
- •А.Д. Абрамов, И.А. Батанова
- •А.С. Алехин, А.О. Башмаков
- •В.А. Антипин
- •Б.Б. Илюшин
- •Институт теплофизики СО РАН, Новосибирск
- •Анализ работы тороидального ДВС
- •Введение
- •Тороидальный двигатель внутреннего сгорания
- •Рабочий цикл РТ1
- •Рабочий цикл РТ2
- •Коэффициент полезного действия
- •Вычисление среднего момента
- •Заключение
- •Библиографический список
- •Ж.К. Ахметов
- •Д.В. Балагин
- •Библиографический список
- •Х.Э. Батиров
- •Библиографический список
- •А.Л. Бобров
- •Библиографический список
- •Результаты испытаний зубчатой передачи
- •Библиографический список
- •В.С. Воробьев, Н.В. Мокин
- •Необходимые начальные объемы воздуха в баке
- •Выводы
- •Библиографический список
- •С.П. Глушков, С.С. Глушков
- •Библиографический список
- •И.К. Далюк
- •Введение
- •Материал и методы исследования
- •Принцип работы универсального подогревателя.
- •Результаты исследований
- •Библиографический список
- •И.Н. Жигулин
- •Библиографический список
- •А.А. Игумнов
- •С.А. Коларж
- •А.Н. Лавизин, В.Н. Говердовский
- •Основные типы дефектов обычных ЛКП
- •Примеры применения модифицированных ЛКП
- •Библиографический список
- •Н.А. Маслов
- •Циклограммы работы стендов для испытаний гидромашин
- •Результаты расчета Σti
- •Выводы
- •Выводы
- •Работа стенда
- •Испытания гидромашины 20 в режиме «гидромотор»
- •Испытания гидромашины 20 в режиме «насос»
- •Библиографический список
- •С.М. Овчаренко, А.Ф. Кабаков
- •Библиографический список
- •Курганский институт железнодорожного транспорта, г. Курган
- •Тепловой расчет салона пассажирского вагона
- •Воздух в салоне
- •Внутренне оборудование
- •Ограждающие конструкции салона
- •Д.С. Воронцов
- •А.Ю. Примычкин
- •Библиографический список
- •Выводы
- •В.Ю. Тэттэр
- •ООО «Резерв», Омск
- •Выводы
- •Библиографический список
- •А.П. Шиляков
- •Библиографический список
- •К.П. Шенфельд
- •ОАО «ВНИИЖТ»
- •П.Н. Рубежанский
- •«Российские Железные Дороги»
- •Библиографический список
- •Г.В. Меркулов
- •В.В. Буровцев
- •С.В. Рачек, А.В. Мирошник
- •И.Ю. Сольская
- •Библиографический список
- •А.П. Дементьев
- •Библиографический список
- •А.В. Давыдов
- •Библиографический список
- •Резюме
- •Библиографический список
- •Т.А. Лунина, С.П. Кретов
- •Библиографический список
- •Н.М. Стецюк
- •Библиографический список
- •М.О. Северова, Е.А. Поверенная
- •В.Л. Незевак, В.С. Голавский
- •Библиографический список
- •В.В. Галтер
- •И.Ю. Сольская, Н.Г. Бобкова
- •Инновационный потенциал
- •Инновационная восприимчивость
- •Оценка инновационной активности
- •Библиографический список
- •Ю.М. Буинцева
- •Ю.М. Буинцева
- •Е. А Корховая
- •Расходы федерального бюджета, млрд р.
- •Бюджетное финансирование приоритетных ФЦП, млрд р.
- •Библиографический список
- •Н.С. Фадеева
- •Библиографический список
- •С.Н. Артыкова
- •Расчет налога на имущество организации за 2012 г.
