
Теоретические основы переработки полимеров (механика процессов)
..pdf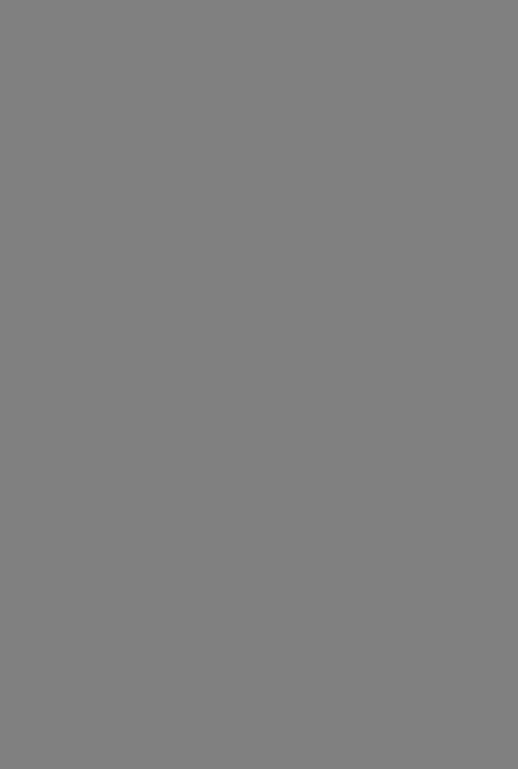
качественного чугуна кокильной отливкой. Поверхностный отбе ленный слой имеет твердость 45—50 HRC. Качество поверхности каландруемого материала в значительной мере определяется каче ством поверхности валков; поэтому рабочая поверхность валка тщательно шлифуется и полируется до зеркального блеска.
Для термостатирования в валках имеется внутренняя полость, в которую при работе подается пар или пароводяная смесь. В но вейших моделях каландров применяют валки, в которых теп лоноситель циркулирует по просверленным непосредственно у поверхности валка периферийным каналам диаметром 38—50 мм.
Центральная |
полость служит в таких валках |
только для подвода |
и отвода теплоносителя [3; 4, с. 72]. |
в диапазоне 15— |
|
Окружные |
скорости валков изменятся |
400 м/мин. Максимальное давление в зазоре в зависимости от рео логических свойств материала и толщины каландруемого изделия
может составлять 7,0 |
70,0 МПа. С увеличением диаметра вал |
|||||
ков распорные |
усилия |
возрастают. |
Так, при |
формовании пленки |
||
толщиной 0,1 |
мм |
из |
пластифицированного |
поливинилхлорида |
||
(32% ДОР) при 443 К |
(скорость |
каландрования 0,6 м/с): для ка |
||||
ландра с диаметром |
валков 915 |
мм |
(длина |
2340 мм) распорное |
усилие равно 93-104 Н, для каландра с диаметром валков 610 мм (длина 1670 мм)— 44• 104 Н.
Валки каландров обычно устанавливают на подшипниках сколь жения. Однако на некоторых современных каландрах для этой цели применяют сферические роликовые подшипники. Величина за зора в подшипниках должна быть минимальна, поскольку смеще ние шеек приводит к изменению зазора и появлению поперечной разнотолщинности каландруемого изделия. В каландрах с рас положением валков в линию для уменьшения влияния «игры» подшипников на точность поперечного размера пленки применяют предварительную нагрузку валков при помощи специальных гид роцилиндров.
Регулирование зазора между валками осуществляется за счет перемещения подшипников внешних валков; для этого на каландре имеется специальный механизм <9, обеспечивающий синхронное сме щение обоих подшипников валка. Валки каландров современной конструкции приводятся от индивидуальных электродвигателей постоянного тока 5, которые устанавливаются на общем блок-ре дукторе 6. Понижающий редуктор привода каждого валка распо лагается в отдельном корпусе. Каждый валок соединяется с вы ходным валом редуктора при помощи своего карданного вала 7. При таком приводе возможные пределы изменения фрикции огра ничиваются только регулированными характеристиками двигателей и обычно позволяет менять окружную скорость валков в диапа зоне 1 10, обеспечивая постоянство заданной скорости с точно стью ±0,2% [3].
