
Современные научные исследования в дорожном и строительном производс
..pdfи ремонту, сделать его конкурентоспособным, повысить заинтересованность исполнителей и самое главное – оправдать ожидания клиентов в плане высокого качества, обеспечив тем самым экономическую эффективность предприятия.
Список литературы
1.ЗАО «Держава». Пояснительная записка к годовому отчету по произ- водственно-хозяйственной деятельности управления технологического транс-
порта. – 2010.
2.Положение о техническом обслуживании и ремонте подвижного состава автомобильного транспорта. – М.: Транспорт, 1986. – 72 с.
3.Масуев М.А. Проектирование предприятий автомобильного транспорта: учеб. пособие. – М.: Феникс, 2009. – 310 с.
4.Дмитренко В.М. Технологические процессы технического обслуживания, ремонта и диагностирования подвижного состава автомобильного транспорта / Перм. гос. техн. ун-т. – Пермь, 2004. – 266 с.
5.Напольский Г.М. Технологическое проектирование автотранспортных предприятий и станций технического обслуживания: учеб. пособие. – М.: Транс-
порт, 1993. – 172 с.
21
ВЫБОР МАТЕРИАЛА ВКЛАДЫША ШАРОВОЙ ОПОРЫ ТРАНСПОРТНОЙ МАШИНЫ
М.А. Верняев
Ижевский государственный технический университет, Россия
Вкладыш является неотъемлемой частью шаровой опоры и располагается между шаровой головкой и корпусом. Вкладыш воспринимает большие нагрузки, передающиеся через палец шаровой опоры от подвески, а также нагрузки, которые воспринимает при движении колесо от опорной поверхности дороги.
В качестве вкладыша большинство производителей используют различные композиции полимерных соединений на основе полиамида, имеющие индивидуальные механические и физические свойства, а также долговечность [1, 2, 3, 4].
Полиамид – наиболее оптимальный с точки зрения эксплуатационных и других свойств материал, который можно использовать в качестве вкладыша. Это синтетический материал с наиболее приемлемыми тепловыми и физическими свойствами, такими как высокая прочность, низкий коэффициент трения с любым материалом, позволяющими использовать их для производства вкладышей шаровых опор. Синтетические материалы, в основе которых полиамид, позволяют получить поверхность с малой шероховатостью, гладкую, устойчивую к износу при работе узла.
На ранних этапах автомобилестроения применялись металлические вкладыши, использование которых приводило к более низким показателям долговечности изделия. Именно внедрение полимерного материала между трущимися металлическими деталями шаровой опоры приводит к увеличению пятна контакта, что, в свою очередь, позволяет снизить давление в центре пятна
Необходимо принять во внимание тот факт, что в процессе эксплуатации вкладыш и смазка подвергаются тепловому воздействию вследствие трения. Металл, как конструкционный материал, имеет коэффициент температурного расширения ниже, чем у вкладыша и смазки, т.е. подвергается температурному воздействию в меньшей степени. А так как зазор в сопряжении корпус– вкладыш–шаровая головка минимален, при работе шаровой опоры на вкладыш вследствие нагрева и недостатка пространства для возможности расширения оказывают воздействия огромные сжимающие нагрузки. Следует учесть и тот факт, что вещество, из которого выполнена смазка, при нагреве начинает расширяться, тем самым занимая и так небольшое пространство между трущимися поверхностями.
Следствием таких процессов внутри узла является сжатие головки пальца шаровой опоры и выдавливание пальца шаровой опоры из корпуса.
22
В том месте вкладыша, куда приложена наибольшая по величине нагрузка, изнашивание материала происходит интенсивнее, что в результате приводит к разрушению вкладыша и к выходу из строя узла.
Следует отметить, что смазка между головкой пальца и вкладышем в шаровой опоре играет важную роль. Она не только снижает коэффициент трения в паре, но и отводит часть температуры при работе узла. При нагревании пар трения в шаровой опоре смазка начинает растекаться, т.е. она стремится покинуть зону трения. Причина тому кроется в теплофизических свойствах смазки, а именно – в коэффициенте теплового расширения. В силу своей природы коэффициент теплового расширения вещества, из которого изготовлена смазка, выше, чем коэффициент теплового расширения металла, из которого изготовлена головка шарового пальца.
