
Процессы обработки заготовок. Часть 1. Методы механической обработки п
.pdf
На рис. 6.7 показано обтачивание сферической головки клапана путем шарнирного соединения суппорта с неподвижной осью 1 и осью 3 при помощи штанги 2, длина которой соответствует радиусу сферы головки клапана. Поперечная подача суппорта производится вручную, причем суппорт одновременно перемещается вдоль станины станка и таким образом резец описывает окружность требуемого радиуса.
Рис. 6.7. Обтачивание сферической головки клапана
Фасонные поверхности можно обрабатывать на токарноревольверных станках, гидрокопировальных станках и на станках с ЧПУ.
Применение станков с ЧПУ позволяет обтачивать фасонные поверхности любой сложности (по конфигурации) с высокой точностью и малой шероховатостью поверхности.
При этом чем сложнее профиль фасонной поверхности, тем эффективнее применение станков с ЧПУ.
6.3. ОБРАБОТКА ВНУТРЕННИХ ФАСОННЫХ ПОВЕРХНОСТЕЙ
РАСТАЧИВАНИЕМ И СВЕРЛЕНИЕМ
Фасонные поверхности на токарных станках обрабатывают фасонными зенкерами и развертками, установленными в задней бабке станка.
111

Кроме того, при растачивании могут быть использованы фасонные резцы, либо растачивание может производиться нормальными расточными резцами на станках с ЧПУ.
Сверление и растачивание на сверлильных и координатнорасточных станках фасонных поверхностей в большинстве случаев осуществляется специальным фасонным инструментом (рис. 6.8).
Фасонное отверстие предварительно сверлят спиральным сверлом, причем, если диаметр отверстия превышает 15 мм, его сначала сверлят сверлом диаметром 10–12 мм, а затем последовательно рассверливают до требуемого диаметра набором сверл
(рис. 6.8, а).
Окончательно фасонную поверхность отверстия формируют путем сверления фасонным перовым сверлом (рис. 6.8, б).
Рис. 6.8. Обработка внутренних фасонных поверхностей:
аи б – сверление фасонного отверстия в два перехода;
ви г – растачивание специальными фасонными резцами
Растачивание фасонных поверхностей отверстий (рис. 6.8, ви г) осуществляется специальными фасонными расточными резцами.
112
6.4. ОБРАБОТКА ФАСОННЫХ ПОВЕРХНОСТЕЙ
ФРЕЗЕРОВАНИЕМ
Замкнутые фасонные поверхности деталей типа дисков
инезамкнутые прямолинейно-фасонные поверхности чаще всего обрабатывают фрезерованием по разметке или при помощи копировальных устройств. Обработка производится обычно при двух движениях, одно из которых получается от соответствующей механической подачи станка, а второе – от копира; к последнему все время прижимается ролик, жестко связанный с частью станка, которой сообщается подача; можно работать
ис ручной подачей.
Основным движением является продольная подача прямоугольного стола или вращение круглого стола.
Копиры представляют собой ведущую деталь копировального устройства, очертания которой определяют траекторию движения режущего инструмента, соответствующую профилю обрабатываемой поверхности.
Системы управления процессом копирования подразделяют на системы прямого и непрямого действия.
При прямом действии контакт копировального ролика (пальца) и копира обеспечивается весом груза, силой гидравлического давления или силой сжатия пружины.
При системе непрямого действия копировальный ролик находится в соприкосновении с копиром под действием незначительной силы, измеряемой десятками граммов. В этой системе копировальный ролик является промежуточным подвижным элементом, незначительные перемещения которого, измеряемые в сотых долях миллиметра, в виде команд передаются в специальные усилительные устройства, которые воздействуют на исполнительные механизмы и перемещают режущий инструмент и обрабатываемую заготовку.
Принципиальные схемы копировальной обработки по системе прямого инепрямого действия приведены нарис. 6.9.
113
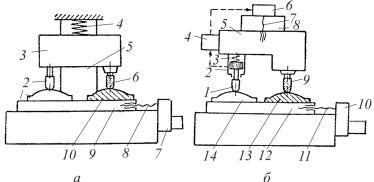
Рис. 6.9. Принципиальные схемы копирования
При копировальной обработке по системе прямого действия
смеханическим управлением (рис. 6.9, а) стол 9 перемещается ходовым винтом 8 от редуктора 7. На столе 9 установлен копир 1 и заготовка 10. При движении палец 2 совместно с бабкой 3 под действием копира 1 сжимает пружину 4 и перемещается в вертикальном направлении по стойке 5. Фреза 6, имеющая форму и размеры пальца 2, при перемещении совместно с бабкой обрабатывает заготовку, придавая ей форму копира. Работа пружины 4, сила которой больше, чем вертикальная слагающая от силы резания на фрезе, обеспечивает постоянный контакт между пальцем и копиром.
