
Современные научные исследования в дорожном и строительном производс
..pdf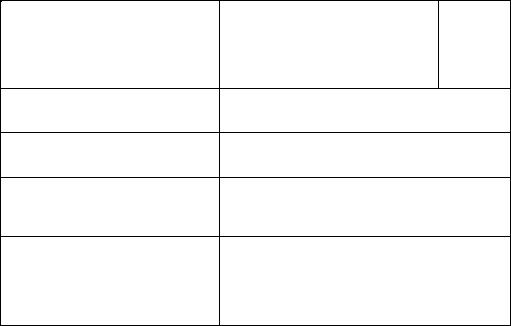
Технология |
Автомо- |
Исходный |
|
источник |
|||
|
биль |
энергии |
|
|
|
||
Двигатель на |
|
Природный |
|
|
|||
природном |
Honda CNG |
||
газе |
|
газ |
|
|
|
||
Водородные |
|
Природный |
|
топливные |
Honda FCX |
||
элементы |
|
газ |
|
|
|
||
Дизельный |
VW Jetta |
Нефть |
|
двигатель |
Diesel |
||
|
|||
Бензиновый |
Honda |
Нефть |
|
двигатель |
Civic VX |
||
|
|||
Гибридный |
Honda |
|
|
автомобиль |
Нефть |
||
Civic |
|||
(Бензин/ |
|||
Hybrid |
|
||
Электро) |
|
||
|
Природный |
||
Электро |
Tesla |
||
Roadster |
газ |
||
|
Эффектив- |
Расстояние, |
Энергетиче- |
|
ность пере- |
|||
работки, |
проходимое |
ская |
|
эффектив- |
|||
доставки |
на единицу |
ность |
|
и заправки |
топлива |
||
автомобиля |
|||
(суммарно) |
|
|
Полная энергетическая эффективность
86,0 % |
17,5 км/кг |
0,39 |
0,32 |
|
км/МДж |
км/МДж |
|||
61,0 % |
84 км/кг |
0,7 км/МДж |
|
|
0,43 |
||||
км/МДж |
||||
90,1 % |
17,2 км/л |
|
|
|
0,47 |
0,42 |
|||
км/МДж |
км/МДж |
|||
|
|
|||
81,7 % |
14,2 км/л |
0,46 |
0,38 |
|
км/МДж |
км/МДж |
|||
|
|
|||
81,7 % |
17,3 км/л |
0,56 |
0,46 |
|
км/МДж |
км/МДж |
|||
|
|
|||
52,5 % |
151 Вт·ч/км |
|
|
|
1,84 |
0,97 |
|||
км/МДж |
км/МДж |
Гибридные автомобили представляют собой сочетание лучших качеств двигателя внутреннего сгорания и электромотора. В последнее время у гибридных авто появляется все больше как почитателей, так и тех, кто достаточно скептически относится к этому новому явлению в области моторов.
Если говорить о преимуществах подобных автомобилей, то их довольно много. К числу основных можно отнести значительное снижение расхода топлива. Практика показывает, что гибридные автомобили потребляют в среднем на 20–25 % меньше горючего, чем традиционные автомобили. При этом стоит отметить, что все базовые параметры гибридного автомобиля не уступают характеристикам машины на двигателе внутреннего сгорания. Таким образом, гибридные автомобили очень экономичны, что можно считать их основным преимуществом.
Не менее важным достоинством можно назвать и экологичность такого типа автомобилей. Экологичность гибридных автомобилей обеспечивается путем рационального расхода углеродного топлива, что позволяет свести к минимуму вредные выбросы в атмосферу.
Однако и на этом перечень преимуществ гибридных автомобией не исчерпывается. Неоспоримое достоинство этих автомобилей – ходовые параметры, которые зачастую превосходят характеристики традиционных автомобилей с двигателем внутреннего сгорания. Обеспечивается это за счет рационального накопления и последующего перераспределения мощностей, которые вырабатываются обоими типами моторов: двигателем внутреннего сгорания и электромотором.
161
Основное препятствие на пути массового применения водорода в качестве топлива для автомобилей – инфраструктура. Продавать сверхдорогие водородные автомобили даже на приемлемых условиях лизинга, не имея развитой сети заправок, невозможно. Строить сеть заправок без водородного автопарка – рискованно. Широкому распространению таких машин пока мешает высокая стоимость топливных ячеек, баков для хранения водорода на борту и отсутствие развитой сети водородных заправок.
Список литературы
1.http://formulahybrid.ru.
2.http://www.popmech.ru.