Всвязи с этим важной проблемой на сегодняшний день является разработка способа удержания смазки или ее частиц на рабочей поверхности головки шаровой, в месте пятна контакта с вкладышем.
Впатентной литературе отражены способы удержания смазки, а именно –
применение модернизированного вкладыша с канавками на поверхности трения (патент на изобретение РФ №2029895, дата публикации 27.02.1995 г.). Модель такого вкладыша предполагает дополнительную обработку поверхности трения с нарезанием канавок, которые способствуют удержанию смазки в зоне трения. Важным недостатком такого конструкторского решения является ослабление конструкции вкладыша вследствие утоньшения слоя при нарезании канавок. Конструктивное исполнение вкладыша выглядит следующим образом: по всей поверхности соприкосновения вкладыша и шара пальца нарезаны канавки определенной глубины.
При действии нагрузки места сопряжения дна и стенки канавки выступают концентраторами напряжений. При прохождении вектора нагрузки это место испытывает наибольшие напряжения, следовательно, и разрушается интенсивнее других поверхностей вкладыша.
В.П. Недиков предложил конструкцию шаровой опоры, которая содержит корпус, палец с шаровой головкой, вкладыш, расположенный между шаровой головкой и корпусом. На наружной поверхности вкладыша выполнены кольцевые канавки для улучшения антифрикционных свойств.
Недостаток образца в том, что поверхность контакта вкладыша и корпуса уменьшена за счет наличия канавок. Каждая канавка содержит стенки и дно. В продольном сечении шаровой опоры наружная граница вкладыша содержит вогнутые и выпуклые участки. Возникают концентраторы напряжений и уменьшается пятно контакта, что негативно сказывается на ресурсе опоры.
Совершенно другую конструкцию вкладыша предложил использовать А.А. Войнов [1]. Долговечность вкладыша на основе полиамида предлагается повысить путем введения в состав композиции дополнительных элементов хи-
23
мической и металлической природы. Предлагается наряду с антифрикционным полимерным вкладышем применять композиционную подложку, представляющую собой гранулированные частицы металла.
Приведенные результаты теоретических и практических исследований позволяют утверждать, что модифицирование композиционной подложки вкладыша металлическими гранулами повышает ее упругие свойства и приводит к снижению интенсивности изнашивания и повышению долговечности шаровой опоры. Следует отметить, что это довольно перспективная разработка с точки зрения надежности и безопасности.
Принимая во внимание вышеизложенную информацию, можно сделать вывод, что выбор материала вкладыша для шаровой опоры транспортной машины является очень сложным процессом. Дело в том, что при выборе материала вкладыша необходимо учитывать не только назначение транспортной машины, будь то дорожная или строительная техника, но и условия ее эксплуатации. При расчете долговечности вкладыша необходимо учитывать нагрузки, которые он будет воспринимать, их продолжительность, амплитуду изменений, условия, в которых ему предстоит работать. Исходя из полученных в расчете данных, проектировщик получает ряд параметров, которые характеризуют показатели материала вкладыша, такие как ресурс, надежность, долговечность. На основании полученной информации подбирается материал вкладыша, наиболее удовлетворяющий с точки зрения требуемых свойств и экономических вложений.
Список литературы
1.Патент на изобретение РФ № 2029895, опубликовано 27.02.1995 г.
2.Патент на изобретение РФ № 2080497, опубликовано 27.05.1997 г.
3.Патент на изобретение РФ № 2130558, опубликовано 20.05.1999 г.
4.Патент на полезную модель РФ № 43046, опубликовано 27.12.2004 г.
5.Войнов А.А., Артемов И.И. Повышение долговечности шаровых опор легковых автомобилей // Изв. вузов. Машиностроение. – 2007. – № 9. − С. 43−51.