При копировальной обработке непрямого действия с гидравлическим, пневматическим или электронным управлением (рис. 6.9, б) стол 12 с копиром 14 и заготовкой 13 перемещается от редуктора 10 через ходовой винт 11. При этом палец 1 под действием копира 14 перемещается в корпусе 2, соединенном
сбабкой 5. Пружина 3 обеспечивает постоянный контакт между пальцем и копиром. Незначительное перемещение пальца, как электронную команду управления, можно увеличить, используя электронные, гидравлические, пневматические или другие устройства. Это усилие происходит в аппарате 4, который затем сообщает команду двигателю 6; последний через редуктор
114
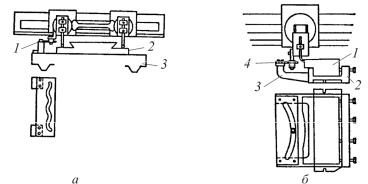
и ходовой винт 7 перемещает по стойке 8 бабку 5. Соответственно фреза 9 обрабатывает заготовку по профилю копира.
Системы прямого действия обычно применяют на копировальных станках с механическим или ручным управлением, а системы непрямого действия – на копировальных станках с электронным, гидравлическим или пневматическим управлением.
Объемное фрезерование по копиру или по специально изготовленной модели производится на специальных копировальнофрезерных станках. Однако наибольший эффект по точности, шероховатости поверхности и экономичности при объемном фрезеровании достигается при работе на станках с ЧПУ.
6.5. ОБРАБОТКА ФАСОННЫХ ПОВЕРХНОСТЕЙ СТРОГАНИЕМ
Строгание фасонных поверхностей обычно производится по копиру (рис. 6.10).
Рис. 6.10. Строгание фасонных поверхностей по копиру
Строгание стружечных канавок (рис. 6.10, а) на направляющих поверхностях детали 2 производится при помощи копира 1, установленного на столе 3 продольно-строгального станка.
Строгание вогнутой поверхности (рис. 6.10, б) на детали 1 осуществляется при помощи копира 4, закрепленного на кронштейне 3 приспособления 2, установленного на столе станка.
115
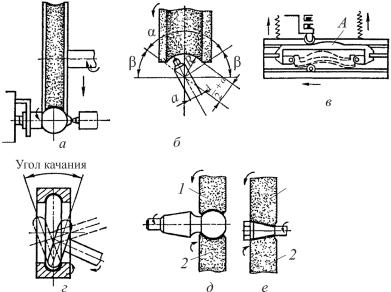
6.6. ОБРАБОТКА ФАСОННЫХ ПОВЕРХНОСТЕЙ
ШЛИФОВАНИЕМ
Шлифование фасонных поверхностей производится фасонными шлифовальными кругами (рис. 6.11, а и б), а также при помощи копиров (рис. 6.11, в и г), по которым перемещаются обрабатываемые заготовки или шлифовальный круг.
Рис. 6.11. Схемы шлифования фасонных поверхностей:
а– фасонным кругом с поперечной подачей;
б– профилирование шлифовального круга по радиусу;
в– вогнутой поверхности по копиру;
г– беговой дорожки шарикоподшипника;
ди е – на бесцентрово-шлифовальных станках
При обработке на бесцентрово-шлифовальных станках (рис. 6.11, д и е) фасонная поверхность обрабатывается между шлифовальным 1 и ведущим 2 кругами.
116
7. МЕТОДЫ ОБРАБОТКИ КРЕПЕЖНЫХ РЕЗЬБ
Резьбовые поверхности по своему назначению подразделяются на крепежные и ходовые. Ходовые резьбы прямоугольного, трапецеидального и полукруглого профиля применяют в ходовых винтах, в станочных, сборочных и контрольно-изме- рительных приспособлениях. Они служат для преобразования вращательного движения в поступательное движение.
Крепежные резьбы служат для соединения и фиксации деталей в разборных соединениях. Крепежные резьбы подразделяются на цилиндрические и конические. К цилиндрическим крепежным резьбам относятся: метрические (нормальные, тугие, плотные), дюймовые, трубные, трапецеидальные, упорные (пилообразные) и специальные резьбы (часовые, круглые, артиллерийские).
Основным видом крепежной цилиндрической резьбы, применяемой в России (ранее в СССР), является метрическая резьба треугольного профиля с углом профиля 60°. Дюймовая резьба треугольного профиля с углом профиля 55° применяется при изготовлении запчастей и ремонта зарубежного оборудования. Применение дюймовых резьб при проектировании нового оборудования ограничено.
Трубная резьба представляет собой измельченную по шагу дюймовую резьбу с закругленными впадинами.
Трапецеидальную резьбу применяют в основном в резьбовых соединениях, передающих движение. В качестве чисто крепежной резьбы резьбу с трапецеидальным и прямоугольным профилем применяют крайне редко, только в исключительных случаях.
