
2395
.pdf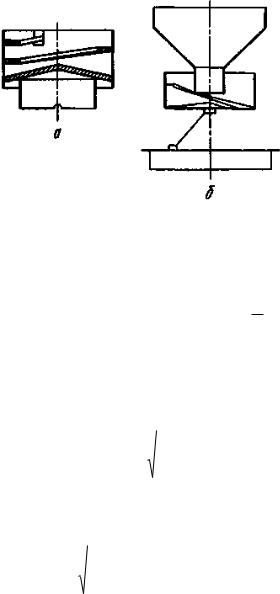
Рис. 30. Схемы одноемкостного (а) и многоемкостного (б) бункеров
где Vд - объем детали, см3; τ - время непрерывной работы бункера (без досыпки), мин; t - такт сборки; q - коэффициент объемного заполнения (для простых деталей q = 0,4...0,6, причем
чем сложнее и длиннее деталь, тем меньше q); Q - средняя
производительность устройства, шт/мин.
Наибольшее распространение в промышленности получили вибробункеры. При их применении рассчитывают диаметр чаши. Для чаши цилиндрической формы (рис. 31, а)
Dц Dв 2bст 3 |
VдПц |
|
2bст , |
Н расч |
|
||
|
|
|
для чаши конической формы (рис. 31, б)
|
|
|
|
|
|
|
|
|
|
Н |
24Vд Пц |
|
|
|
|||||
D D |
|
0,75 1,5 |
|
1 |
2b , |
||||
|
|
||||||||
к в Н расч |
|
Dв2Н расч |
|
|
|
|
ст |
||
|
|
|
|
|
|
|
|
|
91
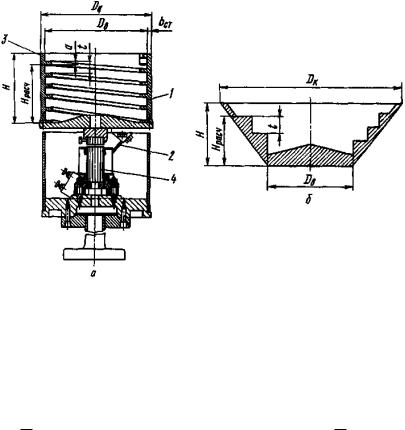
где Dв ≥ (5... 10) lд - внутренний диаметр чаши бункера у днища, мм; bст - толщина стенки, мм (для точеных чаш bст = 2 ... 3
мм, для сварных bст = 1... 1,5 мм); Vд - объем детали, мм3; Пц - цикловая производительность, мин; Нрасч - высота заполнения
бункера, мм; lд -длина детали в преобладающем положении при перемещении по лотку, мм.
Рис. 31. Элементы конструкции вибробункера:
а - вибробункер с цилиндрической чашей; б -коническая чаша вибробункера; 1, 2 - пружинная подвеска; 3 - лоток; 4 - вибропривод
Полная высота чаши бункера Н = Нрасч +(1,0 ...1,5)t, где
t = π D tgβ - шаг подъема спирального лотка, мм; D - средний диаметр лотка, мм; β = 0,5... 3° - угол подъема лотка.
Рассчитанные диаметры чаш бункеров округляют в большую сторону до числа из стандартного ряда: 60, 100, 120, 160, 200, 250, 320, 400, 450, 500, 640, 800, 1000 мм. По общей
92
вибрирующей массе и необходимой производительности рассчитывают вибропривод.
2.2. Ориентирующие устройства
Рассмотрим кратко ориентирующие устройства, используемые при сборке.
При автоматизированной сборке ориентирующие устройства выполняют две функции: ориентируют присоединяемые детали в пространстве и осуществляют взаимную ориентацию сопрягаемых поверхностей перед выполнением соединения в зоне сборки.
Метод ориентации деталей в пространстве зависит от их конструкции, массы, материала и уровня автоматизации. Различают контактные и бесконтактные методы. При контактном методе ориентация детали происходит под воздействием твердого, жидкого или газообразного тела, при бесконтактном методе - под воздействием электрического, магнитного или электромагнитного поля.
