
книги из ГПНТБ / Колпашников, А. И. Армирование цветных металлов и сплавов волокнами
.pdfфрикционной связи между компонентами армированного образца ход кривой на всех участках машинной диаграм мы нестабилен. При соединении высокого качества ход кривой на нервом участке равномерен, а затем, при до стижении напряжений, достаточных для разрушения от дельных волокон и связей .между волокнами и матрицей, кривая принимает «пилообразный» характер, т. е. идет нестабильно. Протяженность нестабильного участка не значительна, он предшествует разрушению образца. На существование такого участка на кривой напряжение — деформация указывают также Саттон и Чорне [1], при водя данные исследования процесса армирования сереб ра волокнистыми монокристаллами окиси алюминия. Появление участка с нестабильным ходом кривой они объясняют для этого случая разрушением отдельных монокристаллов, А120 3 с наименьшей прочностью. При этом нагрузка пропорционально перераспределяется на оставшиеся более прочные кристаллы, и быстрого разру шения образца не происходит. Важный момент исследо вания процесса армирования — определение влияния способа получения армированного материала на состоя ние и свойства волокон, что, в конечном счете, определя ет конечные свойства материала и позволяет судить о степени рациональности принятой технологической схе мы. Наиболее подходит для этой цели моделирование процесса производства армированного полуфабриката (например, процесса прокатки армированных листов) с соблюдением особенностей принятой технологии. .Кроме того, достаточно объективные данные можно получить при исследовании волокон, извлеченных из компактного армированного материала с помощью вытравливания. Моделирование применимо в тех случаях, когда армиро ванный материал изготавливается методами обработки давлением, извлечение волокон вытравливанием возмож но для любого случая (т. е. не зависнет от способа -изго товления армированного полуфабриката или изделия), однако в последнем случае необходимо обращать особое внимание на выбор состава травителя с тем, чтобы не внести каких-либо изменений в характеристики волокон.
В процессе исследований оталеалюминиевых -армиро ванных листов метод моделирования был использован для определения влияния направления прокатки на -со стояние и свойства волокон (в частности, был-а подробно исследована на-ра Д2'0—Х18Н9Т). Перед прокаткой за
201
готовок, состоящих из двух пластин алюминиевого спла ва марки Д20 и размещенного между ними слоя прово лочных волокон из стали марки Х18Н9Т диаметром 0,8 мм, на поверхность компонентов наносили разделитель ный слой (графит), предотвращавший схватывание как матричных элементов между собой, так и волокон с мат рицей. Модельные образцы прокатывали в двух направ лениях— вдоль и поперек расположения волокон. Де формация вдоль волокон была различной, суммарная степень деформации в двух направлениях была постоян ной (50%). Каждую серию образцов прокатывали при температурах 350, 400 и 450°С. Для выявления влияния температур на прочность волокон одновременно с модель ными образцами нагревали проволочные образцы-свиде тели. После прокатки извлекали волокна из пластин и проводили исследования их геометрии, а также испыты вали на растяжение. Исследования геометрии заключа лись в замерах диаметра на различных участках волокна при помощи инструментального микроскопа. Кроме то го, фиксировали присутствие и характер поверхностных дефектов и повреждений волокон. В результате исследо ваний установлено, что горячая прокатка моделей сбор ных заготовок сталеалюминиевых композиционных ли стов не вызывает появления заметных искажений сече ния волокон и дефектов поверхности, резко снижающих их прочность. В то же время прокатка вдоль волокон име ет весьма ограниченную допустимую степень деформа ции, при повышении которой волокна сначала ослабля ются из-за образования множества местных утонений, а затем разрушаются на отдельные отрезки.
Результаты испытания волокон, извлеченных из мо дельных образцов, на растяжение приведены в табл. 50.
