
2395
.pdf
этом случае отверстие для подвода СОЖ в корпусе для сверла с СМП закрыто корпусом резца.
Рис. 21. Резцовый блок с продольным пазом Рис. 22. Блок с централь-
ным цилиндрическим отверстием
В случае крепления шары поворачивают на 90°, перекрывая в корпусе отверстие, и СОЖ подается по каналам через отверстие в корпусе блока во внутренний канал сверла.
Прямые головки для вращающегося инструмента (с цанговым патроном, с конусом Морзе и резьбонарезная) отличаются только конфигурацией шпинделя, поэтому особенности их конструкций рассмотрены на примере головки с цанговым патроном (рис. 23). В головке могут закрепляться режущие инструменты с диаметром хвостовика до 20 мм. Головка состоит из корпуса 2 и шпинделя 1, установленного в подшипниках 3—5, натяг которых обеспечивается пружинящей гайкой 8.
71
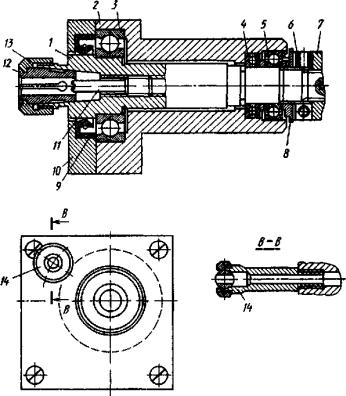
Рис. 23. Прямая вращающаяся головка с цанговым патроном
Уплотнение подшипника 3 со стороны рабочей зоны осуществляется манжетой 9, расположенной в крышке 10. Регулирование осевого положения муфты 7, через которую передается крутящий момент, производится с помощью гайки 6. Для закрепления режущих инструментов с цилиндрическим хвостовиком (фрез, сверл) используются унифицированные элементы: гайка 13, цанга 12 и регулировочный винт 11. СОЖ подается в зону резания с помощью сопла 14.
Угловые головки для вращающихся инструментов так же, как и прямые, отличаются только шпинделем. Угловая го-
72
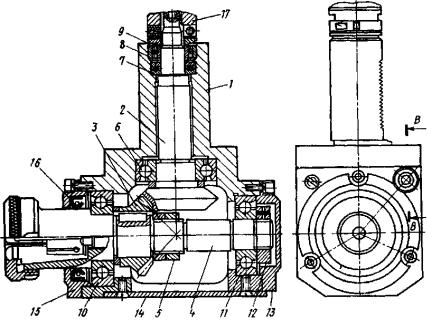
ловка с цанговым патроном представлена на рис. 24. В корпусе 1 размещена коническая передача (передаточное отношение 1), состоящая из ведущего вала-шестерни 2 и ведомой шестерни 3, закрепленной на валу-шпинделе 4 гайками 5. Валшестерня устанавливается в корпусе в подшипниках 6—8, натяг которых обеспечивается пружинящей гайкой 9, а шпиндель
— в подшипниках 10, 11, которые стягиваются гайкой 12. От внешних воздействий шпиндельный узел защищен крышками 13—15, причем в крышке 15 размещена уплотнительная манжета 16. Регулирование осевого положения муфты 17, передающей крутящий момент, подача СОЖ в зону резания и закрепление режущего инструмента осуществляются, так же, как и у прямой головки.
Рис. 24. Угловая вращающаяся головка с цанговым патроном
73
Все рассмотренные выше вращающиеся головки предназначены для работы с частотой вращения до 2500 мин-1; максимальный крутящий момент 50 Н·м.
1.3. Контрольно-измерительные устройства, встраиваемые в станки и станочные системы
1.3.1. Назначение контрольно-измерительных устройств
Контрольно-измерительные устройства необходимы для получения информации о состоянии станка, инструмента, обрабатываемой детали и окружающей среды. Ниже рассмотрим лишь встроенные в станок контрольно-измерительные устройства, сигналы которых используют в системе его управления.
Контроль состояния самого станка осуществляется по многим параметрам. В современных станках используют датчики (преобразователи) для регистрации силовых факторов, упругих перемещений, амплитуды вибраций, температуры и взаимного положения узлов станка. Обрабатываемая деталь контролируется в ответственных случаях до обработки на станке (контроль заготовки), в процессе обработки и после обработки (контроль изделия). Режущий инструмент проверяется по затуплению, размерному износу и отсутствию поломок.
Роль контрольно-измерительных устройств возрастает с повышением степени автоматизации станков и станочных систем. К контрольным и измерительным устройствам в станках предъявляют ряд требований.
1.Погрешность самого измерительного устройства должна быть на порядок ниже допустимой погрешности контролируемой величины. Под погрешностью измерительного устройства обычно подразумевают разность между измеренным и фактическим значениями контролируемой величины.
