
TI-101-P-Gl10-374-2010_s_izm_1-7
.pdf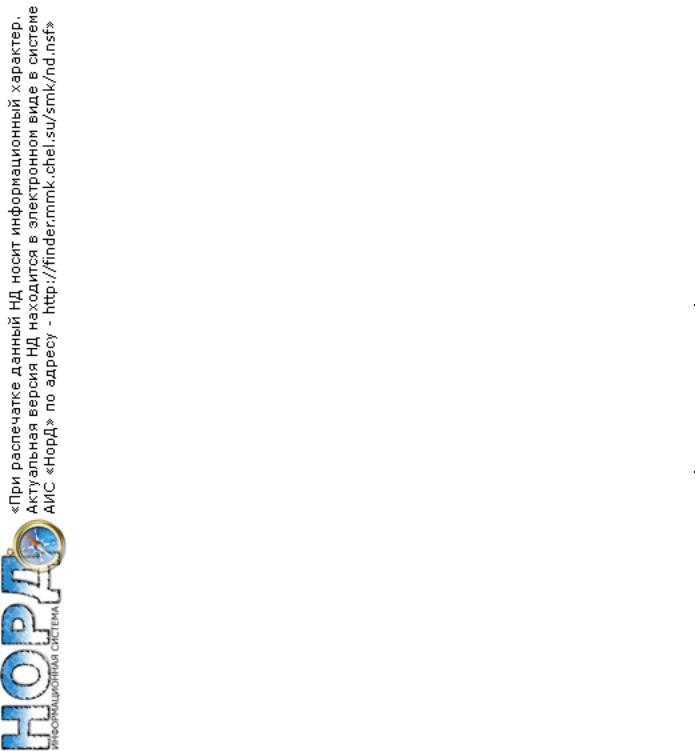
© (Г) ТИ 101-П ГЛ10-374 2010
стр. 29 из 180
по мере выхода металла из печи последовательно снижать расход га-
за на зоны;
в зонах 3 - 8 поддерживать температуру от 900 до 1000 °С;
снизить нагрузку дымососов;
при простоях более 32 часов, дополнительно отключать часть горелок в зонах №3,4,6.
не менее чем за 5 часов до начала прокатки начинать разогрев печи и загрузку слябов.
Таблица 5.6 Снижение температуры в печи при остановках стана
Предполагаемое |
Снижение температуры |
Время выхода на рабочую |
|
температуру перед началом |
|||
время простоя, ч |
в зонах №3–8, °С |
||
прокатки, мин |
|||
|
|
||
До 0,5 |
10–20 |
10 |
|
До 1,0 |
20–40 |
20 |
|
До 4,0 |
100–150 |
60 |
|
До 8,0 |
дежурный газ |
90 |
|
20 и более |
дежурный газ |
300 |
5.4Остановка печи на холодный ремонт
5.4.1Перед остановкой печи на холодный ремонт выгрузить полностью металл из печи. По мере выхода металла из печи закрывать зоны №1,3,4.
5.4.2В зоне № 6 оставить по 2 горелки с каждой стороны.
5.4.3Зоны № №5,7,8 охлаждать до 900 °С со скоростью не более 150 °С /ч.
5.4.4При температуре от 900 до 500 °С охлаждать со скоростью не более 60–80 °С /ч, закрывая газ на зоны №6–10.
5.4.5При 500 °С закрыть все горелки (газ и воздух) и охлаждать печь с максимальной произвольной скоростью для чего:
5.4.5.1Открыть полностью поворотные дымовые клапана перед котлами – утилизаторами;
5.4.5.2Перевести дымосос на работу с максимальной загрузкой;
5.4.5.3Открыть заслонки торца выдачи;
5.4.5.4Открыть крышки смотровых окон;
5.4.5.5Открыть крышки окалиносборников и гидрозатворов;
5.4.5.6Подать воздух через горелки нижних зон.
5.4.6Подача воды на охлаждение элементов печи прекращается только после охлаждения печи ниже 100 °С.
