
методичка
.pdfТаблица 1. Результаты исследований
Номер |
Поверхностный слой |
Сердцевина образца |
Примеча- |
||
глубина |
|
% содер- |
|
||
образ- |
время це- |
марка |
|||
ца |
цемента- |
ментации |
жание |
стали |
ние |
|
ции. |
|
перлита |
|
|
1. |
|
|
|
|
|
2. |
|
|
|
|
|
Контрольные вопросы:
1.В чем сущность процесса цементации стали?
2.Какие среды применяются при цементации?
3.Какие стали используются для цементации?
4.Как определить глубину цементационного слоя?
5.Какое содержание углерода в поверхностном слое?
6.Какаятермическая обработка применяется после цементации?
Лабораторная работа № 11 ТЕРМИЧЕСКАЯ ОБРАБОТКА АЛЮМИНИЕВЫХ
СПЛАВОВ
Цель работы: изучить влияние закалки и режимов старения на свойства алюминиевых сплавов.
Оборудование и материалы:
1.Коллекция шлифов
2.Металлографический микроскоп
3.Прибор для измерения твердости (Роквелл)
4.Справочные таблицы химического состава и механических свойств алюминиевых сплавов
5.Образцы для проведения термической обработки.
6.Электропечи
Теоретическое обоснование:
Из цветных сплавов в машиностроении широко используются алюминиевые сплавы. У алюминиевых сплавов отсутствуют мартенситные превращения, как в железо-углеродистых сплавах. Поэтому упрочняющая термическая обработка, заключающаяся в проведении закалки с получением мартенситной структуры и последующего отпуска, для алюминиевых сплавов неприменима. Для алюминиевых сплавов разработан особый вид упрочняющей термической обработки, который состоит из:
71
-закалки с получением перенасыщенного, термодинамически неустойчивого твердого раствора легирующих элементов
валюминии;
-старениясплава(распаднеустойчивоготвердогораствора). В зависимости от температуры нагрева различают:
-естественное старение (проводится при комнатной температуре):
-искусственное старение (проводится при температуре
150…1800С)
Применительно к алюминиевым сплавам упрочняющая термическая обработка используются как для деформируемых, так и для литейных сплавов.
Закалка алюминиевых сплавов.
Закалка заключается в нагреве сплавов до температуры, при которой избыточные интерметаллидные фазы полностью или большей частью растворяются в алюминии, выдержке при этой температуре и быстром охлаждении до комнатной температуры для получения пересыщенного твердого раствора.
Например, температура закалки сплавов системы "Алю- миний-Медь" (рис. 1) определяется линией abc, проходящей выше линии предельной растворимости для сплавов, содержащих меньше 5,7 % меди, и ниже эвтектической линии (548 °С) для сплавов, содержащих большее количество меди.
При нагреве под закалку сплавов, содержащих до ~5 %
меди, избыточная фаза СuА12 полностью растворяется, и при последующем быстром охлаждении фиксируется только пересыщенный α -твердый раствор.
При содержании более 5 % меди в структуре сплавов после закалки будет пересыщенный α-твердый раствор и нерастворенные при нагреве кристаллы соединения СuА12.
72
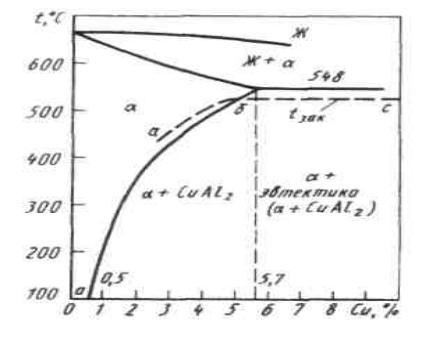
Рис. 1. Диаграмма состояния сплавов "Алюминий-Медь"
штриховая линия – температура закалки сплавов
Основной особенностью алюминиевых сплавов является малый интервал температур нагрева под закалку. Например, температура нагрева для сплавов А1Сu – Mg - составляет
485…510 °С.
Листы, плиты, прутки, полосы толщиной 0,5…150 мм нагревают в селитровых ваннах в течение 10…80 минут. В электропечах с принудительной циркуляцией воздуха нагрев составляет 30…210 минут. Фасонные отливки при закалке выдерживают более длительное время (2…15 ч), чтобы растворились грубые выделения интерметаллидных фаз.
Охлаждение при закалке должно проводиться со скоростью выше критической.
Под критической скоростью закалки понимают минимальную скорость охлаждения, которая предотвращает распад пересыщенного твердого раствора. Частичный распад твердого раствора снижает механические свойства и коррозионную стойкость после старения. Для закалки часто применяют воду (10…40 0С). Чтобы избежать частичного распада твердого раствора время переноса нагретой детали (заготовки) из печи в закалочный бак не должно превышать 15…30 с.
