
книги из ГПНТБ / Фельдман Л.С. Неразрушающий контроль качества клеесварных соединений
.pdfТолщина тонкой |
Допустимый |
||
детали в соеди |
|
диаметр |
|
нении, ММ |
|
ядра, |
мм |
0,3 |
. |
2,5+'-° |
|
0,4 |
• |
2 ,5+' . ° |
|
0,5 |
. |
30+' . ° |
|
0,6 |
• |
3 0+,1 -0 |
|
0,8 |
. |
3 5+1 -0 |
|
1,0 |
• 4 0 + \ ° |
||
1.2 |
• |
7,0+Jj |
|
2,0 |
|||
2,5 |
|
g'n-H,5 |
|
3,0 |
|
||
4,0 |
: i2;o+9 |
2 -° |
|
5,0 |
• |
н а д |
|
6,0 |
. |
18,0+ 2 -° |
|
7,0 |
При сварке деталей неравной толщины диаметр ядра для алюминиевых сплавов должен быть не менее указан ного выше для тонкой детали. При сварке трех деталей диаметр ядра определяется раздельно для каждой пары сопрягаемых деталей. Увеличение размеров литой зоны сварной точки более указанных в таблице не является при знаком брака.
При точечной сварке плакированных сплавов толщиной свыше 3 мм на периферии литой зоны в плоскости соеди нения обычно находится часть нерасплавившегося плаки рующего слоя. В этом случае за диаметр ядра следует при нимать расстояние между краями нерасплавившейся плакировки.
Величина вмятин от электродов на поверхности деталей характеризуется отношением глубины отпечатков к тол
щине детали |
у • 100% |
(рис. 78). Глубина |
вмятины |
изме |
|||
ряется |
отдельно для |
каждой из деталей |
|
[ ^ - |
• 100%; |
||
~ • 100 %j с помощью |
индикатора часового типа |
с ценой |
|||||
деления |
0,01 мм и на шлифах с помощью |
микроскопа. |
|||||
Величина |
вмятин от электродов при |
сварке |
деталей |
||||
с отношением |
толщин не более 2 : 1 не должна |
превышать |
|||||
15 %, а в деталях с соотношением толщин более 2 |
: 1 |
— 20 %. |
|||||
При |
металлографических исследованиях шлифов |
обна |
руживаются внутренние трещины, поры и раковины. Нали-
171
чие дефектов в шлифах технологической пробы свидетель ствует о неправильно подобранном режиме сварки. В свар ных соединениях, выполненных по слою клея или герме тика, в шлифах в ряде случаев обнаруживаются внутрен ние дефекты, возникшие вследствие высыхания клея или большой его вязкости перед сваркой. В этих случаях в литой зоне соединения могут быть остатки клея, большая пори стость и внутренние выплески.
В процессе сварки детали и контрольные образцы, а также готовые сварные изделия подвергают внешнему осмотру: сварные точки осматривают невооруженным гла зом или через лупы 4—10-кратного увеличения, при по мощи индикатора проверяют глубину вмятин от электрода; измерительной линейкой или шаблоном измеряют рас стояние между точками и проверяют расположение точек; наличие непровара на деталях толщиной до 1 мм опреде ляют тонким щупом (0,15 мм) путем ощупывания плоскости стыка деталей в зоне сварной точки, а также специальным пробником путем местного отгиба кромки детали.
Сварные точки с недостаточно развитым ядром под действием отрывающих усилий издают легкий треск и раз рушаются. Точки с удовлетворительной сваркой не раз рушаются.
При внешнем осмотре выявляются наружные дефекты сварных соединений (трещины, выплески, следы меди на поверхности точек и другие), а также контролируются раз меры и форма отпечатков от электродов.
