
конспект Термообработка
.pdfКОНСПЕКТ ЛЕКЦИЙ ПО ДИСЦИПЛИНЕ « ТЕРМООБРАБОТКА»
1.КЛАССИФИКАЦИЯ ПРОЦЕССОВ ТЕРМИЧЕСКОЙ ОБРАБОТКИ МЕТАЛЛОВ 1.1 Понятие термической обработки металлов 1.2 Требования, предъявляемые к металлам и сплавам
1.3 Основные этапы в развитии термообработки. Вклад русских и зарубежных ученых в развитие термообработки как науки 1.4 Классификация видов термической обработки
2.СОСТАВ, КЛАССИФИКАЦИЯ И МАРКИРОВКА МЕТАЛЛОВ, СТАЛЕЙ И СПЛАВОВ
2.1Классификация сталей
2.2Маркировка сталей
2.3Классификация примесей в сталях
3.ФАЗОВЫЕ ПРЕВРАЩЕНИЯ В СТАЛИ ПРИ НАГРЕВЕ
3.1Фазовые и структурные превращения при нагреве выше критических точек сталей с исходной ферритно-карбидной структурой.
3.2Фазовая перекристаллизация. Рост аустенитного зерна при нагреве
3.3Структурная наследственность
4.ПРЕВРАЩЕНИЯ ПЕРЕОХЛАЖДЕНОГО АУСТЕНИТА В СТАЛЯХ
4.1Перлитное превращение.
4.1.1 Кинетика распада переохлажденного аустенита по I ступени
4.1.2 Основные типы изотермических диаграмм распада переохлажденного аустенита в углеродистых сталях
4.1.3Основные структурные формы продуктов распада переохлажденного аустенита при перлитном превращении 4.1.4Факторы, влияющие на устойчивость переохлажденного аустенита при перлитном превращении 4. 1.5 Перлитное превращение в легированных сталях
4.2Мартенситное превращение в сталях
4.2.1Механизм и кристаллография мартенситного превращения
4.2.2Микроструктура мартенсита
4.2.3Кинетика мартенситного превращения
4.2.4Влияние пластической деформации на мартенситное превращение
4.2.5Факторы, влияющие на температуру Мн
4.2.6Свойства сталей с мартенситной структурой
4.3Бейнитное превращение.
4.3.1Механизм бейнитного превращения
4.3.2Кинетика бейнитного превращения
5.ПРЕВРАЩЕНИЯ АУСТЕНИТА ПРИ НЕПРЕРЫВНОМ ОХЛАЖДЕНИИ
5.1 Распад переохлажденного аустенита при непрерывном охлаждении. Углеродистая сталь 5.2 Распад переохлажденного аустенита при непрерывном охлаждении.
Доэвтектоидные углеродистые стали 5.3 Распад переохлажденного аустенита при непрерывном охлаждении. Заэвтектоидные углеродистые стали
5.4 Термокинетические диаграммы распада переохлажденного аустенита.
6. ОТЖИГИ I-ГО И II-ГО РОДА
1
6.1Гомогенизационный отжиг
6.2.Нагрев для снятия остаточных напряжений
6.3.Рекристаллизационный отжиг
6.4.Сфероидизирующий отжиг инструментальных сталей
6.5Полный отжиг конструкционных сталей
6.6Неполный отжиг конструкционных сталей
6.7Нормализация сталей
7.ЗАКАЛКА БЕЗ ПОЛИМОРФНОГО ПРЕВРАЩЕНИЯ
8.ЗАКАЛКА С ПОЛИМОРФНЫМ ПРЕВРАЩЕНИЕМ
8.1.Особенности закалки сталей 8.2 Способы закалки
8.3.Закаливаемость и прокаливаемость
9.ОТПУСК ЗАКАЛЕННОЙ СТАЛИ
9.1 Превращения при отпуске закаленной углеродистой стали
9.2 Влияние легирующих элементов на отпуск стали.
9.3 Отпускная хрупкость стали
2
1. КЛАССИФИКАЦИЯ ПРОЦЕССОВ ТЕРМИЧЕСКОЙ ОБРАБОТКИ МЕТАЛЛОВ
1.1 Понятие термической обработки металлов
Термическая обработка – процессы теплового воздействия на металлы и сплавы с целью изменения их структуры и свойств в заданном направлении.