По виду конструкции эти ориентирующие устройства бывают пассивные и активные. Используя гравитационные силы или конструктивные элементы деталей, пассивные ориентирующие устройства (рис. 32, а) неправильно сориентированные детали сбрасывают обратно в бункер, а правильно сориентированные - пропускают в лотке в зону сборки. Активные устройства всем неправильно сориентированным деталям придают нужное положение в пространстве. В качестве примера на рис. 32, б показано устройство, где присоединяемая деталь - керн 2 в магнитной катушке 1 - получает определенную полярность, что позволяет ей ориентироваться на лотке 4 под воздействием постоянного магнита 3. Переключатель 5 обеспечивает нужную полярность в катушке 1 в зависимости от положения керна 2.
Механические ориентирующие устройства способны различать конструктивные элементы детали размером не менее 0,3 мм, оптические - не менее 0,01... 0,05 мм, элек-
93
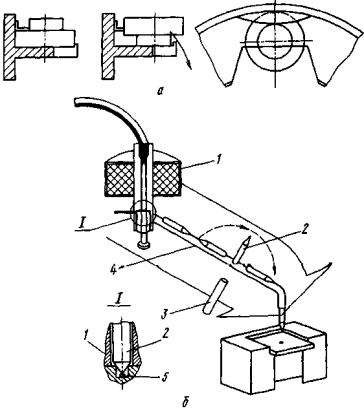
тромагнитные - не менее 0,01... 0,1 мм (в зависимости от массы детали и чувствительности датчика), пневматические - не ме-
нее 0,02 ... 0,03 мм.
Рис. 32. Пассивное (а) и активное (б) ориентирующие устройства
Ориентирующие устройства для взаимной ориентации сопрягаемых поверхностей в зоне сборки чаще всего выполняют механическими. Оптимальные параметры ориентирующего устройства и его положения в зоне сборки (зазор между ориентирующей поверхностью и присоединяемой деталью, жесткость упругих элементов, расстояние ориентирующего
94

устройства до торца базовой детали) зависят от параметров соединения, погрешностей положения сопрягаемых поверхностей и режимов сборочного процесса. Их определяют по математическим моделям, полученным на базе многофакторных экспериментальных исследований автоматического процесса выполнения соединения.
3. Методика расчета экономической эффективности применения технологической оснастки
При конструировании специального приспособления необходимо обосновывать экономическую целесообразность его изготовления и эксплуатации. В расчетах на рентабельность обычно сопоставляют различные конструктивные варианты приспособления для выполнения одной и той же технологической операции. Если считать, что расходы на режущий инструмент, амортизацию станка и электроэнергию одинаковы, то элементы себестоимости обработки, зависящие от конструкции приспособления, для сравниваемых вариантов а и b
Ca
Cb
|
|
La 1 |
|
|
|
|
|
Lb 1 |
|
|
|
zSa 1
100 n i
zSb 1
100 n i
q |
|
|
|
S' |
||
|
|
|
a |
; |
||
|
|
|
||||
100 |
|
|
|
n' |
||
q |
|
|
|
S' |
||
|
|
|
|
b |
, |
|
|
|
|
||||
100 |
|
|
|
n' |
где
(1)
(2)
Са — себестоимость изготовления приспособления по варианту а, руб.;
La — штучная заработная плата при использовании этого приспособления, руб.;
Сb — себестоимость изготовления приспособления но варианту b, руб.;
Lb — штучная заработная плата при этом приспособлении, руб.;
95
z — цеховые накладные расходы на заработную плату,
%;
q — расходы, связанные с применением приспособлений (ремонт, содержание, регулирование), %;
i — срок амортизации приспособления, годы; n — годовая программа выпуска деталей, шт.;
Sa' , Sb' — расходы на конструирование и отладку при-
способлений по вариантам а и b, руб.;
n' — число деталей, обрабатываемых в приспособлении за период освоения выпускаемой продукции.
