
конспект Термообработка
.pdf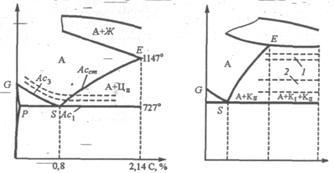
В зависимости от температуры нагрева закалку называют неполной. При полной закалке сталь переводят в однофазное аустенитное состояние, т.е. нагревают выше критических температур Ас3 или Асст, при неполной — до межкритических температур — между Ас1 и Ас3 (Асст) (рис. 8.1, а).
Рис 8.1 Оптимальные температуры нагрева под закалку доэвтектоидных и заэвтектоидных (а), а также высоколегированных ледебуритных сталей (б) Доэвтектоидные стали, как правило, подвергают полной закалке, при этом
оптимальной температурой нагрева является температура Асз + (30 . . .50°С). Такая температура обеспечивает получение при нагреве мелкозернистого аустенита и соответственно после охлаждения — мелкокристаллического мартенсита. Недогрев до температуры Ас3 приводит к сохранению в структуре кристаллов доэвтектоидного феррита, что при некотором уменьшении прочности обеспечивает повышенную пластичность закаленной стали.
Заэвтектоидные стадии подвергают неполной закалке. Оптимальная температура нагрева углеродистых и низколегированных сталей при этомтемпература Ас1 + (30.. 50 °С).
После закалки заэвтектоидная сталь приобретает структуру, состоящую из мартенсита и цементита. Кристаллы цементита тверже кристаллов мартенсита, поэтому при неполной закалке заэвтектоидные стали имеют более высокую твердость, чем при полной. Так как сталь предварительно подвергалась сфероидизирующему отжигу, избыточные карбиды округлой формы не вызывают снижения вязкости. Высоколегированные инструментальные стали ледебуритного класса (рис. 8.1 б) для повышения теплостойкости нагревают при закалке до очень высоких температур (область 1), близких к эвтектической. При этом происходит распад всех вторичных карбидов, аустенит обогащается не только углеродом, но и легирующими элементами, содержащимися в карбидах. В результате получается высоколегированный, а следовательно, и теплостойкий мартенсит.
Если высоколегированные инструментальные стали используют не как теплостойкие, а только как износостойкие, температуру закалки понижают (см. рис.8.1, область 2), сохраняя некоторое количество вторичных карбидов нерастворенными. При такой закалке температура нагрева достаточно высокая (900 - 1000 °С). Это связано с влиянием легирующих элементов на критические температуры стали (см. гл. 4) и с малой скоростью диффузии легирующих элементов в твердом растворе.
Для получения мартенситной структуры необходимо переохладить аустенит до температуры мартенситного превращения; следовательно, скорость охлаждения должна превышать критическую скорость Vкр .
Для углеродистых сталей Vкр составляет 400 — 1400 °С/с. Для того чтобы переохладить аустенит таких сталей до температуры мартенситного превращения, необходимо прибегать к очень резкому охлаждению, которое достигается погружением
51
закаливаемых деталей в холодную воду либо воду с добавками соли или едкого натра
(табл. 8.1).
|
|
|
|
Таблица 6.2. |
Относительная охлаждающая способность закалочных сред |
||||
|
|
|
|
|
Охлаждающая |
|
Температура, С |
Относительная |
|
среда |
Охлаждающей |
|
Пузырькового кипения |
интенсивность охлаждения в |
|
среды |
|
|
середине интервала |
|
|
|
|
пузырькового кипения |
Вода |
20 |
|
400-100 |
1 |
|
40 |
|
350-100 |
0,7 |
|
80 |
|
250-100 |
0,2 |
10%-й |
|
|
|
|
раствор в воде: |
20 |
|
650-100 |
3 |
NaCl |
20 |
|
650-100 |
2,5 |
NaOH |
|
|
|
|
Масло |
20-200 |
|
500-250 |
0,3 |
минеральное |
|
|
|
|
При охлаждении на поверхности стальной детали не должна образовываться паровая пленка, препятствующая теплообмену с закалочной средой.
Лучшей является стадия пузырькового кипения охлаждающей жидкости. Чем больше температурный интервал этой стадии, тем интенсивнее охлаждает закалочная среда.