24
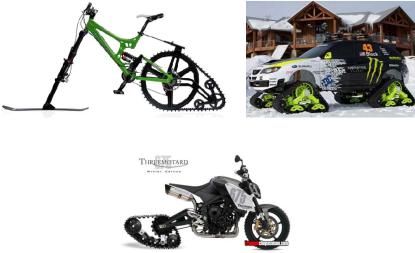
КОМПЛЕКСНАЯ МЕТОДИКА ИССЛЕДОВАНИЯ ГУСЕНИЧНОГО ДВИЖИТЕЛЯ С ПОМОЩЬЮ КИНО- И ФОТОСЪЕМКИ
О.П. Водченко, А.О. Водченко
Национальный технический университет «Харьковский политехнический институт», Украина
Гусеничный движитель отвоевывает у колесного движителя все большее пространство среди транспортных средств (рис. 1, 2, 3).
Рис. 1. Велосипед |
Рис. 2. Внедорожник |
Рис. 3. Мотоцикл
Для разработки новых и реконструирования ранее созданных систем с гусеничным движителем нужно выработать эффективные подходы к исследованию элементов движителя и гусеничного движителя в целом. Известно исследование натяжения гусеничного обвода гусеничного движителя с помощью кино- и фотосъемки, однако в нем мало информации [1]. Комплексный подход к исследованию гусеничного движителя с помощью кино- и фотосъемки расширяет возможности исследования.
Тензотрачный вариант измерения растягивающих усилий в гусеничном обводе [1] требует установки тензотрака в гусеницу, создания кронштейна и упругого жгута с навитым на нем участком кабеля, связывающего тензотрак с тензоусилителем. Кроме того, требуется питание аппаратуры (комплект аккумуляторов, преобразователь напряжений для питания осциллографа и блока тензоусилителей). Также проводится тарировка тензотрака с использованием динамометра, устанавливаемого в неподвижную гусеницу. На ведущем колесе закрепляется нагрузочное устройство. Величина растягивающего усилия в участке
25

гусеничного обвода, где располагается тензотрак, фиксируется на ленте осциллографа в виде расстояния между нулевой линией и линией, определяющей растяжение тензотрака.
Оттарированный тензотрак последовательно информирует о нагрузках в участках гусеничного обвода, которые он проходит. Такой метод оценки нагруженности гусеничного обвода не полон.
Тензотрачный метод измерения растяжения гусеницы может создать картину нагрузок в гусенице плавно двигающегося гусеничного модуля по ровной дороге без препятствий, а для исследования изменяющихся параметров гусеничного обвода такой метод неприемлем.
Рис. 4. Схема измерительного полигона с базовой измерительной сеткой: 1 – фотоаппарат; 2 – сектор фотосъемок; 3 – край сектора киносъемки; 4 – край разрешительного проезда гусениц; 5 – погрешность кинофиксации обекта измерений; 6 – корпус машины; 7 – измеряемая гусеница; 8 – сетка горизонтали; 9 – вертикальные стойки измерительной сетки; 10 – левый край сектора киносъемки; 11 – центральная ось киносъемки; 12 – правый край сектора киносъемки; 13 – сектор настройки измерительной сетки нивелиром; 14 – нивелир;
15 – кинокамера
Методика измерения усилий растяжения участков гусеничного обвода по кадрам кино- и фотосъемок (кинофотосъемочный вариант измерения растягивающих усилий в гусеничном обводе [1]) нуждается в измерительном полигоне (рис. 4, 5) с базовой измерительной сеткой, также необходимы кинокамера и фотокамера на штативах, запас фото- и кинопленки.
Измерительный полигон формируется относительно центральной оси 11 киносьемок. Ось 11 выбирается перпендикулярно к ровному участку скоростного движения транспортных машин с краем 4 разрешительного проезда гусениц. Вдоль края 4 на расстоянии 0,5–1 м формируется базовая измерительная сетка, состоящая из вертикальных стоек 9 и горизонталей 8 (см. рис. 5). Стойки 9 устанавливаются вертикально вдоль края 4 в одну линию с равными промежутками, например через 2 м. К стойкам 9 крепятся горизонтали 8. Каждая из горизонта-
26
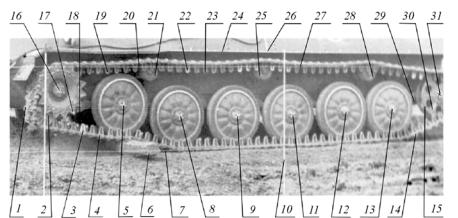
лей 8 состоит из участков между стоек 9 и узлов крепления к стойкам 9. Каждый узел крепления участков устанавливается по высоте при помощи нивелира 14, формируя одну из горизонталей 8. Количество горизонталей 8 (от одной до трех) определяется объектом исследования.
