
методичка
.pdfсировать тепловой эффект, о котором судят по изменению температуры металла, то можно выявить вид превращения и определить условия, способствующие или тормозящие превращение.
Регистрация теплового эффекта превращения может быть осуществлена различными способами, в том числе измерениями теплоемкости, поскольку при выделении тепла теплоемкость падает, а при поглощении тепла - резко возрастает.
В практике металловедения наибольшее применение получил термический анализ – экспериментальная техника проведения которого является менее сложной. В случае термического анализа изменение теплосодержания характеризуется изменением температуры, обычно фиксируемой в функции времени нагрева или охлаждения металла.
При термическом анализе записывается (в т.ч. и автоматически), а затем строится по экспериментальным данным графическая зависимость изменение температуры во времени в процессе нагрева (или охлаждения) с постоянной скоростью. Появление теплового эффекта вызывает при соответствующей температуре появление различного вида аномалий (ступенек или перегибов на кривой охлаждения). Плавление и затвердевание являются фазовыми превращениями первого рода, и поэтому они сопровождаются резкими изменениями энтальпии и соответственно значительными тепловыми эффектами. Об этих изменениях свидетельствует характер зависимостей температуры во времени, изображаемых в виде кривых нагрева или охлаждения. Их рассмотрение позволяет с достаточной точностью определить температуры плавления или кристаллизации металлических сплавов (критические точки).
1.Метод простого термического анализа.
По методу термического анализа испытуемый материал помещают в нагревательное устройство. Схема установки приведена на рис.2. Если определяют температуры плавления или кристаллизации, то этот металл помещают в тигель и доводят до плавления. В тигель вводят горячий спай термопары, соответствующим образом изолированный от непосредственного контакта с этим металлом. Если же определяют превращения в твердом состоянии, то образец помещают в нагревательное устройство таким образом, чтобы исключить непосредственное влияние излучения нагревателей, например, путем установки экранов. Холодный спай от указанных термопар выводят к измерительным приборам. По показаниям этих приборов – по отдельным замерам температуры через определенные интервалы времени строят графики: "Температура – время". По появлению аномалий – перегибов или остановок (площадок) определяют критические точки, т. е. температуры превращений.
11

Рис. 2. Схема установки для определения критических точек:
1 – исследуемый сплав; 2 – электрическая печь; 3 – керамическая крышка; 4 – кварцевый наконечник; 5 – термостат; 6 – потенциометр.
2. Методика определения температур кристаллизации сплавов Рb – Sb
Температуру кристаллизации определяют на установке, приведенной на рис. 2. Для определения температур кристаллизации необходимо:
1.Подготовленное количество (150 – 200 г) чистого металла или сплава определенного состава поместить в тигель, установленный в электропечь.
2.Включить печь и расплавить (с некоторым перегревом) в тигле металл или сплав данного состава.
3.На поверхность расплавленного металла (сплава) насыпать слой толченого древесного угля для предохранения металла (сплава) от окисления.
4.Закрыть тигель крышкой или листовым асбестом.
5.Через отверстие крышки или через листовой асбест в расплавленный металл (сплав) поместить горячий спай термопары. Холодный спай термопары должен находиться в термостате, а медные провода должны быть присоединены к гальванометру.
6.Выключить печь.
7.Через каждые 15 или 30 с. записывать показания гальванометра. Запись прекратить после полного затвердевания металла (2000С). Полученные результаты для всех сплавов занести в таблицу 1.
8.По полученным данным построить кривую охлаждения в координатах "температура – время охлаждения".
9.На построенных кривых охлаждения определить критические точки, которые определяются по горизонтальному участку кривой или точкам перегиба кривой (для всех сплавов, кроме эвтектического). В последнем случае определить две температуры – начала и конца кристаллизации.
Полученные результаты для всех сплавов занести в таблицу 2.
12
2. Методика построения диаграммы состояния сплавов РЬ – SЬ
Диаграмму строят на основании данных таблицы 2. Для построения диаграммы необходимо:
1.Начертить сетку в координатах "температура – состав", температура по оси ординат, состав в процентах по оси абсцисс.
2.Разделить ось абсцисс и обозначить состав сплавов, на оси ординат обозначить температуру.
3.На оси абсцисс отметить точки, соответствующие исследованным сплавам, т. е. сплавам с 5, 13, 40 и 60 % 5Ь (возможна другая концентрация сплавов) и в каждой из этих точек восстановить перпендикуляр, т. е. провести линии сплавов.
