
Строительные и дорожные машины. Основы автоматизации
.pdf
288
Порядок выполнения работ бескопрового погружения призматических свай с использованием сваеустановщика 1, оборудованного захватным устройстврм, и крана 2 представлен на рис. 5.8.
Рис. 5.8. Последовательность операций бескопрового погружения призматических свай: а – установка сваи; б – монтаж наголовника с погружателем; в – погружение сваи; 1– сваеустановщик; 2– кран; 3– погружатель; 4– наголовник; 5 – свая
Различают механические, паровоздушные, дизельные и гидравлические свайные молоты. Механический молот является простейшим механизмом, представляющим собой металлическую отливку массой до 5 т, сбрасываемую на погружаемую сваю. Отливку поднимают вдоль мачты копра канатом подъемной лебедки, откуда ее сбрасывают на сваю, отсоединяя от каната специальным расцепляющим устройством или отключением барабана лебедки от трансмиссии. Из-за низкой производительности (4...12 ударов в 1 мин) механические молоты применяют в основном при незначительных объемах свайных работ.
Паровоздушный молот представляет собой пару цилиндр—поршень. В молотах одиночного действия (рис. 5.9, а) поршень 3 через шток 2 соединяется с наголовником 1 сваи, а ударной частью является цилиндр 4, направляемый поршнем. Под действием сжатого воздуха или пара, подаваемого в поршневую полость цилиндра от компрессорного или паросилового оборудования, цилиндр поднимается вверх, а после перекрытия впускного трубопровода и соединения поршневой полости с атмосферой (рис. 5.9, б) цилиндр падает, ударяя по наголовнику сваи. Управляют впуском и выпуском сжатого воздуха (пара) вручную, полуавтоматически и автоматически. Молоты с автоматическим управлением работают с частотой ударов 40...50 мин-1. В молотах двойного действия (рис. 5.9, в) ударной частью является соединенный с поршнем боек 5, движущийся внутри направляющего цилиндра. Сжатый воздух (пар) подают поочередно в нижнюю штоковую и верхнюю – поршневую (рис.5.9, г) полости паровоздушного цилиндра, обеспечивая тем самым подъем поршня с бойком и принудительное его падение на ударную плиту – наковальню 6 с частотой 3 с-1
По сравнению с молотами одиночного действия описанные молоты более производительны при меньшем отношении массы ударной части к общей массе, не превышающем 1/4, в то время как у молотов одиночного действия это отношение равно в среднем 2/3.
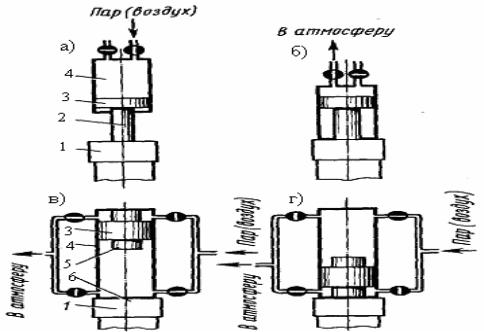
289
Рис. 5.9. Принцип работы паровоздушных молотов одиночного (а, б)
и двойного (в, г) действия: 1– наголовник; 2– шток; 3– поршень; 4–цилиндр; 5 – боек; 6 –наковальня
Паровоздушные молоты используют для забивки вертикальных и наклонных свай на суше, а также под водой. Основным недостатком является зависимость от компрессорных или паросиловых установок.
Гидравлический молот работает по схеме паровоздушного молота двойного действия с тем отличием, что вместо воздуха или пара в рабочий цилиндр подается жидкость, для чего сваебойный агрегат с гидравлическим молотом оборудуют насосной установкой. Для придания ударной части ускорения в момент удара к насосу подсоединяют гидравлический аккумулятор, который подзаряжается во время обратного хода поршня. Распределение подачи рабочей жидкости в различные периоды работы молота осуществляется автоматически. Гидравлические молоты развивают энергию удара от 3,5 до 120 кДж при частоте ударов 50...170 мин-1. Масса ударной части составляет 210...7500 кг.
Наибольшее распространение в строительстве получили дизельные молоты, работающие независимо от внешних источников энергии в режиме двухтактного дизеля. Различают дизель-молоты с направляющими штангами –штанговые и с направляющим цилиндром – трубчатые. У штанговых дизель-молотов (рис. 5.10, а) две направляющие штанги 4 объединены в нижней части основанием 2, отлитым заодно с поршнем 12. Основание поршневого блока опирается на сферическую пяту 1 и наголовник 15. По штангам перемещается цилиндр 10, служащий одновременно ударной частью молота. В верхней части штанги объединены траверсой 7 захвата («кошки»), свободно перемещающейся по ним и подвешенной к канату 8 лебедки копра.