5.4.7Закрыть заслонки окна загрузки для того, чтобы не было противотока воздуха в печь и охлаждение велось по всей длине печи.
5.4.8Получить наряд-допуск на производство газоопасных работ, вызвать газоспасателя, установить заглушку после общей задвижки на печь.
5.4.9Продуть газопроводы печи сжатым воздухом или азотом на свечи. Взять пробы на анализ из газопроводов печи, рабочего пространства печи. При удовлетворительных результатах химического анализа приступить к ремонтным работам.
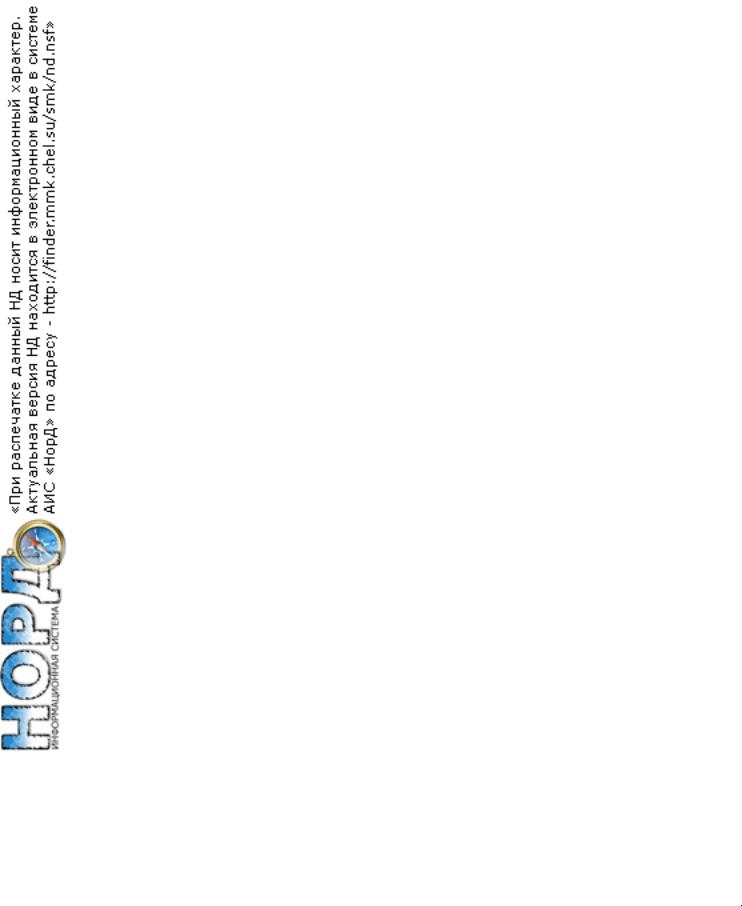
© (Г) ТИ 101-П ГЛ10-374 2010
стр. 30 из 180
5.5Разогрев печи после холодного ремонта
5.5.1 Сушка и разогрев печи после холодного ремонта производится в зависимости от продолжительности ремонта согласно режимам, указанным в таблицах 5.7, 5.8. График разогрева печи после ремонта составляет старший мастер (мастер) печей.
Таблица 5.7 – Сушка и разогрев печи после холодного ремонта продолжительностью до 10 суток
Этап сушки и разогрева печи по |
Время подъѐма |
Скорость |
Действия по отоплению |
|
подъема, |
||||
температуре в зонах № 5,7 |
температуры, ч |
печи |
||
°С /ч |
||||
|
|
|
||
Подъѐм до 300 °С |
2 |
— |
Разжечь горелки зон 8,6 |
|
|
|
|
|
|
Подъѐм от 300 до 800 °С |
26 |
20 |
Разжечь горелки зон 10,9,7 |
|
(при температуре 700 °С) |
||||
|
|
|
||
Подъѐм от 800 до 1100 °С |
7 |
40 |
Разжечь горелки зон 4,5 |
|
|
|
|
|
|
Подъѐм от 1100 °С до рабочей |
5 |
30 |
Разжечь горелки зоны 3 |
|
|
|
|
|
|
Итого |
40 |
— |
|
|
|
|
|
|
5.5.2Вести разогрев по термопарам расположенным в зонах №5,7.