Теория термической обработки - учение об изменениях строения и свойств металлов и сплавов при тепловом воздействии, не исчезающих после его прекращения.
Ни один технологический процесс не позволяет так полно и разнообразно изменять структуру металла, как термическая обработка.
Основные параметры режима термической обработки:
Скорость нагрева
Максимальная температура нагрева
Время выдержки при максимальной температуре
Скорость охлаждения
Любой режим термической обработки может быть представлен графически в координатах температура-время.
Тепловое воздействие может сочетаться с химическим, деформационным и т.д. и термическая обработка обычно делится на:
Собственно термическую обработку
Химикотермическую обработку (ХТО)
Термомеханическую обработку (ТМО)
1.2Требования, предъявляемые к металлам и сплавам
Взависимости от области применения металлических материалов к ним предъявляются чрезвычайно разнообразные требования.
Вобщем случае можно выделить три группы требований к свойствам материала: требования к свойствам, вытекающим из условий применения материала; требования к свойствам обрабатываемости; требования к однородности свойств изделия. В соответствии с этим термическая обработка может быть предварительной (для улучшения обрабатываемости резанием, деформированием, для повышения технологичности, для повышения свойств готовых изделий) и окончательной (для создания требуемых свойств готовых изделий).
1.3Основные этапы в развитии термообработки. Вклад русских и зарубежных ученых в
развитие термообработки как науки
По данным археологии, термическая обработка металлов и сплавов используется человеком с древнейших времен. Рекристаллизационный отжиг для снятия наклепа при изготовлении режущих и колющих предметов из меди начал применяться уже в конце V тысячелетия до н.э., из бронзы – во II тысячелетии до н.э. (в бронзовом веке).
Закалка железа появилась несколько позже во II тысячелетии до н.э., ее сначала использовали совместно с цементацией, так как железо, получавшееся в те времена сыродутным методом прямо из железной руды, содержало очень мало углерода. Упрочняющую термообработку стали начали использовать позднее – в I тысячелетии до н.э.
В средние века уже широко использовались многие виды термообработки: различные закалки, отпуск, отжиги, химико-термическая обработка. На раннем этапе развития термической обработки люди, не понимая сути превращений, использовали только выработанные веками практические рецепты.
3
Этапы развития термической обработки как науки: 1. Середина 19 в.
Павел Петрович Аносов (1799-1851гг.) впервые использовал оптический микроскоп для металлографических исследований. Он же впервые провел систематические исследования по влиянию легирующих элементов на структуру и свойства сталей, показал, что цементация возможна не только в твердой но и в газообразной среде, теоретически обосновал возможность обработки холодом для повышения твердости при закалке.
Массовое производство артиллерийских орудий из стали позволило обнаружить закономерности воздействия температуры на свойства металла. Дмитрий Константинович Чернов (1839-1921 гг.), изучая причины разрушения стволов пушек открыл 2 критические точки: точку а, и b.
Точка а – это температура при нагреве ниже которой сталь не может закалиться. Ас1-температура эвтектоидного превращения.
Точка b – температура, при нагреве выше которой перегретая сталь становится мелкозернистой. Температура начала рекристаллизации аустенита.
Д.К. Чернов сформулировал условия закалки, ввел понятия:
закаливаемость
прокаливаемость
верхняя и нижняя скорости закалки
2. Изучение и построение диаграмм состояния 1886 г. Ф.Осмонд впервые применил термопару Ле-Шателье для определения
критических точек при термическом анализе. Он предложил названия: аустенит, цементит, феррит, ледебурит, карбиды, мартенсит, перлит.
Первые серьезные исследования термообработки сплавов цветных металлов были выполнены в начале XX века, когда А.А. Байков на примере сплавов меди с сурьмой показал, что закаливать можно не только сталь, а немецкий инженер А. Вильм открыл старение после закалки изобретенного им дуралюмина – сплава алюминия с медью и магнием.
3. Изучение кинетики фазовых превращений 1913-1918 гг. – работы Портовена, Бейна, Гарвина, Маслова. Ими были
предложены типы термокинетических диаграмм, которые просуществовали до 1930-х.
В1930 С.С. Штейнберг предложил тип диаграмм, который применяется до сих пор
–это тип изотермических и термокинетических диаграмм распада переохлажденного аустенита.
4. Настоящее время Усовершенствование техники исследований.
