверх ности детали, копируя ее профиль. При этом можно полировать сложнопро фильные поверхности, используя прямолинейные движения, и нет необходи мости периодически править инструмент [6.26, 6.46]. Большое значение при использовании магнитно-абразивных материалов имеет подбор необходимой дисперсности порошка в зависимости от исходной и заданной конечной шеро ховатости поверхности. В случае малой исходной шероховатости (финишная обработка) необходим более мелкий порошок. Например, использование ультрадисперсных МАП, которые были приготовлены методом испарения-конден сации порошковых смесей на основе железа, титана и углерода в аргоновой плазме высокочастотного индукционного разряда, позволило достичь 11—12-го класса шероховатости с 7-го класса за 30...60 с при финишной обработке дета лей из стали ШХ15 [6.47].
Такие МАП должны иметь определенные магнитные свойства: минимальное значение коэрцитивной силы (# с) и возможно более высокие значения намаг ниченности насыщения (4nls).
Исследование УДП KM Fe—ТЮ (20 % масс.) показало, что величина Нсу них составляет ~ 0,6 кЭ, а 4nls ~ 5000 Гс. Введение в эти УДП кобальта ( 2...3 % масс.) повышает значение намагниченности насыщения до ~ 12500 Гс и уменьшает коэрцитивную силу до ~ 0,3 кЭ.
Результаты использования УДП КМ в качестве магнитно-абразивного мате риала представлены в табл. 6.3. На основе полученных результатов можно счи тать, что УДП KM Fe—НС, Fe—Со—НС являются высокоэффективными маг нитно-абразивными материалами.
Таблица 6.3. Абразивныесвойствамагнитно-абразивныхУДП KM Fe-TiC
Обрабатываемый |
Время |
Шероховатостьповерхности Ra, мкм |
|
материал |
обработки,с |
до МАП |
после МАП |
Д161 |
30 |
0,2 |
0,025 |
АЛ |
30 |
0,3 |
0,038 |
ЭИ961 |
120 |
0,4 |
0,04 |
ВТ-9 |
30 |
0,35 |
0,032 |
ВТ-18у |
30 |
0,26 |
0,02 |
В качестве других реально возможных областей применения полученных УДП можно считать следующие. Чрезвычайно высокая дисперсность продуктов пиролиза в импульсной плазме паров Fe(CO)5 и смеси паров Fe(CO)5 и Со2(СО)8 обеспечивает устойчивость суспензии на основе этих УДП в гравитационном поле. В сочетании с этим большое значение намагниченности насыщения (4TU/ S), которая у дисперсного продукта пиролиза Fe(CO)5 составляет ~ 5500 Гс, а