
методичка
.pdfприменяются следующие виды отпуска:
-низкий отпуск (150...300°С) применяется для изделий, где требуется высокая твердость 56-64НRС и износостойкость (инструмент, цементируемые детали, детали, работающие на износ). Охлаждение после отпуска на воздухе. Структура - отпущенный мартенсит;
-средний отпуск (350...500 °С) обеспечивает высокую твердость 40-50НRС и высокий предел упругости. Применяется для рессор и пружин. Структура – троостит;
-высокий отпуск (500...650 °С) применяется для деталей,
вкоторых требуется сочетание высокой вязкости и прочности с твердостью 20-35 НRС (валы, оси, шатуны, ответственные крепежные детали и др.).
Продолжительность выдержки при отпуске выбирается:
-при температурах отпуска ниже 300° С – 2 часа + 1 мин на 1 мм условной толщины;
-при 300-400 ° С – 20 мин + 1 мин на 1 мм условной тол-
щины;
-при температуре отпуска свыше 400 ° С – 10 мин + 1 мин на 1 мм условной толщины.
3. Проведение поверхностного упрочнения
Многие детали согласно техническим требованиям, должны иметь высокую твердость на поверхности и вязкую сердцевину (коленчатые валы, распределительные валы, шестерни, поршневые пальцы и ряд других деталей). Закалкой и отпуском получить указанные свойства не представляется возможным. Для таких деталей необходимо проводить поверхностное упрочнение. Наиболее распространенными видами поверхностного упрочнения являются:
-цементация – применяется для деталей из низкоуглеродистых сталей;
-поверхностная закалка – применяется для деталей из среднеуглеродистых и высокоуглеродистых сталей.
3. 1. Проведение цементации
Цементация – это процесс диффузионного насыщения поверхностного слоя детали углеродом. В процессе цементации содержание углерода в поверхностном слое повышается в сред-
51
нем до 1%. Глубина слоя изменяется от 0, 5 до 2, 5 мм. Цементацию рекомендуется проводить при температуре
920…950 0 С (оптимальная температура).
Время выдержки при цементации выбирают по таблицам или графику, в зависимости от температуры цементации и глубины цементованного слоя.
После цементации проводят закалку и низкий отпуск при температуре 150…300 ° С.
3. 2. Проведение поверхностной закалки токами высокой частоты
Детали, изготовленные из среднеуглеродистых сталей (0,30…0,50% С) ивысокоуглеродистых сталей (свыше 0,50% С) упрочняют поверхностной закалкой. Нагрев упрочняемой части проводят с помощью токов высокой частоты на глубину 3...5 мм или с помощью пламени газовой горелки. Температура нагрева выбирается более высокая, чем при объемной закалке:
tзакалки= А3 + (90…100)оС – для доэвтектоидных сталей
tзакалки = А1 + (90…100)оС – для заэвтектоидных сталей
После закалки проводится низкий отпуск при температуре
180…200°С.
Для измельчения структуры перед поверхностной закалкой рекомендуется проводить нормализацию.
4. Заполнение карты технологического процесса термической обработки
4.1.На эскизе или чертеже детали допускается указывать не все размеры, а только те, которые необходимы для выполнения термической обработки. К таким размерам относятся габаритные размеры, размеры, ограничивающие участок местной термической обработки; размеры, которые могут изменяться в результате коробления при термической обработке.
4.2.Графы технологической карты заполняются следующим образом:
4.2.1.В графе наименование и содержание операций в последовательности перечисляются операции технологического
52
процесса.
Например: закалка, отпуск, очистка от окалины, зачистка площадки под замер твердости.
4.2.2.В графе "Оборудование" указывается тип оборудо-
вания.
4.2.3.В графе "Приспособление, инструмент" указываются: корзина, зажимы и т.д.
4.2.4.В графе "Среда" указывается среда нагрева и охлаждения. Например: масло, вода и т.д.
