
TI-101-P-Gl10-374-2010_s_izm_1-7
.pdf
© (Г) ТИ 101-П ГЛ10-374 2010
стр. 49 из 180
5.14.11 Футеровка печи
5.14.11.1Футеровка печи выполняется с плотных огнеупорных бетонов, изоляционных бетонов, торкрет-масс, изоляционного кирпича, изоляционных плит, волокнистых материалов фирмы «Калдерис».
5.14.11.2Схема футеровки по зонам и элементам печи, а также марки материалов приведены в таблице 5.19.
Таблица 5.19 – Футеровка печи № 4
№ |
Элемент печи |
Качество материала |
Марка материала |
Толщина фу- |
|
теровки, мм |
|||||
|
|
|
|
||
1 |
Торцевая стена загруз- |
Огнеупорный кирпич |
A35 T |
345 |
|
|
ки (верх) |
||||
|
|
|
|
||
|
|
|
|
|
|
|
Торцевая стена загруз- |
Огнеупорный бетон |
Refrabloc ZC |
235 |
|
посада) |
ки (низ) |
Изоляционные плиты |
Calcium silicate |
125 |
|
|
Итого |
|
360 |
||
Выход дыма со свода в |
Огнеупорный бетон |
Refrabloc ZC |
200 |
||
|
|
|
|
||
от |
дымосборник |
Изоляционные плиты |
Calcium silicat |
100 |
|
|
Итого |
|
300 |
||
мм |
|
|
|||
Свод |
Огнеупорный бетон |
Refrabloc ZC |
185 |
||
483 |
|||||
|
Огнеупорный бетон |
Kerlite 120L |
65 |
||
(20 |
|
Изоляционные плиты |
Calcium silicatе |
50 |
|
|
Итого |
|
300 |
||
зона |
|
|
|||
Подина (20220 м от |
Базовая засыпка |
Grec magn tape |
50 |
||
посада) |
Огнеупорный бетон |
Kerlite 130L |
130 |
||
Рекуперативная |
|||||
|
Огнеупорный бетон |
Refrabloc ZC |
100 |
||
|
Изоляционные плиты |
Calcium silicat |
125 |
||
|
Итого |
|
405 |
||
Боковые стены |
Огнеупорный бетон |
Kerlite 130 М |
190 |
||
|
Огнеупорный изоляционный |
Isom 23 A |
|
||
|
кирпич |
|
115 |
||
|
|
|
|||
|
|
Изоляционные плиты |
Calcium silicatе |
100 |
|
|
|
Итого |
|
405 |
|
2 |
Свод |
Огнеупорный бетон |
Phlocast M 25/30 SR |
185 |
|
|
|
Изоляционный бетон |
Kerlite 130L |
65 |
|
|
|
Изоляционные плиты |
Calcium silicat |
50 |
|
|
|
Итого |
|
300 |
|
|
|
|
|
|
|
|
Боковые стены |
Огнеупорный бетон |
Phlocast M 25/30 SR |
195 |
|
|
|
Изоляционный кирпич |
Isom 26 A |
115 |
|
зоны |
|
Изоляционный войлок |
Superwool 607 HT |
25 |
|
|
Изоляционные плиты |
Calcium silicat |
100 |
||
|
Итого |
|
435 |
||
Нагревательные |
|
|
|||
Подина |
Базовая засыпка |
Grec magn tape |
50 |
||
|
Огнеупорный бетон |
Phlocast M25Р SR |
100 |
||
|
Огнеупорный бетон |
Kerlite 140L |
130 |
||
|
Изоляционные плиты |
Calcium silicat |
125 |
||
|
Итого |
|
405 |
||
Стена над окном раз- |
Огнеупорный бетон |
Phlocast M30 SR |
225 |
||
|
|||||
|
грузки |
Изоляционное волокно |
Сeramic Fibre |
25 |
|
|
|
Изоляционные плиты |
Calcium silicat |
50 |
|
|
|
Итого |
|
300 |
|
|
Торцевая стена раз- |
Огнеупорный кирпич |
A35 T |
345 |
|
|
грузки (верх) |
|
|
|
|
|
|
|
|
|

© (Г) ТИ 101-П ГЛ10-374 2010
стр. 50 из 180
|
Торцевая стена раз- |
Огнеупорный бетон |
Phiocast M30 SR |
270 |
|
|
грузки (низ) |
Изоляционный кирпич |
IR 26/145 |
115 |
|
|
|
Изоляционный кирпич |
IR 23/125 |
65 |
|
|
|
Изоляционные плиты |
Calcium silicat |
50 |
|
|
|
Итого |
|
500 |
|
|
|
|
|
|
|
3 |
Загрузочное окно |
Огнеупорный бетон |
Kerlite 130М |
150 |
|
|
|
Изоляционные плиты |
Calcium silicat |
50 |
|
дверцыи |
|
Итого |
|
200 |
|
|
Итого |
|
200 |
||
|
Разгрузочное окно |
Огнеупорный бетон |
Kerlite 140М |
150 |
|
|
|
Изоляционные плиты |
Calcium silicat |
50 |
|
Окна |
|
|
|
|
|
Люки и дверцы |
Огнеупорный бетон |
Kerlite 140М |
150 |
||
|