1.4 Классификация видов термической обработки
Вид термической обработки определяется не изменением основных параметров, а тем типом фазовых и структурных превращений, которые при этом происходят.
Термическая обработка включает в себя:
1.Отжиг I рода
2.Отжиг II рода
3.Закалку без полиморфного превращения (истинную закалку)
4.Закалку с полиморфным превращением
5.Отпуск
6.Старение
Термическая обработка может быть и побочным явлением (например, при литье)
Внастоящее время общепринятой является классификация А.А. Бочвара,
учитывающая тип фазовых и структурных изменений в металле (рис 1.1)
4
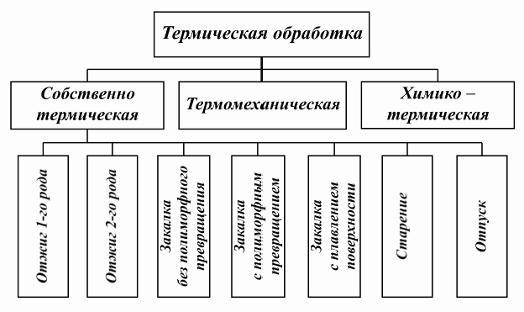
Производственные названия некоторых видов термической обработки складывались исторически и не имеют отношения к характеру структурных и фазовых превращений, протекающих в металле, а описывают лишь внешние признаки. Например, нагрев материала с переходом за критическую точку, выдержка и охлаждение на воздухе обычно называется нормализацией. Такая обработка приводит в углеродистой стали к протеканию процессов фазовой перекристаллизации, которые относятся к отжигу второго рода, в высоколегированных сталях к образованию мартенсита, т.е. к закалке с полиморфным превращением, а в некоторых цветных сплавах происходит закалка без полиморфного превращения.
Рис. 1.1. Схема классификации основных видов термической обработки металлов и сплавов.
2.СОСТАВ, КЛАССИФИКАЦИЯ И МАРКИРОВКА МЕТАЛЛОВ, СТАЛЕЙ И СПЛАВОВ
2.1 Классификация и маркировка сталей
Стали классифицируются по множеству признаков.
1.По химическому составу:
1)углеродистые:
углерод, % низкоуглеродистые………….до 0,25 среднеуглеродистые………..0,25…0,65 высокоуглеродистые……….свыше 0,65
2) легированные:
суммарное содержание легирующий элементов, %
низколегированные………….ниже 2,5 среднелегированные…………2,5…10
высоколегированные……….свыше 10
Если содержание Fe меньше 45 %, то это сплав, если больше – сталь. Основа сплава – элемент самого высокого содержания.
По назначению:
1) конструкционные – применяются для изготовления деталей машин и механизмов;
5
2)инструментальные – применяются для изготовления различных инструментов;
3)с особыми свойствами: электротехнические, с особыми магнитными свойствами
и др.
По структуре в равновесном состоянии:
1)доэвтектоидные;
2)эвтектоидные;
3)заэвтектоидные.
По основной структуре после нагрева до 900 ºC с последующим охлаждением на воздухе: перлитные, бейнитные, мартенситные, ферритные, аустенитные.
Также могут быть смешанные классы: феррито-перлитный и т.д. (при наличии не менее 10 % перлита).
По качеству. Количественным показателем качества является содержания вредных примесей: серы и фосфора, % (не более):
обыкновенного качества………………….S≤0,05, P≤0,04 качественные стали……………………….S, P ≤0,035 высококачественные……………………...S, P ≤0,025 особовысокачественные………………….S≤0,015, P≤0,025
По способу выплавки:
1)в мартеновских печах;
2)в кислородных конверторах;
3)в электрических печах: электродуговых, индукционных и др.
2.2Маркировка сталей
В России принято буквенно-цифровое обозначение сталей.
Углеродистые стали обыкновенного качества. Стали содержат повышенное количество серы и фосфора.
Маркируются Ст.2кп, БСт.3кп, ВСт.3пс, ВСт.4сп.
Ст – индекс данной группы стали. Цифры от 0 до 6 – это условный номер марки стали. С увеличением номера марки возрастает прочность и снижается пластичность стали. По гарантиям при поставке существует три группы сталей – А, Б и В. Для сталей группы А при поставке гарантируются механические свойства, в обозначении индекс группы А не указывается. Для сталей группы Б гарантируется химический состав. Для сталей группы В при поставке гарантируются и механические свойства, и химический состав.