Лучше пользоваться добавками едкого натра, так как щелочная среда не вызывает последующей коррозии стальных деталей. Многие легированные стали приобретают мартенситную структуру при охлаждении в холодных или подогретых маслах, а высоколегированные стали закаливаются на мартенсит даже при охлаждении на воздухе.
Охлаждение при закалке наиболее просто осуществляется погружением закаливаемой детали в жидкую среду (воду или масло) имеющую температуру 20 - 25 °С. Однако в некоторых случаях для уменьшения деформации (коробления) деталей или для предотвращения образования трещин условия охлаждения усложняют.
Коробление и растрескивание вызываются значительными остаточными напряжениями, возникающими при закалке. Основной источник напряжений — увеличение объема при превращении аустенита в мартенсит. Модуль упругости в температурном интервале мартенситного превращения достаточно велик, поэтому возникающие из-за объемных изменений напряжения релаксируют с малой скоростью. Значительные макроскопические напряжения возникают из-за неодновременности превращения по сечению а также в закаливаемых деталях сложной формы. Остаточные напряжения уменьшаются при условии одновременного превращения по сечению и понижения скорости охлаждения в интервале температур Мн — Мк. В практике термической обработки сталей широкое использование нашли следующие способы охлаждения, позволяющие значительно уменьшить величину остаточных напряжений: закалка в двух средах и ступенчатая закалка.
8.2Способы закалки
Взависимости от состава стали, формы и размеров детали и требуемых в термически обработанной детали свойств выбирают оптимальный способ закалки, наиболее просто осуществимый и одновременно обеспечивающий нужные свойства.
Чем сложнее форма термически обрабатываемой детали, тем тщательнее следует выбирать условия охлаждения, потому что чем сложнее деталь, тем больше различие в сечениях детали, тем бớльшие внутренние напряжения возникают в ней при охлаждении.
52

Чем больше углерода содержит сталь, тем больше объѐмные изменения при превращении, тем при более низкой температуре происходит превращение аустенита в мартенсит, тем больше опасность возникновения деформаций, трещин, напряжений и других закалочных пороков, тем тщательнее следует выбирать условия закалочного охлаждения для такой стали.
К основным способам закалки относятся:
1. Закалка в одном охладителе (рис. 8.2, кривая 1) – наиболее простой способ. Нагретую до определенных температур деталь погружают в закалочную жидкость, где она остается до полного охлаждения. Применяют этот способ при закалке несложных деталей из углеродистых и легированных сталей. При этом для углеродистых сталей диаметром более 2-5 мм закалочной средой служит вода, а для меньших размеров и для многих легированных сталей – масло.
Для уменьшения внутренних напряжений деталь иногда не сразу погружают в закалочную жидкость, а некоторое время охлаждают на воздухе, «подстуживают». Такой способ закалки называется закалкой с подстуживанием (рис. 8.2, кривая 5).
Рисунок 8.2 - Схема режимов охлаждения при различных способах закалки: 1 – непрерывная закалка в одном охладителе; 2- прерывистая закалка, или закалка в двух средах; 3 - ступенчатая закалка; 4 - изотермическая закалка; 5 – закалка с подстуживанием
2. Прерывистая закалка или закалка в двух средах (рис.8.2, кривая 2)
используется для деталей сложной формы. Нагретую до температуры закалки деталь (инструмент из углеродистой стали) охлаждают сначала в быстро охлаждающей среде, а затем в медленно охлаждающей. Обычно первое охлаждение проводят в воде, а затем деталь переносят в масло, или охлаждают на воздухе. В мартенситном интервале сталь охлаждается медленно, что способствует уменьшению внутренних напряжений.
3. Ступенчатая закалка (рис.8.2, кривая 3).
Режим ступенчатой закалки: деталь нагревают до температуры закалки .Ас3 + (3050 оС), выдерживают и быстро переносят в охладитель с температурой на 110-150 оС выше мартенситной точки (Мн); выдерживают а нем короткое время (расчетное), затем изделие охлаждают до комнатной температуры на воздухе, но это не должно вызвать превращения аустенита в бейнит.
