
Процессы обработки заготовок. Часть 1. Методы механической обработки п
.pdf
201
Скорость рабочего хода 22 м/мин, обратного 28 м/мин, диапазон подач бесступенчатый от 0,03 до 0,15 мм/дв. ход. Номинальная сила тяги 3000 кГс (30 кН).
Весьма производительным методом обработки шлицев вала является одновременное долбление всех впадин шлицев специальной многорезцовой головкой, аналогичной многорезцовой головке для долбления зубчатого колеса.
Обработка шлицевых поверхностей в отверстиях вту-
лок, зубчатых колес и других деталей производится обычно протягиванием.
Сначала отверстие и торец обрабатывают предварительно (сверлением и зенкерованием с подрезкой торца), потом отверстие протягивается круглой протяжкой, а затем шлицевой протяжкой. Шлицевые отверстия до 50 мм обычно протягиваются одной комбинированной протяжкой.
Если деталь с отверстием подвергается термической обработке (например, закалке), то цилиндрическая поверхность отверстия, которая сопрягается с дном впадины шлицев вала, шлифуется на внутришлифовальном станке (при центрировании по внутреннему диаметру шлицев вала).
Протягивание винтовых шлицев отверстий отличается от протягивания обычных отверстий тем, что в процессе работы движение режущих кромок зубьев протяжки должно осуществляться по винтовой линии, что достигается сочетанием поступательного и вращательного движений двумя способами. Первый способ – оба движения сообщаются протяжке при неподвижной детали. Второй способ – поступательное движение сообщают протяжке, а вращательное – детали.
202
10. СПЕЦИАЛЬНЫЕ МЕТОДЫ ОБРАБОТКИ
Наряду с обработкой заготовок резанием, сопровождающимся снятием стружки, применяется ряд специальных методов обработки без снятия стружки. Применение этих методов повышает производительность и точность обработки, а также увеличивает прочностные свойства деталей.
Эти методы можно разделить на методы обработки давлением в холодном состоянии ифизико-механические методы обработки.
10.1. ОБРАБОТКА ДАВЛЕНИЕМ В ХОЛОДНОМ СОСТОЯНИИ
К обработке заготовок давлением в холодном состоянии относятся: калибрование отверстий шариком и оправкой, редуцирование, обработка поверхностей гладкими роликами и алмазным выглаживанием, давильные работы, накатывание рифлений, накатывание зубчатых колес, упрочнение поверхностей шариками, дробеструйная обработка.
Калиброванию подвергают поверхности гладких цилиндрических отверстий, а также отверстия с фасонным поперечным сечением.
Короткие цилиндрические отверстия калибруют на прессах, проталкивая гладкую оправку (рис 10.1, б, в) или шарик (рис. 10.1, а) через обрабатываемое отверстие с натягом (иногда этот процесс называют дорнованием отверстий).
При калибровании возникает пластическая деформация металла, в результате которой незначительно увеличивается диаметр обрабатываемого отверстия, повышается твердость и снижается шероховатость поверхности.
Длинные отверстия калибруют протягиванием калибрующей оправки через обрабатываемое отверстие на протяжном станке (рис. 10.1, г).
203
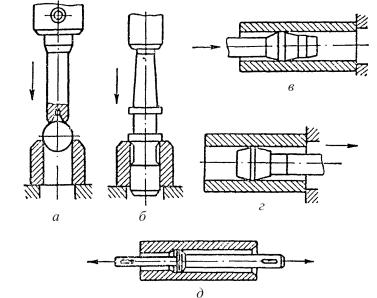
Рис. 10.1. Схемы калибрования отверстий:
а– проталкиванием шарика; б и в – проталкиванием оправки;
г– протягиванием оправки; д – протягиванием оправки
свозвратно-поступательным движением
Если обрабатываемой заготовке или калибрующей оправке придать дополнительное вращение, то можно калибровать участки отверстия, расположенные по винтовой линии.
Несквозные отверстия калибруют оправкой, которая совершает возвратно-поступательные движения (рис. 10.1, д).
Калибрование повышает точность от 25 до 35 %, а также исправляет погрешности формы в поперечном сечении отверстия (погрешности направления оси отверстия калибрование не исправляет). Шероховатость поверхности после калибрования во многом зависит от исходной шероховатости и свойств материала заготовки. Поэтому, чтобы достигнуть хороших результатов, отверстие под калибрование следует растачивать или развертывать, а калибрование производить при обильной подаче
204
сульфофрезола или масла типа И-20А в зону обработки. В этом случае достигается точность 4–5-го квалитета (иногда даже 3-го квалитета), а шероховатость поверхности достигает Ra = = 0,08...0,63 мкм.