5.5.3При достижении температуры 1100 °С начать загрузку слябов в
печь.
5.5.4По окончании разогрева произвести подливку свода шамотным раствором в местах образования трещин.
Таблица 5.8 – Сушка и разогрев печи после холодного ремонта продолжительностью 10 суток и более
Этап сушки и разогрева печи |
Время подъѐма |
Скорость |
Действия по отоплению |
|
подъема, |
||||
по температуре в зонах №5,7 |
температуры, ч |
печи |
||
°С /ч |
||||
|
|
|
||
Подъем до 300 °С |
2 |
|
Разжечь горелки зон №8,6 – 4шт. |
|
|
|
|
|
|
Подъем от 300 до 800 °С |
44 |
10-20 |
Разжечь горелки зон №4,10,6–до |
|
конца |
||||
|
|
|
||
Выдержка при 800 °С |
4 |
|
Разжечь горелки зон №7, 9 |
|
|
|
|
|
|
Подъем от 800 до 1100 °С |
14 |
20 |
Разжечь горелки зон №3,5 |
|
|
|
|
|
|
Выдержка при 1100 °С |
4 |
|
|
|
|
|
|
|
|
Подъем от 1100 °С до рабочей |
4 |
45 |
Разжечь все горелки зоны №3 |
|
|
|
|
|
|
Итого |
72 |
|
|
|
|
|
|
|
5.6Уход за печью и ее оборудованием
5.6.1Нагревальщики следят за состоянием кладки, гарнитуры печи, газового хозяйства, систем охлаждения печи, работой КИП и А.
5.6.2При обнаружении щелей в кладке свода, боковых и торцевых стенах, между плитами горелок и кладкой и других неплотностей, через которые

© (Г) ТИ 101-П ГЛ10-374 2010
стр. 31 из 180
происходит выбивание печных газов или подсос окружающего воздуха в рабочее пространство, нагревальщик сообщает старшему мастеру (мастеру) печей.
5.6.3Не допускается разогрев и покраснения металлических частей печи (подвесок свода, рам рабочих окон, каркаса). При обнаружении неисправностей, мешающих нормальной эксплуатации печи нагревальщику сообщить начальнику смены, старшему мастеру (мастеру) печей.
5.6.4Окалина с подины печи, через проемы шагающих балок, попадает
вокалиносборники, оборудованные течками, которые закрываются крышками. Окалина из окалиносборников, по мере еѐ накопления, с помощью транспортеров удаляется в желоба гидросмыва. Полная очистка подины проводится во время ремонта печи.
5.6.5Уровень воды в гидрозатворе контролируется струей воды, вытекающей из переливной трубы. При обнаружении отсутствия воды или переполнения гидрозатвора вызывается дежурный слесарь-энергетик и совместно с ним регулируют поступление воды в гидрозатвор. Промывку ванн гидрозатворов производить не реже 1 раза в месяц.
5.6.6Выявленные замечания по работе оборудования печей заносятся в журнал сменных рапортов старших нагревальщиков.
5.6.7В течение смены систематически контролируется состояние газового хозяйства печи:
состояние запорных устройств продувочных свечей;
плотность фланцевых соединений, а также сальников задвижек и поворотных клапанов на газопроводе;
световая и звуковая сигнализации систем автоблокировки с записью результатов в эксплуатационный журнал по газовому хозяйству.
Обнаруженные утечки газа немедленно устраняются. При невозможности устранения утечки сообщается начальнику смены, старшему мастеру (мастеру) печей.
5.6.8Знать принцип работы испарительного и водяного охлаждения пе-
чи.
5.6.9Следить за состоянием балок и других охлаждаемых элементов. Появление стуков и треска в водоохлаждаемых деталях свидетельствует о недостаточном охлаждении. В этом случае необходимо увеличить расход охлаждающей воды или сократить подачу топлива до прекращения стуков.
5.6.10В случае повреждения систем охлаждения, появлении течи или выбивании пара в запорной арматуре, немедленно сообщить дежурному слеса- рю-энергетику, начальнику смены, старшему мастеру печей, энергетику цеха.