290
Рис. 5.10. Дизельные молоты: а– штангового типа ; б– трубчатого типа: 1– сферическая пята; 2– нижняя основания; 3– форсунка; 5– палец ударной части; 6– крюк; 7– траверс; 8– канат; 9– рычаг; 10– ударная часть; 11–штырь; 12– поршень; 13– центральный канал; 14– топливный насос; 15– наголовник; 16– штырь; 17– шабот; 18– выхлопной канал; 19– бак;
20– «кошка»; 21– цилиндр; 22– поршень; 23– рычаг
Для запуска молота «кошку» опускают до зацепления подпружиненным крюком 6 пальца 5 ударной части, после чего ударную часть 10 поднимают, а затем рывком нажатием на рычаг 9 через присоединенный к нему канат расцепляют «кошку» с ударной частью. Последняя падает вниз, нанося удар по основанию 2 и сжимая воздух в закрытой поршнем 12 полости цилиндра. Одновременно выступающий на ударной части штырь 11 нажимает на рычаг топливного насоса 14, которым по центральному каналу 13 в поршне топливо с некоторым опережением конца хода подается в цилиндр, распыляясь форсункой 3 и смешиваясь с нагретым вследствие сжатия до высокой температуры воздухом. В последней фазе движения ударной части вниз вследствие дополнительного сжатия топливно-воздушной смеси происходит ее самовоспламенение. Расширяющиеся при сгорании топлива газы отбрасывают ударную часть вверх, откуда она снова падает, повторяя процесс. Молот выключают прекращением подачи топлива.
Ударной частью трубчатого дизель-молота (рис. 5.10, б) служит поршень 22, перемещающийся в направляющем цилиндре 21. Удары поршня воспринимаются шаботом 17, герметично посаженным в нижнюю часть рабочей секции цилиндра. Молот центруют на свае штырем 16. Для пуска молота его поршень «кошкой» 20, подвешенной к канату 8, поднимают в верхнее положение, откуда его сбрасывают. При движении вниз поршень отжимает рычаг 23, которым
291
включается насос 14, впрыскивающий из бака 19 в цилиндр порцию топлива. Последняя, смешиваясь с воздухом, стекает в сферическую выемку в шаботе 17. При дальнейшем падении поршень перекрывает канал 18, сообщающий цилиндр с атмосферой, и сжимает воздух в замкнутом уменьшающемся объеме. От удара поршня о шабот находящаяся в сферическом углублении последнего топливо-воздушная смесь разбрызгивается и воспламеняется. Расширяющиеся при сгорании смеси газы подбрасывают поршень вверх, откуда он снова падает, сжимая воздух, удаляя отработавшие газы через канал 18 в атмосферу и повторяя процесс. Останавливают молот прекращением подачи топлива.
Для отвода теплоты при работе трубчатого дизель-молота его топливный цилиндр выполняют с ребристой внешней поверхностью (воздушное охлаждение) или с дополнительно примыкающими к нему секциями, соединенными в нижней части кольцевым баком, заполненным водой (водяное охлаждение). При нагреве вода циркулирует по вертикальным трубам, равномерно охлаждая цилиндр. Трубчатые дизель-молоты с воздушной системой охлаждения работают без перегрева при температуре окружающего воздуха до 30 оС, а с водяным охлаждением — до 40 оС и выше.
Штанговые дизель-молоты не имеют принудительного охлаждения. Поэтому в летнее время при температуре окружающего воздуха 25 °С они работают с получасовыми перерывами после каждого часа работы. Штанговые дизельмолоты обладают малой энергией удара – 3,2 и 65 кДж при частоте 50...55 мин-1 и массе ударной части 240 и 2500 кг соответственно. Их применяют для забивки легких железобетонных и деревянных свай в слабые и средние грунты, а также для погружения шпунта при ограждении траншей, котлованов и т. п. Трубчатые дизель-молоты применяют для забивки железобетонных свай в любые нескальные грунты. Отечественной промышленностью выпускаются трубчатые дизель-молоты массой ударной части 500...5000 кг с энергией удара 15...150 кДж при частоте ударов 43...45 мин-1, в том числе для работы в условиях низких температур (до − 60 °С). Для запуска этих молотов при низких температурах между фланцем шабота и амортизатором вводят разъемную (из двух частей) прокладку, увеличивая тем самым рабочий ход поршня, а следовательно, и степень сжатия топливно-воздушной смеси. При этом подачу топлива снижают до минимума. После прогрева цилиндра прокладку снимают. При работе в условиях низких температур воду сливают. Заправлять зимой систему охлаждения водой рекомендуется лишь после явных признаков перегрева − снижения высоты подъема ударной части и появления пламени в выхлопных патрубках.