Размеры отпечатков не связаны однозначно с разме рами литой зоны соединений, поэтому по ним нельзя судить о качестве сварки. Однако изменение размеров отпечатков при постановке ряда точек с неизменной настройкой машины свидетельствует о нарушении условий сварки и возможном ухудшении качества соединений. По нарушению правиль ной формы отпечатков (появление эллипсности, непра вильной окружности и т. п.) можно обнаружить плохую заточку электродов, либо перекос деталей при сварке.
Отклонения величины шага сварных точек от чертежа не должны превышать ±2 мм, смещение сварных точек относительно оси допускается не более +1 мм. При поста новке точек близко к краю нахлестки могут возникать разрывы кромки нахлестки, что недопустимо.
Методика выборочного рентгеновского контроля клее сварных конструкций предусматривает проведение одно-
172
двухили трехэтапного просвечивания в зависимости от результатов предыдущих работ. Так первый этап рентге новского контроля,начинается с 10—20% просвечивания наиболее подозрительных участков сварных узлов, отме ченных контролером (места, соответствующие остановкам при сварке, зачистке электродов и т. п.). Если число де фектных точек не превышает установленных норм, просве чивание заканчивают, а узел принимают; если превышает, узел подвергают 50% просвечиванию, а затем опять под считывают число дефектных точек. При числе дефектных точек, не превышающем допустимые нормы, узел прини мают, а при превышении — подвергают 100% просвечива нию и после этого делают окончательный вывод о качестве контролируемого узла. . . . . . .
Как показал опыт контроля, при правильно . подо бранных режимах сварки и отлаженном оборудовании рент геновское просвечивание в основном заканчивается после первого этапа и, как исключение, переходит на второй илитретий этап.
Для рентгеновского просвечивания сварных соедине ний применяют передвижной аппарат типа РУП-60-20-1 или РУМ-7 с трубкой 1БПВ1-60 и плавной регулировкой высокого напряжения в диапааоне 10—60 /се, силы тока в диапазоне 0—20 ма.
Для обеспечения контроля крупногабаритных панелей и повышения степени защиты от рентгеновских лучей рент геновский аппарат РУМ-7 модернизируют:
а) |
пульт управления аппаратом |
снимают с тележки |
и выносят в операторскую комнату; |
вместо пульта управ |
|
ления |
устанавливают противовес в 50—60 кГ; |
б) провода силового электропитания и шланги водяного охлаждения удлиняют настолько, чтобы аппарат можно было передвигать вдоль контролируемых деталей; при такой переделке практически можно контролировать де тали любой длины, если это позволяют размеры поме щения;
в) если ширина контролируемой детали больше двойного полезного вылета консоли аппарата (2 м), штангу креп ления рентгеновской трубки к штативу удлиняют;
г) для повышения четкости рентгенограмм рентгенов скую трубку 1БПВ1-60 аппарата РУМ-7 заменяют на трубку 0,8БСВ2-Мо при соответствующей модернизации бленды аппарата.
12 3-861 |
173 |
Для рентгеновского просвечивания используют пленку типов РТ-1, РТ-2, РТ-5. Лучшие результаты получают при использовании высококонтрастной, малочувствитель ной пленки РТ-5.
При просвечивании фокусное расстояние F = = 500 -f- 700 мм. Для сохранения диапазона нормальных фотографических плотностей вдоль всего просвечиваемого поля необходимо, чтобы фокусное расстояние было не меньше l,5d, где d — диаметр облучаемого поля.
Ориентировочные режимы рентгеновского просвечи вания сварных соединений из алюминиевых сплавов на аппарате РУМ-7 приведены в табл. 13.
Крупногабаритные детали при просвечивании распола гаются на рольгангах или подставках. Детали, имеющие ширину больше двойного полезного вылета консоли рент геновской установки, размещают на приспособлениях, обес печивающих вертикальное или наклонное положение де тали при экспонировании.
Рентгеновская пленка для просвечивания |
помещается |
в конверт из неактиничной бумаги и кассету из |
дерматина. |
Наиболее удобно крепить кассеты к просвечиваемой детали (панель одинарной или двойной кривизны) с помощью ре зинового пояса с двумя крючками — пряжками, укреп ленными по краям детали. Изменяя положение пряжек, можно с помощью одного и того же пояса контролировать детали различной ширины.
