
Конспект лекций по курсу “Механика”. Кирпичев Ю.В., Кирпичев И.Ю
.pdfМИНИСТЕРСТВО ОБРАЗОВАНИЯ И НАУКИ РОССИЙСКОЙ ФЕДЕРАЦИИ
Воронежский государственный технический университет
Ю.В. Кирпичев И.Ю. Кирпичев Ю.Б. Рукин
КОНСПЕКТ ЛЕКЦИЙ ПО КУРСУ «МЕХАНИКА»
Часть 2
Утверждено Редакционно-издательским советом университета в качестве учебного пособия
Воронеж 2005
УДК 621.81
Кирпичев Ю.В., Кирпичев И.Ю., Рукин Ю.Б. Конспект лекций по курсу “Механика”: Учеб. пособие. Воронеж: Воронеж. гос. техн. ун-т, 2005. Ч. 2. 112 с.
Конспект лекций содержит основные материалы по расчету и конструированию соединений (сварных, заклепочных, с натягом, клеммовых, резьбовых, штифтовых, шпоночных, шлицевых); передач (ременных, фрикционных, цепных, винт-гайка).
Учебное пособие предназначено для студентов четвертого курса очной формы обучения.
Издание соответствует требованиям Государственного образовательного стандарта высшего профессионального образования по направлению 230100 ”Информатика и вычислительная техника”, специальности 230104 “Системы автоматизированного проектирования”, дисциплине “Механика”.
Учебное пособие подготовлено на магнитном носителе в текстовом редакторе MS WORD и содержится в файле “Мех-2.doc”.
Ил. 50. Библиогр.: 8 назв.
Научный редактор д-р техн. наук, проф. Д.В. Хван
Рецензенты: кафедра |
“Транспортные |
машины” |
Воронежского |
|||
государственного архитектурно-строительного университета |
||||||
(зав. кафедрой д-р техн. наук, проф. Ю.Ф. Устинов); |
|
|||||
канд. техн. наук, доц. Ю.И. Калинин |
|
|
||||
Издается |
по |
решению |
редакционно-издательского |
совета |
Воронежского государственного технического университета
©Кирпичев Ю.В., Кирпичев И.Ю., Рукин Ю.Б., 2005
©Оформление. Воронежский государственный технический университет, 2005
РАЗДЕЛ I. ОБЩИЕ ВОПРОСЫ
ТЕМА 1. ВВЕДЕНИЕ
1.1. Краткий исторический обзор развития конструкций деталей машин
Наиболее ранними грузоподъемными средствами были рычаги, катки и наклонная плоскость (за 2000 лет до н.э.). Позже появились устройства, которыми поднимали груз – веревки, гибкие ветви деревьев, а также ворот, блок.
Древние греки применяли для подъема «журавель». По мере совершенствования появились лебедки и полиспасты. Соединение ворота с блоком или с полиспастом дало толчок к появлению различных типов кранов (поворотных, переносных). Так, в XVII веке в Московском Кремле был поднят с помощью ручных лебедок с использованием противовесов и рычагов Царь-колокол весом более 130 т.
Множество оригинальных проектов подъемных устройств было предложено русскими изобретателями в XVII-XVIII веках. Было предложено устройство для подъема руды, построенное по проекту Кузьмы Дмитриевича Фролова в 1785 году, с использованием для регулирования скорости тормоза.
До XVIII века основными источниками энергии машин были мускульная сила человека или животного и сила падающей воды.
Машина Фролова К.Д. приводилась в движение силой падающей воды, а направление движения менялось изменением потока воды, на правую и левую половину приводного колеса. Появление гидропривода, а затем и парового привода в корне изменило конструкцию машин. Паровой привод позволил рационально объединить в одной машине несколько механизмов.
С 90-х годов прошлого столетия в машинах начинают использовать электропривод, что привело к коренному улучшению конструкций машин. Сначала одномоторный, а затем много моторный приводы позволили рационально и компактно разместить приводные и передаточные механизмы для подъема, передвижения и поворота.
Применение двигателей внутреннего сгорания имело существенное влияние на развитие автономности механизмов и машин.
1.2. Развитие отечественного машиностроения
Началом отечественного машиностроения принято считать XVIII век. Великий механик и изобретатель И.И. Ползунов (1728-1766) впервые разработал проект 2-х двухцилиндрового парового двигателя, сконструировал автоматический регулятор питания парового котла. Выдающийся механик И.И. Кулибин (1735-1818) создал знаменитые часы в
3

форме яйца, представляющие собой сложнейший механизм автоматического действия.
Всвязи с развитием машиностроения как отрасли промышленности появилась потребность в разработке научных методов исследования и проектирования механизмов, входящих в состав машин.
