
1276
.pdf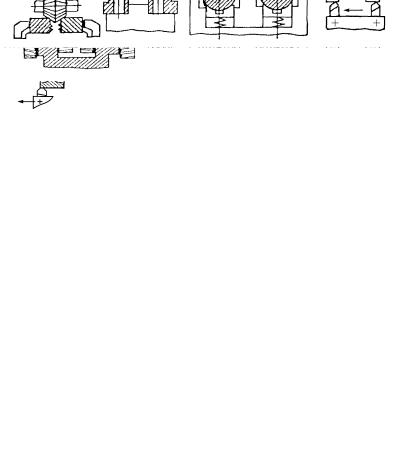
а |
б |
в |
г |
Рис. 1.3. Схемы одноместной параллельной многоинструментальной обработки
Рис. 1.4. Схемы многоместной многоинструментальной обработки
При многоместной обработке заготовок, расположенных в приспособлении рядами вдоль и поперек движения подачи, операция характеризуется как «операция с параллельнопоследовательной обработкой». Схемы многоместной парал- лельно-последовательной обработки представлены на рис. 1.5.
Многоместные схемы обработки дают возможность совмещения как основного, так и вспомогательного времени, за счет чего обеспечивается повышение производительности.
21
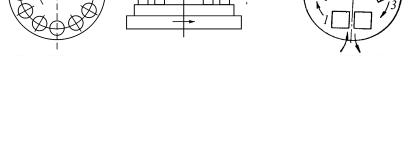
а |
б |
в |
Рис. 1.5. Схемы многоместной параллельно-последовательной обработки: а – с одновременной, б, в – раздельной установкой заготовок: а – плоское шлифование заготовок; б – фрезерование на поворотном столе со сменой группы заготовок; в – обработка на вертикальном полуавтомате: 1 – позиция загрузки; 2, 3 – позиции обработки заготовок
Многоместная параллельно-последовательная обработка с раздельной установкой заготовок не только дает возможность совмещать время установки заготовок с основным временем, сокращая общие затраты вспомогательного времени, но и позволяет осуществить частичное совмещение основного времени переходов.
Наибольшую производительность обработки обеспечивает многоместная параллельно-последовательная обработка с непрерывной установкой и сменой обрабатываемых заготовок на станке.
1.4. Исходные данные для проектирования технологических процессов механической обработки деталей машин
При проектировании технологического процесса механиче-
ской обработки исходными данными являются размер и срок выполнения производственной программы, составленной на основании общей производственной программы завода, рабочие чертежи и технические условия изготовления и приемки детали (изделия).
22
При проектировании технологических процессов необходимо учитывать общую производственную обстановку (состав
истепень загрузки оборудования, обеспеченность предприятия инструментами, приспособлениями, квалифицированной рабочей силой и т.п.), а также располагать нормативными, справочными и руководящими материалами, каталогами оборудования
итехнологической оснастки.
Размер и содержание производственной программы (про-
граммного задания) завода и программы по выпуску конкретных деталей для отдельных цехов и участков зависит от установленного объема выпуска изделий, то есть от количества изделий определенных наименований, типоразмера и исполнения, изготавливаемых или ремонтируемых предприятием или его подразделением в течение планируемого интервала времени.
Чертежи должны включать: рабочие чертежи деталей выпускаемых изделий; сборочные чертежи узлов и отдельных механизмов (агрегатов); чертежи общих видов изделий. К чертежам прилагаются спецификации деталей по каждому изделию, описание конструкций и, если возможно, рисунки или фотографии изделий.
На рабочих чертежах, необходимых для проектирования технологических маршрутов процессов обработки деталей на металлорежущих станках, должны быть указаны: материал детали и его марка; обозначения шероховатости после обработки; допуски на точность обработки; вид термической обработки.
На сборочных чертежах и общих видах должны быть ука-
заны: конструктивные зазоры; допуски на размеры, определяющие взаимное расположение деталей; особые требования, касающиеся сборки соединений или монтажа всего изделия.