Применяемые для калибрования стальные шарики (шарики подшипников) имеют то преимущество, что срок их использования более продолжителен, так как они имеют практически бесконечное количество калибрующих поясков. Кроме того, смещение точки приложения проталкивающей силы не вызывает их перекоса. Однако область применения шариков ограничивается их стандартными размерами.
Калибрующие оправки изготовляются цельными или сборными с поясками любых размеров.
Для повышения износостойкости калибрующий инструмент подвергают хромированию или азотированию, а также применяют наплавку калибрующих поверхностей твердым сплавом.
Редуцирование, или формообразование детали методом обжатия или вытягивания заготовок, является прогрессивным методом, обеспечивающим по сравнению с обработкой точением
ишлифованием увеличение производительности в 5 раз со значительной экономией металла и повышением механических свойств обработанного поверхностного слоя благодаря упрочнению
исозданию напряжений сжатия. Это обеспечивает точность 5–6-го квалитета и шероховатость поверхности Ra = 0,08...0,63 мкм.
Принцип редуцирования наружных поверхностей заключается в последовательном обжатии заготовки (рис. 10.2). Заготовка по мере продвижения вдоль оси деформируется под действием сжимающих сил вращающихся матриц. При этом происходит течение металла заготовки в направлении ее движения до тех пор, пока заготовка не будет обжата до размера, соответствующего наименьшему диаметру желоба матриц. Процесс редуцирования осуществляется следующим образом. Шпиндель 5 редуцирной головки, вращающейся с определенной скоростью, имеет диаметральный паз прямоугольного сечения, по которому к центру и от центра свободно перемещаются бойки с матрицами 3.
205

Последние, соприкасаясь во время работы своими рабочими поверхностями с металлом прутка 2, придают заготовке требуемую форму, обжимая и вытягивая ее. На внешних торцах бойков установлены опорные ролики 1. Шпиндель 5 расположен внутри обоймы 4, в отверстиях которой по окружности свободно установлены ролики 6 таким образом, что их боковые поверхности частично выступают из обоймы.
Рис. 10.2. Схема редуцирования прутка
При взаимодействии шпинделя 5 с бойками и матрицами 3 последние под действием центробежной силы отходят от центра к периферии в тот момент, когда ролики 1 находятся в пространстве между роликами 6 и сходятся к центру, когда ролики 1 наталкиваются на ролики 6. При этом матрицы 3 своими рабочими поверхностями приходят в соприкосновение с металлом заготовки, пластически деформируя его: заготовка обжимается и вытягивается. Станки для редуцирования обеспечивают вращение шпинделя от 150 до 500 об/мин, при этом число обжатий заготовки колеблется от 1000 до 3500 в мин, а сжимающая сила составляет порядка 200 т.
206

Обкатка поверхностей гладкими роликами заключается в том, что свободно вращающиеся ролики, прижимаясь к обрабатываемой поверхности под давлением при обильном охлаждении веретенным маслом, сминают неровности и создают упрочненный слой, повышающий эксплуатационные свойства поверхности детали.
Схемы обработки поверхностей роликами могут быть самыми различными. Выбор той или иной схемы зависит от формы поверхности, жесткости обрабатываемой заготовки и технологического назначения обработки.
При обработке роликами наружных поверхностей диаметр их уменьшается, а при раскатывании отверстий их диаметр увеличивается.
Поверхности жестких деталей обрабатываются односторонними роликовыми оправками (с одним роликом), а менее жесткие – многороликовыми устройствами, которые уравновешивают действующие силы давления.
На рис. 10.3 приведены различные схемы обработки поверхностей гладкими роликами.
Рис. 10.3. Схемы обработки поверхностей гладкими роликами: а и б – многороликовое обкатывание цилиндрических поверхностей; в и г – обкатывание канавки и галтели;
д – обкатывание торцовой поверхности; е и ж – многороликовое раскатывание сферической и конической поверхностей;
з– обкатывание сферической наружной поверхности;
и– раскатывание отверстия; к – обкатывание дна шлицев
207
Как правило, обкатывание и раскатывание гладкими роликами производится после чистового точения или растачивания. Обработка незакаленных поверхностей гладкими роликами заменяет шлифование.