4.На каждой линии отметить точками температуры кристаллизации. Так как линиями чистых металлов свинца и сурьмы являются две ординаты (левая – свинца и правая – сурьмы), то на этих ординатах отметить точками полученные температуры кристаллизации свинца и сурьмы (рис. 1).
Таблица 1. Результаты исследования сплавов |
|
|
|
||||||
Время |
Температура, |
0С |
Время |
Температура, |
0С |
||||
сплав |
сплав |
|
сплав |
сплав |
сплав |
|
сплав |
||
отсчета |
1 |
2 |
|
3 |
отсчета |
4 |
5 |
|
6 |
|
|
|
|
|
|
|
|
|
|
|
|
|
|
|
|
|
|
|
|
5.Соединить линией точки, характеризующие конец кристаллизации сплавов.
6.Соединить плавными линиями точки, характеризующие начало кристаллизации сплавов, продолжить их до точек кристаллизации чистых металлов (свинец – 327° С, сурьма – 631° С)
Таблица 2. Критические точки сплавов
Концентрация |
Критические температуры, 0С |
||
начало |
конец |
||
свинца в сплаве, % |
|||
кристаллизации |
кристаллизации |
||
|
|
|
|
|
|
|
Порядок выполнения работы и содержание отчета:
1. Привести схему установки
13
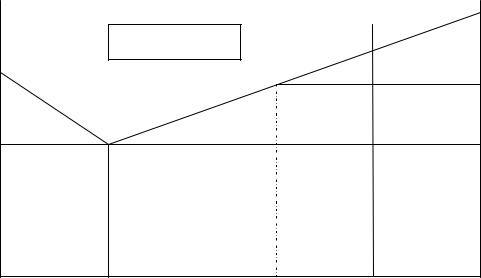
2.Провести охлаждение исследуемых сплавов. Результаты занести в таблицу 1.
3.По полученным данным построить кривые охлаждения.
4.Определить критические точки, результаты занести в таблицу 2.
5.Построить диаграмму состояния (по найденным критическим точкам).
6.Указать структуру и фазовый состав сплавов для всех областей диаграммы, а также превращения в критических точках.
7.Указать методы исследования металлов.
8.Описать сущность термического метода исследования металлов.
Правило отрезков
Правило отрезков позволяет определить соотношение фаз в сплаве при определенной температуре. Рассмотрим правило отрезков на примере диаграммы Pb – Sb, приведенной на рис. 3.
Например, необходимо определить соотношение фаз в точке a.
В точке a в равновесии находятся две фазы (жидкая и твердая).
Жидкий сплав |
|
|
b |
a |
c |
Pb+ж. |
|
|
Pb+эвт |
|
|
Эвт + Sb |
|
|
Pb |
|
Sb |
Рис. 3. Диаграмма сотояния Pb – Sb. |
|
|
Согласно правилу отрезков составляем пропорцию: |
|
14
Qтв / Qж = ba / ac,
где Qтв – количество твердой фазы;
Qж – количество жидкой фазы;
Определив отрезки ba и ac, находим соотношение фаз.
Контрольные вопросы
1.Физическая сущность термического метода анализа.
2.Что называется диаграммой состояния сплавов? Как построить диаграмму состояния сплава?
3.Как называются и что характеризуют линии на диаграмме состояния?
4.Какой метод используется при построении диаграмм состояния?
5.Что представляет собой термопара?
6.Что такое пирометр?
7.Применение правила отрезков и правила фаз для анализа сплавов по диаграмме.
8.Особенности кристаллизации "чистых" металлов и сплавов эвтектического состава.
15
Лабораторная работа № 3 АНАЛИЗ ДИАГРАММЫ СОСТОЯНИЯ СПЛАВОВ
СИСТЕМЫ "ЖЕЛЕЗО - УГЛЕРОД" В РАВНОВЕСНОМ СОСТОЯНИИ
Цель работы: освоить методику проведения металлографического анализа, научиться определять основные фазы и структурные составляющие, изучить превращения, происходящие в сплавах системы "железо-углерод".
Оборудование и материалы:
1.Микроскоп металлографический.
2.Учебный стенд "Диаграмма состояния сплавов железо - углерод".
3.Набор образцов со структурами: феррита, перлита, цементита, ледебурита, пластинчатого графита, округлого графита, хлопьевидного графита.