Изоляционные плиты |
Calcium silicat |
50 |
||
|
|
Итого |
|
200 |
|
|
|
|
|
|
|
|
Балки и стояки 20633 |
Огнеупорный бетон |
Phlox 1400 С SR |
50 |
|
4 |
мм от посада |
Изоляционное волокно |
Сeramic Fibre |
25 |
|
|
|
Итого |
|
75 |
|
|
Балки и стояки 30068 |
Огнеупорный бетон |
Phlox1500 С SR |
50 |
|
5 |
мм к выдаче |
Изоляционное волокно |
Сeramic Fibre |
25 |
|
|
|
Итого |
|
75 |
|
|
Дымосборник над сво- |
Огнеупорный бетон (тор- |
Kеrlite 120MR |
145 |
|
6 |
дом |
крет) |
|
|
|
|
Изоляционные плиты |
Calcium silicat |
75 |
||
|
|
||||
|
|
Итого |
|
220 |
|
|
Дымовой боров (от оси |
Огнеупорный бетон |
Plicast Verilite C/G |
75 |
|
7 |
опускного борова |
(торкрет) |
|
|
|
24730 мм ) |
Изоляционные плиты |
Calcium silicat |
50 |
||
|
|||||
|
|
Итого |
|
125 |
|
8 |
Дымовой боров (до ды- |
Огнеупорный бетон (тор- |
Plicast Verilite C/G |
60 |
|
мососа 111950 мм ) |
крет) |
|
|
||
|
|
|
|||
|
Воздухопроводы го- |
Огнеупорный бетон |
Plicast Verilite C/G |
105 |
|
9 |
рячего воздуха Ø1422, |
(торкрет) |
|
|
|
2500, 3000 мм |
Изоляционные плиты |
Calcium silicat |
75 |
||
|
|||||
|
|
Итого |
|
180 |
5.14.12Дымовой тракт
5.14.12.1Дымовые газы удаляются через дымоотвод в своде с загрузочной стороны печи, затем направляются в рекуператор.
5.14.12.2Шибер расположен в дымоспаде после рекуператора и встроен в контур управления давлением в печи. Он представляет собой четырѐх лопастную заслонку и приводится в действие пневматическим приводом.
5.14.12.3Перед шибером установлена система подачи холодного воздуха для управления давлением в печи на случай ограниченного режима эксплуатации.
5.14.12.4Отвод дымовых газов на дымовую трубу № 2 осуществляется 2-
мя дымососам

© (Г) ТИ 101-П ГЛ10-374 2010
стр. 51 из 180
6 Прокатка и смотка полос на стане «2000» г.п. © (Г)
6.1 Настройка стана © (Г)
Настройка стана «2000» горячей прокатки состоит из следующих последовательных операций:
установки уровня верхней образующей нижнего рабочего валка на определенное превышение над уровнем рольганга;
установки верхней образующей нижнего опорного валка в горизонтальное положение;
выверка горизонтальных валков на параллельность;
калибровки валков;
установки зазоров между горизонтальными и вертикальными валками,
атакже скоростей вращения валков;
установка ширины раствора направляющих линеек;
настройки приборов (толщиномеров, шириномеров).
6.1.1Установка уровня прокатки © (Г)
6.1.1.1 При установке уровня верхней образующей нижнего рабочего валка необходимо учесть: нормальное превышение уровня нижнего рабочего валка над уровнем рольганга или проводкой (осью прокатки) должно быть в пределах:
№1–6 клеть |
|
от 10 до 50 мм; |
|
||
№7–13клеть |
|
от 10 до 25 мм. |
|
||
6.1.1.2 Уровень прокатки поддерживается установкой прокладок под по- |
|||||
душки нижних опорных валков. Толщина прокладок H, мм, определяется по |
|
||||
формуле: |
|
|
ДСТ Д НОВ dН dСР.З , |
|
|
|
Η |
(1) |
|||
|
|
|
2 |
|
|
где ДСТ |
– диаметр вываливаемого опорного валка, мм; |
|
|||
ДНОВ – диаметр заваливаемого опорного валка, мм; |
|
||||
dН |
– максимальный диаметр рабочего валка, мм; |
|
|||
dСР.З |
– средний диаметр заваливаемых рабочих валков, мм. |
|
|||
Причем, если значение |
ДСТ ДНОВ |
получается со знаком «+», то необхо- |
|
||
|
2 |
|
|||
|
|
|
|
|
димо добавлять прокладки на это значение, и наоборот.
