
методичка
.pdfисходит снижение пластичности.
3. Магниевые сплавы
Литой магний имеет крупнокристаллическую структуру и низкие механические свойства: σв = 110…120 МПА; δ = 6…8%; НВ30. Модифицирование магния цирконием и пластическая деформация немного улучшают механические свойства (σв = 260 МПА; δ = 8,5…9%).
Чистый магний применяется в основном пиротехнике, в химической промышленности и металлургии (в виде раскислителя или легирующего элемента). В машиностроении применяются магниевые сплавы.
Магниевые сплавы обладают малой плотностью, хорошо обрабатываются резанием, но плохо сопротивляются коррозии.
Малая плотность магниевых сплавов в сочетании с высокой удельной прочностью и рядом физико-химических свойств делает их ценными для применения в различных областях машиностроения: автомобильной, приборостроении, самолетостроении, космической, радиотехнике и других областях.
Магниевые сплавы по технологии изготовления подразделяют на две группы:
1)литейные сплавы, используемые для получения деталей
изаготовок методом литья;
2)деформируемые сплавы, подвергаемые различным видам обработки давлением.
Для магниевых сплавов применяются следующим видам термической обработки: диффузионный отжиг (гомогенизация), закалка и старение.
Слитки и фасонные отливки подвергают диффузионному отжигу при температуре 400…490°С продолжительностью
10…24 ч.
При отжиге магниевых сплавов избыточные фазы, выделившиеся по границам зерен, растворяются и химический состав по объему зерен выравнивается, что облегчает обработку давлением и способствует повышает механические свойства сплавов.
Для устранения наклепа и уменьшения анизотропии механических свойств магниевые сплавы подвергают рекристаллизационному отжигу при температуре 250…350 °С.
Ряд магниевых сплавов может быть упрочнен закалкой и
61
старением. Особенностью магниевых сплавов является малая скорость диффузионных процессов, поэтому фазовые превращения в них протекают медленно. Это требует больших выдержек при нагреве под закалку (4…24 ч) и искусственное ста-
рение (15…20 ч).
Многие сплавы закаливаются при охлаждении отливок или изделий после горячей обработки давлением на воздухе. Закалку осуществляют при нагреве до 380…540 °С . Старение проводят при 150…200 °С.
Путем старения можно повысить прочность магниевых сплавов на 20…35 %, однако пластичность сплавов при этом уменьшается. Поэтому часто ограничиваются только старением, улучшающим механические свойства сплавов.
Деформируемые сплавы (поставляются по ГОСТ14957-46). Сплавы маркируемые буквами МА и числом, указывающим номер сплава. Деформируемые сплавы изготовляют в виде горячекатаных прутков, полос, профилей, а также поковок и
штамповок.
Чем меньше скорость деформации, тем выше технологическая пластичность магниевых сплавов. Прессование сплавов в зависимости от состава сплава ведут при 300…480°С. Штамповку проводят в интервале температур 480…280 °С в закрытых штампах. Вследствие текстуры деформации полуфабрикаты (листы, прутки, профили и др.) из магниевых сплавов имеют сильную анизотропию механических свойств. Поэтому холодная прокатка сопровождается проведением промежуточных рекристаллизационных отжигов.
Сплав МА1 обладает сравнительно высокой технологической пластичностью, хорошей свариваемостью и высокой коррозионной стойкостью. По механическим свойствам он относится к сплавам низкой прочности.
Сплав МА8 имеет более высокие механические свойства и лучше деформируется в холодном состоянии.
Сплав МА2-1 (Mg—Al—Zn) обладает достаточно высокими механическими свойствами и хорошей свариваемостью. Сплав поддается всем видам листовой штамповки и легко прокатывается. Однако сплав склонен к коррозии под напряжением.
Сплав МА14 отличается повышенными механическими свойствами, жаропрочен (до 250 °С) и не склонен к коррозии под напряжением. К недостаткам сплава относится склонность
62
к образованию трещин при горячей прокатке. Сплав упрочняется в процессе искусственного старения при 160…170 °С.
В связи с малой устойчивостью к коррозии изделия из магниевых сплавов оксидируются. На оксидированную поверхность наносят лакокрасочные покрытия.
Литейные сплавы (поставляются по ГОСТ 2859— 79).
Сплавы маркируемые буквами МЛ и числом, указывающим номер сплава.