5.6.11Следить за звуковыми и световыми сигналами, поступающими от
системы испарительного охлаждения (СИО). Расход циркуляционной воды в подвижном контуре должен быть от 350 до 800 м3/ч, в неподвижном контуре от 460 до 1000 м3/ч. Обо всех отклонениях от нормальной работы СИО нагревальщик немедленно сообщает бригадиру слесарей-энергетиков.
5.6.12Выявленные замечания в работе систем охлаждения печи заносятся в журнал сменных рапортов старших нагревальщиков

© (Г) ТИ 101-П ГЛ10-374 2010
стр. 32 из 180
5.6.13Перед розжигом печи после ремонта старший нагревальщик и бригадир слесарей-энергетиков совместно должны убедиться в том, что на все водоохлаждаемые элементы печи вода поступает нормально.
5.6.14Запрещается технологическому персоналу открывать приборы - самописцы, изменять положение термопар, расходомеров на печи. Обо всех неисправностях сообщать работникам цеха КИП и А ООО НПО «Автоматика».
5.7Учет и переработка выбросов и недокатов
5.7.1Под выбросом следует понимать сляб, выданный из печи после его нагрева и не подвергнутый обжатию ни в одной горизонтальной клети стана.
5.7.2Недокат – сляб, прокатанный в одной или нескольких клетях черновой группы.
5.7.3Все выбросы и недокаты должны иметь маркировку, состоящую из номера плавко-партии, марки стали, размеров (длина, ширина, толщина) и номера бригады. Недокаты маркируют технологи черновой группы, выбросы – старший нагревальщик (нагревальщик) металла. Мастер производства проверяет наличие и правильность маркировки выбросов и недокатов. На выбросы составляется двухсторонний акт на передачу их на склад слябов ККЦ. Один акт хранится в ОКП склада слябов ККЦ, а второй в ОКП ЛПЦ-10. Выбросы и недокаты складируются в специально отведенных для этого местах.
5.7.4Количество полученных и прокатанных выбросов и недокатов в штуках и тоннах должно учитываться в сменных рапортах производства начальником смены (мастером производства).
5.7.5Выбросы и недокаты толщиной 100 мм и более могут быть перекатаны. Недокаты толщиной менее 100 мм дальнейшей переработке не подлежат.
5.7.6Недокаты толщиной 100 мм и более разрезаются на мерные длины, соответствующие любому из трех диапазонов длины (другие типоразмеры не допускаются):
от 4,5 |
до |
5,2 м; |
от 7,7 |
до |
8,1 м; |
от 10,8 |
до |
11,5 м. |
5.7.7Недокаты толщиной от 100 до 150 мм сажать в печь со стороны выдачи (заблаговременно предусмотреть возможность посада во время перевалок) и греть в зоне 7 в течение 50–80 минут при температуре 1240–1280 °С.
5.7.8Недокаты толщиной от 150 до 200 мм сажать в печь со стороны выдачи (заблаговременно предусмотреть возможность посада) во время длительного простоя (до 8 часов) и греть в зоне 7 в течение 90 – 150 минут при температуре 1150 – 1280 °С.
5.7.9Недокаты толщиной 200 мм и более сажать в печь со стороны по-
сада.
5.7.10Ответственность за порезку и перевозку недокатов несут мастер производства и старший вальцовщик черновой группы.
5.7.11Выбросы с помощью передаточной тележки передают на загрузоч-
ный рольганг.

© (Г) ТИ 101-П ГЛ10-374 2010
стр. 33 из 180
5.7.12Ответственность за посад выбросов и недокатов несут мастер производства и старший нагревальщик, за нагрев - старший нагревальщик и нагревальщик.
5.7.13Перекат недокатов толщиной от 100 до 200 мм (посаженных в печи со стороны выдачи), допускается в любом монтаже не зависимо от ширины недокатов. Их прокатку производить в пределах 8 км суммарной длины прокатанных полос от начала монтажной партии, но не ранее прокатки настроечной полосы. Посад и прокатку недокатов толщиной 200 мм и более производить по заданию диспетчеров производственного управления
5.8 Характеристика печей №1-3
5.8.1Назначение печи — нагрев слябов перед прокаткой.