Индексы кп, пс, сп указывают степень раскисленности стали: кп – кипящая; пс – полуспокойная; сп – спокойная.
Качественные углеродистые стали. Качественные стали поставляют с гарантированными механическими свойствами и химическим составом (группа В). Степень раскисленности в основном спокойная.
Конструкционные качественные углеродистые стали. Маркируются двухзначным числом, указывающим среднее содержание углерода в сотых долях процента. Указывается степень раскисленности, если она отличается от спокойной.
Сталь 08, сталь 10 пс, сталь 45.
Содержание углерода соответственно 0,08; 0,10; 0,45 %.
Инструментальные качественные углеродистые стали маркируются буквой У
(углеродистая инструментальная сталь) и числом, указывающим содержание углерода в десятых долях процента.
Сталь У8, сталь У13. Содержание углерода соответственно 0,8 и 1,3 %.
Инструментальные высококачественные углеродистые стали. Маркируются аналогично качественным инструментальным углеродистым сталям, только в конце марки ставят букву А, для обозначения высокого качества стали.
Сталь У10А.
6
Легированные стали. Обозначение буквенно-цифровое. Легирующие элементы имеют условные обозначения. Обозначаются буквами русского алфавита.
Обозначения легирующих элементов:
А – азот (указывается в середине марки),
Б – ниобий, |
|
В – вольфрам, |
Т – титан, |
Г – марганец, |
Ф – ванадий, |
Д – медь, |
Х – хром, |
Е – селен, |
Ц – цирконий, |
К – кобальт, |
Ю – алюминий, |
М – молибден, |
Ч – редкоземельные |
Н – никель, |
|
П – фосфор, Р – бор, С – кремний,
Легированные конструкционные стали. В начале марки указывается двухзначное число, показывающее содержание углерода в сотых долях процента. Далее перечисляются легирующие элементы. Число, следующее за условным обозначением элемента, показывает его содержание в процентах. Если число не стоит, то содержание элемента не превышает 1,5 %.
Сталь 30Х2МА.
В указанной марке стали содержится около 0,30 % углерода, 2 % хрома, менее 1 % молибдена.
Для обозначения высококачественных легированных сталей в конце марки указывается символ А.
Легированные инструментальные стали. В начале марки указывается однозначное число, показывающее содержание углерода в десятых долях процента. При содержании углерода более 1 % число не указывается.
Далее перечисляются легирующие элементы с указанием их содержания. Некоторые стали имеют нестандартные обозначения.
Сталь 9ХС, сталь ХВГ.
Быстрорежущие инструментальные стали. Р – индекс данной группы сталей (от rapid – скорость), далее число, указывающее содержание основного легирующего элемента – вольфрама. Содержание углерода более 1 %. Во всех быстрорежущих сталях содержится около 4 % хрома, поэтому он не указывается. Если стали содержат легирующие элементы, то их содержание указывается после обозначения соответствующего элемента.
Сталь Р5М3.
В указанной стали содержание вольфрама – 5 %, молибдена – 3 %. Шарикоподшипниковые стали. Ш – индекс данной группы сталей. Х – указывает
на наличие в стали хрома. Последующее число показывает содержание хрома в десятых долях процента. Содержание углерода более 1 %.
Сталь ШХ6, сталь ШХ15ГС.
В указанных сталях, соответственно, 0,6 и 1,5 % хрома.
Буква А в конце марки обозначает высококачественную сталь (30ХГСА), в середине марки – азот, в конце марки – сталь автоматная (А35Г2).
Высоколегированные стали сложного состава иногда обозначают по порядковому номеру разработки и освоения на заводе (ЭИ, ЭП – «Электросталь»).
2.3 Классификация примесей в сталях
Примеси делятся на постоянные, случайные скрытые и специальные
7
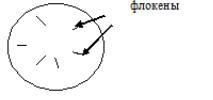
Постоянные: P, S, Mn, Si
Mn вводится для раскисленния
FeO+Mn=Fe+MnO
Если Mn <0,8%, то это примесь если Mn >0,8%, то это специальная добавка. Si вводится также для раскисленния
2FeO+Si=2Fe+ Si2 O
Si полностью практически растворяется в -Fe и структурно не обнаруживается. Если Si < 0,04 %, то это примесь.
