
Оборудование для подготовки материалов
..pdf
Ρ |
≥ |
G sin α |
− G cosα + |
Ρ |
, |
|
|||||
м |
|
f |
ц |
|
|
|
|
|
|
где f — коэффициент трения частицы о поверхность барабана. По полученному значению Pм подбирают конструктивные
параметры магнитной системы сепаратора.
Сила притяжения металлических частиц в большой мере зависит от ряда технологических факторов, таких как температура и химический состав этих частиц. Так, например, присутствие в металлических частицах марганца или никеля изменяет их магнитную проницаемость таким образом, что использование магнитных сепараторов становится невозможным.
Ленточные магнитные сепараторы применяют для извлечения металлических частиц из слоев, близких к поверхности материала, движущегося на ленте транспортера.
Ленточный сепаратор (рис. 1.31) представляет собой короткий ленточный конвейер, который устанавливают на высоте 150– 200 мм над лентой с отработанной смесью в перпендикулярном к ее движению
направлении. Между верхней и нижней ветвями железоотделителя имеется прямоугольная магнитная шайба, которая выбирает из отработанной смеси металлические магнитные частицы, и они выносятся лентой железоотделителя в сторону. Ленту железоотделителя выполняют с поперечными ребрами, из профильной поперечно-ребристой штампованной резины. Подвесные железоотделители могут быть установлены в любом месте над ленточным конвейером отработанной смеси и в дополнение
61
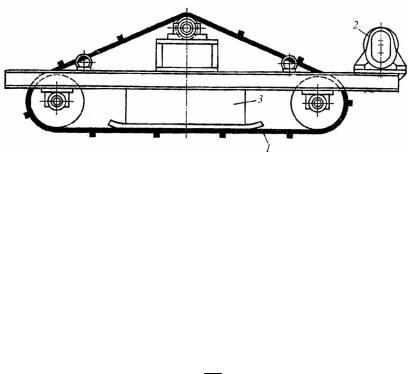
к магнитному шкиву, обычно имеющемуся на приводном конце, дают более эффективное отделение отработанной смеси от магнитных включений, что очень важно в условиях работы современных автоматических литейных линий.
Рис. 1.31. Подвесной магнитный железоотделитель: 1 — лента магнитного железоотделителя; 2 — электродвигатель; 3 — магнитная шайба
Промышленность выпускает подвесные ленточные сепараторы (железоотделители) типа ЭПР-50, ЭПР-65 и ЭПР-120 с шириной лент соответственно 500, 650–800 и 1000–1200 мм.
1.2.2. Сита
При просеивании зернистого материала не все зерна с размерами меньше отверстий сита успевают пройти сквозь отверстия. Эффективность просеивания может быть оценена как:
ε = т ,
т0
где m — масса зерен, прошедших сквозь сито;
m0 — масса зерен, которые по своим размерам могли бы пройти сквозь данное сито.
Величина ε называется коэффициентом полезного действия просеивания и для сит различных видов бывает различной.
Основным фактором, влияющим на КПД просеивания, является направление движения просеиваемого материала относительно полотна сита. Наиболее благоприятным для просеивания
62

будет направление движения материала, перпендикулярное полотну сита. В этом случае зерна имеют наибольшую возможность проникать сквозь отверстия сита. Наихудшим случаем будет движение материала в направлении вдоль полотна сита, в особенности если движение зерен вдоль полотна происходит с большой скоростью. Наиболее неблагоприятные условия будут при этом, если размер зерна приближается к размеру отверстия сита (так называемые трудные, или предельные, зерна). Ввиду этого рационально, в особенности для тонкого просеивания, применять сита с прямоугольными или овальными отверстиями, располагая отверстия большого размера в направлении движения материала по ситу.
В литейных цехах применяются сита плоские и барабанные. Плоские сита могут быть качающимися или вибрационными, барабанные — круглыми или полигональными.