Проведенное исследование позволило установить до пустимый коэффициент вытяжки при прокатке вдоль во локон (для данного вида высокопрочных стальных воло кон он равен — 1,10). Выводы, сделанные при проведении модельных исследований, неоднократно проверены ис следованием изломов компактных армированных листов, состоящих из тех же компонентов и полученных по тем же режимам прокатки. Результаты исследования изломов хорошо согласуются с данными модельных исследова ний. Помимо исследования изломов, проводили испыта ния компактных армированных листов на растяжение с целью выявления влияния степени деформации при про-
202
Таблица 50
Влияние температуры прокати и величины деформации вдоль волокон на свойства волокон в модельных сталеалюминиевых
образцах
|
|
|
Предел прочности |
Температура |
Коэффициент вытяжки при |
волокон, извлеченных |
|
начала |
прокатке вдоль волокон |
из модельного |
|
прокатки, °С |
|
|
образца, |
|
|
|
МН/м2 (кгс/мм2) |
350 |
Не деформированные |
при про |
1850 (185) |
|
катке волокна |
|
1850 (185) |
|
|
|
1870 (187) |
350 |
Поперечная прокатка |
|
1930 (193) |
|
|
|
2020 (202) |
|
|
|
1930 (193) |
|
|
|
2020 (202) |
|
|
|
2060(206) |
350 |
1,035 |
|
2000 (200) |
|
|
|
1980 (198) |
|
|
|
2010 (201) |
|
|
|
1960 (196) |
|
|
|
1980 (198) |
350 |
1,075 |
|
1900 (190) |
|
|
|
1900 (190) |
|
|
|
1950 (195) |
350 |
1,124 |
|
1780 (178) |
|
|
|
1890 (189) |
|
|
|
1800 (180) |
350 |
1,170 |
|
1630 (163) |
|
|
|
1420 (142) |
|
|
|
1600 (160) |
|
|
|
1670 (167) |
|
|
|
1700 (170) |
400 |
Не деформированные |
при про |
2070 (207) |
|
катке волокна |
|
1880 (188) |
|
|
|
2100 (210) |
|
|
|
2090 (209) |
400 |
Поперечная прокатка |
|
2060 (206) |
|
|
|
2060 (206) |
2040 |
(204) |
2080 |
(208) |
203
Продолжение табл. 50
|
|
Предел прочности |
Температура |
Коэффициент вытяжки при прокатке |
волокон, извлеченных |
начала прокатки, |
вдоль волокон |
из модельного |
°С |
|
образца, |
|
|
МН/м2 (кгс/мм8) |
400 |
1,05 |
1820 (182) |
|
|
2020 (202) |
|
|
2030 (203) |
|
|
1960 (196) |
|
|
2000 (200) |
400 |
1,10 |
1820(182) |
|
|
1780(178) |
|
|
1850 (185) |
400 |
1,15 |
1730 (173) |
|
|
1760 (176) |
|
|
1590(159) |
|
|
1420 (142) |
400 |
1,20 |
1480 (148) |
|
|
1560 (156) |
|
|
1620 (162) |
|
|
1500 (150) |
450 |
Не деформированные при про |
1950 (195) |
|
катке волокна |
1910(191) |
|
|
1930(193) |
450 |
Поперечная прокатка |
1960 (196) |
|
|
1900 (190) |
|
|
1930 (193) |
|
|
1930 (193) |
450 |
1,05 |
1900(190) |
|
|
1870 (187) |
|
|
1980(198) |
450 |
1,11 |
1650 (165) |
|
|
1780 (178) |
|
|
1590 (159) |
450 |
1,15 |
1830 (183) |
|
|
1540(154) |
|
|
1640 (164) |
204
|
|
Продолжение табл. 50 |
|
|
Предел прочности |
Температура |
Коэффициент вытяжки при |
волокон, извлеченных |
начала прокатки, |
прокатке вдоль волокон |
из модельного |
°С |
|
образца, |
|
|
МН/м2 (кгс/мм2) |
450 |
1,21 |
1400 (140) |
|
|
1480 (148) |
|
|
1400 (140) |
жатке заготовок вдоль расположения волокон на их проч ность. Эти испытания проводили на образцах различных составов.
Влияние продольной деформации (при прокатке вдоль волокон при температуре 400°С) на прочность ком пактного армированного материала Д20—Х18Н9Т при суммарной степени деформации 50% приведене ниже:
Степень |
деформации |
вдоль |
9,1 |
18,2 |
27,3 |
36,4 |
волокон, |
% ..................................... |
0 |
||||
Предел прочности |
261 |
242 |
231) |
219 |
218 |
|
МН/м2 |
|
|||||
кгс/мм2) |
........................................ |
(26,1) (24,2) |
(23,1 |
(21,9) |
(21,8) |
В процессе изучения армированных материалов важ ное место занимают металлографические исследования, позволяющие установить характер взаимодействия во локон и матрицы, наличие и состояние переходной зоны, состояние компонентов после нагрева, деформации и пол ной упрочняющей термической обработки. В ряде случа ев металлографические исследования позволяют уста новить и дефекты в армированных материалах.
На рис. 118 приведены микрофотографии армирован ных сталеалюминиевых материалов.
К числу методов исследования армирования материа лов относится и метод определения микротвердости. На рис. 119 показана зависимость микротвердости матрицы из сплава марки АМгб от расстояния между контролиру емой точкой и границей волокно—матрица. В данном случае выявлено, что волокно воздействует на прилегаю щие к нему слои матричного материала и вызывает в них повышенное увеличение твердости (и, по-видимому, прочности). Определяя микротвердость матрицы, можно прогнозировать изменения структуры, возможные дефек ты и т. д., которые, например, должна внести упрочняю щая термическая обработка.
