
книги из ГПНТБ / Колпашников, А. И. Армирование цветных металлов и сплавов волокнами
.pdfсхватывания их со стальными волокнами те же, что и для технического алюминия.
Таким образом, для прокатки алюминиевых листов, армированных стальной высокопрочной нержавеющей проволокой, .можно' рекомендовать следующие режимы, обеспечивающие качественное схватывание волокон и матриц:
а) для листов на основе алюминия или листов на основе плакированных алюминием сплавов суммарное обжатие .при прокатке е=40°/о, температура прокатки f='400°C.
16) для листов на основе сплава марки Д20 (без пла кировки) суммарное обжатие при прокатке е=Б54-60%, температура прокатки ^=400°С.
Качество соединения и состояние зон схватывания матрицы и волокон существенно влияют на качество армированного материала, особенно в присутствии дискретных волокон, когда решается вопрос о возмож ности передачи напряжений от матрицы к волокну и от волокна к волокну через матрицу. С точки зрения гра ничных взаимодействий стекловолокно, керамические и карбидные волокна имеют преимущество перед метал лическими волокнами, так как последние более склонны к взаимодействию с матрицей. Надо иметь в виду, что не всякое взаимодействие контактных слоев матрич ного материала и волокон пагубно отражается на свой ствах армированного материала, но все же, в большинст ве случаев оно ослабляет связи (при образовании хрупких интерметаллидов, рекриеталлизованных зон, избирательного местного нарушения граничных слоев волокон;- понижения потенциальной энергии волокон и т. д.). В связи с этим технология производства арми рованных мвтериалов должна строиться с таким расче том, чтобы по возможности предотвратить или замед лить процесс взаимодиффузии матричного материала и волокон, не допустить химического взаимодействия ком понентов. С этой целью выбирают определенное сочета
ние компонентов, |
применяют диффузионные |
барьеры |
|
(в виде промежуточных слоев), определенные |
режимы |
||
деформации заготовок. |
|
|
|
Многие авторы в своих |
исследованиях |
отмечают |
|
вредное влияние |
активных |
легирующих элементов в |
матричных составах на качество соединения. Например, в работах [26, 10 2 ] изучено влияние различных доба
151
вок к медной матрице на свойства армированного мате риала Си—W. Авторы установили различные явления, ослабляющие армированные материалы. Особенно силь ное отрицательное влияние отмечено при легировании меди алюминием и кобальтом. В первом случае проис
ходит диффузионное проникновение |
легирующего |
эле |
||
мента |
матрицы в толщу |
волокон, |
во втором— значи |
|
тельная |
рекристаллизация |
поверхностных слоев' |
воло |
кон. При введении в медь титана и циркония выпадают вторичные фазы в периферийных слоях волокон. Это явление не сопровождается рекристаллизацией. При легировании меди хромом или ниобием на границе матрицы и вольфрамового волокна образуется микрозо на твердого раствора; рекристаллизации в этом случае не наблюдается. Последние из указанных явлений срав нительно слабо вредят свойствам армированного мате
риала (рис. 83). Отмеченное выше ослабление |
армиро |
ванного материала Си — W при легировании |
матрицы |
наблюдается как при комнатной, так и при повышенных температурах.
о . гоо |
ш |
600 |
8оо |
woo |
Температура |
испытаний,°С |
|
Рис. 83. Влияние некоторых легирующих элементов медной мат
рицы |
армированного материала |
на прочность |
вольфрамовых во |
|||||
локон при различных температурах [26]: |
нелегированной |
матри |
||||||
1— волокна, извлеченные из |
материала с |
|||||||
цей- |
2 — волокна, |
извлеченные |
из |
матрицы, |
легированной |
хро |
||
мом; |
3 — волокна, |
извлеченные |
из |
матрицы, |
легированной никелем |
(При армировании металлов и сплавов металличес кими волокнами во многих случаях обеспечивается ка чественное соединение компонентов без их взаимодей ствия. При армировании металлов и сплавов неметал лическими волокнами для обеспечения связей компо
152
центов приходится всемерно способствовать их взаимо действию. Например, при армировании никеля .волок нистыми монокристаллами А120з, чтобы обеспечить взаимодействие волокон с матрицей, в последнюю вво дили различные добавки, из которых наиболее эффек тивными оказались цирконий, хром и особенно титан; добавка 1 % последнею обеспечивает взаимодействие волокон и матрицы. Однако это взаимодействие, поло жительно .влияющее на прочность соединения компонен тов, одновременно существенно ослабляет . волокна
(рис. 84).