1.2.2.1. Основы теории работы плоского качающегося сита
Условие прохода зерна через отверстие выразится уравнениями (рис. 1.32):
х = vt = D − d ;
|
|
|
|
|
|
|
|
|
|
2 |
|
|
|
|
|
|
|
|
||
|
|
|
y = |
|
gt2 |
= |
d |
. |
|
|
|
|
|
|
|
|
||||
|
|
|
|
|
|
|
|
|
|
|
|
|
|
|
|
|||||
|
|
|
2 |
2 |
|
|
|
|
|
|
|
|
|
|||||||
Время свободного падения частиц t = |
2 y |
= |
d |
. |
||||||||||||||||
|
|
|
||||||||||||||||||
|
|
|
|
|
|
|
|
|
|
|
|
|
|
|
|
g |
g |
|||
Подставив значения x и y в формулу, получим |
|
|
||||||||||||||||||
|
|
|
D − |
d |
|
|
|
d |
|
|
|
|
|
|||||||
|
x |
|
2 |
g |
|
|
||||||||||||||
|
|
|
|
|
|
|
||||||||||||||
v = |
|
= |
|
|
= D − |
|
|
|
|
. |
|
|
||||||||
t |
|
|
|
|
|
|
|
|
||||||||||||
|
|
|
d |
|
|
2 |
d |
|
|
g
63
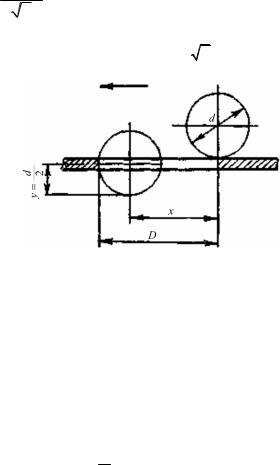
Просеивание будет эффективным, когда размер частиц d несколько меньше отверстий D в системе, т. е. D > d или D = id (i — кратность). Подставляя значение D в формулу, получим
≥ + 0,319v i 0,5 .
d
Наиболее благоприятная скорость, м/с, для просеивания на плоском горизонтальном сите ν = 2,36 d , где d ≈ 0,8D.
Рис. 1.32. Схема к расчету скорости частицы вдоль полотна сита
Работа плоских качающихся сит основана на взаимодействии сил тяжести и сил инерции. Перемещение материала относительно полотна сита возможно только при достаточном ускорении сита.
Найдем ускорение, которое должно быть сообщено частице материала, лежащей на полотне сита, применительно к двум случаям.
Для горизонтального сита (рис. 1.33, а)
Ρи = G a (движущая сила); g
Ρтр = Gf (сила сопротивления),
где Ри — инерционное усилие, Н; a — ускорение сита м/с2;
64
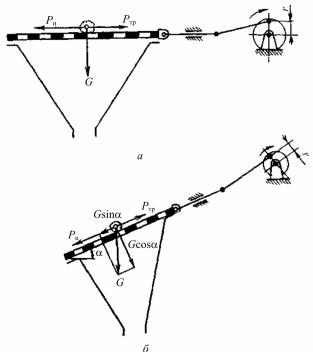
G — |
сила тяжести частицы, Н; |
g — |
ускорение силы тяжести, м/с2; |
f — |
коэффициент трения. |
Движение частицы относительно полотна сита может начаться
только приусловии |
P > P |
, или |
G |
a > Gf , откуда а ≥ gf . |
|
||||
|
и тр |
|
g |
|
|
|
|
Плоское качающееся сито состоит из лотка, который получает возвратно-поступательное движение от шатуннокривошипного механизма. Материал при этом скользит попеременно в ту или другую сторону вдоль полотна сита, просеиваясь сквозь него. Применяются такие сита в малых литейных цехах для приготовления наполнительной смеси на местах формовки.