Р попадает из топливных газов. Воздействие Р зависит от способа производства
стали. 0,12%Р-бессемеровская сталь
При мартеновском производстве содержание Р может быть понижено до 0,02%. Р отрицательно влияет на сопротивление хрупкому разрушению Повышает опасность обратимой отпускной хрупкости В автоматных сталях содержание Р может быть повышенным.
S практически нерастворима в Fe и любое ее количество образует эвтектику. Образуется сульфид железа, а при повышенном содержании серы наблюдается явление красноломкости.
Скрытые примеси
О, N и Н
О2 находится в виде окислов, которые также находятся в виде газа в газовых пузырях.
N может присутствовать в стали в виде нитридов и карбонитридов.
При повышенном содержании Н в стали возможно образование флокенов. Это чрезвычайно опасный дефект. Это микротрещины, которые располагаются на 1/3-2/3 радиуса обычно.
Рис 2.1 Флокены в сталях Крайняя мера-проведение термической противофлокеновой обработки, которая
заключается в длительной выдержке при субкритических температурах. Длительность выдержки может достигать до 100 часов
Случайные примеси.
Cu, Ni, Cr, Sn
Специально в сталь не вводятся, но попадают в металл с шихтой и ломом.
Специальные добавки
Легирующие элементы По отношению к углероду легирующие элементы делятся:
1) некарбидообразующие Cu, Ni, Al, Pb
Эти элементы находятся в феррите или аустените. При соответствующих условиях могут образовывать нитриды карбонитриды интерметаллиды
2)карбидообразующие Fe, Cr, Mo, V, W, Nb, Ti, Zr.
Тип образующихся карбидов и их свойства зависят от недостроенности атомов нижнего уровня. Карбидная фаза характеризуется степенью (или температурой) диссоциации (температурой растворения).
Mn (Fe, Mn)3C
8

Cr, (Fe, Cr)3C, Cr7C3, Cr23C6
Мо, W Mе2C, Mе23C6, Mе3C, Mе3C V, Ti, Nb, Zr MeC
По влиянию на критические точки делятся:
расширяющие -область
Mn, Ni, Со
Путем введения этих легирующих элементов разработаны стали аустенитного класса, которые обладают хорошей износостойкостью, жаропрочностью и коррозионной стойкостью.
Рис. 2.2. Диаграмма состояния железо–легирующий элемент с открытой -областью Существует предельная концентрация легирующих элементов, сплав существует в
однофазном аустенитном состоянии в широком диапазоне температур. Предельные концентрации:
Mn –12%, Ni-25%, Со-85%.
В сплавах с концентрацией добавки, равной или превышающей концентрацию, соответствующую точке b, ГЦК решетка устойчива при 20…25 °С; такие сплавы называют аустенитными сталями. Таким образом, аустенитом называют не только твердый раствор углерода в Fе , но и любые твердые растворы на основе Fе .
Сталь Гадфильда (Г13) 1.2%С, 13%Mn
расширяющие -область.
Si, Mo, Ti, W, V, Cr
Рис.2.3. Диаграмма состояния железо – л.э. с замкнутой γ-областью; а – открытая -область, б – закрытая -область
9

Существует некоторая предельная концентрация К л.э, при которой сплав находится в однофазном ферритном состоянии в широком диапазоне температур.
Cr максимальная к 13% Mo- 2,5%
Si – 1,75%
V – 1,77%
Ti – 1,77%
W – 8,4%
Х13ферритная нержавеющая сталь Под влиянием л.э. т.Е и С могут настолько интенсивно смещаться в область
меньших концентраций углерода, что в структуре стали при %С 2,14 появится ледебуритная эвтектика. Такие стали называют ледебуритными.
Рис. 2.4 Влияние л.э. на протяженность замкнутой γ-области
Влияние легирующих элементов на фазовые превращения сталей. Легирующие элементы, понижающие температуру А3 в безуглеродистых сплавах (Ni и Mn), смещают линии PSK, GS и SE диаграммы Fe – Fе3С в сторону более низких температур.
Легирующие элементы, повышающие температуру A3 в безуглеродистых сплавах, оказывают обратное влияние — они смещают линии PSK, GS и SE в сторону более высоких температур. Влияние некоторых легирующих элементов на положение эвтектоидной линии при нагреве показано на рис. 2.5.
Рис. 2.5. Влияние л.э. на температуру Аc1
10