4.2.5.Остальные графы карты заполняются ранее рассчитанными данными.
Лабораторная работа № 9 ИЗУЧЕНИЕ СТРУКТУР И СВОЙСТВ ЦВЕТНЫХ
СПЛАВОВ
Цель работы: ознакомиться со структурами и свойствами основных сплавов цветных металлов, применяемых в машиностроении. Изучить свойства цветных сплавов, маркировки и их применение.
Оборудование и материалы:
1.Микроскопы.
2.Коллекция микрошлифов (латуни, бронзы, силумины, дуралюмины и подшипниковые сплавы).
3.Плакаты: "Диаграмма AL – Si", "Диаграмма AL – Cu", "Диаграмма Cu - Zn", Механические свойства цветных сплавов."
4.Альбом микроструктур.
Теоретические сведения:
К цветным сплавам, наиболее широко применяемым в машинах для сельскохозяйственного производства, относятся сплавы на основе меди, алюминия, магния и антифрикционные подшипниковые на основе алюминия, олова, свинца и других элементов.
1. Медные сплавы
Медь обладает высокой коррозионной стойкостью, малым электросопротивлением. По электрической проводимости и теплопроводности медь занимает второе место после серебра. Последнее объясняет, почему технически чистую медь широко
53
используют как проводниковый материал (проволока, ленты, шины). Она применяется для проводников электрического тока
иразличных теплообменников, водоохлаждаемых изложниц, поддонов, кристаллизаторов. Недостатки меди - невысокая прочность, плохая обрабатываемость резанием и низкая жидкотекучесть.
Сохраняя положительные качества меди (высокие теплопроводность и электропроводимость, коррозионную стойкость
ит.д.), ее сплавы обладают хорошими механическими, технологическими и антифрикционными свойствами.
По прочности медные сплавы уступают сталям. Временное сопротивление большинства сплавов меди лежит в интервале 300 - 500 МПа, что соответствует свойствам низкоуглеродистых нелегированных сталей в нормализованном состоянии. И только временное сопротивление наиболее прочных бериллиевых бронз после закалки и старения находится на уровне среднеуглеродистых легированных сталей, подвергнутых термическому улучшению (1100... 1200 МПа).
По технологическим свойствам медные сплавы подразделяют на деформируемые (обрабатываемые давлением) и литейные, по способности упрочняться с помощью термической обработки – на упрочняемые и не
упрочняемые термической обработкой. По химическому составу медные сплавы подразделяют на две основные группы: латуни и бронзы.
Медные сплавы маркируют по химическому составу, используя буквы для обозначения элементов и числа для указания их массовых долей. В медных сплавах (так же, как в алюминиевых и магниевых) буквенные обозначения отличаются от обозначений, принятых для сталей. Обозначение легирующих элементов цветных сплавов:
алюминий – А; бериллий – Б; железо – Ж; кремний – К; медь – М; магний – Мг; мышьяк – Мш; никель – Н; олово – О; свинец – С; серебро – Ср; сурьма – Су; фосфор – Ф; цинк – Ц; цирконий – Цr; хром – X; марганец – Мц.
Основную массу медных сплавов составляют латуни (сплавы меди с цинком), в которых главным легирующим элементом является цинк. По содержанию цинка латуни делятся на однофазные (содержащие до 39% цинка) и двухфазные (содержащие более 39% цинка).
54
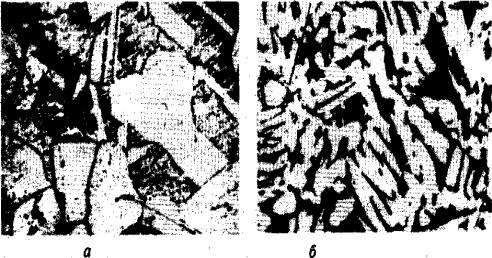
Медь с цинком образует твердый раствор с предельной концентрацией цинка 39 % (рис. 2). При большем содержании цинка образуется электронное соединение (химическое соединение) β-фаза с кристаллической решеткой ОЦК. При 454 – 468 °С (штриховая линия на диаграмме) наступает упорядочение β– фазы (образуется β'–фаза ), что сопровождается значительным повышением ёе твердости и хрупкости.