ВРоссии первые машиностроительные заводы появились в XVIII веке,
в1861 году было свыше ста, а в 1900 году примерно 1417 штук. Однако до Октябрьского переворота наше машиностроение сильно отставало. В годы Советской власти в нашей стране было развить мощное машиностроение.
Возвращаясь к русским ученым надо отметить работы в области теории механизмов и машин академика Чебышева П.Л.(1821-1894). Значительный вклад в динамику машин внес своими трудами «отец русской авиации» Н.Е. Жуковский (1847-1921). У него было много работ по прикладной механике.
1.3. Основные пути повышения эффективности машин
Эффективность работы машин зависит от технико-эксплуатационных характеристик данного механизма. Обобщающим параметром, учитывающим условия эксплуатации машины или механизма и степень нагружения их во времени, является номинальный режим работы данного механизма или всей машины в целом.
Нормативные величины, принимаемые при расчете деталей и узлов механизмов машин на прочность, износ, долговечность и нагрев зависят от того, к какому номинальному режиму работы должна быть отнесена данная машина или ее отдельный механизм.
При установлении номинального режима работы, например, кранового механизма, да и различных других машин и механизмов необходимо учитывать шесть следующих факторов:
1. Использование механизма по грузоподъемности Кгр.; характеризуется коэффициентом:
Кгр |
Qср |
|
(1.1) |
||
|
Qном |
где Qср - средняя (за смену) величина поднимаемого груза;
Qном - номинальная (расчетная) грузоподъемность механизма.
2. Использование механизма по времени Кг и Кс; характеризуется коэффициентами:
Кr = число дней работы механизма в году/365 дней;
3.Кс = число часов работы механизма в сутки/24 часа.
4.Среднее использование механизма в течении цикла; характеризуется величиной ПВ (относительная продолжительность включения в %):
4

ПВ |
время работы механизма в течении цикла |
100% |
t |
100% |
|
|
|
(1.2) |
|||||
полная длительность цикла |
T |
|||||
|
|
|
|
где t –суммарная продолжительность тех операций цикла, при которых работал данный механизм;
Т-полная длительность цикла.
5.Число включений механизма в течение часа (среднее за смену).
6.Температура окружающей среды в градусах.
Таким образом, эффективность работы машин зависит от различного сочетания указанных выше факторов.
Необходимо выделить также 5 основных направлений повышения эффективности машин:
1.Повышение надежности и ресурса машин, достигаемое путем обеспечения их необходимого технического уровня, применения деталей и узлов, надежных и долговечных по своей природе, перехода на вероятностные расчеты и др.
2.Уменьшение материалоемкости конструкций путем их оптимизации, совершенствования расчетов, выбора оптимальных и новых материалов и упрочнений.
3.Уменьшение энергозатрат путем обеспечения совершенного трения и повышения КПД механизмов, применением механизмов с особо высоким КПД.
4.Повышение производительность труда в машиностроении путем стандартизации и унификации объектов производства, организации централизованного изготовления узлов и заготовок, оптимизация структуры промышленности, как средства перехода на технологию крупносерийного и массового производства с повышением производительности в десятки раз.
5.Проектирование технологичных деталей под современную прогрессивную материало-, трудо, и энергосберегающую технологию.
1.4.Роль экономических факторов при выборе типов и конструкций
деталей машин
При проектировании новой машины или решении вопроса о применении для заданных условий одной из выпускаемых уде машин, следует провести сравнительный технико-экономический анализ. Анализ проводится в следующей последовательности:
-устанавливаются критерии (показатели) сравнения;
-выбираются один или несколько определяющихся критериев;
-производится сравнение полученных результатов и выбирается оптимальный вариант.
5
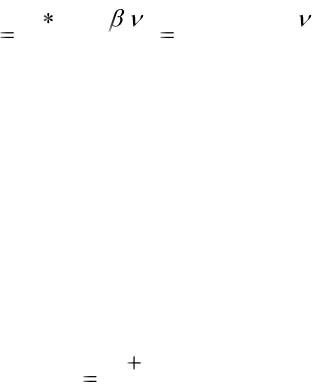
Критериями сравнения для указанных работ являются следующие показатели:
-себестоимость машино-смены работы данной машины;
-эксплуатационная производительность машины;
-затраты, приходящиеся на погрузку 1 т угля;
-капиталовложения;
-трудоемкость (в чел.-час/т);
-степень механизации труда;
-энергоемкость;
-металлоемкость;
Себестоимость машино-смены определяется по следующим статьям затрат:
-заработная плата вспомогательных рабочих;
-отчисления на социальное страхование;
-стоимость электроэнергии или топлива;
-текущий ремонт;
-амортизация;
-услуги обслуживающих производств;
-прочие расходы (расход смазочных материалов, расход обтирочных материалов, износ малоценных и быстроизнашивающихся деталей).