6.1.2Выверка рабочих валков на параллельность © (Г)
6.1.2.1Выверка рабочих валков на параллельность производится после каждой их перевалки, а также после каждого сбоя работы нажимных винтов путем сближения вращающихся валков до усилия 50 МН (500 тс) для клети «ДУО»
и15 МН (1500 тс) – для остальных клетей устранения разности усилий под правым и левым нажимными винтами.
6.1.2.2Перед сближением рабочих валков старший вальцовщик обязан убедиться в отсутствии прокладок и посторонних предметов между подушками

© (Г) ТИ 101-П ГЛ10-374 2010
стр. 52 из 180
рабочих валков, а также между подушками нижнего опорного и нижнего рабочего валка.
6.1.2.3Старший вальцовщик при сближении валков обязан установить визуальный контроль за их сближением до соприкосновения.
6.1.2.4При неработающих месдозах на клетях черновой группы валки сближаются до забоя и далее разводятся на расстояние 30–50 мм. С помощью линейки-кронциркуля измеряются зазоры на расстоянии 250–300 мм от каждого края бочки, и далее нажимными винтами устраняется перекос валков. При этом допустимый перекос по сторонам для клетей №1–6 не должен превышать 0,1 мм.
6.1.2.5На чистовой группе клетей, при неработающих месдозах, выверка валков на параллельность осуществляется по датчикам давления ГНУ*. При неработающих ГНУ, выверка валков на параллельность осуществляется по месдозам (Приложение Е.4), при этом цилиндры ГНУ должны быть слиты
6.1.2.6Перекос валков устраняется перемещением нажимных винтов на расстояние в 1,8–2 раза большее значения перекоса и осуществляется от кнопки «перекос» на пульте управления соответствующей клети. При этом пара нажимных винтов перемещается во взаимно противоположных направлениях и показания цифровой индикации на продуктиметрах ЭПС-1 каждого винта должны изменяться на половину значения перекоса.
6.1.2.7После перевалки опорных валков при работающих месдозах и датчиках давления ГНУ настройка чистовой группы осуществляется следующим образом:
6.1.2.7.1 Сблизить валки до появления нагрузки 2–4 МН (200–400 тс). 6.1.2.7.2 Запустить клеть.
6.1.2.7.3 Нажимными винтами установить усилие 15 МН (1500 тс). 6.1.2.7.4 Обнулить положение нажимных винтов.
6.1.2.7.5 Выставить зазор между валками 6 мм.
6.1.2.7.6 В зазор между валками, на расстоянии 250–300 мм от краев бочки, одновременно пропустить два прутка мягкой проволоки диаметром 6 мм из одного бунта.
6.1.2.7.7 Измерить толщину проволок микрометром и, если есть перекос, устранить его. Допустимый перекос валков по сторонам:
для клетей №7—10 – 0,05 мм;
для клетей №11—13 – 0,03 мм.
6.1.2.7.8Если разность толщины проволоки составляет 0,5 мм и больше, то после устранения перекоса нажимными винтами повторить операции, описанные
впунктах 6.1.2.6.6 и 6.1.2.6.7.
6.1.2.7.9Нажимными винтами установить необходимый зазор.
6.1.2.8 В случае перевалки только рабочих валков прокатка и обжатие прутков не обязательны.
* Датчики давления ГНУ входят в измерительную систему ASEA

© (Г) ТИ 101-П ГЛ10-374 2010
стр. 53 из 180
6.1.3Калибровка валков © (Г)
Существует 2 режима калибровки: ручной и автоматический. Режимы выбираются с экрана на «КАЛИБР» на «NEMATRONE».
6.1.3.1Ручной режим.
Оператор берет все функции отбоя нуля на себя. Опускает рабочий валок до забоя, запускает клеть, создает усилие 15 МПа (1500 тс), выбирает перекос и нажимает мерцающую кнопку «КАЛИБР». В графе «ПОЛОЖЕНИЕ ВИНТОВ» появляется 0.00., в графе калибровка появляется надпись «НУЛЬ», кнопка «КАЛИБР» гаснет. Оператор обнуляет показания продуктимеров.