205
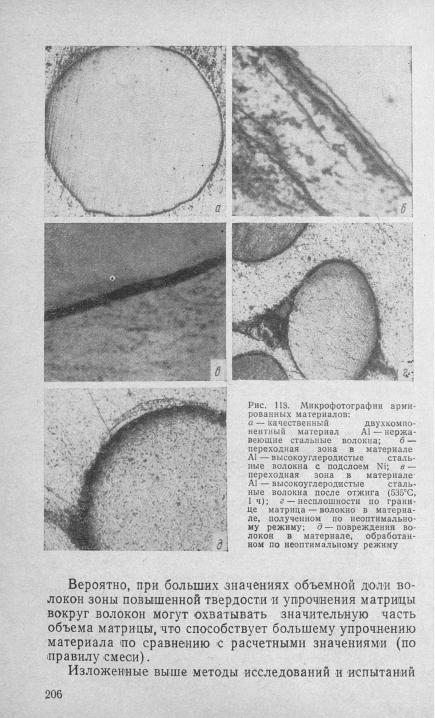
позволяют получить пред ставление о всех слож ных зависимостях струк турных и технологиче ских факторов при созда нии армированных мате риалов. Свойства этих ма териалов освещены в сле дующей главе.
Рис. 119. Распределение микро твердости в матрице армирован ного материала АМгб—Х18Н9Т
$ |
«3 |
Апо |
lL— Li----1------- 1— l J — |
|
S; |
^ |
(gg) |
||
*• |
K |
(80) |
o ioo 200 |
3oo m |
•, |
|
_ |
||
|
|
|
Расстояние |
от края |
волокна, мкм
Глава V
СВОЙСТВА АРМИРОВАННЫХ МАТЕРИАЛОВ
Армирование . материалов и сплавов волокнами в большинстве случаев преследует щель повышения проч
ности, удельной прочности |
(при комнатной, либо при |
повышенных температурах), |
упругости, т.е. повышение |
прочностных характеристик матричных материалов. Предел прочности и модуль упругости армированного материала обычно рассчитываются через соответствую
щие показатели компонентов и их объемные |
доли [см. |
|
гл. I, уравнение (26)] |
по правилу смеси. |
сложнее, |
В действительности |
этот вопрос гораздо |
|
так как, помимо величин предела прочности |
и модуля |
упругости компонентов, напряжения в матрице в момент разрушения волокон и объемных долей матрицы и воло кон, характеристики армированных материалов зави сят также от множества других факторов. К ним сле дует относить:
1)метод получения армированного полуфабриката или изделия;
2)уровень технологии производства;
3)природа матрицы и волокон;
4) присутствие или отсутствие промежуточного слоя
между матрицей и волокном |
(в случае присутствия — |
природа материала этого слоя); |
волокон (степень их |
5) !взаимное расположение |
|
случайной разориентировки); |
|
207
6) вероятность непосредственного контакта |
волокон |
в армированном изделии или полуфабрикате, |
завися |
щая от объемной доли, технологии армирования и жест
кости |
волокон (ослабление при контакте волокон зави |
сит |
от их природы); |
7)температурные условия армирования;
8)добавочная деформация волокон в процессе армирования;
9)наличие и режим окончательной термической об работки армированного материала.
В работах |
зарубежных |
исследователей, в частности |
|||
Саттона |
и |
Чорне [1], |
делаются |
попытки |
косвенно |
учесть |
влияние всех факторов, а |
именно |
определять |
||
«действительную» прочность армированных |
материа |
лов через «действительные» характеристики компо нентов, объединенных в материал.
Однако не следует забывать, что одно и то же изме нение действительных характеристик компонентов и отличие их значений от первоначальных >(т. е. характе ристик компонентов до сборки заготовок) может быть вызвано различными факторами. Эти факторы, кроме всего прочего, взаимозависимы, т. е. в каждом конкрет ном случае нужно учитывать все факторы, либо группы, либо отдельные факторы. Тогда замена прочности «дей ствительно прочностью», например, в формуле расче та предела прочности армированного материала, втео-
рии сводящаяся лишь к замене символов (а в |
на (Тв~), |
|
на практике представляют собой сложную задачу. |
||
От точности решения этой задачи |
зависит |
стабиль |
ность результатов армирования, т. е. |
целесообразность |
|
самого процесса армирования. |
|
|
Введение в правило смеси коэффициента использо вания прочности волокон и учет средней длины волокон решают задачу уточненного расчета лишь частично.
Правильнее не заменять символы исходных характе ристик компонентов символами «действительных» ха рактеристик, а вводить общий коэффициент изменения характеристик компонентов, который в свою очередь должен представлять собой произведение частных коэффициентов, учитывающих влияние отдельных фак торов. В этом случае полученные отклонения от резуль тата расчета по классическому правилу смеси можно предвидеть, адресуясь к конкретным факторам, свойст венным проектируемому технологическому процессу
208
армирования, либо к составу армированного материала и т. д., а также к статистическим данным о количествен ном влиянии этих факторов. Такое представление поз волит вносить корректировку в состав заготовки, режим обработки, т. е. в технологию производства армирован ных полуфабрикатов или изделий с заданными свойст вами.