- •Библиографический список
- •Д.В. Ефименко, Е.С. Чугуева
- •С.В. Ильницкий
- •Библиографический список
- •О.Р. Окрестина
- •М.О. Баранчеев
- •Е.В. Климова
- •Библиографический список
- •И.А. Колпаков
- •Библиографический список
- •С.А. Пащина
- •Библиографический список
- •В.А. Бурмистров
- •Зап.-Сиб. ж.д. – филиал ОАО «РЖД»
- •Оптимальное сочетание стимулов трудовой деятельности работников транспортных компаний
- •Расчет расценки и зарплаты за смену на период освоения
- •Библиографический список
- •Д.В. Бурмистрова
- •Сотрудники, принявшие участие в исследовании.
- •Ранжирование мотивационного типа руководителей
- •Ранжирование мотивационного типа специалистов
- •Результаты диагностики мотивационной среды
- •Библиографический список
- •С.А. Давыдов
- •Библиографический список
- •Т.Е. Шатунова
- •П.И. Кузьмина, И.Ю. Сольская
- •Факторы, влияющие на конкурентоспособность образовательных учреждений разных форм, оказывающих услуги в области ДПО
- •Библиографический список
- •А.Г. Александров
- •Библиографический список
- •А.Н. Быстрова
- •Библиографический список
- •А.В. Веселков
- •О.И. Кашник
- •Библиографический список
- •А.В. Кокшаров
- •П.И. Кузьмина
- •Библиографический список
- •А.М. Лесовиченко, Е.А. Мальцева
- •Н.И. Мартишина
- •Формирование научного мышления в образовании
- •В.И. Мельников
- •Библиографический список
- •Г.В. Попов
- •Н.В. Силкина, Н.А. Касаткина, Р.С. Силкин
- •Библиографический список
- •О.В. Соболева
- •Библиографический список
- •А.А. Черняков
- •А.М. Завьялов
- •Методы исследования рисков
- •Значения лингвистической переменной частоты (вероятности)
- •Значения лингвистической переменной тяжести последствий
- •Библиографический список
- •Библиографический список
- •1. Методика анализа и оценки профессиональных рисков в ОАО «РЖД». Утверждена распоряжением ОАО «РЖД». № 2144 от 19.12.2005 г.
- •3. Методика построения матрицы рисков. ОАО «ВНИИЖТ», 2011.
- •Содержание
- •Научное издание

Инновационные факторы развития Транссиба на современном этапе. Часть 2
ответственно по стали подвижного магнитопровода и ферромагнитной жидкости; Sm c , Smж, Smd – поперечные сечения магнитной
цепи на пути магнитного потока, соответственно подвижного магнитопровода, ферромагнитной жидкости и зазора.
ЭДС, индуктированная в измерительной обмотке рабочим магнитным потоком Фр определяется из выражения
Ен = - jwв wудФр ,
где: wуд = кa – удельное число витков измерительной обмотки,
приходящееся на единицу угла поворота a подвижной части; k - коэффициент пропорциональности.
Таким образом:
Ен = - jwвФр ka.
Поворот спиралевидного сердечника 1 осуществляется с помощью вспомогательной зубчатой передачи. При этом ферромагнитная жидкость 5 под воздействием электромагнитной силы, создаваемой магнитным полем обмотки возбуждения4, удерживается в место размещения подвижного магнитопровода3 нижней части витков спиралевидного сердечника 1. Перемещение подвижного магнитопровода 3 с обмоткой возбуждения4 при повороте спиралевидного сердечника 1 происходит только по направляющей 6.
Использования многооборотного бесконтактного потенциометра переменного тока в целях контроля электрических параметров силового электрооборудования позволяет повысить точность контроля, а бесконтактность измерения упрощает процесс получения информации, следовательно улучшает его оперативность, что очень важна при эксплуатации в пути следования локомотива.
Библиографический список
1.Патент РУз. № IAP 03316, 2007 г. Многооборотный бесконтактный потенциометр переменного тока / Амиров С.Ф., Турдибеков К.Х., Шойимов Й.Ю., Саттаров Х.А., Хушбоков Б.Х. // Расмий ахборотнома. 2007. № 3.