6.1.3.2 Автоматический режим.
Этот режим производится в два этапа:
6.1.3.2.1Оператор нажимает мерцающую кнопку «КАЛИБР». Верхний валок с первоначального значения автоматически опускается до создания усилия 4 МН (400 тс), выбирается перекос. Кнопка горит белым цветом. После этого оператор должен запустить клеть на скорость не менее 0,5 м/с.
6.1.3.2.2Оператор нажимает еще раз кнопку «КАЛИБР». Валок начинает двигаться вниз, создает давление 1500 тонн и выбирает оставшийся перекос. По достижении давления 1500 тонн система ждет прохождения двух оборотов опорного валка, после чего процесс калибровки заканчивается. В графе «ПОЛОЖЕНИЕ ВИНТОВ» появляется 0.00., в графе «КАЛИБРОВКА» появляется надпись «НУЛЬ», кнопка «КАЛИБР» гаснет.
6.1.3.3 Калибровка горизонтальных клетей черновой группы.
6.1.3.3.1 Ручной режим калибровки.
6.1.3.3.1.1Переключить «руч/позиц» установить в положение ручное регу-
лирование.
6.1.3.3.1.2С помощью джойстика установить суммарное усилие 15 МН (1500 тс) для клетей 2,3,4,5,6 и 5 МН (500 тс) – для 1-й клети.
6.1.3.3.1.3Перекос по давлению, который может возникнуть при ручной калибровке, устраняется с помощью кнопок перекоса.
6.1.3.3.1.4Переключатель «РУЧ/ПОЗИЦ» установить в положение «РУЧ», кратковременно нажать кнопку «сельсин/калибр», при этом загораются обе ее половины и обнуляются позиция на дисплейных линейках. После этого необходимо продуктимеры установить на 0000.
6.1.3.3.2 Автоматический режим калибровки.
6.1.3.3.2.1Калибровка в автоматическом режиме может начаться только при вращающейся клети, при включенном питании месдоз при отсутствии металла в клети и если клеть не в забое (суммарное усилие меньше 1 МН (100 тс).
6.1.3.3.2.2Переключатель «РУЧ/ПОЗИЦ» установить в положение
«ПОЗИЦ».
6.1.3.3.2.3Нажать кнопку «СЕЛЬСИН/КАЛИБР». При этом нажимные винты идут вниз на большой скорости. При усилии 1 МН (100 тс) винты переходят на малую скорость. При наличии перекоса по усилию более 0,25 МН (25 тс) происходит выравнивание усилий путем подъѐма винта, который давит больше.

© (Г) ТИ 101-П ГЛ10-374 2010
стр. 54 из 180
6.1.3.3.2.4При достижении суммарного усилия 15 МН (1500 тс) для клетей №2–6 и 5 МН (500 тс) для 1-й клети процесс калибровки заканчивается. Гаснут обе половины кнопки «СЕЛЬСИН/КАЛИБР». Позиция нажимных винтов на дисплейных линейках обнуляется (показания 0000).
6.1.3.3.2.5Процесс калибровки можно прервать в любой момент джойстиком или переключателем «РУЧ/ПОЗИЦ».
6.1.3.3.3Искусственная калибровка горизонтальных клетей при неработающих месдозах.
Вальцовщик измеряет раствор горизонтальной клети справа и слева. Сменный работник службы АСУ ТП вводит в контроллеры полученные результаты измерений, увеличенные на 3 мм (растяжение пружины клети).
6.1.3.3.4Вертикальные клети и направляющие линейки.
6.1.3.3.4.1Переключатель «РУЧ/ПОЗИЦ» в любом положении. Нажать кнопку «СЕЛЬСИН/КАЛИБР», при этом загораются обе еѐ половины
6.1.3.3.4.2Измерить зазор вертикальных валков (или линеек). Набрать на задатчике измеренное значение в миллиметрах.
6.1.3.3.4.3Повторно нажать кнопку «СЕЛЬСИН/КАЛИБР», при этом обе еѐ половины гаснут, а измеренная позиция отображается на дисплейной линейке.
6.1.3.3.4.4Если показания дисплейной линейки не соответствуют позиции на задатчике, то необходимо начать всѐ сначала.
6.1.3.3.4.5Проверить соответствие показаний продуктимера и дисплейной линейки, при необходимости на продуктиметре выставить измеренный зазор.
6.1.3.3.4.6Оператор обнуляет показания продуктиметров.
6.1.3.4При калибровке оператор должен обращать внимание на следую-
щее:
6.1.3.4.1Гидроцилиндры должны быть слиты или налиты до начала процесса калибровки. Диаметры рабочих валков должны быть введены до начала процесса калибровки на стоящей клети.
