
Современные научные исследования в дорожном и строительном производс
..pdfСписок литературы
1. Чоу В.Т. Гидравлика открытых каналов. – М.: Госстройиздат, 1969. –
464 с.
2. Перевозников Б.Ф., Ильина А.А. Сооружения системы водоотвода с проезжей части автомобильных дорог. Обзорная информация. – М.: Информав-
тодор, 2002. – 61 с.
3. Типовые конструкции, изделия и узлы зданий и сооружений. Серия 3.503.1–85. Рассеивающие трамплины, 1988.
231
СОВЕРШЕНСТВОВАНИЕ КОНСТРУКЦИИ ДОРОЖНОЙ ОДЕЖДЫ С МОНОЛИТНЫМ ЦЕМЕНТОБЕТОННЫМ ПОКРЫТИЕМ
А.В. Веселов, Ю.В. Мелешкина
Магнитогорский государственный технический университет им. Г.И. Носова, Россия
Современная Россия постоянно испытывает недостаток качественных автомобильных дорог, и эта негативная тенденция продолжает усугубляться. Вместе с тем автомобильные дороги с асфальтобетонными покрытиями, получившие за последние полвека наибольшее распространение в нашей стране, не отвечают требованиям времени. В то время же интенсивность движения автотранспорта и количество тяжелых большегрузных автомобилей на дорогах ежегодно возрастает, фактические сроки службы асфальтобетонных покрытий по сравнению с установленными нормативными сроками сокращаются. Это сокращение обусловлено в первую очередь ростом интенсивности движения автотранспорта, а также негативным влиянием на покрытия при- родно-климатических факторов.
Выходом из сложившейся ситуации мог бы стать переход к строительству автомобильных дорог с монолитными цементобетонными покрытиями. Преимущества этих покрытий перед асфальтобетонными неоднократно приводились в публикациях многих специалистов в области дорожного строительства. При этом авторы одной из статей [1] отмечают, что наблюдаемый рост грузоподъемности транспортных средств и интенсивности движения закономерно требует соответствующего повышения несущей способности и долговечности покрытий, в связи с чем в мире расширяется применение в дорожных покрытиях цементобетона более высокой прочности, а также увеличение толщины цементобетонных покрытий.
Негативным следствием увеличения толщины покрытий всегда является возрастание их материалоемкости и стоимости. Традиционная конструкция дорожной одежды с цементобетонным монолитным покрытием представляет собой «слоеный пирог», где каждый конструктивный слой выполнен в виде самостоятельно воспринимающей нагрузку от автотранспорта плоской плиты (рис. 1), имеющей необходимую для восприятия нагрузки жесткость. Увеличение грузоподъемности транспортных средств требует соответствующего повышения жесткости слоев дорожной одежды. Но поскольку жесткость плоских монолитных цементобетонных плит дорожных покрытий напрямую зависит от их толщины, приходится увеличивать толщину плит для повышения их жесткости.
232
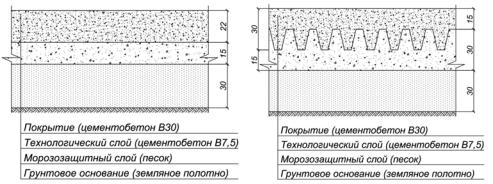
Вместе с тем увеличение жесткости монолитных цементобетонных плит дорожных покрытий без увеличения их толщины становится возможным, если произвести замену плоской монолитной плиты на плиту ребристую (рис. 2), вертикальные продольные ребра которой размещаются в пазах аналогичных ребер плиты нижележащего технологического слоя. В этом случае нагрузка от автотранспорта через систему вертикальных ребер будет совместно восприниматься как монолитным цементобетонным слоем покрытия, так и нижележащим технологическим слоем, т.е. фактически нагрузка будет восприниматься единым совокупным слоем, равным толщине обоих слоев дорожной одежды. При этом жесткость покрытия значительно возрастает как в продольном, так и в поперечном по отношению к оси дороги направлениях. Корректируя расчетным путем толщины обоих слоев и высоту их вертикальных ребер, можно добиться оптимальных соотношений жесткости и материалоемкости слоев в зависимости от предполагаемых транспортных нагрузок на дорожную одежду.