2.Патент Руз. № IAP 04474, 2012 г. Многооборотный бесконтактный потенциометр переменного тока / Амиров С.Ф., Турдыбеков К.Х., Батиров Х.Э., Рустамов Д.Ш., Жураева К.К., Баходиров И.И.
39

Международная научно-практическая конференция
А.Л. Бобров
Сибирский государственный университет путей сообщения, Новосибирск
Методы определения ресурса деталей подвижного состава на основе результатов неразрушающего контроля
Безопасность и надежность в эксплуатации деталей и узлов подвижного состава зависит от качества контроля и достоверности оценки их технического состояния. Поэтому при диагностике и продлении времени эксплуатации таких объектов, как правило, используют комплекс методов, сочетающих способы обнаружения дефектов типа несплошностей и способы прогнозирования деградационных процессов структуры, в том числе в местах нахождения обнаруженных дефектов.
Такой комплексный подход к определению ресурсных параметров деталей требует четких механизмов оценки при прогнозировании поведения потенциальных очагов разрушения. В настоящее время наиболее проработанным методом диагностики развивающихся дефектов, в том числе литыых деталей подвижного состава является метод акустической эмиссии (АЭ) [1].
В связи с условиями эксплуатации и вероятностной оценкой безотказной работы объекта диагностики возникают следующие варианты применения прогнозных методик:
-определение вероятности безотказной работы на задаваемый период времени (например, до следующего ремонта с возможностью повторного контроля);
-определение времени эксплуатации с заданной вероятностью безотказной работы.
Поставленная цель требует ее поэтапного решения на стадии осуществления операций по диагностированию состояния объекта:
-определение участков, несущих наибольшие напряжения, к которым относятся места, к которых находятся скрытые несплошности, наиболее тонкие сечения и конструктивно наиболее нагруженные сечения;
-оценка динамики развития деградации структурного состояния в наиболее уязвимых участках изделия;
40

Инновационные факторы развития Транссиба на современном этапе. Часть 2
- построение корректных эмпирических моделей при оценке технического состояния в зависимости от истории эксплуатации изделия и прогнозируемых режимов работы.
В качестве объектов исследования были взяты литые детали тележки грузового вагона – боковые рамы и надрессорные балки. Это объясняется тем, что для этих деталей используется комплекс методов контроля (магнитные методы, вихретоковый, АЭ) охватывающий поставленные задачи.
Для решения первой задачи проводили статистическую оценку причин отказов деталей и их дефектности на основании периодического контроля. Результаты такого анализа для литых деталей тележек ругулярно проводятся в исследованиях.
Расчет и измерения напряжений в литых деталях тележки грузовых вагонов показывает, что даже в нормальных условиях эксплуатации на детали присутствуют участки, испытывающие напряжения, превышающие предел выносливости. А при наличии дефектов поверхности катания колес, когда детали испытывают дополнительные ударные нагрузки, или других несоответствиях параметров тележки, возникающие, в процессе эксплуатации, напряжения в детали могут достигать предела текучести. Это способствует быстрому развитию усталостных трещин, за период эксплуатации, значительно меньший межремонтному времени.
Таким образом, основной задачей диагностики участков боковых рам и надрессорных балок является выявление участков, в которых нагрузки превышают предел выносливости, особеннои, предел текучести при испытаниях. Решить эту задачу можно за счет применения магнитных методов контроля, визуального контроля, а так же АЭ методом для участков со скрытыми дефектами.
