
Процессы обработки заготовок. Часть 1. Методы механической обработки п
.pdf
Стол станка совершает |
|
возвратно-поступательные дви- |
|
жения в продольном направле- |
|
нии (движение подачи) vпрод. |
|
Стальные ленты 2 закреплены |
|
одной стороной на барабане |
|
ролика обката 1, а другой сто- |
|
роной прикреплены к столу |
|
станка 6. Каретка 3, на которой |
|
установлен делительный меха- |
|
низм 4, оправка с зубчатым ко- |
|
лесом и барабан ролика обката |
|
1, совершает быстрые воз- |
|
вратно-поступательные движе- |
|
ния в поперечном направлении. |
|
Ленты 2, закрепленные на бара- |
Рис. 8.24. Схема работы |
бане ролика обката 1, при нали- |
зубошлифовального станка |
чии возвратно-поступательного |
типа МААГ (Швейцария) |
движения каретки воспроизво- |
|
дят обкаточные движения зуб- |
|
чатого колеса по исходной режущей рейке шлифовальных кругов. Установка длины поперечного хода каретки 3 производится за счет регулирования радиуса кривошипа 8. Автоматический поворот зубчатого колеса на один зуб производится после одно-, двукратного прохождения зубчатого колеса под шлифовальными кругами. Припуск на шлифование составляет от 0,1 до 0,2 мм на толщину зуба и снимается за два прохода и более. Тарельчатые шлифовальные круги 7 шлифуют зубья узкой полоской в 2–3 мм, поэтому силы резания и нагрев детали незначительны, что повышает точность шлифования, но снижает производительность. Станки для зубошлифования, работающие методом обкатки двумя тарельчатыми шлифовальными кругами, снабжены устройством, компенсирующим изнашивание шлифовальных кругов в процессе правки их алмазами. Такие устройства обеспечивают постоянство положения рабочей кромки шлифовального
181
круга при его износе. Постоянство положения рабочей кромки шлифовального круга обеспечивается автоматическим перемещением шпинделя вместе с кругом вдоль оси на величину износа от шлифования и правки. Обработка производится при скорости шлифования vкр = 30...32 м/с; числом качаний каретки 40–250 качаний в минуту (в зависимости от типоразмера зубчатого колеса) и продольной подаче 0,5–2,5 мм наодно качание каретки.
На станках типа МААГ (Швейцария) стабильно достигается 4–5-я степень точности зубчатых колес и шероховатость поверхности Ra = 0,1...0,8 мкм. В особых условиях обработки (при температуре воздуха в цехе (20±0,2) °С) на станках типа МААГ может быть достигнута 3-я степень точности. Шлифовальные круги7 на этих станках могут быть установлены с нулевым углом, то есть оси шлифовальных кругов будут располагаться в горизонтальной плоскости, образуя нулевой профиль исходной режущей рейки. При таком расположении шлифовальных кругов (с нулевым профилем исходной режущей рейки) возможно шлифование только зубьев с выкружкой (попытки обработки зубьев без выкружки приводит к поломке шлифовальных кругов).
Шлифование зубьев двумя тарельчатыми шлифовальными кругами без продольной подачи осуществляется на специальных зубошлифовальных станках, на которых установлены тарельчатые шлифовальные круги большого диаметра (700–880 мм), шлифующие зуб по всей длине без возвратно-поступательного движения зубчатого колеса вдоль своей оси. При таком шлифовании основание (дно) впадины зубчатого колеса образуется не по прямой, а по дуге окружности с радиусом, равным радиусу шлифовального круга. На таких станках рекомендуется шлифовать узкие зубчатые колеса, то есть имеющие зубья небольшой длины. Отсутствие продольной подачи, а следовательно, и потери времени на врезание шлифовальных кругов, значительно повышает производительность по сравнению с методом шлифования двумя тарельчатыми шлифовальными кругами с продольной подачей.