После закалки сплавы имеют сравнительно невысокую прочность и высокую пластичность. Так как при комнатной тем-
73
пературе скорость диффузии мала, поэтому в течение 3...5 ч после закалки сплав будет иметь высокую пластичность и хорошо обрабатываться давлением. При большем времени выдержки пластичность снижается, таккаксплав начинаетстареть.
До начала процесса старения следует проводить операции холодной пластической деформации (штамповку, ковку и т.п.)
Старение закаленных сплавов. После закалки проводят старение сплавов. Различают естественное и искусственное старение. При старении сплавы выдерживают при комнатной температуре несколько суток (естественное старение) или при 150…180°С (искусственное старение) в течение 10…15 часов. В процессе старения происходит распад пересыщенного твердого раствора, что сопровождается упрочнением сплава. Распад пересыщенного твердого раствора происходит в несколько стадий в зависимости от температуры и продолжительности старения. Например, в сплавах алюминий-медь при естественном (при 20°С) или искусственном старении (150…180°С) образуются зоны Гинье – Престона (ГП).
Образовавшиеся при старение зоны Гинье – Престона вызывают искажения кристаллической решетки, которые затрудняют движение дислокаций. В связи с этим пластичность снижается, а прочность растет.
Закалка алюминиевых сплавов с естественным старением обеспечивает максимальную прочность сплавов.
Искусственное старение обычно проводят при температуре 150…1800 С в течение 10…15 часов.
Повышение температуры старения до 200…250°С приводит к коагуляции (укрупнению) фаз и уменьшению растворенных элементов в твердом растворе. Это приводит к снижению твердости и предела прочности, но увеличению пластичности.
Если сплав после старения кратковременно (несколько и минут) нагреть до 240…280°С и затем быстро охладить, то упрочнение полностью снимается и свойства сплава будут соответствовать закаленному состоянию. Это явление получило название возврата. Разупрочнение при возврате связано с тем, что зоны ГП при этих температурах оказываются нестабильными и растворяются в твердом растворе. При последующей выдержки сплава при комнатной температуре происходит новое образование зон ГП, упрочняющих сплав. После возврата и после-
74
дующего старения коррозионные свойства сплава снижаются. Поэтому возврат редко используется для практических целей.
Порядок выполнения работы и содержание отчета:
1. Изучить влияние закалки на твердость алюминиевых сплавов:
-подвергнуть закалке от температуры нагрева 490...510 °С шесть образцов дуралюмина одной марки в воде (время нагрева
ивыдержки 30...40 минут).
-измерить твердость образцов до закалки и после закалки. 2. Изучить влияние температуры и времени старения на
твердость алюминиевых сплавов:
- провести старение закаленных образцов при температурах 100 °С, 180 °С и 250 °С (время нагрева и выдержки каждого образца 10…40 минут);
- измерить твердость образцов после старения.
3.По полученным данным построить график зависимости твердости от температуры старения. Сделать вывод о влиянии температуры старения закаленного дуралюмина на его твердость. Указать, при какой температуре старения достигается максимальная твердость дуралюмина.
4.Результаты работы занести в таблицу 1.
5.Дать определение закалки и старению сплавов.
6.Привести диаграмму состояния сплавов "АлюминийМедь" и указать на ней температурную область под закалку.
Таблица 1. Влияние термической обработки на твердость алюминиевых сплавов
Номер |
Твер- |
|
|
Твердость после |
|
|
||
дость |
Закал |
|
Старения при температуре, 0 С |
|||||
об- |
до за- |
ки |
|
|
|
|
|
|
100 |
180 |
250 |
||||||
разца |
калки |
|
|
|
|
|
|
|
|
10 мин |
40мин |
10 мин |
40мин |
10 мин |
40мин |
||
1 |
|
|
|
|
|
|
|
|
2 |
|
|
|
|
|
|
|
|
3 |
|
|
|
|
|
|
|
|
4 |
|
|
|
|
|
|
|
|
Примечание: температуры старения и время выдержки могут меняться по заданию преподавателя
75
Контрольные вопросы:
1.Какая упрочняющая термическая обработка применяется для алюминиевых сплавов?
2.Какие структурные изменения происходят в процессе закалки алюминиевых сплавов?
3.Какие стадии распада пересыщенного твердого происходят при разных температурах старения в сплавах алюминиймедь?
4.ЧтопредставляютсобойзоныГинье-Престона(зоныГП)?
5.Как изменяется твердость дуралюмина в зависимости от температуры старения?