Вопросы оценки развития дефектов при использовании АЭ метода можно корректно применять только с учетом прилагаемой к детали при испытаниях нагрузки. Относительно металла литых деталей приведены различные результаты исследований[1–3], позволяющие сопоставить данные о напряженном состоянии литых деталей, в том числе с учетом наличия дефектов. Так, например, наличие внутреннего литейного дефекта, площадью сечения 5 % от площади сечения детали и поверхностного концентратора в виде риски, забоины или микротрещины приводит к превышению пре-
41

Международная научно-практическая конференция
дела выносливости в наиболее нагруженных областях боковых рам и надрессорных балок, что, согласно данным работы [2] сопровож-
дается резким повышением активности такого источника . АЭ Наличие же усталостных трещин на большнстве участков, на которых они образуются, так же увеличивает коэффициент концентрации напряжений и приводит к повышению активности источника АЭ. По энергенитческим параметрам и интегральным критериям АЭ можно определить степень напряженного состояния и концентрацию напряжений.
Определив величину напряженного состояния и степень концентрации напряжений в области источника АЭ с использованием вероятностных критериев можно построить модель определения параметров ресурса.
За основу рассуждений возьмем одно распределений, описывающее вероятность P времени безотказной работы t (для упрощения предположим, что число циклов механического нагружения в единицу времени величина постоянная). Такое распределение можно считать непрерывным, так как в зависимости от размеров дефекта и напряженного состояния участка, на котором он находится, разрушение теоретически может произойти в любой момент времени. Кроме того, оценку состояния объекта проводят, когда он еще пригоден к использованию, то есть, распределение не может быть симметричным во времени, а имеет смысл только во временной области t > 0. Наиболее широко, для решения поставленной задачи и отвечающее указанным требованиям, применяется распределение Вейбулла-Гнеденко [4]:
æ |
|
t |
a ö |
|
|
|
ç |
- |
|
÷ |
, |
(1) |
|
|
|
|||||
Р(t) = expç |
|
÷ |
||||
è |
|
q ø |
|
|
где a и q – параметры (коэффициенты) смещения и масштаба соответственно, параметр a > 0.
Очевидно, что изменение этих коэффициентов в процессе эксплуатации объекта влечет за собой уменьшение вероятности безотказной работы и среднего времени наработки до отказа:
1/ a |
æ |
|
1 ö |
|
|
tcp = q |
Gç1 |
+ |
|
÷ . |
(2) |
|
|||||
|
è |
|
a ø |
|
42
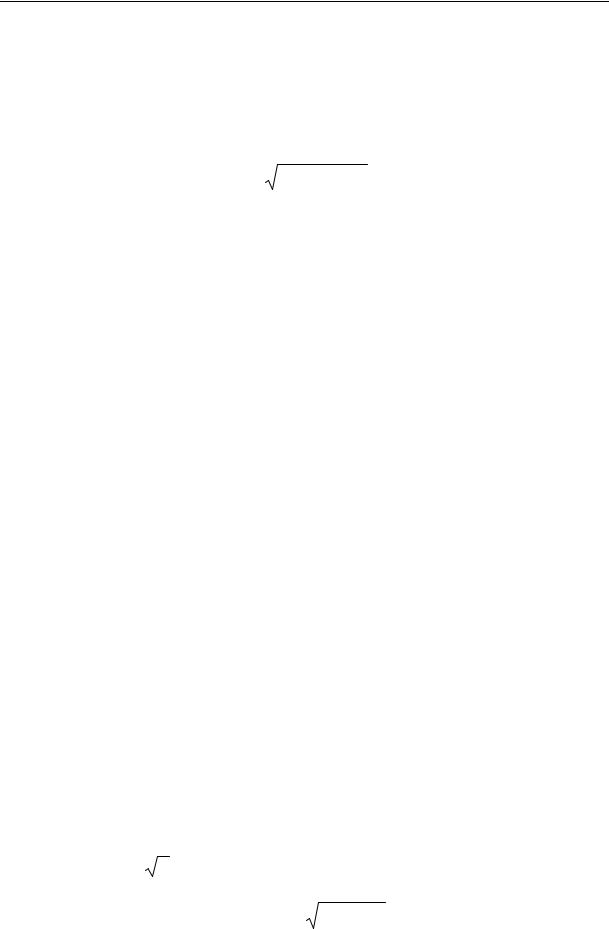
Инновационные факторы развития Транссиба на современном этапе. Часть 2
Таким образом, параметры a и q зависят от физико-механи- ческих свойств объекта, влияющих на долговечность его работы.