5.8.2Тип печи — нагревательная, рекуперативная; десятизонная с шагающими балками, с двухсторонним нагревом, торцевым посадом и выдачей.
Эскиз печи приведен в приложении В-1. Размеры печи приведены в таблице 5.9.
5.8.3Характер работы печи — непрерывный.
5.8.4Топливо — природный газ, объемная теплота сгорания от 7950 до 8100 ккал/м3, давление газа перед печью 10–12 кПа (1000–1200 мм вод. ст.).
5.8.5Характеристика горелок приведена в таблице 5.10.
5.8.6Тип горелок — сводовые радиационные и дутьевые труба в трубе.
5.8.7Максимальный расход на печь:
газа 30000 м3/ч;
воздуха |
283330 м3/ч. |
5.8.8Максимальная производительность печи, при длине сляба 12 м — до 465 т/ч. В зависимости от длины, ширины сляба, сортамента прокатываемого металла, производительность печи указана в таблице 5.3.
5.8.9Напряжение активного пода — до 780 кг/(м2·ч).
5.8.10Рекуператор для подогрева воздуха, подаваемого в печь для сжигания топлива.
Таблица 5.9 – Размеры печи
Наименование |
Значение |
|
|
Длина печи, м: |
|
– габаритная |
50,29 |
– активная |
49,14 |
Ширина печи, м: |
|
– габаритная |
12,76 |
– активная |
12,0 |
Площадь пода, м2: |
|
– габаритная |
642 |
– активная |
590 |
Высота верхних зон от уровня стационарных балок, м |
1,7 |
Высота нижних зон до уровня стационарных балок, м |
2,5 |

© (Г) ТИ 101-П ГЛ10-374 2010
стр. 34 из 180
Таблица 5.10 – Характеристика горелок печи
|
|
Коли- |
Производительность по |
Тепловая |
|||
Зона |
Тип |
газу, м3/ч |
|||||
печи |
горелок |
чество |
|
|
мощность зоны, |
||
Одной |
|
||||||
горелок |
Зоны |
МВт (Гкал/ч) |
|||||
|
|
горелки |
|||||
|
|
|
|
|
|
||
1 |
ГР 350 |
16 |
39,5 |
2744 |
25,1 |
(21,6) |
|
ГР 750 |
24 |
88,0 |
|||||
|
|
|
|
||||
2 |
ДВБ РФ275/36,5 |
6 |
540 |
3240 |
29,8 |
(25,6) |
|
3 |
ГР 750 |
56 |
88,0 |
4928 |
45,2 |
(38,9) |
|
4 |
ДВБ РФ275/36,5 |
12 |
540 |
6480 |
59,4 |
(51,1) |
|
5 |
ГР 350 |
8 |
39,5 |
3132 |
28,7 |
(24,7) |
|
ГР 750 |
32 |
88,0 |
|||||
|
|
|
|
||||
6 |
ДВБ РФ275/38 |
8 |
590 |
4720 |
43,3 |
(37,2) |
|
7 |
ГР 350 |
32 |
39,5 |
1264 |
11,6 |
(10,0) |
|
|
|
|
|
|
|
|
|
8 |
ДВБ КФ200/22 |
12 |
219 |
2628 |
24,1 |
(20,7) |
|
9 |
ГР 350 |
8 |
39,5 |
316 |
2,9 |
(2,5) |
|
10 |
ДВБ КФ200/22 |
2 |
219 |
438 |
4,1 |
(3,5) |
|
Всего |
|
216 |
|
|
274,2 |
(235,8) |
5.8.10.1Тип рекуператора — петлевой, металлический, трубчатый шести-
секционный.
5.8.10.2Количество рекуператоров на печь — 2 шт.
5.8.10.3Проходное сечение рекуператора по дыму — 24,5 м2.