162

РОБОТЫ В КОНВЕЙЕРНОЙ СБОРКЕ АВТОМОБИЛЕЙ
Е.В. Поезжаева, П.В. Смолоногин
Пермский государственный технический университет, Россия
Многих автолюбителей всегда интересовал вопрос производства их автомобилей. При сборке автомобилей из огромного разнообразия деталей получается автомобиль, готовый к эксплуатации. Эта сборка получила определение «отверточная сборка». Основные этапы отверточной сборки:
1.Отверточная сборка или крупноузловая сборка автомобилей представляет собой некий конструктор. Иногда можно встретить выражение, что производство работает в режиме SKD (Semi Knocked Down). На завод в специальных металлических конвейерах поставляются детали автомобиля в сборе – кузов автомобиля, двигатель, элементы подвески, трансмиссия и другие детали (рис 1).
2.После поставки кузова целиком специалисты автосборочного производства полностью проверяют его на механические повреждения.
3.Потом кузов снимают с палеты, на которой он устанавливался в конвейере. Это процесс сборщики называют «перепаковка». Также во время перепаковки извлекают детали автомобиля, которые помещаются в специальный ящик.
Рис. 1. Часть процесса отверточной сборки – установка силового агрегата
4. Далее все детали распределяют согласно их назначению и месту установки. Так, крепеж укладывают в одно место, а пластмассовые детали – в другое. Детали платформы автомобиля и ходовой части устанавливают на специальную
163
платформу, где к ним монтируют элементы подвески и тормозной системы, т.е. полностью подготавливают шасси автомобиля для последующего соединения его
скузовом.
5.«Свадьба» – в профессиональном сленге – процесс соединения кузова автомобиля с его шасси. Это одна из самых ответственных операций при отверточной сборке автомобиля, так как она является очень трудоемкой и сложной.
6.После автомобильной «свадьбы» подсоединяют все недостающие детали и агрегаты. Подключают всю электропроводку, шланги и трубки. После этого заливают в автомобиль все необходимые технические жидкости: масло, антифриз, тормозную жидкость.
7.Последние этапы отверточной сборки можно объединить в один – контроль готового автомобиля. Специальными тестерами проверяют работу электронных систем нового собранного автомобиля, а также проверяют состояние тормозных систем. Далее автомобиль поступает на трек для тестирования его на пригодность к эксплуатации в дорожных условиях. Трек представляет собой дорожку на несколько сотен метров, где автомобиль проверяют на подозрительный шум и стуки, смотрят на работу подвески и АБС. Заключительные этапы проверки – это «водный тест» (контроль на пропускаемость воды при дожде) и проверка лакокрасочного покрытия.
На первой стадии в сварочном цеху появляется первая цельная конструкция из иностранных комплектующих, напоминающая скелет автомобиля. Когда каркас модели, выверенный вплоть до 0,1 мм, приобретает узнаваемый вид, детали отправляются на проверку сварки.
Найдя ошибку, рабочие отправляют кузов на доработку – в зависимости от сложности недостатка. Модель, которая прошла проверку, перемещается в покрасочный цех, где погружается в ванны с различными растворами, в которых происходит подготовка поверхности кузова к последующей окраске. После сушки кузов отправляется на заделку швов специальным роботом. Далее на все поверхности кузова наносится грунт. Свой финальный цвет кузов автомобиля получает на следующей стадии конвейера – покраской и нанесением лака занимаются специальные роботы. Высушенный кузов отправляется в цех сборки, где в первую очередь рабочие завода прокладывают всю электропроводку. После этого будущий автомобиль оборудуют изоляционными материалами и устанавливают переднюю панель. Следующий этап конвейера – сборка салона и установка элементов моторного отсека, далее – установка дверей, колес и сидений. Последний этап конвейера – программирование электронных блоков автомобиля с использованием технологий, применяемых в мехатронике.
Создаваемые производителями системы работают быстро, производительно и, что самое главное, являются высокоавтоматизированными. Они поставляются в различных формах и размерах, передвигаются при помощи колес, рельсов, роликов и даже магнитного поля.
Технологии робототехники делятся на три основные категории: роботы, автоматически управляемые транспортные средства (AGV) и «умные» конвейе-
164
ры. В большинстве случаев системы транспортировки являются гибридным решением, разработчики которого используют подходящую технологию для выполнения работы в определенном месте, поэтому основная задача заключается в определении технологии, наилучшим образом соответствующей поставленной задаче.
Роботы – превосходное средство для переноса грузов с одного транспортного средства на другое, например для перемещения изделий с конвейера на поддоны или укладки заказа на поддоне с помощью выбора изделий, находящихся на других поддонах.