Восновном литейные сплавы имеют более низкие, чем у деформируемых сплавов, механические свойства.
Впрактике широко используют сплав МЛ5, в котором сочетаются высокие механические и литейные свойства. Он используется для литья нагруженных крупногабаритных отливок.
Сплав МЛ6 имеет лучшими литейными свойствами, чем сплав МЛ5, и предназначается для изготовления тяжелонагруженных деталей.
Механические свойства сплавов МЛ5 и МЛ6 могут быть повышены отжигом при температуре 420 °С и закалкой на воздухе.
Более высокие значения прочности и предела текучести сплав МЛ5 приобретает после дополнительного старения при температуре 175 °С, а сплав МЛ6 после старения при температуре 190 °С.
Сплав МЛ 10 относится к группе жаропрочных и применяется для отливок, работающих при температурах до 300 °С.
Сплав МЛ 12 наряду с высокими механическими свойствами отличается большой коррозионной стойкостью и хорошими литейными свойствами. Сплав может быть упрочнен отжигом, закалкой от 400 °С на воздухе и длительным старением (50 ч) при температуре 150 °С.
При выплавке и литье магниевых сплавов применяют специальные меры предосторожности для предотвращения загорания сплава. Плавку ведут в железных тиглях подслоем флюса, а при разливке струю металла посыпают серой; образующей сернистый газ, предохраняющий металл от воспламенения. В песчаную почву для уменьшения окисления металла добавляют специальные присадки, например фтористые соли алюминия.
Химический состав и механические свойства типичных деформируемых и литейных сплавов приведены в приложении 6.
63
4. Антифрикционные (подшипниковые) сплавы
Сплавы применяют для изготовления подшипников трения скольжения. Они должны удовлетворять следующим требованиям:
–высокое сопротивление износу;
–малый коэффициент трения;
–высокая теплопроводность;
–хорошая прирабатываемость;
–способность удерживать смазку на поверхности;
–устойчивость против коррозии.
Для обеспечения этих свойств структура антифрикционных сплавов должна состоять из мягкой основы и твердых включений. При вращении вал опирается на твердые частицы, обеспечивающие износоустойчивость, а мягкая основа истирается более быстро, прирабатывается к валу и образует сеть микроскопических каналов, по которым циркулирует смазка и уносятся продукты износа.
К сплавам для подшипников трения скольжения относятся оловянистые и свинцовые баббиты, сплавы на алюминиевой и цинковой основе, металлокерамические пористые сплавы, антифрикционные чугуны и бронзы.
Баббиты состоят из мягких пластичных металлов (олово и свинец) с добавками меди, сурьмы, кадмия, никеля и др. примесей.
Высокооловянистые баббиты Б89, Б83 применяют для подшипников особо нагруженных машин (паровые турбины, турбокомпрессоры, электромоторы мощностью более 750 кВт). Свинцовые баббиты Б6, Б16, БН, СОС6-6 – для подшипников тракторных и автомобильных двигателей. Заменителями оловянистых и свинцовистых баббитов являются кальциевые (БКА, БК2), цинковые (ЦАМ10-5, ЦАМ9-15), алюминиевые (АСС6, АСМ, АО 20-1) и др. В настоящее время широкое распространение получили двух- и трехслойные подшипники трения скольжения. Основой является стальная лента из стали 08 кп, на которую наносят слой 0,1-0,4 мм подшипникового сплава. Микроструктура подшипниковых сплавов показана на рисунке 3.
Металлокерамические пористые подшипниковые сплавы состоят из порошков железо-графит, железо-медь- графит, железо-свинец-графит, бронза-графит. Данные сплавы
64
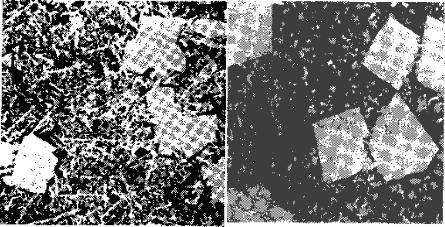
работают часто как самосмазывающиеся подшипники.
а) |
б) |
Рис. 3. |
Микроструктура подшипниковых сплавов: |
а) баббит на свинцовой основе–Б16; б) баббит на оловянной основе–Б83.
Порядок выполнения работы и содержание отчета:
1.Рассмотреть под микроскопом структуры сплавов и зарисовать их.
