
Пайка металлов
..pdfкотемпературный нагрев усиливает также процессы растворения паяемого металла в расплавленном припое, что может вызвать образование в шве хрупких структур и ослабить связь в основном металле по границам зерен. Кроме того, при высоких температурах может происходить выгорание легирующих компонентов и изменение состава основного металла и припоя. Поэтому температура пайки обычно выбирается на 30–50° выше температуры плавления припоя. Если припой вносится в виде порошка, то для его расплавления необходим более высокий нагрев за счет большей поверхности окисления отдельных зерен и трудности удаления окисной пленки с их поверхности.
Скорость нагрева при пайке определяется теплопроводностью материала и толщиной стенок паяемого изделия. При низких температуре и теплопроводности материала и большой толщине стенок нагрев паяемого изделия необходимо производить медленно во избежание коробления и образования трещин.
Выдержка при температуре пайки выбирается на основе экспериментальных данных и должна быть такой, чтобы обеспечить расплавление припоя, заполнение зазоров и образование галтелей. В зависимости от способа пайки она может быть от нескольких секунд до часа и более. Кратковременные выдержки обычно имеют место при индукционной пайке и пайке погружением. Наиболее длительные выдержки применяются при диффузионном методе пайки. Выдержка в значительной мере определяется свойствами основного материала и припоя: чем менее активно припой взаимодействует с основным металлом при температуре пайки, тем большей должна быть выдержка.
Режим охлаждения после пайки назначается таким, чтобы предупредить излишнее окисление металла изделия и не вызвать разрушения шва, когда припой еще находится в твердо-жидком состоянии. Максимальные значения скорости охлаждения ограничиваются опасностью образования трещин вследствие чрезмерных термических напряжений и возникновения пористости в связи с сокращением времени пребывания металла шва в жидком состоянии,
81
в течение которого растворенные в расплавленном металле газы не успевают выделиться.
После пайки детали подвергаются дальнейшей обработке: удаляются остатки флюса, зачищаются наплывы припоя и проводится термическая обработка. Для удаления остатков флюса деталь промывают в холодной или горячей воде, в специальных растворах или зачищают металлической щеткой, обдувают песком и т.п. Остатки флюсов, содержащих хлористые соли щелочных и щелочно-земельных металлов, необходимо удалять особенно тщательно, так как они оказывают активное коррозионное воздействие на металл. Если после удаления остатков флюса швы подвергаются механической обработке, то в случае коррозионно-активных флюсов необходима повторная промывка, таккакмогутбытьвскрытывключенияфлюса.
Если после пайки производится термическая обработка, то после затвердевания припоя последующее охлаждение производится
вохлаждающей среде. При этом если нагрев изделия производился
вприспособлении, то и охлаждение изделия во избежание деформации также необходимо производить в закрепленном положении. Детали из углеродистых и легированных сталей могут подвергаться любому виду термической обработки: отжигу, нормализации, закалке, отпуску. В отдельных случаях, при наличии коробления, паяные детали подвергаются правке как в холодном состоянии, так и при нагреве. Допустимая величина относительной деформации при холодной правке для низкоуглеродистых сталей составляет 2–3 %, а для аустенитных сталей и сплавов – до 8 %. Если деформации превышают указанные пределы, то правку производят с нагревом.
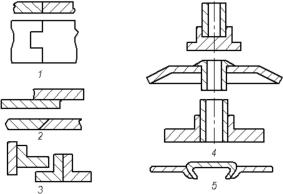
ГЛАВА 9. СОЕДИНЕНИЯ, ПРИМЕНЯЕМЫЕ ПРИ ПАЙКЕ
Паяным соединением называется элемент паяного изделия, включающий паяный шов и прилегающие к нему участки соединяемых металлов (ГОСТ 19249-73 Соединения паяные).
Прочность паяного соединения обычно определяется прочностью сплава, образующегося в шве в результате взаимодействия припоя с основным металлом, точнее, прочностью наиболее слабой зоны паяного шва, а также силами связи в контакте припой–основной металл. Поскольку прочность припоя и металла шва обычно ниже прочности основного металла, для обеспечения равнопрочности паяного изделия увеличивается площадь шва. Поэтому основным соединением при пайке является нахлесточное, в противоположность сварке, где основным соединением является стыковое. При конструировании паяных изделий необходимо стремиться к тому, чтобы паяные соединения в конструкции были равнопрочны с наиболее слабым ее звеном. При пайке, как уже указывалось выше, используются в основном нахлесточные швы, прочность соединения которых тесно связана с величиной нахлеста. Однако при паяльных работах применяются еще стыковые, втулочные, специальныешвы, атакжешвысотбортовкой(рис. 17).