Измерение толщины каландруемого листа может осуществ ляться контактным и бесконтактным методами. При контактном
Рис. X. 4. Схемы расположения валка при листовании резиновых смесей:
а —трехвалковый каландр; б —четырехвалковый |
каландр; в —четырехвалковый Г-образный |
каландр с нижним питанием; г — четырехвалковый |
Г-образный каландр с верхним питанием; |
д—Z-образный каландр. |
|
методе лента каландруемого материала проходит между опорными роликами механического или электрического толщиномера. При менение индуктивного датчика позволяет выносить вторичный при бор на щит управления, а также производить непрерывную регист рацию толщины каландруемого материала. Точность измерения контактных толщиномеров составляет ±(10-т-25) мкм.
Бесконтактные толщиномеры подразделяются на пневматиче ские, емкостные и радиоизотопные.
В пневматических толщиномерах, принцип действия которых основан на изменении сопротивления потоку воздуха, вытекающе му из тарированного сопла, в зависимости от расстояния от сопла
до поверхности ленты, |
измеряется не абсолютная толщина листа, |
||||||||||
а лишь |
ее отклонение |
от |
некоторого |
номинального |
значения |
||||||
[6, с. 211; |
7]. |
|
|
|
|
|
|
|
|
|
|
Работа толщиномеров емкостного типа основана на том, что |
|||||||||||
лента каландруемого материала, |
пропускаемая между двумя |
изо |
|||||||||
|
|
|
лированными |
электродами, |
образует |
конденса |
|||||
|
|
|
тор, емкость которого изменяется в зависимости |
||||||||
|
|
|
от толщины слоя диэлектрика. Эти изменения |
||||||||
|
|
|
емкости |
определяются |
компенсационным |
мето |
|||||
|
|
|
дом и позволяют судить о толщине каландруе |
||||||||
|
|
|
мого |
материала с точностью до ± (10 -^20)Х |
|||||||
|
|
|
X Ю~6 мкм. |
|
|
толщиномерах |
обычно |
||||
|
|
|
В |
радиоизотопных |
|||||||
|
|
|
применяют источник p-излучения. О колебаниях |
||||||||
|
|
|
толщины листа судят по изменению интенсивно |
||||||||
Рис. X. 5. Дублирова |
сти потока |
излучения |
[8—10]. |
|
|
||||||
ние с гуммированным |
В резиновой промышленности каландрование |
||||||||||
Дублирующим роли |
|||||||||||
ком: |
|
|
применяют для следующих технологических про |
||||||||
I—смесь; 2—дубли- |
цессов: листование резиновых смесей, при кото |
||||||||||
рующнй ролик; 5—бо |
|||||||||||
бина с |
листованной |
ром |
получают |
бесконечные |
листы толщиной от |
||||||
смесью; 4—ролик для |
0,2 до 1,5 мм. Листование |
обычно производят |
|||||||||
приема |
прокладоч |
||||||||||
ного холста; |
5— сдуб |
на каландрах с тремя,четырьмя и пятью валка- |
|||||||||
лированный лист. |
|
|
|
|
|
|
|
|
|
ми (рис. Х.4), причем валки формующего зазора вращаются с одинаковой скоростью.
Изготовление профилированных заготовок, иногда имеющих односторонний рельеф, производят на профильных каландрах.
Дублирование (сдавливание) листов применяют для получе ния листов толщиной свыше 1,5 мм, поскольку при каландровании через зазор, превышающий 1,5 мм, в массиве листа образуются воздушные пузыри. Различают несколько способов дублирования: а) дублирование с помощью гуммированного дублирующего ва лика, который установлен на станинах каландра (рис. Х.5). Предварительно листованная резиновая смесь подается с раскаточного устройства (или другого каландра) в зазор между дублировочным валком и нижним валком каландра, где она прижи мается давлением грузов (или пружин) и прикатывается к по верхности выходящей из последнего зазора листовальной смеси. Дублированная полоса резиновой смеси охлаждается и заматы вается в прокладочный холст; б) дублирование с применением дублировочного барабана, который устанавливают непосредствен но возле каландра. Барабан диаметром около 1 м нагревают па ром до 313—333 К и прикатывают к его поверхности слой за слоем поступающий с каландра лист. По достижении заданной толщины прикатка прекращается. Лист разрезают по образующей и снимают с барабана. Этим способом получают листы толщиной до 40 мм.
Для получения недублированных листов большей толщины при меняют каландры с клиновым рассекателем, установленным на входе в формующий зазор (рис. X. 6). Установка клина позволяет существенно повысить удельные давления, улучшить условия де газации и, благодаря этому, увеличить толщину листовых загото вок до 5—7 мм [11].