182
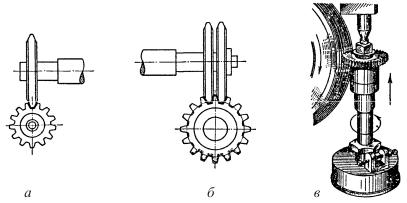
Применяется также шлифование методом обкатки на станках: фирмы НАЙЛЬС (Швейцария) и отечественных станках мод. 5840 и 5841, работающих одним дисковым шлифовальным кругом (рис. 8.25, а), рабочие поверхности которого заправлены алмазами в виде конуса с углом между двумя конусными поверх-
ностями 40° (угол исходной режущей рейки 20°); фирмы ЭРЛИКОН (Швейцария – США) и отечественных
станках мод. 5841, работающих двумя дисковыми шлифовальными кругами (рис. 8.25, б), рабочие поверхности которых заправлены алмазами в виде конуса с углом между двумя конусными поверхностями одного шлифовального круга 40° (угол исходной режущей рейки 20°);
фирм МАТРИКС (Великобритания), РЕЙСХАУЭР (Швейцария) и отечественных станках мод. 5832 и 5833, работающих червячным кругом (рис. 8.25, в), имеющим в осевом сечении прямобочный профиль с углом 40° (угол исходной режущей рейки 20°).
Рис. 8.25. Зубошлифование цилиндрического зубчатого колеса: а – одним шлифовальным кругом;
б– двумя шлифовальными кругами;
в– червячным шлифовальным кругом
183
На станках типа НАЙЛЬС кулисе с установленным на ней конусным шлифовальным кругом, представляющим как бы зуб исходной режущей рейки, сообщается посредством кривошип- но-шатунного механизма быстрое возвратно-поступательное перемещение в горизонтальной, а чаще в вертикальной плоскости. Шлифуемое зубчатое колесо имеет обкаточное движение. При обкатке в одну сторону производится шлифование одной эвольвентной поверхности одного из зубьев, образующих впадину (по эвольвенте обкатка идет от ножки зуба к его головке), а при обкатке в другую сторону производится шлифование эвольвентной поверхности другого зуба этой же впадины. После обработки эвольвентной поверхности зубьев, образующих впадину, зубчатое колесо поворачивают на один зуб и производят обработку зубьев следующей впадины. Шлифование, таким образом, обычно происходит за два оборота зубчатого колеса. Окончательное шлифование осуществляется на более мягких режимах (с меньшей глубиной резания и меньшей скоростью обката). В процессе шлифования шлифовальный круг автоматически правится, и его режущие кромки возвращаются в исходное положение.
Простая форма круга и наличие обкатки позволяют получать 6–7-ю степень точности и шероховатость поверхности
Ra = 0,15...0,63 мкм.
Обработка на станках этого типа производится с применением СОЖ (обычно используют сульфофрезол или масло индустриальное И-20А) при скорости шлифования vкр = 30...32 м/с, числе качаний кулисы 15–250 качаний в минуту (в зависимости от типоразмера зубчатого колеса) и круговой подаче
30–450 мм/мин.
Для увеличения производительности на шпиндель станка 5841 устанавливают два конусных шлифовальных круга
(см. рис. 8.25, б).
При обработке цилиндрических зубчатых колес модулем до 7 мм и диаметром до 700 мм широкое распространение полу-
184

чил метод шлифования червячными шлифовальными кругами (см. рис. 8.25, в) на станках фирм РЕЙСХАУЭР (Швейцария), МАТРИКС (Великобритания) и на отечественных станках мод. 5832, 5833. Правка червячного шлифовального круга с прямолинейным профилем осуществляется многониточными алмазными накатниками (черновым и чистовым). Обработка производится при скорости шлифовального круга 30–32 м/с и соответствующей скорости вращения обрабатываемого зубчатого колеса, с продольной подачей вдоль направляющей зуба от 0,02 до 0,5 мм на оборот обрабатываемого колеса, в качестве СОЖ используется масло индустриальное И-20А.