Преимущества ступенчатой закалки:
-уменьшаются объемные изменения, вследствие присутствия большого количества остаточного аустенита и возможности самоотпуска мартенсита;
-уменьшается коробление в результате того, что мартенситное превращение протекает почти одновременно во всех участках изделия;
-меньше опасность появления трещин;
-во время фазовых превращений (мартенситного) снижается прочность стали
53
и повышается пластичность.
Горячие, а следовательно, сравнительно медленно охлаждающие среды не позволяют достигнуть критической скорости закалки для более или менее крупных сечений. Поэтому ступенчатая закалка для углеродистой стали применима лишь для деталей диаметром не более 10-12 мм, а для легированных сталей до 20-30 мм.
4. Изотермическая закалка (рис.8.2, кривая 4). В отличие от ступенчатой при изотермической закалке необходимо выдерживать сталь в закалочной среде столько времени, чтобы успело закончиться изотермическое превращение аустенита.
Режим изотермической закалки: нагрев до температуры закалки A3 + (30-50 оС ), выдержка и быстрый перенос в закалочную среду, температура которой выше точки Мн на 100-150 оС, затем дается длительная выдержка, чтобы полностью прошли превращения переохлажденного аустенита. При выдержке происходит распад аустенита с образованием структуры нижнего бейнита с хорошим коплексом механических свойств.
5. Закалка с самоотпуском.
Режим закалки: нагрев до температуры закалки А3 + (30-50 оС), выдержка и охлаждение в одном охладителе; прерывание охлаждения с тем, чтобы сердцевина сохранила запас тепла. Под действием теплообмена за счет внутреннего тепла снова нагревается поверхность. Тем самым происходит отпуск поверхности стали (самоотпуск). Сталь приобретает сочетание высокой твердости на поверхности детали с повышенной вязкостью в сердцевине. Примененяется такая закалка для изготовления зубил, кернов, кувалд и слесарных молотков.
6. Поверхностная закалка.
Конструкционная прочность многих деталей машин зависит от состояния материала в поверхностных слоях деталей.
Долговечность деталей, работающих в условиях изнашивания (валы, шестерни), зависит от сопротивления поверхности износу.
Разрушение деталей, работающих при изгибающих нагрузках в условиях циклических нагружений, начинается в поверхностных слоях детали. В этих случаях делают поверхностную закалку (при сохранении вязкой сердцевины), либо химикотермическую обработку (ХТО).
При поверхностной закалке нагрев только поверхности можно проводить :
-в расплавленных металлах или солях;
-пламенем ацетелено-кислородной или газовой горелки;
-в электролитах;
-лучом лазера;
-электротоком, индуцируемым в поверхностных слоях детали. Такая закалка называется индукционной или высокочастотной закалкой.
8.3. Закаливаемость и прокаливаемость
Выбор охлаждающей среды при термической обработке определяется закаливаемостью и прокаливаемостью стали.
Закаливаемость - способность стали принимать закалку, т.е. приобретать при закалке высокую твердость поверхности (определяется содержанием углерода в стали; при содержании углерода ниже 0,2 % сталь практически не закаливается).
Прокаливаемость - способность стали получать закаленный слой с мартенситной или троостито-мартенситной структурой с высокой твердостью на ту или иную глубину. Глубиной считают расстояние от поверхности до слоя, где в структуре содержится 50 % мартенсита + 50 % троостита.
Чем больше устойчивость переохлажденного аустенита, чем меньше критическая скорость закалки, тем больше прокаливаемость стали (рис. 8.3).
54

а) |
|
б) |
охл |
|
|
V |
|
|
|
Dкрит |
|
Закаленная |
Незакаленная |
Закаленная |
зона |
зона |
зона |
t |
|
|
|
|
A1 |
|
|
Поверхность |
|
Центр |
|
|
|
1/2 r |
П |
|
|
о |
|
|
в |
|
центр |
е |
|
|
р |
|
|
х |
|
|
н |
|
|
о |
|
|
с |
|
|
т |
|
|
ь |
1/2r |
|
|
M |
|
|
|
lg τ
Рис. 8.3. Схемы, показывающие различную скорость охлаждения по сечению
Характеристикой прокаливаемости является критический диаметр (Дкр). Критический диаметр - это максимальный диаметр прутка, прокаливающийся
насквозь в данном охладителе.