Для непосредственной транспортировки робот – не самое экономичное решение, но если вам необходимо правильно расположить изделие, взять его с конвейера и установить на машину, робот идеально подходит для этого.
Роботы на линиях сборки автомобилей начинались с моделей в виде классической шарнирной руки. Постепенно у них появилось зрение, интеллект и способность работать вместе. Еще более гибкими являются системы произвольной формы, структура и динамика которых точно соответствует поставленной задаче. Чаще всего такие структуры имеют вид портала подъемного крана, составленного из двух тележек, которые перемещаются по параллельным рельсам. Они поддерживают большую крестообразную балку с третьей тележкой, которая обеспечивает роботу вторую степень свободы. Лебедка или кран, висящие на этой тележке, предоставляют третью степень свободы.
Дельта-роботы имеют крестообразную структуру с продуманной геометрией, которая обеспечивает им жесткость при небольшой массе и, соответственно, делает их легкими и быстрыми. Эти роботы имеют ограниченные пределы перемещения в пространстве и полезную грузоподъемность, но перемещают грузы с удивительной скоростью и ловкостью.
Автоматически управляемые транспортные средства (AGV) – самоходные и самоуправляемые транспортные средства, которые могут поднимать, переносить или буксировать грузы от места хранения до места назначения. Для выполнения этих функций AGV должно иметь на борту серьезную интеллектуальную систему и большое количество датчиков. Конечно, поскольку AGV, по определению, является свободно перемещающимся устройством, это вызывает больше вопросов обеспечения безопасности по сравнению с другими технологиями транспортировки материалов. Значительная часть сенсорных и вычислительных возможностей AGV направлена на снижение этих рисков.
Как правило, используются управляемые транспортные средства в интегрированных системах, где необходимо перемещать тяжелые грузы на большие расстояния и/или в разные места. Математические расчеты подтверждают, что это самое дешевое решение. Если необходимость перемещения на большие расстояния возникает не очень часто, использование AGV дает существенный экономический эффект.
AGV c установленным вилочным захватом могут перемещать крупногабаритные грузы на большие расстояния. Могут устанавливаться другие подъемные
165

системы, например боковые захваты. Автоматические управляемые тележки с платформами могут использоваться как мобильные фиксаторы заготовок, передвигающиеся от одного производственного участка к другому. Автоматические управляемые тягачи могут переместить нагруженные тележки, куда это необходимо, и оставить их там для загрузки/разгрузки или на временное хранение.
Во многих отраслях машиностроительной промышленности погрузочноразгрузочные механизмы предназначены для перемещения изделий с одного производственного участка на другой (рис. 2), и при выполнении таких перемещений роботы играют немаловажную роль. Разработан и внедрен робот на английском автомобилестроительном заводе. Он передвигается на гусеницах между пятью производственными участками завода. Робот извлекает пластмассовую деталь автомобиля из установки для инжекторного прессования и последовательно переносит деталь на доводочные участки, где с нее снимаются заусенцы. Далее робот помещает деталь на специализированный станок, который полирует ее, и наконец деталь перемещается с полировального станка на конвейер.
Рис. 2. Робот-укладчик
Наиболее приспособленным для тяжелых условий работы является промышленный робот-манипулятор KUKA KR-16 (рис. 3), предназначенный для перемещения устройства напыления (плазмотрона, высокоскоростного газопламенного пистолета).
Рассмотрим алгоритм работы робота (рис. 4). Выходные параметры объекта регулирования и характеристики возмущающих факторов находятся под постоянным контролем и управлением с помощью устройств, дополнительно включаемых в состав управляющей системы. Анализируя функции программной
иадаптивной систем управления роботом, решающим рассматриваемую задачу, можно заметить, что они отличаются только устройствами, воспринимающими информацию о внешней среде. Эти устройства обрабатывают эту информацию
ивыбирают последовательность обхода уже имеющихся в программе робота точек позиционирования по заданному алгоритму.