5.8.10.4Проходное сечение рекуператора по воздуху — 2,67 м2.
5.8.10.5Количество труб в секции — 130 шт.
5.8.10.6Диаметр труб (наружный) — 76 мм, толщина стенки — 4,5 мм.
5.8.10.7Материал труб: сталь 20Х23Н18 — первый ряд секций со стороны дыма, сталь 12Х17 — второй ряд секций.
5.8.10.8Температура подогрева воздуха в рекуператоре — до 450 °С.
5.8.10.9Температура дымовых газов перед рекуператором — до 950 °С.
5.8.10.10Температура стенок рекуператора – 800 °С.
5.8.11Вентилятор для подачи воздуха на горение:
5.8.11.1Количество вентиляторов — 8 шт.
5.8.11.2Тип — ВВН-20.
5.8.11.3Число оборотов электродвигателя — 1500 об/мин.
5.8.11.4Мощность электродвигателя — 800 кВт.
5.8.11.5Напор создаваемый вентилятором — 16,4 кПа (1640 кгс/м2), давление воздуха перед печью 10–12 кПа.
5.8.11.6Производительность вентилятора — 142000 м3/ч.
5.9Перемещение металла в печи
5.9.1 Перемещение металла в печи осуществляется с помощью системы неподвижных и подвижных (шагающих) балок.

© (Г) ТИ 101-П ГЛ10-374 2010
стр. 35 из 180
5.9.2Работа системы перемещения шагающих балок осуществляется циклами, автоматически. Предусмотрена также возможность работы в режиме ручного управления.
5.9.3Каждый цикл состоит из четырѐх движений, выполняемых балками последовательно: подъем на 200 мм, перемещение вперед на 450 мм, опускание на 200 мм, возврат в исходное положение.
5.9.4Время цикла – 56 секунд.
5.9.5Работа системы перемещения балок сблокирована с работой других механизмов, обеспечивающих загрузку и выдачу слябов, толкателем, приемником слябов, механизмами подъема и опускания заслонок окон посада и выдачи печи.
5.10 Системы охлаждения печи и правила эксплуатации
5.10.1На печи применяется испарительное и водяное охлаждение эле-
ментов.
5.10.2Система испарительного охлаждения (СИО):
5.10.2.1СИО предназначена для охлаждения подовых балок (подвижных и неподвижных) химически очищенной водой, а также утилизации тепла за счет вырабатываемого ею насыщенного пара.
5.10.2.2Для каждой печи предусмотрено две установки испарительного охлаждения (УИО), независимые одна от другой: одна для подвижных балок, вторая – для неподвижных балок.
5.10.2.3Циркуляция в установках принудительная в связи с большим гидравлическим сопротивлением системы.
5.10.2.4Циркуляция осуществляется насосами НКУ-630/80. Производительность – 630 м3/ч, создаваемый напор – 0,8 МПа (8 кгс/см2), мощность электродвигателя – 200 кВт, частота вращения вала двигателя – 2970 об/мин.
5.10.2.5УИО подвижных балок состоит из 16 контуров (12 подвижных балок размерами 219×25 мм со вставкой размерами 127×8 мм и 4 группы стоек без вставок в зоне выдачи слябов).
5.10.2.6УИО неподвижных балок состоит из 18 контуров (18 неподвижных балок со стойками размерами 219×25 мм со вставкой размерами 127×8 мм). Сочленение коммуникаций с балками осуществляется при помощи шарнирных соединений.
5.10.2.7Каждая УИО печи состоит из: барабана-сепаратора, четырѐх циркуляционных насосов (два – в работе, два – в резерве), бака мгновенного испарения (общий), охлаждаемых элементов печи, сливного бака (общий на 2 УИО), пробоотборного устройства, запорной и регулирующей арматуры, соединительных трубопроводов, приборов КИП и А.
5.10.2.8Производительность установки испарительного охлаждения подвижных балок по выработке пара: максимальная – 30 т/ч, минимальная – 8 т/ч.
Теплосъем с охлаждаемых элементов от 4,8 до 18 Гкал/ч.