Станки этой группы обеспечивают 5–6-ю степень точности и шероховатость поверхности Ra = 0,08...0,65 мкм. В особых условиях обработки (при температуре воздуха в цехе (20±0,2) °С) на станках фирмы «РЕЙСХАУЭР» может быть достигнута 4-я, а по некоторым отдельным показателям – 3-я степень точности.
Шлифование прямых зубьев конических зубчатых колес по методу обкатки двумя тарельчатыми кругами производится на станках, сконструированных на базе зубострогальных станков
(рис. 8.26, а).
Рис. 8.26. Зубошлифование конического зубчатого колеса: а – с прямым зубом; б – с криволинейным зубом
185
Криволинейные зубья конических зубчатых колес шлифуются на станках фирмы ГЛИССОН (Швейцария–США) чашечным шлифовальным кругом (рис. 8.26, б).
Сечение боковой стороны шлифовального круга должно иметь профиль зуба исходной режущей рейки. Чашечный шлифовальный круг, вращаясь со скоростью 30–32 м/с, обкатывает рабочую поверхность профиля шлифуемого зуба.
Зубохонингование применяется для окончательной отделки поверхности прямых, косых и криволинейных зубьев цилиндрических зубчатых колес. Инструмент – хон, имеющий вид геликоидального зубчатого колеса наружного или внутреннего зацепления, изготовленного из пластической массы, в составе которой содержится мелкозернистый абразивный или алмазный порошок. Процесс зубохонингования осуществляется на станках внешнего или внутреннего зацепления без жесткой кинематической связи и заключается в совместной обкатке зубчатого колеса
иинструмента. Обкатка сопровождается относительным проскальзыванием при наличии радиального давления. Оси изделия и инструментаустанавливают подуглом скрещивания от15 до 20°.
Обработку производят при постоянном давлении между зубьями обрабатываемого зубчатого колеса и хона или способом беззазорного зацепления зубчатого колеса и хона при неизменном межцентровом расстоянии. Первый способ обеспечивает изготовление зубчатых колес более высокой точности.
Хонингуемое зубчатое колесо, находясь в зацеплении с хоном (без зазора), совершает реверсируемое вращение (попеременно в обе стороны) и возвратно-поступательное движение вдоль своей оси с частотой 17–220 Гц. Зубохонингование производится с окружной скоростью 2–5 м/с при обильном охлажде-
нии керосином.
Величина припуска при зубохонинговании не должна превышать 5 мкм, ибо при увеличении снимаемого припуска возникает искажение профиля эвольвенты: возникает подрез ножки
ифланкирование головки зуба. Искажение эвольвенты при зубо-
186
хонинговании связано с неравномерным проскальзыванием по высоте зуба сопряженных профилей (зубчатого колеса и хона).
После зубохонингования величина шероховатости поверхности по сравнению с исходной уменьшается до 0,02–0,1 мкм и обеспечивается 6–8-я степень точности.
При припуске менее 0,002 мм и высокой точности (3–4-я степень точности) зубчатого колеса до хонингования, после хонингования точность зубчатого колеса может соответствовать 4-й степени точности.
Зубохонингование является высокопроизводительным методом окончательной отделки, например, на обработку зубчатого колеса модулем 2–3 мм и числом зубьев 30–40, производимом при обильном охлаждении керосином за 30–40 с, то есть время хонингования одного зуба составляет от 1 до 1,2 с. Припуск под хонингование составляетна сторону 0,002–0,005 мм.
Станки для хонингования зубчатых колес во многом аналогичны станкам для шевингования.
Притирка (ляппинг-процесс) широко применяется для чистовой, окончательной отделки зубьев закаленных зубчатых колес.
Притирка получила большое распространение в тех отраслях машиностроения, где требуется изготовление зубчатых колес 4–7-й степени точности при шероховатости поверхности
Ra = 0,04...0,63 мкм.