На проэкспонированной рентгеновской пленке должны быть указаны номера просвечиваемых изделий и детали, а также порядковый номер снимка. Чтобы найти дефект ные точки на детали, по рентгеновскому снимку делается, привязка его к одной из просвечиваемых точек с помощью свинцовой стрелки-маркира, укладываемого на деталь. Место: расположения стрелки на детали отмечается ка рандашом.
В рентгеновской лаборатории должны быть изготовлены эталонные рентгенограммы для всех просвечиваемых ма териалов и толщин свариваемых пакетов. Результаты рент геновского контроля деталей фиксируют в регистрацион ном журнале лаборатории, на детали выписывают свиде тельство и производят запись в технологическом паспорте.
Наличие непроклеев в клеевых соединениях клеесвар ных.конструкций определяют с помощью ультразвукового испытателя клеевых 'соединений ИКС-IB (рис. 79). При
174
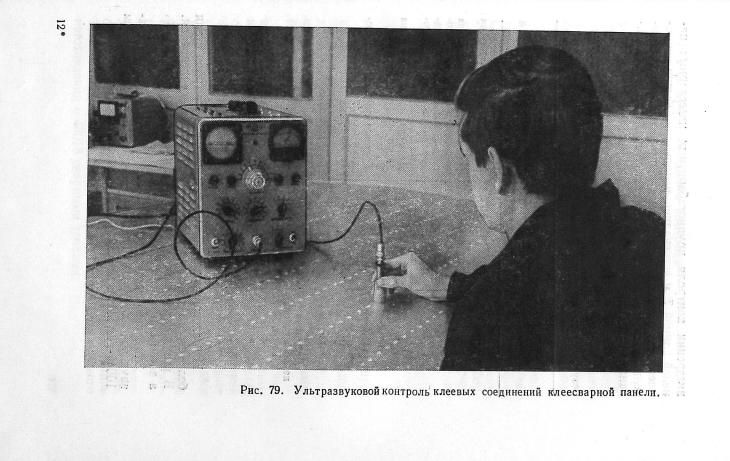
внедрении контроля крупногабаритных клеесварных па нелей длиной 7 м встречались непроклеи. Обычно непроклеи располагались на одном-двух профилях и это свиде тельствовало о нарушении технологического режима склеи вания (табл. 38).
Таблица 38
Результаты проверки качества склейки клеесварных панелей
Суммарная |
Общая |
Процент |
|
непрокле- |
|
||
площадь |
площадь |
Примечания |
|
непроклеев, |
склеива |
енных |
|
см' |
ния, см- |
участков, |
|
|
|
% |
|
1050 |
2100 |
50 |
|
510 |
5700 |
9 |
|
131 |
1000 |
13 |
|
165 |
4759 |
3,5 |
|
123,5 |
4050 |
3,0 |
|
70 |
6750 |
1,0 |
|
20 |
4500 |
0,5 |
|
43 |
4500 |
1,0 |
|
13 |
2400 |
0,5 |
|
Дефектов |
2100 |
0 |
|
не обнаружено |
|||
1000 |
0 |
||
То же |
|||
» |
3450 |
0 |
|
|
2700 |
0 |
|
» |
2400 |
0 |
|
» |
2500 |
0 |
Нарушение технологии склеивания Из общего количества
непроклеев 18 общей пло щадью 200 см2 были распо ложены на одном из про филей Дефекты расположены на одном профиле То же
Крупные дефекты располо жены на одном профиле То же
—
—
—
—
—
—
—
На основании данных ультразвукового контроля стали более строго соблюдать технологический режим склеивания.
В результате резко |
уменьшилось количество непроклеев, |
а затем они совсем |
исчезли. |
Это дало возможность применить выборочный ультра |
|
звуковой контроль |
качества склейки при обязательном |
100%-ном внешнем осмотре всех клеевых соединений.