Для передачи ударных нагрузок свае без разрушения ее головы применяют наголовники со сдвоенным деревянным − обычно дубовым амортизатором. После износа амортизатора его заменяют новым. Забивка свай без амортизатора приводит к их разрушению (до 15...20%).
Вибропогружатели и вибромолоты. Вибропогружатель представляет собой возбудитель направленных колебаний вдоль оси сваи. Соединяясь со сваей по-

292
средством наголовника 4 (рис. 5.11), он сообщает ей возмущающее периодическое усилие, которым преодолеваются сопротивления погружению сваи в грунт.
Рис. 5.11. Низкочастотный (а) и высокочастотный (б) вибропогружатели
Вибропогружатели состоят обычно из электродвигателя, возбудителя и наголовника. В отдельных случаях, когда дебалансы устанавливают на валу электродвигателя, электродвигатель и возбудители совмещаются в одном агрегате.
При установке вибровозбудителя отдельно от двигателя конструкция его представляет систему горизонтально расположенных валов с дебалансами, привод их от электродвигателя 1 осуществляют через ременную, цепную или шестеренчатую передачу.
Главным параметром вибропогружателей является установленная мощность электродвигателей; кроме того, вибропогружатели характеризуются следующими параметрами: возмущающей силой, моментом дебалансов, частотой колебаний и массой.
Возмущающей силой называют суммарную центробежную силу, развиваемую дебалансами. Она зависит от массы дебалансов и скорости их вращения. Для увеличения амплитуды возмущающей силы вибропогружатели изготавливают многодебалансными.
Вибропогружатели принято характеризовать также моментом дебалансов, численно равным сумме произведений массы неуравновешанной части дебалансов на расстояние от их центра тяжести до оси вращения.
Вибропогружатели разделяют на две группы: низкочастотные (рис.5.11, а), развивающие 300…500 колебаний в минуту, и высокочастотные (рис.5.11, б), развивающие 700…1500 колебаний в минуту.

293
Первая группа предназначена для погружения крупногабаритных элементов значительной массы, в основном свай и оболочек.
Вторая группа обеспечивает погружения элементов небольшой массы с малым лобовым сопротивлением (шпунт, металлические трубы, балки и т. п). Основным преимуществом вибропогружателей являются: большая скорость погружения, удобство управления, обеспечение сохранности погружаемых элементов, в том числе тонкостенных железобетонных оболочек большой длины.
В пределах своего назначения – погружения свай и шпунта в песчанные и супесчаные водонасыщенные грунты – вибропогружатели в 2…3 раза производительнее свайных молотов, они удобны в управлении, не разрушают погружаемых ими строительных элементов.
К недостатком вибропогружателей относятся ограниченная область применения и сравнительно небольшой срок службы электродвигателей из-за вредного влияния вибрации, затруднительность применения в связных и плотных маловлажных грунтах.
Вибромолоты отличаются от вибропогружателей видом соединения корпуса вибровозбудителя с наголовником 6 (рис. 5.12). Это соединение выполнено через пружинные амортизаторы 5, которые позволяют корпусу вибровозбудителя совершать большие размахи, отрываясь от наголовника и ударяя бойком 3 по
наковальне 4 при обратном движении. |
|
Обычно вибромолоты изготавливают бестрансмис- |
|
сионными, сажая дебалансы 2 непосредственно на |
|
валы двух синхронно работающих электродвигате- |
|
лей, статоры которых установлены в едином корпу- |
|
се 1. |
|
Оптимальный режим работы вибромолотов зави- |
|
сит как от соотношения параметров вибровозбудите- |
|
ля, так и от размера зазора между бойком и наковаль- |
|
ней, который устанавливают на заводе-изготовителе |
|
на специальном стенде. Для сообщения свае боль- |
|
шой энергии удара пружинные амортизаторы подби- |
|
рают так, чтобы один удар бойка о наковальню прихо- |
|
дился на два, три и т. д. оборота дебалансовых валов. |
Рис. 5.12.Принципиаль- |
Важной особенностью работы вибромолотов являет- |
ная схема вибромолота: |
ся их способность к самонастройке − повышению |
1– ударнавя часть; |
энергии удара с увеличением сопротивления погруже- 2 – дебалансы; 3− верхняя
нию сваи. Это объясняется тем, что с ростом сопроти- |
плита; 4,6− наголовники; |
влений уменьшается податливость сваи (увеличива- |
5− рабочие пружины |
ется ее жесткость), чем определяется более высокая скорость обратного хода (после удара) и последующего прямого движения
(вниз). Выпускаемые отечественной промышленностью вибромолоты характеризуются энергией удара до 3,9 кДж при массе ударной части 2850 кг.