6.Какое влияние оказывает время старения на твердость дуралюмина?
Лабораторная работа № 12 ТЕПЛОСТОЙКОСТЬ ИНСТРУМЕНТАЛЬНЫХ СТАЛЕЙ
Цель работы: изучить структуру и свойства инструментальных сталей; ознакомиться с понятием теплостойкости (красностойкости) и структурными изменениями, происходящими при нагревании инструментальных сталей.
Оборудование и материалы:
1.Коллекция шлифов
2.Металлографический микроскоп
3.Прибор для измерения твердости (Роквелл)
4.Справочные таблицы химического состава и механических свойств инструментальных сталей.
5.Образцы для проведения термической обработки.
6.Электропечи.
Теоретическое обоснование:
К инструментальным сталям относятся углеродистые и легированные стали, обладающие высокой твердостью (60-65 HRC), прочностью и износостойкостью. Обычно это заэвтектоидные или ледебуритные стали, структура которых после закалки и низкого отпуска состоит из мартенсита и избыточных карбидов. Стали применяются для изготовления различного инструмента.
По назначению инструментальные стали делятся на: - стали для режущего инструмента;
76
-стали для измерительного инструмента;
-стали для изготовления штампов.
Маркировка инструментальных сталей.
Углеродистые инструментальные стали маркируют бук-
вой «У» (углеродистая); следующая за ней цифра (7, 8, 9, 10, 11, 12 и 13) показывает среднее содержание углерода в десятых долях процента. Буква «А» в конце маркировки указывает, что сталь высококачественная. (Например, сталь У10А – углеродистая, инструментальная, высококачественная сталь, содержа-
щая 1,0 %С).
Легированные инструментальные стали маркируют цифрами, показывающими среднее содержание углерода в десятых долях процента, если его содержание меньше 1 %. Буквы за цифрами означают легирующие элементы, а следующие за ними цифры — содержание (в целых процентах) соответствующего легирующего элемента. Если легированная сталь содержит примерно 1% углерода, то цифра в марке не ставится (например, ХВГ).
Быстрорежущие стали маркируют буквой «Р». Следующая за ней цифра указывает среднее содержание вольфрама (в целых процентах). Содержание углерода в пределах 1%.
Среднее содержание хрома в большинстве быстрорежущих сталей составляет 4% и поэтому в обозначении марки стали не указывается.
В процессе резания происходит выделение тепла, которое приводит к разогреву режущей кромки инструмента. Увеличение скорости резания повышает температуру инструмента. Последующее охлаждение инструмента приводит к снижению твердости.
Снижение твёрдости инструмента при нагревании определяется процессами, протекающими в сталях. Прежде всего это вызвано распадом мартенсита и коагуляцией (укрупнением) карбидных частиц. Легирование стали тугоплавкими элементами (вольфрамом, молибденом, ванадием, хромом) уменьшает скорость диффузии и тем самым замедляет эти процессы, сдвигая их к более высоким температурам (550...600) 0С. Поэтому в легированных сталях снижение твердости происходит при нагреве до более высоких температур.
77
Одной из главных характеристик инструментальных сталей является теплостойкость (красностойкость), т. е. способность стали сохранять высокую твердость при нагреве (устойчивость против отпуска при нагреве инструмента в процессе работы).
Теплостойкость (красностойкость) инструментальной стали определяется максимальной температурой, до которой она сохраняет свою высокую твёрдость.
По теплостойкости углеродистые стали и сплавы классифицируются на:
-нетеплостойкие, сохраняющие твёрдость до 200°С (углеродистыеУ7, У8, У12 низколегированные стали9ХС,В2Фидр.);
-полутеплостойкие, сохраняющие твёрдость до 400…500 °С (среднелегированные стали Х6ВФ, Х6Ф4М, Х12М и др.);
-теплостойкие, сохраняющие твёрдость до 600…650°С (высоколегированные быстрорежущие стали Р18, Р9, Р6М5 и др.);
-с повышенной теплостойкостью, сохраняющие твёрдость до 800…1000°С (металлокерамические твёрдые сплавы ВК6, ВК8,
Т15К6 и др. ).
Второй важной характеристикой инструментальных сталей является прокаливаемость.
Прокаливаемость инструментальных сталей определяется их химическим составом
Инструментальные углеродистые стали имеют небольшую прокаливаемость.
Высоколегированные теплостойкие и полутеплостойкие стали обладают более высокой прокаливаемостью.
Для режущего инструмента используются: углеродистые, легированные и быстрорежущие стали, а также металлокерамические твердые сплавы. Твердость режущей кромки инструмента должна быть не ниже 60…64 HRC. Такую твёрдость обеспечивает закалка с последующим низким отпуском для снятия остаточных напряжений.