4.Атлас структур железоуглеродистых сплавов.
Теоретические сведения
Микроанализ применяют для изучения внутреннего строения металлов и сплавов на оптическом микроскопе при увеличении от 50 до 1500 раз.
Для проведения микроисследования от изучаемой детали или заготовки отрезают образец, который специально обрабатывают для придания одной из его поверхностей прямолинейности и зеркального блеска. Образец, подготовленный к микроанализу, называют микрошлифом. Изготовление микрошлифа включает следующие операции: отрезку образца, его торцовку, шлифование и полирование.
Выявление структуры металлической основы шлифа после полирования осуществляется травлением его реактивом. Для сталей и чугуна чаще всего применяют 2...5% раствор азотной кислоты (НМО3) в этиловом спирте. Полированную поверхность шлифа погружают в реактив на 3...15 с или протирают ватой, смоченной в реактиве, до появления ровного матового оттенка без наличия каких-либо пятен. Затем шлиф промывают спиртом или водой и просушивают фильтровальной бумагой.
Известно, что любой металл или сплав является поликристаллическим телом, т. е. состоит из большого числа различно
16
ориентированных кристалликов или зерен. В результате неодинаковой степени травимости структурных составляющих на поверхности шлифа создается микрорельеф. Изучение протравленной поверхности шлифа под оптическим микроскопом позволяет увидеть микроструктуру металлической основы. Она обычно состоит из светлых (ферритных) и темных (перлитных) участков. Это объясняется неодинаковой степенью отражения света от структурных составляющих. Структура, растворившаяся на большую глубину, под микроскопом имеет темный цвет, так как дает больше рассеивающих лучей, структура же, растворившаяся меньше, за счет прямого отражения света имеет светлый цвет. Границы зерен будут видны в виде тонкой темной сетки.
1. Компоненты в железоуглеродистых сплавах
Железо и углерод – элементы полиморфные. Железо с температурой плавления 1539°С имеет две модификации – α иү.
Модификация α– Fe существует при температурах до 911°С и от 1392 до 1539 °С, имеет ОЦК решетку с периодом 0,286 нм (при 20-25°С). Важной особенностью α – Fe является его ферромагнетизм ниже температуры 768°С, называемой точкой Кюри.
Модификация γ – Fe существует в интервале температур от 911 до 1392°С, и имеет ГЦК решетку. Решетка ГЦК более компактна, чем ОЦК. В связи с этим при переходе α – Fe в γ – Fe объем железа уменьшается приблизительно на 1 %.
Углерод существует в двух модификациях: графита и ал-
маза.
При нормальных условиях стабилен графит, алмаз представляет собой его метастабильную модификацию. При высоких давлениях и температурах стабильным становится алмаз (это используют при получении синтетических алмазов).
2. Фазы в железоуглеродистых сплавах
Основными фазами в железоуглеродистых сплавах могут быть: жидкий раствор, феррит, аустенит, цементит и свободный углерод в виде графита.
Феррит – твердый раствор внедрения углерода в α-Fe. Предельная концентрация углерода составляет лишь 0,025. Феррит – мягкая, пластичная фаза со следующими механиче-
17
скими свойствами: в – 250 МПа; δ – 50 %; твердость – 80… 90 НВ.
Аустенит (обозначается буквой А) – твердый раствор внедрения углерода в γ-Fe. Он имеет ГЦК решетку. Растворимость углерода в γ-Fe значительно больше чем в феррите и достигает 2,14 % при температуре 1147 0С. Аустенит пластичен и прочнее феррита. Твердость аустенита (НВ 160 – 200) при 20… 25 °С. В углеродистых сталях аустенит устойчив до температу-
ры 7270 С.
Цементит (обозначается буквой Ц) – карбид железа (почти постоянного состава) Fе3С, содержит 6,67% С и имеет сложную ромбическую решетку. При нормальных условиях цементит тверд (800 НВ) и хрупок. Он слабо ферромагнитен и теряет ферромагнетизм при 210°С. Температуру плавления цементита трудно определить в связи с его распадом при нагреве. При нагреве лазерным лучом она установлена равной 1260°С.
Графит – углерод, выделяющийся в железоуглеродистых сплавах в свободном состоянии. Имеет гексагональную кристаллическую решетку. Графит электропроводен, химически стоек, имеет низкую прочность.