Определяют прокаливаемоеть экспериментально. Основной способ определения прокаливаемости - стандартный метод торцевой закалки (ГОСТ 5657-69 ) (рис.8.4).
Рис. 8.4. Количественная связь термокинетической -диаграммы(1) с графиком прокаливаемости, построенным методом торцевой закалки (2)
Метод торцевой закалки для определения прокаливаемости заключается в следующем:
-нагревают образец до заданной температуры;
-охлаждают с торца. При таком охлаждении нижний торец охлаждается с
55
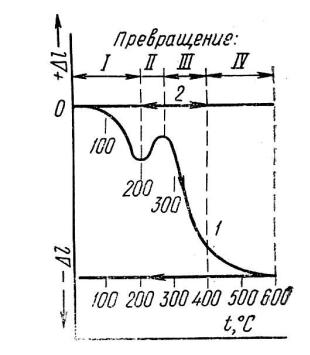
максимальной скоростью и скорость охлаждения убывает по мере удаления от торца;
-измеряют твердость по длине образца, начиная от торца;
-изображают графически результаты промера твердости на торце и по длине образца, определяют зону, содержащую 50 % мартенсита + 50 % троостита;
-определяют Дкр по номограммам прокаливаемости.
Прокаливаемость стали прямо пропорциональна содержанию в ней углерода. Легирующие элементы, входящие в состав стали, уменьшают критическую скорость закалки и увеличивают прокаливаемость.
9. ОТПУСК ЗАКАЛЕННОЙ СТАЛИ
Отпуск – это нагрев кристаллографически упорядоченной метастабильной структуры (мартенсит, нижний бейнит) до температур ниже Ас1 с последующей выдержкой при этой температуре и охлаждении.
Основные параметры отпуска: температура нагрева, время выдержки при этой температуре, скорость охлаждения.
Цели отпуска:
Снижение закалочных напряжений
Повышение пластичности, вязкости, сопротивления хрупким разрушениям.
Формирование требуемого комплекса свойств.
Процессы, протекающие при отпуске связаны с особенностями исходной структуры:
Мартенсит – метастабильный твердый раствор, пересыщенный по углероду.
Мартенситная структура отличается высоким уровнем неоднородных напряжений, высокой плотностью дефектов.
9.1 Превращения при отпуске закаленной углеродистой стали
Мартенсит – исходная структура, имеет максимальный объем, поэтому нагрев вызовет структурные и фазовые изменения, которые будут сопровождаться объемными эффектами
(рис.9.1).
Рис. 9.1 Дилатометрическая кривая отпуска углеродистой стали (1,2 % С) 1- закаленная сталь; 2- отожженная сталь
56
Первое превращение при отпуске сопровождается уменьшением объема и объединяет совокупность процессов, происходящих в мартенсите (распад мартенсита).
При нагреве мартенсита происходит перераспределение атомов углерода по междоузлиям, скопление их в участках с повышенной плотностью дефектов, образование микрообъемов феррита с повышенной концентрацией углерода, образование предвыделений, а затем и выделений карбидной фазы.
Возможность диффузионного перераспределения атомов углерода при нагреве до низких температур отпуска связано с высокой плотностью дефектов кристаллической решетки феррита мартенсита. Скорость диффузии атомов внедрения по дислокациям на несколько порядков выше, чем в бездефектной кристаллической решетке.
Распад мартенсита может протекать по двум механизмам:
1.Гетерогенному (двухфазному)
2.Однофазному
При низких температурах отпуска (до 170 оС) диффузионная подвижность атомов углерода еще мала, и при образовании карбидной фазы не происходит выравнивания концентрации углерода в объеме феррита мартенсита.
Мартенсит закалки однородный гомогенный, а при низких температурах отпуска мартенсит имеет различный по углероду состав.
При более высокой температуре отпуска диффузионная подвижность атомов углерода повышается, тем самым обеспечивается рост карбидной фазы и выравнивание состава мартенсита по углероду.
При низких температурах отпуска выделяется - карбид, когерентно связанный с матрицей (ферритом).
При более высоких температурах - карбид заменяется карбидом цементитного
типа.