2.Сравнить рассматриваемые структуры со структурами, приведёнными в атласе, и определить марки сплавов.
3.По справочным таблицам указать механические свойства и применения сплавов.
4.Указать способы упрочнения сплавов.
5.Привестидиаграммысостояниясоответствующихсплавов.
Контрольные вопросы:
1.Связь между диаграммами состояния соответствующих сплавов и их свойствами (технологическими и механическими).
2.Классификация цветных сплавов (медных, алюминиевых, магниевых)
3.Требования, предъявляемые к литейным сплавам.
4.Требования,предъявляемыекподшипниковымсплавам.
5.Методы упрочнения сплавов.
6.Применения сплавов.
Лабораторная работа №10 ЦЕМЕНТАЦИЯДЕТАЛЕЙВТВЕРДОМКАРБЮРИЗАТОРЕ
Цель работы: научится определять основные параметры процесса цементации в твердом карбюризаторе; изучить мик-
65
роструктуру и свойства стали после цементации и последующей закалки.
Оборудование и материалы:
1.Коллекция шлифов
2.Металлографический микроскоп
3.Справочные таблицы химического состава и механических свойств углеродистых сталей
4. Атлас структур цементированных сталей.
Теоретические сведения:
Цементацией (науглероживанием) называется химико - термическая обработка, заключающаяся в диффузионном насыщении поверхностного слоя стали углеродом при нагреве в науглероживающей среде (карбюризаторе). Одним из основных процессов, происходящих при цементации, является процесс диффузии углерода. Диффузия углерода в сталь возможна только в том случае, если углерод находится в атомарном состоянии. Атомарный углерод адсорбируется поверхностью детали и диффундирует в глубь металла. В связи с этим, цементацию рекомендуется проводят при температурах выше точки Ас3 (930—950 °С), когда устойчив аустенит, растворяющий углерод в большом количестве чем феррит. Обычно это темпера-
тура 920…950 0С.
Цель цементации и последующей термической обработки - придать поверхностному слою высокую твердость и износостойкость, повысить предел контактной выносливости и предел выносливости при изгибе и кручении.
Цементируют шестерни, поршневые пальцы, толкатели и другие детали.
Окончательные свойства цементированные изделия приобретают в результате закалки и низкого отпуска, которые проводят после процесса цементации.
Для цементации обычно используют низкоуглеродистые (0,1…0,18% С), в том числе и легированные стали. Для цементации крупногабаритных деталей применяют стали с более высоким содержанием углерода (0,2…0,3 %). Использование таких сталей необходимо для того, чтобы сердцевина изделия, которая не насыщающаяся углеродом при цементации, сохраняла высокую вязкость после закалки.
66
На цементацию детали поступают после механической обработки с припуском на шлифование (50…100 мкм). Во многих случаях цементации подвергается только часть детали. Участки, не подлежащие цементации, защищают тонким слоем меди (20…40 мкм), которую наносят электролитическим способом. Можно использовать специальные обмазки, состоящие из смеси огнеупорной глины, песка и асбеста, замешанных на жидком стекле.
Время выдержки при цементации выбирают по таблицам или графикам в зависимости от температуры цементации и глубины цементованного слоя.
Цементованный слой имеет переменную концентрацию углерода по толщине, убывающую от поверхности к сердцевине детали (рис.1). В структуре цементованного слоя можно выделить три зоны:
-заэвтектоидную, состоящую из перлита и вторичного цементита, образующего сетку по бывшему зерну аустенита;
-эвтектоидную, состоящую из одного пластинчатого перлита;
-доэвтектоидную, состоящую из перлита и феррита. Количество феррита в этой зоне непрерывно увеличивается по мере приближения к сердцевине образца.
После закалки и низкого отпуска структура цементированных деталей в поверхностном заэвтектоидном слое (0,8… 1,0 % С) состоит из мартенсита и небольшого количества остаточного аустенита и цементита; в эвтектоидном слое (0,8% С) структура мартенсит. Структура сердцевины остается такой же, как до закалки.
Твердость на поверхности цементированных деталей после термической обработке должна составлять НRC > 56…60.
На рисунке 1 приведены структуры стали 15 после цементации и закалки.
Концентрация углерода в поверхностном слое должна составлять 0,8…1,0%. Для получения высокой контактной усталости содержание углерода может быть повышено до 1,1…1,2%. Более высокая концентрация углерода вызывает ухудшение механических свойств в поверхностном слое образца.