|
к о м п о н ен т о в |
|
Вы т яж ка при |
прокат ы |
|||
Рис. 84. |
Качественная |
диаграмма |
из |
|
|
||
менения |
прочности |
соединения |
ком |
|
|
||
понентов |
армированного |
материала |
Рис. 85. Изменение предела проч |
||||
Ni — АЬОз и прочности |
в |
волокнистых |
|||||
монокристаллов А120 3 |
|
зависимости |
ности проволоки из |
стали марки |
от интенсивности |
взаимодействия |
Х18Н9Т |
в результате продольной |
|||
компонентов |
[2]: |
|
моно |
прокатки |
по различным |
режи |
I — прочность |
волокнистых |
мам в модельных образцах. |
Тем |
|||
кристаллов А120 3; |
2 — прочность |
сое |
пература |
прокатки: 1— 350°С; 2 — |
||
динения Ni — А12Оз |
|
|
400°С; 3 — 450°С |
|
Учитывая вышеизложенное, следует отметить, что ослабление неметаллических армирующих волокон (в связи с их взаимодействием с матричными материа лами для обеспечения работоспособности композиций) значительно уменьшает их преимущество ;в прочности перед металлическими волокнами; кроме того, точное регулирование реакций .взаимодействия .в реальных ус ловиях производства затруднительно, а это означает, что очень сложно предсказывать свойства материалов, ар мированных неметаллическими волокнами. Учитывая также малую пластичность этих волокон, большую чув ствительность к механическим повреждениям .и высо кую стоимость многих из них, можно отметить, что, повидимому, при производстве армированных полуфабри
153
катов совместной пластической деформацией целесооб разнее ориентироваться на металлические составы.
Помимо граничных явлений, важную роль в выборе оптимального режима прокатки армированных листов играет влияние деформации сборной заготовки на сос тояние и свойства волокон. При изучении поведения волокон проволоки из нержавеющих сталей в армируе мых алюминиевых листах авторы определяли допусти мое обжатие при прокатке вдоль волокон ;на обычных армированных листовых образцах и изменение свойств в результате прокатки модельных образцов.
Модельные образцы составляли из чередующихся слоев матричных материалов и волокон, но схватывание при прокатке предупреждалось введением разделитель ных веществ в контактные зоны компонентов. После прокатки модельных образцов при различных темпера турах с разными степенями деформации волокна извле кали и (если они сохраняли сплошность) подвергали ис пытаниям на разрыв. Результаты этих испытаний приве дены на рис. 85.
На рис. 86 показаны изломы армированных листов алюминиевый сплав— нержавеющая проволока, прока танных с постоянным суммарным обжатием, но с раз личными обжатиями при продольной прокатке*. 1По итогам этих экспериментальных исследований можно рекомендовать получать алюминиевые листы, армиро ванные нержавеющей стальной проволокой, с суммар ными обжатиями, равными или выше тех, которые опре делены как степени деформации схватывания, но вели чина продольной деформации не должна превышать е= 7-^23% (р,= 1,08-4-1,3) [92].
При поперечной прокатке армированных полос наб людается тенденция к некоторому искривлению волокон, причем это искривление обращено выпуклостью в сто рону направления прокатки (в сторону выхода полосы из клети стана). Это искривление усугубляется при прокатке с высшими обжатиями по проходам и с увели чением температуры прокатки. Нами установлено, что предел прочности армированных листов, в которых ис кривление волокон характеризуется максимальным уг лом 30°, следует рассчитывать по правилу смеси с вве дением коэффициента р [(см. уравнение (34)], равного
* В данном случае продольной называется прокатка в направ лении, совпадающем с продольным расположением волокон.