Если вероятность безотказной работы объекта задавать как постоянную величину P0, отвечающую заданному уровню безопасности, то время безотказной работы можно выразить из формулы (1):
t = a - q×ln( P ) . |
(3) |
0 |
|
Полученные данные можно интерпретировать следующим образом. Параметр времени несет в себе смысл числа циклов нагружения, в граничном состоянии, когда t → 1, то есть численные значения параметров P0 и q соответсвуют времени одного цикла нагружения до разрушения с соответствующим значением вероятности 1 – P0.
Отметим, что при малых значениях параметраa ® 0 формулы
(3) и относительно высоких численных значениях параметровP0 и q – время безотказной работы стремится к 0, то есть разрушение неизбежно при малейших нагрузках в предлагаемой интерпретации. А при относительно низких численных значениях параметров P0 и q – время безотказной работы или количество циклов до разрушения наоборот t ® ∞. Кроме того, существенное увеличение параметра α приводит к приближению к ситуации с одним полным циклом нагружения до разрушения, то есть напряженное состояние s при максимальной нагрузке цикла в месте разрушения стремится к sкр – критическому значению напряжений.
На практике, при продлении времени эксплуатации или ресурса и при диагностике деталей, наиболее важным обстоятельством является принципиальное разделение деталей на пригодные к эксплуатации до момента времени следующей диагностики, пригодные в ограниченных условиях или при сокращенном времени до следующей диагностики и отбраковка деталей с критическими источниками с высокой степенью вероятности. В такой, достаточно ограниченной временными параметрами, ситуации возможно разделить влияющие на результаты диагностики критерииa и q, вынеся из под корня член a q , тогда получаем уравнение вида:
N = |
Кин |
×a - ln(P ), |
(4) |
|
|||
|
ESl |
0 |
|
|
|
|
43
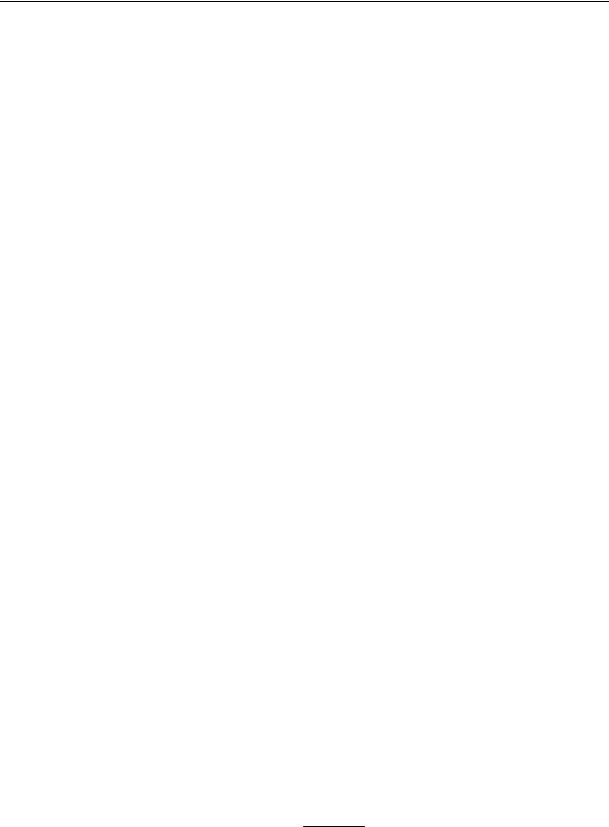
Международная научно-практическая конференция
где Кин – параметр, учитывающий величину относительных напряжений в зоне локализации источника сигналов АЭ; EΣ – параметр, отражающий влияние на долговечность изделия– суммарная энергия сигналов АЭ в зоне локализации источника; оценивающий опасность дефекта по степени идентичности локальных динамических процессов, протекающих из дефектного участка под нагрузкой; l – коэффициент активности дефекта. Тогда мы получаем приближенную зависимость, параметры которой определяются эмпирическим путем и зависят от характеристик сопровождающих разрушение в области дефекта или деградацию структуры в более обширной области (например, ползучесть, коррозию и напряженное состояние в неупругой области деформаций и др.).
