
Оборудование для подготовки материалов
..pdf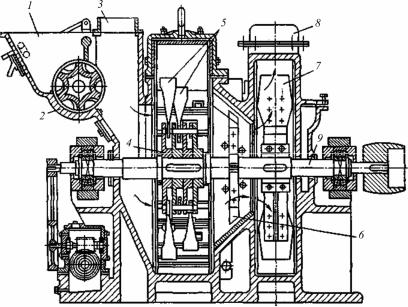
паратор для отделения недомола, а затем в циклон для осаждения годного помола. Установка имеет рециркуляцию воздуха, к которому для подсушки размалываемого материала примешиваются топочные газы. Часть воздуха из системы выбрасывается в атмосферу. Для окончательного обеспыливания эту часть воздуха после циклона желательно пропускать через матерчатый фильтр или второй циклон. Для задержания крупных частиц материала и недопущения их прохода из мельницы в вентилятор служит крестовина сножами, которую можно переставлять на валу. Чем меньше зазор между ножами крестовины и стенкой, тем более тонкий помол пропускает крестовина из мельницы. Кожух мельницы изнутри имеет сменную футеровку в виде плит из стали. Производительность описанной мельницы — 1 т/ч угля. Молотковые мельницы хорошозарекомендовали себяв эксплуатации.
Рис. 1.24. Молотковая мельница: 1 — загрузочная воронка; 2 — звездчатый питатель; 3 — подвод воздуха и продуктов горения; 4 — ротор; 5 — молотки; 6 — крестовина с ножами; 7 — вентилятор; 8 — выход аэросмеси; 9 — вал
51

Если вместо свободного подвешивания на шарнирах била закрепить на роторе мельницы жестко, то получится крестовая мельница. На рис. 1.25 показана крестовая мельница для размалывания угля. На роторе мельницы имеются жестко закрепленные лопатки, которые размельчают материал. В остальном устройство мельницы аналогично шаровым или молотковым мельницам с воздушной сепарацией продукта размалывания. Производительность крестовой мельницы описанного типа (с диаметром ротора 850 мм иn = 1500 об/мин) составляет 2–2,5 т/ч(считаяпо бурому углю).
Рис. 1.25. Размалывающая установка с крестовой мельницей: 1 — мельница; 2 — ротор; 3 — лопатки; 4 — вентилятор; 5 — проточный сепаратор; 6 — загрузка угля; 7 — вход горячего воздуха; 8 — питатель сырого угля; 9 — магнитный сепаратор
52

1.1.2.2.3. Мельницы по типу бегунов
Чаша мельницы (рис. 1.26) вращается от привода и имеет форму конической тарелки со сменной рабочей частью. Над чашей находятся три катка, один из которых показан на чертеже. Катки также имеют коническую форму, однако вершина конуса катка не совпадает с вершиной конуса рабочей поверхности чаши. Вследствие этого качение катков по чаше происходит со скольжением, и материал катками не только размалывается, но и истирается.
Рис. 1.26. Мельница по типу бегунов: 1 — чаша; 2 — каток; 3 — пружина катка; 4 — упорный винт; 5 — питатель; 6 — кожух, в который подводится воздух от вентилятора; 7 — проточный сепаратор
53
Оси катков монтированы на рычагах, которые с помощью пружин с регулируемым натяжением прижимают катки к чаше. При помощи упорных винтов рычаги с катками можно установить так, чтобы между катком и чашей оставался зазор определенного размера. Обычно катки устанавливают с постепенно уменьшающимися зазорами относительно чаши, считая от места загрузки материала в мельницу.
В спиральный кожух, имеющийся вокруг мельницы, вдувается тангенциально по трубе от вентилятора воздух, уносящий размолотый продукт в проточный сепаратор, встроенный
вмельницу. В сепараторе отделяется недомол, падающий снова
вмельницу. Далее поток направляется в циклон для осаждения готового помола. Часть воздуха из циклона выбрасывается в атмосферу, по пути проходя второй циклон или матерчатый фильтр для окончательного обеспыливания. Взамен этой части воздуха, удаляемой в атмосферу, в систему добавляется свежий воздух и топочные газы для подогрева воздуха в системе подсушивания размалываемого материала.
Мельницы по типу бегунов хорошо зарекомендовали себя
вработе.
1.1.2.2.4. Вибрационные мельницы
Вибрационные мельницы применяют для тонкого помола кварцевого песка, огнеупорной глины, угля, кокса и других материалов. В отличие от шаровых мельниц и бегунов, в вибромельницах материал разрушается в результате ударного и истирающего воздействия мелющих тел, что позволяет резко интенсифицировать процесс, а вследствие равномерной и значительной циркуляции мелющих тел достигается высокая однородность помола.
Вибрационная мельница (рис. 1.27) состоит из помольной камеры 2, вибратора 1, вынесенного на внешнюю сторону корпуса мельницы (помольной камеры), опорной рамы 3, электродвигателя 6 и упругой муфты 4, соединяющей валы электродви-
54