154
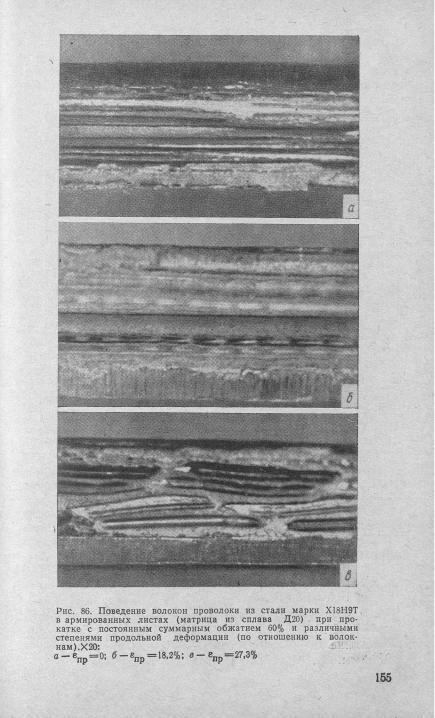
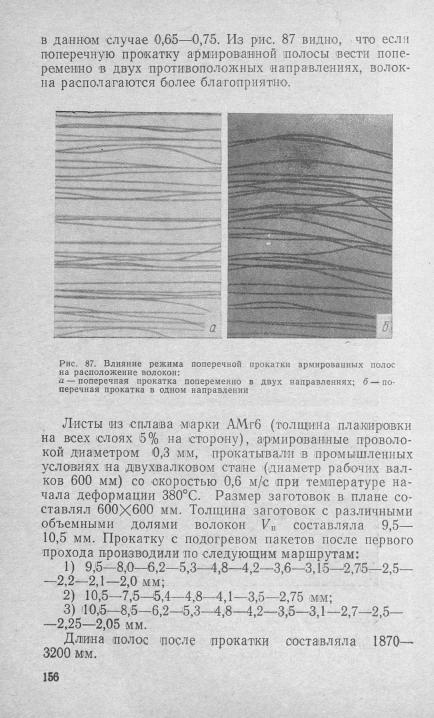
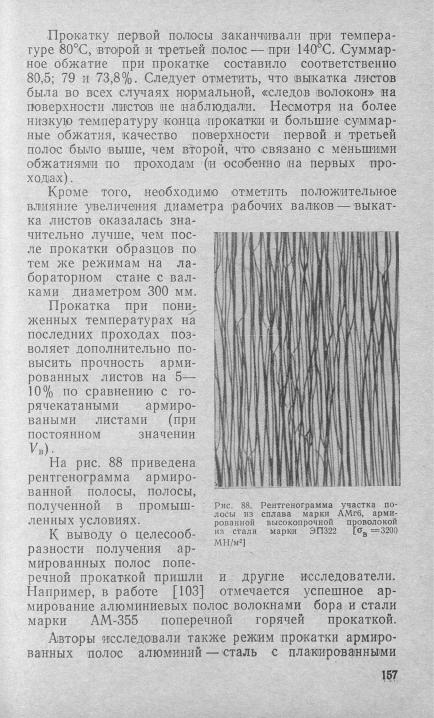
боковыми кромками. Плакирование боковых кромок листовых полуфабрикатов широко применяется в прак тике обработки многих материалов. Применительно к прокатке широких полос из алюминиевых сплавов эта проблема решена* в 50-х годах.
Если плакирование основных граней повышает кор розионную стойкость и до некоторой степени технологи ческую пластичность полосы, то плакирование' боковых кромок преследует в основном технологические цели — сокращение потерь металла полос за счет ликвидации растрескивания кромок вследствие действия растягиваю щих напряжений.
Боковые кромки стандартных полос из прочных алю миниевых сплавов плакируют на линии стана горячей прокатки с помощью эджерных валков. Плакирование боковых кромок армированных полос (получаемых про каткой в направлении поперек расположения волокон) преследует следующие цели:
11 уменьшение растрескивания боковых кромок;
2) снижение опасности коррозионного повреждения кромок (при выходе на боковые кромки волокон кромка армированной полосы имеет «гетерогенное» строение);
3) обеспечение возможности сварки армированных листов по кромкам.
(Плакировать боковые кромки широких армирован ных полос можно также, как и обычные широкие по лосы**. Кромки узких полос плакируют по схеме, представленной на рис. 89.
12 5 |
Рис. |
89. |
Схема |
плакирования |
бо |
||||
ковых |
кромок |
узких |
армирован |
||||||
|
ных полос: |
брус |
из |
матричного |
|||||
|
1 — боковой |
||||||||
|
сплава на основе алюминия; |
2 — |
|||||||
|
заклепки; |
3 — прокладки из |
алю |
||||||
|
миния; |
4 — верхняя |
обкладка |
из |
|||||
|
матричного |
материала; |
5 — ниж |
||||||
5 S |
няя обкладка |
из |
матричного |
ма |
|||||
териала; |
6 — армированная часть |
||||||||
|
заготовки |
|
|
|
|
|
|
|
Применение прокладок из алюминия толщиной 1,5—
2 мм обеспечивает хорошую приварку |
боковых |
кромок |
при прокатке с суммарным обжатием 60%. |
|
|
* А. И. К о л п а ш н и к о в . Исследование |
процесса |
плакирова |
ния сплавов типа дюралюмина и САПа. Автореф. докт. |
дис. М , |
|
МАТИ, 1963. |
|
|
** Эти исследования проведены авторами совместно с В. С. Со
коловым.