Рис. 17. Типыпаяныхшвов: 1 – стыковые; 2 – нахлесточные; 3 – сотбортовкой; 4 – втулочные; 5 – специальные
83
В зависимости от вида конструкции и ее назначения пайка может применяться при соединении плоских элементов деталей; стержневых и трубчатых элементов деталей; криволинейных поверхностей элементов деталей между собой и с плоскими.
9.1.Конструкции паяных соединений
вплоских элементах
Конструкции паяных соединений в плоских элементах деталей являются наиболее простыми. Они включают, в себя соединения внахлестку, ступенчатое, гребенчатое, косостыковое, стыковое и тавровое. Схемы соединений приведены на рис. 18. и в прил. 1.
Наиболее распространенными в паяных конструкциях являются соединения внахлестку (рис. 18, а). Изменение величины перекрытия деталей позволяет достичь равнопрочности паяного соединения. Величина нахлестки устанавливается расчетным путем в зависимости от прочности основного материала и припоя. Практически применяемая величина нахлестки колеблется в пределах от двух до пяти толщин более тонкой из соединений деталей.
При пайке серебряными, латунными, медными, никелевыми и другими высокопрочными припоями нахлестка обычно не превышает двух-трех толщин. При пайке оловянно-свинцовыми и другими припоями, обладающими сравнительно низкой прочностью, величина нахлестки достигает пяти толщин наиболее тонкой из соединяемых деталей. При этом следует иметь в виду, что очень большой нахлестку делатьнецелесообразно, таккакусилие среза воспринимается главным образом внешними (концевыми) участками паяного шва, а его средняя часть остается малонагруженной и может полноценно включиться вработу при большой нахлестке лишь после начала разрушения концевыхучастков паяного шва.
На рис. 18, а изображено простейшее нахлесточное соединение 1, образуемое простым перекрытием плоских элементов деталей. В тех случаях, когда с одной стороны соединение необходимо
84
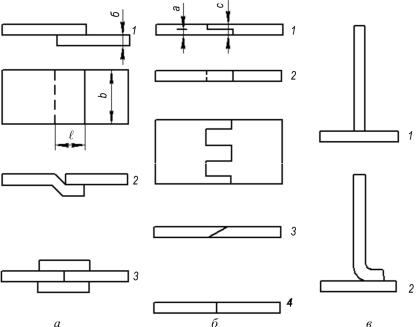
сохранить плоским, применяют нахлестку (см. рис. 18, а, 2), образуемую подгибкой одного из соединяемых элементов. После пайки плоская сторона таких соединений обычно выравнивается путем заполнения щели, образуемой кромками соединяемых листов, низкотемпературными припоями.
Для более симметричного распределения нагрузок, а также в целях повышения прочности иногда применяют соединения с накладкамисдвухсторон(см. рис. 18, а, 3).
В тех изделиях, в которых необходимо сохранить толщину стенки неизменной или применение обычного нахлесточного соединения невозможно, применяют ступенчатые, гребенчатые, косостыковые и стыковые паяные соединения (рис. 18, б).
Рис. 18. Соединения плоских элементов деталей при пайке
85
Ступенчатые и гребенчатые соединения (см. рис. 18, б, 1 и 2) наряду с сохранением сечения соединяемых элементов деталей обеспечивают высокую прочность, но требуют сложной подготовки кромок, поэтому применяются только в ответственных конструкциях.
При применении косостыковых соединений (см. рис. 18, б, 3) довольно трудно обеспечить плотное прилегание паяемых поверхностей, поэтому они применяются редко, обычно при пайке ленточных пил. Косой стык следует делать под углом не более 30°, иначе площадь пайки будет мала и, следовательно, прочность соединения недостаточна.
Стыковые соединения (см. рис. 18, б, 4) в паяных изделиях в редких случаях обеспечивают равнопрочность конструкции, поэтому широко не используются.
Применение тавровых соединений (рис. 18, в, 1) обусловлено необходимостью компоновки изделий. Более высокую прочность имеют тавровые соединения с подгибкой вертикального элемента, увеличивающей площадь паяного шва (см. рис. 18, в, 2).
9.2. Конструкции паяных соединений стержней и труб
Соединения стержней и труб между собой, соединения стержней и труб с фланцами, втулками, трубными досками и т.п. представлены на рис. 19.
При соединении стержней между собой наиболее простым является применение охватывающей втулки (рис. 19, а, 2). Соединение стержней встык из-за недостаточной прочности применяется редко. Прочность стыкового соединения может быть увеличена сочетанием его с втулочным (см. рис. 19, а, 3). При соединении труб (рис. 19, б) применение втулки также рационально. Она может устанавливаться внутри в виде бужа, что позволяет наружное сечение трубы по шву сохранить неизменным (см. рис. 19, б, 4). Для сохранения неизмененным внутреннего сечения паяемого трубопровода применяют телескопическое соединение путем развальцовки концов одной или обеих труб (см. рис. 19, б, 1 и 2).