Рис.1. Традиционное конструктивное |
Рис. 2. Предлагаемое конструктивное |
решение дорожной одежды с плоской |
решение дорожной одежды с ребристой |
плитой монолитного цементобетонного |
плитой монолитного цементобетонного |
покрытия |
покрытия |
Технологический процесс выполнения дорожных одежд с ребристой монолитной цементобетонной плитой покрытия лишь незначительно отличается от традиционной технологии устройства одежд с монолитными цементобетонными покрытиями. Дополнительно к обычному комплекту дорожно-строительных машин потребуется использование 10–16-тонного тандемного двухвальцового катка с жесткой рамой, металлические вальцы которого выполнены с ребрами по окружности вальца. Ребра, расположенные на определенном расстоянии друг от друга и имеющие поперечное сечение в виде равнобедренной трапеции (рис. 3), предназначены для формирования в технологическом слое дорожной одежды матрицы (опалубочной формы) для последующего устройства ребристой монолитной цементобетонной плиты.
233
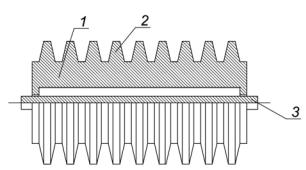
Рис. 3. Конструкция вальца дорожного катка с ребрами: 1 – барабан вальца; 2 – ребра; 3 – ось вальца
Общий технологически процесс устройства дорожной одежды с монолитной ребристой цементобетонной плитой покрытия представляется в виде последовательного производства следующих операций на захватке:
–планировка, придание заданных уклонов и уплотнение поверхности грунтового основания дорожной одежды;
–отсыпка, планировка и уплотнение морозозащитного песчаного слоя;
–укладка с помощью асфальтоукладчика нижней части технологического слоя, уплотнение его последовательно легкими, средними и тяжелыми катками необходимым числом проходов до требуемых значений плотности;
–укладка с помощью асфальтоукладчика в верхней части технологического слоя, прикатка его легкими катками с последующим формированием из этого материала несколькими проходами «вперед-назад» по одному следу тандемного 10–16-тонного катка с ребристыми вальцами матрицы для устройства ребер монолитного покрытия;
–уход за бетоном отформованной матрицы с использованием полимерной пленкообразующей композиции до набора бетоном прочности на сжатие не менее 50 % от марочной;
–установка в матрице металлических штырей и закладных деталей для устройства температурных и деформационных швов покрытия;
–устройство ребристой плиты монолитного цементобетонного покрытия (укладка, разравнивание и виброуплотнение бетонной смеси, заглаживание горизонтальной поверхности плиты и устройство на ней бороздок шероховатости);
–уход за уложенным бетонным покрытием с использованием полимерной пленкообразующей композиции до набора им требуемых значений прочности;
–нарезка швов на поверхности монолитного цементобетонного покрытия, заполнение швов мастикой.
Основным недостатком используемого для устройства технологического слоя низкомарочного бетона класса В7,5 является медленный (в течение 28 сут при нормальных условиях твердения) набор марочной прочности. Поэтому для выполнения матрицы в качестве альтернативных низкомарочному бетону могут
234
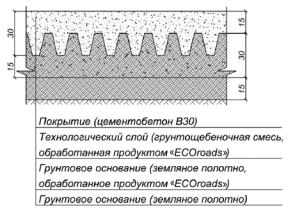
быть использованы другие, равноценные по прочностным и стоимостным показателям дорожно-строительные материалы, имеющие меньшие сроки набора прочности. Это могут быть мелкозернистые или песчаные асфальтобетонные или дегтебетонные смеси, серобитумные асфальтобетонные смеси и другие, быстро твердеющие с понижением их температуры. Вместе с тем наиболее привлекательным вариантом материала технологического слоя, сочетающим в себе лучшие свойства перечисленных ранее материалов, видится вариант использования грунта, обработанного продуктом «ECOroads». «ECOroads» – это новый, производимый в США жидкий продукт на основе биомассы, используемый для стабилизации грунтов. В настоящее время он мало известен в нашей стране. Согласно имеющейся рекламной информации производителя данного продукта [2], обработанный водным раствором «ECOroads» природный грунт, содержащий в своем составе не менее 15–20 % глинистых или илистых частиц и имеющий после обработки близкую к оптимальной влажность, в результате последующего уплотнения и 3-суточной выдержки приобретает новые свойства. Он становится значительно более плотным и прочным, практически водонепроницаемым, не подвержен вспучиванию при морозах и образованию колейности при интенсивном движении автотранспорта. Следовательно, по совокупности этих качеств грунт, обработанный продуктом «ECOroads», может быть успешно использован в качестве материала технологического слоя для формирования матрицы. По мнению авторов статьи, конструктивное решение дорожной одежды с ребристой плитой монолитного цементобетонного покрытия при использовании в качестве материала технологического слоя грунта обработанного «ECOroads», может выглядеть, как представлено на рис. 4.