Процесс притирки заключается в том, что обрабатываемое зубчатое колесо вращается в зацеплении с чугунными шестер- нями-притирами и смазываемыми пастой, состоящей из смеси мелкого абразивного порошка с маслом. Помимо этого обрабатываемое зубчатое колесо и притиры имеют в осевом направлении возвратно-поступательное движение относительно друг друга. Осевое движение ускоряет процесс обработки и повышает ее точность. В большинстве случаев движение в осевом направлении придается притираемому зубчатому колесу.
Притирочные станки изготавливаются с параллельными (рис. 8.27, а) иперекрещивающимися (рис. 8.27, б) осямипритиров.
187

Рис. 8.27. Схемы притирки зубьев цилиндрических зубчатых колес: а – с параллельными осями притиров; б – со скрещивающимися осями притиров
Наибольшее распространение получили притирочные станки, работающие со скрещивающимися осями притиров, устанавливаемых под разными углами. Один из трех притиров часто устанавливают параллельно оси обрабатываемого зубчатого колеса. При таком расположении притиров зубчатое колесо работает как в винтовой передаче, и путем дополнительного осевого перемещения притираемого зубчатого колеса притирка происходит равномерно по всей боковой поверхности зуба. Притираемое зубчатое колесо получает вращение попеременно в обе стороны для равномерной притирки обеих сторон зуба, необходимое давление на боковой поверхности зубьев во время притирки создается гидравлическими тормозами, действующими на шпиндели притиров.
Притирка сглаживает неровности и шероховатости поверхности зубьев, придает эвольвентным поверхностям зубьев зеркальный блеск, значительно уменьшает шум и увеличивает плавность работы зубчатых колес. Притиркой можно исправить лишь незначительные погрешности формы. При наличии значи-
188
тельных погрешностей формы зубчатые колеса перед притиркой следует шлифовать, а затем притирать.
Приработка зубьев отличается от притирки тем, что притираются не зубчатое колесо с притиром, а два парных зубчатых колеса, изготовленных для совместной работы в собранной машине.
Приработка производится при помощи абразивного материала, который ускоряет взаимную приработку зубьев зубчатых колес и придает им гладкую поверхность.
189
9.МЕТОДЫ ОБРАБОТКИ ШПОНОЧНЫХ ПАЗОВ
ИШЛИЦЕВЫХ ПОВЕРХНОСТЕЙ
9.1. ОБРАБОТКА ШПОНОЧНЫХ ПАЗОВ
Шпоночные пазы (канавки) на валах изготавливаются для призматических и сегментных шпонок. Шпоночные пазы для призматических шпонок могут быть закрытыми с двух сторон (глухие), закрытыми с одной стороны и сквозными.
Шпоночные пазы изготавливаются различными способами в зависимости от конфигурации паза и вала, применяемого инструмента. Они выполняются на горизонтально-фрезерных или вер- тикально-фрезерных станках общего назначения или на специальных станках.
Сквозные и открытые с одной стороны шпоночные пазы изготавливаются фрезерованием дисковыми фрезами (рис. 9.1, а).
Фрезерование паза производится за один-два прохода. Этот способ наиболее производителен и обеспечивает достаточную точность ширины паза. Применение этого способа ограничивает конфигурация пазов: закрытые пазы с закруглением на концах не могут выполняться этим способом. Такие пазы изготовляются концевыми фрезами с продольной подачей за один или несколько проходов (рис. 9.1, б).
Фрезерование концевой фрезой за один проход производится таким образом, что сначала фреза при вертикальной подаче проходит на полную глубину канавки, потом включается продольная подача, с которой шпоночный паз фрезеруется на полную длину. При этом способе требуется мощный станок, прочное крепление фрезы и обильное охлаждение эмульсией. Вследствие того, что фреза работает в основном периферийной частью, диаметр которой уменьшается от переточки к переточке, по мере увеличения числа переточек точность обработки (по ширине паза) ухудшается.
190