Второе превращение при отпуске сопровождается повышением объема и состоит в распаде остаточного аустенита. Остаточный аустенит при отпуске распадается на те же продукты, на которые при данной температуре отпуска распадается мартенсит.
Третье превращение при отпуске сопровождается уменьшением объема и тепловым эффектом.
Втемпературном интервале третьего превращения появляется некоторая диффузионная подвижность у металлических атомов. Выделение - карбида прекращается происходит его растворение и формирование карбида цементитного типа.
С повышением температуры отпуска происходит рост цементитных частиц, что приводит к потере когерентной связи с матрицей.
Вэтом температурном интервале наиболее полно снимаются остаточные напряжения.
Четвертое превращение при отпуске объединяет совокупность процессов, происходящих в твердом растворе на основе феррита и в карбидной фазе.
Вкарбидной фазе происходит сфероидизация и коагуляция.
Вферрите протекают процессы рекристаллизации (рис. 9.2).
57

Рис.9.2 Схема, иллюстрирующая процессы, совершающиеся при отпуске
9.2 Влияние легирующих элементов на отпуск стали.
Распад мартенсита
При низких температурах отпуска распад мартенсита в легированных сталях происходит аналогично распаду мартенсита в углеродистых сталях.
Легирующие элементы существенно понижают скорость выделения углерода из кристаллической решетки феррита мартенсита.
Вуглеродистых сталях распад мартенсита заканчивается при температурах
250…300 оС.
Влегированных сталях распад мартенсита заканчивается при более высоких температурах 400…500 оС, т.к. : карбидообразующие элементы, образуя твердые растворы замещения, изменяют силы связи в кристаллической решетке феррита мартенсита, уменьшая тем самым термодинамическую активность углерода.
Наиболее сильно влияют Cr, Mo, V, Nb, W.
Некарбидообразующие элементы (Ni, Si, Mn, Co) не влияют на процессы распада мартенсита, а по некоторым данным даже ускоряют его.
Образование специальных карбидов
Образование специальных карбидов возможно по двум механизмам:
Растворение цементита с дальнейшим зарождением специального карбида в твердом растворе.
Насыщение кристаллической решетки цементита легирующими элементами до предела растворимости с последующим изменением типа кристаллической решетки (in situ).
Из всех легирующих элементов хром имеет высокую растворимость в цементите (до 20%), поэтому только карбиды хрома могут образовываться по механизму in situ.
(Fe, Cr)3C→Cr7C3
Если в стали много хрома, то возможно дальнейшее карбидное превращение:
Cr7C3 →Cr23C6
По механизму непосредственного зарождения образуются специальные карбиды
Nb, Mo, V, W, Ti (MeC, Me2C, Me23C6, Me7C3).
При реализации механизма непосредственного зарождения происходит сложное перераспределение углерода между ранее выделившимся цементитом, твердым раствором на основе феррита и специальными карбидами.
58
Выделившийся ранее цементит, растворяясь, обеспечивает необходимое для образования специальных карбидов содержание углерода в твердом растворе на основе феррита.
in situ
м→ о + (FeMe)3C
Fe3C+MexCy
непосредственное зарождение
м→ + (FeMe)3C
о +MexCy
Формирование специальных карбидов происходит в температурном интервале
450…600 оС.
После выделения специальных карбидов начинается процесс их коагуляции.
Распад остаточного аустенита.
В закаленных конструкционных сталях количество остаточного аустенита 3…5%, в легированных конструкционных сталях 8…10%, в быстрорежущих сталях 20…40%, в высокохромистых сталях 60…80%.
Распад остаточного аустенита в легированных сталях может протекать с образованием продуктов промежуточного превращения (бейнит) либо с образованием мартенсита при охлаждении с температуры отпуска. При распаде остаточного аустенита на бейнит легирующие элементы повышают температурный интервал , в котором происходит это превращение (400…600 оС). В этом случае кинетика превращения существенно отличается от кинетики бейнитного превращения переохлажденного аустенита при изотермической выдержке.
Т.к. остаточный аустенит имеет повышенную плотность дислокаций, расположен в виде прослоек между кристаллами мартенсита, и следовательно, находится в напряженном состоянии, то его распад при соответствующих температурах отпуска происходит без инкубационного периода, практически мгновенно.