Однофазные латуни имеют структуру – твердого раствора (α-фаза). Они обладают высокой пластичностью и хорошо деформируются и в холодном и в горячем состояниях.
Двухфазные латуни имеют структуру (α + β) – фаз. Они обладают более высокой твердостью и прочностью, но более низкой пластичностью. Двухфазные латуни хорошо деформируются только в горячем состоянии.
Рис. 1. Микроструктуры латуней:
а - однофазной; б – двухфазной (темная – фаза, светлая – а-фаза)
Когда латунь имеет структуру а-твердого раствора, увеличение содержания цинка вызывает повышение ее прочности и пластичности (рис. 2. б).
Появление β'-фазы сопровождается резким снижением пластичности, прочность продолжает повышаться при увеличении цинка до 45 %, пока латунь находится в двухфазном состоянии. Переход латуни в однофазное состояние со структурой β'-фазы вызывает резкое снижение прочности. Практическое значение имеют латуни, содержащие до 46 % цинка.
55
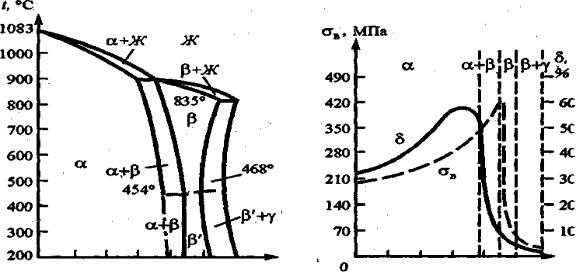
а ) б)
Рис. 2. Диаграмма состояния сплавов "Медь - Цинк" (а) и график изменения механических свойств латуней (б).
Повышение содержания цинка удешевляет латуни, улучшает их обрабатываемость резанием, способность прирабатываться и противостоять износу. Вместе с тем снижается теплопроводность и электрическая проводимость, которые составляют 20 - 50 % от характеристик меди.
Примеси повышают твердость и снижают пластичность латуней. Особенно неблагоприятно действуют свинец и висмут, которые в однофазных латунях вызывают красноломкость.
Однофазные латуни в основном выпускают в виде холоднокатаных полуфабрикатов: полос, лент, проволоки, листов, из которых изготавливают детали методом глубокой вытяжки (радиаторные трубки, снарядные гильзы, сильфоны, трубопроводы).
Латуни маркируют буквой Л. В деформируемых латунях, не содержащих кроме меди и цинка других элементов, за буквой Л ставится число, показывающее среднее содержание меди. В многокомпонентных латунях после Л ставятся буквы – символы элементов, а затем числа, указывающие содержание меди и каждого легирующего элемента. Например, латунь Л 68 содержит 68% Си, латунь ЛАН59-3-2 содержит 59 % Си, 3 % А1, 2 % Ni (остальное Zn). В марках литейных латуней указывается содержание цинка, а количество каждого легирующего элемента ставится непосредственно за буквой, обозначающей его. Например, латунь ЛЦ40МцЗА содержит 40 % Zn, 3 % Мn и 1% Al.
Из однофазных латуней Л90 изготавливают трубки водя-
56
ного и масляного радиаторов, Л80 – бачки радиаторов системы охлаждения. Из двухфазных латуней ЛЦ40С1 – направляющие втулки клапанов.
По технологическому признаку латуни делятся на деформируемые (листы, ленты, полосы и др.) и литейные (фасонные отливки).