гателя и дебалансный. Помольная камера 2 представляет собой стальной полый цилиндр, служащий корпусом мельницы, он футерован листовой сталью в зоне действия мелющих тел и материала.
Помольная камера установлена на четыре пружины 7, ее торцовая стенка 8 съемная. В верхней части камеры имеется загрузочная воронка 5, а в нижней — разгрузочная 9, с решеткой колосникового типа, свободно пропускающей измельченный материал, но задерживающей мелющие тела. Во избежание пылевыделения все отверстия закрывают пробками с резиновыми уплотнениями.
Опорную металлическую раму 3 вибрационной мельницы устанавливают на деревянный настил, а под нее подкладывают листовую резину. Это исключает вредное воздействие вибрации на фундамент.
Мелющие тела представляют собой стальные цилиндры диаметром 10–20 мм и высотой 1,5D. Масса мелющих тел в 2–3 раза больше массы загружаемого для помола материала.
Рис. 1.27. Вибромельница
55
Производительность вибрационных мельниц в два раза больше производительности шаровых мельниц (с тем же электродвигателем), а энергозатраты на 1 т продукции — в 1,5– 2 раза меньше. Вибрационные мельницы менее чувствительны к высокой влажности материала. Например, при помоле на бегунах и в шаровой мельнице требуется предварительная сушка глины до влажности 2–3 %, а в вибрационной мельнице можно измельчать глину влажностью до 6–8 %.
Собственная масса вибрационных мельниц и их габаритные размеры значительно меньше шаровых для одной и той же мощности привода. Частота колебаний вибратора мельниц обычно составляет 25 Гц, амплитуда колебаний помольной камеры 4–5 мм. Вибрационная мельница, представленная на рис. 1.27, не является типовой, существуют и другие типы вибрационных мельниц, но принцип их работы тот же.
1.2. Оборудование для подготовки оборотной формовочной смеси
В современных условиях автоматизации технологических процессов однородность всех исходных материалов имеет весьма большое значение для стабильной работы оборудования и получения запрограммированного качества формовочных смесей. Оборотная смесь, отработанная, выбитая из залитых форм и подготовленная для повторного использования, основной компонент формовочной смеси. Она имеет весьма нестабильные качественные показатели и неудовлетворительные технологические свойства. Подготовка этой смеси для использования в составе приготовляемых формовочных смесей включает следующие операции: удаление металлических включений; просев и разрушение комьев, удаление пыли; гомогенизация (повышение степени однородности) по влаге; охлаждение до заданной температуры.
Оборудование, используемое для перечисленных операций, разделяется на группы: магнитные сепараторы; оборудование
56
для просеивания смесей; устройства для гомогенизации; охладители смесей.
1.2.1. Магнитные сепараторы
Отработанная смесь содержит металлические частицы, образующиеся при заливке металла в формы. Удаленные из отливок стержни после дробления освобождаются от металлической арматуры и каркасов, которые попадают в отработанную смесь. Кроме того, в смесь часто попадают случайные металлические предметы и металлические пылевидные частицы. Общая масса металлических включений в отработанной формовочной смеси (если их не удалять) составляет 0,5–1,0 мас. % смеси. От содержания металлических частиц в смеси зависит не только ее качество, но и величина межремонтного периода оборудования (технологического и транспортного), составляющего смесеприготовительный комплекс.
Удаляются металлические частицы при помощи специальных устройств — магнитных сепараторов. Материал пропускается через зону с сильным магнитным полем. Железосодержащие частицы и куски металла притягиваются магнитом к несущему органу, а затем отводятся им.
В качестве магнитных железоотделителей используются магнитные шкивы, магнитные барабаны и ленточные магнитные сепараторы.
Магнитный шкив (рис. 1.28) представляет собой вращающийся многополюсный электромагнит, который обычно устанавливается в качестве приводного барабана на ленточных транспортерах или питателях. Обрабатываемый материал движется на ленте к магнитному шкиву. При этом содержащиеся в нем металлические частицы притягиваются к шкиву, перемещаются вместе с ним на некоторый угол, а затем лентой выводятся из зоны действия магнитного поля и падают вниз в специальную тару или на транспортер.
Магнитная система шкивного сепаратора состоит из насаженных на вал 1 железных колец 2 (сердечников) и намотанных
57