Рис. 1.33. Схемы плоских качающихся сит: а — горизонтального; б — наклонного
65

Для сита с качанием |
вдоль наклонной плоскости |
|||
(рис. 1.33, б) |
|
|
|
|
(Ρи + G sin α )≥ |
Gf cosα ; |
|||
Ρ |
= |
G |
ω 2r= 4G π2 n2r, |
|
|
||||
и |
|
g |
g |
|
|
|
где ω — угловая скорость кривошипа механизма, приводящего в движение сито, рад/с;
r — радиус кривошипа, м;
n — частота вращения вала кривошипа, с–1.
Частота вращения кривошипа n, обеспечивающая движение материала вниз по полотну сита, определяется по формуле
≥ 1 f cos α − sinα
n .
2r
Втаком сите при наличии симметричного кривошипного механизма материал будет двигаться вниз по уклону, однако угол наклона сита во избежание самоскольжения материала
должен быть меньше его угла трения ϕ по полотну сита.
1.2.2.2. Вибрационные сита
Вибрационное сито представляет собой плоское сито, совершающее под действием динамических факторов колебания в направлении, перпендикулярном к полотну сита. По методу сообщения колебаний полотну вибрационные сита делятся на инерционные и ударные.
Рама инерционного вибрационного сита опирается на пру-
жины и совершает колебания под действием инерционной силы неуравновешенной массы, вращающейся на валу, подшипники которого укреплены на раме (рис. 1.34). Привод с простым дебалансом (а) сообщает колебания ситу не только перпендикулярно плоскости полотна, но частично и в плоскости полотна. Траектория точек сита при этом имеет вид эллипсовидных кривых, параметры которых зависят от соотношения жесткости уп-
66

ругих связей сита в направлениях, перпендикулярном и параллельном полотну.
Рис. 1.34. Схемы привода инерционных вибрационных сит: а — с простым дебалансом; б — с самобалансом
Привод с помощью механизма самобаланса (б) сообщает ситу колебания только в направлении, перпендикулярном к полотну. В направлении же, параллельном полотну сита, возмущающие силы обоих дебалансов уравновешиваются.
Инерционные вибрационные сита устанавливают чаще всего под углом 15–25° к горизонту. Полная амплитуда колебаний 2а = 2… 5 мм. Число полных колебаний в минуту n = 1200… 3000 . Производительность инерционных вибрационных сит на 1 м2 площади сетки, по практическим данным, составляет: 3–5 м3/ч — при размерах ячеек 0,5–2 мм, 5–10 м3/ч — при размерах ячеек 2–5 мм и 10–20 м3/ч — при размерах ячеек
5–12 мм.
На рис. 1.35 показано двухъярусное инерционное вибрационное сито для отработанной формовочной смеси. Сито имеет сварную раму, установленную на восьми пружинах. На раме смонтирован вал с дебалансом, приводимый от стационарного электродвигателя через ременную передачу. Верхнее полотно сита выполнено в виде листа толщиной 4 мм с отверстиями диаметром 40 мм (на рисунке условно показана сетка). Нижнее полотно представляет собой сетку, плетеную из проволоки диаметром 4 мм, с ячейками 15 × 15 мм. Ширина сита 1900 мм, длина 5000 мм, число колебаний в минуту 870. Материал пода-
67

ется на верхнее полотно и, пройдя сначала сквозь него (грубое просеивание), попадает на нижнее, на котором подвергается уже тонкому просеиванию. Производительность сита (до 200 м3/ч) регулируется изменением угла его наклона. Для одновременного дробления комьев просеиваемой смеси над верхним полотном на переставных по высоте осях надеты с большим зазором чугунные кольца, а над нижним полотном на шарнирах смонтирован ряд металлических башмаков с приклепанной к их основанию резиной.