Для получения более точных данных измерений неободимо размещать объект исследования на центральной оси 11 киносъемки, как показано на рис. 4.
Расстояние LGr от кинокамеры или от фотоаппарата до базовой сетки должно быть максимальным по возможностям кинокамеры и фотоаппарата.
Расстояние LC от базовой сетки до разрешительного края 4 должно быть минимально возможным и зависит от профессиональных навыков водителя машины. Погрешность b5 – 5 и расстояние b3 до края 3 сектора киносъемки соотносятся как LC и LGr. Меньшая погрешность b5 – при меньшей величине расстояния LC.
Рис. 5. Опытный образец гусеничного движителя с рычажной системой управления натяжением гусениц [2] (режим – переезд бревна): 1 – наклонный участок гусеничного обвода между ведущим колесом и натяжным роликом; 2 – натяжной ролик; 3 – меченый трак 01; 4 – участок гусеницы у натяжного ролика; 5 – маркер центра первого опорного катка; 6 – преграда «Бревно»; 7 – нижняя горизонталь измерительной сетки; 8 – маркер центра второго опорного катка; 9 – маркер центра третьего опорного катка; 10 – вторая вертикальная стойка измерительной сетки; 11 – маркер центра четвертого опорного катка; 12 – маркер центра пятого опорного катка; 13 – маркер центра шестого опорного катка; 14 – нижняя наклонная ветвь гусеницы у натяжного колеса; 15 – натяжное колесо; 16 – маркер центра ведущего колеса; 17 – маркер зуба ведущего колеса; 18 – рычаг управления положением натяжного ролика; 19 – центральный трак наклонной ветви гусеницы у ведущего колеса; 20 – верхняя горизонталь измерительной сетки; 21 – первый поддерживающий ролик; 22 – меченый трак 02; 23 – центральный трак второй верхней ветви гусеницы; 24 – горизонталь корпуса модуля у центра масс модуля; 25 – второй поддерживающий ролик; 26 – центр масс модуля; 27 – второй участок верхней горизонтали измерительной сетки; 28 – третий поддерживающий ролик; 29 – рычаг управления положением; натяжного колеса; 30 – маркер поворота натяжного колеса; 31 – маркер центра
натяжного колеса
27

Дополнительная разметка элементов гусеничного обвода и корпуса гусеничного модуля позволяет расширить грани анализа гусеницы.
Так, разметка центра масс корпуса гусеничного модуля (см. поз. 26 на рис. 5) позволяет отслеживать вертикальные перемещения и наклоны (в плоскости базовой измерительной сетки) корпуса гусеничного модуля.
Разметка (в виде перекрестия – см. поз. 16 рис. 5) центра ведущего колеса позволяет с высокой точностью определить угол наклона корпуса гусеничного модуля (при вертикальном перемещении этого маркера 16 и нулевом перемещении маркера 26 центра масс корпуса гусеничного модуля).
Маркер 17 позволяет оценивать угол поворота ведущего колеса от кадра к кадру.
Использовалась новая методика для двух вариантов опытных гусеничных движителей (рис. 6): с рычажными четырехзвенниками и без них.
Рис. 6. Опытный образец гусеничного движителя без передней рычажной системы управления натяжением гусеницы
Рис. 7. Измерение длин и провисаний переднего участка гусеничного обвода с помощью линейки: 1 – начало волнообразно провисающего переднего наклонного участка гусеничного обвода; 2 – измерительная линейка; 3 – трак провисающего участка гусеницы; 4 – конец волнообразно провисающего переднего наклонного участка гусеничного обвода у ве-
дущего колеса при преезда бревна
28
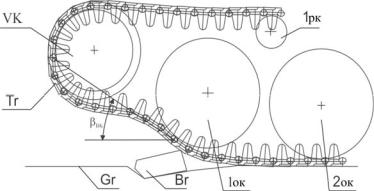
Силу Т растяжения провисающих участков гусеничного обвода (рис. 7, 8) считают по формуле [2]: Т = ql2/(8f), где q – вес единицы длины гусеницы.