на них катушек 3, к которым с помощью двух колец 4 и щеток 5 подводится постоянный ток, вырабатываемый моторгенератором. Направление витков тока в катушках обеспечивает чередование полярности сердечников. Катушки пропитываются и заливаются теплопроводящим изолирующим составом, а для предохранения от повреждений закрываются латунными кольцами.
Рис. 1.28. Схема магнитного шкива
Объемная производительность, м3/с, магнитного шкива
Π = ψ bhv,
где ψ — коэффициент, учитывающий использование ширины
ленты;
b — ширина ленты, м;
h— толщина слоя материала, м;
ν— скорость вращения барабана, м/с.
Магнитный барабан состоит из вращающегося полого цилиндра и неподвижной магнитной системы. Он может быть использован и как приводной барабан ленточного транспортера, и как самостоятельное пересыпное устройство. Принципиальное различие между электросепараторами шкивного и барабанного типов состоит в том, что в первом магнитная система вращается вместе со шкивом, а во втором она неподвижна. В барабанных
58
сепараторах нет распределительных, колец и угольных щеток для передачи тока вращающимся электромагнитам. Они более надежны в работе, но применение их вызывает конструктивное усложнение привода. Кроме того, барабанные сепараторы при тех же размерах имеют поле меньшей напряженности и поэтому обладают меньшей производительностью, чем шкивные.
Магнитная система барабанных железоотделителей выполняется в двух вариантах (рис. 1.29, а и б). В первом варианте катушки надеты на ось барабана, во втором они расположены по диаметрам барабана. Магнитная система второго варианта позволяет получить при одном и том же диаметре барабана более сильное поле (разместить большее число витков обмотки).
Как в шкивном, так и в барабанном сепараторе сила притяжения, металлических частиц зависит от их массы и удельной магнитной восприимчивости, а также напряженности магнитного поля на окружности вращения центра тяжести этих частиц. Частицы, обладающие меньшей массой, а также лежащие дальше от поверхности шкива или барабана, испытывают меньшее притяжение и, кроме того, при перемещении преодолевают сопротивление смеси, в которую вкраплены.
Для качественной очистки смеси рекомендуется шкивы устанавливать последовательно в цепи ленточных транспортеров. Вэтом случае металлические частицы, располагавшиеся в верхних слояхпотока, окажутся внизу, у самойповерхности сепаратора.
Отечественная промышленность выпускает шкивные сепараторы типа ШЭ для конвейеров с шириной лент 650–1400 мм.
Расчет магнитных сепараторов шкивного и барабанного типов заключается в определении силы притяжения Pм. Эту задачу удобнее всего решить, рассматривая движение металлических частиц на барабане магнитного сепаратора (рис. 1.30).
На металлическую частицу массой m, находящуюся на радиусе с углом α к вертикали, действуют следующие силы: сила тяжести G, центробежная сила инерции Pц, сила магнитного притяжения Pм, сила трения частицы о поверхность барабана Pтр.
59

Рис. 1.29. Магнитные барабаны с осевым (а) и поперечным (б) расположением катушек: 1 — сердечник; 2 — ось; 3 — катушки; 4 — подача сепарируемого материала; 5 — немагнитный материал; 6 — магнитные включения
Частица будет удерживаться на поверхности барабана при условии, что Ртр ≥ G sinα .
Сила трения может быть представлена в виде
Ρтр = (РМ + G cos α− PЦ ) f ,
откуда
60