2.Порог чувствительности измерительного устройства также должен быть на порядок ниже общего порога чувстви-
74
тельности всей цепи обратной связи в системе автоматического управления. Под порогом чувствительности подразумевают минимальное изменение входного параметра (контролируемой величины), способное вызвать изменение выходного параметра. На порог чувствительности в условиях смешанного трения большое влияние оказывает скачкообразное скольжение.
3.При конструировании контрольно-измерительных устройств следует по возможности соблюдать принцип Аббе, согласно которому измеряемую величину и образец (эталон) надо располагать на одной прямой. По принципу Аббе, в частности, необходимо расположение направляющих в одной плоскости с измеряемым объектом.
4.Контрольно-измерительные устройства в системах автоматического управления должны обладать достаточным быстродействием, т. е. обеспечивать измерение переменной во времени величины в требуемом частотном диапазоне. Это требование важно для контроля быстропротекающих переходных процессов, связанных с врезанием и выходом инструмента, резким изменением направления движения узла станка и т. п. Постоянная времени контрольно-измерительных устройств должна быть на порядок меньше постоянной времени контролируемого объекта. Так, например, постоянная времени современных приводов станков лежит в пределах 0,02...0,05 с.
5.Важным требованием, которое предъявляют к измерительным устройствам, встраиваемым в станки, является то, чтобы эти устройства не ухудшали существенно характеристики тех узлов, в которые их встраивают. Так, высокие требования к порогу чувствительности измерительных устройств могут повлечь за собой снижение жесткости и динамических характеристик станка в такой степени, что это отрицательно сказывается на точности обработки. Датчики контрольноизмерительных устройств должны иметь небольшие габариты
иудобно встраиваться в узел станка, не изменяя существенно его конструкцию.
6.Надежность контрольно-измерительных устройств должна быть весьма высокой, особенно в тех случаях, когда их
75
отказ может вызвать аварийную ситуацию и вывести из строя ответственный узел станка.
Рассмотрим контрольно-измерительные устройства, встраиваемые в станки, в соответствии с их основным функциональным назначением.
1.3.2. Контроль заготовок и инструмента
Контроль заготовок предусматривает измерение фактических их размеров. При крупносерийном и массовом производстве однотипных деталей размеры их заготовок должны укладываться в поле допуска для нормальной работы зажимных приспособлений и стабильности точности настройки станка. В универсальных обрабатывающих системах контроль размеров заготовок необходим для их идентификации и для использования этой исходной информации в целях оптимизации технологического процесса.
Устройства для контроля габаритов заготовок в автоматических линиях обычно представляют собой стационарный проходной шаблон. Заготовки, прошедшие шаблон, передаются на последующую обработку, а заготовки, не прошедшие контрольную позицию, удаляются из потока. Контроль отверстий и полостей в заготовках осуществляют обычно на комбинированных устройствах с выдвижными упорами.
Универсальные устройства обычно не только измеряют все необходимые поверхности, но различают и окончательно устанавливают заготовки по результатам измерений в целях оптимального распределения припуска. Результаты визуального осмотра и данные измерения поступают на пульт ручного управления или в логическое устройство управляющей ЭВМ. Контрольное устройство управляется системой ЧПУ,
Контроль режущего инструмента включает проверку наличия и целостности каждого инструмента перед операцией и контроль износа его рабочих поверхностей.
Контроль целостности инструмента типа сверл, разверток, зенкеров осуществляется устройствами, использующими
76
индуктивные, электроконтактные, фотоэлектрические и пневматические датчики. Также используют устройства генераторного типа, которые обладают высокой чувствительностью и пригодны для обнаружения выкрашивания режущей кромки инструмента. Наиболее удобны и перспективны те устройства для контроля целостности инструмента, которые проверяют инструмент в его исходной позиции, а не во время ускоренного перемещения к обрабатываемой детали.
Контроль износа режущего инструмента приобретает особое значение с повышением степени автоматизации и по мере распространения систем адаптивного управления. В качестве основного критерия износа чаще всего используют величину износа по задней поверхности режущего инструмента, так как его более удобно измерять, и он достаточно полно отражает режущую способность инструмента. Обычно контролируют среднюю ширину площадки износа по задней поверхности, которую называют также фаской износа. Фотоэлектрический метод измерения износа основан на том, что угол отражения на изношенном участке задней поверхности отличается от угла отражения неизношенного участка, расположенного под главным задним углом α. Если фототранзистор регистрирует отраженное световое излучение, то его показания будут существенно при этом различаться. При установке фотоэлектрического устройства у вращающейся фрезы каждый зуб, проходя перед датчиком, будет формировать импульсный сигнал, регистрируемый счетчиком импульсов. Длительность импульсов пропорциональна ширине площадки износа по задней поверхности.
Величина размерного износа в направлении, перпендикулярном обрабатываемой поверхности, может быть измерена теми же способами, которые используют при активном контроле на станках. Если датчик, измеряющий обработанную поверхность, расположить на режущем инструменте в непосредственной близости от режущей кромки, то он будет измерять положение задней поверхности в зависимости от величины из-
77
носа. Используют электроконтактные или пневматические датчики.