Эксплуатационная производительность машин ПЭ (в т в смену)
определяется:
Пэ |
А 3600 0 0 |
|
3600АК1К2 0 |
|
Т |
|
Т |
(1.3) |
|
|
|
|
где А- длительность смены в часах;
Во = К1*К2;
Vo - объем груза, поднимаемого за один цикл, в м куб.:
К1 - коэффициент использования машин, учитывающий технологические перерывы;
К2 - коэффициент использования машины, учитывающий организационные простои: текущий уход, заправка горючим и топливом, прием и сдача машины и т.п.
Затраты, приходящиеся на погрузку 1 т. угля зависят от себестоимости машино-смены, заработной платы и отчислений на социальное страхование. Зарплата основных рабочих состоит из основной и дополнительной зарплаты и отчислений на социальное страхование.
Затраты Зп на погрузку 1 т. могут быть определены по формуле:
ЗП |
С |
Ф |
|
|
|
руб./т.; (1.4) |
|
|
|
||
|
ПЭ |
Где С- себестоимость машино-смены в руб.; Ф - зарплата основных рабочих в руб.
6
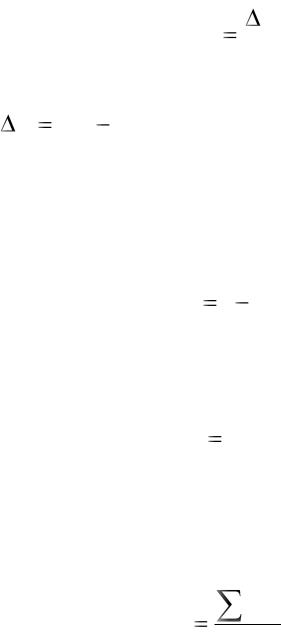
Капиталовложения определяются путем сравнения с аналогичными существующими машинами: сначала определяется стоимость 1 кг металла существующей машины, а затем она умножается на вес проектируемой машины.
Трудоемкость характеризует трудовые затраты, выраженные с человеко-часах на 1 т. груза. Для уменьшения трудозатрат машину следует оснащать автоматическими устройствами, чтобы обойтись минимальным числом занятых рабочих.
Трудоемкость работ влияет на важный экономический показатель – степень механизации труда Км, характеризующий отношение сэкономленных от введения механизмов трудовых затрат Т к трудовым затратам при выполнении тех же работ без механизмов Тр.:
|
|
|
|
|
Км |
Т |
|
|
|
|
|
|
|
(1.5) |
|
|
|
|
Тр. |
||||
|
|
|
|
|
|
||
|
Т |
QC |
|
QC |
|
|
|
Здесь |
qP |
|
|
- человеко-смен в сутки; |
|||
|
|
|
|||||
|
|
|
qM |
|
|
где Qc - суточный объем работ в т.;
qр - норма выработки одного рабочего в смену при ручной погрузке груза
в т.;
qМ - то же при механизированной работе. Следовательно:
КМ 1 |
qP |
|
(1.6) |
||
|
qM |
Энергоемкость Эм показывает стоимость электроэнергии (в квт.ч ) или топлива в кг на 1т груза. При этом следует знать расход за смену электроэнергии или топлива:
ЭМ |
А0С |
|
(1.7) |
||
|
ПЭ |
Где Ао - расход в смену электроэнергии в квт.час или топлива в кг/т; С - стоимость энергии или топлива в руб.
Металлоемкость единицы продукции М характеризуется весом металла в машине или в комплекте машины, отнесенным к сменной эксплуатационной производительности, т.е.:
М МТ
GПЭ (1.8)
7
где Мт - суммарный вес металла в машине или в комплексе машины в
кг.
G - амортизационный срок службы машины в городах.
1.5. Понятие о типизации, стандартизации и агрегатировании
Процесс конструирования машины заключается в следующем:
1.Исходный документ – техническое задание.
2.В разрабатываемой конструкции все детали и сборочные единицы
должны обладать |
одинаковой степенью соответствия требованиям |
||||
надежности, |
точности, |
жесткости, |
прочности |
художественного |
|
конструирования и д.р. |
|
|
|
|
3.Конструированное изделие должно иметь рациональную компоновку сборочных единиц, обеспечивающих малые габариты, удобство сборки, регулировки, замены деталей или сборочных единиц.
4.При создании новых машин необходимо соблюдать конструктивную преемственность и модульный(агрегатный) принцип.
Модульный принцип (агрегатирование) заключается в компоновке машины из отдельных законченных узлов – блоков, соединяемых между собой быстроразъемными соединениями.
5.Конструируемая машина должна отвечать требованиям унификации
истандартизации.
Унификация – рациональное сокращение многообразия видов, типов и типоразмеров изделий одинакового функционального назначения.