6.1.3.4.2Калибровка клети теряется, если произошло налитее или слитие гидроцилиндров или были введены новые диаметры валков.
6.1.3.4.3При необходимости остановки процесса калибровки необходимо надавить джойстик ручного управления нажимными винтами или нажать кнопку «АВТ не ВКЛ». Если движение винтов не прекращается – разобрать схему.
6.1.3.4.4Если клеть залита после длительного перерыва, то калибровать необходимо только еѐ одну, затем – остальные.
6.1.3.4.5При калибровке обязательно следить за перекосами как по месдозам, так и по силоизмерительным датчикам.
6.1.4Установка зазора между валками и скоростей вращения © (Г)
6.1.4.1 Диапазон обжатий в клетях черновой группы от минимальных до максимальных значений следует назначать в зависимости от 1-ой до 4-ой групп марок сталей (см. таблицу 5.1 и Д.1).

© (Г) ТИ 101-П ГЛ10-374 2010
стр. 55 из 180
6.1.4.2Настройку клетей черновой группы целесообразно назначать по режимам, предоставленным в приложении Д (таблицы Д.1, Д.2, Д.4).
6.1.4.3При нестандартной ситуации (выходе из строя какой либо клети) настройку стана следует производить путем переноса показаний задатчиков раствора валков и скоростей отключаемой клети на последующие.
6.1.4.4Значения заправочной скорости, темпа, начала ускорения и торможения выбираются оператором из условий:
- поддержания температуры конца прокатки в заданных пределах; - стабилизация толщины по всей длине полосы; - получение качественной смотки рулона.
6.1.4.5Характерный режим скорости прокатки на стане «2000», предусмотренный ПЭВМ (фирмы «General Electric»), приведен в приложении Е (таблица Е.7).
6.2 Перестройка стана © (Г)
6.2.1Получив сообщение от учѐтчика выдачи слябов о перестройке, оператор ПУ№7 обязан оповестить операторов и вальцовщиков на ПУ№9 о предстоящей перестройке.
6.2.2Перестройку стана по ширине необходимо производить не более чем через 250 мм.
Перестройку стана по толщине необходимо производить в зависимости от требуемой толщины готовой полосы не более чем через:
2,0 мм при толщине готовой полосы от 20 до 8,01 мм; 1,5 мм при толщине готовой полосы от 8,0 до 3,01 мм; 1,0 мм при толщине готовой полосы от 3,0 до 2,01 мм; 0,8 мм при толщине готовой полосы от 2,0 до 1,2 мм.
6.2.3Операторы и вальцовщики ПУ-7 и ПУ-9 могут осуществлять перестройку по ширине и толщине полосы в автоматическом и ручном режиме. При автоматической перестройке вальцовщики и операторы проверяют правильность рассчитанной с помощью ПЭВМ перестройки и следят за прохождением по стану полосы и в случае необходимости вносят коррективы в настройку стана.
6.2.4Перед перестройкой чистовой группы клетей на другой профилеразмер показания цифровых задатчиков нажимных винтов записываются вальцовщиками и операторами.
6.2.5Изменение зазора между валками и окружных скоростей при перестройке производится при изменении химического состава, температуры, толщины и ширины подката и готового профиля
6.2.6.1Изменение раствора между валками по клетям и скоростей прокатки при изменении только толщины готовой полосы производится согласно таблиц Д.3, Д.5 и Д.6.
6.2.6.2При перестройке чистовой группы на прокатку полосы другой ширины без изменения толщины и марки стали раствор валков увеличивают на 0,1 мм на каждые 100 мм уменьшения ширины и уменьшают раствор валков на 0,1 мм на каждые 100 мм увеличения ширины.