Структура и свойства продуктов распада остаточного аустенита при этом близки к аналогичным, полученным при распаде мартенсита.
Распад остаточного аустенита с образованием мартенсита при охлаждении после отпуска характерен для сталей с высоким содержанием углерода и легированных сильными карбидообразующими элементами.
Диаграмма распада переохлажденного аустенита для таких сталей характеризуется высокой устойчивостью к распаду по первой и второй ступеням, наличием широкого температурного интервала повышенной устойчивости переохлажденного аустенита и линией выделения избыточных карбидов из переохлажденного аустенита.
При нагреве остаточного аустенита до температур 400…600 оС и выдержке, происходит выделение специальных карбидов, в результате которого остаточный аустенит обедняется по углероду и легирующим элементам. Температура начала мартенситного превращения остаточного аустенита растет и при охлаждении с температуры отпуска возможно превращение остаточного аустенита в мартенсит. Это превращение сопровождается повышением твердости и называется вторичной закалкой.
Возврат и рекристаллизация феррита.
При нагреве закаленной стали протекают процессы возврата, полигонизации, рекристаллизации, аналогичные процессам, протекающим при нагреве холоднодеформированного металла.
По сравнению с холоднодеформированным металлом мартенситная структура имеет ряд особенностей:
Высокая плотность дислокаций (1012 1/см2), но они распределены равномерно. Отсутствует ячеистая структура.
59
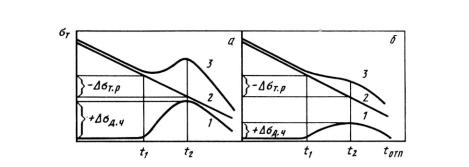
Имеются множественные границы между мартенситными кристаллами.
По мере повышения температуры в тонкой структуре мартенсита происходят процессы перераспределения и аннигиляции дислокаций, формирование полигональной структуры, а затем рекристаллизация.
Температурный интервал и степень реализации каждого из этих процессов зависит от устойчивости сегрегаций примесных атомов (сегрегации типа облаков Котрелла образуются на скоплениях дислокаций и закрепляют их), от количества, типа, характера выделения дисперсных частиц вторых фаз (карбиды, нитриды, карбонитриды, интерметаллиды).
В углеродистых сталях процессы рекристаллизации завершаются при температурах 350…400 оС. Введение легирующих элементов (Cr, Mn, Si, Mo, W, V, Nb, Ti) смещают этот температурный интервал до 450… 600 оС.
Дисперсионное упрочнение
При отпуске закаленной стали одновременно протекают два процесса: твердорастворное разупрочнение (вследствие обеднения феррита мартенсита по углероду) и упрочнение за счет выделения дисперсной карбидной фазы (рис. 9.3).
Рис 9.3 Изменение прочности вследствие распада мартенсита (1), из-за выделения
дисперсных карбидных частиц (2) и суммарное (3) при отпуске закаленной стали: а- -т.р. < + д.ч. ; б- - т.р. > + д.ч.
С повышением температуры отпуска 0,2 непрерывно снижается за счет твердорастворного разупрочнения (углерод уходит из феррита мартенсита, с/а снижается, уменьшается твердость и прочность).
При tотп= t1 начинается процесс выделения дисперсных частиц, что вызывает повышение прочности. Чем выше температура, тем больше объемная доля карбидной фазы, тем больше степень упрочнения.
При tотп > t2 начинается коагуляция выделившихся частиц и они уже не являются барьерами для движения дислокаций, происходит разупрочнение.
1) - 0,2 т.р. < + 0,2 д.ч. 2) - 0,2 т.р. > + 0,2 д.ч.
Вторичное твердение – повышение твердости, прочности (с пиком указанных характеристик).
Степень упрочнения при выделении дисперсных частиц зависит от количества вводимого легирующего элемента, размеров образующихся частиц и их объемной доли.
При легировании Mo, W (4%), V(1%), Nb, Cr (8...10%) наблюдается пик твердости.
9.3 Отпускная хрупкость стали
Отпускной хрупкостью называется охрупчивание стали при определенных условиях отпуска.
Существует два типа отпускной хрупкости:
60