Рис. 4. Предлагаемое конструктивное решение дорожной одежды с использованием продукта
«ECOroads»
Несмотря на то, что рыночная стоимость «ECOroads» составляет около 350$ за литр, его применение при устройстве дорожных одежд с монолитным цементобетонным ребристым покрытием представляется экономически целесообразным. Использование продукта «ECOroads» в случае подтверждения его свойств, приводимых в рекламной информации, позволит:
235
–отказаться от дорогостоящих традиционных дорожно-строительных материалов (низко марочного цементобетона, песка и др.);
–снизить объемы грузоперевозок и транспортные расходы при строительстве автомобильных дорог;
–упростить технологию производства дорожных одежд с монолитными цементобетонными покрытиями;
–сократить сроки строительства автомобильных дорог.
В заключение сделаем следующие выводы:
1.Дорожные одежды с цементобетонными монолитными покрытиями имеют ряд преимуществ перед аналогичными одеждами с асфальтобетонными покрытиями.
2.Традиционное конструктивное решение дорожных одежд с монолитными цементобетонными покрытиями может быть усовершенствовано.
3.При устройстве дорожных одежд с цементобетонными монолитными покрытиями может быть эффективным использование продукта «ECOroads» вместо традиционных дорожно-строительных материалов.
Список литературы
1.Шейнин А.М., Эккель С.В. «Зеленый свет» цементобетонным покрытиям // Автомобильные дороги. – 2010. – № 3. – С. 42–44.
2.Есоroads@mail.ru
236
СРАВНЕНИЕ ФИЗИКО-МЕХАНИЧЕСКИХ СВОЙСТВ ЩМА С ПРИМЕНЕНИЕМ СТАБИЛИЗИРУЮЩИХ ДОБАВОК СД-2 (ПРОИЗВОДСТВА ООО «ФИРМА ГБЦ»)
И «КАМА» (ПРОИЗВОДСТВА ЦБК «КАМА»)
А.О. Добрынин, И.В. Осипов
Пермский государственный технический университет, Россия
Щебеночно-мастичная асфальтобетонная смесь (ЩМАС) – рацио-
нально подобранная смесь минеральных материалов (щебня, песка из отсевов дробления и минерального порошка), дорожного битума (с полимерными или другими добавками или без них) и стабилизирующей добавки, взятых в определенных пропорциях и перемешанных в нагретом состоянии.
Щебеночно-мастичный асфальтобетон (ЩМА) – уплотненная щебе-
ночно-мастичная асфальтобетонная смесь.
Стабилизирующая добавка – вещество, оказывающее стабилизирующее влияние на ЩМАС и обеспечивающее устойчивость ее к расслаиванию.
Целью данной учебно-исследовательской работы является подбор состава ЩМА, проведение испытаний и сравнение физико-механических свойств ЩМА с использованием стабилизирующей добавки СД-2 производства ООО «Фирма ГБЦ» (г. Екатеринбург) и наполнителя волокнистого «Кама» производства ЦБК «Кама» (г. Краснокамск).
Основной задачей исследования является выявление оптимального процентного содержания добавки «Кама» в ЩМА, при котором материал будет удовлетворять требованиям ГОСТ 31015–2002.