Результаты длительного контроля клеесварных конструкций
Для оценки эффективности применяемой системы конт роля технологического процесса изготовления клеесвар ных соединений, а также качества готовых конструкций из алюминиевых сплавов были проанализированы и стати стически обработаны результаты длительного рентгенов ского просвечивания большого числа клеесварных кон струкций.
Для оценки качества дефектных точек, пропущенных в клеесварных панелях, был применен статистический ме тод, предложенный академиком А. Н. Колмогоровым. Согласно этому методу оценка производится по числу выяв ленных дефектных точек в проконтролированных выбор ках. В этом случае доля пропущенных дефектных точек (2л:1) в принятых клеесварных панелях определится по формуле
Sx1 |
= Бе ± j/^ES2 |
+ 0,86 • у Ё^Ѳ* + 2,34 • VzJ* , |
||
где е — оценка |
определяемой величины; |
ô — табулиро |
||
ванная |
функция; |
Ѳ = ~—параметр, |
определяющий |
|
долю выборки |
во всей генеральной совокупности; 2„ — |
|||
суммирование по малочисленным партиям; |
2 г — сумми |
|||
рование по большим |
партиям. |
|
Для расчета количества дефектных точек, пропущенных в принятых клеесварных панелях, автор взял результаты выборочного (10%) рентгеновского контроля 100 панелей с 108152 сварными точками. При расчете малочисленной партией считались панели с числом сварных точек менее 1000, большой партией — с числом сварных точек более 1000.
Расчет показал, что количество пропущенных дефект ных точек за счет применения 10%-го рентгеновского конт роля составляет 0,245 ± 0,055%.
Для сравнения расчетных данных с фактическим чис лом дефектов, пропущенных при выборочном контроле, было произведено 100%-ное рентгеновское просвечивание 71 клеесварной панели из сплава Д16 производственного изготовления с 43018 сварными точками:
177
|
|
|
|
шт. |
|
% |
|
Количество просвеченных точек . . . |
: |
43018 |
|
— |
|||
Количество точек с дефектами типа: |
|
|
|
|
|
||
трещины |
. |
|
64 |
|
0,15 |
||
непровары |
|
|
21 |
|
0,05 |
||
поры, раковины . .' |
|
|
18 |
|
0,04 |
||
выплески |
|
|
75 |
|
0,17 |
||
Всего |
|
|
178 |
0,41 |
|
||
• Сравнение |
расчетных данных |
по |
числу |
пропущен |
|||
ных дефектных |
точек (0,2—0,3%) с фактически |
найденным |
|||||
числом (0,41 %) |
показывает удовлетворительное совпадение |
||||||
полученных результатов. |
|
|
|
|
|
|
|
Результаты длительного рентгеновского |
контроля клее |
сварных конструкций сведены в табл. 39. Результаты оценки
количества клеесварных панелей с теми |
или иными |
|||||||||
видами |
дефектов приведены в табл. 40. |
|
|
|
||||||
|
|
|
|
|
|
|
|
|
Таблица |
39 |
Результаты |
длительного рентгеновского просвечивания |
|
||||||||
клеесварных |
|
конструкций |
|
|
|
|
|
|
||
Период |
|
|
Общее количество |
Количество про |
Количество де |
|||||
|
|
фектных точек |
||||||||
контроля |
анализируемых точек |
свеченных точек |
(% по отношению |
|||||||
|
|
|
|
|
|
|
|
|
к просвеченным) |
|
Освоение |
сварки |
247000 (100%) |
24700 (10%) |
300 (1,2%) |
||||||
Серийное |
произ |
1 000 000 ( 100%) |
110000(10,1%) |
890 (0,8%) |
||||||
водство |
|
|
|
|
|
|
|
|
|
|
|
|
|
|
Таблица |
40 |
|
|
Таблица |
41 |
|
Результаты |