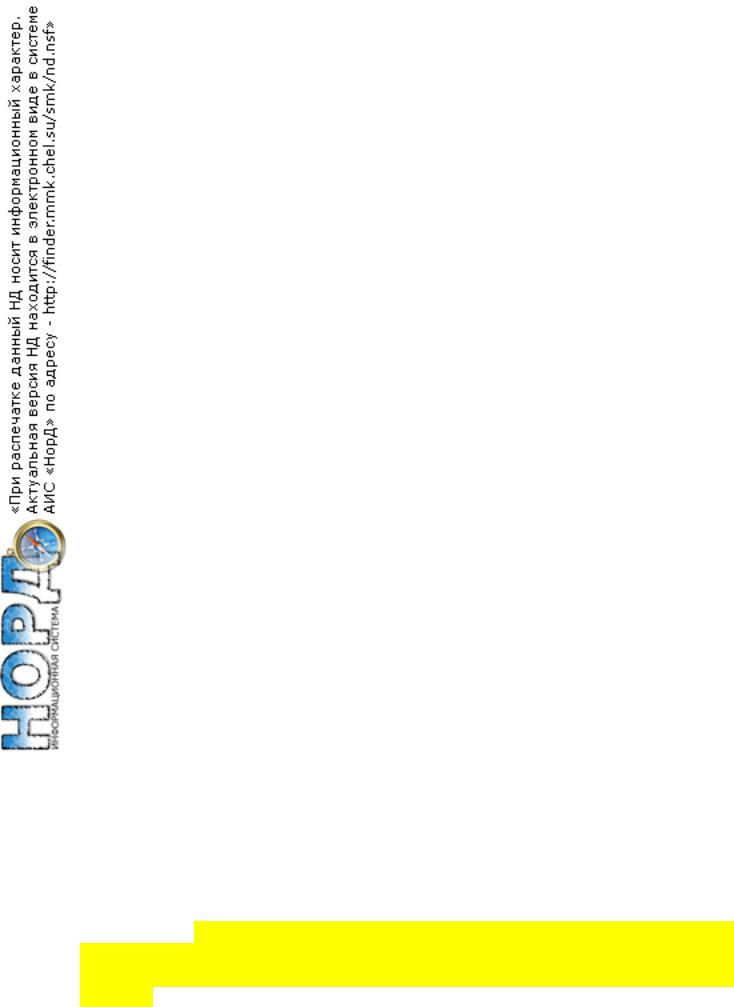
© (Г) ТИ 101-П ГЛ10-374 2010
стр. 56 из 180
6.2.6.3 При изменении массовой доли углерода в стали на каждые ±0,05 % требуется изменять раствор между валками на ±0,1 мм соответственно.
6.2.6При перестройке стана на другой профиль скорость прокатки и раствор валков корректируются на первой полосе после перестройки. При работе
сУВМ перестройка стана производится автоматически. Вальцовщики и операторы обязаны контролировать перестройку стана от УВМ используя таблицы Д.3, Д.4, Д.5, Д.6, Д.8.
6.2.7Минимальная толщина прокатываемых полос в зависимости от их ширины указаны в таблице Д.12.
6.3Порядок технологических операций при прокатке на стане «2000» © (Г)
6.3.1Слябы, нагретые до заданной температуры, выдаются из печи и двигаются по рольгангу к черновой группе клетей.
6.3.2В вертикальном окалиноломателе производится взламывание окалины и обжатие боковых граней сляба. Абсолютное обжатие с учетом теплового расширения и допуска по ширине находится от 30 до 100 мм. Минимальное значение обжатия установлено из необходимости получения требуемой ширины полосы и создания нормальных условий для разрыхления окалины.
6.3.3На линии стана – за вертикальным окалиноломателем, перед клетями № 2,3,4,5,6 и после чистового роликового окалиноломателя установлены гидросбивы высокого давления, с помощью которых происходит сбив окалины с поверхности полос.
6.3.4От ВОЛа сляб поступает в горизонтальную клеть «ДУО» и далее последовательно в клети №2,3,4,5,6. Клеть «ДУО» и клети №2,3 имеют главные приводы с двигателями постоянной скорости (синхронные). Клети №4,5,6 объединены в непрерывную подгруппу с регулируемым натяжением между клетями. Вертикальные клети работают с линейной скоростью, равной скорости последующей горизонтальной клети с коррекцией по обжатию. Скорости рольгангов синхронизируются со скоростью прокатки и управляются в зависимости от положения раската.
Существует возможность работы черновой группы при выведенных из процесса прокатки избранных как вертикальных, так и горизонтальных клетях (см. таблицы 6.1, 6.2) направляющие линейки устанавливаются на 100 мм больше ширины прокатываемого металла.
6.3.4.1Минимальное уменьшение ширины сляба по отношению к заказанной ширине полосы не менее 20 мм. Максимально допустимое абсолютное обжатие в вертикальном окалиноломателе 100 мм.
6.3.4.2Настройку вертикальных валков черновой группы производить в соответствии с таблицей 6.3.