Стабилизирующая гранулированная добавка для производства ЩМА комплексного действия производства ООО «Фирма ГБЦ»
Высокое качество и долговечность ЩМА обеспечиваются следующими условиями: правильным подбором компонентов смеси (прежде всего выбором прочных, трудношлифуемых щебней), их рациональным соотношением, адгезионным взаимодействием между вяжущим и минеральным заполнителем.
Во многих случаях использование щебней так называемого «кислого» состава (гранитов, кварцевых порфиров и т.п.) ограничено их плохим взаимодействием с битумом и требует применения адгезионных добавок. В таких случаях требуется дополнительная технологическая последовательность по дозированию и введению добавок в вяжущее.
СД-2 позволяет «интеллигентно» решить данную проблему. Добавка состоит из хорошо зарекомендовавших себя в качестве битумоносителя волокон целлюлозы и полимерной добавки комплексного действия – окисленного атактического полипропилена (ОАПП).
237
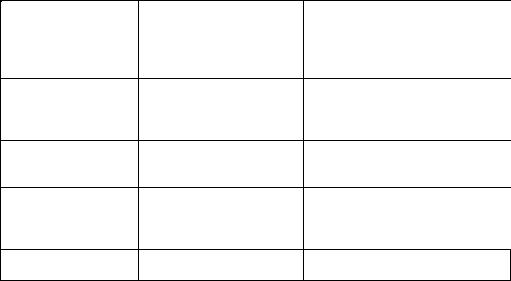
Учеными доказано, что ОАПП обеспечивает не только повышение адгезии битума к поверхности щебней кислого состава, значительное улучшение реологических свойств битумов, но и защищает вяжущее от старения как во время приготовления смеси, так и в составе асфальтобетонного покрытия. Разработан состав СД-2 с соотношением компонентов, максимально обеспечивающим их синергетическое комплексное действие.
Добавка представляет собой цилиндрические гранулы длиной 5–10 мм, диаметром 3 мм, светло-серого цвета с насыпной плотностью 450–500 кг/м3. Процессы транспортировки, хранения, подачи СД-2 в смеситель не отличаются от известной технологии ЩМА. Добавка может вводиться в смеситель по линиям подачи со шнековыми или пневматическими системами транспортирования. Компоненты СД-2 нетоксичны и не оказывают раздражающего действия на персонал при погрузо-разгрузочных операциях, приготовлении и укладке щебеноч- но-мастичного асфальтобетона. Ориентировочный расход добавки в зависимости от битумоемкости минеральных компонентов составляет 0,4–0,55 % от массы смеси.
С применением при приготовлении ЩМА СД-2 в одной технологической операции решается 4 задачи: стабилизация ЩМА волокнами целлюлозы, обеспечение гарантированного сцепления битума со щебнем, улучшение реологические свойства битума, защита вяжущего от старения. Таким образом, достигается главная цель – повышенная долговечность ЩМАв составе покрытия.
Наполнитель волокнистый для асфальтобетонных щебеночно-мастичных смесей производства ЦБК «Кама»
По показателям качества наполнитель был испытан на соответствие ТУ
5422-002-57448909–2005, данные приведены в табл. 1.