Другой группой сплавов на медной основе являются бронзы. В качестве легирующих элементов в состав бронз могут входить практически все элементы (олово, алюминий, бериллий, кремний, свинец и др.). Бронзы обладают высокими механическими и антифрикционными свойствами, коррозионной устойчивостью, хорошими литейными свойствами и обрабатываемость резанием. Из бронз изготавливают детали, требующие антифрикционные свойства, высокую коррозионную стойкость. Например, Бр О 4 Ц4 С 2,5 идет на изготовление втулок шатунов и поворотного кулака; Бр К3Н для пружин топливного насоса.
Бронзы обозначают буквами Бр, за которыми ставятся буквы и числа: БрО10; Бр А5; Бр Б2; Бр К3; Бр ОЦС 5-5-5; Бр А9Ж4; Бр ОЦ 4-3.
Вмарках деформируемых бронз сначала помещают буквы
–символы легирующих элементов, а затем числа, указывающие их содержание. Например, БрАЖ 9-4 содержит 9% А1, 4% Fе, остальное – Сu.
Вмарках литейных бронз после каждой буквы указывается содержание этого легирующего элемента. Например, БрОбЦбСЗ содержит 6 % 8п, 6 % 2п, 3 % РЬ, остальное — Сu.
По химическому составу бронзы делятся на оловянные, алюминиевые, кремнистые, бериллиевые и другие. По структуре бронзы бывают однофазные и двухфазные.
Оловянные бронзы
Однофазные бронзы содержат до 6 – 8 % олова. Структура таких бронз представляет α–твердый раствор. Двухфазные бронзы содержат олова более 6 – 8 %. Структура двухфазных бронз содержит эвтектоид (α + δ). Появление δ–фазы в структуре бронз вызывает резкое снижение их вязкости и пластичности. Практическое значение имеют бронзы, содержащие до 10 % олова (Sn). По технологическим свойствам бронзы делятся на деформируемые и литейные.
57
Кремнистые бронзы
Бронзы содержат до 3 % кремния (Si) и имеют однофазную структуру. Кремнистые бронзы характеризуются хорошими механическими, упругими и антифрикционными свойствами. Кремнистые бронзы выпускаются в виде лент, полос, прутков и проволоки.
Алюминиевые бронзы
Бронзы, содержащие до 4 - 5 % алюминия (Al), имеют однофазную структуру и характеризуются высокой пластичностью.
С увеличением содержания алюминия (свыше 4…5 %) пластичность резко падает, а прочность продолжает расти. Наибольшую прочность имеют бронзы, содержащие 10 – 11 % алюминия. Свойства алюминиевых бронз значительно улучшаются при модифицировании их железом, никелем, марганцем.
Бериллиевые бронзы
Бронзы содержат в основном 1,6 – 2,5 % бериллия (Be). По структуре они двухфазные – (α + γ) фазы. В бронзах, содержащих бериллия в интервале 1,6…2,0 % временное сопротивление(σв) резко увеличивается. При содержании бериллия более 2,0 % временное сопротивление повышается незначительно, а пластичность становится очень низкой. Бериллиевые бронзы обладают высокими механическими свойствами (в частности, упругими), стойкие против коррозии, хорошо свариваются. Бронзы упрочняются закалкой и старением. Бериллиевые бронзы выпускаются в виде лент, полос и проволоки.
2. Алюминиевые сплавы
Алюминий характеризуется низкой плотностью, высокой теплопроводностью и электрической проводимостью, высокой пластичностью. Алюминий слабо подвергается коррозии в целом в ряде агрессивных сред. Примеси ухудшают указанные свойства алюминия.
Технический алюминий применяют для электротехнических целей, изготовления трубопроводов, цистерн для молока, посуды, строительных конструкций.
В машиностроении применяются алюминиевые сплавы, так как чистый алюминий имеет низкую прочность. Прочность алюминиевых сплавов достигает 500 – 700 МПа.
58
Сплавы на алюминиевой основе по технологическим свойствам делятся на три группы:
–литейные сплавы;
–деформируемые сплавы;
–сплавы, получаемые методом порошковой металлургии (САП – спечённые алюминиевые порошки; САС – спечённые алюминиевые сплавы).