Дублирование прорезиненных тканей осуществляют на двух валковых каландрах, через которые одновременно пропускают до
пяти слоев ткани. |
|
при |
котором резиновая смесь, |
||||||
Прорезинивание ткани — процесс, |
|||||||||
|
проходя через зазор вместе с |
||||||||
|
тканью, вдавливается в меж- |
||||||||
|
нитевое |
пространство. |
Обычно |
||||||
|
прорезинивание |
производят |
на |
||||||
|
трехвалковых |
промазочных |
ка |
||||||
|
ландрах |
(рис. X. 7). Средний |
ва |
||||||
|
лок, |
подающий |
смесь, |
вращается |
|||||
|
быстрее, |
чем внешний |
(фрикция |
||||||
|
/ = |
1 |
1,5). Ткань |
с |
раскаточно- |
||||
|
го устройства затягивается в за |
||||||||
|
зор между средним и нижним |
||||||||
|
валками каландра, где сна про- |
||||||||
Рис. X. 6. Схема установки клина у калиб- |
МаЗЫВаеТСЯ реЗИНОВОИ |
СМССЬЮ, 3 |
|||||||
рующегося зазора каландра. |
затем |
поступает |
на |
закаточное |
устройство. Скорость вращения закаточного валика всегда несколько превышает скорость вращения валков каландра. Этим создается необходимое продольное натяжение ткани. Поскольку диаметр приемного барабана, на который наматывается ткань, в процессе за катки увеличивается, скорость вращения ба рабана по мере его заполнения понижается.
Если ткань обкладывается с двух сторон или имеет очень редкую текстуру, при закатке для предотвращения слипания применяют прокладочную ткань. Толстые ткани перед промазкой подсушивают на барабанных су шилках или на сушильных каландрах так, чтобы их остаточная влажность не превыша ла 2-2,5% .
Температура валков каландра при перера ботке резиновых смесей сильно зависит от со держания наполнителя. Обычно, при увеличе
нии степени наполнения температура валков понижается. Для большинства резиновых смесей температура верхнего и среднего валков поддерживается в диапазоне 368—333 К, нижнего 288 К.
В промышленности переработки пластмасс каландрование ши роко применяется для формования тонких листов и пленок из жесткого и пластифицированного поливинилхлорида, ацетата цел люлозы, АВС. Большое распространение получил каландровый способ изготовления линолеума и других покрытий для полов из сильно наполненных композиций ПВХ.
Каландрованием из пластифицированного ПВХ изготавливают пленки толщиной 0,2—0,5 мм. Обычно для этой цели применяют L и Z-образные четырех- и пятивалковые каландры. Температура поверхности валков при каландровании ПВХ поддерживается на значительно более высоком уровне, чем при каландровании рези новых смесей [3, 5].
X. 2. НЕКОТОРЫЕ АСПЕКТЫ ГИДРОДИНАМИЧЕСКОЙ ТЕОРИИ КАЛАНДРОВАНИИ В ИЗОТЕРМИЧЕСКОМ ПРИБЛИЖЕНИИ
Математическое описание процесса каландрования полностью по добно описанию процесса вальцевания, изложенному в гл. IX. Следовало бы отметить, что основные теоретические результаты были получены именно при анализе процесса каландрования [12 —15; 16, с. 227]. Поэтому для описания кинематики потока, возникающих в зазоре напряжений сдвига, распорных усилий и мощности, необходимой для привода валика можно пользоваться зависимостями, выведенными в гл. IX. При этом следует иметь


|
теории |
вальцевания. |
Присутствие |
||||
|
обкладываемой |
ткани толщиной б |
|||||
|
приводит, как |
это видно |
из |
схемы, |
|||
|
к уменьшению |
величины |
фактиче |
||||
|
ского зазора. Увеличение |
диаметра |
|||||
|
нижнего валка |
настолько |
незначи |
||||
|
тельно |
(б//? ^ |
|
10_3),что в дальней |
|||
|
шем им пренебрегаем. |
|
|
||||
|
Для |
определения |
глубины зате |
||||
|
кания |
воспользуемся |
уравнениями |
||||
|
течения |
псевдопластичной |
жидко |
||||
|
сти по трубам с прямоугольным |
||||||
|
профилем поперечного сечения [17, |
||||||
Рис. X. 10. Изменение глубины затека |
с. 287]. Пренебрегая |
инерционными |
|||||
ния по зазору. |
эффектами и |
считая |
течение уста |
||||
|
новившимся, |
можно выразить сред |
нюю скорость v движения материала в пространстве между во локнами ткани:
я+1
г
(Х.1)
(п + 3) п
где — текущая глубина затекания (рис. X. 10); гг - ■гидравлический радиус межволокопного пространства.