Обработка гладкими роликами обычно выполняется на универсальных станках. Так, например, обкатывание наружных поверхностей осуществляется на токарных, револьверных
икарусельных станках, а раскатывание отверстий, кроме указанных, также на сверлильных и горизонтально-расточных станках. Плоские поверхности обкатывают на поперечно-стро- гальных станках.
Основное требование получения заданной точности и шероховатости поверхности – создание соответствующего давления на ролик из износостойкого материала высокой твердости и применение в качестве СОЖ конопляного масла или масла индустриального И-20А. Так, при ширине рабочей поверхности ролика 3 мм
идиаметра до 100 мм усилие на ролик колеблется в зависимости от обрабатываемого материала от 50 до 200 кГс. Продольная подача выбирается в пределах 0,1–0,2 мм/об. В качестве материала для роликов рекомендуются инструментальные углеродистые
илегированные стали марок ХВГ, 5ХНМ и др., закаленные до твердости HRC 58–64.
При обработке гладкими роликами обеспечивается точность 5–7-гоквалитета, ашероховатостьповерхностиRa = 0,16...1,25 мкм.
Обработка алмазным выглаживанием, в отличие от обра-
ботки роликами, позволяет обрабатывать поверхности закаленных деталей.
Основное требование при алмазном выглаживании – плавность работы, отсутствие пиковых и вибрационных нагрузок.
Для обеспечения этого условия необходимо станочное оборудование высокой жесткости и точности.
Вкачестве инструмента используются технические алмазы.
Оправки для алмазного выглаживания могут быть жесткими и подпружиненными.
208

Использование подпружиненных оправок снижает риск разрушения алмаза из-за возникновения пиковых нагрузок, но не исправляет погрешности формы обработки, предшествующей алмазному выглаживанию. Алмазное выглаживание с применением жестких оправок обеспечивает точность 3–5-го квалитета. Шероховатость поверхности при алмазном выглаживании (при использовании как жестких, так и подпружиненных оправок)
составляет Ra = 0,04...0,63 мкм.
Давильные работы (метод обработки выдавливанием)
применяют при изготовлении из листового металла пустотелых деталей – тел вращения выпукловогнутой конфигурации, узких горловин на цилиндрических заготовках и т.п., для которых экономически нецелесообразно изготовление специальных вытяжных штампов.
Этот метод применяют при вращательном движении заготовки, а в ряде случаев и деформирующего инструмента как на обычных токарных станках, так и на станках, специализированных дляэтого видаобработки.
На рис. 10.4 показана схема выдавливания простым давильником с шаровой головкой.
На рис. 10.5 приведены различные виды давильных работ. При выдавливании на давильных станках металл заготовки утоняется и наклепывается сильнее, чем при вытяжке на прессах, поэтому детали, выдавливаемые за несколько операций, обычно подвергают промежуточному отжигу.
209

Рис. 10.5. Виды давильных работ: а – наружное выдавливание по контуру дисковым роликом;
б – выпуклое выдавливание изнутри роликом 1 по контуру наружного ролика 2; в – вогнутое выдавливание горловины роликом 1 по контуру внутреннего ролика 2
Поверхность выдавленных деталей имеет следы давильника и шероховатость поверхности Ra = 1,25...2,5 мкм. Для уменьшения шероховатости поверхности после окончания выдавливания по обработанной поверхности проходят давильникомшабером, снимающим стружку толщиной 0,05–0,1 мм.
Точность выдавливания деталей обычно находится в пределах 0,001–0,002 их диаметра.
Накатывание рифлений на цилиндрических поверхностях деталей осуществляют плоскими плашками (на резьбонакатных станках) или вращающимися цилиндрическими роликами (на токарных и револьверных станках).
Плоские поверхности накатывают на поперечно-строгаль- ных станках свободно вращающимися роликами с принудительной подачей заготовки.
Накатывание рифлений может быть прямым, угловым и сетчатым. Выбор конструкции накатного инструмента зависит от технологического назначения и заданной формы поверхности.
Прямое и угловое накатывание обычно выполняют одним, а сетчатое – двумя роликами с одновременным встречным накатыванием под углом. В процессе накатывания происходит увеличение диаметра обрабатываемой поверхности.
210