158
Авторы исследовали также влияние отношения ljdB
дискретных волокон из нержавеющей стали на их спо |
|
собность к упрочнению алюминиевых спла-вов. Образцы |
|
из сплава марки Д20 |
армировали (Ув= |5%) проволо |
кой диаметром 0,6 мм |
из стали марки Х18Н9Т, прока |
тывали при 400°С с суммарным обж-атием есум=50%, затем испытывали на растяжение. Результаты испыта ний приведены на рис. 90. По итогам испытаний можно
сделать |
вывод, что упрочнение |
обеспечивается |
при |
/ / g?b> 6 0 . |
При нарушении этого |
условия понижаются |
|
механические свойства, особенно |
при l/dB<C30, |
когда |
прочность армированного материала уступает прочности матрицы.
Рис. 90. Влияние |
отношения |
Рис. 91. Влияние отноше |
|||
ния алитирующего |
слоя к |
||||
длины дискретных |
волокон к |
диаметру |
волокна |
на |
пре |
их диаметру на прочность ар |
дельную |
объемную |
долю |
||
мированного материала Д20 — |
волокон в |
армированных |
|||
Х1879Т (VB=5%) |
|
полосах |
|
|
|
Три технологические схемы производства армирован ных листов с алюминиевой матрицей изложены в рабо те [404]. В первой из них волокно (борволокно, стекло волокно, пол-икристаллические волокнаSi02, стальную проволоку) протягивают через ванну с матричным ра сплавом, после чего наматывают в несколько слоев на центральную тонкую пластину. Между -слоями алитиро ванных волокон прокладывают листы алюминиевой фольги. Затем скрепленный пакет -нагревают до темпе ратуры начала деформации матричного алюминиевого Ьплава -и прокатывают в направлении, поперечном по отношению к направлению волокон в заготовке (паке те). На рис. 91 показано влияние отношения толщины алитированного слоя к диаметру волокон dB на пре дельную объемную долю волокон VB в армированных листах, получаемых по этой технологии.
159
iB другой технологической схеме с ‘некоторым смеще нием наматывали армирующие волокна бора без пок рытия и проволоку из алюминиевого сплава так, что в каждом слое они чередовались. Между слоями волокон прокладывали алюминиевую фольгу для предотвраще ния непосредственного контакта волокон различных слоев. После ‘получения заготовок производили нагрев и вакуумное спрессовывание при температуре 480°С, пос ле чего заготовки прокатывали на необходимую толщи ну. По изложенной схеме получали армированные лис ты, содержащие 25% (объемн.) волокон.
Третья схема производства армированных листов с алюминиевой матрицей заключается в намотке прово локи из мартенситостареющей стали на относительно толстую среднюю пластину (а затем последовательно на -полученную намоткой часть заготовки устанавливают обкладки и вновь производят намотку и т. д.), нагреве и прокатке пакета. Тот же метод успешно использован для армирования алюминия бериллиевой проволокой и волокнами бора. Эта схема отличается простотой, малы ми производственными затратами, большим габари тами получаемых листов, -отсутствием реакций между волокнами и матрицей. Очень высокой производитель ностью отличается процесс армирования полос сеткой. Однако следует о-тметить, что яри получении таких лис тов прокаткой заметное упрочнение ‘может достигаться лйшь в том случае, ко-гда степень деформации при про катке мала и не приводит к разрушению сетки. Прове
денные эксперименты показали, что армирование |
алю |
||
миниевых листов стальной |
сеткой |
позволяет повышать |
|
их прочность ,и жесткость*. |
К этим же выводам пришли |
||
и другие исследователи**. |
|
осуществить |
непре |
Армирование сеткой позволяет |
|||
рывную -прокатку*** (рис. |
92). С трех разматывателей |
поступают компоненты армированной полосы: с первого
и третьего — алюминиевые |
полосы толщиной |
0,625 |
мм, |
со второго — сетка из стальной проволоки |
диаметром |
||
0,625 мм. Прокатку ведут |
при температуре, |
обычно |
ис- |
*Эксперименты по армированию алюминиевых листов стальны ми сетками авторы провели совместно с И. И. Ивановым.
**Б о т в и н а Л. Р. Исследование металлических армирован ных систем при различных видах нагружения. Автореф. канд. дис.
М. ИМЕТ АН СССР, М„ 1969.
*** Пат. (США), кл. 29—497.5, № 3406446, 1969.
160