294
Конструкция наголовника обеспечивает упругую связь между вибромолотом и погружаемым элементом (через резиновую прокладку и короткие пружины крепления). Благодаря этому удар молота передается только погружаемому элементу (через накавальню), а плитой наголовника не воспринимается. Если наголовки перемонтировать, то вибромолот может быть повернут на 180° для нанесения ударов снизу вверх. В такой компоновке вибромолоты используют как виброударные выдергиватели свай и шпунта.
К недостатком вибропогружателей относятся ограниченная область применения и сравнительно небольшой срок службы электродвигателей из-за вредного влияния вибрации, затруднительность применения в связных и плотных маловлажных грунтах.
Контрольные вопросы по пятой главе. 1. Виды современного оборудования для свайных работ. 2. Назначение, устройство и рабочий процесс копров и копрового оборудования. 3. Перечень машин и оборудования для бескопрового погружения свай. 4. Классификация, устройство и принцип работы гидравлических и дизельных свайных молотов. 5. Принцип работы вибропогружателй и вибромолотов. 6. Объяснить последовательность операций бескопрового погружения призматических свай. 7. Отличительные признаки штангового ди- зель-молота от трубчатого. 8. В каких случаях используют низкочастотный вибропогружатель?.
6. МАШИНЫ ДЛЯ ДРОБЛЕНИЯ, СОРТИРОВКИ И МОЙКИ КАМЕННЫХ МАТЕРИАЛОВ
6.1.Машины для дробления каменных материалов
Вдорожном строительстве ежегодно потребляется большое количество каменных материалов: щебня, гравия и песка. Большая часть этих материалов используется на приготовление бетона. Добыча песка и гравия производится в естественных отложениях механическим или гидравлическим способом, а щебня
–из естественного камня путем дробления взорванных скальных пород. Добываемые каменные материалы перерабатываются на камнедробильных, используя различные схемы дробления (рис.6.1), и промывочно-сортировочных заводах, а затем в виде готового продукта стандартного качества доставляются потребителю.
Рис.6.1. Схемы дробления материалов: а)- раздавливанием; б)-ударным воздействием; в, д)- раскалыванием; г)- истиранием; е)- взрывом

295
Качество щебня характеризуется зерновым составом, формой зерен, механической прочностью и содержанием вредных примесей. В зависимости от крупности зерен щебень разделяют на фракции 5...10; 10...20; 20...40 и 40...70 мм. Кроме того, для дорожного строительства допускаются фракции 3...10; 10...15; 15...20 мм и для балластного слоя железнодорожного пути 25...50 мм. Для массивных бетонных сооружений верхний предел крупности может достигать 120...150 мм. По форме зерен их классифицируют на лещадные, у которых ширина в три раза и более меньше длины, и кубообразные. Действующие стандарты не допускают содержание в щебне и гравии зерен лещадной формы более 15 %. Щебень из гравия получают дроблением гравия и валунов. Требования к щебню, полученному из гравия, в основном такие же, как к щебню, полученному из взорванных каменных пород. Механическая прочность щебня определяется прочностью горных пород, из которых он получен. Различают породы малой прочности 30...80 МПа, средней – 80...150 и высокой – более 150 МПа.
Основными характеристиками, определяющими сопротивление каменных материалов и пород сжатию, является предел прочности σв, равный отношению максимального разрушающего усилия Fmax , вызывающего раздавливание образца, к начальной площади его поперечного сечения А
σв Fmax / A.
Деформация пород оценивается модулем упругости Е, определяемым путем деления σвна относительную деформацию образца l/l (где l первоначальная длина образца; l деформация образца под действием силы F )
E σв / .
Силу, необходимую для дробления материала, можно определить из следующих условий. Работа сил деформации L F l/2. Согласно закону Гука деформация тела при сжатии l Fl /(EA).
Тогда
1 F2l L 2 EA .
Если примем, что максимальное значение силы деформации Fmax σв А, то получим
L |
0,5 |
в2 Аl |
0,5 |
в2V |
, |
|
|
||||
max |
|
E |
|
E |
|
|
|
|
где V объем каменного материала.