Величину износа режущего инструмента можно контролировать косвенным путем по изменению составляющих силы резания, которые связаны с износом зависимостью, близкой к линейной. Измерение составляющих силы резания дает возможность судить о скорости изнашивания и не этом основании
отекущем значении стойкости режущего инструмента.
Вкачестве косвенного метода для контроля износа режущего инструмента используют также измерение температуры в зоне резания. Для степенной зависимости стойкости инструмента по износу от температуры необходима высокая точность измерения температуры в зоне резания. Если ограничить погрешность измерения 20% стойкости, то температуру следует измерять с ошибкой не более ±5°С. Часто для измерения температуры в зоне резания применяют метод естественной термопары.
1.3.3. Контроль силовых параметров
Измерение сил и моментов, возникающих в процессе обработки на станках, необходимо для наблюдения за процессом резания и его оптимизации в системах адаптивного управления, а также для предохранения ответственных узлов станка и инструмента от возможных перегрузок. Наибольшие трудности при встраивании датчиков в конструкцию узлов станка возникают в связи с тем, что основные характеристики элементов станка (жесткость, виброустойчивость) не должны сильно изменяться, а также не должны сужаться технологические возможности и универсальность оборудования.
Большинство методов измерения силовых параметров основаны на преобразовании упругого перемещения, возникающего под действием силы или момента, в соответствующий электрический сигнал. Искусственное снижение жесткости для получения упругого перемещения значительной величины в большинстве случаев для станков недопустимо; поэто-
78
му датчики упругих перемещений должны обладать высокой чувствительностью. При записи нагрузок в переходных процессах, связанных, например, с врезанием и выходом инструмента, необходимо высокое быстродействие датчиков. Постоянная времени, как правило, не должна превышать 0,002...0,005 с. Контроль силовых параметров в станках с ЧПУ и с адаптивным управлением должен обеспечивать высокую надежность с наработкой на отказ не менее 350...400 ч.
В качестве датчиков при измерении упругих перемещений в станках наибольшее распространение получили полупроводниковые тензорезисторы (кремниевые и германиевые) и магнитоупругие датчики, использующие эффект магнитострикции. Индуктивные, фазоимпульсные и некоторые другие типы датчиков применяют главным образом в предохранительных устройствах, ограничивающих допустимые значения сил и моментов.
1.3.4. Средства активного контроля обрабатываемых деталей
Контроль деталей при их обработке на станках получил название активного контроля на том основании, что результаты измерения всегда используют как дополнительную информацию для системы управления станком. Принципиальная сложность измерения детали в процессе обработки состоит в том, что измеряется уже обработанная поверхность. Таким образом, результаты измерения могут быть использованы лишь для управления последующей обработкой (для других деталей или других поверхностей обработки). Лишь в тех случаях, когда при обработке на станке осуществляется постепенный подход к заданному размеру, как это имеет место при врезном шлифовании, или обработка ведется за много проходов, можно использовать результаты измерения для управления точностью обработки на станке. Именно в силу этого обстоятельства системы активного контроля получили наибольшее распространение в шлифовальных станках.
79
Контактные датчики при подходе к заготовке дают сигнал о переходе с ускоренного перемещения на рабочую подачу. При шлифовании ступени на детали датчики дают команду на ограничение продольной подачи при сходе со ступени или упирании датчика в торец соседней ступени большего диаметра. При врезном шлифовании датчики могут быть использованы для подачи команды на выключение поперечной подачи в тот момент, когда диаметр обрабатываемой детали достаточно близок к заданному. Измерительную головку с соответствующими датчиками, преобразующими тот или иной сигнал, как правило, в электрическую величину, располагают в непосредственной близости к обрабатываемой детали. Образованный в процессе резания размер измеряется непрерывно или периодически. Результаты измерения усиливаются и передаются в систему управления.
Средства активного контроля обычно различают по типу датчиков, используемых в измерительной головке.
Измерительные головки с электроконтактными датчиками отличаются значительными габаритами, и поэтому их чаще используют для периодического контроля путем ввода головки в зону обработки. Кроме того, устройства этого типа применяют для контроля деталей, перемещенных из зоны обработки в специальную измерительную позицию.
Используют различные варианты схем измерительных головок с двумя контактами. Общим в этих схемах является то, что один из контактов жестко связан с корпусом измерительной головки, а другой имеет одну степень свободы. Относительное перемещение контактов фиксируется датчиком — электроконтактным, фотоэлектрическим, индуктивным. Встречаются измерительные головки с тремя контактами, которые используют обычно для контроля длинных валов, поскольку при измерении эти головки могут перемещаться вдоль оси вала и нет необходимости в поперечной подаче.
В качестве примера реализации средств активного контроля рассмотрим устройство для контроля размеров в процессе обработки на круглошлифовальном станке (рис. 25).
80