67
Качество цементации оценивается по эффективной толщине цементованного слоя, которая определяется по одному из двух показателей – структуре слоя или по значению твердости.
Эффективную толщину цементованного слоя по структуре изучают на металлографических шлифах. Границей цементованного слоя считается структура состоящая из 50% перлита и 50% феррита, что соответствует концентрации углерода рав-
ной 0,4%.
Если за критерий оценки толщины цементованного слоя принимается твердость, то оценка ведется на термически обработанных образцах. За конец цементованного слоя принимается слой с твердостью 50 HRC.
Цементациюдеталейпроводятв твердойилигазовойсредах.
Цементация в твердой среде.
В этом процессе насыщающей средой является древесный уголь (дубовый или березовый) к которому добавляют активизаторы: углекислый барий (ВаС03) и кальцинированную соду (Na2COs) в количестве 10…40 % от массы древесного угля.
Детали после предварительной очистки укладывают в ящики: стальные или чугунные прямоугольной или цилиндрической формы. При упаковке изделий на дно ящика насыпают и утрамбовывают слой карбюризатора толщиной 20…30 мм, на который укладывают первый ряд деталей, выдерживая расстояния между ними и до боковых стенок ящика 10…15 мм. Затем засыпают и утрамбовывают слой карбюризатора толщиной 1…15 мм, на него укладывают другой ряд деталей и т. д. Верхний ряд деталей засыпают слоем карбюризатора толщиной 35…40 мм с тем, чтобы компенсировать возможную его усадку. Ящик накрывают крышкой, кромки которой обмазывают огнеупорной глиной. После этого ящик помещают в печь.
Нагрев до температуры цементации и продолжительность выдержки при температуре цементации выбирается по специальным таблицам
После цементации ящики охлаждают на воздухе до 400…500°С, а затем ящики раскрывают.
Цементация в газовой среде.
Этот процесс осуществляют нагревом изделия в среде га-
68
зов, содержащих углерод. Газовая цементация широко применяется на заводах при серийном производстве деталей и проводится в специальных шахтных печах. Она имеет ряд преимуществ по сравнению с цементацией в твердом карбюризаторе.
В случае газовой цементации:
-легче получить заданную концентрацию углерода в поверхностном слое;
-сокращается длительность процесса, так как отпадает необходимость прогрева цементационных ящиков, заполненных малотеплопроводным карбюризатором;
-обеспечивается возможность полной механизации и автоматизации процессов;
-значительно упрощается последующая термическая обработка деталей, так как закалку можно проводить непосредственно из цементационной печи.
Наиболее качественный цементованный слой получается при использовании в качестве карбюризатора природного газа, состоящего из метана (СН4) и пропан-бутановых смесей, подвергнутых специальной обработке, а также жидких углеводородов.
Процесс газовой цементации ведут при температуре 910…930°С (6…12 ч). Необходимая для газовой цементации атмосфера создается при подаче в камеру печи жидкостей, богатых углеродом (керосин, спирты и т. д.). Углеводородные соединения при высокой температуре разлагаются с образованием цементующего газа.
69
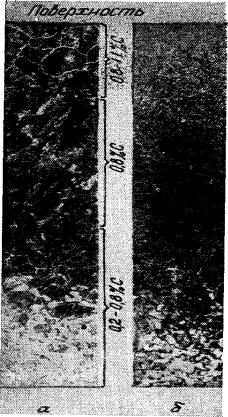
Рис. 1 Микроструктура стали марки 15:
а) после цементации; б) после цементации и термической обработки
Порядок выполнения работы и содержание отчета:
1.Подготовить образцы для проведения цементации
2.Уложить образцы в цементационный ящик, засыпать цементационной смесью и закрыть крышкой.
3.Определить время проведения цементации в твердой среде.
4.Установить цементационный ящик в электрическую печь.
5.Провести цементацию
6.Рассмотреть под микроскопом структуры коллекции образцов, ранее подвергающихся цементации и зарисовать их.
7.Определить глубину цементационного слоя и по таблицам найти время цементации.
8.Определить марку стали (по сердцевине образца).
9.Результаты работы занести в таблицу 1.
Примечание: процесс цементации в рассматриваемых образцах проводился при температуре 920..950 0С.
70