оценки |
количества |
|
Фактический объем |
|
|||||
клеесварных |
|
панелей с дефектами |
|
|||||||
|
рентгеновского |
контроля |
|
|||||||
|
|
|
Количество панелей |
клеесварных панелей |
|
|||||
|
|
|
|
Количество панелей, |
||||||
|
|
|
с дефектами типа |
|
Количество |
|||||
|
|
|
|
|
|
|
подвергавшихся |
|||
|
|
|
|
|
«Я |
Я |
просвечен |
просвечиванию |
||
.. Количество |
|
|
|
S O- |
ных |
|
|
|
||
просвеченных |
|
|
3 |
S |
£i |
панелей |
|
|
|
|
|
|
X |
Я |
ю % |
5 0 % |
100% |
||||
панелей |
|
2 |
1 | |
11? |
|
|||||
|
|
|
|
|
||||||
|
|
|
і> |
5- m |
|
|
|
|
||
|
|
|
ч |
=JCL) CLсо |
HlС S « |
5053 |
4799 |
199 |
55 |
|
|
|
|
с |
|||||||
|
|
|
а |
ь s |
|
|
100% |
95% |
3,95% |
1,05 |
5053 |
|
|
253 |
87 |
79 |
|
|
|
|
|
100% |
|
|
5,1% |
1,7% |
1,5» |
|
|
|
|
178
Поскольку для контроля клеесварных конструкций применяется методика выборочного' рентгеновского про свечивания, предусматривающая трехэтапное проведение работ (просвечивание 10%, 50% и 100%-ное сварных то чек) в зависимости от качества соединении, представляет интерес оценка фактического объема рентгеновского конт роля. Результаты обобщения по 5053 панелям сведены в табл. 41. Из таблицы видно, что в основном применяется 10%-ное просвечивание.
Анализ результатов рентгеновского просвечивания сварных соединений показывает лучшее качество сварки конструкций отечественного производства (табл. 39) по сравнению с зарубежными (табл. 42). Полученные средние значения числа дефектных точек могут служить критерием оценки степени отлаженности технологического процесса и состояния сварочного оборудования при анализе состоя ния производства клеесварных конструкций.
Таблица 42
Результаты рентгеновского просвечивания сварных конструкций по данным зарубежных фирм
|
|
|
Количество |
|
|
Общее количество |
Количество |
дефектных |
|
Наименование |
точек (% по |
|||
анализируемых |
просвеченных |
|||
фирмы |
отношению |
|||
точек |
точек |
|||
|
к просвечен |
|||
|
|
|
ным) |
«Боинг» (контроль
втечение длитель
ного времени) [72] |
7 230 000(100%) |
1 800000(25%) |
46 000(2,5%) |
||
«Боинг» |
(100%-ное |
|
|
|
|
просвечивание |
свар |
|
|
|
|
ных соединений |
двух• |
|
|
|
|
самолетов) |
[72] |
|
300 000 (100%) |
300 000 (100%) |
9000 (3%) |
«Хендли |
Пейдж» |
|
|
|
|
(контроль |
173 |
свар |
|
|
|
ных панелей) [87] |
224 000 (100%) |
21 500 (9,6%) |
811 (3,8%) |
Помимо контроля качества изготовления сварных со единений, в условиях производства производится наблю дение за поведением сварных конструкций в условиях эксплуатации и капитального ремонта. При проверке в течение более 10 лет в контролируемых конструкциях
179
не наблюдалось случаев разрушения, появления трещин или вырывов в сварных точках. При выборочной вырезке образцов из конструкций, находящихся в эксплуатации, с последующим металлографическим анализом и механи
ческими |
испытаниями |
установлено, |
что |
внутренних |
дефектов, |
деформационных явлений, |
а также |
изменений |
|
в структуре сварных точек не наблюдается. |
|
|||
Система |
контроля |
качества ответственных |
клеесвар |
ных конструкций внедрена в серийное производство и ус пешно применяется в течение многих лет.