Стандартизация – установление и применение единообразия и обязательных требований к изделиям и продукции массового производства.
Взаимозаменяемость – свойство деталей и узлов, позволяющее заменять их без дополнительной обработки с сохранением всех требований к работе данной машины.
1.6. Классификация деталей машин
Машины состоят из деталей. Детали машин – это составные части машин, каждая из которых изготовлена без применения сборочных операций. Количество деталей в машине от нескольких десятков до нескольких тысяч.
Курс «Детали машин» охватывает и совокупность совместно работающих деталей, представляющих собой конструктивно обособленные единицы, объединенные одним назначением и называемые сборочными
8

единицами или узлами(редукторы, коробки передач, муфты, подшипники и т.д.).
Неподвижные и взаимно неподвижные, скрепленные между собой детали называют звеньями. Выполнение звеньев не из одной, а из нескольких соединенных между собой деталей обеспечивает возможность:
1.Изготовление деталей из разных материалов, например, вкладыш подшипников из бронзы, а корпусов из чугуна.
2.Удобной замены быстроизнашивающихся деталей.
3.Сборки (например, установка коленвала двигателя в коренные подшипники выполнима при съемных крышках) и и облегчения сборки машины.
4.Большей стандартизации и централизованного изготовления деталей.
Общая классификация деталей машин.
1.Выполнение машин и их звеньев из различных деталей вызывает
необходимость соединения их между собой. Общая группа деталей является группа соединений (неразъемные и разъемные).
2.Машины состоят из двигательного, передаточного и исполнительных механизмов.
Общими для всех машин являются передаточные механизмы. Двигательные и исполнительные механизмы имеют много специфических деталей.
Для передачи энергии при вращательном движении(наиболее удобном способе передачи механической энергии) в основном применяют передачи, муфты и валы.
Передачи вращательного движения являются механизмами,
предназначенными передавать энергию с одного вала на другой, как правило
сизменением, т.е. с уменьшением или увеличением узловых скоростей и соответственным изменением вращательных моментов.
Передачи разделяют на передачи зацеплением (зубчатые, червячные и цепные передачи) и передачи трением, передающие энергию посредством сил трения, вызываемых начальным натяжением ремня(ременная передача) или прижатием одного катка к другому(фрикционная передача жесткими телами качения).
3.Вращающиеся детали передач (зубчатые колеса, шкивы, звездочки) устанавливаются на валах.
Валы служат для передачи вращающего момента вдоль своей оси и для поддержания деталей передач.
Валы соединяются с помощью муфт. Муфты бывают постоянные, не допускающие разъединения валов при работе машин, и сцепные, допускающие сцепление и расцепление валов.
Валы и оси вращаются в подшипниках (скольжения и качения). Поступательно движущиеся детали поддерживают направляющие
поступательного движения скольжения и качения.
Подшипники и направляющие базируются на основаниях: станинах и других корпусных деталях.
9
4. Для преобразования видов движений (вращательное в возвратнопоступательное, качательное или наоборот), осуществления движений с заданным законом изменения скорости и движения со сложной траекторией применяют шарнирно-рычажные и кулачковые механизмы. К
шарнирно-рычажным механизмам относятся кривошипно-шатунный механизм (двигатель внутреннего сгорания). Основные детали шарнирнорычажных механизмов – кривошипы, шатуны, коромысла, направляющие, кулисы, ползуны. Основные детали кулачковых механизмов – кулачки, эксцентрики, ролики.
5.В большинстве машин необходимо использовать упругие элементы: пружины или рессоры. Их применяют для защиты от вибраций и ударов (автомобили, вагоны), для совершения в течение длительного времени полезной работы путем предварительного аккумулирования или накапливания энергии (заводные пружины в часах); для осуществления обратного хода в кулачковых и др. механизмах; для соединения натяга.
6.Для повышения равномерности движения, уравновешивания деталей машин и для накопления энергии в целях повышения силы удара или для ее восприятия применяют детали, использующие для выполнения своих функций массу – маховики, маятники, грузы, бабы, шаботы.
7.Долговечность машин в значительной степени определяется устройствами для защиты от загрязнений и для смазывания.
8.Важную группу составляют детали и механизмы управления. Значительные группы составляют детали специфические (имеющие
наибольшее применение) для отдельных групп машин.
Для энергетических машин наиболее характерными являются цилиндры, поршни, клапаны, лопатки и диски турбомашин, роторы и статоры электрических машин.
Для транспортных машин характерны: колеса, рельсы, гусеницы, винты водяные и воздушные, крюки, ковши и др.
Для машин-орудий специфическими являются: валки, шаботы, бабы, патроны, суппорты, лемехи, отвалы, веретена, катушки, челноки и др.
10