Литейные сплавы
Требования к литейным сплавам: высокая жидкотекучесть, малая усадка, низкая склонность к образованию горячих трещин. Указанные свойства наиболее полно проявляются в сплавах эвтектического состава (или близких к нему). Литейные алюминиевые сплавы классифицируются по химическому составу: АL – Si; АL – Сu; АL – Мg.
Лучшими литейными алюминиевыми сплавами являются сплавы АL – Si (Si – 8…13 %). Такие сплавы называют силуминами. Недостатками силуминов являются повышенная хрупкость и невозможность упрочнить их термической обработкой. Единственным способом упрочнения таких сплавов является модифицирование сплавов натрием, что дает измельчение структуры. Силумины (АL – Si) используются для отливок сложных конфигураций неответственного назначения.
Для ответственных деталей используют легированные силумины (АL – Si + легирующей элемент). Для легирования используют – медь, магний, марганец, титан и другие элементы. Легированные силумины используют для получения средних и крупных отливок ответственного назначения: корпусов компрессоров, картеров, головок цилиндров и т.д. Легированные силумины упрочняются термической обработкой (закалка и последующие старение).
Пример маркировки литейных сплавов:
АК 12 (алюминиевый сплав – Si – 12 %); АК8М (алюминиевый сплав – Si – 8 %, Си – 1 %); АМг 10 (алюминиевый сплав – Мg – 10 %); АМ5 (алюминиевый сплав – Сu – 5 %).
Примечание: согласно ранее существующей маркировке литейные алюминиевые сплавы маркировались АЛ 2; АЛ 4; АЛ 20 и т.д. (АЛ – алюминий литейный; число – условный номер сплава).
Сплавы системы АL – Сu (АМ 4,5; АМ 5) имеют высокую
59
прочность при обычных и повышенных температурах; сплавы хорошо свариваются и обрабатываются резанием. Сплавы имеют низкие литейные свойства. Литейные и механические свойства сплавов системы АL – Сu улучшаются при легировании сплавов титаном и марганцем. Сплавы используются для деталей, работающих при температурах до 300 0С.
Сплавы системы АL – Мg (АМг; АМг 10) обладают высокой коррозионной стойкостью, прочностью, вязкостью и хорошо обрабатываются резанием. Сплавы обладают невысокими литейными свойствами. Наилучшие механические свойства сплавы системы АL – Мg приобретают после закалки от 5300С.
Деформируемые алюминиевые сплавы
Деформируемые сплавы должны обладать высокой пластичностью. Структура деформируемых сплавов должна состоять из твердых растворов.
Деформируемые сплавы подразделяются на:
–сплавы, не упрочняемые термической обработкой;
–сплавы,упрочняемые термической обработкой.
Ксплавам, не упрочняемым термической обработкой, относятся сплавы AL – Mn (АМц) и AL – Mg (АМг2; АМг6) (сварные резервуары, трубопроводы, заклепки, баки для масла
ибензина и т.п.).
Ксплавам, упрочняемым термической обработкой от-
носятся сплавы нормальной прочности (до 550 МПа) и высокопрочные. Сплавы характеризуются хорошим сочетанием прочности и пластичности.
Сплавы нормальной прочности – AL – Cu – Mg (дуралюмины), высокопрочные сплавы – AL – Zn – Mg – Cu.
Дуралюмины маркируются буквой Д и числом, а высокопрочные сплавы маркируются буквой В и числом. Число – условный (порядковый) номер сплава.
Пример маркировки: Д1, Д16, В95.
Упрочнение дуралюминов заключается в закалке с последующим старением.
Закалку проводят с температуры 490 – 510°С. Охлаждение проводят в воде. После закалки структура сплава состоит из пересыщенного твердого раствора и характеризуется высокой пластичностью и низкой твердостью. Старение сплава позволяет повысить прочность и твердость сплава. При старении про-
60