Наименование
показателя
Внешний вид
Состав по волокну
Содержание волокон длиной от 0,1 до 2,0 мм, %, не менее Термостойкость при температуре 220 оС по изменению массы при прогреве, %, не более Влажность, %
по массе, не более
Значение показателя
сыпучий волокнистый порошок от белого до светло-желтого цвета 70–80 % целлюлоза биосульфитная хвойной и лиственной пород, 30–20 % древесноеволокно
80
7,0
8,0
|
Таблица 1 |
|
|
Метод испытаний |
|
Фактические |
|
|
|
||
|
|
данные |
|
|
|
Цвет белый |
|
ГОСТ 7500 |
|
|
|
|
80 |
|
|
|
|
|
|
|
|
20 |
|
По п. 4.3 ТУ 5422- |
|
100 |
|
002-57448909–2005 |
|
|
|
|
|
|
|
ГОСТ 31015 |
|
|
|
|
0,13 |
|
|
ГОСТ 31015 |
|
|
|
|
5,5 |
|
|
|
|
|
|
238
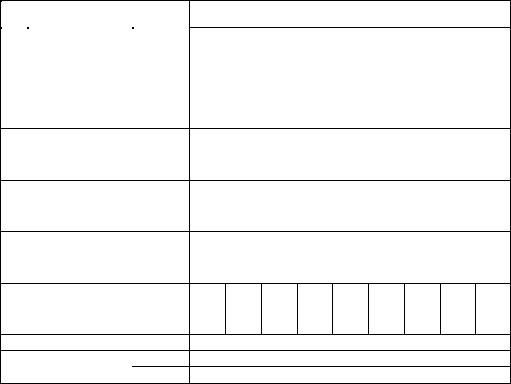
Вкачестве материала для проведения испытаний был взят ЩМА-15. На первом этапе был сделан подбор состава ЩМА с применением добавки СД-2
вколичестве 0,5 % и минерального порошка в количестве 11 %. Количество добавки СД-2 в составе 0,5 % обусловливалось тем, что за основу был взят готовый подбор состава ЩМА-15, предоставленный ОАО «Пермдорстрой».
Вкачестве исходных материалов для приготовления смеси были исполь-
зованы:
–щебень фр. 10–15 – карьер «Кушва», Свердловская обл.;
–щебень фр. 5–10 – карьер «Кушва», Свердловская обл.;
–отсев фр. 0–5 – карьер «Кушва», Свердловская обл.;
–мин. порошок (МП) активированный – г. Пермь;
–битум БНД 90/130 – г. Кунгур, Пермский край.
Зерновой состав смеси приведен в табл. 2.
Таблица 2
№ |
Наименование |
Содер- |
|
п/п |
материалов |
жание, % |
|
|
Щебень к-р |
|
|
|
|
||
1 |
«Кушва» фр. |
55,0 |
|
|
10-15 |
|
|
2 |
Щебень к-р |
17,0 |
|
«Кушва» фр. 5-10 |
|||
3 |
Отсев к-р |
17,0 |
|
«Кушва» фр. 0-5 |
|||
4 |
МП активиро- |
|
|
11,0 |
|||
|
ванный |
|
|
5 |
Стабилизирую- |
|
|
0,5 |
|||
|
щая добавка |
|
|
|
|
|
|
|
|
100 |
|
|
Требования |
min |
|
ГОСТ 31015–2002 |
max |
Размер зерен, мм, мельче
15 |
10 |
5 |
2,5 |
1,25 |
0,63 |
0,315 |
0,16 |
0,071 |
50,3 |
|
|
|
|
|
|
|
|
8,3 |
0,3 |
0,3 |
0,3 |
0,3 |
0,3 |
0,2 |
0,1 |
|
17,0 |
|
|
|
|
|
|
|
|
15,6 |
0,7 |
0,2 |
0,2 |
0,2 |
0,2 |
0,1 |
0,1 |
|
17,0 |
|
|
|
|
|
|
|
|
17,0 |
15,2 |
10,6 |
8,6 |
6,5 |
4,6 |
3,0 |
1,8 |
|
11,0 |
|
|
|
|
|
|
|
|
11,0 |
11,0 |
11,0 |
11,0 |
11,0 |
10,9 |
10,5 |
9,4 |
|
|
|
|
|
|
|
|
|
|
95,3 |
51,9 |
27,2 |
22,0 |
20 |
18 |
16 |
13,8 |
11,2 |
90 |
40 |
25 |
18 |
15 |
12 |
10 |
9 |
9 |
100 |
60 |
35 |
28 |
25 |
22 |
20 |
16 |
14 |
В соответствии с ГОСТ 12801–98 были проведены физико-механические испытания образцов щебеночно-мастичного асфальтобетона по всем показателям. Сравнивались образцы ЩМА-15 с добавкой СД-2 и «Кама» в количестве 0,5 %, а также образцы ЩМА-15 с добавкой «Кама» в трех процентных содержаниях: 0,5 %, 0,4 % и 0,3 %. Оказалось, что добавка «Кама» (0,5 %) ничуть не ус-
239
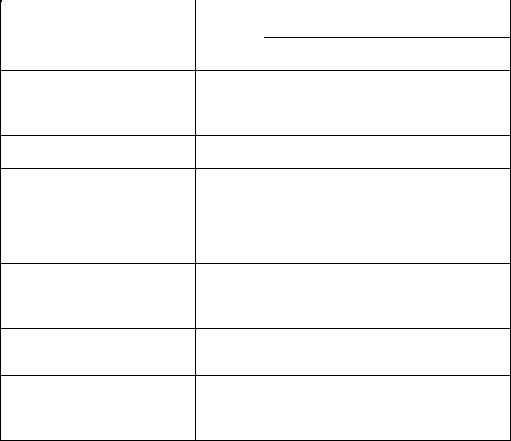
тупает по своим физико-механическим свойствам широко использующейся добавке СД-2 (0,5 %). И даже с меньшим количеством добавки «Кама» (0,4 %) материал также удовлетворяет требованиям ГОСТ 31015–2002.