Средняя скорость затекания определяется также соотношением:
V = |
dh6 |
(Х.2) |
|
dt |
|
Подставив выражение (X. 1) в уравнение (Х.2), получим диф
ференциальное уравнение: |
|
|
|
||||
dh. |
|
rn+l |
|
|
|
(Х.З) |
|
dt |
h i |
2" (п + |
3) яц£ |
|
|
||
|
|
|
|||||
Разделяя переменные и переходя от интегрирования по времени |
|||||||
к интегрированию по безразмерной координате |
получим: |
||||||
|
|
/„ |
]) г п + > |
|
|
|
|
Л"+' |
= _____ ■ ■ ■ ! ■ ! :----------гг- \ Рп (1) й\ |
|
( X |
||||
6 |
(п + 3) лц[{2пи (2 R h 0) /} J |
|
|
|
|||
Подстановка в уравнение (Х.4) приближенного выражения для |
|||||||
Давления |
из уравнения (IX.28) |
позволяет определить глубину за |
|||||
текания: |
|
|
|
|
|
|
|
|
( |
R \ h |
( |
(» +1)3"" г [g(i2.i) + 5 g r ^ |
^ +' .2 |
7n(п+1) |
|
м ы |
= ( л 7) Гг! |
«(« + зГ \ |
1+ I 2 |
Г |
(Х.5) |
||
|
|||||||
|
|
Из выражения (Х.5) следует, что глубина затекания при промазке очень сильно зависит от радиуса валков каландра,
увеличиваясь пропорционально радиусу в степени V2l а также от
толщины накладываемого слоя, уменьшаясь пропорционально fto/2’ Очевидным следствием полученного результата является вывод о том, что для надежного сцепления между полимером и тканью при наложении сравнительно толстых слоев на ткань с плотной текстурой необходимо увеличивать диаметр валков. Именно этим, а отнюдь не стремлением увеличить жесткость валков, объясняется современная тенденция к увеличению диаметра валков промазочных каландров, достигающего у некоторых машин 1050 мм [3, 14, 18].
Несколько неожиданным оказывается независимость глубины затекания от скоростного и температурного режимов. Этог факт объясняется тем, что увеличение скорости, которое приводит к уменьшению времени затекания, одновременно вызывает и умень шение эффективной вязкости, приводящее к увеличению скорости затекания. Изменение температуры, проявляющееся в основном в изменении параметра ц, приводит к таким изменениям эффек тивной вязкости и давления, при которых скорость затекания остается постоянной.
Для определения глубины затекания необходимо вычислить входящий в уравнение (X. 5) определенный интеграл. Хотя анали тически это сделать не удается, в каждом конкретном случае этот интеграл может быть вычислен графо-аналитическим или непо средственно численным методом. Если же реологические свойства каландруемого полимера близки к свойствам ньютоновской жидко сти (п = 1), то входящий в уравнение (X. 5) интеграл легко вы числяется. В этом случае глубина затекания определяется выра жением:
Лб (Ы = 0,06/> (Л/Ло)1'1 Ur, (h)]'1 |
(X. 6) |
Здесь функция £2(Ы определяется выражением |
(IX. 31)— см. |
номограмму на рис. IX. 9. |
вязкости, оно |
Хотя уравнение (X. 6) не учитывает аномалии |
вполне пригодно для прикидочных оценок толщины слоя обкладки, который может быть наложен на каландре с известным диаметром валков на ткань с заданной густотой переплетения волокон.
Поскольку одновременно с пластической деформацией при про хождении ткани через зазор в контактирующем с поверхностью ткани полимере развивается и высокоэластическая деформация, промазку и обкладку выгоднее вести на повышенных скоростях, при которых доля обратимой деформации будет минимальна.
Каландровый эффект. Специфической особенностью, при сущ ей всем каландрованным изделиям, является существование явно вы раженной продольной анизотропии механических свойств, извест ной под названием каландрового эффекта. Эта анизотропия возни кает как следствие .«замороженной» продольной ориентации, кото рой полимер подвергается при прохождении через зазор каландра. Скорость каландрованного листа обычно либо равна окружной скорости валков, либо несколько превышает ее. Поэтому возникаю