Рис. 1.35. Вибрационное инерционное сито для грубого и тонкого просеивания отработанной формовочной смеси: 1 — рама сита; 2 — опорные пружины; 3 — вал с дебалансом; 4 — верхнее полотно; 5 — нижнее полотно; 6 — кольца; 7 — башмаки; 8 — электродвигатель
Кроме инерционных сит, применяют также ударные вибрационные сита, в которых колебания сообщаются не всему ситу, а лишь его полотну, и передаются ему от специального — электромагнитного или механического — ударного механизма. При этом полотно сита закреплено с двух противоположных (коротких) сторон на раме. Электромагнитный ударный механизм представляет собой электромагнит с подпружиненным якорем,
68
колебания которого с помощью штока, или толкателя, передаются полотну сита. Механический ударный механизм передает колебания полотну сита с помощью подпружиненного штока, который приводится от вращающегося кулачка.
Применяют также ударные вибрационные сита с электромагнитными вибраторами на раме. В них колебания сообщаются не только одному полотну сита, но и легкой подвижной части рам, которая вложена в неподвижную, опертую на амортизаторы основную часть рамы.
Вибрационные сита различных типов имеют амплитуду колебаний 2a в пределах 2–5 мм и число колебаний в минуту чаще всего 1000–2000 (иногда значительно выше).
Положительным качеством вибрационных сит является характер движения на них просеиваемого материала. При колебаниях полотна сита материал подбрасывается кверху и, падая, движется в направлении, приближающемся к перпендикулярному относительно полотна. Такое направление наиболее благоприятно для просеивания. Кроме того, при подбрасывании и падении материала, как и при всяком встряхивании, происходит концентрация наиболее мелких фракций около самого полотна сита, а более крупные фракции располагаются над мелкими, дальше от сетки сита. Это также благоприятствует быстрому просеиванию.
Благодаря указанным обстоятельствам КПД просеивания вибрационных сит весьма высок, обычно в пределах ε = 0,90… 0,98. Вибрационные сита особенно эффективны при тонком просеивании. В литейном производстве вибрационные сита в последнее время применяются все чаще вместо более громоздких барабанных сит, как для отработанной смеси, так и для свежих формовочных материалов.
Общим недостатком вибрационных сит является передача колебаний опорной конструкции. Поэтому при их установке на значительной высоте поддерживающая конструкция должна быть достаточно надежной.
69

При колебании инерционного вибрационного сита возникают два типа колебаний: собственные и вынужденные (в результате действия возмущающей центробежной силы) с периодами времени tc и tb соответственно.
tc = 2π
где m — масса системы
|
|
m |
|
= 2π |
G ≈ |
|
G |
, |
||||
|
∑ Κ |
|
|
|||||||||
|
|
|
|
|
|
|
4K |
|
K |
|||
|
|
t |
|
= |
60 |
|
с. |
|
|
|
||
|
|
в |
|
п |
|
|
|
|||||
|
|
|
|
|
|
|
|
|
|
|||
|
т = |
|
G |
|
|
|
|
|||||
|
|
|
|
; |
|
|
|
|
||||
|
|
|
|
|
|
|
||||||
|
|
|
|
g |
|
|
|
|
G — вес системы с грузами; g — ускорение силы тяжести; K — жесткость пружины;
n — частота колебаний сита.
При совпадении tc и tв сито будет работать в режиме резонанса. Теоретически при резонансе должно быть постепенное возрастание амплитуды колебания до разрушения системы. Однако этого не происходит, так как энергия поглощается на трение в подшипниках и на движение песка.
Для сита, работающего при резонансе tc |
= tв |
; |
G |
= |
60 |
, от- |
K |
|
|||||
|
|
|
|
n |
сюда
K = Gn2 кгс/м. 3600
Возмущающаяся сила P0, представляющая центробежную силу груза G0 (рис. 1.36),
Р0 |
|
m0V 2 |
|
G0 |
|
πn 2 |
G0n2ρ |
|||
= |
|
= |
|
|
|
|
ρ = |
|
. |
|
ρ |
g |
|
900 |
|||||||
|
|
|
|
30 |
|
|
Принимая приближенно, что амплитуда колебания сита a соответствует статической деформации четырех пружин под
70