5.10.2.9Производительность установки испарительного охлаждения неподвижных балок по выработке пара: максимальная–40 т/ч, минимальная–10 т/ч.

© (Г) ТИ 101-П ГЛ10-374 2010
стр. 36 из 180
Теплосъем с охлаждаемых элементов от 6 до 24 Гкал/ч.
5.10.2.10Эксплуатация СИО при обрушении изоляции подовых балок свыше 30 % от общего количества балок запрещается.
5.10.2.11Циркуляция в системе осуществляется следующим образом: вода из барабана-сепаратора по всасывающему трубопроводу поступает к циркуляционному насосу, от насоса по нагнетательному трубопроводу через распределительную гребенку подводящих трубопроводов подается в подвижные (неподвижные) балки; из балок образовавшаяся пароводяная смесь через отводящие коллекторы подается обратно в барабан-сепаратор. В барабане-сепараторе пароводяная смесь разделяется на пар и воду. Пар поступает в КУ-150, где перегревается и поступает в общезаводской паропровод, а вода идет к циркуляционному насосу.
5.10.3 Технической водой из чистого оборотного цикла на одной печи охлаждаются:
5.10.3.1Заслонки торца выдачи – 2 шт.
5.10.3.2Балка торца загрузки – 2 шт.
5.10.3.3Балка торца выдачи – 1 шт.
5.10.3.4Водоохлаждаемые экраны нижней зоны (комплект) - 1 шт.
5.10.3.5Водяные затворы – 18 шт.
5.10.3.6Подшипники механизма подъема заслонок торца загрузки и выдачи – 2 комплекта.
5.10.3.7Кожуха телекамер и лазерные датчики торца выдачи –2 комплекта.
5.10.3.8Насосы для откачки воды из приямков – 2 шт.
5.10.3.9 Водоохлаждаемая рама шибера – 2 шт.
Температура воды, отходящей из охлаждаемых элементов, не должна превышать 45 °С во избежание выпадения солей в охлаждаемом элементе, что приводит к образованию накипи, ухудшению теплообмена, прогару элемента. При низком давлении воды в питательном водоводе или повышении температуры отходящей воды, температура в печи должна снижаться до таких значений, чтобы охлаждение элементов печи было надежным. В случае нехватки воды или аварии на водоводах, печи должны быть остановлены.
5.10.4 Техническая вода из грязного оборотного цикла поступает для смыва окалины в желобах гидроудаления и для бокового гидроудаления на окалиносборники.
5.11 Кладка печи
5.11.1Кладка стен печи выполнена из кирпича марки ШБ в низкотемпературной зоне и марки ША в высокотемпературной зоне. Толщина стен в верхних зонах 615 мм, в нижних зонах – 730 мм. Толщина подины 557 мм.
5.11.2Прямой свод печи выполнен из подвесных огнеупоров марки ША в низкотемпературной зоне и муллитокремнеземистым кирпичом в высокотемпературной зоне. Толщина свода 270 мм.

© (Г) ТИ 101-П ГЛ10-374 2010
стр. 37 из 180
5.11.3Контроль геометрических параметров кладки печи ведѐтся при еѐ замене и осуществляется представителями ремонтных подразделений, производящих еѐ замену.
5.11.4Для изоляции стен печи использованы изоляционные плиты МКРП толщиной 40 мм, для изоляции подины - диатомитовый кирпич.
5.11.5Горелочные блоки выполнены из муллитокремнеземистого кирпи-
ча.
5.11.6Отверстия в подине, через которые проходят стояки подвижных балок, выполнены в виде набивных блоков из жаростойкого муллитокремнеземистого бетона.
5.11.7Подвижные и неподвижные балки изолируются муллитокремнеземистым бетоном марки СМКРБТ (по ТИ 101-П- ГЛ10-387-99). Толщина изоляции 60–65 мм. Стояки неподвижных подовых балок могут изолироваться муллитошамотными блоками.
5.11.8Футеровка дымопроводов выполнена из шамота класса Б толщиной 300 мм и шамотного легковеса толщиной 160 мм.