Изложенная комплексная методика с использованием кино- и фотосъемок проста в использовании (настраивается в течении двух-трех часов), информативна и наглядна. Эта методика органично вписывается в исследование управляемого гусеничного обвода.
Рис. 8. Модель волнообразного провисания переднего наклонного участка гусеничного обвода (с учетом рис. 7): VK – ведущее колесо; Tr – трак участка гусеницы; Gr – грунт; Br – бревно; 1ок – первый опорный каток; 2ок – второй опорный каток; 1рк – первый поддерживающий каток; βвк – угол наклона участка гусеничного обвода
у ведущего колеса при переезде бревна
Изложенная кинофотосъемочная методика имеет перспективы использования в широком круге исследований.
Список литературы
1. Водченко О.П. Исследование натяжения гусеницы транспортной машины с помощью кино- и фотосъемки // Инновации в транспортном комплексе. Безопасность движения. Охрана окружающей среды: материалы междунар. науч.-практ. конф. – Т. 1. – Пермь: Изд-во Перм. гос. техн. ун-та, 2010. –
С. 50–53.
2.Гусеничные транспортеры-тягачи / В.Ф. Платонов. – М.: Машинострое-
ние, 1978. – 350 с.
3.Водченко О.П. Ходовая часть гусеничного транспортного средства.
АС СССР № 1270049. – М., 15.07.86.
29
ИССЛЕДОВАНИЕ СИЛОВОЙ ЗАГРУЗКИ И ПОВЫШЕНИЕ ЭФФЕКТИВНОСТИ МОДЕЛИРОВАНИЯ ПРОЦЕССОВ ФУНКЦИОНИРОВАНИЯ СКРЕПЕРА
Г.Н. Волков, В.И. Кычкин
Пермский государственный технический университет, Россия
В настоящее время решению вопросов повышения эффективности функционирования землеройно-транспортных машин (ЗТМ) на основе разработки физической теории, включающей системный подход, энергетическую концепцию, аксиомы и законы механики, уделяется значительное внимание [1]. Однако следует отметить, что модели указанных процессов еще не получили достаточного количественного подтверждения.
Цель работы – создать алгоритм и программу (ПК) расчетов количественных показателей, устанавливающих корреляционные связи реакций опорной поверхности, усилия резания, мощности двигателя внутреннего сгорания (ДВС), рабочей скорости машины, загрузки рабочего оборудования для достижения максимальной эффективности с последующими рекомендациями по автоматизации процессов управления и применения информационных технологий.
Наиболее энергоемкой является операция копания грунта, так как кроме сил сопротивления передвижению скрепера и резания грунта могут возникать проблемы проталкивания грунта в ковш через слой находящегося там грунта в заключительной стадии заполнения ковша. Вследствие этого тяговая способность скрепера может исчерпаться прежде, чем заполнится ковш. Нормальные реакции опорной поверхности на колеса скрепера влияют на его тяговые, тормозные и скоростные качества, а также на устойчивость и прочность ряда узлов и деталей. Их величина определяется значениями эксплуатационной массы, компоновкой, режимами и условиями работы машины.
Проведем расчет нормальных реакций при использовании трех методов вычисления. Для примера примем следующие исходные данные:
GT |
= 80 кH, Gr = 200 кH, L = 6 м, P1 = 60 кH и P2 =1 кH, hp = 0,15 м, |
rk |
=1,1 м, T = 80 кH, c =1,1 м, d = 2,1 м, r = 3,1 м, а = 2,47, е = 2,9 м. |
Будем рассматривать прямолинейное равномерное движение скрепера по горизонтальной поверхности. Типовая расчетная схема для определения нормальных реакций заимствована из теории автомобилей и тракторов и основана на законах и аксиомах статики твердого тела, определяющих равновесие машины под действием системы сил (метод 1). Недостаток данной схемы состоит в том,
30