Упорную резьбу применяют в резьбовых соединениях, испытывающих большое одностороннее давление (в винтовых прессах, специальных нажимных винтах и т.п.).
Часовую резьбу применяют в точном приборостроении для резьбовых соединений диаметром менее 1 мм.
117
Круглую резьбу используют в резьбовых соединениях с повышенными динамическими нагрузками или в условиях, загрязняющих резьбу.
Артиллерийские резьбы используют для крепления командных деталей (трубы артиллерийского ствола, кубика и т.п.), работающих в условиях периодических нагрузок пикового характера.
Конические резьбы, как правило, применяют в трубных соединениях, если необходимо обеспечить герметичность соединения без специальных уплотняющих материалов (пряжи с суриком, льняных нитей и т.п.). Наиболее распространенным видом является трубная коническая резьба, профиль которой соответствует профилю трубной цилиндрической резьбы.
На машиностроительных заводах в зависимости от размеров и точности среднего диаметра резьбы, а также объема производства изготовление крепежных резьб производят на токарных, токарно-револьверных, сверлильных, резьбофрезерных, резьбошлифовальных и резьбонакатных станках. Наружные резьбы нарезают резьбонарезными резцами, гребенками, плашками, фрезами, резьбовыми головками, профилированными шлифовальными кругами, резьбонакатными роликами и плашками. Внутренние резьбы нарезают метчиками, резцами, фрезами.
7.1. НАРЕЗАНИЕ РЕЗЬБЫ РЕЗЦАМИ И ГРЕБЕНКАМИ
Треугольную резьбу часто нарезают на токарно-винторезном станке или на станке с ЧПУ резьбовыми резцами, то есть резцами, заточенными под углом в плане 60° для метрической резьбы и 55° для дюймовой резьбы. Получение профиля резьбы обеспечивается соответствующим профилем резьбового резца, который должен быть заточен достаточно точно, и правильной установки резца относительно заготовки: резец должен быть расположен строго перпендикулярно оси шпинделя станка, так как в противном случае резьба получится косой; кроме того, передняя часть резца должна быть расположена на высоте центров станка.
118
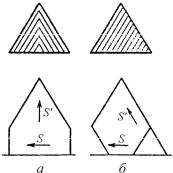
При другом расположении резьба будет нарезана с неправильным углом.
Нарезание резьбы резцами является малопроизводительным методом обработки, так как формирование полного профиля производится за несколько проходов. При нарезании резьб с крупным шагом применяют две схемы резания: генераторную и профильную (рис. 7.1).
Генераторную схему реза- |
|
|
ния применяют при предвари- |
|
|
тельном нарезании резьб скруп- |
|
|
нымшагом (более 3 мм). |
|
|
Профильную схему при- |
|
|
меняют для чистового нареза- |
|
|
ния резьбы. |
|
|
Высокие требования, пре- |
Рис. 7.1. Схема нарезания |
|
дъявляемые к заточке резцов и |
||
резьбы: а – профильная; |
||
сохранению правильного про- |
||
б – генераторная |
||
филя, привели к использованию |
|
в производстве не только нормальных резьбовых резцов, но и к использованию фасонных резьбовых резцов (рис. 7.2).
У призматических (рис. 7.2, а) и круглых (рис. 7.2, б) резцов размеры элементов профиля резьбы выдерживаются более точно, чем у обычных резцов, так как такие резьбовые резцы затачиваются по передней поверхности, а у шлифованных при изготовлении задние (боковые) поверхности сохраняют профиль при переточках неизменным.
Для улучшения качества поверхности резьбы относительно часто применяют пружинные державки (рис. 7.2, в). Некоторые предприятия применяют многорезцовые (чаще всего трехрезцовые) резьбовые головки. Трехрезцовая головка (рис. 7.2, г) состоит из корпуса 3, к которому болтом 4 прикрепляется трехрезцовая пластина 1 (рис. 7.2, д). По мере затупления одного из резцов пластина перезакрепляется в корпусе так, чтобы в работе
119

был новый острый резец. Для этой цели в корпусе имеется штифт 2 (рис. 7.2, г), по которому пластина фиксируется своими тремя точно расположенными цилиндрическими отверстиями. Применение многорезцовых головок наиболее целесообразно в условиях серийного производства.
Рис. 7.2. Резцы для нарезания резьбы:
а– призматический; б – круглый;
в– пружинная державка; г – трехрезцовая головка;
д– трехрезцовая пластина
При нарезании одним резцом его режущая кромка вследствие быстрого притупления теряет форму, поэтому рекомендуется черновые проходы производить одним резцом с менее точным профилем, а чистовые проходы осуществлять чистовым резцом с более точным профилем.
120