6.3.4.3Старшие вальцовщики черновой группы клетей после перевалки эджеров должны производить проверку на соответствие показаний продуктиметров эджеров и фактического раствора между валками с последующей записью в журнале. (изменение №3)
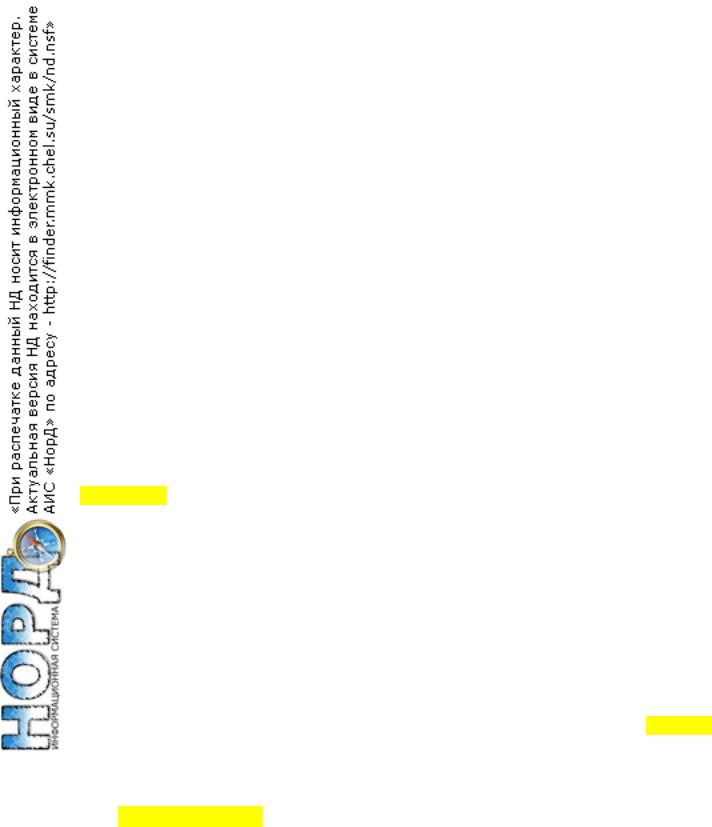
© (Г) ТИ 101-П ГЛ10-374 2010
стр. 57 из 180
Таблица 6.1 – Предельные размеры полос из различных марок сталей, получаемых в клетях с горизонтальными валками черновой группы при нестандартных ситуациях на стане «2000»
В миллиметрах
|
Состояние клети при |
|
|
Максимальная ширина полосы для марок стали |
|
|||||||||
нестандартной ситуации* |
|
|
|
|||||||||||
№1 |
№2 |
№3 |
№4 |
№5 |
№6 |
08ю |
|
Ст3сп |
17ГС |
Ст45 |
09ГДС |
|
65Г |
|
Р |
Р |
Р |
Р |
Р |
|
Р |
1850 |
|
1800 |
1750 |
1650 |
1500 |
|
1600 |
|
|
|
|
|
|
|
|
|
|
|
|
|
|
|
Н |
Р |
Р |
Р |
Р |
|
Р |
|
|
|
|
|
|
|
|
Р |
Н |
Р |
Р |
Р |
|
Р |
|
|
|
|
|
|
|
|
Р |
Р |
Н |
Р |
Р |
|
Р |
|
|
|
|
|
|
|
|
Р |
Р |
Р |
Н |
Р |
|
Р |
1600 |
|
1450 |
1300 |
1150 |
1100 |
|
1120 |
Р |
Р |
Р |
Р |
Р |
|
Н |
|
|
|
|
|
|
|
|
Р |
Р |
Р |
Р |
Н |
|
Р |
|
|
|
|
|
|
|
|
Р |
Р |
Р |
Р |
Н |
|
Н |
|
|
|
|
|
|
|
|
Н |
Р |
Р |
Н |
Р |
|
Р |
|
|
|
|
|
|
|
|
Н |
Р |
Р |
Р |
Н |
|
Р |
1300 |
|
1150 |
1050 |
720 |
700 |
|
750 |
Н |
Р |
Р |
Р |
Р |
|
Н |
|
|
|
|
|
|
|
|
___________ |
|
|
|
|
|
|
|
|
|
|
|
|
||
*Р – работающая клеть, Н – неработающая клеть. |
|
|
|
|
|
Таблица 6.2 – Максимальные уменьшения ширины слябов в черновой группе клетей по отношению к заказанной ширине полосы при неработающей вертикальной клети
|
|
|
|
В миллиметрах |
||
Номер вертикальной |
Максимальное уменьшение ширины слябов для групп сталей |
|||||
|
по выкатываемости и ширины |
|
|
|||
клети, выведенной из |
|
|
|
|||
Группа 1, 2 и 6 |
Группа 3, 4 и 5 |
|||||
работы |
||||||
|
|
|
|
|
||
от 750 до 1400 |
св. 1400 |
от 750 до 1400 |
|
св.1400 |
||
|
|
|||||
|
|
|
|
|
|
|
ВОЛ |
минус70 |
минус60 |
минус60 |
|
минус50 |
|
2 |
минус130 |
минус120 |
минус120 |
|
минус110 |
|
3 |
минус130 |
минус120 |
минус120 |
|
минус110 |
|
4 |
минус135 |
минус125 |
минус125 |
|
минус125* |
|
5 |
минус145 |
минус135 |
минус135 |
|
минус125 |
|
6 |
минус145 |
минус135 |
минус135 |
|
минус125 |
|
все клети в работе |
минус150 |
минус140 |
минус140 |
|
минус130 |
|
|
|
|
|
|
|
* (изменение №3)
6.3.5Прокатные клети (черновой и чистовой групп клетей) оснащены силоизмерительными датчиками (месдозы), входящими в измерительную систему «ASEA» (тип V101), характеристики которой изложены в приложении Е (таблица Е.1 и приложение Е.4). Фотореле, установленные в прокатной линии, следят за продвижением прокатываемой полосы. Перечень точек и датчиков слежения приведен в приложении Е (таблицы Е.4 и Е.5)
