
Процессы обработки заготовок. Часть 1. Методы механической обработки п
.pdf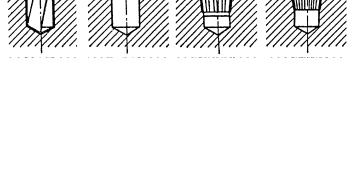
держателем и закрепленной в нем жесткой борштангой с резцом на заданный угол, равный половине угла при вершине обрабатываемого конуса. Продольная подача в направлении, параллельном образующей конуса, обеспечивается перемещением верхних салазок.
Обработка отверстий небольшого диаметра (до 100 мм) с протяженностью до 250 мм достаточно часто производится набором конических зенкеров и разверток, установленных в задней бабке токарного станка или в шпинделе сверлильного или фрезерного станка. На рис. 5.3 показан порядок обработки конусных отверстий.
Рис. 5.3. Схема обработки конического отверстия
При диаметрах отверстия более 25 мм отверстие рекомендуется сверлить последовательно несколькими сверлами различного диаметра для образования ступенчатого отверстия, приближающегося к форме конического зенкера. После сверления 1 поочередно применяются зенкер 2, черновая развертка 3 и чистовая развертка 4.
Обработку конусных поверхностей отверстий, к которым предъявляются повышенные требования по точности и шероховатости поверхности, в том числе закаленных поверхностей, можно производить на внутришлифовальных станках.
Шлифование относительно длинных конусов (протяженность конуса в несколько раз превышает высоту шлифовального
101

круга) производят методом продольной подачи периферией шлифовального круга при повороте шпиндельной бабки станка на заданный угол, равный половине угла при вершине шлифуемого внутреннего конуса.
Обрабатываемая заготовка устанавливается и закрепляется в самоцентрирующемся патроне или в специальном приспособлении с точными шейками. Благодаря такому приспособлению можно устранить влияние биения шпинделя обрабатывающего станка на точность положения вращающейся обрабатываемой заготовки (рис. 5.4).
Рис. 5.4. Приспособление для шлифования внутреннего конуса: 1 – установочное кольцо; 2 – поводковая планшайба
Шлифование коротких внутренних конусов с протяженностью конуса менее высоты шлифовального круга производят при установке и закреплении заготовки в самоцентрирующемся патроне или в специальном приспособлении, приведенном на рис. 5.4 периферией шлифовального круга, методом врезания при повороте шпиндельной бабки (оси шлифовального круга) на угол, равный половине угла при вершине шлифуемого конуса.
В ряде случаев для финишной отделочной обработки внутренних конусов применяют притирку конусными чугунными притирами вручную или на доводочных станках, обеспечивающую получение плотного, или герметичного, разъемного и подвижного соединения.
102
6. МЕТОДЫ ОБРАБОТКИ ФАСОННЫХ ПОВЕРХНОСТЕЙ
6.1.КЛАССИФИКАЦИЯ ФАСОННЫХ ПОВЕРХНОСТЕЙ
Кфасонным поверхностям относятся поверхности, отличающиеся своей формой от плоскости, цилиндра и конуса. В конструкциях турбин, автомобилей, станков, самолетов, ракет, винтовых двигателей турбобуров, бытовой техники применяют детали сложной формы. Использование в деталях фасонных поверхностей обусловлено назначением, требованиями эксплуатации, необходимостью повышения КПД силовых и энергетических установок
иосуществлением заданной траектории движения. На рис. 6.1 приведены характерные виды деталей сфасонными поверхностями.
Наиболее распространенными являются три вида поверхностей:
– поверхности, подчиненные математическому описанию определенной формы и с определенным расположением в пространстве, называются алгебраическими;
– поверхности, форма которых определена отдельными точками, а координаты этих точек заданы в виде числовых отметок и обычно сведены в таблицу, называются поверхностями с числовыми отметками;
– поверхности, форма которых определяется конструктивной необходимостью, называются конструктивными.
Алгебраические поверхности подразделяются на линейчатые, нелинейчатые и винтовые.
Поверхности с образующей в виде прямой линии называются линейчатыми.
В свою очередь линейчатые поверхности подразделяются на два вида: развертываемые и неразвертываемые поверхности.
103