Расходы на конструирование и отладку относят на первые образцы нового изделия или распределяют на себестоимость изделия в течение одного-двух лет его производства. Сопоставление экономической эффективности приспособлений по вариантам а и b для установившегося периода производства, когда расходы на конструирование и отладку погаше-
ны, можно производить по формулам (1) и (2), приняв Sa' =
= Sb' = 0.
Величину программы выпуска деталей, при которой оба сопоставляемых варианта в экономическом отношении равноценны, находим, решая совместно уравнения (1) и (2) относительно n:
|
|
|
|
|
|
1 |
|
|
q |
|
|
|
||
|
S |
|
S |
|
|
|
|
|
|
|
||||
|
b |
a |
|
|
|
|
|
|
|
|||||
|
|
|
|
|
|
|
||||||||
|
|
|
|
|
|
|
|
|
|
|
|
|||
n |
|
|
|
|
i |
|
|
100 |
. |
(3) |
||||
|
|
|
|
|
|
|
|
|
z |
|
||||
|
|
|
|
|
|
|
|
|
|
|
||||
|
L |
L |
|
1 |
|
|
|
|
||||||
|
|
|
|
|
|
|||||||||
|
|
|
|
|
||||||||||
|
|
a |
|
b |
|
|
|
|
|
|
|
|
|
|
|
|
|
|
|
|
|
|
|
100 |
|
|
Если заданная программа больше рассчитанной по формуле (3) величины n, то выгоднее применять более сложное приспособление, и наоборот.
Для расчета n нужно знать величины Sa и Sb. Их точные значения можно определить на основе калькуляций после составления рабочих чертежей и разработки технологических
96
процессов изготовления приспособлений. Однако этот способ сложен и трудоемок, задание же на конструирование приспособления должно выполняться в короткие сроки. Поэтому применяют более простые, приближенные способы определения затрат на изготовление приспособлений. Для ориентировочных расчетов можно пользоваться приближенной формулой
S = СК,
где S — себестоимость изготовления приспособления, руб.;
К — число деталей в приспособлении; С — постоянная, зависящая от сложности приспособления. Для простых приспособлений С = 1,5, для приспособлений средней сложности С = 3,0 и для сложных С = 4,0.
Величину i берут равной сроку (год), в течение которого конструируемое специальное приспособление будет использовано для выпуска заданной продукции. Если, например, данные детали выпускаются в течение двух лет, то и i также принимается равным двум годам. Если производимая продукция стабильна и сроки прекращения ее выпуска неизвестны, то i рекомендуется брать для простых приспособлений равным одному году, для приспособлений средней сложности — от двух до трех лет и для сложных — от четырех до пяти лет. Величину q рекомендуется брать равной 20 %. Для определения L нужно знать штучное время на данную операцию tш и минутную заработную плату рабочего l: L = tшl.
У сопоставляемых вариантов эти величины различны. При использовании более совершенного приспособления tш и l снижаются в результате уменьшения основного и вспомогательного времени, а также облегчения условий труда и упрощения выполняемых манипуляций.
Расчет по формуле (3) необходимо выполнять при усло-
вии, что Sa > Sb и Lb > La или Sb > Sa и La > Lb. При иных условиях (Sa > Sb и La > Lb или Sb > Sa и Lb > La) при любом n следует применять вариант b или а.
97
Использование приспособлений часто вызывает изменение технологического процесса в связи с ликвидацией или видоизменением отдельных операций. В этом случае можно сопоставить себестоимость механической обработки детали, зависящей от оснастки, не по отдельным операциям, а по процессам:
|
|
|
|
z |
|
|
S |
1 |
|
|
|
q |
|
|||||
CI |
I L 1 |
|
|
|
|
|
|
|
I |
|
|
|
|
|
|
|
; |
|
100 |
n |
|
|
|
100 |
|||||||||||||
|
|
|
|
|
i |
|
|
|
||||||||||
|
|
|
|
z |
|
|
S |
|
1 |
|
|
q |
|
|||||
CII II L 1 |
|
|
|
|
|
|
II |
|
|
|
|
|
|
|
, |
|||
100 |
n |
|
|
|
|
|
|
|||||||||||
|
|
|
|
|
i |
|
|
|
100 |
где индексы I и II относятся к сопоставляемым вариантам процессов.