6.3.6Для измерения температуры раската в прокатной линии за клетью №3, на выходе из черновой и чистовой групп и перед 1 и 2 группой моталок установлены пирометры. Характеристика пирометров приведена в приложении Е (таблица Е.1)

© (Г) ТИ 101-П ГЛ10-374 2010
стр. 58 из 180
Таблица 6.3 – Расчетная таблица для настройки вертикальных валков группы стана «2000» г.п.
В миллиметрах
Уменьшение шири- |
Увеличение раствора эджеров по клетям от |
Абсолют- |
|||||
ны сляба к заказной |
|
заказной ширины рулона |
|
ное обжа- |
|||
ширине полосы |
ВОЛ |
2 |
3 |
4 |
5 |
6 |
тие в ВОЛ |
150 |
80/— |
60/— |
35/— |
10/— |
15/— |
20/— |
92/— |
140 |
80/80 |
60/60 |
35/40 |
10/20 |
15/20 |
20/25 |
82/90 |
130 |
70/80 |
50/60 |
30/40 |
10/15 |
15/20 |
20/25 |
82/80 |
120 |
70/70 |
50/50 |
30/30 |
10/15 |
15/20 |
20/25 |
72/80 |
110 |
70/70 |
50/50 |
30/30 |
10/15 |
15/20 |
20/25 |
62/70 |
100 |
60/60 |
40/40 |
30/30 |
10/15 |
15/20 |
20/25 |
62/70 |
90 |
50/50 |
35/35 |
20/20 |
10/15 |
15/20 |
20/25 |
62/70 |
80 |
40/40 |
30/30 |
20/20 |
10/15 |
15/20 |
20/25 |
62/70 |
70 |
40/40 |
30/30 |
20/20 |
10/15 |
15/20 |
20/25 |
52/60 |
60 |
30/30 |
20/20 |
15/15 |
10/15 |
15/20 |
20/25 |
52/60 |
50 |
30/30 |
20/20 |
15/15 |
10/15 |
15/20 |
20/25 |
42/50 |
40 |
20/20 |
15/15 |
15/15 |
10/15 |
15/20 |
20/25 |
42/50 |
30 |
10/20 |
10/15 |
10/15 |
10/15 |
15/20 |
20/25 |
42/40 |
20 |
0/15 |
5/15 |
10/15 |
10/15 |
15/20 |
20/25 |
42/40 |
______________
* Числитель в таблице соответствует слябам шириной до 1400 мм, знаменатель – слябам шириной свыше 1400 мм.
Пример расчета:
Ширина сляба 1370 мм, заказная ширина рулона 1220 мм. Изменение ширины равно: 1370 – 1220 = 150 мм.
По строке, соответствующей уменьшению ширины сляба на 150 мм, вычисляем растворы эджеров по клетям:
Клеть |
ВОЛ |
2 |
3 |
4 |
5 |
6 |
Раствор эджера, мм |
1300 |
1280 |
1255 |
1230 |
1235 |
1240 |
6.3.7Управление оборудованием черновой группы осуществляется с
ПУ№7.
6.3.8После черновой группы полоса по промежуточному рольгангу направляется к летучим ножницам и далее в чистовую группу клетей.
6.3.9Скорость промежуточного рольганга должна быть синхронизирована (одинакова) со скоростью последней катающей клети черновой группы. После выхода раската из последней катающей клети черновой группы скорость промежуточного рольганга перестраивается на транспортную скорость.