Рис. 6.1. Виды деталей с фасонными поверхностями:
а– гребной винт; б – крыльчатка; в – колесо насоса;
г– винт с переменным шагом; д – колесо водяной турбины; е – дисковый кулачок; ж – цилиндрический кулачок; з – блок из кулачков
Кразвертываемым относятся цилиндрические и конические поверхности. К неразвертываемым поверхностям относятся конусоиды, коноиды и различные гиперболоиды и параболоиды.
Поверхности с образующей в виде кривой линии называются нелинейчатыми. К ним относятся поверхности второго порядка (шаровые, сфероидальные и т.п.).
Поверхности с числовыми отметками применяют при необходимости задать форму поверхности, исходя из физических условий ее работы. К ним относятся профили лопаток паровых, газовых и водяных турбин, гребных винтов и др.
Конструктивные поверхности классифицировать практически невозможно, так как зависят от конструктивной необходимости
104

и фантазии конструктора. Такие формы часто встречаются
всочетании с алгебраическими поверхностями или поверхностями с числовыми отметками.
Различают также переходные поверхности, к которым относятся, например, поверхности перехода от ступицы к лопасти
вгребных винтах, от хвостовой части к рабочей части в лопатке турбины и т.п.
Методы обработки фасонных поверхностей можно разделить на две основные группы:
–обработка фасонным инструментом, имеющим профиль обрабатываемой поверхности;
–обработка нормальным инструментом, которому сообщается криволинейное движение относительно обрабатываемой заготовки вручную, при помощи копировальных устройств или на станках с ЧПУ.
6.2. ОБРАБОТКА НАРУЖНЫХ ФАСОННЫХ
ПОВЕРХНОСТЕЙ ТОЧЕНИЕМ
Фасонные поверхности вращения небольшой длины обтачивают фасонными (призматическими или дисковыми) резцами
(рис. 6.2).
Рис. 6.2. Обтачивание фасонной поверхности: а – призматическим резцом; б – дисковым резцом
105

Фасонный резец снимает широкую стружку, что часто влечет за собой вибрацию обрабатываемой поверхности. Чтобы избежать вибрации или уменьшить ее, применяют малые подачи и низкие скорости резания при обильном охлаждении резца эмульсией или маслом.
Величина подачи в зависимости от диаметра детали (от 10 до 100 мм) и ширины резца (от 8 до 100 мм) принимается равной 0,01–0,08 мм/об. Чем меньше диаметр детали и чем больше ширина резца, тем меньшей должна быть подача. Скорость резания при обтачивании фасонными резцами фасонных поверхностей при указанных подачах меньше, чем при обтачивании цилиндрических поверхностей и составляет от 25 до 40 м/мин.
Когда приходится обрабатывать детали, у которых фасонные поверхности настолько велики, что изготовить для них соответствующий фасонный резец затруднительно или невозможно, обтачивание фасонной поверхности производят нормальными проходными резцами двумя методами.
При небольшом количестве обрабатываемых заготовок обтачивание фасонных поверхностей ведут с ручными (продольной и поперечной) подачами за один или несколько проходов, придавая заготовке форму, соответствующую образцу или шаблону (рис. 6.3).
Рис. 6.3. Обтачивание фасонной поверхности проходными резцами
При больших припусках фасонную поверхность сначала обтачивают черновыми резцами 1 и 2, а потом чистовым резцом 3.
Обточенную фасонную поверхность обычно проверяют специально изготовленным шаблоном. Этот метод можно применять без использования специальных приспособлений, но он малопроизводителен и требует высокой квалификациирабочего.
106