Режущие инструменты из углеродистых сталей пригодны
для обработки при небольших скоростях резания. Твердость в таких сталях сильно снижается при нагреве свыше 2000С.
Фрезы, зенкеры, сверла, спиральные пилы, шаберы, ножовки ручные, напильники изготавливают из сталей У10, У11,
У12 и У13.
Стали У7 и У8 применяют для изготовления зубил, керне-
78
ров, бородков, отверток и топоров.
Легированные стали 9ХС и ХВСГ имеют большую теплостойкость (250…260°С) и хорошие режущие свойства. Стали мало деформируются при закалке. Эти стали применяют для инструмента большего сечения (ручные сверла, развертки, плашки).
Быстрорежущие стали рекомендуются для всех видов инструмента при обработке углеродистых и легированных сталей. Наиболее часто применяют сталь Р6М5. Для обработки высокопрочных, коррозионно-стойких и жаропрочных сталей и сплавов применяют стали с кобальтом (Р18К5Ф2, Р9К5, Р6М5К5, Р9М4К8). Для чистовых инструментов при обработке вязкой аустенитной стали и материалов, обладающих абразивными свойствами, используется сталь Р12Ф3 с ванадием.
Металлокерамические твердые сплавы, составленные из карбидов вольфрама, титана и тантала в связке с кобальтом, сохраняют режущие свойства до 1000 °С (ВК8, Т15К6, ТТ7К12 и др.). Их применяют для резания с повышенной скоростью труднообрабатываемых материалов.
Для измерительного инструмента (плитки, калибры, шаблоны и др.) в основном используются высокоуглеродистые хромистые стали Х, ХВГ, ШХ15 и др. Стали должны обладать высокой твердостью, износостойкостью, хорошо шлифоваться и сохранять постоянство размеров. После закалки и низкого отпуска в сталях возможно процессы частичного распада мартенсита и превращения остаточного аустенита в мартенсит. Это вызывает изменение объема и линейных размеров изделия, что является недопустимым для измерительных инструментов высоких классов точности. В связи с этим большинство измерительных инструментов подвергают обработке холодом (при температуре минус 70°С) сразу после закалки. Твердость после указанной обработки 63…64 HRC.
При выборе сталей для изготовления штампов необходимо учитывать способ деформирования. Штамповые стали делятся на стали для холодного деформирования и стали для горячего деформирования (рабочая температура 600…750°С).
Для холодного деформирования применяют высокохромистые стали, которые должны обладают высокой износостой-
79
костью и глубокой прокаливаемостью. Для этих целей используются стали - Х12Ф1, Х12М, Х6ВФ.
Стали для горячего деформирования, кроме уже сказанного, должны обладать высокой теплостойкостью и окалиностойкостью. Для горячего деформирования используют стали – 5ХНМ, 5ХНВ, 4Х5В2ФС и др.
Примерное назначение различных инструментальны сталей приведено в приложении 7.
Порядок выполнения работы и содержание отчета:
1.Получить образцы инструментальных материалов, подвергнутых закалке и низкому отпуску.
2.Измерить твёрдость образцов после закалки и отпуска (по Роквеллу).
3.Поместить образцы в печь и выдержать при температурах, указанных ниже:
а) углеродистые стали до 200, 250, 400°С; б) быстрорежущие стали до 500, 600, 700°С; в) металлокерамические сплавы до 800.
(время выдержки 40 мин, охлаждение на воздухе)
4.Измерить твёрдость образцов после отпуска и результаты испытаний занести в табл. 1.
5.Оценить теплостойкость каждой марки сплава. Таблица 1. Результаты испытания
|
|
Твердость материала после: |
|
|
|||||
Марка ма- |
закалки и |
нагрева и выдержки при температурах, 0С |
|||||||
териала |
низкого |
200 |
250 |
400 |
500 |
600 |
700 |
800 |
|
отпуска |
|||||||||
|
|
|
|
|
|
|
|
||
Сталь У 8 |
|
|
|
|
|
|
|
|
|
Сталь Р18 |
|
|
|
|
|
|
|
|
|
Сталь |
|
|
|
|
|
|
|
|
|
Х6ВФ |
|
|
|
|
|
|
|
|
|
Сплав ВК 8 |
|
|
|
|
|
|
|
|
Примечание: температуры нагрева и время выдержки могут меняться по заданию преподавателя
Контрольные вопросы:
1.Укажите достоинства и недостатки углеродистых сталей для режущего инструмента?
2.В чем преимущества легированных сталей для режущего инструмента перед углеродистыми сталями?
80