Для того чтобы располагать такими обширными статистическими данными, необходимо провести мас совое исследование в лабораторных и производственных условиях, досконально изучить влияние всех факторов на конечные характеристики армированных материа лов.
К настоящему времени накоплены данные о свой ствах лишь небольшого числа пар компонентов. Наибо лее изучены свойства армированных материалов алю миний—сталь и медь—вольфрам.
Ниже рассмотрим влияние процесса армирования различными волокнами на свойства цветных металлов и сплавов, а также влияние различных факторов на ре зультат армирования.
1. СВОЙСТВА АРМИРОВАННЫХ МАТЕРИАЛОВ НА ОСНОВЕ АЛЮМИНИЯ И МАГНИЯ
Из армированных материалов наиболее изучены
конструкционные |
материалы |
на |
основе |
алюминия и |
||
его |
сплавов, армированных |
волокнами |
(чаще |
всего |
||
проволочными) из высокопрочных сталей. |
В настоящее |
|||||
время получены |
материалы этой пары (разного |
соста |
||||
ва), |
имеющие |
предел прочности |
1100—1400 |
МН/м2 |
(ПО—140 кгс/мм2) при плотности 3,5—4,0 г/см3.
При получении листовых армированных полуфабри катов продольной или продольно-поперечной прокаткой необходимо учитывать изменение предела прочности изза их добавочной долевой деформации (см. главу IV). Естественно, это сказывается и на прочности армиро ванных листов, а именно: если долевая, деформация снижает прочность волокон, с увеличением степени де формации ухудшаются свойства армированного листа. Это положение иллюстрируется данными исследования влияния степени долевой деформации при прокатке за готовок из сплава марки Д20 с волокнами из стали мар
203
ки Х18Н9Т (VB=6°/o) на свойства армированных листов*:
Степень продольной де |
|
|
|
|
|
|||
формации при поперечно- |
|
9,1 |
18,0 |
27,5 |
36,3 |
|||
продольной |
прокатке, % Поперечная |
|||||||
Предел прочности |
прокатка |
|
|
|
|
|||
261 |
242 |
230 |
218 |
218) |
||||
МН/м2 |
|
|||||||
(кгс/мм2) |
|
(26,1) |
(24,2) |
(23,0) |
(21,8) |
(21,8) |
||
Результат |
армирования |
дискретными |
волокнами, |
|||||
как показано в гл. I, должен определяться отношением |
||||||||
их длины |
к |
диаметру. |
Например, |
при армировании |
||||
листов из сплава марки Д20 |
дискретными |
стальными |
||||||
волокнами |
(Ув= 5 % ) |
с |
пределом |
прочности |
||||
~2000 МН/м2 |
(200 кгс/мм2) изменение этого соотноше |
ния вызывает весьма существенные колебания их проч ности**:
Отношение длины мерных воло |
|
30 |
40 |
60 |
75 |
90 |
|
кон к их диаметру....................... 16 |
|||||||
Предел прочности листа, |
|
210 |
270 |
' |
• |
' |
|
МН/м2 |
194 |
|
|
290 |
|
||
кгс/мм2) .......................................(19,4) |
|
(21,0) |
(27,0) |
(29,0) |
|
||
Короткие |
волокна могут |
(особенно |
при |
малых |
|||
объемных долях) даже ослабить материал, играя |
роль |
||||||
дефектов. В |
рассматриваемом |
|
примере |
это |
наблюда |
ется при lB/dB^.Q0. Увеличение отношения длины воло кон к диаметру (при постоянной объемной доле воло кон) повышает прочность армированного изделия до тех пор, пока предел прочности не достигнет установленного значения. В данном случае упрочнение стабилизируется при использовании волокон с /в/^в^ 6 0 .
Перепады в свойствах армированных листов в за висимости от отношения lB/dB тем больше, чем выше прочность волокон и чем значительнее разница в проч ности волокон и матрицы.
Армирование непрерывными стальными |
волокнами |
|
(или мерными волокнами большой длины) |
при |
опти |
мальном режиме прокатки (см. тл. III) позволяет |
зна |
|
чительно повысить прочностные свойства |
алюминия и |
|
* П р е д е л п р о ч н о с т и н е а р м и р о в а н н о г о л и с т а и з с п л а в а |
м а р к и |
|
Д 2 0 2 1 8 М Н / м 2 и л и 2 1 , 8 к г с / м м 2. |
|
(21 кгс/ |
** Предел прочности неармированного листа 210 МН/м2 |
||
/мм2). |
|
|
210