В спецификациях деталей по каждому изделию должны быть указаны: наименования всех деталей (включая покупные); вес (масса) – чистый и черный; вид материала; количество деталей на одно изделие; для нормализованных деталей – обозначение стандарта.
Описание конструкции изделий должно давать правильное и полное представление об их работе, назначении и функциях отдельных частей и их взаимодействии.
23
Технические условия изготовления и сдачи деталей или изделий определяют требования, предъявляемые к его деталям
ик изделию в целом.
1.5.Общие правила разработки технологических процессов
иосновные принципы составления технологических маршрутов
механической обработки заготовок
Общие правила организации и управления процессом технологической подготовки производства регламентированы Р-50-54-94–88. Этим документом определены следующие основные этапы разработки технологического процесса, выполняемые в определенной последовательности:
•анализ исходных данных;
•определение типа производства;
•определение класса детали и выбор в качестве аналога действующего типового или группового технологического процесса;
•выбор исходной заготовки и методов ее изготовления;
•выбор технологических баз;
•план обработки отдельных поверхностей;
•составление технологического маршрута обработки;
•разработка технологических операций;
•нормирование технологического процесса;
•определение требований техники безопасности;
•расчет экономической эффективности технологического процесса;
•оформление технологической документации.
Прежде чем приступить к проектированию технологического процесса механической обработки, необходимо тщательно изучить сборочный чертеж изделия и (или) рабочий чертеж детали с соответствующими техническими условиями изготовления.
Кроме того, необходимо изучить и такие дополнительные условия проектирования, как наличие или отсутствие оборудования, на котором предполагается осуществить изготовление
24
проектируемого изделия; возможности применения совершенных видов исходных заготовок, прогрессивного инструмента и приспособлений, и т.п.
Проектирование технологических процессов представляет собой сложную многовариантную задачу, для решения которой необходимо составить несколько возможных конкурирующих вариантов обработки.
Окончательный выбор одного из вариантов производится на основании расчетов и сопоставления, достигаемых точности, трудоемкости, выражаемой нормой штучного или штучнокалькуляционного времени, технологической себестоимости
исрока окупаемости капитальных затрат. Такое сопоставление производится как по важнейшим технологическим операциям, так и по всему технологическому процессу в целом.
По величине программного задания определяют коэффициент закрепления операций, тип производства, необходимые такт
иритм обработки заготовок и разрабатывают рациональный технологический маршрут механической обработки.
При составлении технологического маршрута процесса механической обработки заготовки технолог руководствуется следующими основными принципами.
При низкой точности исходных заготовок технологический маршрут начинается с черновой обработки поверхностей, имеющих наибольшие припуски. При этом в первую очередь снимается припуск с тех поверхностей, на которых возможны литейные раковины, трещины и другие дефекты, с целью скорейшего отсеивания возможного брака или устранения обнаруженных дефектов заваркой, наплавкой металла и т.п.
Вдальнейшем технологический маршрут строится по принципу обработки сначала более грубых и затем – более точных поверхностей.
Наиболее точные и (или) легкоповреждаемые поверхности (наружные резьбы, особо точные шлифованные и доведенные поверхности) выполняют на заключительных этапах технологического маршрута.
Вконце технологического маршрута размещают второстепенные операции (сверление мелких отверстий, нарезание крепежных резьб, прорезка пазов, снятие фасок и заусенцев).
25
При обработке заготовок, подвергающихся термической обработке, в технологическом маршруте предусматривают дополнительные операции, связанные с особенностями термической обработки (например, операция меднения или операция снятия дополнительного припуска для удаления цементированного слоя на поверхностях, не подлежащих закалке).
Необходимость выявления брака на первых операциях в не-
которых случаях заставляет изменять маршрут обработки заготовки.
При назначении технологических баз технолог руководствуется принципом совмещения и постоянства баз, то есть технолог стремится выбрать в качестве технологических баз поверхности или сочетание поверхностей, которые одновременно являются конструкторскими и измерительными базами, и старается не менять технологические базы в процессе обработки.