С целью повышения производительности и точности обтачивание фасонных поверхностей производят по копиру (рис. 6.4).
Рис. 6.4. Обтачивание фасонной поверхности по копиру:
а– ролик закреплен в тяге; б – ролик с грузом;
в– ролик с пружиной
На рис. 6.4, а показано обтачивание рукоятки 1 при помощи копира 2. Ролик 3, закрепленный в тяге 4, совершает с суппортом продольное движение. При этом он перемещается в криволинейном пазу, образованном двумя пластинами копира, и перемещает в поперечном направлении салазки суппорта с резцом 5. Резец повторяет движение ролика и воспроизводит на заготовке поверхность, профиль которой соответствует профилю копира. Иногда фасонные поверхности обтачивают при помощи одностороннего копира. В этом случае ролик прижимается к копиру с помощью груза, подвешиваемого на тросе за станиной станка, и перемещается вместе с кареткой (рис. 6.4, б). Копир 1 прикреплен к плите 2. Ролик 4 под действием груза 5 находится в постоянном контакте с копиром 1. Ролик вращается на оси, укрепленной в тяге 3, которая привернута к поперечным салазкам суппорта. Вместо груза 5 можно использовать одну или две
107
пружины, устанавливаемые в поперечных салазках суппорта. Этими пружинами обеспечивается плавное прижимание поперечных салазок, а вместе с ними и ролика 4 к поверхности копи-
ра 1 (рис. 6.4, в).
В современной металлообработке широко применяется гидрокопирование. Для этой цели используют гидрокопировальные станки или универсальные токарные станки, оборудованные специальными гидрокопировальными устройствами (рис. 6.5). Для установки гидрокопировального устройства необходимо снять верхнюю часть суппорта и освободить поперечные салазки каретки суппорта, после чего закрепить устройство на плите 10, установленной на поперечных салазках каретки станка с задней стороны. При необходимости использовать токарный станок как универсальный, нормальный поворотный резцедержатель крепят к плите 11, установленной на салазках в передней части станка. При обработке ступенчатых заготовок гидравлический суппорт 6 должен быть повернут на некоторый угол, чем обеспечивается нормальная работа резца при переходе от одной ступени к другой. Копирный палец 3, перемещаясь по профилю копира 1, находится в контакте со щупом 4 гидравлического механизма 5. Копир, установленный на кронштейне 8, прикреплен неподвижно к станине 7 станка. Иногда вместо копира применяют эталонную деталь, которую устанавливают между центрами бабок приспособления, размещаемого на кронштейне. В резцедержателе 2 устанавливают резец, который обтачивает заготовку 9.
Работа гидравлической схемы основана на изменении давления копирного пальца на щуп, который, являясь плунжером золотника, при перемещении изменяет исходное сечение золотниковой выточки, вследствие чего происходит регулирование движения суппорта.
Это гидравлическое устройство работает по однокоординатной схеме с продольной и поперечной подачами.
108

Рис. 6.5. Гидрокопировальное устройство к токарному станку
109

Если необходим второй проход, то каретку суппорта отводят вручную в исходное положение и после замены копира первого прохода на копир второго прохода повторяют цикл обработки.
С применением лепестковых копиров (рис. 6.6) может быть осуществлена как многопроходная обработка данной заготовки, так и обработка различных по конфигурации заготовок без замены копира, при этом каждой новой форме поверхности будет соответствовать свой шаблон лепесткового копира.
Рис. 6.6. Общий вид лепесткового копира
Лепестковый копир представляет собой набор из плоских шаблонов (1, 2, 3, 4) (в масштабе 1: 1 с контуром обработки), закрепленных на оправке, устанавливаемой в центрах гидравлического суппорта. При применении лепестковых копиров обычный универсальный токарный станок, снабженный гидравлическим копировальным устройством, оснащается механизмом для ускоренного возврата каретки суппорта в исходное положение (обгонной муфтой), механизмами включения и выключения гидравлического суппорта и поворота лепесткового копира. Если необходимо обеспечить передачу движения в масштабе или конструктивной связи между расположенными в разных плоскостях подвижными узлами, применяют сочетание копиров с рычажными механизмами.
Сферические выпуклые и вогнутые поверхности можно обрабатывать также при помощи штанг или пластинок, заменяющих собой копиры.
110