Коэффициент учитывающий величину напряженного состояния в окрестностях источника определяется как:
Кин |
= |
s-1 |
, |
(5) |
|
||||
|
|
sи |
|
где s-1 – предел выносливости материала; sи – напряжение под испытательной нагрузкой в области источника АЭ, которое определяется из уравнения:
DЕS |
|
C (n×s |
|
) |
|
C (s |
|
) |
|
|
= e |
|
и |
|
- e |
|
и |
, |
(6) |
|
|
|
|
В
где В и С – коэффициенты, значения которых для сталей типа 20ГЛ, 20 ГТЛ определенны в работе [2] и соответственно имеющие значения 436 и 4,5; n – коэффициент – отношение рабочей нагрузки
к испытательной, который в случае АЭ контроля литых деталей тележки составляет 0,8.
Корреляционный параметр a определяется из коэффициентов корреляции сигналов от источника АЭ по формуле:
n |
|
|
å ki,i+1 |
|
|
i =1 |
|
|
a = kср m -1 |
, |
(7) |
где kcp – средний коэффициент корреляции между всеми сигналами источника; ki, i+1 – коэффициент корреляции между двумя соседними по времени прихода сигналами от источника; m – общее число сигналов от источника.
44

Инновационные факторы развития Транссиба на современном этапе. Часть 2
Параметр активности l вычисляется следующим образом:
|
æ tr |
æ |
A |
ö |
F |
ö |
|
|
|
l = К |
ç å |
ç |
max |
÷ |
max |
|
÷ |
, |
(8) |
A |
F ( A |
|
|||||||
1 |
çt =0 |
ç |
÷ |
) ÷ |
|
|
|||
|
è |
è |
Dt |
ø |
max |
ø |
|
|
где К1 – коэффициент, определяемый экспериментально по времени работы до разрушения и зависящий от размерности энергии суммарного счета сигналов АЭ EΣ и размерности параметра ресур-
са; ADt – активность источника сигналов акустической эмиссии в интервале времени Dt; tк – время окончания испытаний; Amax – максимальная активность источника за время испытаний; F(Amax) – нагрузка при максимальной активности источника; Fmax – максимальная нагрузка за время испытания.
Предложенная модель определения параметров ресурса деталей подвижного состава приведена в[5] и была опробована для боковых рам и надрессорных балок грузовых вагонов на основании АЭ данных контроля этих деталей при продлении их времени эксплуатации. Ресурс определяли в количествах циклов нагружения,
2
суммарную энергию сигналов АЭ источника в мВ, поэтому размерный коэффициент К1 равнялся 7,5·10–5. Результаты оценки ресурса некоторых годных к эксплуатации и забракованных деталей приведены в таблице.
Таблица
Результаты испытаний боковых рам с определением их остаточного ресурса в циклах N с вероятностью безотказной работы 0,999
№ детали |
EΣ, мВ2 |
a |
l |
|
Кин |
N |
|
Детали с продленным ресурсом |
|
|
|||
6492 |
2262000 |
0,027 |
3,9·10-5 |
|
0,74 |
9,82·1028 |
20301 |
9765625 |
0,034 |
0,005 |
|
0,6 |
5,77·1019 |
|
|
Забракованные |
детали |
|
|
|
29114 |
2,03E+08 |
0,129 |
0,00003 |
|
0,4 |
209 |
10973 |
2,65·108 |
0,109 |
0,0003 |
|
0,39 |
243 |
569667 |
93779856 |
0,133 |
0,00009 |
|
0,43 |
103 |
Аналогичные результаты получены при испытаниях и продлении ресурса надрессорных балок.
45