Результаты всех испытаний были обработаны, проанализированы и сведены в сравнительную табл. 3, дающую возможность наглядно сопоставить показатели конкурирующих добавок.
Наименование показателя
1.Средняя плотность, г/см3
2.Пористость минерального остова, % по объему не более
3.Остаточная пористость, % по объему
4.Водонасыщение, % пообъему
5.Прочность при сжатии,
МПа,не менее
20 оС
50 оС
6.Коэффициент внутреннего трения, не менее
7.Сцепление при сдвиге при
50оС, не менее
8.Трещиностойкость: предел
прочности на растяжение при расколе при 0 оС
9.Водостойкость при длительном водонасыщении, не менее
10.Показатель стекания,
не более
Таблица 3
Требова- |
|
Фактические показатели |
|
||||
ния ГОСТ |
СД-2 |
|
«Кама» |
|
«Кама» |
|
«Кама» |
|
|
|
|||||
31015–02 |
|
|
|
||||
|
0,5 % |
|
0,5 % |
|
0,4 % |
|
0,3 % |
– |
2,62 |
|
2,63 |
|
2,62 |
|
2,59 |
15–19 |
|
|
|
|
|
|
16,5 |
17,1 |
|
16,2 |
|
15,5 |
|
||
1,5–4,5 |
|
|
|
|
|
|
5,5 |
4,4 |
|
4,0 |
|
4,4 |
|
||
1,0–4,0 |
|
|
|
|
|
|
3,55 |
3,36 |
|
3,01 |
|
2,66 |
|
||
2,20 |
|
|
|
|
|
|
3,07 |
3,33 |
|
3,29 |
|
2,93 |
|
||
0,65 |
0,86 |
|
0,8 |
|
0,93 |
|
0,77 |
0,93 |
0,95 |
|
0,94 |
|
0,96 |
|
0,96 |
0,18 |
|
|
|
|
|
|
0,17 |
0,22 |
|
0,23 |
|
0,22 |
|
||
2,5–6,0 |
|
|
|
|
|
|
2,66 |
3,01 |
|
3,21 |
|
3,22 |
|
||
0,85 |
|
|
|
|
|
|
0,75 |
0,91 |
|
0,90 |
|
0,88 |
|
||
0,2 |
|
|
|
|
|
|
0,22 |
0,16 |
|
0,16 |
|
0,2 |
|
||
|
|
|
|
|
|
|
|
Подводя итог исследовательской работы, отметим, что ЩМА указанного выше конкретного состава с использованием стабилизирующих добавок СД-2 (0,5 %) и «Кама» (0,5 %; 0,4 %) отвечают требованиям ГОСТ 31015–2002. ЩМА с использованием добавки «Кама» в количестве 0,3 % не удовлетворяет требованиям ГОСТа по следующим показателям: остаточная пористость, сцепление при сдвиге, водостойкость при длительном водонасыщении и показатель стекания. Испытания образцов ЩМА-15 с добавкой СД-2 (0,5 %) и «Кама» (0,5 %) показали, что добавка «Кама» в нашем случае ничуть не уступает широко использующейся добавке СД-2. Возможно использовать добавку «Кама» даже в меньшем
240