86
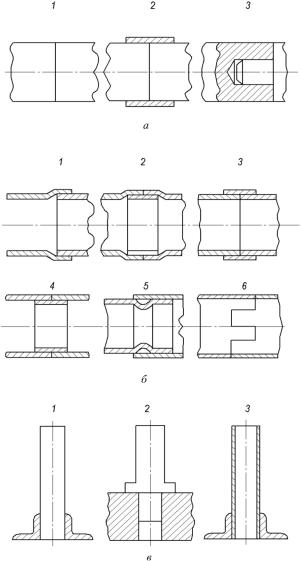
Рис. 19. Соединения стержневых и трубчатых элементов деталей при пайке между собой и с плоскими элементами
87
В случае рис. 19, б, 2 при соединении используется переходная втулка. Если необходимо сохранить и наружное, и внутреннее сечение трубы по месту соединения постоянным, то применяют пазовое соединение, или гребенчатое (см. рис. 19, б, 6). Однако такое соединение затрудняет сборку и пайку, поэтому применяется редко.
Соединение 5 (см. рис. 19, б) позволяет вносить припой при сборке между паяемыми поверхностями, что обеспечивает более равномерный пропай.
Конструктивные формы соединений стержней и труб с фланцами, трубными досками (рис. 19, в, 1, 2, 3), втулками в значительной мере определяются конфигурацией изделия, но во всех случаях необходимо учитывать, что прочность паяных соединений будет обеспечена только при наличии достаточной нахлестки. Размер площади поверхностей фланцев, втулок, трубных досок и т.п., контактирующих сo стержнями и трубами, необходимо определять расчетным путем с учетом требуемой прочности.
9.3. Соединения криволинейных поверхностей
Соединения криволинейных поверхностей между собой и с плоскими элементами нашли большое распространение в последние годы в связи с производством сотовых конструкций и паяных панелей с гофрированными проставками, которые широко используются в самолетостроении и для изготовления теплообменников. Схематичное изображение этих типов паяных соединений приведено на рис. 20. В случае рис. 20, а пайка плоских листов с гофрированной проставкой осуществляется по вершинам гофр. В случае рис. 20, б пайка происходит в местах касания гофрированных лент, образующих сотовый заполнитель, а также в местах соединения торцов сотового заполнителя с листовой обшивкой. Встречаются также конструкции, в которых трубы соединяются между собой по образующей или припаиваются к плоским листам.
88

Рис. 20. Соединения криволинейных элементов при пайке между собой и с плоскими элементами
К паяным соединениям в зависимости от назначения изделия могут предъявляться наряду с общими специальные требования: герметичность, электропроводность, коррозионная стойкость и т.д., которые также должны учитываться при выборе основного металла, припоя, способа пайки и при конструировании изделия.
ГЛАВА 10. ОСОБЕННОСТИ КОНСТРУИРОВАНИЯ ПАЯНЫХ СОЕДИНЕНИЙ
При конструировании паяных изделий необходимо правильно выбрать основной металл и припой и определить способ пайки. Припой и способ пайки оказывают существенное влияние на выбор типа паяных соединений, величину зазоров, условия сборки и закрепления элементов изделия перед пайкой.
При конструировании паяного изделия следует стремиться к уменьшению количества паяных соединений, если это не противоречит экономичности и другим соображениям. В этом случае соединения должны равномерно располагаться по изделию, по возможности вменее нагруженных местах. Основной металл выбирается в соответствии с условиями работы проектируемой конструкции и требованиями прочности, герметичности, коррозионной стойкости и др. Выбранный припойдолжен обеспечиватьзаданнуюпрочностьизделия.
При конструировании большое значение имеет правильный выбор припоя. Припой выбирается в зависимости от физико-химических свойств основного металла, условий прочности, технологии пайки итребованийжаростойкости, коррозионной стойкости ит.п.
При конструировании изделий из разнородных металлов необходимо прежде всего учитывать различие в коэффициентах их термического расширения, в противном случае в процессе пайки могут значительно измениться соединительные зазоры, и припой не заполнит их. Второй фактор, который следует учитывать при пайке разнородных металлов, – сочетание материалов, позволяющее получать пластичные и прочные паяные соединения. Например, при высокотемпературной пайке титана с медью и никелем, алюминия с магнием и медью, магния со сталью и т.д. невозможно получить качественные паяные соединения без нанесения барьерных покрытий, предохраняющих разнородные металлы от активного взаимодействия и, следовательно, отвозникновениявпаяном швехрупкихинтерметаллидов.
90