5.11.9В цех огнеупорные изделия поступают на поддонах с центрального склада автотранспортом и складируются на складе огнеупоров или на участке печей.
5.12 Дымовой тракт
5.12.1В состав дымового тракта входят 2 круглых вертикальных дымовых канала, расположенных за рекуператорами, - дымоспады (левый и правый) диаметром 4520 мм, которые переходят в горизонтальные дымовые борова на отметке -14 м.
5.12.2Борова на расстоянии 88330 мм от оси дымоспадов имеют перемычку диамером 3820 мм, предназначенную для отвода продуктов сгорания из печи при работе на один дымосос.
5.12.3В боровах на расстоянии 97330 мм от оси дымоспадов расположены дымовые шибера.
5.12.4На расстоянии 139330 мм от оси дымоспадов расположены котлы - утилизаторы КУ-150 (2 шт. на каждую печь)
Производительность КУ-150 |
до 34,5 т/ч |
Температура перегрева пара |
до 368 °С |
Давление пара |
до 1,8 МПа (18 кгс/см2) |
Пропускная способность по дыму |
до 150000 м3/ч |
5.12.5 За котлами – утилизаторами имеются поворотные дымовые клапаны диаметром 3500 мм для регулирования давления в печи. Управление поворотными дымовыми клапанами осуществляется с теплового щита печи.
5.13 Дымовая труба
5.13.1 Ствол дымовой трубы выполнен конической формы из бетона класса В25, F200 на сульфатостойком портландцементе. Футеровка - кирпич керамический марки КР 100/1800/15 на цементоглиняном растворе.

© (Г) ТИ 101-П ГЛ10-374 2010
стр. 38 из 180
Теплоизоляция - плиты теплоизоляционные из минеральной ваты на синте-
тическом связующем марки 25. |
|
|
Фундамент – бетон класса В 25 на портландцементе. |
|
|
Высота дымовой трубы |
150 |
м |
Внутренний диаметр устья трубы |
5,4 м |
|
Температура отводимых дымовых газов |
170 |
– 230 °С |
Температура точки росы отводимых дымовых газов 45 °С
5.13.2Дымовые газы подаются на трубу принудительно дымососами ти-
па ДН-26х2-062 (за КУ № 1,3,5 – двухскоростные, производительностью 477/382 м3/ч, за КУ № 2,4,6 – односкоростные производительностью 477 м3/ч). От дымососов на дымовую трубу отходящие газы поступают через металлические газоходы прямоугольного сечения.
5.13.3В трубе предусмотрено два проема размерами сечения 2560×6260
ммна отметке +10,27 м для подвода дымовых газов от котлов-утилизаторов двух печей.
5.13.4Проектом предусмотрены молниезащита, ходовая лестница с балконами, светофорные площадки.
5.13.5Отвод дымовых газов от печей №1,2 осуществляется через трубу №1, отвод дымовых газов от печи №3,4 осуществляется через трубу №2.
5.14Печь №4 фирмы «Stein Heurtey» © (Г)
5.14.1Краткая характеристика печи №4 фирмы «Stein Heurtey»
5.14.1.1В состав оборудования печи входят:
–промежуточный загрузочный рольганг конструкции фирмы «Stein
Heurtey»;
–рольганг загрузки конструкции фирмы «Stein Heurtey» перед печью;
–загрузочная машина конструкции фирмы «Stein Heurtey»;
–механизм привода шагающего пода (рама подъѐма / рама перемещения);
–нагревательная печь с шагающими балками конструкции фирмы «Stein Heurtey» производительностью 425 т/ч. Схема нагревательной печи №4 в приложении В.3;
–разгрузочная машина конструкции фирмы «Stein Heurtey»;
–рольганг выгрузки конструкции фирмы «Stein Heurtey» перед печью.
5.14.1.2 Характеристики основного и вспомогательного оборудования печи изложены в таблице 5.11.
5.14.2 Посад и перемещение слябов в печи
5.14.2.1 На промежуточном рольганге загрузки перед печью установлены телеметрические датчики для измерения размеров сляба. Эта информация используется в системе позиционирования.