При вынужденной смене технологических баз и нарушении принципа их совмещения необходимо произвести перерасчет допусков и технологических размеров заготовки.
Во всех возможных случаях в качестве черновых баз принимаются поверхности, удобные для установки и в дальнейшем не обрабатываемые. Черновые базы связываются размерами или условиями (параллельность, перпендикулярность) с обрабатываемой при первой операции поверхностью или совокупностью поверхностей, которые в дальнейшем используются в качестве технологических баз для последующих операций обработки заготовки.
В целях уменьшения пространственных отклонений в расположении технологических баз, используемых при последующих операциях механической обработки, желательно в процессе первой операции, выполняемой от черновых баз, произвести обработку всех указанных баз при одном установе заготовки.
Выбор типа станка определяется его способностью обеспечить выполнение технических требований, предъявляемых к детали в отношении точности ее размеров, формы и шероховатости поверхности. Если по характеру обработки эти требования можно выполнить на различных станках, выбирают тот или иной станок для выполнения данной операции, руководствуясь следующими соображениями:
26
•соответствие основных размеров станка габаритным размерам обрабатываемой заготовки;
•соответствие производительности станка количеству заготовок, подлежащих обработке в течение года;
•наиболее полное использование станка по мощности и по времени;
•наименьшие затраты времени на обработку;
•наименьшая себестоимость обработки;
•наименьшая цена станка;
•реальная возможность приобретения того или другого станка;
•необходимость использования имеющихся на предприятии станков.
При проектировании рабочего технологического процесса
производится конструктивная разработка приспособления с изготовлением рабочих чертежей. Обычно это выполняется
взаводских конструкторских бюро приспособлений.
Вединичном и мелкосерийном производстве применяют универсальные приспособления, которые являются принадлежностями станков (токарные патроны, тиски, делительные универсальные головки, поворотные столы и т.п.).
Вкрупносерийном и массовом производстве применяют, главным образом, специальные приспособления, которые сокращают вспомогательное и основное время обработки.
Одновременно с выбором станка и приспособления для ка-
ждой операции выбирается необходимый режущий инструмент и средства измерения, обеспечивающие достижение высокой производительности, требуемой шероховатости и точности обработки и контроля.
При выборе инструмента в единичном и мелкосерийном производстве предпочтение отдается нормализованным режущим и измерительным инструментам, выполненным по стандарту или в соответствии с техническими условиями. В крупносерийном и массовом производстве предпочтение отдается специальным измерительным инструментам.
Структура операции выбирается технологом, который принимает решение, исходя из условий обеспечения заданных
27
чертежом точности, шероховатости, а также достижения наибольшей производительности и минимальной себестоимости обработки. При этом технолог стремится реализовать принцип многоместной параллельной или многоместной параллельнопоследовательной обработки.
2. ТЕХНОЛОГИЧЕСКИЕ МАРШРУТЫ ОБРАБОТКИ ТИПОВЫХ ДЕТАЛЕЙ МАШИН
Ввиду большого разнообразия форм и размеров деталей машин, наличия на заводах различного оборудования и разной степени подготовки персонала разработка технологических маршрутов для типовых деталей машин, пригодных для любого машиностроительного завода, даже в пределах одного типа деталей, является неосуществимой задачей.
Однако существует ряд общих условий, о которых говорилось выше и которые предопределяют маршрут обработки деталей всех типов.
Это – особенности конструкции деталей, требования к точности обработки, применение технологических средств повышения износоустойчивости и надежности деталей машин, соблюдение принципа единства базы, необходимость обработки с одной установки возможно большего количества поверхностей заготовки и выявления брака при выполнении первых операций.