С другой стороны, работу сил деформации можно определить как произведение силы Fmax на ход s/2 рабочего элемента дробилки, при котором наступает разрушение образца
L max Fmaxs/2.
Приравнивая правые части обоих выражений для L max , получаем

296
0,5F s 0,5 |
в2V |
, |
|
||
max |
E |
|
|
|
откуда
Fmax в2V .
Es
При разрушении материалов и пород ударом необходимую скорость рабочего элемента определяют из условия равенства кинетической энергии, развиваемой им, работе деформации при сжатии материала, т. е.
0,5mv2 L max 0,5 в2V /E,
откуда необходимая скорость рабочего элемента v |
в2V |
, |
|
||
|
mE |
где m масса рабочего элемента.
Степенью дробления называют отношение размера наиболее крупных, загружаемых в дробилку камней, к размеру максимальных зерен в продукте дробления:
I = Dmax/dmax. |
(6.1) |
Дробление разделяют на крупное (Dmax = 1200...1500 мм, dmax= 100...300
мм), среднее (Dmax= 100...300 мм, dmax= 30...100 мм), мелкое (Dmax= 30...100 мм, dmax=5…30 мм) и тонкое (помол). Дробление пород высокой и средней прочности осуществляют раздавливанием, раскалыванием и ударом; помол – истиранием и ударом.
В зависимости от степени измельчения материалов дробильные машины разделяют на дробилки и мельницы. Некоторые машины могут работать как дробилки и как мельницы (например, валковые дробилки, бегуны). По принципу действия и конструктивным признакам дробилки делят на щековые, конусные, валковые, молотковые и роторные дробилки; мельницы – на барабанные, шаровые, бегунковые и вибрационные. Различные типы дробилок позволяют получить определенную, присущую данной конструкции, степень дробления: щековые –2...8; валковые –1,5...10; конусные – 3...8; молотковые – 5...30;
мельницы –10...20.
Выбор типа дробильного оборудования осуществляют в зависимости от максимальной крупности кусков исходного материала, его прочности, необходимой степени дробления и требуемой производительности.
Дробление материалов ведут в одну или несколько стадий. Преимущественное распространение получило стадийное дробление, при котором материал дробят в 2...3 приема на дробилках разных типов. Уже на каждой стадии дробления получают материал с требуемыми размерами кусков. Такие куски отсеиваются на грохоте, установленном перед дробилками разных стадий. Дробилки последних стадий работают, как правило, в замкнутом цикле с виброгрохотом, при этом материал крупнее заданного размера возвращается в ту же дробилку для повторного дробления (рис. 6.2).

297
Рис. 6.2. Типовая схема дробильно-сортировочной установки:
1 — вагонетка; 2 — пластинчатый конвейер; 3 — колосниковый грохот; 4 — щековая дробилка; 5,7 — виброгрохоты; 6—валковая дробилка; 8—бункер
для песка и пыли; 9 — расходный бункер; 10 — склады товарного щебня
При одностадийном дроблении получаемые мелкие зерна заполняют промежутки между крупными и защищают их от непосредственного воздействия дробящих органов машины, что сопровождается дополнительным измельчением материала и расходом энергии. Основными показателями работы дробилок являются: максимальная крупность дробления, степень измельчения, удельный расход энергии (кВт-ч/м3), производительность (м3/ч или т/ч).
Щековые дробилки. Их применяют для крупного и среднего дробления прочных и средней прочности пород на первичной и вторичной стадиях дробления. По характеру движения подвижной щеки щековые дробилки разделяют на дробилки с простым и сложным качанием щеки.
Дробилка с простым качанием щеки (рис. 6.3, а, б) состоит из сварного корпуса 1, в котором в подшипниках установлен эксцентриковый вал 7 с подвешенным к нему шатуном 8. Нижний конец шатуна имеет специальные гнезда, в которых свободно вставлены концы распорных плит 12 и 13. Противоположный конец распорной плиты 13 вставлен в гнездо подвижной щеки 3, подвешенной на оси 5. Конец плиты 12 упирается в клиновой упор регулировочного устройства 9. Тяга 11 и пружина 10 обеспечивают обратное движение подвижной щеки и удерживают от выпадания распорные плиты. К неподвижной 2 и подвижной щекам крепятся дробящие плиты 4 с вертикальным рифлением, являющиеся основными рабочими органами щековых дробилок. Рабочие поверхности дробящих плит и боковые стенки корпуса дробилки образуют камеру дробления.