166
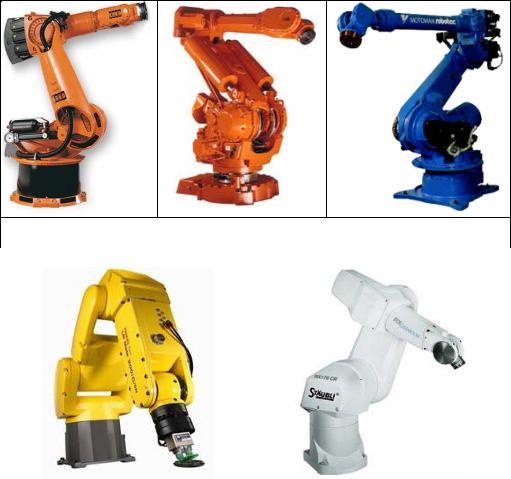
KUKA |
ABB |
MOTOMAN |
|
|
|
ANUC |
STAEUBLI |
Рис. 3. Основные марки роботов, применяемых на конвейерах по сборке автомобилей
Наблюдаемое поведение объекта описывается некоторым показателем качества, оценивающим в количественной форме характер протекания процесса управления. Отклонение показателя качества за пределы допуска влечет за собой автоматическую настройку параметров регулятора или замену алгоритма управления, результатом которых является достижение желаемого показателя качества или реализации поставленной цели (рис. 5). Описанные свойства присущи в разной степени всем адаптивным системам управления, всегда являющимися системами с обратной связью. В зависимости от цели управления адаптивные системы в робототехнике можно условно разделить на следующие уровни.
167

Рис. 4. Алгоритм работы робота, оснащенного адаптивной системой
Первый уровень характеризуется способностью самонастройки параметров регулятора на основе информации о состоянии объекта, находящегося под возмущающим действием внешней среды. Оценка состояния объекта может осуществляться либо прямым измерением требуемых параметров, либо путем их идентификации. В последнем случае на объект подаются определенные пробные управляющие воздействия, фиксируется его реакция и на основании анализа поведения объекта дается оценка его априорно неизвестным или изменившимся параметрам.
Для второго уровня адаптации робототехнических систем характерно включение в состав управляющего устройства дополнительных информационных средств, обеспечивающих сбор и обработку данных о состоянии внешней среды. На основании анализа изменений внешней среды осуществляется коррекция управляющей программы робота, позволяющая в новых условиях достичь поставленной цели. Хотя на этом уровне адаптации коррекция программных действий допускается лишь в небольших пределах, эффект от применения таких адаптивных систем управления на практике значителен. Примером может служить электродуговая роботизированная сварка крупногабаритных изделий. В этом технологическом процессе трудно обеспечить постоянство пространственного расположения линии стыка свариваемых частей от изделия к изделию. Поэтому сварочный робот должен уметь корректировать программную траекторию движения электрода в соответствии с реальным положением линии стыка, измеряемым специальными датчиками.
168

Рис. 5. Рабочая структура робота
Понятие цели управления для адаптивных робототехнических систем третьего уровня вытекает из требования реализации максимальной производительности при обеспечении отсутствия брака. Характерны для этого уровня адаптации развитые средства для сбора информации о внешней среде, самодиагностирования, а возможно, и саморемонта компонента управляемой производственной системы. Рассмотренные уровни адаптации робототехнических систем различаются не столько количеством дополнительных устройств, обеспечивающих сбор и обработку информации об изменении параметров оборудования, внешней среды и характере их взаимодействия, сколько возможностью организовывать системы, способные функционировать во все более сложных, непредсказуемых изменениях условий эксплуатации. Таким образом, основное свойство адаптивных систем – реализация цели управления в условиях недетерминированной внешней среды и дрейфа параметров робота – отражается в структуре двумя новыми элементами: информационной системой, а также устройством для вычисления координат целевых точек и последовательности их обхода, использующим информацию об изменениях, произошедших во внешней среде и компонентах робота. Функции управления адаптивным роботом выполняет вычислительное устройство, уровень сложности которого определяется уровнем адаптации робота. В простейшем случае это может быть микропроцессор или микроЭВМ, для сложных адаптивных робототехнических систем вычислительное устройство может представлять собой мультимикропроцессорную сеть. Для современных адаптивных робототехнических систем характерно совмещение в вычислитель-
169
ном устройстве функции адаптации к изменениям внешней среды и параметров приводов робота с широким набором аппаратурных и программных средств самодиагностики и устранения мелких неисправностей в самой системе управления.
Таким образом, развитие технологий, применяемых в современных автомобилях, заставляет использовать на сборочных конвейерах сложные с технической точки зрения роботы и системы их управления. Совершенствование этих механических помощников и производственной линии в целом позволит достичь высоких показателей качества сборки, а также сделать этот процесс более экономически выгодным и эффективным.
Список литературы
1.http://www.bestreferat.ru/referat-32217.html
2.http://www.controlengrussia.com/mar08-5.php4?art=1683
3.Поезжаева Е.В. Промышленные роботы: учеб. пособие: в 3 ч. – Пермь: Изд-во Перм. гос. техн. ун-та, 2009. – Ч. 2. – 185 с.
4.Поезжаева Е.В. Промышленные роботы: учеб. пособие: в 3 ч. – Пермь: Изд-во Перм. гос. техн. ун-та, 2009. – Ч. 3. – 164 с.
170