2.1. Технологические маршруты обработки станин станков
Станина металлорежущего станка является базовой деталью станка, которая соединяет все узлы и детали станка воедино. Именно относительно станины ориентируются и перемещаются подвижные узлы станка. Для большинства станин характерным является наличие двух и более прямолинейных поверхностей. Наличие точно обработанных отверстий не является типичным для станин. Станины относятся к деталям с большими габаритными размерами, с точными направляющими поверхностями, деформирующимися при обработке и эксплуатации.
По служебному назначению станины подразделяют на шесть групп:
28
•с горизонтальными направляющими и несколькими тумбами (станины токарных, револьверных и других подобных станков);
•с горизонтальными направляющими и несколькими тумбами, с отлитыми как одно целое со станиной корпусом передней бабки;
•с горизонтальными направляющими, устанавливаемыми непосредственно своим основанием на пол или фундамент без тумб (станины продольно-строгальных, продольно-фрезерных
ит.п. станков);
• с вертикальными направляющими и перпендикулярно к ним расположенными отверстиями под опоры шпинделя (станины долбежных станков);
•с вертикальными направляющими, но без шпиндельных отверстий (станины вертикально-сверлильных станков);
•станины в виде цилиндрической вертикальной колонны
сплоским основанием, расположенным перпендикулярно к оси цилиндра (станины радиально-сверлильных станков).
Точность работы станка в значительной степени определяется точностью направляющих станины и ее износоустойчивостью. Отклонение от прямолинейности и параллельности направляющих станин станков нормальной точности допускается
впределах 0,01–0,05 мм на длине 1 м, для прецизионных станков – меньше в 5–10 раз.
Шероховатость поверхности направляющих станин станков
нормальной точности допускается в пределах Ra = 0,3–1,25 мкм, а для прецизионных станков Ra = 0,08–0,2 мкм.
Заготовками для станин служат отливки из серого чугуна СЧ 20, СЧ 25 и СЧ 30. Реже станины делают сварными.
Технологический маршрут обработки станин (технологи-
ческая последовательность механической обработки) для всех
видов производства принципиально одинаков и заключается
вследующем:
•черновая обработка плоскостей основания и направляющих;
•чистовая обработка тех же плоскостей;
•обработка крепежных и других отверстий;
•отделочная обработка плоскостей направляющих.
29
Заготовки литых станин поступают на механическую обработку с припусками, подлежащими обработке на всех поверхностях направляющих. Чтобы обеспечить точность станка на длительный период, в машиностроении проводят технологические мероприятия, устраняющие внутренние остаточные напряжения в обрабатываемых заготовках станин, а именно: производят естественное или искусственное старение. Естественное старение производится обычно после обдирки (черновой обработки плоскостей основания и направляющих): станина вылеживается в цехе или, еще лучше, на открытом воздухе вне цеха от 10 дней до 6–8 месяцев. Искусственное старение обычно производится путем нагрева заготовки в печи до 500–550 °С в течение 12–15 часов, с выдержкой при этой температуре в течение 4–6 часов и охлаждением в печи до 200 °С в течение 8–10 часов. Для прецизионных станков это время увеличивается в 2–3 раза с повышением температуры нагрева до 600–650 °С. Значительно реже снятие остаточных напряжений осуществляют «обстукиванием» подвешенной отливки пневматическим молотком в течение 1–2 часов или многократным встряхиванием.
Припуски на обработку станин больших станков в индивидуальном и мелкосерийном производстве составляют 12–25 мм на сторону, а станин средних станков в серийном и крупносерийном производстве – 6–8 мм.
Конструктивные особенности, вес (масса), габаритные размеры, параметры точности, а также годовой выпуск определяют технологический маршрут обработки станины и выполнение отдельных операций.
Станины тяжелых и уникальных станков начинают обрабатывать с направляющих, что позволяет своевременно выявить литейный брак. Обработку станин станков средних размеров начинают с основания. На первой операции станины устанавливают по черным поверхностям направляющих, которые являются установочными технологическими базами. Это позволяет на следующей операции снимать с направляющих слой металла меньшей толщины, обеспечивая сохранение наиболее плотного, однородного и износоустойчивого слоя металла на направляющих станины.
30