Если в сопоставляемых вариантах применяется различное оборудование (например, горизонтально-расточный станок заменяется вертикально-сверлильным), то, учитывая дополнительную стоимость 1 мин работы станка lст, получим
CI
CII
tшl1 |
|
|
|
z |
|
tшlстI |
||
1 |
|
|
|
|
||||
100 |
||||||||
|
|
|
|
|
||||
tшl1I |
|
|
|
z |
|
tшlстII |
||
1 |
|
|
|
|
||||
100 |
||||||||
|
|
|
|
|
|
S |
I |
|
1 |
|
|
|
q |
|
|||||
|
|
|
|
|
|
|
|
|
; |
|||||
|
|
|
|
|
|
|
|
|||||||
|
|
n |
|
i |
|
|
100 |
|
||||||
|
S |
II |
1 |
|
q |
|
|
|||||||
|
|
|
|
|
|
|
|
. |
||||||
|
|
|
|
|
|
|
||||||||
|
|
n |
|
i |
|
|
100 |
Рассмотрим теперь себестоимость обработки, если данная технологическая операция выполняется на переналаживаемом универсальном приспособлении, оснащенном сменной наладкой:
|
|
z |
|
|
S y |
1 |
|
q |
|
|
S |
н |
|
1 |
|
q |
|
|
S' |
||
C L 1 |
|
|
|
|
|
|
|
|
|
|
|
|
|
|
|
|
|
|
н |
, |
|
|
|
|
|
|
|
|
|
|
|||||||||||||
|
|
100 |
|
|
N |
|
|
|
100 |
|
|
N |
|
|
|
100 |
|
|
N |
||
|
|
iy |
|
|
|
iн |
|
|
|
98
где Sy — стоимость универсального приспособления; Sн — себестоимость изготовления сменной наладки; iy — число лет амортизации универсального приспособления; iн — число лет
амортизации сменной наладки iy > iн; Sн' — расходы на конст-
руирование и отладку сменной наладки. Расходы Sн' относят
на первый год выпуска изделий.
Приведенная формула может быть использована для сопоставления рентабельности различных вариантов переналаживаемых приспособлений или специального и переналаживаемого приспособлений.
99
ЗАКЛЮЧЕНИЕ
Технологическая оснастка - орудия производства, дополняющие технологическое оборудование для выполнения определенной части технологического процесса.
К технологической оснастке относятся: приспособления; режущий инструмент; вспомогательный инструмент; кон- трольно-измерительный инструмент.
Станочное приспособление - технологическая оснастка, предназначенная для закрепления заготовки на станке при выполнении технологической операции. Приспособления являются наиболее сложной и трудоемкой частью технологической оснастки.
Сложность построения технологических процессов в машиностроении обуславливает большое разнообразие конструкций приспособлений и высокий уровень предъявляемых к ним требований.
Применение приспособлений расширяет технологические возможности металлорежущего оборудования.
Для решения задач интенсификации производства, улучшения качества и снижения себестоимости продукции машиностроительные предприятия располагают разнообразными приспособлениями для станков.
Основное направление интенсификации машиностроения
— механизация и автоматизация производственных процессов. Поэтому необходимо создавать приспособления с механизированными приводами зажимных устройств, автоматизированным и автоматическим циклами работы.
Вспомогательный инструмент выбирают по уже выбранному режущему инструменту. Вспомогательный инструмент должен иметь, с одной стороны, установочные поверхности и элементы крепления, соответствующие режущему инструменту, а с другой - поверхности установки и элементы крепления, соответствующие посадочным местам станка.
Существующие конструкции приспособлений в дальнейшем будут совершенствоваться в направлении типизации
100