3.Структурные составляющие в железоуглеродистых сплавах
Перлит – механическая смесь феррита и цемента. Образуется при вторичной кристаллизации из аустенита. Содержание углерода в перлите составляет 0,83%.
Ледебурит - механическая смесь аустенита и цементита или перлита и цементита (ниже температуры 7270С). Образуется из жидкого сплава. Содержание углерода составляет 4,3%.
Микроструктуры основных фаз и структурных составляющих представлены на рисунке 1.
4.Диаграмма состояния железоуглеродистых сплавов
Среди диаграмм состояния металлических сплавов самое
важное значение имеет диаграмма состояния системы Fе – С. Это объясняется тем, что в технике наиболее широко применяют железоуглеродистые сплавы. Имеются две диаграммы состояния железоуглеродистых сплавов: метастабильная, харак-
18
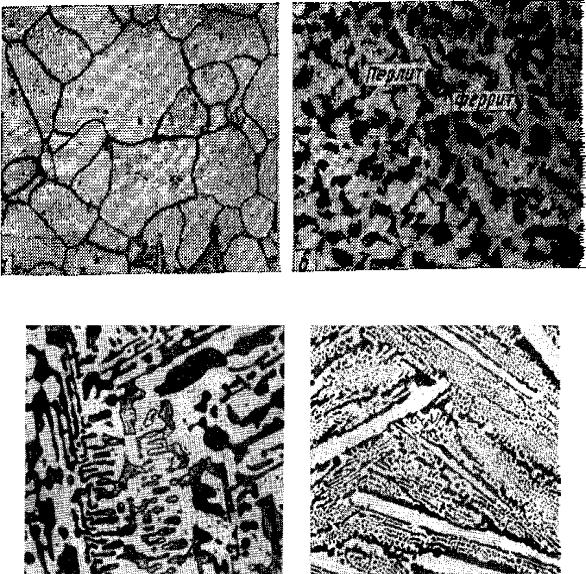
теризующая превращения в системе Fе–Fе3С (цементит), и стабильная, характеризующая превращение в системе Fе – графит. Диаграмма приведена на рис. 2. Метастабильная диаграмма показана сплошными линиями, а стабильная диаграмма – штриховыми линиями.
Система Fе – графит является более стабильной, чем система Fе–Fе3С, на это указывает тот факт, что при нагреве до высоких температур цементит распадается на железо и графит, т.е. переходит в более стабильное состояние.
а) |
б) |
в) |
г) |
19
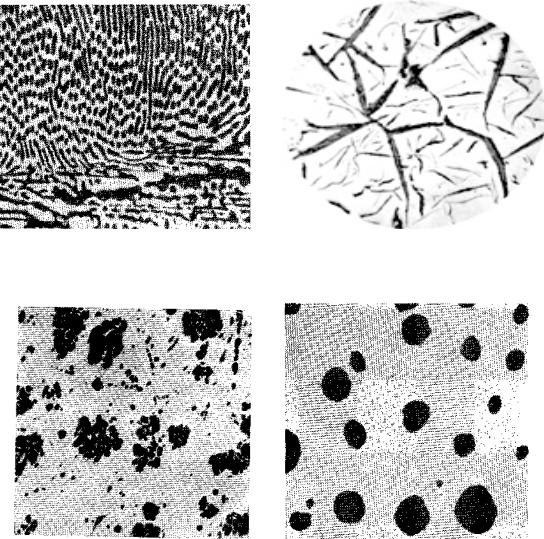
д) |
е) |
ж ) з)
Рис. 1. Микроструктура фаз и структурных составляющих:
а) структура феррита; б) структура феррита и перлита; в) структура перлита и ледебурита; г) структура ледебурита и цементита первичного (светлые полосы); д) структура ледебурита; е) графит пластинчатый; ж) графит хлопьевидный; з) графит округлый.
Анализ диаграммы проводится по упрощенной диаграмме без верхнего левого угла. При анализе рассматриваются линии диаграммы и критические точки. Основные фазовые превращения по линиям диаграммы приведены в таблице 1.
Для всех превращений, происходящих в железоуглеродистых сплавах, может быть применено правило фаз (правило Гиббса): С = К + 1 – Ф.
Выше линии АС все сплавы находятся в жидком состоянии, и число степеней свободы С = К – Ф + 1 = 2 – 1 + 1= 2 . Это значит, что сплавы можно нагревать и охлаждать, менять
20